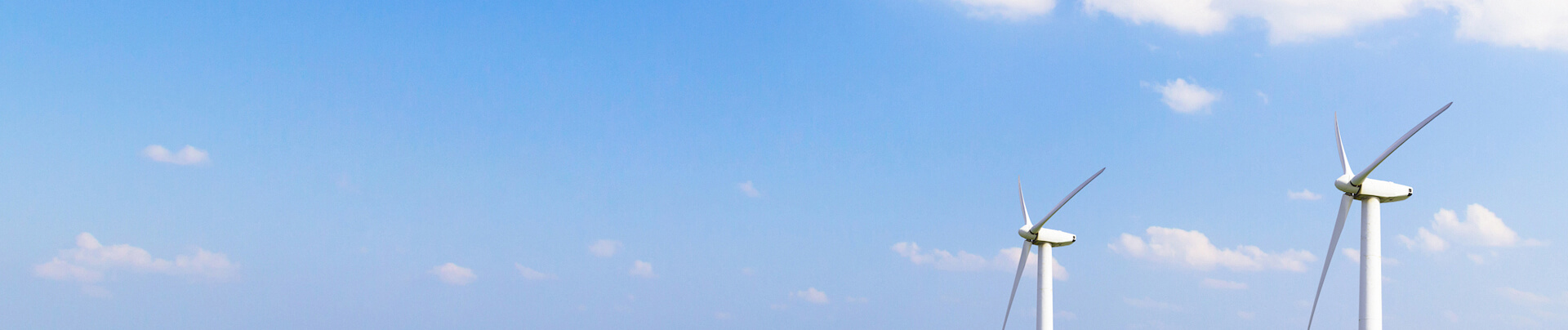
à comprendre vos objectifs commerciaux
et à nous efforcer d’améliorer les avantages de votre projet.
À mesure que les systèmes de stockage d'énergie évoluent vers une plus grande capacité et une densité énergétique plus élevée, la conception de la taille et de la compatibilité des Boîtier de bloc de batterie de stockage d'énergie sont devenues des problèmes essentiels pour améliorer l'efficacité et la fiabilité du système. Cet article combine les derniers cas de conception technique, les technologies brevetées et les tendances de l'industrie pour mener une analyse à partir de trois dimensions : l'utilisation de l'espace, la compatibilité modulaire et la conception de l'agencement et du support des cellules de batterie.
1- Optimiser l'utilisation de l'espace
L’amélioration de l’utilisation spatiale des systèmes intégrés de stockage d’énergie est essentiellement une démarche à double sens, issue de l’itération technologique et des exigences du scénario. Grâce à l’innovation collaborative de technologies telles que les cellules de batterie de grande capacité, l’architecture modulaire et l’intégration du refroidissement liquide, l’industrie passe de « l’empilement extensif » à la « réutilisation spatiale extrême ».
a. Application de cellules de batterie de grande capacité : augmentation de la densité énergétique et de l'efficacité
Résumé des idées : L'essence de l'application de cellules de batterie de grande capacité est de réduire les niveaux structurels internes du bloc-batterie et d'améliorer directement l'utilisation de l'espace des cellules de batterie au bloc-batterie. Les packs de batteries traditionnels adoptent un mode d'intégration à trois niveaux « cellule de batterie → module → pack de batteries », et la structure du module (poutres transversales, poutres longitudinales, boulons, etc.) conduit à une faible utilisation de l'espace. Les cellules de batterie de grande capacité peuvent ignorer le niveau du module en allongeant ou en augmentant le volume de la cellule unique et utiliser la technologie CTP (Cell to Pack) pour intégrer les cellules de batterie directement dans le pack de batteries.
Noyau technique : utiliser des cellules de batterie ultra-larges de 600 Ah+ pour réduire le nombre de cellules de batterie et de points de connexion, et augmenter la capacité de chaque cellule.
b. Réutilisation spatiale et optimisation des coûts : de « l'empilement de composants » à la « réutilisation multidimensionnelle »
Résumé des idées : La réutilisation spatiale et l’optimisation des coûts sont les deux faces d’une même pièce, et la logique sous-jacente est de briser les limites physiques et financières des systèmes de stockage d’énergie traditionnels grâce à la simplification structurelle, l’intégration fonctionnelle, l’itération matérielle et la conception standardisée.
Le cœur de la réutilisation spatiale est de réduire les liens intermédiaires en simplifiant à l’extrême la hiérarchie structurelle. Par exemple : Conception de boîtier haute tension deux en un : la technologie brevetée de Jiangsu Trina Energy Storage combine deux boîtiers haute tension en un seul, partageant l'ensemble des relais positifs/négatifs et des connexions électriques, réduisant ainsi de 30 % l'espace horizontal occupé et réduisant de 15 % le coût des composants électriques.
Réutilisation inter-domaines des modules fonctionnels, intégration des pièces structurelles et des canaux de dissipation thermique, comme l'intégration de la plaque de refroidissement liquide avec la plaque inférieure du boîtier, et le partage de l'espace entre le tuyau de refroidissement liquide et le support structurel, réduisant ainsi de 15 % les composants de dissipation thermique indépendants ; le corps de la cellule de batterie en tant que pièce structurelle : la batterie BYD Blade offre une résistance de support grâce à des parois latérales de cellule de batterie longues et fines, éliminant le cadre du module et augmentant l'utilisation de l'espace à 60 %-80 %.
L'optimisation approfondie de la topologie électrique, telle que la topologie en cascade haute tension, qui réduit le nombre de circuits parallèles en augmentant la capacité et le niveau de tension des cellules individuelles (comme le stockage d'énergie à chaîne intelligente de Huawei), réduit l'espace physique de la pile de batteries de 20 % et raccourcit le temps de réponse du système de 50 %. ; Conception de relais partagé, le boîtier haute tension deux-en-un de Jiangsu Trina Energy Storage permet à deux lignes de partager le même relais, réduisant ainsi le nombre de relais et la longueur du câble de 50 % et améliorant l'efficacité de l'installation de 30 %
2-Disposition des cellules de batterie et conception du support : équilibre entre la capacité de charge, la dissipation thermique et la résistance aux vibrations
L’essence de l’agencement cellulaire est un jeu entre l’utilisation de l’espace, la distribution de la chaleur et la stabilité mécanique. La forme physique et la direction de disposition de la cellule affectent directement l'efficacité de remplissage de l'espace :
a. Optimiser la disposition des cellules de la batterie
Conception de cellule de batterie inversée : la soupape antidéflagrante de la cellule de batterie est pointée vers le bas de sorte que l'échappement d'emballement thermique et l'espace anti-balle inférieur sont partagés, libérant ainsi l'espace de hauteur de la cellule de batterie et atteignant un taux d'utilisation du volume.
Disposition des cellules couchées : optimise l'utilisation de l'espace dans le sens de la hauteur du bloc-batterie, augmente la proportion de matériaux actifs et permet une utilisation du volume nettement supérieure à celle des cellules verticales.
Cellules de batterie ultra-longues et fines : Le nombre de cellules de batterie par unité de volume est réduit grâce à la conception allongée et amincies des cellules de batterie, améliorant ainsi l'efficacité du regroupement.
b. Conception de couplage de la dissipation thermique et de la portance : vise à obtenir une double optimisation de la dissipation thermique efficace et de la résistance structurelle grâce à l'innovation collaborative de la structure, des matériaux et des processus.
Parcours de conception structurelle :
Structure intégrée, telle que la conception conforme de la plaque de refroidissement liquide et de la poutre de support : intégration du canal de refroidissement liquide dans la poutre de support en alliage d'aluminium, réduisant les composants indépendants et améliorant l'utilisation de l'espace ;
Disposition en couches et compartimentée, empilant le bloc-batterie, le système de refroidissement liquide et le BMS en couches pour réduire l'interférence mutuelle entre le flux de chaleur et les contraintes mécaniques ;
Optimisation mécanique bionique, telle que la structure en nid d'abeille/ondulée, la conception d'une couche centrale en nid d'abeille ou ondulée dans le cadre de support en alliage d'aluminium (comme la solution brevetée de Mufeng.com), absorbant l'énergie de vibration par déformation tout en optimisant le chemin de dissipation thermique.
Parcours d'innovation matérielle :
Conductivité thermique et intégration porteuse, tels que les matériaux composites en fibres d'alliage d'aluminium (conductivité thermique ≥ 200 W/m·K, résistance +30 %) ; matériaux intelligents, la couche de remplissage à changement de phase (PCM) absorbe la chaleur et la libère lentement, avec une différence de température de ±1,5℃ ; Amortissement léger : la couche de coussin en silicone élastique absorbe les vibrations (amortissement +40%).
Chemin de mise en œuvre du processus :
Procédés de formage de précision, tels que le formage par extrusion : utilisés pour fabriquer des poutres refroidies par liquide en alliage d'aluminium avec des canaux d'écoulement complexes ;
Technologie de traitement de surface, telle que la génération d'une couche d'oxyde céramique sur la surface de l'alliage d'aluminium pour améliorer la résistance à la corrosion (test au brouillard salin ≥ 1000h) et améliorer l'efficacité de la dissipation thermique (émissivité de surface augmentée de 20%) ;
Processus d'assemblage intelligent et réglage dynamique de la précharge, comme l'intégration de capteurs de pression et d'actionneurs électriques pour ajuster la précharge des boulons (5-20 kN) en temps réel afin d'éviter d'endommager les cellules de la batterie par surpression.
c. Conception coordonnée de la résistance à la charge et aux vibrations de la structure de support : Le système de support doit répondre à la double exigence de résistance à la charge statique (poids des cellules de batterie + pression d'empilement) et de résistance aux vibrations dynamiques (impact du transport/sismique).
3- Modularité et compatibilité : interfaces standardisées et architecture évolutive
L’essence de l’utilisation d’une interface standardisée pour s’adapter aux cellules de batterie de tailles multiples est de parvenir à une extension flexible des spécifications des cellules de batterie sur une plate-forme unifiée grâce à l’innovation collaborative dans la gestion mécanique, électrique et thermique. La technologie actuelle est passée de la compatibilité statique à l’ajustement dynamique et évoluera vers l’intelligence, la légèreté et l’intégration inter-scénarios à l’avenir.
a. Innovation collaborative de structure mécanique :
Normalisation des interfaces mécaniques : définition de dimensions uniformes des dispositifs de connexion.
Conception modulaire de packs de batteries/armoires : des modules évolutifs et des armoires de batteries sont construits à partir d'unités de batteries standardisées (telles que des cellules de 280 Ah et 314 Ah) pour prendre en charge des combinaisons flexibles avec différentes exigences de capacité.
Figure 1-Boîtier de bloc de batterie de stockage d'énergie 280Ah
b. Réglage dynamique du système électrique
Protocoles et interfaces de communication standardisés, tels que la compatibilité BMS : formuler un protocole de communication BMS (système de gestion de batterie) unifié pour prendre en charge une connexion transparente avec les PCS et les cellules de batterie de différents fabricants ; régulation dynamique de la puissance, grâce au contrôle de l'inertie virtuelle et à l'algorithme d'optimisation multi-échelle de temps, pour obtenir un ajustement en temps réel de la puissance active/réactive ; et une conception adaptative de correspondance des paramètres électriques.
c. Adaptation intelligente du système de gestion thermique
Solutions de gestion thermique hiérarchique, telles que l'utilisation de mousse ignifuge à haute résilience, d'adhésif thermoconducteur et d'autres matériaux au niveau cellulaire pour équilibrer les exigences d'isolation et de dissipation thermique et inhiber la diffusion de chaleur ; la conception intégrée de la plaque de refroidissement liquide intégrée au niveau du module et de la couche d'isolation thermique pour améliorer la durée de vie du cycle ; Le système ajuste dynamiquement la capacité de refroidissement au niveau du système grâce à des compresseurs à fréquence variable et à plusieurs branches de réfrigération.
Surveillance et prédiction intelligentes, fusion multi-capteurs. Des capteurs de température sont placés à des endroits clés tels que les pôles des cellules de batterie et les grandes surfaces pour obtenir une acquisition de température de haute précision ; La technologie des jumeaux numériques optimise les stratégies de dissipation thermique en temps réel grâce à la surveillance du cloud et à la maintenance prédictive.
4- Conclusion
L’optimisation de l’espace des Boîtier de bloc de batterie de stockage d'énergie est passée d’une simple amélioration structurelle à une innovation collaborative multidimensionnelle :
La fusion du matériau, de la structure et de l'algorithme, comme la combinaison de la boîte en fibre de carbone + de la technologie CTP + de l'algorithme de disposition de l'IA, deviendra le courant dominant.
La modularisation et la standardisation s'accélèrent, et la conception standardisée avec Pack comme plus petite unité fonctionnelle incitera l'industrie à réduire les coûts et à augmenter l'efficacité.
La gestion thermique et l’utilisation de l’espace sont profondément intégrées, et les technologies de refroidissement liquide par immersion et de contrôle dynamique de la température libèrent davantage le potentiel de l’espace.
Nous mettrons régulièrement à jour les informations et technologies relatives à la conception thermique et à l’allègement. Merci de votre intérêt pour Walmate.
Avec la croissance explosive de la puissance de calcul de l'IA et l'augmentation continue de la densité de puissance des centres de données, la technologie traditionnelle de refroidissement par air ne peut plus répondre aux besoins de dissipation thermique. La technologie de refroidissement liquide est devenue incontournable en raison de ses avantages tels que la dissipation efficace de la chaleur, les économies d'énergie et la réduction de la consommation. Dans la technologie du refroidissement liquide, la concurrence entre la plaque froide et l’immersion est particulièrement féroce. Cet article analysera les avantages et les inconvénients des deux du point de vue des caractéristiques techniques, des scénarios d’application, de la rentabilité et des tendances futures, et explorera leurs futures directions dominantes.
1- Comparaison des caractéristiques techniques : le type à plaque froide a une forte compatibilité, le type à immersion a une efficacité de dissipation thermique plus élevée
un. Refroidissement liquide par plaque froide : une « amélioration » de la transition en douceur
Forte compatibilité : aucune modification majeure de la structure du serveur n'est requise et il est compatible avec l'infrastructure des centres de données refroidis par air existants, avec de faibles coûts de transformation et des cycles courts.
Haute sécurité : le liquide de refroidissement n'entre pas en contact direct avec les composants électroniques, le risque de fuite est donc faible et le risque peut être encore réduit grâce à une conception modulaire (comme des connecteurs à changement rapide et des tuyaux redondants).
Haute maturité : la technologie des plaques froides a été largement utilisée dans des scénarios tels que les projets de coopération Alibaba Cloud Qiandao Lake Data Center et Intel, représentant 90 % du marché actuel du refroidissement liquide.
Limitations : Le type de plaque froide ne peut couvrir que certains composants haute puissance (tels que le processeur, le GPU), et la chaleur restante doit toujours s'appuyer sur le refroidissement par air pour aider à la dissipation de la chaleur. La valeur PUE est généralement de 1,1 à 1,2, légèrement supérieure à celle du type d'immersion.
b. Refroidissement liquide par immersion : une approche innovante pour une dissipation thermique efficace
Le refroidissement liquide par immersion immerge complètement le serveur dans un liquide de refroidissement isolant, permettant ainsi la dissipation de la chaleur de tous les composants par contact direct. Ses principaux avantages incluent :
Efficacité énergétique extrême : la conductivité thermique du liquide est 20 à 30 fois supérieure à celle de l'air, le PUE peut être aussi bas que 1,05 et l'efficacité de dissipation thermique est améliorée de plus de 3 fois.
Gain de place : le volume du système de refroidissement ne représente que 1/3 de celui du refroidissement par air, et la densité de puissance d'une seule armoire peut atteindre plus de 50 kW, ce qui convient aux scénarios à haute densité tels que le supercalcul IA.
Silencieux et respectueux de l'environnement : aucun ventilateur n'est nécessaire, le bruit est réduit de plus de 90 % et il n'y a pas de pollution par la poussière, ce qui prolonge la durée de vie de l'équipement.
Défis : L'immersion nécessite des serveurs personnalisés, le coût du liquide de refroidissement représente jusqu'à 60 % (comme le liquide fluoré), l'investissement initial est élevé et la compatibilité écologique doit être améliorée.
2-Différenciation des scénarios d'application : le type de plaque froide à moyen et court terme domine, le potentiel de type immersion à long terme est libéré
un. Type de plaque froide : le choix le plus rentable pour la rénovation d'IDC existants et la construction de nouveaux IDC
Rénovation d'anciens centres de données : Le type de plaque froide peut être rapidement adapté à l'architecture de refroidissement par air existante, avec un cycle de rénovation court et des coûts contrôlables. Par exemple, la solution modulaire sur laquelle Intel et Bich ont collaboré réduit la difficulté de déploiement grâce à une conception de plaque froide standardisée.
Scénarios de calcul à moyenne et haute densité : le type de plaque froide prend déjà en charge une puissance de 130 à 250 kW par armoire (comme les GPU NVIDIA série B), répondant à la plupart des besoins de formation en IA.
b. Immersion : la solution ultime pour le supercalcul et les centres de données écologiques
Puissance de calcul ultra-haute densité : la puissance des puces de nouvelle génération (comme la série Rubin de NVIDIA) dépassera 1 000 kW, et l'immersion deviendra la seule solution envisageable.
Besoins d'économie d'énergie verte : le PUE d'immersion est proche de 1,05 et l'efficacité de récupération de chaleur perdue atteint 90 % (comme la solution de Lenovo), ce qui est conforme à la politique cible « double carbone ».
c. Situation actuelle du marché
Le type de plaque froide domine le marché actuel : en 2025, le type de plaque froide représentera 80 à 90 % du marché du refroidissement liquide, et le type à immersion représentera moins de 10 %. De plus, des interfaces standardisées ont été formées (comme la conception de plaque froide OCP d'Intel) et les solutions de fabricants tels qu'Inspur et Sugon sont hautement compatibles. Le projet national « East Data West Computing » exige que le PUE des centres de données nouvellement construits soit ≤ 1,25 et que le type de plaque froide devienne le premier choix pour la transition.
L'immersion est prête à démarrer : la solution d'immersion à changement de phase C8000 de Sugon Digital atteint un PUE de 1,04, et le centre de données « Kirin » d'Alibaba Cloud vérifie la faisabilité de l'immersion monophasée. Les puces haute puissance telles que le GPU NVIDIA B200 (1 000 W+) ont favorisé l'utilisation de la technologie d'immersion, augmentant la densité de puissance de calcul du refroidissement liquide de 30 à 50 %. L’UE prévoit d’interdire les liquides fluorés en 2028, et la recherche et le développement de liquides de refroidissement à base d’hydrocarbures/huiles de silicone nationaux se sont accélérés (comme la série « Kunlun » de Sinopec).
3-Avis faisant autorité PK
Refroidissement liquide par plaque froide : Le refroidissement liquide par plaque froide est le « brise-glace » pour la popularisation du refroidissement liquide. Au cours des cinq prochaines années, il représentera encore 80 % du marché du refroidissement liquide incrémental. Le refroidissement liquide par immersion doit attendre que la consommation d'énergie de la puce franchisse le point critique.
Faction de refroidissement liquide par immersion : Le refroidissement liquide par immersion à changement de phase est la forme ultime de refroidissement liquide, et le refroidissement liquide par plaque froide n'est qu'une solution transitoire. Lorsque la consommation électrique d'une seule puce dépasse 800 W, le refroidissement liquide par immersion devient la seule option.
Neutres : La différenciation des voies techniques reflète la stratification de la demande de puissance de calcul. Les plaques froides servent à « l'informatique orientale » et le refroidissement liquide par immersion soutient « l'informatique occidentale ». Le développement parallèle à double voie sera le thème principal de la prochaine décennie.
4-Opportunités et stratégies industrielles
Jeu coût et écologie : le refroidissement liquide par plaque froide aura le dessus à court terme, tandis que le refroidissement liquide par immersion doit réduire les coûts pour sortir de l'impasse.
Refroidissement liquide par plaque froide : optimiser les matériaux (composite cuivre-aluminium), améliorer la précision du traitement (processus anti-fuite) et promouvoir une conception modulaire et standardisée.
Refroidissement par liquide par immersion : développer des liquides de refroidissement rentables (tels que le liquide d'immersion monophasé), des armoires compatibles et coopérer avec les fabricants de puces pour personnaliser les solutions de refroidissement.
Réserves technologiques : Explorez les plaques froides à flux diphasique et les systèmes de surveillance intelligents (tels que la régulation dynamique du flux par IA) pour faire face aux futures demandes de puissance élevées.
5- Conclusion
Court terme (2025-2027) : Le refroidissement liquide par plaque froide domine les scénarios généraux, et le taux de pénétration du refroidissement liquide par immersion augmente à 15-20 % ; À long terme (2030+) : le refroidissement liquide par immersion à changement de phase devient courant dans le domaine de la puissance de calcul élevée, et le refroidissement liquide par plaque froide se retire sur le marché de la densité moyenne et faible.
Les facteurs déterminants sont : le coût du liquide de refroidissement, la vitesse d’augmentation de la consommation d’énergie des puces et les politiques internationales de protection de l’environnement.
Nous mettrons régulièrement à jour les informations et technologies relatives à la conception thermique et à l’allègement. Merci de votre intérêt pour Walmate.
Avec le développement rapide des véhicules à énergies nouvelles et des industries du stockage d'énergie, la légèreté, la sécurité élevée et une gestion thermique efficace sont devenues des exigences essentielles. Notre entreprise est fortement impliquée dans le domaine de la transformation des alliages d'aluminium. Grâce à une sélection de matériaux, des procédés de formage et des technologies de soudage de pointe, nous nous concentrons sur la recherche, le développement et la fabrication plateau de batterie, de Plaque Froide Liquide, de boîtiers de stockage d'énergie et de radiateurs. L'alliage d'aluminium est devenu un choix idéal pour la légèreté et la gestion thermique des équipements à énergies nouvelles grâce à sa faible densité (environ 2,7 g/cm³), sa grande solidité, sa résistance à la corrosion et son excellente conductivité thermique (environ 150-220 W/m·K).
1- Sélection des alliages d'aluminium et considérations clés
Les exigences de performance des alliages d'aluminium varient considérablement selon les produits. Il est donc nécessaire de combiner la résistance mécanique, la résistance à la corrosion, la soudabilité et l'adaptabilité des procédés pour une sélection complète des matériaux :
a. Plateau de batterie
Nuances courantes : 6061-T6, 6005A-T6, 6063-T6.
Critères de sélection :
·Doit présenter une résistance à la traction ≥ 240 MPa (par exemple, 6061-T6) pour satisfaire aux normes nationales d'extrusion, de chute et d'impact de bille ;
·Exigences de soudabilité élevées, les fissures thermiques doivent être évitées (la série 6xxx renforcée au magnésium/si est privilégiée) ;
·La résistance à la corrosion est améliorée par anodisation ou placage aluminium.
Figure 1 - Plateau de batterie en alliage d'aluminium
b. Boîtier de stockage d'énergie
Marques courantes : 5083, 6061-T6 (résistance mécanique et résistance à la corrosion).
Critères de sélection :
· Résistance aux vibrations et aux chocs, limite d'élasticité ≥ 200 MPa ;
· Traitement de surface rigoureux pour éviter la corrosion électrochimique.
c. Plaque Froide Liquide
Marques courantes : 3003, 6061/6063, 6082.
Critères de sélection :
· Conductivité thermique et résistance à la corrosion élevées ;
· Le canal de refroidissement liquide nécessite un moulage complexe, et la série 6xxx, offrant d'excellentes performances d'extrusion, est privilégiée.
2- Différences de performances et difficultés d'usinage
L'usinage des alliages d'aluminium doit s'adapter à leurs propriétés physiques, notamment en découpe, CNC, soudage et traitement de surface :
a. Découpe et usinage CNC
Difficultés :
· L'usinage de trous de haute précision est sujet aux bavures et aux déformations (comme des saillies sur le bord des trous étagés) en raison de la ductilité du matériau ;
· Les structures à parois minces (comme les canaux d'écoulement des plaques de refroidissement liquide) nécessitent un contrôle des forces de coupe pour éviter le gauchissement.
Solution :
· Utiliser des outils diamantés pour améliorer la netteté des arêtes et réduire la déformation par extrusion ;
· Optimiser les paramètres d'usinage (tels que la vitesse élevée et l'avance lente) et coopérer avec les équipements CNC généraux pour obtenir un usinage stable.
b. Procédé de soudage
Principaux défis :
· Le film d'oxyde (point de fusion Al₂O₃ : 2050 °C) entrave la fusion et favorise la formation de pores et d'inclusions de scories ; · Certains alliages présentent une forte tendance aux fissures à chaud, et l'énergie de la ligne et la composition du fil de soudage doivent être contrôlées.
Procédés privilégiés :
·Soudage TIG (alimentation CA) : adapté aux tôles fines, le film d'oxyde est éliminé par « nettoyage cathodique » ;
·Soudage MIG (mélange de gaz à courant élevé + hélium) : rendement de soudage élevé pour les tôles épaisses et apport de chaleur contrôlable.
Figure 2- Soudage du plateau de batterie
c. Traitement de surface
·Revêtement isolant résistant à la pression : appliqué sur le plateau de batterie et àboîtier de stockage d’énergie, il doit réussir le test de pression (≥ 3 000 V CC/1 min). L’épaisseur du revêtement est de 20 à 50 µm, afin de garantir la sécurité de l’isolation dans un environnement haute tension.
·Revêtement isolant et déshumidifiant : pour le boîtier de stockage d’énergie, des matériaux hydrophobes (tels que la résine fluorocarbonée) sont utilisés pour réduire le risque de condensation interne, et la valeur dyne est ≥ 34 pour garantir l’adhérence.
·Revêtement anti-collision : utilisé pour la paroi extérieure du support de batterie, un élastomère de polyuréthane (dureté ≥ 80 Shore A) a été sélectionné, offrant une résistance aux chocs améliorée de plus de 30 %.
·Anodisation : traitement anticorrosion conventionnel, erreur d’épaisseur du film ≤ 3 µm, adapté aux structures complexes.
3- Inspection de vérification et adaptabilité des équipements
Afin de répondre aux normes du secteur des nouvelles énergies (telles que GB/T31467.3, UL2580), une vérification multidimensionnelle et une adaptation des procédés sont nécessaires :
a. Inspection de vérification
· Résistance structurelle : Vérification des performances de portance, d’extrusion et de résistance aux impacts de billes du plateau par simulation par éléments finis (contrainte maximale ≤ limite d’élasticité du matériau) ;
· Test d’étanchéité : Le système de refroidissement liquide utilise la détection de fuites à l’hélium (taux de fuite ≤ 1 × 10⁻⁶ mbar·L/s) et un test de pression cyclique (0,5-1,5 MPa/5 000 fois) ;
· Vérification des performances du revêtement :
Test de tenue à la tension du revêtement isolant (5 000 V CC/60 s sans claquage) ;
Le revêtement anticollision a passé avec succès l’essai de chute de billes (bille d’acier de 1 kg à 1 m de hauteur) et le test au brouillard salin (1 000 heures sans décollement).
b. Optimisation de l'adaptabilité des équipements
· Transformation d'équipements CNC généraux : Grâce à la conception de dispositifs de haute précision et à un algorithme de compensation dynamique, la déformation par usinage des pièces à parois minces peut être inférieure ou égale à 0,1 mm ;
· Bibliothèque de paramètres de soudage : Définition de paramètres de soudage standard (tels que le courant et la vitesse d'alimentation du fil) pour différentes nuances d'alliages d'aluminium afin de réduire le cycle de mise au point ;
· Projection automatisée du revêtement : Grâce à la projection robotisée multiaxes, combinée à la technologie de durcissement infrarouge, l'erreur d'uniformité du revêtement est inférieure ou égale à 5 %.
Conclusion
La large application des alliages d'aluminium dans les nouveaux équipements énergétiques est non seulement une victoire de la science des matériaux, mais aussi une manifestation d'innovation en matière de procédés. Notre entreprise continuera d'explorer de nouveaux alliages d'aluminium à haute résistance, résistants à la corrosion et faciles à usiner, et de promouvoir l'amélioration des performances de produits tels que les plateau de batterie et les Plaque Froide Liquide grâce à l'innovation en matière de procédés, contribuant ainsi à la transition de l'industrie vers un avenir plus efficace et plus léger.
Nous mettrons régulièrement à jour les informations et technologies relatives à la conception thermique et à l’allègement. Merci de votre intérêt pour Walmate.
Face à l'augmentation constante de la densité de puissance des appareils électroniques, la conception de la dissipation thermique est devenue un élément clé de la fiabilité et de la durée de vie des systèmes. Forts de 19 ans d'expérience en gestion thermique, nous combinons des cas d'ingénierie classiques avec une expérience en simulation multiphysique sur le terrain pour analyser en profondeur les cinq principales erreurs techniques souvent négligées par les ingénieurs dans les scénarios haute puissance, et proposer des solutions conformes aux pratiques du secteur.
Malentendu 1 : abus de matériaux à haute conductivité thermique, écart de calcul de la résistance thermique de l'interface
Problème typique : recherche excessive des valeurs théoriques des matériaux conducteurs thermiques, ignorant la réalité technique de la résistance thermique des contacts d'interface.
Analyse de cas : Un module de dissipation thermique pour radar laser automobile utilise un substrat en cuivre pur (conductivité thermique de 401 W/m·K), mais l'épaisseur du revêtement du matériau d'interface thermique (TIM) n'est pas contrôlée avec précision (conçue à 0,1 mm, fluctuation réelle de ± 0,05 mm), et la résistance thermique de contact mesurée atteint 0,6 °C·cm²/W, ce qui entraîne un dépassement de 22 % de la température de jonction du FPGA par rapport à la norme. Après le passage à des tampons thermiques préformés (tolérance ± 0,02 mm, résistance thermique < 0,03 °C·cm²/W) et la combinaison avec le procédé de frittage sous vide, la température de jonction est réduite de 17 °C et le MTBF (temps moyen entre pannes) est porté à 100 000 heures.
Plan d'optimisation :
Sélection des matériaux : Conformément à la norme ASTM D5470, la résistance thermique des TIM est mesurée, et les matériaux à changement de phase ou les élastomères chargés de métal sont privilégiés.
Contrôle du procédé : Utilisation d'un équipement de distribution automatique (précision ± 3 %) pour garantir une tolérance d'épaisseur < 10 % et éviter les entrefers.
Malentendu 2 : Inadéquation de l'organisation du flux d'air dans le système de refroidissement par air, points chauds locaux hors de contrôle
Problème typique : empiler aveuglément le nombre de ventilateurs, en ignorant l'adaptation d'impédance du canal d'écoulement et l'effet de séparation de la couche limite.
Exemple d'ingénierie : Un cluster de GPU pour centre de données utilise 4 ventilateurs 12038 (volume d'air de 200 pi³/min). Cependant, en raison d'une conception incorrecte de l'angle de guidage d'air (coude à angle droit de 90°), le volume d'air effectif réel n'est que de 65 % de la valeur nominale et l'écart de température local atteint 40 °C. Après optimisation par simulation CFD, le guidage d'air est remplacé par un canal d'écoulement à expansion progressive (angle de diffusion < 7°) et une disposition des ailettes décalées est adoptée (le gradient d'espacement passe de 2 mm à 3,5 mm). La résistance globale au vent est réduite de 30 % et l'écart de température du point chaud est contrôlé à 8 °C. Stratégie principale :
Conception du champ d'écoulement : Des essais en soufflerie sont réalisés conformément à la norme ISO 5801 afin d'optimiser le rapport des surfaces d'entrée et de sortie (recommandé : 1:1,2).
Contrôle dynamique : D'après la courbe Q-H du ventilateur PWM, le point d'impédance du système est adapté à la plage d'efficacité la plus élevée (généralement 60 à 80 % du volume d'air maximal).
Malentendu 3 : L’échec de la conception respectueuse de l’environnement accélère le vieillissement des matériaux
Problème typique : se concentrer uniquement sur les performances initiales de dissipation thermique, en ignorant les effets des contraintes environnementales à long terme telles que l'humidité, la chaleur, la poussière et le brouillard salin.
Analyse de cas : Un convertisseur éolien offshore utilise un dissipateur thermique en alliage d’aluminium 6061 (anodisé en surface). Après six mois de fonctionnement en brouillard salin, la couche d’oxyde s’est détachée, entraînant une augmentation de 50 % de la résistance thermique de contact et une forte augmentation du taux de défaillance des IGBT. Le passage à l’alliage d’aluminium 5052 (résistance au brouillard salin > 1 000 h) et l’application d’une peinture polyuréthane triple résistance (épaisseur 50 μm, conforme à la norme CEI 60068-2-11) ont permis de réduire de 75 % le taux de défaillance sur trois ans. Points de conception :
Technologie de revêtement : Revêtement céramique Al₂O₃ par projection plasma (conductivité thermique : 30 W/m·K, résistance à la température : > 800 °C) utilisé pour les applications à haute température.
Étanchéité : Indice de protection IP69K (joint silicone double passage + soupape de surpression) pour garantir une étanchéité totale aux poussières et vapeurs d'eau.
Malentendu 4 : Absence de modélisation de la charge thermique transitoire et sélection inappropriée des matériaux à changement de phase
Problème typique : la solution de dissipation thermique conçue par simulation en régime permanent ne peut pas gérer des impulsions de puissance de l'ordre de la milliseconde.
Données mesurées : Un amplificateur de puissance à semi-conducteurs est soumis à une charge pulsée de 2 ms à 2 000 W dans une station de base 5G. L’élévation de température transitoire du substrat en aluminium traditionnel atteint 55 °C, tandis que le matériau à changement de phase à microcapsules (composite paraffine/graphène, chaleur latente de changement de phase de 220 J/g) associé à la simulation thermique transitoire (pas transitoire ANSYS Icepak de 1 ms) permet de contrôler l’élévation de température à 18 °C, conformément aux exigences de l’essai d’impact MIL-STD-810G.
Technologie de gestion dynamique :
Emballage à changement de phase : La structure en nid d’abeille est utilisée pour encapsuler le matériau à changement de phase (porosité > 70 %) afin d’éviter les fuites de liquide et d’améliorer l’efficacité de la diffusion de la chaleur.
Calibrage du modèle : Les conditions limites de simulation sont corrigées en fonction de l'imagerie thermique infrarouge (taux d'échantillonnage 100 Hz) et l'erreur est <±1,5 °C
Malentendu 5 : l'évaluation du TCO est unilatérale et ignore les coûts cachés d'exploitation et de maintenance
Problème typique : seul le coût initial du matériel est comparé et les pertes de consommation d'énergie/maintenance/temps d'arrêt ne sont pas quantifiées.
Comparaison des coûts : Une usine de semi-conducteurs utilisait initialement des armoires refroidies par air (coût initial de 500 000 yuans), avec une facture d’électricité annuelle de 1,2 million de yuans (PUE = 1,8). Après la mise à niveau vers un refroidissement liquide par immersion biphasé (coût initial de 1,8 million de yuans), la facture d’électricité annuelle est tombée à 450 000 yuans (PUE = 1,05). Grâce à la réduction de la charge de climatisation des salles blanches, les économies annuelles globales ont atteint 900 000 yuans, et l’investissement supplémentaire peut être amorti en 2,1 ans (TRI > 25 %).
Modèle de décision :
Modélisation affinée : Introduction d’une simulation de Monte-Carlo pour quantifier l’impact du taux de défaillance des équipements (distribution de Weibull) sur le coût total de possession. Superposition de politiques : combinées à des mécanismes de taxe carbone (tels que le CBAM de l'UE), les émissions de carbone des systèmes de refroidissement liquide sur l'ensemble de leur cycle de vie sont réduites de 60 %, et une subvention supplémentaire de 15 % est obtenue.
Conclusion : Faire évoluer le paradigme de conception thermique, passant d’une approche axée sur l’expérience à une approche axée sur les données.
Processus standardisé : Introduire la norme de test thermique JESD51-14 dès la phase de conception afin d’éviter toute reprise ultérieure (le cycle de projet d’un module optique est raccourci de 30 %).
Collaboration multidisciplinaire : Grâce au couplage COMSOL Multiphysics des pertes électromagnétiques (extraction HFSS) et du champ de contrainte thermique, l’efficacité de dissipation thermique d’un composant radar TR est améliorée de 40 %.
Exploitation et maintenance intelligentes : Déployer des capteurs de température à réseau de fibres (précision ± 0,1 °C) et des plateformes de jumeaux numériques pour prédire les pannes (les temps d’arrêt imprévus d’un centre de calcul intensif sont réduits de 90 %).
Grâce à une réflexion technique rigoureuse et à la vérification complète des données, les ingénieurs en conception thermique peuvent éviter avec précision les « tueurs invisibles » et poser les bases de systèmes hautement fiables. En tant que professionnels du secteur, nous nous engageons à fournir des solutions en boucle fermée, des matériaux aux systèmes, et à relever conjointement avec nos clients les défis de la gestion thermique.
Nous mettrons régulièrement à jour les informations et technologies relatives à la conception thermique et à l’allègement. Merci de votre intérêt pour Walmate.
1- Exigences de tolérance particulières pour les pièces clés
Dans la fabrication de plateaux de batterie EV et de boîtiers de batteries de stockage d'énergie à refroidissement liquide, le contrôle de tolérance des surfaces et interfaces de connexion clés affecte directement l'étanchéité, l'efficacité de la dissipation thermique et la précision de l'assemblage.
a. Surface d'installation de la plaque de refroidissement liquide
La plaque de refroidissement liquide est le composant principal du système de gestion thermique de la batterie. La planéité de sa surface d'installation influence directement l'étanchéité du canal de circulation du liquide de refroidissement. Une planéité hors tolérance peut entraîner une compression inégale du joint en silicone, provoquant des fuites locales ou une augmentation de la résistance thermique.
b. Désalignement des cordons de soudure
Le support de batterie utilise souvent une structure soudée en alliage d'aluminium. Un désalignement des cordons de soudure peut entraîner une concentration de contraintes et réduire la durée de vie en fatigue. En particulier pour les applications exigeant une étanchéité à l'air élevée pour les boîtiers de batteries (comme IP67), le désalignement doit être strictement contrôlé.
c. Trou de positionnement du module de batterie
Le trou de positionnement permet de fixer précisément le module de batterie. Une tolérance excessive peut entraîner un désalignement du module, ce qui peut entraîner une défaillance des connexions électriques ou des risques de vibrations mécaniques.
d. Position du trou de fixation
Le trou de fixation sert à fixer le boîtier de la batterie au châssis. Un écart de position peut entraîner des contraintes d'assemblage, voire la rupture des boulons.
e. Rectitude des bords du boîtier de la batterie
La rectitude des bords du boîtier de la batterie influence l'assemblage des couvercles supérieur et inférieur et le niveau de protection IP, en particulier pour les boîtiers soudés au laser, où le bord doit servir de référence pour le suivi de la tête laser.
2- Impact des tolérances dimensionnelles sur l'efficacité de la fabrication
L'impact des tolérances dimensionnelles sur l'efficacité de la fabrication se reflète principalement dans l'équilibre entre le flux de production, la maîtrise des coûts et la qualité du produit. Une conception avec des tolérances raisonnables permet non seulement de garantir la fonctionnalité du produit, mais aussi d'optimiser le rythme de production. L'impact d'un contrôle raisonnable des tolérances dimensionnelles sur l'efficacité de la fabrication se reflète principalement dans les aspects suivants :
a. Équilibre entre précision de fabrication et coût de production
· Bien qu'une tolérance dimensionnelle stricte puisse améliorer la précision de l'étanchéité et de l'assemblage, des équipements de fabrication de haute précision et des procédés complexes sont nécessaires, ce qui augmente considérablement les investissements et les délais de fabrication.
· Une recherche excessive de précision peut entraîner une augmentation des coûts de fabrication. Des tolérances strictes doivent être définies pour les pièces fonctionnelles clés, et les tolérances doivent être assouplies de manière appropriée dans les zones non critiques afin de réduire les coûts.
b. Contrôle du taux de reprise et du taux de rebut
· Une conception avec des tolérances raisonnables peut réduire les reprises dues aux écarts dimensionnels.
· La déformation par soudage est le principal problème dans la fabrication des bacs à batteries. L'utilisation du procédé de soudage à froid CMT permet d'optimiser l'apport de chaleur, de réduire la déformation après soudage et de raccourcir le cycle de reprise. c. Production modulaire et standardisée
· Grâce à des composants standardisés, les exigences de tolérance sont concentrées sur les pièces remplaçables localement, réduisant ainsi la difficulté globale de traitement.
· La conception à tolérances standardisées permet également la compatibilité multi-modèles et réduit le besoin de traitement personnalisé.
3- Normes industrielles et applications pratiques du contrôle de la planéité
Pour les bacs à batteries des véhicules à énergies nouvelles, les normes industrielles imposent des exigences strictes :
a. Norme de planéité : La planéité de la surface d’installation de la plaque de refroidissement liquide doit être ≤ 0,2 mm, celle de la plaque de support inférieure ≤ 0,5 mm/m² et l’erreur de planéité du cadre après soudage doit être ≤ 0,8 mm6.
b. Optimisation du processus de fabrication : L’usinage de précision CNC, le soudage à froid CMT et le traitement de vieillissement par vibration (VSR), combinés à la détection en ligne par interféromètre laser, réduisent le risque de déformation.
c. Sélection des matériaux : Il est recommandé d’utiliser des alliages d’aluminium à haute résistance tels que le 6061, avec une limite d’élasticité ≥ 1 180 MPa, en tenant compte à la fois de la légèreté et de la stabilité structurelle.
4- Stratégie d'ajustement des tolérances basée sur les matériaux et les procédés
a. L'innovation des matériaux favorise l'allègement
L'utilisation d'alliages d'aluminium légers à haute résistance (tels que le 6061) et de matériaux composites (matrice d'aluminium renforcée au carbure de silicium), associés à l'anodisation et à un revêtement isolant, permet d'obtenir une réduction de poids de 30 % et d'améliorer la résistance à la corrosion, tout en s'adaptant aux exigences de dissipation thermique des systèmes de refroidissement liquide.
b. La collaboration entre les procédés améliore la précision de fabrication
Le moulage par extrusion monobloc et le soudage par friction-malaxage (FSW) réduisent le nombre de soudures, tandis que le soudage à froid CMT et le soudage laser contrôlent la déformation thermique.
c. La détection par simulation en boucle fermée garantit la fiabilité
La simulation IAO optimise la disposition des nervures de renfort, tandis que le balayage laser et la technologie de détection des fuites d'hélium assurent une surveillance complète du processus. La conception modulaire est compatible avec une tolérance de ± 5 mm, réduisant ainsi les coûts et augmentant l'efficacité.
Nous mettrons régulièrement à jour les informations et technologies relatives à la conception thermique et à l’allègement. Merci de votre intérêt pour Walmate.
1- Caractéristiques du procédé de soudage des alliages d'aluminium des bacs à batteries et des boîtiers de stockage d'énergie
Dans la fabrication de nouveaux boîtiers à refroidissement liquide, de bacs à batteries et d'autres produits, les canaux de refroidissement liquide et les structures multi-cavités sont des caractéristiques de conception complexes typiques (voir la figure 1). Ces structures présentent souvent les caractéristiques suivantes :
Figure 1 : Conception typique d'un bac à batterie
Entrelacement spatial tridimensionnel : les canaux d'écoulement sont répartis en serpentin, avec un grand nombre de points de retournement spatiaux ;
Connexion multi-niveaux : la cavité principale et la sous-cavité sont reliées par des cloisons à parois minces (épaisseur 2-3 mm) ;
Caractéristiques de miniaturisation : petite section du canal d'écoulement (l'épaisseur minimale de la paroi du canal d'écoulement du profilé en aluminium est de 1,2 mm) et faible accessibilité au soudage.
2- Analyse des difficultés liées à la combinaison de plusieurs technologies de soudage dans la fabrication de bacs à batteries
Dans la fabrication de bacs à batteries, il est nécessaire de combiner plusieurs technologies de soudage, telles que l'application coordonnée du soudage par friction-malaxage (FSW), du soudage par transition métal froid (CMT), du soudage par fusion traditionnel (TIG/MIG) et d'autres technologies. Cette combinaison vise à prendre en compte la légèreté, la résistance, l'étanchéité et l'efficacité de la production, mais elle se heurte également aux principales difficultés suivantes :
a. Le problème de l'apport thermique coordonné de plusieurs procédés
Les différentes technologies de soudage (telles que le FSW et le soudage laser) présentent d'importantes différences d'apport thermique, ce qui peut facilement entraîner des variations de performances des matériaux et des déformations thermiques. Il faut donc optimiser la séquence de soudage et le réglage des paramètres.
b. Compatibilité des équipements et goulot d'étranglement en termes d'efficacité
La commutation des équipements est complexe et les exigences de précision en matière de synchronisation des paramètres sont élevées. La conception modulaire des postes de travail et des machines de soudage intelligentes sont nécessaires pour améliorer l'efficacité collaborative et réduire les temps de cycle.
c. Défis liés à l'équilibre entre résistance de l'étanchéité et coût
Le risque de fuite à l'intersection de plusieurs soudures est élevé (représentant 70 % des défauts), et une conception d'étanchéité redondante et d'optimisation de la topologie est nécessaire.
3- Pratique d'ingénierie : Coordination de plusieurs processus de soudage pour un bac à batteries et un boîtier de stockage d'énergie à refroidissement liquide
a. Planification de la position des traces de soudure
· Optimisation de la position de soudure : Lors de la conception du produit, la rationalité de la position de soudure doit être pleinement prise en compte afin d'éviter l'apparition de traces de soudure sur des pièces ou zones clés affectant les fonctions du produit. Par exemple, ajuster l'espace entre le cadre avant et la buse d'eau pour éviter toute interférence avec les traces de soudure ; optimiser la position de soudure de la buse d'eau pour réduire l'impact sur les performances du produit.
· Adaptation à la structure du produit : La position de soudure doit être adaptée à la structure du produit afin de garantir que la soudure puisse supporter diverses charges et contraintes lors de son utilisation. Par exemple, dans le projet de plaque de refroidissement liquide, la stabilité structurelle et la fiabilité du produit sont améliorées par une planification rationnelle de la position de soudure.
· Facilité d'utilisation et de détection : La position de soudure doit être pratique pour les opérateurs lors des opérations de soudure et des contrôles qualité ultérieurs. Par exemple, éviter de souder dans des endroits difficiles d'accès ou avec une mauvaise visibilité afin d'améliorer l'efficacité et la qualité du soudage.
b. Contrôle des traces de soudure
· Taille des traces de soudure : La taille des traces de soudure doit être rigoureusement contrôlée. En général, la hauteur des traces de soudure doit être comprise entre 4 et 6 mm et ne pas dépasser le plan afin de garantir l'aspect et la précision de l'assemblage du produit. Par exemple, pour le projet de plaque de refroidissement liquide, la taille des traces de soudure a été contrôlée avec succès en ajustant les paramètres et le procédé de soudage, évitant ainsi tout impact sur les performances et la qualité du produit.
· Forme des traces de soudure : La forme des traces de soudure doit être aussi régulière que possible afin d'éviter une fusion excessive ou incomplète. L'optimisation des paramètres de soudage et des techniques opératoires permet d'améliorer efficacement la forme des traces de soudure et la qualité de la soudure.
· Traitement de meulage : Pour les traces de soudure concaves produites au point de soudage par friction, un traitement de meulage est utilisé afin d'obtenir une surface lisse répondant aux exigences d'aspect et de performance du produit.
c. Optimisation de la séquence de soudage
· Soudage par partition : Pour les produits de grande taille, le soudage par partition permet de contrôler efficacement la déformation globale. En divisant le produit en plusieurs zones et en les soudant séquentiellement, la concentration de chaleur pendant le soudage est réduite et le risque de déformation thermique est diminué.
· Correction progressive : Pendant le soudage, la méthode de correction progressive permet d'ajuster la déformation de soudage au fil du temps. La mesure et la correction continues de la déformation du produit pendant le soudage garantissent la précision dimensionnelle et la forme du produit final, conformément aux exigences de conception.
· Optimisation du chemin de soudage : Planifiez rationnellement le chemin de soudage afin d'éviter les soudures répétées dans la même zone et de réduire l'apport de chaleur. Par exemple, dans le projet de plaque de refroidissement liquide, l'apport de chaleur pendant le soudage a été réduit et la qualité du soudage a été améliorée grâce à l'optimisation du chemin de soudage.
d. Contrôle collaboratif de la déformation
La plaque de refroidissement liquide subit une déformation thermique pendant le soudage, ce qui entraîne une diminution de la précision dimensionnelle du produit. Mesures d'optimisation :
· Utiliser le soudage par partition et des méthodes de correction progressive pour contrôler la déformation globale.
· Optimiser les paramètres de soudage, réduire le courant et la tension, et diminuer l'apport de chaleur.
· Utiliser des fixations pour fixer le produit afin de réduire les mouvements et les déformations pendant le soudage.
· Utiliser une méthode de soudage symétrique pour répartir uniformément la chaleur de soudage.
Nous mettrons régulièrement à jour les informations et technologies relatives à la conception thermique et à l’allègement. Merci de votre intérêt pour Walmate.
La technologie CTC (Cell-to-Chassis) a suscité un vif intérêt car elle permet d'améliorer considérablement l'autonomie et l'efficacité énergétique des véhicules électriques. Cependant, sa capacité à remplacer véritablement la technologie des batteries traditionnelles reste controversée. Le principal obstacle à la fabrication – le procédé de soudage des bacs de batterie – est devenu déterminant pour l'avenir de cette technologie : la complexité de la conception structurelle, la compatibilité multi-matériaux et les exigences strictes en matière de gestion thermique ont mis à rude épreuve la technologie de soudage traditionnelle. En partant du point de vue d'ingénieurs de terrain, en combinant les tendances du secteur et les pratiques d'ingénierie, cet article analyse le potentiel et les limites de la technologie CTC et explore comment le soudage est devenu la pierre angulaire de cette révolution technologique.
1- L'idéal et la réalité de la technologie CTC
La technologie CTC permet théoriquement de réduire les pièces structurelles redondantes et d'améliorer la densité énergétique en intégrant la cellule de batterie directement au châssis. Cependant, la faisabilité de son application à grande échelle se heurte à des défis concrets :
Radicalisme et prudence des constructeurs automobiles : Tesla, BYD et d'autres leaders ont lancé des solutions CTC, mais de nombreux constructeurs attendent encore. Les données du secteur montrent qu'en février 2025, les modèles CTC produits en série représentaient 15 à 20 % du marché mondial, et la technologie CTP (Cell-to-Pack) traditionnelle reste la technologie dominante.
Le coût de l'amélioration de la durée de vie des batteries : Bien que la technologie CTC puisse augmenter la densité énergétique de 15 à 20 %, la complexité de la structure du châssis entraîne une augmentation des coûts de fabrication de 30 à 50 % (calculée par un cabinet de conseil), et le rapport coût-bénéfice n'est pas encore clairement établi.
Controverse économique sur la maintenance : La conception intégrée a fait exploser les coûts de maintenance des batteries. Les données des compagnies d'assurance montrent que le taux de remplacement des batteries après accident des modèles CTC atteint 70 %, soit bien plus que les 25 % des modèles traditionnels.
Ces contradictions rendent l'avenir de la technologie CTC complexe. La capacité du marché à dépasser les 20 % dépend de trois facteurs principaux : l'avancement de la production en série du Tesla Cybertruck ; la guerre des prix entre les constructeurs automobiles chinois qui obligerait CTC à réduire ses coûts ; et le degré de compromission de la réglementation européenne sur la réparabilité des batteries. Le niveau de technologie de soudage en production sera déterminant pour déterminer la capacité à franchir le pas entre le laboratoire et la production en série.
2 - Trois obstacles majeurs au procédé de soudage
Pour les fabricants de bacs à batteries, la mise en œuvre de la technologie CTC doit surmonter trois problèmes majeurs :
a. Le compromis entre précision micrométrique et efficacité
Les procédés de soudage traditionnels tolèrent des erreurs de 0,5 mm, mais les bacs CTC doivent accueillir davantage de batteries, ce qui multiplie par plus de trois le nombre de soudures, la plupart étant réparties sur des pièces courbes et irrégulières. Des tests réalisés par un fabricant montrent qu'une erreur de positionnement de soudure supérieure à 0,15 mm entraîne une chute brutale du taux de rendement de l'assemblage des cellules de batterie, passant de 99 % à 82 %. Plus complexe encore, l'amélioration de la précision s'accompagne souvent d'une baisse d'efficacité : malgré la précision élevée du soudage laser, le coût de l'équipement est plus de cinq fois supérieur à celui du soudage traditionnel.
b. Le mélange de matériaux
Afin d'équilibrer légèreté et résistance, les bacs CTC utilisent souvent une structure mixte « alliage d'aluminium + fibre de carbone + acier spécial ». La différence de coefficient de dilatation thermique entre différents matériaux peut atteindre 20 fois (par exemple, 23 μm/m·K pour l'aluminium et 0,8 μm/m·K pour la fibre de carbone), ce qui peut facilement générer des contraintes internes lors du soudage et provoquer des fissures. Lorsqu'une entreprise a tenté d'assembler de l'aluminium et de la fibre de carbone, le taux de fissuration de la soudure a atteint 18 %, dépassant largement le seuil acceptable de 3 % dans l'industrie.
c. « Tueur invisible » de la zone affectée thermiquement
Une température de soudage élevée peut endommager les matériaux isolants ou les circuits des capteurs autour de la cellule de batterie. Un constructeur automobile a déjà augmenté le taux d'autodécharge du module de batterie de 50 % en raison d'un mauvais contrôle de l'apport de chaleur de soudage. Les ingénieurs doivent contrôler les fluctuations de température de soudage à ± 15 °C en 0,1 seconde, ce qui équivaut à installer un « frein thermique de haute précision » sur le pistolet de soudage.
3- Solution : Il n’existe pas de solution miracle, seule l’innovation systémique est possible.
Face à ces défis, l’industrie explore trois voies innovantes :
a. « Cocktail thérapeutique » de la combinaison de procédés
Soudage hybride laser-arc : Combinant la précision du soudage laser aux avantages de la pénétration du soudage à l’arc, la vitesse de soudage des alliages d’aluminium est augmentée de 40 % ;
Technologie de transition métal froid (CMT) : Grâce à un contrôle précis de l’apport de chaleur, la zone affectée thermiquement est réduite de 60 % ;
Système de compensation intelligent robotisé : Ajuste automatiquement la trajectoire du pistolet de soudage en fonction des données de balayage de soudure en temps réel et augmente le taux de qualification du soudage de surfaces courbes complexes de 75 % à 95 %.
b. « Pré-compromis » côté matériaux
Certaines entreprises ont commencé à développer conjointement des matériaux composites « soudables » avec des fournisseurs. Par exemple, la sensibilité aux fissures de soudage d’un alliage d’aluminium modifié national (alliage d’aluminium ajusté par des moyens physiques, chimiques ou de procédé) a été réduite du niveau 7 au niveau 3 (selon les normes ISO). Bien qu'elle sacrifie 5 % de l'effet de légèreté, elle augmente le rendement de soudage à 98 %.
c. « Jumeau numérique » dans la dimension détection
En collectant toutes les données du procédé de soudage (courant, température, vitesse, etc.), combinées à des modèles d'IA pour prédire la probabilité de défauts, une usine a adopté cette technologie, ce qui a permis de passer de 80 % à 97 % du taux de détection en ligne des défauts de soudage et de réduire les coûts de rebut de 45 %.
4- Nouvelle proposition des ingénieurs : Trouver la certitude dans l’incertitude
a. La controverse autour de la technologie CTC repose essentiellement sur un jeu entre « optimisation système » et « limites locales » :
Si la vitesse de percée du procédé de soudage est inférieure aux attentes des constructeurs automobiles en matière de réduction des coûts, la technologie CTC pourrait devenir une technologie de niche ;
Si les matériaux, les procédés et les technologies de test réalisent des avancées de manière coordonnée, cela devrait ouvrir la voie à une nouvelle ère de conception structurelle des véhicules électriques.
b. Pour les ingénieurs, il est nécessaire de reconstruire les capacités à partir de deux dimensions :
Intégration des connaissances inter-domaines : comprendre le seuil de sensibilité des propriétés électrochimiques à l’apport de chaleur de soudage ;
Capacité de réponse agile : Une étude de cas menée auprès d’un fournisseur européen montre qu’une équipe capable d’optimiser les paramètres de soudage de nouveaux alliages en une semaine voit ses chances d’obtenir des commandes tripler.
La technologie CTC se situe à la croisée des chemins entre « innovation disruptive » et « piège de la production de masse ». Cela ne remplacera peut-être pas complètement la technologie existante, mais cela oblige le procédé de soudage à évoluer vers une plus grande précision, une meilleure compatibilité et un contrôle plus intelligent. Dans ce marathon technologique, le véritable gagnant ne sera peut-être pas le premier constructeur automobile, mais l'équipe d'ingénieurs qui transforme les « soudures impossibles » en « interfaces standardisées » côté fabrication.
Nous mettrons régulièrement à jour les informations et technologies relatives à la conception thermique et à l’allègement. Merci de votre intérêt pour Walmate.
La technologie CTP (Cell to Pack) bouleversant la structure traditionnelle des batteries, le rôle du support de batterie est passé d'une simple fonction de support passif à une fonction d'intégration active. La technologie de soudage est devenue essentielle à la sécurité et à la performance. Les exigences de légèreté (épaisseur de paroi de seulement 1,5 mm), d'étanchéité zéro pore et d'intégration multi-matériaux (aluminium, cuivre, fibre de carbone) ont plongé le soudage traditionnel dans le dilemme des déformations et des défauts. L'industrie réalise des avancées majeures grâce à l'innovation des matériaux, au contrôle qualité intelligent et à l'itération des procédés. Cet article analyse les défis disruptifs posés par la technologie CTP au soudage et explore la voie technique vers une haute précision et une fiabilité optimales.
1- Analyse des changements dans les exigences de conception structurelle des bacs de batterie grâce à la technologie CTP
La technologie CTP (Cell to Pack) intègre directement les cellules de batterie au bloc-batterie en supprimant la structure modulaire des blocs-batteries traditionnels. Cette innovation technologique impose des exigences d'amélioration globales et multidimensionnelles pour la conception structurelle du bac de batterie. Voici une analyse spécifique des matériaux, des performances, du procédé, de l'intégration, etc. :
(1) Amélioration globale de la résistance structurelle et de la résistance aux chocs
a. Exigences en matière de support mécanique après suppression du module :
Après suppression de la structure modulaire par la technologie CTP, le bac de batterie doit assurer directement les fonctions de support, de fixation et d'amortissement des forces externes de la cellule de batterie. Le module traditionnel disperse la charge mécanique, tandis que le bac CTP doit absorber la déformation de la cellule de batterie lors de la charge et de la décharge (par exemple, la force de dilatation d'une cellule de batterie carrée peut atteindre 10 à 20 kN), tout en résistant aux vibrations, à l'extrusion et aux chocs pendant la conduite du véhicule.
b. Orientation vers l'optimisation des matériaux et des structures
· Dominance de l'alliage d'aluminium à haute résistance : L'acier a été progressivement remplacé en raison de son poids élevé, et le 6061-T6 s'est imposé. Il présente une résistance spécifique élevée et une forte résistance à la corrosion, ce qui permet de répondre à la double exigence de légèreté et de rigidité élevée.
· Conception de structures composites : Par exemple, la structure « double cadre à poutre annulaire » du Leapmotor améliore la résistance aux chocs locaux grâce à des compartiments de poutre longitudinaux et transversaux, tout en utilisant la technologie d'extrusion pour optimiser la répartition des matériaux et réduire le poids superflu.
· Exploration de l'alliage magnésium-aluminium et de la fibre de carbone : L'alliage magnésium-aluminium est 30 % plus léger que les matériaux en aluminium traditionnels, et les matériaux composites en fibre de carbone présentent à la fois des caractéristiques de résistance et de légèreté élevées, mais ne sont actuellement utilisés que dans les modèles haut de gamme en raison de leur coût et de la maturité de leur procédé.
(2) Exigences relatives à l'étanchéité à l'air et à la gestion thermique intégrées
a. Amélioration des performances d'étanchéité
Une fois le module retiré, la circulation interne du liquide de refroidissement et l'étanchéité au gaz du bloc-batterie dépendent entièrement du plateau, et les défauts de soudure (tels que les pores et les fissures) peuvent entraîner des risques de fuite.
Figure 1 - Test d'étanchéité du bac à piles
b. Intégration des fonctions de gestion thermique
Les plateaux CTP doivent intégrer des composants tels que des plaques de refroidissement liquide et des adhésifs thermoconducteurs. Par exemple, des adhésifs structuraux sont utilisés pour fixer les cellules de batterie et transférer les contraintes de dilatation, tandis que des adhésifs thermoconducteurs polyuréthane (conductivité thermique > 1,5 W/m·K) assurent la conduction thermique entre les cellules de batterie et avec les tubes de refroidissement liquide. La quantité d'adhésif utilisée dans un seul PACK est supérieure de plus de 50 % à celle des structures traditionnelles. Des canaux d'écoulement doivent être conçus à l'intérieur du plateau pour optimiser l'efficacité du refroidissement tout en évitant les dommages à l'étanchéité causés par la zone affectée thermiquement par le soudage.
(3) Allègement et innovation des matériaux
a. Tendances en matière de choix des matériaux
Procédés d'extrusion et de moulage sous pression d'alliages d'aluminium : des profilés en aluminium extrudé sont utilisés pour les structures de cadre (comme le plateau de batterie 4680 de Tesla), et les procédés de moulage sous pression (comme le moulage sous pression intégré) simplifient le soudage et réduisent le poids de 15 à 20 %.
Application des matériaux composites plastiques : Par exemple, les matériaux PA6 renforcés de fibres de verre sont utilisés dans les pièces non porteuses afin de réduire davantage le poids, mais le problème de compatibilité avec l’interface de connexion métallique doit être résolu.
b. Stratégie de conception légère
Optimisation de la topologie : Réduire les matériaux redondants grâce à la simulation IAO et alléger le plateau tout en garantissant sa résistance.
Parois fines et intégrées : L’épaisseur de la paroi du plateau est réduite de 3 mm à 1,5-2 mm, et des composants fonctionnels tels que les supports BMS et les canaux de faisceau de câbles sont intégrés pour réduire le nombre de pièces.
(4) Intégration et conception modulaire
a. Forte intégration des composants fonctionnels
Les plateaux CTP doivent intégrer des modules tels que le système de gestion de batterie (BMS), les connecteurs haute tension et les couches d’isolation ignifuges.
b. Conception modulaire et compatible
La ligne de production de soudage doit prendre en charge la production mixte de plusieurs modèles de plateaux, permettre un changement de type en un clic et être compatible avec des structures de plateaux de différentes tailles de cellules de batterie (par exemple, carrées et cylindriques).
2 - Défis spécifiques de l'innovation technologique CTP pour le procédé de soudage
La technologie CTP (Cell to Pack) a considérablement amélioré l'utilisation de l'espace et la densité énergétique, mais elle a également posé des défis sans précédent au procédé de soudage.
(1) La difficulté de contrôler les défauts de soudage a fortement augmenté.
a. Problèmes de porosité et d'étanchéité
Une fois le module éliminé par la technologie CTP, le support de batterie doit directement assurer l'étanchéité. Les pores de soudage (un défaut fréquent dans le soudage des alliages d'aluminium) entraînent directement un risque de fuite de liquide de refroidissement ou de pénétration de gaz.
b. Fissures et compatibilité des matériaux
Les alliages d'aluminium à haute teneur en zinc (tels que la série 7) sont sujets aux fissures dues aux contraintes thermiques lors du soudage.
c. Erreur d'assemblage et d'espacement
L'intégration directe de plusieurs cellules entraîne une augmentation du nombre de points de jonction de la structure du support. L'accumulation d'erreurs d'assemblage peut entraîner un espacement de soudure supérieur à ± 1 mm.
(2) Problèmes d'adaptation du procédé liés à la mise à niveau du système de matériaux
a. Défis du soudage des matériaux légers
Le matériau des plateaux CTP est passé de l'acier à l'alliage d'aluminium (6061-T6, 7075-T6), à l'alliage magnésium-aluminium (réduction de poids de 30 %) et aux composites en fibre de carbone. Le soudage des alliages d'aluminium doit résoudre le problème de pénétration insuffisante dû à la fusion difficile du film d'oxyde et à une conductivité thermique élevée.
b. Technologie d'assemblage de matériaux différents
Lorsque le plateau intègre des composants fonctionnels tels qu'une plaque de refroidissement liquide (cuivre/aluminium) et une couche ignifuge (matériau composite à matrice céramique), des composés intermétalliques fragiles sont susceptibles d'apparaître à l'interface de matériaux différents.
(3) Complexité structurelle accrue et exigences de précision accrues
a. Contrôle de la déformation des structures minces de grande taille
L'épaisseur de paroi du plateau CTP est réduite de 3 mm à 1,5-2 mm, et la sensibilité à la déformation thermique du soudage augmente considérablement.
b. Joints de soudure haute densité et efficacité du processus
Le nombre de joints de soudure sur un seul plateau est passé de 2 000 dans les modules traditionnels à plus de 5 000.
Figure 2 - Soudage du bac à batterie
3- Modernisation des processus de production et du contrôle qualité
La technologie CTP favorise la transformation du soudage des bacs de batteries, passant d'un « processus unique » à une « collaboration multi-technologies, intelligence et éco-responsabilité ». Les fabricants doivent se concentrer sur trois axes majeurs :
Mise à niveau technologique : amélioration du contrôle des défauts tels que les pores et les fissures, et adaptation aux matériaux légers ;
Transition intelligente : numérisation complète des processus et contrôle qualité par IA pour une production de haute précision ;
Collaboration écologique : élaboration conjointe de normes techniques avec les fournisseurs de matériaux, les équipementiers et les équipementiers.
Nous mettrons régulièrement à jour les informations et technologies relatives à la conception thermique et à l’allègement. Merci de votre intérêt pour Walmate.
Les matériaux légers comme les alliages d'aluminium sont devenus courants grâce à leurs performances supérieures. Cependant, des défis tels que le contrôle de l'apport de chaleur, la suppression des déformations et la stabilité du procédé de soudage des plaques minces constituent des obstacles majeurs pour les technologies de soudage traditionnelles. Le soudage par transfert de métal à froid (CMT), avec ses avantages : faible apport de chaleur, transfert sans projections et contrôle intelligent des paramètres, offre une solution innovante pour la fabrication de bacs de batteries.
Cet article examine les stratégies de contrôle de précision de la technologie CMT pour le soudage des plaques minces destinées aux bacs de batteries, en analysant son adaptabilité, les défis du procédé et les scénarios d'application des composites, afin de fournir des orientations théoriques et pratiques pour une production efficace et de haute qualité.
Figure 1 : Soudage CMT du boîtier inférieur de refroidissement liquide de la batterie de stockage d'énergie 104S
1- Exigences relatives au soudage des bacs de batterie et adaptabilité du CMT
La technologie CMT, avec son faible apport de chaleur, son transfert sans projections et son contrôle intelligent des paramètres, répond parfaitement aux exigences de haute précision, de faible déformation et d'efficacité du soudage des bacs de batterie.
(1)Exigences fondamentales du procédé de soudage des bacs de batterie
a. Compatibilité des matériaux et exigences d'allègement
Les bacs de batterie utilisent principalement des alliages d'aluminium légers (par exemple, série 6xxx, 6061) ou des composites en fibre de carbone pour les modèles haut de gamme, exigeant une résistance élevée (résistance à la traction du matériau de base de 60 à 70 %) et une faible densité (alliage d'aluminium : 2,7 g/cm³).
Assemblage de matériaux différents : Pour les structures hybrides acier-aluminium, les différences de coefficient de dilatation thermique doivent être prises en compte afin de minimiser la déformation.
b. Qualité et performances des soudures
Faible apport de chaleur et contrôle de la déformation : Pour les plaques minces (0,3 à 3 mm), la déformation doit être ≤ 2 mm. Les soudures linéaires longues nécessitent un soudage segmenté ou une conception anti-déformation.
Étanchéité et résistance : Les soudures doivent être parfaitement étanches pour éviter les fuites d’électrolyte et réussir les tests de cisaillement (par exemple, normes T/CWAN 0027-2022).
Contrôle de la porosité : Le soudage des alliages d’aluminium est sujet à la porosité, nécessitant un taux de porosité ≤ 0,5 %.
c. Exigences en matière d’efficacité de production et d’automatisation
La production par lots exige une vitesse de soudage ≥ 7 mm/s, réduisant le temps de soudage d’un seul plateau à 5 à 10 minutes.
Les postes de travail automatisés doivent prendre en charge la conception à deux postes (assemblage et soudage simultanés) et la collaboration multi-robots.
(2) Principaux avantages du CMT pour le soudage des bacs à batteries
a. Contrôle précis de l'apport de chaleur
Le CMT réduit l'apport de chaleur de 33 % par rapport au soudage MIG traditionnel en rétractant le fil de soudage pour couper le courant lors du court-circuit des gouttelettes, éliminant ainsi les risques de brûlure pour les plaques ultra-fines (0,3 mm).
L'alternance des cycles froid-chaud (chauffage de l'arc, transfert des gouttelettes, rétraction du fil) minimise l'accumulation de chaleur et contrôle la déformation à ≤ 1,5 mm (études de cas BYD et BAIC).
b. Stabilité du procédé et amélioration de la qualité
Soudage sans projections : La rétraction mécanique élimine les projections de gouttelettes, réduisant ainsi les reprises.
Optimisation de la porosité : L'utilisation d'un gaz de protection Ar+30 % He réduit la porosité de 50 % par rapport à l'Ar pur, avec des pores ≤ 0,3 mm.
Tolérance élevée aux jeux : Prise en charge des jeux d'assemblage jusqu'à 1,5 mm, réduisant ainsi les exigences de précision des fixations.
c. Intégration de l'automatisation et gains d'efficacité
Les postes de travail à deux postes (par exemple, ceux conçus par Taixiang Tech) permettent le soudage et l'assemblage en parallèle, doublant ainsi l'efficacité.
Le soudage robotisé symétrique (synchronisation à deux robots) avec conception anti-déformation réduit le temps de cycle à ≤ 10 minutes.
2-Défis du processus CMT pour les bacs à batteries
Figure 2 : Déroulement du processus de soudage CMT
(1) Propriétés des matériaux et contrôle des défauts de soudure
a. Sensibilité à la porosité dans le soudage des alliages d'aluminium
Les plateaux en alliage d'aluminium (par exemple, 6061, 6063) sont sujets à la porosité en raison de leur solidification rapide et des variations de solubilité de l'hydrogène. La composition du gaz de protection est essentielle : l'argon pur entraîne une porosité d'environ 5 %, tandis que l'argon + 30 % d'hélium réduit la porosité à ≤ 0,5 %. Le réglage de l'inductance (par exemple, réglage négatif) optimise l'écoulement du bain de fusion et minimise la taille des pores.
b. Fissuration à chaud et ségrégation de composition
La ségrégation de Mg, Si, etc., dans les alliages d'aluminium peut entraîner une fragilisation des joints de grains. Bien que le faible apport de chaleur du CMT réduise la zone de fusion, un contrôle précis de la vitesse de soudage et du dévidage du fil est nécessaire pour éviter une pénétration insuffisante ou une surchauffe localisée.
c. Compatibilité métallurgique dans le soudage de matériaux différents
Les interfaces des joints Al-acier ou Al-composite (par exemple, poutres et enceintes de protection) doivent atténuer les phases fragiles (par exemple, FeAl₃) et les interférences de vapeur de Zn.
(2) Défis liés à l'optimisation des paramètres du procédé
a. Équilibrage de la pénétration et de l'apport thermique
Les soudures doivent respecter la norme T/CWAN 0027 relative à la profondeur de pénétration (≥ 0,8 mm). Le faible apport thermique du CMT peut entraîner une pénétration insuffisante, nécessitant un ajustement de la longueur de l'arc ou un courant pulsé pour améliorer la pénétration.
b. Compromis entre vitesse et stabilité
Les lignes automatisées exigent des vitesses ≥ 1,2 m/min, mais les vitesses élevées risquent d'entraîner une instabilité de l'arc ou un transfert irrégulier des gouttes.
c. Pontage des jeux dans les soudures complexes
Les plateaux présentent souvent des jeux importants (0,5 à 1,5 mm) ou des joints irréguliers (par exemple, des joints en T).
(3) Compatibilité entre la conception structurelle et le procédé de fabrication
a. Contrôle de la déformation par soudage de plaques minces
L'épaisseur de paroi des palettes en alliage d'aluminium est généralement de 2 à 3 mm. La déformation du soudage MAG traditionnel peut atteindre 1,2 mm, tandis que le soudage CMT permet de la réduire à moins de 0,3 mm grâce à un faible apport de chaleur. Cependant, la conception d'outillages anti-déformation et le soudage symétrique robotisé (poste de travail double) sont nécessaires pour améliorer encore la précision.
b. Continuité et étanchéité des soudures longues
La longueur de la soudure scellée du bac de batterie peut atteindre plusieurs mètres, et il est impératif d'éviter les ruptures d'arc ou les fluctuations du bain de fusion. La technologie CMT assure l'uniformité de la soudure grâce à plus de 70 cycles de rallumage d'arc par seconde, et le taux de qualification de l'étanchéité à l'air peut atteindre 99 % grâce au système de suivi laser.
c. Synergie des applications composites multi-procédés
Les palettes haut de gamme utilisent souvent le procédé composite CMT+FSW (soudage par friction-malaxage). Le CMT est utilisé pour les structures complexes (comme l'assemblage entre le cadre et la plaque inférieure). Le FSW est utilisé dans les zones à forte charge (comme les poutres longitudinales) pour améliorer la résistance. Le problème de compatibilité des paramètres d'assemblage des deux procédés (comme la température de préchauffage et le traitement thermique après soudage) doit être résolu.
3-Scénarios d'application typiques du procédé CMT dans la fabrication de bacs à batteries
(1) Assemblage de la structure principale du bac à batteries
a. Soudage du cadre et de la plaque inférieure
Le procédé CMT est largement utilisé pour l'assemblage du cadre et de la plaque inférieure des bacs à batteries en alliage d'aluminium, notamment pour les soudures longues et les plaques fines (2-3 mm d'épaisseur).
b. Assemblage de la poutre et de la plaque inférieure
Dans la conception des bacs à batteries CTP, en raison du nombre réduit de poutres et de la structure complexe, le procédé CMT est utilisé pour : le soudage de positionnement de haute précision : la connexion locale entre la poutre et la plaque inférieure (comme un joint en T) doit éviter une pénétration insuffisante. Le procédé CMT permet une pénétration stable ≥ 0,8 mm grâce au contrôle numérique de la longueur d'arc (comme la technologie Fonis CMT Advanced). Adaptation multi-matériaux : si la poutre est en alliage aluminium-magnésium (comme le 6061) et la plaque inférieure en aluminium haute résistance, le procédé CMT permet de réduire les pores grâce à la protection par gaz mixte Ar+He, tout en s'adaptant aux différences de conductivité thermique des différents matériaux.
(2) Soudage de plaques minces et de structures géométriques complexes
a. Soudage d'alliages d'aluminium à parois minces (2-3 mm)
La légèreté des bacs de batterie favorise l'utilisation de plaques minces, mais le soudage MIG traditionnel est sujet à la déformation. Les avantages du procédé CMT sont les suivants :
b. Soudage de plaques ultra-minces : Taixiang Automation utilise la technologie CMT pour réaliser un soudage sans projections de plaques ultra-minces de 0,3 mm pour les structures d'étanchéité des bords des bacs de batterie.
c. Pontage de soudures de formes spéciales : Pour les structures de formes spéciales telles que les nervures de renfort internes et les poutres anti-collision du bac, le mode de pontage CMT permet de combler un espace de 0,5 à 1,5 mm par rétraction du fil et redirection de l'arc afin d'éviter les défauts de fusion.
d. Soudures exigeant une étanchéité élevée : L'étanchéité du bac de batterie est directement liée à la sécurité de la batterie. Le procédé CMT garantit cela de la manière suivante :
· Soudures longues et continues : plus de 70 cycles de réamorçage d'arc par seconde (comme la technologie Fronius LaserHybrid) garantissent la continuité de plusieurs mètres de soudures, avec un taux de réussite de 99 %.
· Contrôle de l'apport de chaleur faible : par rapport au soudage laser, le CMT présente un apport de chaleur plus faible, ce qui réduit l'impact thermique des fluctuations du bain de fusion sur la couche de scellant et convient au procédé de revêtement de colle.
(3) Scénario de fabrication composite multi-processus
a. Procédé composite CMT+FSW
Sur les lignes de production de bacs de batteries haut de gamme, le CMT est souvent associé au soudage par friction-malaxage (FSW) :
Division du travail et coopération : le CMT est utilisé pour le soudage flexible de structures complexes (telles que les cadres et les joints de formes spéciales), tandis que le FSW est utilisé pour les zones à forte charge (telles que les poutres longitudinales) afin d'améliorer la résistance. Par exemple, la ligne de production automatisée de Shanghai Weisheng utilise une combinaison CMT+FSW+CNC pour augmenter l'efficacité de la production de bacs de 30 %.
Optimisation des connexions de processus : la ligne de production de Huashu Jinming adopte une conception modulaire et permet une connexion transparente avec le FSW grâce à l'adaptation des paramètres de préchauffage (par exemple, un chauffage local à 150 °C après le soudage CMT).
b. Combiné à la technologie de rivetage FDS/SPR
Dans la technologie CTP de deuxième génération, le CMT est coordonné avec les technologies de rivetage auto-serrant par friction (FDS) et auto-perçant (SPR) : Solution de connexion hybride : Par exemple, la zone porteuse du cadre et la plaque inférieure adoptent le soudage FSW, tandis que les pièces détachables (telles que les plaques de refroidissement par eau et les couches isolantes) sont prépositionnées par soudage CMT, puis fixées par rivetage FDS, en tenant compte à la fois de la résistance et de la facilité d'entretien.
Nous mettrons régulièrement à jour les informations et technologies relatives à la conception thermique et à l’allègement. Merci de votre intérêt pour Walmate.
En tant qu’ingénieur de terrain dans une usine de fabrication de plateaux de batterie, ayant participé à plusieurs projets de boîtiers pour véhicules électriques, je constate les arbitrages complexes entre "allègement, sécurité et coût". Cet article analyse les logiques de sélection technologique actuelle et les défis d’industrialisation, à travers trois dimensions : matériaux, procédés de fabrication et tendances futures, illustrées par des cas concrets.
1- Choix des matériaux : Arbitrage entre allègement et coût
Le choix des matériaux du boîtier impacte directement les performances et l’économie du véhicule. Les options dominantes sont l’aluminium, les aciers haute résistance et les composites, chacun adapté à des scénarios spécifiques.
a. Aluminium : Pilier de l’allègement
· Profilés en aluminium extrudé : Utilisés par BYD pour plusieurs modèles, ces profilés optimisent la forme des sections pour réduire le poids et augmenter la rigidité.
· Coulée intégrée (Gigacasting) : La batterie 4680 de Tesla, combinée à la technologie CTC, réduit le poids de plus de 50%. Cependant, les coûts de moules dépassent 200 millions de yuans, nécessitant une production annuelle de 500 000 pièces pour rentabiliser, adaptée aux constructeurs leaders.
· Composites à base d’aluminium : La Porsche Taycan utilise une structure hybride aluminium-fibre de carbone, réduisant le poids de 15%, mais augmentant les coûts de 30%, réservée aux véhicules haut de gamme.
b. Aciers haute résistance : L’option économique
Les aciers à durcissement structural (ex. 22MnB5) offrent une limite d’élasticité de 1 500 MPa. Avec un taux de pénétration de 40% dans les véhicules utilitaires et un coût par GWh inférieur de 40% à l’aluminium, ils dominent les modèles d’entrée de gamme (moins de 100 000 yuans), malgré une densité énergétique réduite de 8%.
c. Composites : L’expérimentation haut de gamme
· Matériaux SMC : Les coques supérieures en composites renforcés de fibre de verre allègent de 30% par rapport à l’acier, mais nécessitent une épaisseur accrue (3 mm + nervures de 5 mm) pour compenser la résistance aux chocs.
· Fibre de carbone : Le boîtier de la BMW i3 est 50% plus léger que l’aluminium, mais coûte 800 yuans/kg, limitant son usage aux modèles luxueux.
Synthèse pratique : Le choix des matériaux doit correspondre au positionnement du véhicule. Le marché moyen (200 000-300 000 yuans) privilégie l’aluminium, l’entrée de gamme l’acier, et le luxe explore les composites.
2- Procédés de fabrication : Équilibre entre efficacité et fiabilité
Les technologies de fabrication influencent la productivité et la fiabilité. Les principales méthodes incluent la coulée sous pression, l’extrusion-soudage et l’intégration structurelle.
a. Coulée vs extrusion-soudage
· Profilés en aluminium extrudé (ex. General Motors Bolt) : Coût unitaire ~800 yuans, adapté à la production de masse, mais processus complexe.
· Coulée d’aluminium (ex. NIO ET5) : Coût unitaire 1 500 yuans, mais productivité multipliée par 5, idéal pour les montées en cadence rapides.
· Soudage par friction-malaxage (FSW) : Réduit la déformation de 50% et améliore la résistance à la fatigue de 30%, malgré un investissement en équipement accru de 40%, adapté aux utilitaires exigeants en durée de vie.
b. Technologies d’intégration structurelle
· CTP (Cell-to-Pack) : La technologie de CATL (batterie Qilin) porte le taux d’utilisation de l’espace de 72% à 85%, réduisant les coûts de 15-20%, mais exige une meilleure protection contre les emballements thermiques.
· CTC (Cell-to-Chassis) : Le Model Y de Tesla supprime 370 pièces et augmente l’autonomie de 54%, mais les coûts de réparation bondissent de 300%, posant des défis pour le service après-vente.
Comparaison des données clés
Expérience de la ligne de production : la technologie CTP reste actuellement la technologie dominante en raison de sa grande compatibilité, tandis que la technologie CTC nécessite une collaboration approfondie entre les constructeurs automobiles et les fabricants de batteries et il est peu probable qu'elle soit popularisée à court terme.
3- Tendances futures : Fusion technologique et amélioration intelligente
a. Hybridation des matériaux
Les structures aluminium-fibre de carbone (ex. concept Porsche Taycan) allègent de 15% avec une résistance en compression de 800 MPa. Cependant, la résistance d’interface doit dépasser 25 MPa (taux de conformité de 65% pour la Toyota bZ4X), nécessitant des progrès en stabilité de production.
b. Innovation fonctionnelle
· Intégration du refroidissement liquide (ex. batterie de magasin GAC) : La surface de contact augmente de 50%, avec un écart de température <5°C, mais exige une optimisation des soudures aluminium-cuivre (soudage laser oscillant) pour réduire la porosité.
· Capteur à fibre optique intégré (solution Continental Group) : surveillance en temps réel de la déformation et de la température de la coque, vitesse de réponse du BMS augmentée de 30 %, mais le problème de durabilité du capteur doit être résolu.
c. Recyclage vert
La technologie de recyclage en boucle fermée de BMW réduit les émissions de CO2 de 60%, mais la perte de performance des matériaux recyclés doit être limitée à 10%. De plus, les grandes pièces en coulée mince (ex. presse 9 000T de LK) exigent un contrôle précis de la température des moules (±5°C), l’élimination des bavures étant un goulot d’étranglement.
Axes de progrès:
Réduction des cycles de moulage des composites (ex. LGF-PP : de 180 à 90 secondes)
Application des jumeaux numériques pour réduire l’erreur de simulation de crash de ±20% à ±5%, améliorant la fiabilité de conception
4- Segmentation du marché et perspectives
Court terme (1-3 ans) : Le CTP avec profilés en aluminium reste dominant, CATL conservant 34% de parts de marché.
Moyen terme (5-10 ans) : Adoption accrue du CTC et de la fibre de carbone dans le haut de gamme, avec une part prévue de 25% pour la fibre de carbone d’ici 2030.
Long terme : Densité énergétique ciblant 400 Wh/kg, et amélioration de la sécurité au-delà des normes actuelles (30 minutes de protection contre l’emballement thermique).
5- Conclusion
Le choix des technologies de boîtiers de batterie relève d’une « adaptation contextuelle », intégrant positionnement du constructeur, seuils de coûts et maturité de la chaîne d’approvisionnement. En tant qu’ingénieurs, nous devons embrasser l’innovation tout en respectant les contraintes de production, cherchant un équilibre dynamique entre allègement, sécurité et coût. À l’avenir, avec l’essor des technologies intelligentes et de fabrication verte, les boîtiers évolueront d’une « protection passive » vers une « sécurité active », soutenant la généralisation des véhicules électriques.
Nous mettrons régulièrement à jour les informations et technologies relatives à la conception thermique et à l’allègement. Merci de votre intérêt pour Walmate.
Dans le processus de production, d'assemblage et d'utilisation réel, la défaillance de la tension de tenue d'isolation des plateau de batterie se produit souvent, comme un récif caché dans le développement rapide de la nouvelle industrie énergétique, menaçant la sécurité de conduite des véhicules et le fonctionnement fiable du système de stockage d'énergie. Cet article tente d'analyser les modes de défaillance typiques en se basant sur les pratiques de fabrication, afin de fournir des références superficielles aux praticiens concernés et d'aider les collègues de l'industrie à explorer conjointement des moyens efficaces pour améliorer les performances de tenue d'isolation des plateau de batterie.
Partie 3 - Analyse des défaillances courantes
Figure 1 Essai de tenue à la tension de l'isolant
1- Analyse des mécanismes de défaillance courants
Les scénarios d'application des plateau de batterie pour le stockage d'énergie et les véhicules à énergie nouvelle sont différents, ce qui entraîne à la fois des points communs et des différences dans les exigences de tension de tenue d'isolation et les conditions de défaillance, comme suit :
a. Différences
Charge dynamique : les véhicules à énergie nouvelle doivent faire face à des vibrations mécaniques à haute fréquence de 20 à 2 000 Hz, tandis que les systèmes de stockage d'énergie sont principalement confrontés à une déformation statique à long terme, avec une durée de déformation cumulée supérieure à 10 ans.
Niveau de tension : la tension de tenue d'isolation des plateau de batterie des véhicules à énergie nouvelle doit atteindre 3 000 VDC et plus (sur la base de la norme GB 38031), tandis que les systèmes de stockage d'énergie nécessitent une tension de tenue d'isolation de 4 200 VAC et plus (sur la base de la norme IEC 61439).
Facteur d'accélération de défaillance : les véhicules à énergie nouvelle génèrent une contrainte thermique due à plus de 2 000 cycles de charge et de décharge par an, ce qui accélère la défaillance de l'isolation ; Les systèmes de stockage d'énergie fonctionnent 24 heures sur 24, 7 jours sur 7, avec une durée de fonctionnement annuelle moyenne de plus de 8 000 heures, ce qui entraîne un vieillissement électrochimique qui accélère à son tour la défaillance de l'isolation.
b. Points communs
Les deux doivent permettre une alerte précoce en cas de défaillance de l'isolation grâce à la surveillance de la résistance de l'isolation (pas moins de 100 MΩ à froid et pas moins de 1 MΩ/kV à chaud) et au contrôle des décharges partielles (moins de 5 pC).
2- Défauts de fabrication courants qui provoquent une défaillance de la tension de tenue d'isolation des plateau de batterie
(1) Étape de construction de la tension de tenue d'isolation
a. Défaillance potentielle et analyse des causes
· Défauts de matériaux :
Cause : Le niveau de tension de tenue du matériau isolant est insuffisant, vieillissement dû à l'humidité ou à une contamination de surface (taches d'huile, débris métalliques).
Performances : Faible résistance d'isolation (< 100 MΩ), courant de fuite supérieur à la norme ou panne directe pendant le test de tension de tenue.
Problèmes de processus :
Cause : Débris métalliques résiduels (processus de soudage/coupe grossier), épaisseur inégale du revêtement isolant ou non durci.
Performances : Décharge partielle, endommagement de la couche isolante provoquant un court-circuit.
Interférence environnementale :
Cause : Une température et une humidité élevées provoquent l'absorption d'humidité du matériau et la corrosion chimique.
Performances : Les performances d'isolation se détériorent avec l'environnement et l'eau condensée provoque un fluage.
Erreurs de test :
Cause : Mauvais réglage de la tension/du temps de test (par exemple non conforme à la norme GB/T 38661), mauvaise mise à la terre.
Performances : Mauvaise évaluation des dommages qualifiés ou dus à une surtension sur les composants.
b. Stratégie de réponse
· Optimisation des matériaux : sélectionner des matériaux résistants à l'humidité (tels que des matériaux composites en fibre de carbone) avec une tension de tenue ≥ 1000 V CC et appliquer un revêtement antisalissure.
· Contrôle du processus : utiliser des équipements de soudage/pulvérisation automatisés et mettre en place un atelier propre.
· Gestion de l'environnement : installer un dispositif de surveillance de la température et de l'humidité et pré-sécher les matériaux avant la construction.
· Spécifications des tests : tests segmentés (pré-test 500 V + test formel 1000 V), étalonner les instruments et enregistrer les données.
(2) Étape d'installation du module
a. Analyse des défaillances potentielles et des causes
· Erreur d'assemblage :
Cause : La doublure isolante est manquante et les boulons sont trop serrés et la couche isolante est endommagée.
Performance : Faible résistance d'isolement entre le module et la coque, et tenue à la rupture de tension.
· Dommages mécaniques
Cause : Rayures sur les outils de manipulation, débris métalliques perçant le film isolant.
Performance : Court-circuit local ou panne soudaine pendant le fonctionnement.
· Compatibilité de conception
Cause : Espace électrique insuffisant en raison de l'écart de taille entre le module et le plateau.
Performance : La capacité parasite provoque une rupture de superposition de tension.
· Risques de connexion électrique :
Cause : Usure et défaillance du joint du connecteur en raison d'un faisceau de câbles non fixé.
Performance : Usure et fuite de la couche isolante du faisceau de câbles haute tension.
b. Contre-mesures
· Conception anti-erreur : Utilisez un outillage de goupille de positionnement pour éviter toute installation manquante et personnalisez la longueur du boulon pour éviter un serrage excessif.
· Opération de nettoyage : nettoyage par aspiration avant l'installation et envelopper les outils avec du silicone anti-rayures.
· Simulation de tolérance : vérifier le degré de correspondance entre le module et le plateau par CAE pour s'assurer que l'écart est ≥ 10 mm.
· Inspection du processus : après l'installation, effectuer une inspection aléatoire avec un mégohmmètre (≥ 100 MΩ) et effectuer un test de tension de tenue segmentée pour localiser le point de défaut.
(3) Phase d'intégration du système
a. Analyse des causes et des défaillances potentielles
· Défaillance de l'interface inter-systèmes :
Cause : les paramètres d'isolation des composants ne correspondent pas (comme les différences de tension nominale de tenue du connecteur).
Performances : panne de connexion de jeu de barres haute tension ou interférence BMS.
· Superposition de capacité parasite :
Cause : la capacité parasite totale augmente après la connexion de plusieurs modules en parallèle, et l'effet d'augmentation de la capacité est significatif.
Performances : le courant de fuite de test au niveau du système dépasse la norme.
· Défaillance due aux contraintes environnementales :
Cause : les vibrations provoquent une fatigue de l'isolation et le liquide de refroidissement s'infiltre dans l'interface haute tension.
Performances : la résistance de l'isolation diminue périodiquement pendant le fonctionnement.
· Angle mort du test :
Cause : échec de simulation des conditions de travail réelles (température élevée/vibrations/humidité).
Performances : réussi en laboratoire mais échec en fonctionnement réel.
b. Contre-mesures
· Conception de compatibilité : unifier les normes des composants des fournisseurs.
· Contrôle de la capacité parasite : ajoutez une couche d'isolation en polyimide et optimisez la disposition grâce à la simulation SPICE.
· Test de simulation des conditions de fonctionnement : effectuez un test composite « cycle de -40 ℃ à 85 ℃ + vibration de 5 Hz à 200 Hz + tension de tenue ».
· Surveillance intelligente : module de surveillance d'isolation en ligne intégré, l'IA prédit les risques potentiels.
3-Test de tenue à la tension d'isolement
Le test de tenue à la tension d'isolement est à la fois une mesure de sécurité et une cause possible de défaillance. Le test de tenue à la tension d'isolement lui-même peut provoquer une défaillance en raison d'un fonctionnement incorrect, de problèmes d'équipement ou de défauts de conception, et même causer des dommages secondaires à l'appareil testé.
(1)Types courants de défaillances pendant le test
(2) Les stratégies de réponse sont les suivantes :
a. Contrôle précis des paramètres de test
· Tension et durée : définies selon les normes ; activer l'algorithme de compensation dynamique pour les charges capacitives (telles que les modules de batterie) afin de supprimer l'effet d'augmentation de la capacité.
· Seuil de courant de fuite : défini selon les spécifications de l'équipement (par exemple ≤ 10 mA) et faire la distinction entre les modes CC/CA (les tests CC nécessitent un seuil inférieur).
b. Spécifications de l'équipement et du fonctionnement
· Étalonnage de l'instrument : le testeur de tension de tenue est étalonné tous les 6 mois et la couche d'isolation de la ligne haute tension est inspectée visuellement quotidiennement.
· Fonctionnement sûr : déconnexion forcée des circuits basse tension avant le test ; utiliser des bras robotisés ou des dispositifs automatiques pour éviter tout contact manuel avec les zones haute tension.
c. Prévention et réparation des pannes
· Tests segmentés : tester des systèmes complexes en modules (par exemple, tester d'abord le bus haute tension, puis tester l'isolation du module) pour localiser le point de panne.
· Réparation des pannes : utiliser de la résine époxy pour combler la zone endommagée après la panne, et après réparation, il est nécessaire de repasser le test de gradient de tension complet (par exemple, pression par paliers de 500 V→1 000 V).
d. Gestion de l'environnement et des données
· Contrôle environnemental : démarrer le déshumidificateur lorsque l'humidité dans la zone de test est supérieure à 75 %, ou retarder le test jusqu'à ce que l'environnement soit conforme à la norme.
· Traçabilité des données : enregistrer la tension de test, la courbe de courant de fuite et les paramètres environnementaux, et utiliser le système MES pour associer le numéro de lot de production.
Nous mettrons régulièrement à jour les informations et technologies relatives à la conception thermique et à l’allègement. Merci de votre intérêt pour Walmate.
Le plateau de batterie utilise des matériaux isolants principalement pour empêcher les fuites de courant, protéger la sécurité du personnel et assurer le fonctionnement normal du système de batterie. Lors de la sélection, il est nécessaire de prendre en compte les propriétés isolantes du matériau, sa résistance à la chaleur, sa stabilité chimique et sa résistance mécanique. Ces facteurs déterminent ensemble l'effet d'application du matériau isolant dans le plateau de batterie, affectant ainsi la sécurité et la fiabilité de l'ensemble du système de batterie.
Partie 2 - Garantie de performance de résistance à la pression
Figure 1 Plateau de batterie pour véhicule électrique
1-Sélection des matériaux isolants et conception de solutions
Lors de la sélection des matériaux isolants pour les Plateau de batterie, l'accent est mis sur les propriétés diélectriques, la tolérance environnementale et les propriétés mécaniques des matériaux. Voici 6 matériaux isolants couramment utilisés dans les plateau de batterie et leurs informations associées :
Lors de la conception d'une solution, nous devons généralement prendre en compte de manière exhaustive les trois facteurs clés du scénario d'application, les exigences de performance et le budget de coût pour sélectionner le matériau isolant approprié. Par exemple :
(1) Sélectionnez en fonction du scénario d'application : dans un système de batterie de stockage d'énergie à haute tension et à courant élevé, si le côté du plateau de batterie nécessite un matériau isolant haute performance, il est recommandé d'utiliser la solution de fixation de film PI ; si les exigences de performance d'isolation ne sont pas élevées, la solution de pulvérisation de poudre isolante peut être sélectionnée. Pour la plaque inférieure du plateau de batterie, si une solution d'isolation à faible coût est recherchée, la solution de pulvérisation de poudre isolante ou de revêtement de peinture isolante est plus adaptée.
(2) Sélectionnez en fonction des exigences de performance : lorsque les exigences de performance d'isolation, de résistance aux hautes températures, de résistance à la corrosion chimique, etc. sont élevées, la solution de fixation de film PI est un meilleur choix ; si ces exigences de performance sont relativement faibles, la solution de pulvérisation de poudre isolante ou de revêtement de peinture isolante peut répondre aux besoins.
(3) Sélectionnez en fonction du budget de coût : lorsque le budget de coût est limité, la solution de pulvérisation de poudre isolante ou de revêtement de peinture isolante est plus économique ; lorsque le budget est suffisant, la solution de fixation du film PI peut être sélectionnée.
2-Exigences techniques pour le film PI pour les plateau de batterie
(1) Matériau : PI, épaisseur du film de base 0,1-0,14 mm, épaisseur de l'adhésif arrière 0,03 mm, conductivité thermique du film PI > 0,3 W/(m·k) ;
(2) Résistance à la pression : AC 3000 V, 60 S, courant de fuite ≤ 0,5 mA ;
(3) (pâte froide) résistance au pelage à 180° ≥ 15 N/24 mm ;
(4) Isolation : DC 1500 V, 60 S, résistance d'isolation > 1000 MΩ ;
(5) Performances d'isolation de résistance à la chaleur et à l'électrolyte : à 500 ℃, tension DC 700 V, ajouter 2 ml d'électrolyte (zone de test 13 000 mm<H>2<H>), conserver pendant 1 h, pas de panne et pas d'étincelles ; (6) Performances thermiques et d'isolation : à 500±2℃, poursuivre la cuisson (four à moufle) pendant 0,5 h, la morphologie globale de l'échantillon change sans combustion spontanée et l'échantillon passe deux fois. Un courant alternatif de 1000 V est appliqué à la surface et la tension est augmentée de 0 V à 3000 pendant 10 S, puis continue pendant 60 S. L'échantillon testé ne présente aucune panne ni aucune étincelle ;
(7) Qualité ignifuge : UL94 V-0 ;
(8) Haute température et humidité élevée : après 1000 heures de test à 85℃ et 85 % d'humidité, l'échantillon ne présente aucune fissure ni déformation, répondant à la norme nationale « GBT 13542.6-2006 Film d'isolation électrique Partie 6 : Film polyimide pour isolation électrique » sur la résistance d'isolation, la valeur de tension de tenue et les exigences de résistance électrique. La résistance à la traction, l'allongement à la rupture et la résistance au pelage sont réduits de moins de 30 % par rapport au matériau non vieilli ;
(9) Choc à chaud et à froid : 85 °C pendant une heure, commuté à -40 °C pendant une heure, puis commuté à 85 °C pour les cycles à haute et basse température. Le temps de commutation est compris dans une heure et le temps de commutation est ≤ 3 min. Après 1 000 heures de cycles à haute et basse température, l'échantillon ne présente aucune fissure ni déformation, répondant à la norme nationale « GBT 13542.6-2006 Film d'isolation électrique Partie 6 : Film polyimide pour isolation électrique » pour la résistance d'isolation, la valeur de tension de tenue et les exigences de résistance électrique. La résistance à la traction, l'allongement à la rupture et la résistance au pelage sont réduits de moins de 30 % par rapport au matériau non vieilli.
(10) Test au brouillard salin : test au brouillard salin neutre (NSS) selon la norme GB/T 10125, température 35℃, humidité ≥85%RH, solution d'essai (5±0,1%) (fraction massique) NaCl, PH=6,5~7,2, pulvérisation continue pendant 72h. Après le test au brouillard salin, l'échantillon ne présente aucune fissure ni déformation, répondant à la norme nationale « GBT 13542.6-2006 Film d'isolation électrique Partie 6 : Film polyimide pour isolation électrique » pour la résistance d'isolation, la valeur de tension de tenue et les exigences de résistance électrique. La résistance à la traction, l'allongement à la rupture et la résistance au pelage sont réduits de moins de 30 % par rapport au matériau non vieilli.
(11) Le produit est conforme à la directive RoHS.
Figure 2 Film PI pour plateau de batterie
3-Méthodes de test de tension de tenue d'isolement et solutions aux problèmes courants
(1) Méthode de test de tension de tenue d'isolation
Le test de tension de tenue d'isolation est un moyen important d'évaluer les performances d'isolation des équipements électriques, notamment le test de tension de tenue CC et le test de tension de tenue CA. Le test de tension de tenue CC détecte si le matériau isolant se décompose dans un délai spécifié en appliquant une haute tension CC. L'équipement comprend un générateur de haute tension CC, un voltmètre, etc. Les étapes consistent à appliquer la tension, à maintenir la tension et à réduire la tension. Le test de tension de tenue CA applique une haute tension CA. L'équipement et les étapes sont similaires au test CC. Les deux méthodes nécessitent une préparation avant le test pour garantir que l'équipement est bien mis à la terre et que l'état de surface du matériau isolant est étroitement observé pendant le test.
(2) Problèmes courants et solutions
Les problèmes courants dans le test de tension de tenue d'isolation comprennent la rupture d'isolation, le courant de fuite excessif et la défaillance de l'équipement de test. La rupture d'isolation peut être causée par des performances insuffisantes du matériau isolant, des défauts internes ou de l'humidité. Les solutions comprennent la sélection de matériaux de haute qualité, le renforcement de la maintenance et l'amélioration de la structure de l'isolation. Un courant de fuite excessif peut être causé par une résistance d'isolation réduite, une contamination de surface ou une précision insuffisante de l'équipement de test. Les solutions comprennent le maintien du matériau isolant propre et sec et l'étalonnage de l'équipement de test. La défaillance d'un équipement de test peut être causée par son vieillissement, un entretien ou un fonctionnement inadéquat. Les solutions incluent un entretien régulier, un fonctionnement correct et une réparation rapide.
Nous mettrons régulièrement à jour les informations et technologies relatives à la conception thermique et à l’allègement. Merci de votre intérêt pour Walmate.
Avec le développement rapide des véhicules à énergie nouvelle et des technologies de stockage d'énergie, le système de batterie, en tant que vecteur d'énergie central, a attiré une grande attention en termes de sécurité et de fiabilité. Le plateau bac de batterie, en tant que structure de support et de protection des modules de batterie, ses performances d'isolation électrique sont directement liées au fonctionnement en sécurité du véhicule complet, à la durée de vie de la batterie et à la sécurité personnelle des utilisateurs. La conception de la sécurité électrique du plateau bac de batterie est la pierre angulaire de la sécurité du système de batterie. Par des protections multi niveaux, telles que l'isolation, la structure, la chaleur, la surveillance, etc., elle garantit le fonctionnement stable de la batterie dans des conditions de travail complexes, réduit le risque d'incendie, d'explosion ou de choc électrique causé par des pannes électriques, et prolonge en même temps la durée de vie de la batterie et améliore la fiabilité du système.
Cet article, centré sur la sécurité d'isolation électrique du plateau bac de batterie, expose systématiquement ses principes de conception, les méthodes de vérification des performances de résistance à la pression, ainsi que l'analyse de la cause fondamentale et les stratégies d'amélioration des cas typiques de défaillance, en vue de fournir un soutien théorique et une référence pratique pour la conception de haute sécurité du système de batterie.
Part 1: Design Essentials
Le cœur de la conception de la sécurité électrique du système de batterie réside dans la trinité « prévention contrôle urgence » : prévenir les pannes par des mesures telles que l'isolation, la connexion fiable, la gestion de la chaleur, etc. ; réaliser le contrôle en temps réel avec l'aide de capteurs et de BMS ; répondre aux situations extrêmes en utilisant des conceptions telles que la prévention du feu, la décompression, etc. Chaque point doit agir en synergie pour garantir la sécurité et la fiabilité du système de batterie tout au long de son cycle de vie, tout en tenant compte de la maintenabilité et de la conformité. Le plateau bac de batterie dans le système de batterie non seulement supporte la structure, mais assume également de multiples fonctions telles que l'isolation électrique, la gestion de la chaleur, l'anti glissement, la protection mécanique, la mise à la terre et la conception modulaire, ce qui est crucial pour garantir la sécurité électrique du système de batterie.
1-Le support structurel assure la fiabilité de la connexion électrique
Le bac à batterie assure la fiabilité et la sécurité des connexions électriques dans des conditions de travail complexes en fixant les modules de batterie, en réduisant les contraintes mécaniques, en résistant aux vibrations et aux chocs, en maintenant l'alignement et en intégrant la protection de l'environnement et la gestion thermique.
Figure 1 Plateau de batterie
A. Support physique et fixation, assure le positionnement exact des points de connexion électrique (tels que les barres omnibus, les faisceaux de câbles, les connecteurs), évite le mauvais contact causé par la déformation ou le déplacement structurel ; fournit un cadre rigide, fixe les modules de batterie et les pièces de connexion, empêche la desserrage ou la rupture causée par les vibrations ou les chocs.
B.Isolement et protection environnementaux, empêche l'intrusion d'eau vapeur, de poussière, de brouillard salin, etc. par un design d'étanchéité (tels que IP67/IP68), évite le court circuit causé par la corrosion ou l'échec d'isolation ; bloque les chocs mécaniques externes ou les impacts d'objets étrangers, protège les pièces de connexion haute tension.
C. Synergie de la gestion de la chaleur, intègre une structure de dissipation de chaleur (tels que la plaque de refroidissement liquide, le coussin thermoconducteur) pour équilibrer la température, empêche l'oxydation ou le soudage par fusion des points de connexion causés par la surchauffe locale ; réduit les interférences thermiques entre les modules adjacents par un design d'isolation thermique, évite la différence d'expansion des matériaux causée par le gradient de température.
D. Support de la compatibilité électromagnétique (EMC), supprime les interférences électromagnétiques par une couche de blindage métallique ou un revêtement conducteur, protège les lignes de signal basse tension (tels que la ligne de communication BMS) contre les interférences du circuit haute tension.
2-La protection d'isolement crée un environnement d'isolement efficace
La conception d'isolation électrique de la batterie a pour but de construire un environnement capable non seulement d'isoler efficacement l'électricité haute tension, mais aussi de garantir le fonctionnement efficace du système, de sorte que le module de batterie puisse être emballé en toute sécurité dans toutes les conditions de travail, prévenant la libération accidentelle de l'énergie électrique et évitant ainsi les risques électriques potentiels.
A.La structure du plateau bac de batterie tient compte à la fois du support et de la protection par isolation :
l Préférer les matériaux d'aluminium alliage, tels que l'aluminium alliage extrudé, pour réaliser la légèreté tout en maintenant une haute rigidité et une résistance aux chocs. La structure extérieure supporte le poids du système de batterie entier et les chocs externes, utilise des profilés à section fermée pour renforcer la force structurelle, et la structure intérieure est conçue pour supporter les modules de batterie et la plaque de refroidissement à eau, assurant leur stabilité et leurs besoins de dissipation de chaleur.
l Utiliser des matériaux isolants en tant que garnitures ou revêtements pour assurer une bonne isolation électrique entre le module de batterie et le plateau bac, les faisceaux de câbles haute tension doivent avoir un trajet de gestion spécial et une gaine isolante, garantissant la distance d'espacement électrique et la distance de creepage par rapport au plateau bac.
l Utiliser des techniques de soudage avancées telles que le soudage par friction-malaxage, améliorer la force de connexion, en même temps réduire la zone d'influence thermique, éviter la déformation et les fissures potentielles. Pour les parties difficiles à souder, utiliser la connexion par boulons ou le rivetage, combiné avec la colle d'étanchéité, assurer la fiabilité de la connexion mécanique et l'isolation électrique.
l Prendre en compte la modularité lors de la conception, faciliter le remplacement et la maintenance des batteries, sans affecter la stabilité de la structure globale.
Figure 2 Schéma de principe de la distance d'isolement et de fuite dans l'air
B.Points clés de la conception d'isolation haute basse tension :
l Les points de potentiel positif et négatif du système de batterie doivent être isolés du système d'alimentation basse tension et du plateau bac de batterie, assurer une distance d'espacement électrique et une distance de creepage suffisantes entre le circuit haute tension et le circuit de contrôle basse tension, conformément aux normes de sécurité, empêcher la fuite haute tension vers le système basse tension.
l La conception d'isolation haute basse tension doit prendre en compte la compatibilité électromagnétique (EMC), assurer que les mesures d'isolation n'introduisent pas d'interférences, maintenir le fonctionnement stable du système.
l Connexion à haute impédance, les systèmes haute basse sont connectés par une connexion à haute impédance, seulement autorisés à être connectés à la mise à la terre du véhicule (plateau bac de batterie) pour limiter le flux de courant, assurer que la panne du système haute tension ne se propage pas au système basse tension.
l Mesures d'isolation physique, lors de la conception du plateau bac de batterie, on peut disposer les composants haute basse tension dans différentes chambres fermées, réduire l'influence mutuelle par une séparation physique ; utiliser des matériaux isolants en tant que garnitures entre le module de batterie et le plateau bac, tels que des plastiques polymères ou du caoutchouc, pour assurer l'isolation physique et électrique.
l Prendre en compte la maintenabilité des mesures d'isolation lors de la conception, assurer qu'on peut réaliser la réparation ou le remplacement en toute sécurité lorsqu'il y a besoin.
C.Points clés de la conception de protection par contact :
l Gestion des faisceaux de câbles haute tension : les faisceaux de câbles haute tension doivent être bien enveloppés dans une gaine isolante et gérés de manière ordonnée par des pinces de fixation ou des rainures de conducteur, éviter d'être exposés, réduire le risque de contact direct.
l Cloison de sécurité : installer des cloisons isolantes entre les modules de batterie et entre le module de batterie et la paroi du plateau bac, pour prévenir le risque d'électrochoc indirect causé par la fuite d'électrolyte en cas de dommage de la batterie.
l Encapsulation des composants haute tension : effectuer une encapsulation des composants clés tels que les connecteurs haute tension, les relais, etc., assurer que même à l'intérieur du plateau bac, ces composants ne peuvent pas être touchés directement par accident.
l Design fermé : le plateau bac de batterie est conçu en tant que structure fermée, utilise une coque métallique ou composite, assure que les composants haute tension à l'intérieur ne seront pas exposés, et la coque elle même doit également avoir de bonnes performances d'isolation.
l Mécanisme de verrouillage : pour les points de connexion haute tension pouvant être maintenus, utiliser un mécanisme de verrouillage, assurer qu'ils ne s'ouvrent pas facilement lors d'un opération non professionnelle, réduire le risque de toucher par erreur.
l Application des matériaux isolants : utiliser des matériaux isolants en tant que couche d'isolation entre le plateau bac de batterie et le module de batterie, assurer que même en cas de dommage du plateau bac, on peut empêcher le contact direct du corps humain avec la partie sous tension. Ces matériaux comprennent, mais ne sont pas limités à, les plastiques polymères, les rondelles de caoutchouc ou les revêtements.
3-Conception des identifications électriques
Les identifications électriques du plateau bac de batterie peuvent non seulement améliorer la sécurité des opérations, mais aussi simplifier le processus de maintenance, réduire le risque d'opérations erronées.
A.Identification claire
l Marquer clairement des avertissements tels que « Danger haute tension », « Ne pas toucher » sur le plateau bac de batterie et les composants haute tension environnants, assurer qu'ils peuvent être rapidement identifiés même en cas d'urgence.
l Utiliser le codage de couleur internationalement reconnu, par exemple, utiliser le rouge ou l'orange pour identifier la zone haute tension, le bleu pour représenter le courant continu, pour distinguer intuitivement les différentes caractéristiques électriques.
l Appliquer des symboles de sécurité électrique standardisés, tels que les symboles graphiques dans l'IEC 60417, pour représenter la haute tension, la mise à la terre, les points de coupure d'alimentation, etc., assurer la compréhensibilité mondiale des informations.
l Inclure le numéro de série, la date de production et l'information de lot du plateau bac de batterie, faciliter le suivi et la gestion du rappel.
l Sélectionner des matériaux et des techniques d'impression résistants à l'usure et à la corrosion, assurer que les identifications restent claires et lisibles tout au long du cycle de vie du plateau bac de batterie.
B.Avertissements d'identification
l Identifier clairement le danger haute tension sur le plateau bac de batterie et dans la région environnante, rappeler aux techniciens de maintenance d'attacher attention à la sécurité électrique et de respecter les procédures d'opération.
l Indiquer la distance de sécurité d'opération, en particulier près des connecteurs haute tension et des conducteurs nus, rappeler de maintenir une distance appropriée.
C.Guide d'opération
l Marquer clairement la position de mise à la terre du système de batterie et du plateau bac, assurer la mise en œuvre correcte des mesures de mise à la terre.
l Identifier les points de test en sécurité et les points d'accès de maintenance, ces points doivent être conçus en tant que points d'opération sous basse tension ou non sous tension.
l On peut également énumérer brièvement les opérations de base et les guides de sécurité dans la région non critique du plateau bac, guider le processus d'opération correct.
Nous mettrons régulièrement à jour les informations et technologies relatives à la conception thermique et à l’allègement. Merci de votre intérêt pour Walmate.
Les blocs d'eau les plus populaires sont essentiellement de type microcanal en cuivre pur. La plaque inférieure en cuivre est directement traitée avec un racloir et les ailettes sont intégrées à la plaque inférieure pour réduire la résistance thermique. La plaque inférieure et la plaque de recouvrement sont brasées ou diffusées pour assurer la fiabilité de l'étanchéité.
Partie 3 : La principale structure de coût du bloc d'eau traité par le processus de découpage
1- Avantages de l'utilisation du procédé de skiving pour la fabrication de blocs d'eau
l Conception intégrée : le processus de découpe peut intégrer le fond et les ailettes, ce qui permet de réduire la résistance thermique de contact et d'améliorer la conductivité thermique. De plus, la conception intégrée de la plaque inférieure et des ailettes peut également améliorer la résistance structurelle.
l Traitement de haute précision : le processus de découpe peut produire une structure de dent très fine, et la hauteur, l'épaisseur et le pas des dents peuvent être contrôlés avec précision, ce qui rend les ailettes du dissipateur thermique plus denses, la zone de dissipation thermique plus grande et la dissipation thermique plus efficace. En même temps, il peut également mieux répondre aux besoins personnalisés des différents clients en termes de forme, de taille, etc.
l L'efficacité de la production est élevée et le processus de découpe peut être produit en série. Par rapport à la CNC traditionnelle, le processus de découpe peut traiter plusieurs pièces d'engrenage en même temps, ce qui améliore considérablement l'efficacité de la production.
Figure 1 : Base de bloc d'eau avec différentes technologies de traitement a-Skiving b-CNC c-Forgeage à froid
2- Structure des coûts du bloc d'eau de skiving
l Coûts de conception et de développement : La complexité de conception du bloc d'eau de découpage est relativement élevée, en particulier lorsque des exigences élevées en matière de performances de dissipation thermique sont requises, ce qui nécessite une conception et une optimisation complexes du processus.
l Coût des matériaux : Les matériaux utilisés dans le processus de découpage sont principalement de l'aluminium et un alliage de cuivre. La conception combinant une plaque d'aluminium et un alliage de cuivre est plus courante dans la fabrication de radiateurs et présente un rapport coût-performance plus élevé, de sorte que la qualité de l'aluminium et du cuivre affecte directement le coût.
l Coût de traitement :
Coût du processus de découpage : Le processus de découpage implique des équipements d'usinage CNC de haute précision, tels que des machines-outils CNC à trois axes. L'utilisation de tels équipements nécessite un coût d'investissement élevé et les exigences techniques pour les opérateurs sont également élevées, ce qui augmentera les coûts de production.
Coût du processus de soudage : Dans le processus de fabrication des blocs d'eau, le processus de soudage est également un facteur de coût important. Le brasage sous vide et le soudage par diffusion sont deux méthodes de soudage couramment utilisées. Le brasage peut souder plusieurs joints en même temps, a une efficacité de production élevée, nécessite des matériaux de brasage, a des exigences élevées pour les conditions de processus et est difficile à contrôler la qualité ; l'équipement de soudage par diffusion a un investissement ponctuel important et le soudage par diffusion ne nécessite pas de charges, mais a des exigences élevées pour le traitement de surface de la pièce.
Coût du traitement de surface : Les méthodes de traitement de surface courantes comprennent l'anodisation, le placage, etc. Pour les blocs d'eau en alliage d'aluminium, l'anodisation peut améliorer la dureté de surface, la résistance à l'usure et la résistance à la corrosion, tout en augmentant l'esthétique du produit ; les blocs d'eau en cuivre seront plaqués, comme le nickelage, pour empêcher l'oxydation et la corrosion du cuivre, et augmenter la durée de vie et la fiabilité du produit.
l Autres coûts : inspection et tests, emballage et transport, etc.
3-Suggestions d'optimisation des coûts
l Optimisation de l'utilisation des matériaux:
Choisissez le bon matériau : par exemple, le cuivre présente une conductivité thermique élevée, une densité unitaire élevée et un prix unitaire élevé ; l'aluminium est léger, a un prix unitaire faible et une conductivité thermique légèrement médiocre.
Utilisation des matériaux : assurez une utilisation efficace des matériaux et réduisez le gaspillage de matériaux en calculant avec précision l'épaisseur et la marge des matériaux.
Figure 2 : Schéma de principe du calcul de la consommation de matériaux
l Optimisation des processus de production
Simplification des moules : Concevez des moules simples pour réduire la complexité et le coût des moules.
Réduction du taux de rebut : Réduisez le taux de rebut grâce à un contrôle précis des processus et à une inspection de la qualité.
Moulage en une seule étape : Optimisez les itinéraires de processus, réduisez les étapes de traitement multiples et améliorez l'efficacité de la production.
Nous mettrons régulièrement à jour les informations et technologies relatives à la conception thermique et à l’allègement. Merci de votre intérêt pour Walmate.
En tant que composant clé du système de refroidissement liquide, la conception du bloc d'eau doit prendre en compte de multiples facteurs tels que les performances d'échange thermique, la résistance structurelle, la résistance à la corrosion, la résistance aux fuites et le contrôle des coûts. Le bloc d'eau est généralement conçu avec une structure complexe de fentes d'échange thermique (c'est-à-dire un canal d'écoulement), et la qualité de la conception de son canal d'écoulement interne détermine directement l'efficacité de l'échange thermique de l'ensemble du système.
Partie 2 : Conception de blocs d'eau, technologie de traitement et défis
1-Exigences de conception pour les blocs d'eau dans différents scénarios
Les appareils de calcul haute performance (tels que les processeurs haute performance, les GPU, etc.) génèrent beaucoup de chaleur pendant leur fonctionnement, de sorte que le bloc d'eau doit avoir des capacités de dissipation thermique efficaces. Afin de répondre aux exigences de dissipation thermique à haute densité de flux thermique, le bloc d'eau adopte généralement une conception de microcanaux haute densité pour augmenter la zone d'échange thermique et améliorer l'efficacité de la dissipation thermique. De plus, certaines conceptions intègrent le bloc d'eau directement sur le processeur, éliminant ainsi l'étape d'application de graisse silicone, ce qui simplifie non seulement le processus d'assemblage, mais améliore également encore les performances de dissipation thermique. En termes de fiabilité, le bloc d'eau doit avoir d'excellentes performances d'étanchéité pour éviter les fuites et assurer un fonctionnement stable à long terme.
l Refroidissement de la carte graphique :
Les cartes graphiques sont des zones à forte production de chaleur, le bloc d'eau doit donc être entièrement recouvert pour garantir que tous les composants générateurs de chaleur de la carte graphique peuvent être refroidis efficacement. Dans le même temps, le refroidissement de la carte graphique nécessite un débit élevé de liquide de refroidissement, de sorte que la structure interne du bloc d'eau doit prendre en charge un débit élevé pour évacuer rapidement la chaleur.
l Centre de données :
Dans les centres de données, la conception structurelle du bloc d'eau doit répondre à de multiples exigences telles qu'une dissipation thermique efficace, un faible bruit, une fiabilité élevée, une adaptabilité à une densité de puissance élevée, une gestion intelligente et une adaptabilité environnementale pour assurer un fonctionnement stable et une dissipation thermique efficace des centres de données.
2- Tendance évolutive de la structure des blocs d'eau
La tendance évolutive de la conception structurelle des blocs d'eau reflète la double recherche d'innovation technologique et d'amélioration des performances, qui se reflète principalement dans les aspects suivants :
l Amélioration des performances de dissipation thermique :
Augmentation de la surface de contact : Certaines conceptions de blocs d'eau améliorent les performances de dissipation thermique en augmentant la surface de contact avec l'élément chauffant. Par exemple, une conception de base en cuivre de grande surface peut obtenir un bon contact et une bonne conduction thermique.
Optimisation de la structure interne : Optimisation du canal d'eau interne. Une idée consiste à optimiser l'écoulement du fluide, par exemple en passant d'ailettes ordinaires à des ailettes de direction, en présentant un canal d'écoulement à longue bande, en favorisant la séparation de la couche limite d'écoulement, en réduisant l'épaisseur de la couche limite et en améliorant l'efficacité de l'échange thermique ; une autre idée consiste à augmenter la zone de capacité thermique, par exemple en passant des canaux d'eau grossiers traditionnels à une conception à microcanaux, ce qui augmente considérablement la surface de contact entre le liquide de refroidissement et la plaque de base et améliore l'efficacité de la dissipation thermique. Dans certaines conceptions, le liquide de refroidissement est pulvérisé sur la plaque de base à microcanaux via une plaque de guidage pour augmenter la vitesse d'écoulement locale et la turbulence, améliorant ainsi considérablement l'efficacité d'absorption thermique.
l Conception intégrée et intelligente :
Conception intégrée : La conception intégrée intègre la pompe à eau, les ailettes du dissipateur thermique, la base de conduction thermique et d'autres composants ensemble pour réduire le nombre de points de connexion et améliorer la stabilité du système et l'efficacité de la dissipation thermique.
Intégration multifonctionnelle : En plus des performances de dissipation thermique, les blocs d'eau modernes ont également des fonctions d'affichage et de surveillance de la température.
Conception modulaire : La structure de boucle modulaire améliore la commodité et la liberté d'organisation.
Figure 1 : Base du bloc d'eau avec différentes épaisseurs d'ailettes
l Matériaux et finitions hautes performances :
L'utilisation de matériaux hautes performances tels que la base en cuivre pur, combinée à des technologies de traitement de surface telles que le nickelage, améliore la conductivité thermique et la résistance à la corrosion.
3-Technologie de traitement et défis
l Les propriétés des matériaux affectent le traitement :
Problèmes de dureté et de ténacité des matériaux : les radiateurs fabriqués à partir de différents matériaux, tels que le cuivre, l'aluminium et leurs alliages, ont une dureté et une ténacité différentes, ainsi que des exigences différentes en matière d'outils et de processus de traitement. Les matériaux ayant une dureté plus élevée s'usent plus rapidement et nécessitent des changements d'outils plus fréquents ; les matériaux ayant une meilleure ténacité sont sujets à la déformation et aux bavures lors de la coupe.
Le traitement des matériaux composites cuivre-aluminium est complexe : les dissipateurs thermiques à dents de pelle en matériaux composites cuivre-aluminium doivent d'abord être transformés en matériaux composites à l'aide de la technologie de pressage à l'état semi-fondu par coulée continue, puis le traitement à dents de pelle est effectué. Le processus est plus compliqué et nécessite une plus grande précision pour les équipements et les processus.
l Exigences élevées en matière de précision dimensionnelle :
Il est difficile de garantir la cohérence de la hauteur et de l'épaisseur des dents : pour certains dissipateurs thermiques à dents haute densité, la hauteur et l'épaisseur de chaque dent doivent être très cohérentes pour garantir les performances et l'uniformité du dissipateur thermique. Si la différence de hauteur et d'épaisseur des dents est trop importante, cela entraînera un transfert de chaleur inégal et affectera l'effet de dissipation thermique. Pendant le traitement, des équipements de haute précision et des systèmes de contrôle automatisés sont nécessaires pour garantir la cohérence des spécifications de chaque dent.
Il est difficile de contrôler l'espacement des dents : lorsque les dents du dissipateur thermique sont trop denses, leur densité et leur espacement compliquent le processus de traitement, et l'équipement de traitement doit avoir une vitesse et une précision plus élevées pour maintenir l'uniformité des dents. Par exemple, lorsque l'espacement des dents est trop petit, l'outil est sujet à des interférences pendant la coupe, ce qui affecte la précision de traitement et la qualité de surface.
l Exigences strictes en matière de qualité de surface
Problème de bavures : des bavures se forment facilement pendant le traitement, ce qui affecte non seulement l'esthétique du radiateur, mais peut également gêner le flux d'air et réduire l'effet de dissipation thermique. La génération de bavures peut être causée par une faible précision de coupe du matériau, l'usure des outils de traitement, etc., et des processus d'ébavurage correspondants doivent être adoptés pour les résoudre.
Rugosité de surface : la rugosité de surface du radiateur affecte ses performances de dissipation thermique et les effets du traitement de surface ultérieur. Une rugosité de surface excessive augmentera la résistance au flux d'air et réduira l'efficacité de la dissipation thermique. Un traitement de surface supplémentaire est nécessaire pour réduire la rugosité, ce qui augmente les coûts et le temps de traitement.
l Équipements de traitement et exigences de processus élevés
Précision et stabilité de l'équipement : le pelletage des engrenages nécessite une pelleteuse de haute précision, et la précision de l'équipement affecte directement la précision dimensionnelle et la qualité de surface des dents. Dans le même temps, l'équipement doit avoir une bonne stabilité pour assurer la cohérence dimensionnelle pendant le traitement à long terme.
Sélection et usure des outils : des outils appropriés sont essentiels à la qualité du traitement. Le matériau, les paramètres géométriques, etc. de l'outil doivent être sélectionnés en fonction des propriétés du matériau. Pendant le processus de traitement, l'usure de l'outil entraînera une augmentation de la force de coupe, une diminution de la précision dimensionnelle et une augmentation de la rugosité de la surface, et l'outil devra être ajusté ou remplacé à temps.
Vitesse d'avance et profondeur de coupe : des réglages déraisonnables de la vitesse d'avance et de la profondeur de coupe peuvent facilement entraîner des défauts de traitement. Si la vitesse d'avance est trop rapide et la profondeur de coupe trop importante, l'outil sera surchargé, ce qui entraînera un arrachement de l'outil, un rebond de l'outil, une chute de l'outil, etc., affectant la précision de traitement et la qualité de surface.
Figure 2 : Processus de coupe des dents
l Exigences de personnalisation élevées
Différents scénarios d'application ont des exigences différentes en matière de taille, de forme, de hauteur de dent, d'épaisseur de dent, d'espacement de dent et d'autres paramètres du radiateur, qui doivent être personnalisés en fonction des besoins spécifiques. Cela nécessite que le fabricant de traitement dispose de capacités d'ajustement de processus flexibles et d'une riche expérience pour répondre aux divers besoins de personnalisation.
Nous mettrons régulièrement à jour les informations et technologies relatives à la conception thermique et à l’allègement. Merci de votre intérêt pour Walmate.
Avec la croissance rapide de la puissance de calcul de l'intelligence artificielle mondiale et l'augmentation continue de la consommation d'énergie thermique (TDP) des puces, la demande de refroidissement des centres de données est confrontée à des défis sans précédent. Dans le même temps, les politiques de plus en plus strictes en matière d'économie d'énergie et de réduction des émissions de carbone dans le monde entier ont encore favorisé l'innovation en matière de technologie de refroidissement. Dans ce contexte, les solutions de refroidissement par air traditionnelles sont progressivement devenues difficiles à satisfaire à la double exigence de dissipation thermique efficace et d'économie d'énergie. La technologie de refroidissement liquide progresse rapidement en raison de ses excellentes performances de dissipation thermique et de ses avantages significatifs en matière d'économie d'énergie, devenant le choix dominant pour les solutions de refroidissement des centres de données. En tant qu'équipement de base pour le traitement et le stockage des données, les performances et la stabilité du serveur sont directement liées à l'efficacité de fonctionnement de l'ensemble du système. Les composants de base du serveur, notamment la carte mère, le processeur, la mémoire, le disque dur et la carte graphique, génèrent beaucoup de chaleur en fonctionnement continu à forte charge. Si la chaleur ne peut pas être dissipée de manière opportune et efficace, cela affectera gravement les performances et la durée de vie du serveur. À cette fin, des systèmes de refroidissement liquide avancés ont été introduits dans les solutions de refroidissement des serveurs et installés directement sur les principales sources de chaleur telles que les processeurs et les cartes graphiques pour améliorer considérablement l'efficacité de la dissipation thermique.
Partie 1 : Structure et principe de fonctionnement du bloc d'eau
L'un des composants principaux du système de refroidissement liquide est le bloc d'eau, qui est généralement constitué de matériaux en cuivre ou en aluminium à haute conductivité thermique et est conçu avec des canaux d'eau précis et des structures de dissipateur de chaleur. Ces blocs d'eau s'adaptent parfaitement à la surface des sources de chaleur telles que les processeurs et les GPU, et absorbent et transfèrent rapidement la chaleur grâce à l'eau de refroidissement qui circule à l'intérieur. La chaleur est ensuite transportée vers le dissipateur de chaleur, qui circule ensuite dans le système de refroidissement par eau et finit par se dissiper dans l'air ambiant.
Figure 1 : Tendances de la consommation d'énergie thermique des principaux fabricants de puces
1- Types et caractéristiques courantes des blocs d'eau
l Bloc d'eau à microcanaux
Caractéristiques : Le bloc d'eau à microcanaux adopte une conception précise de micro-canaux d'eau. La structure du canal d'eau est fine et complexe, ce qui peut augmenter considérablement la zone de contact entre le liquide de refroidissement et les composants générateurs de chaleur, améliorant ainsi considérablement l'efficacité de la dissipation thermique. La conception du micro-canal d'eau peut également produire un fort effet de turbulence pendant l'écoulement du liquide de refroidissement, améliorant encore le coefficient de transfert de chaleur par convection et obtenant un transfert de chaleur efficace.
Scénarios d'application : Il est particulièrement adapté aux processeurs et aux GPU à forte génération de chaleur, en particulier dans le calcul haute performance, l'overclocking et les centres de données, qui ont des exigences de dissipation thermique extrêmement élevées.
l Bloc d'eau à grand débit
Caractéristiques : La structure interne du bloc d'eau à grand débit est relativement simple, utilisant généralement une plaque de cuivre ou une conception de rainure gravée, et le coût de fabrication est faible. Son principal avantage est qu'il s'appuie sur un débit d'eau à grande vitesse pour évacuer rapidement la chaleur et qu'il convient à une utilisation avec un système de refroidissement par eau à grand débit. Bien que la structure soit simple, sa capacité de dissipation thermique efficace en fait un choix très rentable.
Scénario d'application : Convient aux scénarios avec certaines exigences en matière d'efficacité de dissipation thermique mais un budget limité, tels que les systèmes informatiques DIY de milieu à haut de gamme ou les clusters de serveurs de petite et moyenne taille.
l Bloc d'eau de type injection
Caractéristiques : Le bloc de refroidissement à eau de type jet pulvérise le liquide de refroidissement d'une buse étroite vers la plaque inférieure à micro-canaux à grande vitesse à travers la plaque de guidage, formant un fort effet de turbulence et améliorant considérablement l'efficacité de la dissipation thermique. Cette conception augmente non seulement la surface de contact entre le liquide de refroidissement et la base, mais optimise également davantage les performances d'échange thermique grâce à un flux à grande vitesse.
Scénarios d'application : Convient aux processeurs et GPU hautes performances, en particulier dans les scénarios à forte dissipation thermique et à haut débit, tels que l'overclocking, la formation à l'intelligence artificielle et le rendu graphique.
2-Structure générale du bloc d'eau
Un waterblock est un bloc métallique contenant des canaux d'eau à l'intérieur, généralement en cuivre ou en aluminium. Il n'entre pas en contact avec le processeur, la carte graphique ou d'autres appareils générateurs de chaleur. Sa conception structurelle détermine directement la qualité des performances de dissipation de chaleur. Un waterblock typique se compose généralement des éléments clés suivants :
l La base est généralement constituée de matériaux à haute conductivité thermique tels que le cuivre ou l'alliage d'aluminium, et la surface est finement traitée pour assurer un contact étroit avec les composants générateurs de chaleur. La base est équipée d'une conception de canal d'écoulement complexe pour augmenter la surface de contact entre le liquide de refroidissement et la base.
l La plaque de recouvrement, avec la base, forme une cavité d'étanchéité du canal d'écoulement pour protéger le canal d'écoulement, le joint et les autres composants à l'intérieur du bloc d'eau de la poussière, des impuretés et des dommages physiques externes.
l L'entrée et la sortie d'eau sont les interfaces permettant au liquide de refroidissement d'entrer et de sortir de la tête de refroidissement par eau. Elles sont généralement conçues sur le côté ou sur le dessus de la tête de refroidissement par eau pour garantir que le liquide de refroidissement puisse entrer et sortir en douceur. La conception de la position doit tenir compte du trajet d'écoulement du fluide pour réduire la résistance à l'écoulement et augmenter le débit du liquide de refroidissement.
l Les clips sont utilisés pour fixer fermement la tête de refroidissement par eau au processeur ou à d'autres composants générateurs de chaleur afin de garantir une base solide et d'obtenir une conduction thermique efficace.
Figure 2 : Structure typique d'un bloc d'eau
3- Optimisation complète des performances de dissipation thermique
l Optimisation de la conception des canaux d'écoulement
Augmenter la surface de contact du canal d'écoulement : En concevant des canaux d'écoulement plus étroits et plus denses, la surface de contact entre le liquide de refroidissement et la base peut être considérablement augmentée, améliorant ainsi le coefficient de transfert de chaleur par convection. Par exemple, la conception du microcanal présente une structure de canal d'eau fine. Les paramètres de conception du bloc d'eau à microcanaux (tels que la largeur, la hauteur et l'espacement du canal) ont une influence décisive sur son efficacité de dissipation thermique : à mesure que la largeur du canal diminue, le coefficient de transfert de chaleur augmente considérablement, grâce à l'effet de turbulence amélioré du flux de liquide de refroidissement dans le canal étroit, améliorant ainsi l'efficacité de l'échange thermique ; la hauteur de canal plus élevée contribue à augmenter l'espace d'écoulement du liquide de refroidissement, améliorant ainsi les performances de transfert de chaleur ; l'espacement plus petit des canaux peut augmenter la surface de contact entre le liquide de refroidissement et la source de chaleur, améliorant ainsi l'efficacité de dissipation thermique.
Il peut également être optimisé en optimisant la disposition des canaux d'écoulement et en réduisant les coudes des canaux d'écoulement : une disposition raisonnable des canaux d'écoulement peut garantir que le liquide de refroidissement recouvre uniformément la surface des composants générateurs de chaleur et réduire la différence de température locale. Les coudes dans le canal d'écoulement augmentent la perte de charge et la résistance interne à l'écoulement, réduisant ainsi l'efficacité du refroidissement. Le nombre de coudes doit être réduit au minimum lors de la conception. Si cela ne peut être évité, les coudes doivent être conçus comme des transitions douces pour réduire la chute de pression et optimiser les performances d'écoulement.
l Matériaux à haute conductivité thermique : La base du bloc d'eau est généralement constituée de matériaux à haute conductivité thermique tels que le cuivre pur ou l'alliage d'aluminium. Ces matériaux peuvent transférer efficacement la chaleur de la source de chaleur au liquide de refroidissement, améliorant ainsi les performances globales de dissipation thermique.
l Optimisation des paramètres structurels, tels que l'épaisseur du substrat de base, les ailettes, la structure du spoiler, etc. L'augmentation de l'épaisseur du substrat entraînera une augmentation de la température maximale, de sorte que la conception doit trouver le meilleur équilibre entre l'effet de dissipation thermique et la résistance structurelle ; en augmentant la hauteur, l'épaisseur et l'espacement des ailettes, les performances de dissipation thermique peuvent être améliorées, mais en même temps, la résistance à l'écoulement augmentera également. Trouvez la meilleure combinaison de conception d'ailettes pour maximiser les performances de dissipation thermique. La forme de la colonne de spoiler peut améliorer efficacement l'effet de turbulence et améliorer l'efficacité de l'échange thermique.
Nous mettrons régulièrement à jour les informations et technologies relatives à la conception thermique et à l’allègement. Merci de votre intérêt pour Walmate.
Basé sur la production réelle, cet article résume les problèmes courants, les causes et les méthodes d'amélioration du processus de soudage par friction-malaxage pour votre référence.
1-Défauts de surface
(1) Rainures de surface
l Description du problème : Les rainures de surface, également appelées défauts de labour, apparaissent généralement sur la surface supérieure de la soudure, tendant vers le bord avancé de la soudure, et ont la forme de rainures.
l Cause : Le flux de métal thermoplastique autour de la soudure est insuffisant et le métal plastique de la soudure ne peut pas remplir complètement la cavité instantanée laissée par l'aiguille d'agitation pendant son mouvement.
l Méthode d'amélioration : augmenter le diamètre de l'épaulement, augmenter la pression et réduire la vitesse de soudage.
Figure 1 : Rainures
(2)Bavures de bord
l Description du problème : Des bavures apparaissent sur le bord extérieur de la soudure et sont de forme ondulée.
l Cause : Mauvaise adaptation de la vitesse de rotation et de la vitesse de soudage, pression vers le bas excessive.
l Méthode d'amélioration : Optimiser les paramètres de soudage et réduire la quantité de pression.
Figure 2 : Bavures de bord
(3)Décapage de surface
l Description du problème : Un pelage ou un filetage superficiel apparaît à la surface de la soudure sous forme de peau ou de filetage.
l Cause : Une grande quantité de chaleur générée par le frottement du métal s'accumule dans la surface du métal de la soudure, ce qui fait que le métal local à la surface atteint un état de fusion.
l Méthode d’amélioration : optimiser les paramètres de soudage, réduire la vitesse de rotation et augmenter la vitesse de soudage.
Figure 3 : Peeling de surface
(4) Cicatrice de soudure au dos
l Description du problème : Un cordon de soudure se forme à l'arrière de la soudure.
l Cause : Contrôle incorrect de la profondeur et de la pression de la tête d'agitation pendant le soudage.
l Méthode d'amélioration : Optimiser les réglages de profondeur et de pression de la tête de mélange.
2-Défauts internes
(1) Pénétration incomplète
l Description du problème : Un défaut de type « fissure » se produit lorsque le fond de la soudure n'est pas connecté ou n'est pas complètement connecté.
l Cause : L'aiguille d'agitation n'est pas assez longue, ce qui entraîne une agitation insuffisante du matériau au fond de la soudure.
l Méthode d'amélioration : Sélectionnez la longueur d'aiguille d'agitation appropriée pour garantir que le matériau sur l'épaisseur de la soudure puisse être entièrement agité.
Figure 4 : Pénétration incomplète
(2) Trous
l Description du problème : Un défaut de type « fissure » se produit lorsque le fond de la soudure n'est pas connecté ou n'est pas complètement connecté.
l Cause : Pendant le processus de soudage, en raison d'un apport de chaleur par friction insuffisant, une quantité insuffisante de matériau atteint l'état plastifié, ce qui entraîne un flux de matériau insuffisant et une fermeture incomplète de la zone de soudure.
l Méthodes d'amélioration : optimiser les paramètres de soudage, améliorer la conception de l'aiguille d'agitation et contrôler la vitesse de soudage et la vitesse de rotation.
Figure 5 : Trous
Nous mettrons régulièrement à jour les informations et technologies relatives à la conception thermique et à l’allègement. Merci de votre intérêt pour Walmate.
Récemment, l'éditeur a remarqué que de nombreuses entreprises s'intéressent au stockage d'énergie par refroidissement liquide par immersion et planifient ce type de stockage. Après une période de silence, la technologie du refroidissement liquide par immersion a de nouveau attiré l'attention et semble redevenir populaire. Je pense que de nombreux pairs prêtent également attention à cette évolution.
1- Caractéristiques de la technologie de refroidissement liquide par immersion
Les cellules de stockage d'énergie évoluent vers 300+Ah, et les systèmes de stockage d'énergie évoluent vers 5MWh+. Plus la cellule est grande, plus elle génère de chaleur, plus il est difficile de dissiper la chaleur et plus il est difficile d'assurer la cohérence de la température. De plus, le système de stockage d'énergie est composé d'un grand nombre de cellules empilées et les conditions de fonctionnement sont complexes et changeantes, ce qui est plus susceptible de provoquer une génération de chaleur inégale et une distribution de température inégale. Si les problèmes de dissipation de chaleur et d'uniformité de température ne sont pas correctement résolus, les performances de charge et de décharge, la capacité et la durée de vie de la batterie diminueront, affectant les performances de l'ensemble du système. De plus, la sécurité a toujours été l'« épée de Damoclès » suspendue au-dessus du stockage d'énergie des batteries au lithium, et le moyen le plus courant d'améliorer la sécurité est de s'orienter vers les trois dimensions de la sécurité intrinsèque, de la sécurité active et de la sécurité passive.
Le refroidissement liquide par immersion consiste à immerger la cellule de la batterie dans un liquide isolant, non toxique et dissipant la chaleur. Le liquide de refroidissement a une conductivité thermique et une capacité thermique spécifique plus élevées. Cette méthode de contact direct peut fournir une efficacité de transfert de chaleur extrêmement élevée tout en améliorant une meilleure uniformité de température. De plus, en plus d'être un moyen de contrôle de la température, le liquide de refroidissement peut également être utilisé comme fluide anti-incendie pour les systèmes de stockage d'énergie, combinant contrôle de la température et protection contre l'incendie, ce qui est également une caractéristique importante de la technologie de refroidissement par liquide par immersion. Le refroidissement par liquide par immersion présentera sans aucun doute plus d'avantages dans le contexte d'une industrie qui exige des performances de dissipation thermique plus élevées et une sécurité renforcée.
Figure 1 : Boîtier de batterie Pack à refroidissement liquide immersif
2- Solution de stockage d'énergie par refroidissement liquide immergé
En tant que branche de la technologie de refroidissement liquide, la technologie de refroidissement liquide par immersion n'est pas la première à être utilisée dans l'industrie du stockage d'énergie. Elle a été initialement utilisée dans le domaine du calcul haute performance, puis progressivement étendue aux centres de données, à l'intelligence artificielle, à la crypto-monnaie, etc.
L'intention initiale de la conception du système de stockage d'énergie par refroidissement liquide par immersion est de résoudre les lacunes du refroidissement par air traditionnel et du refroidissement liquide indirect en termes d'efficacité de refroidissement et de contrôle de la différence de température de la batterie. La mise en service officielle du projet Southern Power Grid Meizhou Baohu marque l'application réussie du refroidissement liquide par immersion, une technologie de pointe, dans le domaine de la nouvelle ingénierie de stockage d'énergie.
l Méthode de refroidissement et méthode de circulation du liquide de refroidissement
Les méthodes de refroidissement sont divisées en monophasé et à changement de phase. Le refroidissement liquide par immersion monophasé est utilisé, comprenant principalement de l'huile minérale, de l'huile de silicone, de l'ester naturel, etc. D'autres schémas utilisent le refroidissement liquide par immersion biphasé, principalement représenté par l'hydrofluoroéther, et utilisent la chaleur latente à changement de phase pour dissiper la chaleur et améliorer l'efficacité de la dissipation thermique. Selon des statistiques incomplètes, le schéma de « refroidissement par immersion monophasé » est le plus courant parmi les systèmes de stockage d'énergie par refroidissement liquide par immersion actuellement commercialisés.
Selon la différence de mode de circulation du liquide de refroidissement, il existe trois voies techniques dans le refroidissement liquide par immersion monophasé : la convection naturelle, l'entraînement par pompe et le refroidissement liquide par plaque froide couplée par immersion. La convection naturelle utilise les caractéristiques de dilatation du volume du liquide et de réduction de la densité après chauffage pour obtenir la flottaison du liquide de refroidissement chaud et son affaissement après refroidissement, complétant ainsi la dissipation thermique par circulation ; le cœur du système d'entraînement par pompe est que l'unité de refroidissement liquide entraîne le liquide de refroidissement à circuler entre la canalisation de refroidissement liquide et le boîtier d'immersion de la batterie pour compléter l'ensemble du processus de dissipation thermique par circulation ; et dans le schéma de refroidissement liquide à plaques couplées par immersion, la batterie est immergée dans le fluide diélectrique, et la plaque froide en contact avec le fluide diélectrique est utilisée pour évacuer la chaleur, évitant l'utilisation de circuits secondaires complexes pour refroidir le fluide diélectrique.
l Forme du produit et solution d'intégration
L'itération de la solution d'intégration du système de stockage d'énergie refroidi par liquide par immersion est un processus allant de l'ensemble à la partie puis aux détails. Chaque étape est optimisée et améliorée sur la base de l'étape précédente pour obtenir des performances et une sécurité supérieures.
Du niveau de la cabine au niveau du pack, la technologie d'intégration du système présente les caractéristiques de la personnalisation de la scène. La diversification des scénarios de stockage d'énergie rend la demande de systèmes de stockage d'énergie différente. Un seul produit ne peut pas répondre à la demande du marché. La conception modulaire permet d'optimiser et d'étendre les produits de stockage d'énergie en fonction de l'échelle et de la demande de puissance du projet, ce qui permet d'ajuster et de déployer rapidement les solutions de stockage d'énergie en fonction de différents scénarios d'application et besoins.
3-Défis et scénarios de mise en œuvre dans le processus d'industrialisation
Les systèmes de stockage d’énergie refroidis par liquide immergés sont confrontés à de nombreux défis au cours du processus de commercialisation, notamment la faisabilité économique, la complexité technique, l’acceptation du marché et la maturité de la chaîne industrielle.
l Complexité technique : Comparés aux systèmes de refroidissement liquide à plaque froide, les systèmes de refroidissement liquide par immersion sont plus complexes à concevoir et à mettre en œuvre.
l Maturité de la chaîne industrielle : La chaîne industrielle de la technologie du refroidissement liquide par immersion n'est pas encore totalement mature, ce qui limite son application à un plus large éventail de domaines. La maturité de la chaîne industrielle affecte directement la promotion et la commercialisation de la technologie.
l Défis économiques : L'industrie du stockage d'énergie en est encore aux premiers stades de son développement commercial et le manque de rentabilité rend difficile la promotion des technologies à coût élevé par le marché. De nombreuses entreprises rivalisent avec des prix bas pour des commandes temporaires, ce qui limite la pénétration du refroidissement liquide par immersion.
À l'heure actuelle, le marché principal de l'industrie du stockage d'énergie est toujours dominé par le refroidissement par air et le refroidissement par liquide à plaque froide, et le refroidissement par liquide par immersion n'est pas encore pleinement accepté par le marché. Bien que la pénétration du marché et l'acceptation de la technologie de refroidissement par liquide par immersion ne soient pas élevées, elle peut ne pas montrer un potentiel considérable dans certains scénarios particuliers, tels que :
l Industrie des produits chimiques dangereux : les entreprises de produits chimiques dangereux appliquent des contrôles de sécurité extrêmement stricts sur les équipements de stockage d'énergie, car la plupart des produits chimiques qu'elles produisent et stockent sont hautement inflammables, explosifs, toxiques ou corrosifs. En cas d'accident, celui-ci entraînera non seulement de graves pertes pour l'entreprise elle-même, mais pourra également entraîner une pollution de l'environnement et des dommages aux communautés environnantes.
l Stations de base et centres de données : les stations de base et les centres de données ont une faible tolérance à l'emballement thermique. Les systèmes de stockage d'énergie des centres de données doivent disposer de batteries aux performances stables et ne sont pas sujets à l'emballement thermique pour garantir la sécurité du système. Les exigences en matière de qualité de l'énergie sont élevées et le système de stockage d'énergie doit avoir une capacité de réponse rapide. En cas d'urgence telle qu'une panne de réseau ou une coupure de courant, le système de stockage d'énergie doit pouvoir passer directement en mode décharge pour assurer la continuité et la stabilité de l'alimentation électrique.
l Station de charge rapide : lors d'une charge et d'une décharge à des vitesses élevées, la batterie génère une grande quantité de chaleur en peu de temps, ce qui entraîne une température trop élevée et inégale de la batterie, ce qui constitue une menace pour les performances, la durée de vie et la sécurité de la batterie. Cela signifie que la gestion thermique de la batterie devient particulièrement importante dans les scénarios de charge et de décharge à vitesse élevée.
Nous mettrons régulièrement à jour les informations et technologies relatives à la conception thermique et à l’allègement. Merci de votre intérêt pour Walmate.
L'étanchéité à l'air du pack de batteries est un indicateur crucial dans les véhicules électriques et les systèmes de stockage d'énergie. Le test d'étanchéité à l'air du pack de batteries est principalement effectué sur la coque du pack de batteries, l'interface, le connecteur, l'ensemble de refroidissement, etc. pour garantir que l'intérieur du pack de batteries n'est pas contaminé ou envahi par des impuretés telles que la poussière et l'humidité de l'environnement extérieur, et que l'ensemble de refroidissement ne fuit pas, afin de garantir que le pack de batteries conserve des performances et une durée de vie normales, et ne provoque pas d'accidents de sécurité tels qu'un court-circuit ou une explosion.
1-Formulation standard des tests de niveau de protection et d'étanchéité des batteries
Norme de protection internationale (IEC60529), également connue sous le nom de niveau de protection contre les corps étrangers ou code IP. Le système de niveaux de protection IP (Ingress Protection) est une norme établie par la Commission électrotechnique internationale (IEC) pour classer le niveau de protection des boîtiers d'équipements électriques contre l'intrusion de corps étrangers et l'intrusion d'eau. Le niveau d'étanchéité à l'air du boîtier de la batterie doit généralement atteindre IP67 ou IP68, ce qui signifie que le boîtier de la batterie doit être complètement protégé contre la pénétration de poussière (niveau d'étanchéité à la poussière 6) et peut être immergé dans l'eau à une certaine pression pendant une période de temps sans pénétration d'eau à un niveau nocif (niveau d'étanchéité 7). Des exigences plus strictes prévoient que la batterie puisse être immergée dans de l'eau de 1 m de profondeur pendant 60 minutes sans pénétration d'eau (niveau d'étanchéité 8). Le niveau de protection IP se compose généralement de deux chiffres. Plus le nombre est élevé, plus le niveau de protection est élevé, comme le montre la figure 1 :
Figure 1 : Description du niveau de protection IP
Afin de garantir que le bloc-batterie répond aux exigences IP67 et IP68, le bloc-batterie doit être immergé dans l'eau. Cette méthode prend du temps, détruit le bloc-batterie et présente certains risques pour la sécurité. Elle ne convient pas comme test hors ligne pour les batteries d'alimentation. Par conséquent, il est devenu une pratique courante dans l'industrie d'utiliser des tests d'étanchéité à l'air pour garantir que le bloc-batterie répond aux exigences IP67 et IP68. La formulation des normes de test d'étanchéité à l'air doit prendre en compte la relation entre la valeur de chute de pression et le taux de fuite, ainsi que la relation entre l'ouverture et la fuite d'eau. La formulation des normes de test d'étanchéité à l'air implique une série d'étapes allant des extrêmes théoriques à la vérification expérimentale pour parvenir à la conversion du niveau IP aux normes de test d'étanchéité à l'air. Par exemple, en prenant l'IP68 comme exemple :
Figure 2 : Étapes de formulation des normes d'essai d'étanchéité à l'air
2- Sélection des méthodes d'essais d'étanchéité à l'air et analyse des difficultés d'essai
La conception et la qualité de fabrication du bloc-batterie sont des facteurs clés affectant l'étanchéité à l'air, notamment la solidité et la résistance du couvercle du boîtier de la batterie, l'étanchéité de la coque du bloc-batterie, les interfaces et les connecteurs, les évents antidéflagrants et l'étanchéité du connecteur électrique lui-même. De plus, certains problèmes affecteront l'étanchéité à l'air pendant l'utilisation, tels que les problèmes de dilatation et de contraction thermiques, le vieillissement du matériau, les vibrations et les impacts. Dans la production et la fabrication de coques de blocs-batteries, nous accordons plus d'attention à la mauvaise étanchéité à l'air causée par des problèmes tels que les points de soudure et la qualité des joints, tels que les points de soudure irréguliers, les soudures faibles ou fissurées, les entrefers et la mauvaise étanchéité des connexions de joint.
Le test d'étanchéité à l'air du bloc-batterie est principalement divisé en test d'étanchéité à l'air de la coque supérieure, de la coque inférieure et des pièces d'assemblage. Le test d'étanchéité à l'air des coques supérieure et inférieure doit répondre aux exigences de fuite d'étanchéité à l'air après l'assemblage. Lors de la sélection de la méthode de test d'étanchéité à l'air pour le bloc-batterie, les caractéristiques du bloc-batterie, les exigences de précision des tests, l'efficacité de la production et le coût sont généralement pris en compte de manière exhaustive.
En ingénierie, les tests de coque de batterie sont généralement divisés en tests d'étanchéité à l'air de processus et tests d'étanchéité à l'air d'expédition. De plus, les tests d'étanchéité à l'air des coques supérieure et inférieure doivent répondre aux exigences d'étanchéité à l'air après l'assemblage, ce qui impose des exigences plus strictes en matière de normes de test. Pour garantir que l'étanchéité à l'air répond aux exigences, les difficultés suivantes doivent être surmontées en fonctionnement réel :
l Stabilité de la structure du produit : la qualité des soudures, y compris les soudures en bouchon, les soudures au robinet, les soudures de poutre, les soudures de la plaque inférieure du cadre, les soudures des plaques de recouvrement avant et arrière du cadre, etc. Les problèmes de fuite de soudure sont principalement concentrés aux points de démarrage et de fin d'arc et les défauts causés par le brûlage ; les fissures causées par la contrainte de déformation de soudure, telles que le soudage des parois latérales de la cavité de la plaque inférieure, la stratification du matériau de la cavité de la plaque inférieure et l'incapacité à résister à la contrainte de déformation de soudure.
l Adaptabilité et stabilité des dispositifs de test étanches : la conception des dispositifs de test doit correspondre étroitement à la forme et aux dimensions des composants testés, garantissant que les composants peuvent être solidement fixés aux dispositifs de test pendant le processus de test, réduisant ainsi les erreurs de test causées par des décalages de position ou des vibrations. Cependant, dans la pratique, la taille et la forme des blocs-batteries varient considérablement, ce qui nécessite la conception et la fabrication de plusieurs dispositifs de test différents, ce qui augmente les coûts et la complexité opérationnelle. La conception d'un dispositif universel compliquerait encore davantage le processus de conception.
l Répétabilité des résultats des tests d'étanchéité à l'air : des facteurs tels que la pression de l'air, la température et la sécheresse de la pièce/du dispositif d'essai affecteront les résultats des tests d'étanchéité à l'air.
l Pour les pièces présentant de nombreuses petites fissures non pénétrantes, en raison de l'influence de facteurs tels que la précision de l'équipement de détection et les paramètres de détection, la source de fuite peut ne pas être découverte, ce qui entraîne une détection manquée.
Figure 3 : Outillage de test d'étanchéité à l'air
3-Combinaison de solutions de détection d'étanchéité à l'air des packs de batteries couramment utilisées en ingénierie
Le test d'étanchéité à l'air du processus de coque de la batterie comprend généralement un test d'étanchéité à l'air et un test d'immersion dans l'eau. Dans le test d'étanchéité à l'air, le couvercle supérieur du boîtier de la batterie est scellé, ne laissant qu'un port de connecteur comme entrée d'air. L'étanchéité à l'air de la batterie est jugée en contrôlant la pression d'air et en observant s'il y a des fuites d'air. Le test d'immersion dans l'eau consiste à immerger complètement l'ensemble du boîtier de batterie dans l'eau et à juger de son étanchéité à l'air en vérifiant s'il y a de l'eau dans le boîtier.
La détection des fuites d'hélium est une technologie qui utilise l'hélium comme gaz traceur pour détecter les fuites en détectant la concentration d'hélium au point de fuite. Lorsque l'hélium pénètre à l'intérieur ou à l'extérieur de l'appareil testé où il peut y avoir une fuite, s'il y a une fuite, l'hélium entrera ou s'échappera rapidement du système par la fuite et sera détecté par le spectromètre de masse. La méthode de détection des fuites d'hélium a une efficacité de détection élevée, en particulier pour détecter les petites fuites.
Figure 4 : Comparaison des méthodes de détection des fuites
En production réelle, plusieurs méthodes de détection sont généralement combinées pour améliorer l'efficacité et la précision de la détection. Par exemple, la méthode de détection des fuites à l'hélium convient à la détection de fuites de haute précision et de petite taille, tandis que la méthode de pression différentielle présente les caractéristiques d'une haute précision et d'une réponse rapide. De plus, bien que la méthode traditionnelle de détection de l'eau ait une faible précision de détection, elle est intuitive et peu coûteuse, et constitue un moyen pratique de localiser les fuites.
Nous mettrons régulièrement à jour les informations et technologies relatives à la conception thermique et à l’allègement. Merci de votre intérêt pour Walmate.
La défaillance potentielle de l'étanchéité au liquide du pack de refroidissement liquide de stockage d'énergie implique de multiples aspects, tels que : les fuites, la corrosion et le dépôt, l'eau de condensation et d'autres modes de défaillance.
1- Interconnexion et composition des fluides
Dans le système de refroidissement liquide de stockage d'énergie, l'interconnexion des fluides est responsable du transfert du liquide de refroidissement entre les différents composants. Grâce à une interconnexion efficace des fluides, le liquide de refroidissement circule efficacement dans le système, éliminant ainsi l'excès de chaleur généré pendant le processus de charge et de décharge de la batterie.
Un système bien scellé peut empêcher efficacement les fuites de liquide de refroidissement. Les fuites entraîneront non seulement une perte de liquide de refroidissement et nécessiteront un réapprovisionnement fréquent, mais affecteront également les performances de dissipation thermique et la stabilité du système. Dans le stockage d'énergie, les fuites de liquide de refroidissement peuvent également provoquer un court-circuit de la batterie, ce qui entraîne des problèmes de sécurité.
2-Conception étanche du système d'interconnexion des fluides
La conception étanche du système d'interconnexion de fluides est le lien clé pour garantir que le système maintient l'étanchéité et empêche les fuites de fluide dans diverses conditions de fonctionnement.
Figure 1 : Déploiement typique d'un système de refroidissement liquide de stockage d'énergie
(1) Analyser les sources de fuite possibles et les points de risque dans le système :
l La propriété d'auto-étanchéité de l'ensemble de refroidissement liquide. Par exemple, dans la conception intégrée du système de canaux de refroidissement liquide et du boîtier d'emballage, les composants sont reliés par soudage. Les défauts de qualité de soudage, les soudures médiocres, les pores, les fissures, etc. peuvent tous entraîner des problèmes d'infiltration de liquide.
l La conception structurelle est déraisonnable. Par exemple, les trous de positionnement ou les trous filetés du boîtier de refroidissement liquide sont trop proches du canal d'écoulement et les pièces mal soudées peuvent facilement devenir des canaux d'infiltration de liquide.
l Pièces de raccordement : Les raccords de tuyaux, les vannes et les joints du système de refroidissement liquide sont des points de fuite courants. Si la structure de raccordement n'est pas conçue correctement ou si le processus de fabrication n'est pas sophistiqué, de minuscules défauts se forment à l'intérieur des joints et le liquide de refroidissement peut également fuir à partir de ces défauts.
l Fuite causée par une mauvaise installation, le vieillissement ou l'endommagement du matériel, etc.
(2) Conception de la structure d'étanchéité :
l Le PACK refroidi par liquide utilise une méthode de refroidissement par plaque froide séparée sèche-humide. Dans des conditions de fonctionnement normales, les cellules de la batterie n'ont aucun contact avec le liquide de refroidissement, ce qui peut assurer le fonctionnement normal des cellules de la batterie. Une solution pour le refroidisseur liquide de stockage d'énergie consiste à le former par un processus d'extrusion, à intégrer le canal d'écoulement directement sur la plaque froide, puis à utiliser un traitement mécanique pour ouvrir le chemin de circulation du refroidissement. Dans ce processus, le choix du bon procédé de soudage est une étape importante pour assurer l'étanchéité. Pour plus de détails, veuillez vous référer à « Conception du procédé de soudage pour le boîtier inférieur pour le stockage d'énergie ».
l Les conduites de refroidissement liquide sont principalement utilisées pour les raccordements de tuyaux souples (rigides) de transition entre les sources de refroidissement liquide et les équipements, entre les équipements et entre les équipements et les conduites. Les principales méthodes de raccordement sont les suivantes :
Connexion rapide : L’une des méthodes de connexion pour les systèmes de refroidissement liquide de stockage d’énergie consiste à utiliser une connexion rapide VDA ou CQC.
Connexion filetée : les deux extrémités de la structure de connexion sont connectées de manière coulissante aux tuyaux, et la connexion filetée entre la bague filetée interne et le manchon fileté augmente la fermeté de la connexion.
Raccordement du tube de limitation et de l'écrou : un tube de raccordement est serré à une extrémité du tube et des tubes de limitation sont installés de manière fixe des deux côtés du tube de raccordement. Des rondelles en caoutchouc et des bagues convexes sont installées de manière fixe à l'intérieur des tubes de limitation et une rainure de bague de limitation est ouverte sur la surface de la tête du tube de raccordement. Un écrou est relié de manière rotative au sommet du tube de limitation et est relié de manière rotative au tube de limitation par des filetages.
Connexion de bague d'étanchéité : une bague d'étanchéité est collée à la paroi intérieure du manchon fileté par une colle forte, et la paroi intérieure de la bague d'étanchéité est reliée de manière mobile à la surface extérieure du tuyau pour éviter les fuites pendant l'utilisation.
(3) La plaque de refroidissement liquide PACK, l'interface de cabine, la tuyauterie de cabine, etc. sont toutes conçues avec une protection anticorrosion à long terme dans des conditions de liquide de refroidissement, de température et de débit communes pour assurer un fonctionnement à long terme sans corrosion. Effet des conditions de fonctionnement sur l'étanchéité au liquide :
l Température. Influence de la température élevée : lorsque la température augmente, la viscosité du liquide diminue généralement, ce qui peut entraîner une diminution des performances d'étanchéité du liquide, affectant ainsi l'étanchéité du liquide. Par exemple, certains matériaux d'étanchéité peuvent se déformer ou se détériorer à des températures élevées, provoquant des fuites. Influence de la basse température : dans un environnement à basse température, le liquide peut devenir visqueux, augmentant la difficulté d'écoulement, mais il peut également améliorer les performances du matériau d'étanchéité, améliorant ainsi l'étanchéité du liquide dans une certaine mesure.
l Pression. Environnement haute pression : sous haute pression, la densité et la viscosité du liquide peuvent augmenter, améliorant ainsi les performances d'étanchéité du liquide. Cependant, une pression excessive peut également endommager le matériau d'étanchéité et provoquer des fuites. Environnement basse pression : sous basse pression, les performances d'étanchéité du liquide peuvent être relativement faibles, en particulier si le matériau d'étanchéité lui-même est défectueux ou vieilli, il est plus susceptible de fuir.
l Débit. Débit élevé : lorsque le liquide s'écoule à grande vitesse, il peut produire une force d'impact importante sur la surface d'étanchéité, provoquant une usure ou une déformation du matériau d'étanchéité, affectant ainsi l'étanchéité du liquide. Faible débit : à faible débit, les performances d'étanchéité du liquide sont relativement bonnes, mais cela peut également masquer certains problèmes d'étanchéité potentiels tels que des défauts mineurs du matériau.
3-Problèmes de corrosion et de dépôt
l L'impact du blocage sur l'étanchéité à l'air :
Le liquide de refroidissement, les dépôts ou la croissance de la chaudière peuvent provoquer des blocages internes, un mauvais débit de liquide de refroidissement et une efficacité de refroidissement réduite.
Encrassement et tartre : les minéraux présents dans le liquide de refroidissement peuvent former des dépôts sur la paroi intérieure du tuyau après un fonctionnement à long terme, ce que l'on appelle « tartre ». L'encrassement peut également se former en raison de la précipitation de particules solides, de la cristallisation, de la corrosion ou de l'activité microbienne. Ces saletés obstruent les tuyaux et les plaques froides, augmentent la résistance à l'écoulement et réduisent l'efficacité du transfert de chaleur.
Problème de mousse : de la mousse peut se former dans le système de refroidissement liquide. La mousse adhère à la surface de la plaque froide, ce qui entraîne une diminution de l'effet de transfert de chaleur et peut augmenter la résistance au fonctionnement du système, provoquer une corrosion par cavitation de la pompe, etc., et endommager l'équipement.
l L'influence des courants de Foucault sur l'étanchéité à l'air :
Lorsqu'un fluide s'écoule dans un tuyau ou un espace, les changements de vitesse peuvent provoquer la formation de tourbillons, en particulier lorsque le fluide traverse des parties étroites ou des obstacles, des tourbillons sont plus susceptibles de se former. La viscosité et la densité du fluide affectent également la génération de tourbillons. Les fluides ayant une viscosité plus élevée sont plus susceptibles de former des tourbillons, tandis que les fluides ayant une densité plus élevée peuvent affaiblir la formation de tourbillons.
Chemins de fuite : les courants de Foucault forment des tourbillons sur les surfaces de contact, qui peuvent former de minuscules chemins de fuite dans des espaces ou des surfaces irrégulières, entraînant une fuite de gaz ou de liquide.
Usure de surface : l'écoulement tourbillonnaire peut provoquer l'usure des surfaces de contact, en particulier dans des conditions d'écoulement à grande vitesse. Cette usure peut réduire encore davantage l'étanchéité à l'air, car les surfaces usées sont plus susceptibles de former de nouveaux canaux de fuite.
Effets thermiques : Le flux de courants de Foucault génère de la chaleur, ce qui peut provoquer une déformation ou une dilatation thermique du matériau de la surface de contact, affectant ainsi l'étanchéité à l'air, en particulier dans les systèmes soumis à de grandes variations de température.
4-Problème d'eau de condensation
Français Dans certaines conditions, de la condensation peut se former dans les conduites de refroidissement liquide, ce qui peut endommager l'équipement ou réduire l'efficacité. Défaillance de l'isolation : Si le matériau isolant du tuyau est endommagé ou vieilli, de la chaleur sera perdue et l'effet de refroidissement sera affecté. En particulier dans les environnements à basse température, une défaillance de l'isolation peut provoquer la formation de givre ou de glace à la surface du tuyau. Fissuration par le gel : Dans les environnements froids, si des mesures antigel appropriées ne sont pas prises, le liquide de refroidissement dans les tuyaux peut geler et provoquer la rupture des tuyaux.
Solutions
l Mesures d'étanchéité : Assurez-vous que l'entrée et la sortie du tuyau de refroidissement liquide sont complètement bloquées pour empêcher l'air humide extérieur de pénétrer dans le compartiment de la batterie.
l Équipement de déshumidification : Installez un climatiseur déshumidifiant ou utilisez la fonction de déshumidification pour maintenir l'humidité dans le compartiment de la batterie dans une plage appropriée.
l Contrôle de la température : En installant des systèmes de climatisation ou de ventilation, la température et l'humidité de l'environnement dans lequel se trouve l'armoire de stockage d'énergie peuvent être contrôlées. Par exemple, la température peut être maintenue à 20-25 degrés Celsius et l'humidité relative peut être contrôlée à 40-60 %.
l Isolation measures: Simple isolation of empty battery racks to prevent moisture from entering the compartment containing the battery cluster.
Nous mettrons régulièrement à jour les informations et technologies relatives à la conception thermique et à l’allègement. Merci de votre intérêt pour Walmate.
La conception entièrement étanche du pack de stockage d'énergie est la clé pour assurer sa sécurité et son fonctionnement stable à long terme. L'étanchéité consiste essentiellement à utiliser un dispositif pour fermer (sceller) un espace ou rendre un joint étanche. La conception entièrement étanche peut empêcher efficacement les fuites de liquide et de gaz à l'intérieur de la cellule de batterie, ce qui est essentiel pour assurer le fonctionnement sûr et stable du système de stockage d'énergie. Par conséquent, lors de la conception, l'étanchéité à l'air et l'étanchéité du milieu liquide doivent être prises en compte.
En fonctionnement réel, la conception de l'étanchéité du pack de stockage d'énergie doit prendre en compte de manière exhaustive de nombreux facteurs tels que les matériaux, les processus, les équipements de test, les conditions environnementales et les processus de fabrication pour garantir que ses performances d'étanchéité peuvent répondre aux normes attendues. Cet article explique la pratique d'application et les points clés de la conception de l'étanchéité du pack de stockage d'énergie dans l'ingénierie réelle sous les aspects de l'étanchéité à l'air du boîtier du pack, de l'étanchéité au liquide du cycle de refroidissement liquide et du fluide de refroidissement liquide.
Partie supérieure : Conception de l'étanchéité du boîtier de pack de stockage d'énergie
La conception de l'étanchéité permet de maintenir la température et la pression à l'intérieur du bloc de stockage d'énergie stables, ce qui joue un rôle clé dans le fonctionnement normal et les performances de la batterie. De plus, la conception de l'étanchéité peut réduire l'impact de l'environnement externe sur la batterie interne, comme l'humidité, la poussière et d'autres polluants, etc., améliorant ainsi la fiabilité et la durée de vie du système. De plus, l'utilisation de matériaux et de structures d'étanchéité appropriés peut améliorer efficacement la résistance à l'usure et au vieillissement des joints, améliorer la durabilité de l'ensemble du système de stockage d'énergie et réduire les coûts de maintenance.
L'idée générale de la conception étanche à l'air est d'analyser la structure de la boîte pour découvrir les zones clés où des fuites peuvent exister, puis de prendre des mesures ciblées en fonction des performances spécifiques et des exigences fonctionnelles des différentes zones.
1-analyse de la structure de la boîte
Le boîtier n'est pas seulement le support physique des modules de batterie et des composants électriques, mais aussi une garantie importante pour le fonctionnement sûr et fiable de l'ensemble du système de stockage d'énergie. Il s'agit du « squelette » du pack de stockage d'énergie, qui est généralement composé d'un couvercle supérieur, d'un boîtier inférieur, de composants de support, de pièces d'étanchéité et de boulons, etc.
Figure 1 : Schéma du boîtier de stockage d'énergie et zones clés sur lesquelles se concentrer dans la conception de l'étanchéité (par exemple, indiquées par des flèches rouges)
Comme le montre la figure ci-dessus, déterminez où des fuites potentielles peuvent se produire :
l Points de connexion de plusieurs pièces, tels que : l'interface d'assemblage entre le couvercle supérieur et le boîtier inférieur, l'interface d'installation entre les connecteurs haute et basse tension et le boîtier, l'interface d'installation entre les composants exposés et le boîtier de batterie, etc.
l Si des boulons sont utilisés pour la connexion, il peut également y avoir un risque de fuite au niveau du point d'installation et de fixation, comme l'interface électrique et l'interface d'installation du panneau avant du boîtier.
l Il ne doit y avoir aucun trou ni espace dans le couvercle supérieur et le corps inférieur de la boîte pour assurer l'étanchéité et les performances de protection de la boîte.
Figure 2 : Boîtier inférieur de refroidissement liquide par immersion (cadre en tôle + plaque inférieure de refroidissement liquide en aluminium)
2- Conception d'étanchéité de l'interface d'installation entre le couvercle supérieur et le boîtier inférieur
Le couvercle supérieur peut généralement être divisé en deux types : type plat et type de forme spéciale. Leurs caractéristiques structurelles sont également différentes. Par exemple, matériau composite SMC, aluminium, quel que soit le matériau, afin de réduire la complexité de la structure auto-obturante, le couvercle supérieur de la coque de la batterie Le couvercle est généralement de conception monobloc. De plus, les exigences d'ouverture du couvercle supérieur doivent également répondre aux exigences de l'interface et doivent être indépendantes de l'interface d'étanchéité pour réduire l'impact sur l'étanchéité du bloc-batterie. La conception du joint du couvercle supérieur suit généralement les principes suivants :
l La conception des pièces intégrées est adoptée pour éviter la conception de pièces séparées, garantissant ainsi la stabilité des performances « auto-obturantes » du couvercle supérieur.
l Les trous de positionnement et les dispositifs de positionnement sont conçus sur le bord du couvercle supérieur (à l'extérieur de l'interface d'étanchéité entre le couvercle supérieur et le plateau inférieur).
l L'interface d'étanchéité entre le couvercle supérieur et le corps inférieur du boîtier nécessite une surface correspondante pour répondre aux exigences d'étanchéité « uniforme » et « continue ».
Actuellement, les solutions courantes pour le boîtier inférieur du pack de stockage d'énergie sont : boîtier en tôle + plaque de refroidissement liquide, boîtier moulé sous pression + plaque de refroidissement liquide, boîtier intégré profilé, boîtier intégré moulé sous pression, etc. Parmi elles, le boîtier intégré profilé et d'autres solutions En revanche, il présente les avantages d'une bonne capacité portante du canal d'écoulement et d'un faible coût d'ouverture du moule, et est largement utilisé. Le choix du procédé de soudage a une grande influence sur les performances d'étanchéité. Pour les soudures de différents matériaux et épaisseurs, le choix d'une méthode de soudage appropriée peut améliorer efficacement la qualité de la soudure pour garantir la résistance globale et les performances d'étanchéité du système.
De plus, la conception de l'étanchéité du boîtier inférieur doit suivre les principes d'étanchéité suivants :
l Pour la construction du cadre, on utilise des profilés à section fermée et au niveau des joints, on utilise une technologie de connexion linéaire auto-étanche, telle que la technologie de soudage CMT.
l Les plateaux de batteries constitués de profilés en aluminium doivent être conçus avec une ou plusieurs couches continues de colloïde d'étanchéité.
l Dans le cas d'une plaque de refroidissement liquide intégrée dans le boîtier inférieur, il est nécessaire d'envisager l'utilisation de joints colloïdaux ou de technologies de connexion linéaire auto-obturantes, telles que la technologie de soudage par friction-malaxage FSW.
l L'interface d'étanchéité entre le couvercle supérieur et le corps inférieur du boîtier doit être dotée d'une surface adaptée pour répondre aux exigences d'étanchéité « uniforme » et « continue ». Si nécessaire, l'interface d'étanchéité doit être usinée et polie.
Figure 3 : Formes d'étanchéité courantes entre le couvercle supérieur et le boîtier inférieur
Habituellement, le couvercle supérieur et le boîtier inférieur du boîtier de stockage d'énergie adoptent une conception à bride courbée et à joint d'étanchéité, comme illustré dans la figure 2. Le couvercle supérieur, le corps du boîtier inférieur et le joint d'étanchéité sont entièrement compactés et couplés par des boulons de fixation pour garantir que le boîtier de stockage d'énergie répond aux exigences pertinentes de l'IP67.
3- Conception d'étanchéité des interfaces électriques et de communication et de l'interface d'installation du panneau avant du boîtier inférieur
Le panneau avant du boîtier (comme illustré dans la figure 3) est usiné avec des trous sur le profil extrudé pour l'installation d'interfaces électriques et de communication afin de réaliser des fonctions telles que la transmission de courant, l'interaction de communication et le contrôle de sécurité.
Figure 4 : Interface électrique, interface de communication et interface d'installation du panneau avant de l'armoire inférieure
L'étanchéité à l'air de l'interface d'installation entre le boîtier et les interfaces électriques, de communication et autres doit suivre les principes suivants :
l La forme de l’interface est conçue pour être profilée afin de réduire la possibilité d’accumulation et de pénétration de gaz et de liquide à l’interface.
l L'alignement précis évite les écarts causés par un mauvais alignement des interfaces lors de l'installation.
l Pré-sceller l'interface avant l'installation et ajouter des tampons anti-vibrations ou des produits d'étanchéité pour améliorer l'effet d'étanchéité initial ou réduire les défaillances d'étanchéité causées par les vibrations.
De plus, en termes de sélection des fixations, des fixations à haute résistance et à couple élevé sont utilisées et elles sont serrées plusieurs fois pendant le processus d'installation pour assurer l'étanchéité de l'interface. Par exemple, si un écrou à souder bout à bout est utilisé, sa caractéristique est qu'il peut être directement connecté au trou de paroi de la partie connectée (le panneau avant du boîtier) pour le soudage bout à bout. Cette conception structurelle peut améliorer considérablement l'étanchéité à l'air de la partie de connexion.
Figure 5 : Utilisation d'écrous soudés bout à bout pour augmenter l'étanchéité à l'air
4-Choix des joints d'étanchéité
La conception et la sélection des joints sont essentielles car elles affectent directement la fiabilité et la durée de vie du système. Voici les facteurs clés à prendre en compte lors de la conception et de la sélection des joints pour les systèmes de refroidissement liquide de stockage d'énergie :
l Le matériau d'étanchéité doit avoir une certaine compatibilité chimique et de pression et être capable de résister à la plage de températures de fonctionnement du système, y compris les environnements à haute et basse température. Le choix du matériau du joint dépend de l'environnement d'utilisation et des exigences de durée de vie. Les matériaux d'étanchéité courants comprennent le caoutchouc, le polytétrafluoroéthylène (PTFE), le nylon, le métal, etc.
l Absence de fuite : le joint doit pouvoir s'adapter à la légère déformation qui peut survenir dans le système pendant le fonctionnement afin de garantir une bonne étanchéité dans diverses conditions de travail. En général, la déformation du joint doit être supérieure à 30 % et inférieure à 60 %, et la pression de l'interface d'étanchéité doit être supérieure à 30 kPa.
Nous mettrons régulièrement à jour les informations et technologies relatives à la conception thermique et à l’allègement. Merci de votre intérêt pour Walmate.
SIMULATION FLUIDE
Utilisation de logiciels de simulation pour analyser les performances thermiques des radiateurs et des plaques froides
Scénario d'application
Conditions de fonctionnement: Scénario à haute densité de flux thermique
Installation et disposition: Installation sur un seul côté
Application typique: Personnalisation client
Caractéristique : Bonne dissipation thermique
Scénario d'application:0.5-1C
Installation et disposition: Refroidissement liquide par le bas
Application typique: 36s, 48s, 52s, 104s
Caractéristique : Bonne efficacité de refroidissement
Le réfrigérant, à travers un évaporateur, libère la chaleur qui doit être absorbée par les plaques froides de la batterie, puis l'électricité générée par le fonctionnement de la pompe à eau est envoyée vers les plaques froides pour absorber la chaleur produite par l'équipement.
La technologie de refroidissement liquide utilise un liquide comme milieu pour l'échange thermique. Comparé à l'air, le liquide a une plus grande capacité thermique et une résistance à l'écoulement plus faible, ce qui permet une dissipation de chaleur plus rapide et une efficacité de refroidissement plus élevée. De plus, les systèmes de refroidissement liquide n'exigent pas la conception de conduits d'air, réduisant ainsi le besoin de composants mécaniques tels que les ventilateurs. Cela entraîne des taux de panne plus faibles, moins de bruit et une solution plus respectueuse de l'environnement. La nature économe en espace du refroidissement liquide le rend particulièrement adapté aux grandes centrales de stockage d'énergie de plus de MW, et il est largement utilisé dans des scénarios nécessitant une densité énergétique élevée des batteries et des vitesses de charge-décharge rapides.
Les systèmes de stockage d'énergie par batterie (BESS) utilisent des batteries comme moyen de stockage de l'énergie. Contrairement aux combustibles fossiles traditionnels, les systèmes de stockage d'énergie par batterie peuvent stocker des sources d'énergie renouvelables telles que l'énergie solaire et éolienne, et les libérer lorsqu'il est nécessaire d'équilibrer l'offre et la demande d'énergie.
SUGGESTIONS D'OPTIMISATION DE LA DFM
Help reduce potential errors and defects throughout the production process, ensuring that the product meets the quality standards required by the design.
Scénario d'application
Conditions de fonctionnement: Scénario à haute densité de flux thermique
Installation et disposition: Installation sur un seul côté
Application typique: Personnalisation client
Caractéristique : Bonne dissipation thermique
Scénario d'application:0.5-1C
Installation et disposition: Refroidissement liquide par le bas
Application typique: 36s, 48s, 52s, 104s
Caractéristique : Bonne efficacité de refroidissement
À mesure que les systèmes de stockage d'énergie évoluent vers une plus grande capacité et une densité énergétique plus élevée, la conception de la taille et de la compatibilité des Boîtier de bloc de batterie de stockage d'énergie sont devenues des problèmes essentiels pour améliorer l'efficacité et la fiabilité du système. Cet article combine les derniers cas de conception technique, les technologies brevetées et les tendances de l'industrie pour mener une analyse à partir de trois dimensions : l'utilisation de l'espace, la compatibilité modulaire et la conception de l'agencement et du support des cellules de batterie.
1- Optimiser l'utilisation de l'espace
L’amélioration de l’utilisation spatiale des systèmes intégrés de stockage d’énergie est essentiellement une démarche à double sens, issue de l’itération technologique et des exigences du scénario. Grâce à l’innovation collaborative de technologies telles que les cellules de batterie de grande capacité, l’architecture modulaire et l’intégration du refroidissement liquide, l’industrie passe de « l’empilement extensif » à la « réutilisation spatiale extrême ».
a. Application de cellules de batterie de grande capacité : augmentation de la densité énergétique et de l'efficacité
Résumé des idées : L'essence de l'application de cellules de batterie de grande capacité est de réduire les niveaux structurels internes du bloc-batterie et d'améliorer directement l'utilisation de l'espace des cellules de batterie au bloc-batterie. Les packs de batteries traditionnels adoptent un mode d'intégration à trois niveaux « cellule de batterie → module → pack de batteries », et la structure du module (poutres transversales, poutres longitudinales, boulons, etc.) conduit à une faible utilisation de l'espace. Les cellules de batterie de grande capacité peuvent ignorer le niveau du module en allongeant ou en augmentant le volume de la cellule unique et utiliser la technologie CTP (Cell to Pack) pour intégrer les cellules de batterie directement dans le pack de batteries.
Noyau technique : utiliser des cellules de batterie ultra-larges de 600 Ah+ pour réduire le nombre de cellules de batterie et de points de connexion, et augmenter la capacité de chaque cellule.
b. Réutilisation spatiale et optimisation des coûts : de « l'empilement de composants » à la « réutilisation multidimensionnelle »
Résumé des idées : La réutilisation spatiale et l’optimisation des coûts sont les deux faces d’une même pièce, et la logique sous-jacente est de briser les limites physiques et financières des systèmes de stockage d’énergie traditionnels grâce à la simplification structurelle, l’intégration fonctionnelle, l’itération matérielle et la conception standardisée.
Le cœur de la réutilisation spatiale est de réduire les liens intermédiaires en simplifiant à l’extrême la hiérarchie structurelle. Par exemple : Conception de boîtier haute tension deux en un : la technologie brevetée de Jiangsu Trina Energy Storage combine deux boîtiers haute tension en un seul, partageant l'ensemble des relais positifs/négatifs et des connexions électriques, réduisant ainsi de 30 % l'espace horizontal occupé et réduisant de 15 % le coût des composants électriques.
Réutilisation inter-domaines des modules fonctionnels, intégration des pièces structurelles et des canaux de dissipation thermique, comme l'intégration de la plaque de refroidissement liquide avec la plaque inférieure du boîtier, et le partage de l'espace entre le tuyau de refroidissement liquide et le support structurel, réduisant ainsi de 15 % les composants de dissipation thermique indépendants ; le corps de la cellule de batterie en tant que pièce structurelle : la batterie BYD Blade offre une résistance de support grâce à des parois latérales de cellule de batterie longues et fines, éliminant le cadre du module et augmentant l'utilisation de l'espace à 60 %-80 %.
L'optimisation approfondie de la topologie électrique, telle que la topologie en cascade haute tension, qui réduit le nombre de circuits parallèles en augmentant la capacité et le niveau de tension des cellules individuelles (comme le stockage d'énergie à chaîne intelligente de Huawei), réduit l'espace physique de la pile de batteries de 20 % et raccourcit le temps de réponse du système de 50 %. ; Conception de relais partagé, le boîtier haute tension deux-en-un de Jiangsu Trina Energy Storage permet à deux lignes de partager le même relais, réduisant ainsi le nombre de relais et la longueur du câble de 50 % et améliorant l'efficacité de l'installation de 30 %
2-Disposition des cellules de batterie et conception du support : équilibre entre la capacité de charge, la dissipation thermique et la résistance aux vibrations
L’essence de l’agencement cellulaire est un jeu entre l’utilisation de l’espace, la distribution de la chaleur et la stabilité mécanique. La forme physique et la direction de disposition de la cellule affectent directement l'efficacité de remplissage de l'espace :
a. Optimiser la disposition des cellules de la batterie
Conception de cellule de batterie inversée : la soupape antidéflagrante de la cellule de batterie est pointée vers le bas de sorte que l'échappement d'emballement thermique et l'espace anti-balle inférieur sont partagés, libérant ainsi l'espace de hauteur de la cellule de batterie et atteignant un taux d'utilisation du volume.
Disposition des cellules couchées : optimise l'utilisation de l'espace dans le sens de la hauteur du bloc-batterie, augmente la proportion de matériaux actifs et permet une utilisation du volume nettement supérieure à celle des cellules verticales.
Cellules de batterie ultra-longues et fines : Le nombre de cellules de batterie par unité de volume est réduit grâce à la conception allongée et amincies des cellules de batterie, améliorant ainsi l'efficacité du regroupement.
b. Conception de couplage de la dissipation thermique et de la portance : vise à obtenir une double optimisation de la dissipation thermique efficace et de la résistance structurelle grâce à l'innovation collaborative de la structure, des matériaux et des processus.
Parcours de conception structurelle :
Structure intégrée, telle que la conception conforme de la plaque de refroidissement liquide et de la poutre de support : intégration du canal de refroidissement liquide dans la poutre de support en alliage d'aluminium, réduisant les composants indépendants et améliorant l'utilisation de l'espace ;
Disposition en couches et compartimentée, empilant le bloc-batterie, le système de refroidissement liquide et le BMS en couches pour réduire l'interférence mutuelle entre le flux de chaleur et les contraintes mécaniques ;
Optimisation mécanique bionique, telle que la structure en nid d'abeille/ondulée, la conception d'une couche centrale en nid d'abeille ou ondulée dans le cadre de support en alliage d'aluminium (comme la solution brevetée de Mufeng.com), absorbant l'énergie de vibration par déformation tout en optimisant le chemin de dissipation thermique.
Parcours d'innovation matérielle :
Conductivité thermique et intégration porteuse, tels que les matériaux composites en fibres d'alliage d'aluminium (conductivité thermique ≥ 200 W/m·K, résistance +30 %) ; matériaux intelligents, la couche de remplissage à changement de phase (PCM) absorbe la chaleur et la libère lentement, avec une différence de température de ±1,5℃ ; Amortissement léger : la couche de coussin en silicone élastique absorbe les vibrations (amortissement +40%).
Chemin de mise en œuvre du processus :
Procédés de formage de précision, tels que le formage par extrusion : utilisés pour fabriquer des poutres refroidies par liquide en alliage d'aluminium avec des canaux d'écoulement complexes ;
Technologie de traitement de surface, telle que la génération d'une couche d'oxyde céramique sur la surface de l'alliage d'aluminium pour améliorer la résistance à la corrosion (test au brouillard salin ≥ 1000h) et améliorer l'efficacité de la dissipation thermique (émissivité de surface augmentée de 20%) ;
Processus d'assemblage intelligent et réglage dynamique de la précharge, comme l'intégration de capteurs de pression et d'actionneurs électriques pour ajuster la précharge des boulons (5-20 kN) en temps réel afin d'éviter d'endommager les cellules de la batterie par surpression.
c. Conception coordonnée de la résistance à la charge et aux vibrations de la structure de support : Le système de support doit répondre à la double exigence de résistance à la charge statique (poids des cellules de batterie + pression d'empilement) et de résistance aux vibrations dynamiques (impact du transport/sismique).
3- Modularité et compatibilité : interfaces standardisées et architecture évolutive
L’essence de l’utilisation d’une interface standardisée pour s’adapter aux cellules de batterie de tailles multiples est de parvenir à une extension flexible des spécifications des cellules de batterie sur une plate-forme unifiée grâce à l’innovation collaborative dans la gestion mécanique, électrique et thermique. La technologie actuelle est passée de la compatibilité statique à l’ajustement dynamique et évoluera vers l’intelligence, la légèreté et l’intégration inter-scénarios à l’avenir.
a. Innovation collaborative de structure mécanique :
Normalisation des interfaces mécaniques : définition de dimensions uniformes des dispositifs de connexion.
Conception modulaire de packs de batteries/armoires : des modules évolutifs et des armoires de batteries sont construits à partir d'unités de batteries standardisées (telles que des cellules de 280 Ah et 314 Ah) pour prendre en charge des combinaisons flexibles avec différentes exigences de capacité.
Figure 1-Boîtier de bloc de batterie de stockage d'énergie 280Ah
b. Réglage dynamique du système électrique
Protocoles et interfaces de communication standardisés, tels que la compatibilité BMS : formuler un protocole de communication BMS (système de gestion de batterie) unifié pour prendre en charge une connexion transparente avec les PCS et les cellules de batterie de différents fabricants ; régulation dynamique de la puissance, grâce au contrôle de l'inertie virtuelle et à l'algorithme d'optimisation multi-échelle de temps, pour obtenir un ajustement en temps réel de la puissance active/réactive ; et une conception adaptative de correspondance des paramètres électriques.
c. Adaptation intelligente du système de gestion thermique
Solutions de gestion thermique hiérarchique, telles que l'utilisation de mousse ignifuge à haute résilience, d'adhésif thermoconducteur et d'autres matériaux au niveau cellulaire pour équilibrer les exigences d'isolation et de dissipation thermique et inhiber la diffusion de chaleur ; la conception intégrée de la plaque de refroidissement liquide intégrée au niveau du module et de la couche d'isolation thermique pour améliorer la durée de vie du cycle ; Le système ajuste dynamiquement la capacité de refroidissement au niveau du système grâce à des compresseurs à fréquence variable et à plusieurs branches de réfrigération.
Surveillance et prédiction intelligentes, fusion multi-capteurs. Des capteurs de température sont placés à des endroits clés tels que les pôles des cellules de batterie et les grandes surfaces pour obtenir une acquisition de température de haute précision ; La technologie des jumeaux numériques optimise les stratégies de dissipation thermique en temps réel grâce à la surveillance du cloud et à la maintenance prédictive.
4- Conclusion
L’optimisation de l’espace des Boîtier de bloc de batterie de stockage d'énergie est passée d’une simple amélioration structurelle à une innovation collaborative multidimensionnelle :
La fusion du matériau, de la structure et de l'algorithme, comme la combinaison de la boîte en fibre de carbone + de la technologie CTP + de l'algorithme de disposition de l'IA, deviendra le courant dominant.
La modularisation et la standardisation s'accélèrent, et la conception standardisée avec Pack comme plus petite unité fonctionnelle incitera l'industrie à réduire les coûts et à augmenter l'efficacité.
La gestion thermique et l’utilisation de l’espace sont profondément intégrées, et les technologies de refroidissement liquide par immersion et de contrôle dynamique de la température libèrent davantage le potentiel de l’espace.
Nous mettrons régulièrement à jour les informations et technologies relatives à la conception thermique et à l’allègement. Merci de votre intérêt pour Walmate.
Avec la croissance explosive de la puissance de calcul de l'IA et l'augmentation continue de la densité de puissance des centres de données, la technologie traditionnelle de refroidissement par air ne peut plus répondre aux besoins de dissipation thermique. La technologie de refroidissement liquide est devenue incontournable en raison de ses avantages tels que la dissipation efficace de la chaleur, les économies d'énergie et la réduction de la consommation. Dans la technologie du refroidissement liquide, la concurrence entre la plaque froide et l’immersion est particulièrement féroce. Cet article analysera les avantages et les inconvénients des deux du point de vue des caractéristiques techniques, des scénarios d’application, de la rentabilité et des tendances futures, et explorera leurs futures directions dominantes.
1- Comparaison des caractéristiques techniques : le type à plaque froide a une forte compatibilité, le type à immersion a une efficacité de dissipation thermique plus élevée
un. Refroidissement liquide par plaque froide : une « amélioration » de la transition en douceur
Forte compatibilité : aucune modification majeure de la structure du serveur n'est requise et il est compatible avec l'infrastructure des centres de données refroidis par air existants, avec de faibles coûts de transformation et des cycles courts.
Haute sécurité : le liquide de refroidissement n'entre pas en contact direct avec les composants électroniques, le risque de fuite est donc faible et le risque peut être encore réduit grâce à une conception modulaire (comme des connecteurs à changement rapide et des tuyaux redondants).
Haute maturité : la technologie des plaques froides a été largement utilisée dans des scénarios tels que les projets de coopération Alibaba Cloud Qiandao Lake Data Center et Intel, représentant 90 % du marché actuel du refroidissement liquide.
Limitations : Le type de plaque froide ne peut couvrir que certains composants haute puissance (tels que le processeur, le GPU), et la chaleur restante doit toujours s'appuyer sur le refroidissement par air pour aider à la dissipation de la chaleur. La valeur PUE est généralement de 1,1 à 1,2, légèrement supérieure à celle du type d'immersion.
b. Refroidissement liquide par immersion : une approche innovante pour une dissipation thermique efficace
Le refroidissement liquide par immersion immerge complètement le serveur dans un liquide de refroidissement isolant, permettant ainsi la dissipation de la chaleur de tous les composants par contact direct. Ses principaux avantages incluent :
Efficacité énergétique extrême : la conductivité thermique du liquide est 20 à 30 fois supérieure à celle de l'air, le PUE peut être aussi bas que 1,05 et l'efficacité de dissipation thermique est améliorée de plus de 3 fois.
Gain de place : le volume du système de refroidissement ne représente que 1/3 de celui du refroidissement par air, et la densité de puissance d'une seule armoire peut atteindre plus de 50 kW, ce qui convient aux scénarios à haute densité tels que le supercalcul IA.
Silencieux et respectueux de l'environnement : aucun ventilateur n'est nécessaire, le bruit est réduit de plus de 90 % et il n'y a pas de pollution par la poussière, ce qui prolonge la durée de vie de l'équipement.
Défis : L'immersion nécessite des serveurs personnalisés, le coût du liquide de refroidissement représente jusqu'à 60 % (comme le liquide fluoré), l'investissement initial est élevé et la compatibilité écologique doit être améliorée.
2-Différenciation des scénarios d'application : le type de plaque froide à moyen et court terme domine, le potentiel de type immersion à long terme est libéré
un. Type de plaque froide : le choix le plus rentable pour la rénovation d'IDC existants et la construction de nouveaux IDC
Rénovation d'anciens centres de données : Le type de plaque froide peut être rapidement adapté à l'architecture de refroidissement par air existante, avec un cycle de rénovation court et des coûts contrôlables. Par exemple, la solution modulaire sur laquelle Intel et Bich ont collaboré réduit la difficulté de déploiement grâce à une conception de plaque froide standardisée.
Scénarios de calcul à moyenne et haute densité : le type de plaque froide prend déjà en charge une puissance de 130 à 250 kW par armoire (comme les GPU NVIDIA série B), répondant à la plupart des besoins de formation en IA.
b. Immersion : la solution ultime pour le supercalcul et les centres de données écologiques
Puissance de calcul ultra-haute densité : la puissance des puces de nouvelle génération (comme la série Rubin de NVIDIA) dépassera 1 000 kW, et l'immersion deviendra la seule solution envisageable.
Besoins d'économie d'énergie verte : le PUE d'immersion est proche de 1,05 et l'efficacité de récupération de chaleur perdue atteint 90 % (comme la solution de Lenovo), ce qui est conforme à la politique cible « double carbone ».
c. Situation actuelle du marché
Le type de plaque froide domine le marché actuel : en 2025, le type de plaque froide représentera 80 à 90 % du marché du refroidissement liquide, et le type à immersion représentera moins de 10 %. De plus, des interfaces standardisées ont été formées (comme la conception de plaque froide OCP d'Intel) et les solutions de fabricants tels qu'Inspur et Sugon sont hautement compatibles. Le projet national « East Data West Computing » exige que le PUE des centres de données nouvellement construits soit ≤ 1,25 et que le type de plaque froide devienne le premier choix pour la transition.
L'immersion est prête à démarrer : la solution d'immersion à changement de phase C8000 de Sugon Digital atteint un PUE de 1,04, et le centre de données « Kirin » d'Alibaba Cloud vérifie la faisabilité de l'immersion monophasée. Les puces haute puissance telles que le GPU NVIDIA B200 (1 000 W+) ont favorisé l'utilisation de la technologie d'immersion, augmentant la densité de puissance de calcul du refroidissement liquide de 30 à 50 %. L’UE prévoit d’interdire les liquides fluorés en 2028, et la recherche et le développement de liquides de refroidissement à base d’hydrocarbures/huiles de silicone nationaux se sont accélérés (comme la série « Kunlun » de Sinopec).
3-Avis faisant autorité PK
Refroidissement liquide par plaque froide : Le refroidissement liquide par plaque froide est le « brise-glace » pour la popularisation du refroidissement liquide. Au cours des cinq prochaines années, il représentera encore 80 % du marché du refroidissement liquide incrémental. Le refroidissement liquide par immersion doit attendre que la consommation d'énergie de la puce franchisse le point critique.
Faction de refroidissement liquide par immersion : Le refroidissement liquide par immersion à changement de phase est la forme ultime de refroidissement liquide, et le refroidissement liquide par plaque froide n'est qu'une solution transitoire. Lorsque la consommation électrique d'une seule puce dépasse 800 W, le refroidissement liquide par immersion devient la seule option.
Neutres : La différenciation des voies techniques reflète la stratification de la demande de puissance de calcul. Les plaques froides servent à « l'informatique orientale » et le refroidissement liquide par immersion soutient « l'informatique occidentale ». Le développement parallèle à double voie sera le thème principal de la prochaine décennie.
4-Opportunités et stratégies industrielles
Jeu coût et écologie : le refroidissement liquide par plaque froide aura le dessus à court terme, tandis que le refroidissement liquide par immersion doit réduire les coûts pour sortir de l'impasse.
Refroidissement liquide par plaque froide : optimiser les matériaux (composite cuivre-aluminium), améliorer la précision du traitement (processus anti-fuite) et promouvoir une conception modulaire et standardisée.
Refroidissement par liquide par immersion : développer des liquides de refroidissement rentables (tels que le liquide d'immersion monophasé), des armoires compatibles et coopérer avec les fabricants de puces pour personnaliser les solutions de refroidissement.
Réserves technologiques : Explorez les plaques froides à flux diphasique et les systèmes de surveillance intelligents (tels que la régulation dynamique du flux par IA) pour faire face aux futures demandes de puissance élevées.
5- Conclusion
Court terme (2025-2027) : Le refroidissement liquide par plaque froide domine les scénarios généraux, et le taux de pénétration du refroidissement liquide par immersion augmente à 15-20 % ; À long terme (2030+) : le refroidissement liquide par immersion à changement de phase devient courant dans le domaine de la puissance de calcul élevée, et le refroidissement liquide par plaque froide se retire sur le marché de la densité moyenne et faible.
Les facteurs déterminants sont : le coût du liquide de refroidissement, la vitesse d’augmentation de la consommation d’énergie des puces et les politiques internationales de protection de l’environnement.
Nous mettrons régulièrement à jour les informations et technologies relatives à la conception thermique et à l’allègement. Merci de votre intérêt pour Walmate.
Avec le développement rapide des véhicules à énergies nouvelles et des industries du stockage d'énergie, la légèreté, la sécurité élevée et une gestion thermique efficace sont devenues des exigences essentielles. Notre entreprise est fortement impliquée dans le domaine de la transformation des alliages d'aluminium. Grâce à une sélection de matériaux, des procédés de formage et des technologies de soudage de pointe, nous nous concentrons sur la recherche, le développement et la fabrication plateau de batterie, de Plaque Froide Liquide, de boîtiers de stockage d'énergie et de radiateurs. L'alliage d'aluminium est devenu un choix idéal pour la légèreté et la gestion thermique des équipements à énergies nouvelles grâce à sa faible densité (environ 2,7 g/cm³), sa grande solidité, sa résistance à la corrosion et son excellente conductivité thermique (environ 150-220 W/m·K).
1- Sélection des alliages d'aluminium et considérations clés
Les exigences de performance des alliages d'aluminium varient considérablement selon les produits. Il est donc nécessaire de combiner la résistance mécanique, la résistance à la corrosion, la soudabilité et l'adaptabilité des procédés pour une sélection complète des matériaux :
a. Plateau de batterie
Nuances courantes : 6061-T6, 6005A-T6, 6063-T6.
Critères de sélection :
·Doit présenter une résistance à la traction ≥ 240 MPa (par exemple, 6061-T6) pour satisfaire aux normes nationales d'extrusion, de chute et d'impact de bille ;
·Exigences de soudabilité élevées, les fissures thermiques doivent être évitées (la série 6xxx renforcée au magnésium/si est privilégiée) ;
·La résistance à la corrosion est améliorée par anodisation ou placage aluminium.
Figure 1 - Plateau de batterie en alliage d'aluminium
b. Boîtier de stockage d'énergie
Marques courantes : 5083, 6061-T6 (résistance mécanique et résistance à la corrosion).
Critères de sélection :
· Résistance aux vibrations et aux chocs, limite d'élasticité ≥ 200 MPa ;
· Traitement de surface rigoureux pour éviter la corrosion électrochimique.
c. Plaque Froide Liquide
Marques courantes : 3003, 6061/6063, 6082.
Critères de sélection :
· Conductivité thermique et résistance à la corrosion élevées ;
· Le canal de refroidissement liquide nécessite un moulage complexe, et la série 6xxx, offrant d'excellentes performances d'extrusion, est privilégiée.
2- Différences de performances et difficultés d'usinage
L'usinage des alliages d'aluminium doit s'adapter à leurs propriétés physiques, notamment en découpe, CNC, soudage et traitement de surface :
a. Découpe et usinage CNC
Difficultés :
· L'usinage de trous de haute précision est sujet aux bavures et aux déformations (comme des saillies sur le bord des trous étagés) en raison de la ductilité du matériau ;
· Les structures à parois minces (comme les canaux d'écoulement des plaques de refroidissement liquide) nécessitent un contrôle des forces de coupe pour éviter le gauchissement.
Solution :
· Utiliser des outils diamantés pour améliorer la netteté des arêtes et réduire la déformation par extrusion ;
· Optimiser les paramètres d'usinage (tels que la vitesse élevée et l'avance lente) et coopérer avec les équipements CNC généraux pour obtenir un usinage stable.
b. Procédé de soudage
Principaux défis :
· Le film d'oxyde (point de fusion Al₂O₃ : 2050 °C) entrave la fusion et favorise la formation de pores et d'inclusions de scories ; · Certains alliages présentent une forte tendance aux fissures à chaud, et l'énergie de la ligne et la composition du fil de soudage doivent être contrôlées.
Procédés privilégiés :
·Soudage TIG (alimentation CA) : adapté aux tôles fines, le film d'oxyde est éliminé par « nettoyage cathodique » ;
·Soudage MIG (mélange de gaz à courant élevé + hélium) : rendement de soudage élevé pour les tôles épaisses et apport de chaleur contrôlable.
Figure 2- Soudage du plateau de batterie
c. Traitement de surface
·Revêtement isolant résistant à la pression : appliqué sur le plateau de batterie et àboîtier de stockage d’énergie, il doit réussir le test de pression (≥ 3 000 V CC/1 min). L’épaisseur du revêtement est de 20 à 50 µm, afin de garantir la sécurité de l’isolation dans un environnement haute tension.
·Revêtement isolant et déshumidifiant : pour le boîtier de stockage d’énergie, des matériaux hydrophobes (tels que la résine fluorocarbonée) sont utilisés pour réduire le risque de condensation interne, et la valeur dyne est ≥ 34 pour garantir l’adhérence.
·Revêtement anti-collision : utilisé pour la paroi extérieure du support de batterie, un élastomère de polyuréthane (dureté ≥ 80 Shore A) a été sélectionné, offrant une résistance aux chocs améliorée de plus de 30 %.
·Anodisation : traitement anticorrosion conventionnel, erreur d’épaisseur du film ≤ 3 µm, adapté aux structures complexes.
3- Inspection de vérification et adaptabilité des équipements
Afin de répondre aux normes du secteur des nouvelles énergies (telles que GB/T31467.3, UL2580), une vérification multidimensionnelle et une adaptation des procédés sont nécessaires :
a. Inspection de vérification
· Résistance structurelle : Vérification des performances de portance, d’extrusion et de résistance aux impacts de billes du plateau par simulation par éléments finis (contrainte maximale ≤ limite d’élasticité du matériau) ;
· Test d’étanchéité : Le système de refroidissement liquide utilise la détection de fuites à l’hélium (taux de fuite ≤ 1 × 10⁻⁶ mbar·L/s) et un test de pression cyclique (0,5-1,5 MPa/5 000 fois) ;
· Vérification des performances du revêtement :
Test de tenue à la tension du revêtement isolant (5 000 V CC/60 s sans claquage) ;
Le revêtement anticollision a passé avec succès l’essai de chute de billes (bille d’acier de 1 kg à 1 m de hauteur) et le test au brouillard salin (1 000 heures sans décollement).
b. Optimisation de l'adaptabilité des équipements
· Transformation d'équipements CNC généraux : Grâce à la conception de dispositifs de haute précision et à un algorithme de compensation dynamique, la déformation par usinage des pièces à parois minces peut être inférieure ou égale à 0,1 mm ;
· Bibliothèque de paramètres de soudage : Définition de paramètres de soudage standard (tels que le courant et la vitesse d'alimentation du fil) pour différentes nuances d'alliages d'aluminium afin de réduire le cycle de mise au point ;
· Projection automatisée du revêtement : Grâce à la projection robotisée multiaxes, combinée à la technologie de durcissement infrarouge, l'erreur d'uniformité du revêtement est inférieure ou égale à 5 %.
Conclusion
La large application des alliages d'aluminium dans les nouveaux équipements énergétiques est non seulement une victoire de la science des matériaux, mais aussi une manifestation d'innovation en matière de procédés. Notre entreprise continuera d'explorer de nouveaux alliages d'aluminium à haute résistance, résistants à la corrosion et faciles à usiner, et de promouvoir l'amélioration des performances de produits tels que les plateau de batterie et les Plaque Froide Liquide grâce à l'innovation en matière de procédés, contribuant ainsi à la transition de l'industrie vers un avenir plus efficace et plus léger.
Nous mettrons régulièrement à jour les informations et technologies relatives à la conception thermique et à l’allègement. Merci de votre intérêt pour Walmate.
Face à l'augmentation constante de la densité de puissance des appareils électroniques, la conception de la dissipation thermique est devenue un élément clé de la fiabilité et de la durée de vie des systèmes. Forts de 19 ans d'expérience en gestion thermique, nous combinons des cas d'ingénierie classiques avec une expérience en simulation multiphysique sur le terrain pour analyser en profondeur les cinq principales erreurs techniques souvent négligées par les ingénieurs dans les scénarios haute puissance, et proposer des solutions conformes aux pratiques du secteur.
Malentendu 1 : abus de matériaux à haute conductivité thermique, écart de calcul de la résistance thermique de l'interface
Problème typique : recherche excessive des valeurs théoriques des matériaux conducteurs thermiques, ignorant la réalité technique de la résistance thermique des contacts d'interface.
Analyse de cas : Un module de dissipation thermique pour radar laser automobile utilise un substrat en cuivre pur (conductivité thermique de 401 W/m·K), mais l'épaisseur du revêtement du matériau d'interface thermique (TIM) n'est pas contrôlée avec précision (conçue à 0,1 mm, fluctuation réelle de ± 0,05 mm), et la résistance thermique de contact mesurée atteint 0,6 °C·cm²/W, ce qui entraîne un dépassement de 22 % de la température de jonction du FPGA par rapport à la norme. Après le passage à des tampons thermiques préformés (tolérance ± 0,02 mm, résistance thermique < 0,03 °C·cm²/W) et la combinaison avec le procédé de frittage sous vide, la température de jonction est réduite de 17 °C et le MTBF (temps moyen entre pannes) est porté à 100 000 heures.
Plan d'optimisation :
Sélection des matériaux : Conformément à la norme ASTM D5470, la résistance thermique des TIM est mesurée, et les matériaux à changement de phase ou les élastomères chargés de métal sont privilégiés.
Contrôle du procédé : Utilisation d'un équipement de distribution automatique (précision ± 3 %) pour garantir une tolérance d'épaisseur < 10 % et éviter les entrefers.
Malentendu 2 : Inadéquation de l'organisation du flux d'air dans le système de refroidissement par air, points chauds locaux hors de contrôle
Problème typique : empiler aveuglément le nombre de ventilateurs, en ignorant l'adaptation d'impédance du canal d'écoulement et l'effet de séparation de la couche limite.
Exemple d'ingénierie : Un cluster de GPU pour centre de données utilise 4 ventilateurs 12038 (volume d'air de 200 pi³/min). Cependant, en raison d'une conception incorrecte de l'angle de guidage d'air (coude à angle droit de 90°), le volume d'air effectif réel n'est que de 65 % de la valeur nominale et l'écart de température local atteint 40 °C. Après optimisation par simulation CFD, le guidage d'air est remplacé par un canal d'écoulement à expansion progressive (angle de diffusion < 7°) et une disposition des ailettes décalées est adoptée (le gradient d'espacement passe de 2 mm à 3,5 mm). La résistance globale au vent est réduite de 30 % et l'écart de température du point chaud est contrôlé à 8 °C. Stratégie principale :
Conception du champ d'écoulement : Des essais en soufflerie sont réalisés conformément à la norme ISO 5801 afin d'optimiser le rapport des surfaces d'entrée et de sortie (recommandé : 1:1,2).
Contrôle dynamique : D'après la courbe Q-H du ventilateur PWM, le point d'impédance du système est adapté à la plage d'efficacité la plus élevée (généralement 60 à 80 % du volume d'air maximal).
Malentendu 3 : L’échec de la conception respectueuse de l’environnement accélère le vieillissement des matériaux
Problème typique : se concentrer uniquement sur les performances initiales de dissipation thermique, en ignorant les effets des contraintes environnementales à long terme telles que l'humidité, la chaleur, la poussière et le brouillard salin.
Analyse de cas : Un convertisseur éolien offshore utilise un dissipateur thermique en alliage d’aluminium 6061 (anodisé en surface). Après six mois de fonctionnement en brouillard salin, la couche d’oxyde s’est détachée, entraînant une augmentation de 50 % de la résistance thermique de contact et une forte augmentation du taux de défaillance des IGBT. Le passage à l’alliage d’aluminium 5052 (résistance au brouillard salin > 1 000 h) et l’application d’une peinture polyuréthane triple résistance (épaisseur 50 μm, conforme à la norme CEI 60068-2-11) ont permis de réduire de 75 % le taux de défaillance sur trois ans. Points de conception :
Technologie de revêtement : Revêtement céramique Al₂O₃ par projection plasma (conductivité thermique : 30 W/m·K, résistance à la température : > 800 °C) utilisé pour les applications à haute température.
Étanchéité : Indice de protection IP69K (joint silicone double passage + soupape de surpression) pour garantir une étanchéité totale aux poussières et vapeurs d'eau.
Malentendu 4 : Absence de modélisation de la charge thermique transitoire et sélection inappropriée des matériaux à changement de phase
Problème typique : la solution de dissipation thermique conçue par simulation en régime permanent ne peut pas gérer des impulsions de puissance de l'ordre de la milliseconde.
Données mesurées : Un amplificateur de puissance à semi-conducteurs est soumis à une charge pulsée de 2 ms à 2 000 W dans une station de base 5G. L’élévation de température transitoire du substrat en aluminium traditionnel atteint 55 °C, tandis que le matériau à changement de phase à microcapsules (composite paraffine/graphène, chaleur latente de changement de phase de 220 J/g) associé à la simulation thermique transitoire (pas transitoire ANSYS Icepak de 1 ms) permet de contrôler l’élévation de température à 18 °C, conformément aux exigences de l’essai d’impact MIL-STD-810G.
Technologie de gestion dynamique :
Emballage à changement de phase : La structure en nid d’abeille est utilisée pour encapsuler le matériau à changement de phase (porosité > 70 %) afin d’éviter les fuites de liquide et d’améliorer l’efficacité de la diffusion de la chaleur.
Calibrage du modèle : Les conditions limites de simulation sont corrigées en fonction de l'imagerie thermique infrarouge (taux d'échantillonnage 100 Hz) et l'erreur est <±1,5 °C
Malentendu 5 : l'évaluation du TCO est unilatérale et ignore les coûts cachés d'exploitation et de maintenance
Problème typique : seul le coût initial du matériel est comparé et les pertes de consommation d'énergie/maintenance/temps d'arrêt ne sont pas quantifiées.
Comparaison des coûts : Une usine de semi-conducteurs utilisait initialement des armoires refroidies par air (coût initial de 500 000 yuans), avec une facture d’électricité annuelle de 1,2 million de yuans (PUE = 1,8). Après la mise à niveau vers un refroidissement liquide par immersion biphasé (coût initial de 1,8 million de yuans), la facture d’électricité annuelle est tombée à 450 000 yuans (PUE = 1,05). Grâce à la réduction de la charge de climatisation des salles blanches, les économies annuelles globales ont atteint 900 000 yuans, et l’investissement supplémentaire peut être amorti en 2,1 ans (TRI > 25 %).
Modèle de décision :
Modélisation affinée : Introduction d’une simulation de Monte-Carlo pour quantifier l’impact du taux de défaillance des équipements (distribution de Weibull) sur le coût total de possession. Superposition de politiques : combinées à des mécanismes de taxe carbone (tels que le CBAM de l'UE), les émissions de carbone des systèmes de refroidissement liquide sur l'ensemble de leur cycle de vie sont réduites de 60 %, et une subvention supplémentaire de 15 % est obtenue.
Conclusion : Faire évoluer le paradigme de conception thermique, passant d’une approche axée sur l’expérience à une approche axée sur les données.
Processus standardisé : Introduire la norme de test thermique JESD51-14 dès la phase de conception afin d’éviter toute reprise ultérieure (le cycle de projet d’un module optique est raccourci de 30 %).
Collaboration multidisciplinaire : Grâce au couplage COMSOL Multiphysics des pertes électromagnétiques (extraction HFSS) et du champ de contrainte thermique, l’efficacité de dissipation thermique d’un composant radar TR est améliorée de 40 %.
Exploitation et maintenance intelligentes : Déployer des capteurs de température à réseau de fibres (précision ± 0,1 °C) et des plateformes de jumeaux numériques pour prédire les pannes (les temps d’arrêt imprévus d’un centre de calcul intensif sont réduits de 90 %).
Grâce à une réflexion technique rigoureuse et à la vérification complète des données, les ingénieurs en conception thermique peuvent éviter avec précision les « tueurs invisibles » et poser les bases de systèmes hautement fiables. En tant que professionnels du secteur, nous nous engageons à fournir des solutions en boucle fermée, des matériaux aux systèmes, et à relever conjointement avec nos clients les défis de la gestion thermique.
Nous mettrons régulièrement à jour les informations et technologies relatives à la conception thermique et à l’allègement. Merci de votre intérêt pour Walmate.
1- Exigences de tolérance particulières pour les pièces clés
Dans la fabrication de plateaux de batterie EV et de boîtiers de batteries de stockage d'énergie à refroidissement liquide, le contrôle de tolérance des surfaces et interfaces de connexion clés affecte directement l'étanchéité, l'efficacité de la dissipation thermique et la précision de l'assemblage.
a. Surface d'installation de la plaque de refroidissement liquide
La plaque de refroidissement liquide est le composant principal du système de gestion thermique de la batterie. La planéité de sa surface d'installation influence directement l'étanchéité du canal de circulation du liquide de refroidissement. Une planéité hors tolérance peut entraîner une compression inégale du joint en silicone, provoquant des fuites locales ou une augmentation de la résistance thermique.
b. Désalignement des cordons de soudure
Le support de batterie utilise souvent une structure soudée en alliage d'aluminium. Un désalignement des cordons de soudure peut entraîner une concentration de contraintes et réduire la durée de vie en fatigue. En particulier pour les applications exigeant une étanchéité à l'air élevée pour les boîtiers de batteries (comme IP67), le désalignement doit être strictement contrôlé.
c. Trou de positionnement du module de batterie
Le trou de positionnement permet de fixer précisément le module de batterie. Une tolérance excessive peut entraîner un désalignement du module, ce qui peut entraîner une défaillance des connexions électriques ou des risques de vibrations mécaniques.
d. Position du trou de fixation
Le trou de fixation sert à fixer le boîtier de la batterie au châssis. Un écart de position peut entraîner des contraintes d'assemblage, voire la rupture des boulons.
e. Rectitude des bords du boîtier de la batterie
La rectitude des bords du boîtier de la batterie influence l'assemblage des couvercles supérieur et inférieur et le niveau de protection IP, en particulier pour les boîtiers soudés au laser, où le bord doit servir de référence pour le suivi de la tête laser.
2- Impact des tolérances dimensionnelles sur l'efficacité de la fabrication
L'impact des tolérances dimensionnelles sur l'efficacité de la fabrication se reflète principalement dans l'équilibre entre le flux de production, la maîtrise des coûts et la qualité du produit. Une conception avec des tolérances raisonnables permet non seulement de garantir la fonctionnalité du produit, mais aussi d'optimiser le rythme de production. L'impact d'un contrôle raisonnable des tolérances dimensionnelles sur l'efficacité de la fabrication se reflète principalement dans les aspects suivants :
a. Équilibre entre précision de fabrication et coût de production
· Bien qu'une tolérance dimensionnelle stricte puisse améliorer la précision de l'étanchéité et de l'assemblage, des équipements de fabrication de haute précision et des procédés complexes sont nécessaires, ce qui augmente considérablement les investissements et les délais de fabrication.
· Une recherche excessive de précision peut entraîner une augmentation des coûts de fabrication. Des tolérances strictes doivent être définies pour les pièces fonctionnelles clés, et les tolérances doivent être assouplies de manière appropriée dans les zones non critiques afin de réduire les coûts.
b. Contrôle du taux de reprise et du taux de rebut
· Une conception avec des tolérances raisonnables peut réduire les reprises dues aux écarts dimensionnels.
· La déformation par soudage est le principal problème dans la fabrication des bacs à batteries. L'utilisation du procédé de soudage à froid CMT permet d'optimiser l'apport de chaleur, de réduire la déformation après soudage et de raccourcir le cycle de reprise. c. Production modulaire et standardisée
· Grâce à des composants standardisés, les exigences de tolérance sont concentrées sur les pièces remplaçables localement, réduisant ainsi la difficulté globale de traitement.
· La conception à tolérances standardisées permet également la compatibilité multi-modèles et réduit le besoin de traitement personnalisé.
3- Normes industrielles et applications pratiques du contrôle de la planéité
Pour les bacs à batteries des véhicules à énergies nouvelles, les normes industrielles imposent des exigences strictes :
a. Norme de planéité : La planéité de la surface d’installation de la plaque de refroidissement liquide doit être ≤ 0,2 mm, celle de la plaque de support inférieure ≤ 0,5 mm/m² et l’erreur de planéité du cadre après soudage doit être ≤ 0,8 mm6.
b. Optimisation du processus de fabrication : L’usinage de précision CNC, le soudage à froid CMT et le traitement de vieillissement par vibration (VSR), combinés à la détection en ligne par interféromètre laser, réduisent le risque de déformation.
c. Sélection des matériaux : Il est recommandé d’utiliser des alliages d’aluminium à haute résistance tels que le 6061, avec une limite d’élasticité ≥ 1 180 MPa, en tenant compte à la fois de la légèreté et de la stabilité structurelle.
4- Stratégie d'ajustement des tolérances basée sur les matériaux et les procédés
a. L'innovation des matériaux favorise l'allègement
L'utilisation d'alliages d'aluminium légers à haute résistance (tels que le 6061) et de matériaux composites (matrice d'aluminium renforcée au carbure de silicium), associés à l'anodisation et à un revêtement isolant, permet d'obtenir une réduction de poids de 30 % et d'améliorer la résistance à la corrosion, tout en s'adaptant aux exigences de dissipation thermique des systèmes de refroidissement liquide.
b. La collaboration entre les procédés améliore la précision de fabrication
Le moulage par extrusion monobloc et le soudage par friction-malaxage (FSW) réduisent le nombre de soudures, tandis que le soudage à froid CMT et le soudage laser contrôlent la déformation thermique.
c. La détection par simulation en boucle fermée garantit la fiabilité
La simulation IAO optimise la disposition des nervures de renfort, tandis que le balayage laser et la technologie de détection des fuites d'hélium assurent une surveillance complète du processus. La conception modulaire est compatible avec une tolérance de ± 5 mm, réduisant ainsi les coûts et augmentant l'efficacité.
Nous mettrons régulièrement à jour les informations et technologies relatives à la conception thermique et à l’allègement. Merci de votre intérêt pour Walmate.
1- Caractéristiques du procédé de soudage des alliages d'aluminium des bacs à batteries et des boîtiers de stockage d'énergie
Dans la fabrication de nouveaux boîtiers à refroidissement liquide, de bacs à batteries et d'autres produits, les canaux de refroidissement liquide et les structures multi-cavités sont des caractéristiques de conception complexes typiques (voir la figure 1). Ces structures présentent souvent les caractéristiques suivantes :
Figure 1 : Conception typique d'un bac à batterie
Entrelacement spatial tridimensionnel : les canaux d'écoulement sont répartis en serpentin, avec un grand nombre de points de retournement spatiaux ;
Connexion multi-niveaux : la cavité principale et la sous-cavité sont reliées par des cloisons à parois minces (épaisseur 2-3 mm) ;
Caractéristiques de miniaturisation : petite section du canal d'écoulement (l'épaisseur minimale de la paroi du canal d'écoulement du profilé en aluminium est de 1,2 mm) et faible accessibilité au soudage.
2- Analyse des difficultés liées à la combinaison de plusieurs technologies de soudage dans la fabrication de bacs à batteries
Dans la fabrication de bacs à batteries, il est nécessaire de combiner plusieurs technologies de soudage, telles que l'application coordonnée du soudage par friction-malaxage (FSW), du soudage par transition métal froid (CMT), du soudage par fusion traditionnel (TIG/MIG) et d'autres technologies. Cette combinaison vise à prendre en compte la légèreté, la résistance, l'étanchéité et l'efficacité de la production, mais elle se heurte également aux principales difficultés suivantes :
a. Le problème de l'apport thermique coordonné de plusieurs procédés
Les différentes technologies de soudage (telles que le FSW et le soudage laser) présentent d'importantes différences d'apport thermique, ce qui peut facilement entraîner des variations de performances des matériaux et des déformations thermiques. Il faut donc optimiser la séquence de soudage et le réglage des paramètres.
b. Compatibilité des équipements et goulot d'étranglement en termes d'efficacité
La commutation des équipements est complexe et les exigences de précision en matière de synchronisation des paramètres sont élevées. La conception modulaire des postes de travail et des machines de soudage intelligentes sont nécessaires pour améliorer l'efficacité collaborative et réduire les temps de cycle.
c. Défis liés à l'équilibre entre résistance de l'étanchéité et coût
Le risque de fuite à l'intersection de plusieurs soudures est élevé (représentant 70 % des défauts), et une conception d'étanchéité redondante et d'optimisation de la topologie est nécessaire.
3- Pratique d'ingénierie : Coordination de plusieurs processus de soudage pour un bac à batteries et un boîtier de stockage d'énergie à refroidissement liquide
a. Planification de la position des traces de soudure
· Optimisation de la position de soudure : Lors de la conception du produit, la rationalité de la position de soudure doit être pleinement prise en compte afin d'éviter l'apparition de traces de soudure sur des pièces ou zones clés affectant les fonctions du produit. Par exemple, ajuster l'espace entre le cadre avant et la buse d'eau pour éviter toute interférence avec les traces de soudure ; optimiser la position de soudure de la buse d'eau pour réduire l'impact sur les performances du produit.
· Adaptation à la structure du produit : La position de soudure doit être adaptée à la structure du produit afin de garantir que la soudure puisse supporter diverses charges et contraintes lors de son utilisation. Par exemple, dans le projet de plaque de refroidissement liquide, la stabilité structurelle et la fiabilité du produit sont améliorées par une planification rationnelle de la position de soudure.
· Facilité d'utilisation et de détection : La position de soudure doit être pratique pour les opérateurs lors des opérations de soudure et des contrôles qualité ultérieurs. Par exemple, éviter de souder dans des endroits difficiles d'accès ou avec une mauvaise visibilité afin d'améliorer l'efficacité et la qualité du soudage.
b. Contrôle des traces de soudure
· Taille des traces de soudure : La taille des traces de soudure doit être rigoureusement contrôlée. En général, la hauteur des traces de soudure doit être comprise entre 4 et 6 mm et ne pas dépasser le plan afin de garantir l'aspect et la précision de l'assemblage du produit. Par exemple, pour le projet de plaque de refroidissement liquide, la taille des traces de soudure a été contrôlée avec succès en ajustant les paramètres et le procédé de soudage, évitant ainsi tout impact sur les performances et la qualité du produit.
· Forme des traces de soudure : La forme des traces de soudure doit être aussi régulière que possible afin d'éviter une fusion excessive ou incomplète. L'optimisation des paramètres de soudage et des techniques opératoires permet d'améliorer efficacement la forme des traces de soudure et la qualité de la soudure.
· Traitement de meulage : Pour les traces de soudure concaves produites au point de soudage par friction, un traitement de meulage est utilisé afin d'obtenir une surface lisse répondant aux exigences d'aspect et de performance du produit.
c. Optimisation de la séquence de soudage
· Soudage par partition : Pour les produits de grande taille, le soudage par partition permet de contrôler efficacement la déformation globale. En divisant le produit en plusieurs zones et en les soudant séquentiellement, la concentration de chaleur pendant le soudage est réduite et le risque de déformation thermique est diminué.
· Correction progressive : Pendant le soudage, la méthode de correction progressive permet d'ajuster la déformation de soudage au fil du temps. La mesure et la correction continues de la déformation du produit pendant le soudage garantissent la précision dimensionnelle et la forme du produit final, conformément aux exigences de conception.
· Optimisation du chemin de soudage : Planifiez rationnellement le chemin de soudage afin d'éviter les soudures répétées dans la même zone et de réduire l'apport de chaleur. Par exemple, dans le projet de plaque de refroidissement liquide, l'apport de chaleur pendant le soudage a été réduit et la qualité du soudage a été améliorée grâce à l'optimisation du chemin de soudage.
d. Contrôle collaboratif de la déformation
La plaque de refroidissement liquide subit une déformation thermique pendant le soudage, ce qui entraîne une diminution de la précision dimensionnelle du produit. Mesures d'optimisation :
· Utiliser le soudage par partition et des méthodes de correction progressive pour contrôler la déformation globale.
· Optimiser les paramètres de soudage, réduire le courant et la tension, et diminuer l'apport de chaleur.
· Utiliser des fixations pour fixer le produit afin de réduire les mouvements et les déformations pendant le soudage.
· Utiliser une méthode de soudage symétrique pour répartir uniformément la chaleur de soudage.
Nous mettrons régulièrement à jour les informations et technologies relatives à la conception thermique et à l’allègement. Merci de votre intérêt pour Walmate.
La technologie CTC (Cell-to-Chassis) a suscité un vif intérêt car elle permet d'améliorer considérablement l'autonomie et l'efficacité énergétique des véhicules électriques. Cependant, sa capacité à remplacer véritablement la technologie des batteries traditionnelles reste controversée. Le principal obstacle à la fabrication – le procédé de soudage des bacs de batterie – est devenu déterminant pour l'avenir de cette technologie : la complexité de la conception structurelle, la compatibilité multi-matériaux et les exigences strictes en matière de gestion thermique ont mis à rude épreuve la technologie de soudage traditionnelle. En partant du point de vue d'ingénieurs de terrain, en combinant les tendances du secteur et les pratiques d'ingénierie, cet article analyse le potentiel et les limites de la technologie CTC et explore comment le soudage est devenu la pierre angulaire de cette révolution technologique.
1- L'idéal et la réalité de la technologie CTC
La technologie CTC permet théoriquement de réduire les pièces structurelles redondantes et d'améliorer la densité énergétique en intégrant la cellule de batterie directement au châssis. Cependant, la faisabilité de son application à grande échelle se heurte à des défis concrets :
Radicalisme et prudence des constructeurs automobiles : Tesla, BYD et d'autres leaders ont lancé des solutions CTC, mais de nombreux constructeurs attendent encore. Les données du secteur montrent qu'en février 2025, les modèles CTC produits en série représentaient 15 à 20 % du marché mondial, et la technologie CTP (Cell-to-Pack) traditionnelle reste la technologie dominante.
Le coût de l'amélioration de la durée de vie des batteries : Bien que la technologie CTC puisse augmenter la densité énergétique de 15 à 20 %, la complexité de la structure du châssis entraîne une augmentation des coûts de fabrication de 30 à 50 % (calculée par un cabinet de conseil), et le rapport coût-bénéfice n'est pas encore clairement établi.
Controverse économique sur la maintenance : La conception intégrée a fait exploser les coûts de maintenance des batteries. Les données des compagnies d'assurance montrent que le taux de remplacement des batteries après accident des modèles CTC atteint 70 %, soit bien plus que les 25 % des modèles traditionnels.
Ces contradictions rendent l'avenir de la technologie CTC complexe. La capacité du marché à dépasser les 20 % dépend de trois facteurs principaux : l'avancement de la production en série du Tesla Cybertruck ; la guerre des prix entre les constructeurs automobiles chinois qui obligerait CTC à réduire ses coûts ; et le degré de compromission de la réglementation européenne sur la réparabilité des batteries. Le niveau de technologie de soudage en production sera déterminant pour déterminer la capacité à franchir le pas entre le laboratoire et la production en série.
2 - Trois obstacles majeurs au procédé de soudage
Pour les fabricants de bacs à batteries, la mise en œuvre de la technologie CTC doit surmonter trois problèmes majeurs :
a. Le compromis entre précision micrométrique et efficacité
Les procédés de soudage traditionnels tolèrent des erreurs de 0,5 mm, mais les bacs CTC doivent accueillir davantage de batteries, ce qui multiplie par plus de trois le nombre de soudures, la plupart étant réparties sur des pièces courbes et irrégulières. Des tests réalisés par un fabricant montrent qu'une erreur de positionnement de soudure supérieure à 0,15 mm entraîne une chute brutale du taux de rendement de l'assemblage des cellules de batterie, passant de 99 % à 82 %. Plus complexe encore, l'amélioration de la précision s'accompagne souvent d'une baisse d'efficacité : malgré la précision élevée du soudage laser, le coût de l'équipement est plus de cinq fois supérieur à celui du soudage traditionnel.
b. Le mélange de matériaux
Afin d'équilibrer légèreté et résistance, les bacs CTC utilisent souvent une structure mixte « alliage d'aluminium + fibre de carbone + acier spécial ». La différence de coefficient de dilatation thermique entre différents matériaux peut atteindre 20 fois (par exemple, 23 μm/m·K pour l'aluminium et 0,8 μm/m·K pour la fibre de carbone), ce qui peut facilement générer des contraintes internes lors du soudage et provoquer des fissures. Lorsqu'une entreprise a tenté d'assembler de l'aluminium et de la fibre de carbone, le taux de fissuration de la soudure a atteint 18 %, dépassant largement le seuil acceptable de 3 % dans l'industrie.
c. « Tueur invisible » de la zone affectée thermiquement
Une température de soudage élevée peut endommager les matériaux isolants ou les circuits des capteurs autour de la cellule de batterie. Un constructeur automobile a déjà augmenté le taux d'autodécharge du module de batterie de 50 % en raison d'un mauvais contrôle de l'apport de chaleur de soudage. Les ingénieurs doivent contrôler les fluctuations de température de soudage à ± 15 °C en 0,1 seconde, ce qui équivaut à installer un « frein thermique de haute précision » sur le pistolet de soudage.
3- Solution : Il n’existe pas de solution miracle, seule l’innovation systémique est possible.
Face à ces défis, l’industrie explore trois voies innovantes :
a. « Cocktail thérapeutique » de la combinaison de procédés
Soudage hybride laser-arc : Combinant la précision du soudage laser aux avantages de la pénétration du soudage à l’arc, la vitesse de soudage des alliages d’aluminium est augmentée de 40 % ;
Technologie de transition métal froid (CMT) : Grâce à un contrôle précis de l’apport de chaleur, la zone affectée thermiquement est réduite de 60 % ;
Système de compensation intelligent robotisé : Ajuste automatiquement la trajectoire du pistolet de soudage en fonction des données de balayage de soudure en temps réel et augmente le taux de qualification du soudage de surfaces courbes complexes de 75 % à 95 %.
b. « Pré-compromis » côté matériaux
Certaines entreprises ont commencé à développer conjointement des matériaux composites « soudables » avec des fournisseurs. Par exemple, la sensibilité aux fissures de soudage d’un alliage d’aluminium modifié national (alliage d’aluminium ajusté par des moyens physiques, chimiques ou de procédé) a été réduite du niveau 7 au niveau 3 (selon les normes ISO). Bien qu'elle sacrifie 5 % de l'effet de légèreté, elle augmente le rendement de soudage à 98 %.
c. « Jumeau numérique » dans la dimension détection
En collectant toutes les données du procédé de soudage (courant, température, vitesse, etc.), combinées à des modèles d'IA pour prédire la probabilité de défauts, une usine a adopté cette technologie, ce qui a permis de passer de 80 % à 97 % du taux de détection en ligne des défauts de soudage et de réduire les coûts de rebut de 45 %.
4- Nouvelle proposition des ingénieurs : Trouver la certitude dans l’incertitude
a. La controverse autour de la technologie CTC repose essentiellement sur un jeu entre « optimisation système » et « limites locales » :
Si la vitesse de percée du procédé de soudage est inférieure aux attentes des constructeurs automobiles en matière de réduction des coûts, la technologie CTC pourrait devenir une technologie de niche ;
Si les matériaux, les procédés et les technologies de test réalisent des avancées de manière coordonnée, cela devrait ouvrir la voie à une nouvelle ère de conception structurelle des véhicules électriques.
b. Pour les ingénieurs, il est nécessaire de reconstruire les capacités à partir de deux dimensions :
Intégration des connaissances inter-domaines : comprendre le seuil de sensibilité des propriétés électrochimiques à l’apport de chaleur de soudage ;
Capacité de réponse agile : Une étude de cas menée auprès d’un fournisseur européen montre qu’une équipe capable d’optimiser les paramètres de soudage de nouveaux alliages en une semaine voit ses chances d’obtenir des commandes tripler.
La technologie CTC se situe à la croisée des chemins entre « innovation disruptive » et « piège de la production de masse ». Cela ne remplacera peut-être pas complètement la technologie existante, mais cela oblige le procédé de soudage à évoluer vers une plus grande précision, une meilleure compatibilité et un contrôle plus intelligent. Dans ce marathon technologique, le véritable gagnant ne sera peut-être pas le premier constructeur automobile, mais l'équipe d'ingénieurs qui transforme les « soudures impossibles » en « interfaces standardisées » côté fabrication.
Nous mettrons régulièrement à jour les informations et technologies relatives à la conception thermique et à l’allègement. Merci de votre intérêt pour Walmate.
La technologie CTP (Cell to Pack) bouleversant la structure traditionnelle des batteries, le rôle du support de batterie est passé d'une simple fonction de support passif à une fonction d'intégration active. La technologie de soudage est devenue essentielle à la sécurité et à la performance. Les exigences de légèreté (épaisseur de paroi de seulement 1,5 mm), d'étanchéité zéro pore et d'intégration multi-matériaux (aluminium, cuivre, fibre de carbone) ont plongé le soudage traditionnel dans le dilemme des déformations et des défauts. L'industrie réalise des avancées majeures grâce à l'innovation des matériaux, au contrôle qualité intelligent et à l'itération des procédés. Cet article analyse les défis disruptifs posés par la technologie CTP au soudage et explore la voie technique vers une haute précision et une fiabilité optimales.
1- Analyse des changements dans les exigences de conception structurelle des bacs de batterie grâce à la technologie CTP
La technologie CTP (Cell to Pack) intègre directement les cellules de batterie au bloc-batterie en supprimant la structure modulaire des blocs-batteries traditionnels. Cette innovation technologique impose des exigences d'amélioration globales et multidimensionnelles pour la conception structurelle du bac de batterie. Voici une analyse spécifique des matériaux, des performances, du procédé, de l'intégration, etc. :
(1) Amélioration globale de la résistance structurelle et de la résistance aux chocs
a. Exigences en matière de support mécanique après suppression du module :
Après suppression de la structure modulaire par la technologie CTP, le bac de batterie doit assurer directement les fonctions de support, de fixation et d'amortissement des forces externes de la cellule de batterie. Le module traditionnel disperse la charge mécanique, tandis que le bac CTP doit absorber la déformation de la cellule de batterie lors de la charge et de la décharge (par exemple, la force de dilatation d'une cellule de batterie carrée peut atteindre 10 à 20 kN), tout en résistant aux vibrations, à l'extrusion et aux chocs pendant la conduite du véhicule.
b. Orientation vers l'optimisation des matériaux et des structures
· Dominance de l'alliage d'aluminium à haute résistance : L'acier a été progressivement remplacé en raison de son poids élevé, et le 6061-T6 s'est imposé. Il présente une résistance spécifique élevée et une forte résistance à la corrosion, ce qui permet de répondre à la double exigence de légèreté et de rigidité élevée.
· Conception de structures composites : Par exemple, la structure « double cadre à poutre annulaire » du Leapmotor améliore la résistance aux chocs locaux grâce à des compartiments de poutre longitudinaux et transversaux, tout en utilisant la technologie d'extrusion pour optimiser la répartition des matériaux et réduire le poids superflu.
· Exploration de l'alliage magnésium-aluminium et de la fibre de carbone : L'alliage magnésium-aluminium est 30 % plus léger que les matériaux en aluminium traditionnels, et les matériaux composites en fibre de carbone présentent à la fois des caractéristiques de résistance et de légèreté élevées, mais ne sont actuellement utilisés que dans les modèles haut de gamme en raison de leur coût et de la maturité de leur procédé.
(2) Exigences relatives à l'étanchéité à l'air et à la gestion thermique intégrées
a. Amélioration des performances d'étanchéité
Une fois le module retiré, la circulation interne du liquide de refroidissement et l'étanchéité au gaz du bloc-batterie dépendent entièrement du plateau, et les défauts de soudure (tels que les pores et les fissures) peuvent entraîner des risques de fuite.
Figure 1 - Test d'étanchéité du bac à piles
b. Intégration des fonctions de gestion thermique
Les plateaux CTP doivent intégrer des composants tels que des plaques de refroidissement liquide et des adhésifs thermoconducteurs. Par exemple, des adhésifs structuraux sont utilisés pour fixer les cellules de batterie et transférer les contraintes de dilatation, tandis que des adhésifs thermoconducteurs polyuréthane (conductivité thermique > 1,5 W/m·K) assurent la conduction thermique entre les cellules de batterie et avec les tubes de refroidissement liquide. La quantité d'adhésif utilisée dans un seul PACK est supérieure de plus de 50 % à celle des structures traditionnelles. Des canaux d'écoulement doivent être conçus à l'intérieur du plateau pour optimiser l'efficacité du refroidissement tout en évitant les dommages à l'étanchéité causés par la zone affectée thermiquement par le soudage.
(3) Allègement et innovation des matériaux
a. Tendances en matière de choix des matériaux
Procédés d'extrusion et de moulage sous pression d'alliages d'aluminium : des profilés en aluminium extrudé sont utilisés pour les structures de cadre (comme le plateau de batterie 4680 de Tesla), et les procédés de moulage sous pression (comme le moulage sous pression intégré) simplifient le soudage et réduisent le poids de 15 à 20 %.
Application des matériaux composites plastiques : Par exemple, les matériaux PA6 renforcés de fibres de verre sont utilisés dans les pièces non porteuses afin de réduire davantage le poids, mais le problème de compatibilité avec l’interface de connexion métallique doit être résolu.
b. Stratégie de conception légère
Optimisation de la topologie : Réduire les matériaux redondants grâce à la simulation IAO et alléger le plateau tout en garantissant sa résistance.
Parois fines et intégrées : L’épaisseur de la paroi du plateau est réduite de 3 mm à 1,5-2 mm, et des composants fonctionnels tels que les supports BMS et les canaux de faisceau de câbles sont intégrés pour réduire le nombre de pièces.
(4) Intégration et conception modulaire
a. Forte intégration des composants fonctionnels
Les plateaux CTP doivent intégrer des modules tels que le système de gestion de batterie (BMS), les connecteurs haute tension et les couches d’isolation ignifuges.
b. Conception modulaire et compatible
La ligne de production de soudage doit prendre en charge la production mixte de plusieurs modèles de plateaux, permettre un changement de type en un clic et être compatible avec des structures de plateaux de différentes tailles de cellules de batterie (par exemple, carrées et cylindriques).
2 - Défis spécifiques de l'innovation technologique CTP pour le procédé de soudage
La technologie CTP (Cell to Pack) a considérablement amélioré l'utilisation de l'espace et la densité énergétique, mais elle a également posé des défis sans précédent au procédé de soudage.
(1) La difficulté de contrôler les défauts de soudage a fortement augmenté.
a. Problèmes de porosité et d'étanchéité
Une fois le module éliminé par la technologie CTP, le support de batterie doit directement assurer l'étanchéité. Les pores de soudage (un défaut fréquent dans le soudage des alliages d'aluminium) entraînent directement un risque de fuite de liquide de refroidissement ou de pénétration de gaz.
b. Fissures et compatibilité des matériaux
Les alliages d'aluminium à haute teneur en zinc (tels que la série 7) sont sujets aux fissures dues aux contraintes thermiques lors du soudage.
c. Erreur d'assemblage et d'espacement
L'intégration directe de plusieurs cellules entraîne une augmentation du nombre de points de jonction de la structure du support. L'accumulation d'erreurs d'assemblage peut entraîner un espacement de soudure supérieur à ± 1 mm.
(2) Problèmes d'adaptation du procédé liés à la mise à niveau du système de matériaux
a. Défis du soudage des matériaux légers
Le matériau des plateaux CTP est passé de l'acier à l'alliage d'aluminium (6061-T6, 7075-T6), à l'alliage magnésium-aluminium (réduction de poids de 30 %) et aux composites en fibre de carbone. Le soudage des alliages d'aluminium doit résoudre le problème de pénétration insuffisante dû à la fusion difficile du film d'oxyde et à une conductivité thermique élevée.
b. Technologie d'assemblage de matériaux différents
Lorsque le plateau intègre des composants fonctionnels tels qu'une plaque de refroidissement liquide (cuivre/aluminium) et une couche ignifuge (matériau composite à matrice céramique), des composés intermétalliques fragiles sont susceptibles d'apparaître à l'interface de matériaux différents.
(3) Complexité structurelle accrue et exigences de précision accrues
a. Contrôle de la déformation des structures minces de grande taille
L'épaisseur de paroi du plateau CTP est réduite de 3 mm à 1,5-2 mm, et la sensibilité à la déformation thermique du soudage augmente considérablement.
b. Joints de soudure haute densité et efficacité du processus
Le nombre de joints de soudure sur un seul plateau est passé de 2 000 dans les modules traditionnels à plus de 5 000.
Figure 2 - Soudage du bac à batterie
3- Modernisation des processus de production et du contrôle qualité
La technologie CTP favorise la transformation du soudage des bacs de batteries, passant d'un « processus unique » à une « collaboration multi-technologies, intelligence et éco-responsabilité ». Les fabricants doivent se concentrer sur trois axes majeurs :
Mise à niveau technologique : amélioration du contrôle des défauts tels que les pores et les fissures, et adaptation aux matériaux légers ;
Transition intelligente : numérisation complète des processus et contrôle qualité par IA pour une production de haute précision ;
Collaboration écologique : élaboration conjointe de normes techniques avec les fournisseurs de matériaux, les équipementiers et les équipementiers.
Nous mettrons régulièrement à jour les informations et technologies relatives à la conception thermique et à l’allègement. Merci de votre intérêt pour Walmate.
Les matériaux légers comme les alliages d'aluminium sont devenus courants grâce à leurs performances supérieures. Cependant, des défis tels que le contrôle de l'apport de chaleur, la suppression des déformations et la stabilité du procédé de soudage des plaques minces constituent des obstacles majeurs pour les technologies de soudage traditionnelles. Le soudage par transfert de métal à froid (CMT), avec ses avantages : faible apport de chaleur, transfert sans projections et contrôle intelligent des paramètres, offre une solution innovante pour la fabrication de bacs de batteries.
Cet article examine les stratégies de contrôle de précision de la technologie CMT pour le soudage des plaques minces destinées aux bacs de batteries, en analysant son adaptabilité, les défis du procédé et les scénarios d'application des composites, afin de fournir des orientations théoriques et pratiques pour une production efficace et de haute qualité.
Figure 1 : Soudage CMT du boîtier inférieur de refroidissement liquide de la batterie de stockage d'énergie 104S
1- Exigences relatives au soudage des bacs de batterie et adaptabilité du CMT
La technologie CMT, avec son faible apport de chaleur, son transfert sans projections et son contrôle intelligent des paramètres, répond parfaitement aux exigences de haute précision, de faible déformation et d'efficacité du soudage des bacs de batterie.
(1)Exigences fondamentales du procédé de soudage des bacs de batterie
a. Compatibilité des matériaux et exigences d'allègement
Les bacs de batterie utilisent principalement des alliages d'aluminium légers (par exemple, série 6xxx, 6061) ou des composites en fibre de carbone pour les modèles haut de gamme, exigeant une résistance élevée (résistance à la traction du matériau de base de 60 à 70 %) et une faible densité (alliage d'aluminium : 2,7 g/cm³).
Assemblage de matériaux différents : Pour les structures hybrides acier-aluminium, les différences de coefficient de dilatation thermique doivent être prises en compte afin de minimiser la déformation.
b. Qualité et performances des soudures
Faible apport de chaleur et contrôle de la déformation : Pour les plaques minces (0,3 à 3 mm), la déformation doit être ≤ 2 mm. Les soudures linéaires longues nécessitent un soudage segmenté ou une conception anti-déformation.
Étanchéité et résistance : Les soudures doivent être parfaitement étanches pour éviter les fuites d’électrolyte et réussir les tests de cisaillement (par exemple, normes T/CWAN 0027-2022).
Contrôle de la porosité : Le soudage des alliages d’aluminium est sujet à la porosité, nécessitant un taux de porosité ≤ 0,5 %.
c. Exigences en matière d’efficacité de production et d’automatisation
La production par lots exige une vitesse de soudage ≥ 7 mm/s, réduisant le temps de soudage d’un seul plateau à 5 à 10 minutes.
Les postes de travail automatisés doivent prendre en charge la conception à deux postes (assemblage et soudage simultanés) et la collaboration multi-robots.
(2) Principaux avantages du CMT pour le soudage des bacs à batteries
a. Contrôle précis de l'apport de chaleur
Le CMT réduit l'apport de chaleur de 33 % par rapport au soudage MIG traditionnel en rétractant le fil de soudage pour couper le courant lors du court-circuit des gouttelettes, éliminant ainsi les risques de brûlure pour les plaques ultra-fines (0,3 mm).
L'alternance des cycles froid-chaud (chauffage de l'arc, transfert des gouttelettes, rétraction du fil) minimise l'accumulation de chaleur et contrôle la déformation à ≤ 1,5 mm (études de cas BYD et BAIC).
b. Stabilité du procédé et amélioration de la qualité
Soudage sans projections : La rétraction mécanique élimine les projections de gouttelettes, réduisant ainsi les reprises.
Optimisation de la porosité : L'utilisation d'un gaz de protection Ar+30 % He réduit la porosité de 50 % par rapport à l'Ar pur, avec des pores ≤ 0,3 mm.
Tolérance élevée aux jeux : Prise en charge des jeux d'assemblage jusqu'à 1,5 mm, réduisant ainsi les exigences de précision des fixations.
c. Intégration de l'automatisation et gains d'efficacité
Les postes de travail à deux postes (par exemple, ceux conçus par Taixiang Tech) permettent le soudage et l'assemblage en parallèle, doublant ainsi l'efficacité.
Le soudage robotisé symétrique (synchronisation à deux robots) avec conception anti-déformation réduit le temps de cycle à ≤ 10 minutes.
2-Défis du processus CMT pour les bacs à batteries
Figure 2 : Déroulement du processus de soudage CMT
(1) Propriétés des matériaux et contrôle des défauts de soudure
a. Sensibilité à la porosité dans le soudage des alliages d'aluminium
Les plateaux en alliage d'aluminium (par exemple, 6061, 6063) sont sujets à la porosité en raison de leur solidification rapide et des variations de solubilité de l'hydrogène. La composition du gaz de protection est essentielle : l'argon pur entraîne une porosité d'environ 5 %, tandis que l'argon + 30 % d'hélium réduit la porosité à ≤ 0,5 %. Le réglage de l'inductance (par exemple, réglage négatif) optimise l'écoulement du bain de fusion et minimise la taille des pores.
b. Fissuration à chaud et ségrégation de composition
La ségrégation de Mg, Si, etc., dans les alliages d'aluminium peut entraîner une fragilisation des joints de grains. Bien que le faible apport de chaleur du CMT réduise la zone de fusion, un contrôle précis de la vitesse de soudage et du dévidage du fil est nécessaire pour éviter une pénétration insuffisante ou une surchauffe localisée.
c. Compatibilité métallurgique dans le soudage de matériaux différents
Les interfaces des joints Al-acier ou Al-composite (par exemple, poutres et enceintes de protection) doivent atténuer les phases fragiles (par exemple, FeAl₃) et les interférences de vapeur de Zn.
(2) Défis liés à l'optimisation des paramètres du procédé
a. Équilibrage de la pénétration et de l'apport thermique
Les soudures doivent respecter la norme T/CWAN 0027 relative à la profondeur de pénétration (≥ 0,8 mm). Le faible apport thermique du CMT peut entraîner une pénétration insuffisante, nécessitant un ajustement de la longueur de l'arc ou un courant pulsé pour améliorer la pénétration.
b. Compromis entre vitesse et stabilité
Les lignes automatisées exigent des vitesses ≥ 1,2 m/min, mais les vitesses élevées risquent d'entraîner une instabilité de l'arc ou un transfert irrégulier des gouttes.
c. Pontage des jeux dans les soudures complexes
Les plateaux présentent souvent des jeux importants (0,5 à 1,5 mm) ou des joints irréguliers (par exemple, des joints en T).
(3) Compatibilité entre la conception structurelle et le procédé de fabrication
a. Contrôle de la déformation par soudage de plaques minces
L'épaisseur de paroi des palettes en alliage d'aluminium est généralement de 2 à 3 mm. La déformation du soudage MAG traditionnel peut atteindre 1,2 mm, tandis que le soudage CMT permet de la réduire à moins de 0,3 mm grâce à un faible apport de chaleur. Cependant, la conception d'outillages anti-déformation et le soudage symétrique robotisé (poste de travail double) sont nécessaires pour améliorer encore la précision.
b. Continuité et étanchéité des soudures longues
La longueur de la soudure scellée du bac de batterie peut atteindre plusieurs mètres, et il est impératif d'éviter les ruptures d'arc ou les fluctuations du bain de fusion. La technologie CMT assure l'uniformité de la soudure grâce à plus de 70 cycles de rallumage d'arc par seconde, et le taux de qualification de l'étanchéité à l'air peut atteindre 99 % grâce au système de suivi laser.
c. Synergie des applications composites multi-procédés
Les palettes haut de gamme utilisent souvent le procédé composite CMT+FSW (soudage par friction-malaxage). Le CMT est utilisé pour les structures complexes (comme l'assemblage entre le cadre et la plaque inférieure). Le FSW est utilisé dans les zones à forte charge (comme les poutres longitudinales) pour améliorer la résistance. Le problème de compatibilité des paramètres d'assemblage des deux procédés (comme la température de préchauffage et le traitement thermique après soudage) doit être résolu.
3-Scénarios d'application typiques du procédé CMT dans la fabrication de bacs à batteries
(1) Assemblage de la structure principale du bac à batteries
a. Soudage du cadre et de la plaque inférieure
Le procédé CMT est largement utilisé pour l'assemblage du cadre et de la plaque inférieure des bacs à batteries en alliage d'aluminium, notamment pour les soudures longues et les plaques fines (2-3 mm d'épaisseur).
b. Assemblage de la poutre et de la plaque inférieure
Dans la conception des bacs à batteries CTP, en raison du nombre réduit de poutres et de la structure complexe, le procédé CMT est utilisé pour : le soudage de positionnement de haute précision : la connexion locale entre la poutre et la plaque inférieure (comme un joint en T) doit éviter une pénétration insuffisante. Le procédé CMT permet une pénétration stable ≥ 0,8 mm grâce au contrôle numérique de la longueur d'arc (comme la technologie Fonis CMT Advanced). Adaptation multi-matériaux : si la poutre est en alliage aluminium-magnésium (comme le 6061) et la plaque inférieure en aluminium haute résistance, le procédé CMT permet de réduire les pores grâce à la protection par gaz mixte Ar+He, tout en s'adaptant aux différences de conductivité thermique des différents matériaux.
(2) Soudage de plaques minces et de structures géométriques complexes
a. Soudage d'alliages d'aluminium à parois minces (2-3 mm)
La légèreté des bacs de batterie favorise l'utilisation de plaques minces, mais le soudage MIG traditionnel est sujet à la déformation. Les avantages du procédé CMT sont les suivants :
b. Soudage de plaques ultra-minces : Taixiang Automation utilise la technologie CMT pour réaliser un soudage sans projections de plaques ultra-minces de 0,3 mm pour les structures d'étanchéité des bords des bacs de batterie.
c. Pontage de soudures de formes spéciales : Pour les structures de formes spéciales telles que les nervures de renfort internes et les poutres anti-collision du bac, le mode de pontage CMT permet de combler un espace de 0,5 à 1,5 mm par rétraction du fil et redirection de l'arc afin d'éviter les défauts de fusion.
d. Soudures exigeant une étanchéité élevée : L'étanchéité du bac de batterie est directement liée à la sécurité de la batterie. Le procédé CMT garantit cela de la manière suivante :
· Soudures longues et continues : plus de 70 cycles de réamorçage d'arc par seconde (comme la technologie Fronius LaserHybrid) garantissent la continuité de plusieurs mètres de soudures, avec un taux de réussite de 99 %.
· Contrôle de l'apport de chaleur faible : par rapport au soudage laser, le CMT présente un apport de chaleur plus faible, ce qui réduit l'impact thermique des fluctuations du bain de fusion sur la couche de scellant et convient au procédé de revêtement de colle.
(3) Scénario de fabrication composite multi-processus
a. Procédé composite CMT+FSW
Sur les lignes de production de bacs de batteries haut de gamme, le CMT est souvent associé au soudage par friction-malaxage (FSW) :
Division du travail et coopération : le CMT est utilisé pour le soudage flexible de structures complexes (telles que les cadres et les joints de formes spéciales), tandis que le FSW est utilisé pour les zones à forte charge (telles que les poutres longitudinales) afin d'améliorer la résistance. Par exemple, la ligne de production automatisée de Shanghai Weisheng utilise une combinaison CMT+FSW+CNC pour augmenter l'efficacité de la production de bacs de 30 %.
Optimisation des connexions de processus : la ligne de production de Huashu Jinming adopte une conception modulaire et permet une connexion transparente avec le FSW grâce à l'adaptation des paramètres de préchauffage (par exemple, un chauffage local à 150 °C après le soudage CMT).
b. Combiné à la technologie de rivetage FDS/SPR
Dans la technologie CTP de deuxième génération, le CMT est coordonné avec les technologies de rivetage auto-serrant par friction (FDS) et auto-perçant (SPR) : Solution de connexion hybride : Par exemple, la zone porteuse du cadre et la plaque inférieure adoptent le soudage FSW, tandis que les pièces détachables (telles que les plaques de refroidissement par eau et les couches isolantes) sont prépositionnées par soudage CMT, puis fixées par rivetage FDS, en tenant compte à la fois de la résistance et de la facilité d'entretien.
Nous mettrons régulièrement à jour les informations et technologies relatives à la conception thermique et à l’allègement. Merci de votre intérêt pour Walmate.
En tant qu’ingénieur de terrain dans une usine de fabrication de plateaux de batterie, ayant participé à plusieurs projets de boîtiers pour véhicules électriques, je constate les arbitrages complexes entre "allègement, sécurité et coût". Cet article analyse les logiques de sélection technologique actuelle et les défis d’industrialisation, à travers trois dimensions : matériaux, procédés de fabrication et tendances futures, illustrées par des cas concrets.
1- Choix des matériaux : Arbitrage entre allègement et coût
Le choix des matériaux du boîtier impacte directement les performances et l’économie du véhicule. Les options dominantes sont l’aluminium, les aciers haute résistance et les composites, chacun adapté à des scénarios spécifiques.
a. Aluminium : Pilier de l’allègement
· Profilés en aluminium extrudé : Utilisés par BYD pour plusieurs modèles, ces profilés optimisent la forme des sections pour réduire le poids et augmenter la rigidité.
· Coulée intégrée (Gigacasting) : La batterie 4680 de Tesla, combinée à la technologie CTC, réduit le poids de plus de 50%. Cependant, les coûts de moules dépassent 200 millions de yuans, nécessitant une production annuelle de 500 000 pièces pour rentabiliser, adaptée aux constructeurs leaders.
· Composites à base d’aluminium : La Porsche Taycan utilise une structure hybride aluminium-fibre de carbone, réduisant le poids de 15%, mais augmentant les coûts de 30%, réservée aux véhicules haut de gamme.
b. Aciers haute résistance : L’option économique
Les aciers à durcissement structural (ex. 22MnB5) offrent une limite d’élasticité de 1 500 MPa. Avec un taux de pénétration de 40% dans les véhicules utilitaires et un coût par GWh inférieur de 40% à l’aluminium, ils dominent les modèles d’entrée de gamme (moins de 100 000 yuans), malgré une densité énergétique réduite de 8%.
c. Composites : L’expérimentation haut de gamme
· Matériaux SMC : Les coques supérieures en composites renforcés de fibre de verre allègent de 30% par rapport à l’acier, mais nécessitent une épaisseur accrue (3 mm + nervures de 5 mm) pour compenser la résistance aux chocs.
· Fibre de carbone : Le boîtier de la BMW i3 est 50% plus léger que l’aluminium, mais coûte 800 yuans/kg, limitant son usage aux modèles luxueux.
Synthèse pratique : Le choix des matériaux doit correspondre au positionnement du véhicule. Le marché moyen (200 000-300 000 yuans) privilégie l’aluminium, l’entrée de gamme l’acier, et le luxe explore les composites.
2- Procédés de fabrication : Équilibre entre efficacité et fiabilité
Les technologies de fabrication influencent la productivité et la fiabilité. Les principales méthodes incluent la coulée sous pression, l’extrusion-soudage et l’intégration structurelle.
a. Coulée vs extrusion-soudage
· Profilés en aluminium extrudé (ex. General Motors Bolt) : Coût unitaire ~800 yuans, adapté à la production de masse, mais processus complexe.
· Coulée d’aluminium (ex. NIO ET5) : Coût unitaire 1 500 yuans, mais productivité multipliée par 5, idéal pour les montées en cadence rapides.
· Soudage par friction-malaxage (FSW) : Réduit la déformation de 50% et améliore la résistance à la fatigue de 30%, malgré un investissement en équipement accru de 40%, adapté aux utilitaires exigeants en durée de vie.
b. Technologies d’intégration structurelle
· CTP (Cell-to-Pack) : La technologie de CATL (batterie Qilin) porte le taux d’utilisation de l’espace de 72% à 85%, réduisant les coûts de 15-20%, mais exige une meilleure protection contre les emballements thermiques.
· CTC (Cell-to-Chassis) : Le Model Y de Tesla supprime 370 pièces et augmente l’autonomie de 54%, mais les coûts de réparation bondissent de 300%, posant des défis pour le service après-vente.
Comparaison des données clés
Expérience de la ligne de production : la technologie CTP reste actuellement la technologie dominante en raison de sa grande compatibilité, tandis que la technologie CTC nécessite une collaboration approfondie entre les constructeurs automobiles et les fabricants de batteries et il est peu probable qu'elle soit popularisée à court terme.
3- Tendances futures : Fusion technologique et amélioration intelligente
a. Hybridation des matériaux
Les structures aluminium-fibre de carbone (ex. concept Porsche Taycan) allègent de 15% avec une résistance en compression de 800 MPa. Cependant, la résistance d’interface doit dépasser 25 MPa (taux de conformité de 65% pour la Toyota bZ4X), nécessitant des progrès en stabilité de production.
b. Innovation fonctionnelle
· Intégration du refroidissement liquide (ex. batterie de magasin GAC) : La surface de contact augmente de 50%, avec un écart de température <5°C, mais exige une optimisation des soudures aluminium-cuivre (soudage laser oscillant) pour réduire la porosité.
· Capteur à fibre optique intégré (solution Continental Group) : surveillance en temps réel de la déformation et de la température de la coque, vitesse de réponse du BMS augmentée de 30 %, mais le problème de durabilité du capteur doit être résolu.
c. Recyclage vert
La technologie de recyclage en boucle fermée de BMW réduit les émissions de CO2 de 60%, mais la perte de performance des matériaux recyclés doit être limitée à 10%. De plus, les grandes pièces en coulée mince (ex. presse 9 000T de LK) exigent un contrôle précis de la température des moules (±5°C), l’élimination des bavures étant un goulot d’étranglement.
Axes de progrès:
Réduction des cycles de moulage des composites (ex. LGF-PP : de 180 à 90 secondes)
Application des jumeaux numériques pour réduire l’erreur de simulation de crash de ±20% à ±5%, améliorant la fiabilité de conception
4- Segmentation du marché et perspectives
Court terme (1-3 ans) : Le CTP avec profilés en aluminium reste dominant, CATL conservant 34% de parts de marché.
Moyen terme (5-10 ans) : Adoption accrue du CTC et de la fibre de carbone dans le haut de gamme, avec une part prévue de 25% pour la fibre de carbone d’ici 2030.
Long terme : Densité énergétique ciblant 400 Wh/kg, et amélioration de la sécurité au-delà des normes actuelles (30 minutes de protection contre l’emballement thermique).
5- Conclusion
Le choix des technologies de boîtiers de batterie relève d’une « adaptation contextuelle », intégrant positionnement du constructeur, seuils de coûts et maturité de la chaîne d’approvisionnement. En tant qu’ingénieurs, nous devons embrasser l’innovation tout en respectant les contraintes de production, cherchant un équilibre dynamique entre allègement, sécurité et coût. À l’avenir, avec l’essor des technologies intelligentes et de fabrication verte, les boîtiers évolueront d’une « protection passive » vers une « sécurité active », soutenant la généralisation des véhicules électriques.
Nous mettrons régulièrement à jour les informations et technologies relatives à la conception thermique et à l’allègement. Merci de votre intérêt pour Walmate.
Dans le processus de production, d'assemblage et d'utilisation réel, la défaillance de la tension de tenue d'isolation des plateau de batterie se produit souvent, comme un récif caché dans le développement rapide de la nouvelle industrie énergétique, menaçant la sécurité de conduite des véhicules et le fonctionnement fiable du système de stockage d'énergie. Cet article tente d'analyser les modes de défaillance typiques en se basant sur les pratiques de fabrication, afin de fournir des références superficielles aux praticiens concernés et d'aider les collègues de l'industrie à explorer conjointement des moyens efficaces pour améliorer les performances de tenue d'isolation des plateau de batterie.
Partie 3 - Analyse des défaillances courantes
Figure 1 Essai de tenue à la tension de l'isolant
1- Analyse des mécanismes de défaillance courants
Les scénarios d'application des plateau de batterie pour le stockage d'énergie et les véhicules à énergie nouvelle sont différents, ce qui entraîne à la fois des points communs et des différences dans les exigences de tension de tenue d'isolation et les conditions de défaillance, comme suit :
a. Différences
Charge dynamique : les véhicules à énergie nouvelle doivent faire face à des vibrations mécaniques à haute fréquence de 20 à 2 000 Hz, tandis que les systèmes de stockage d'énergie sont principalement confrontés à une déformation statique à long terme, avec une durée de déformation cumulée supérieure à 10 ans.
Niveau de tension : la tension de tenue d'isolation des plateau de batterie des véhicules à énergie nouvelle doit atteindre 3 000 VDC et plus (sur la base de la norme GB 38031), tandis que les systèmes de stockage d'énergie nécessitent une tension de tenue d'isolation de 4 200 VAC et plus (sur la base de la norme IEC 61439).
Facteur d'accélération de défaillance : les véhicules à énergie nouvelle génèrent une contrainte thermique due à plus de 2 000 cycles de charge et de décharge par an, ce qui accélère la défaillance de l'isolation ; Les systèmes de stockage d'énergie fonctionnent 24 heures sur 24, 7 jours sur 7, avec une durée de fonctionnement annuelle moyenne de plus de 8 000 heures, ce qui entraîne un vieillissement électrochimique qui accélère à son tour la défaillance de l'isolation.
b. Points communs
Les deux doivent permettre une alerte précoce en cas de défaillance de l'isolation grâce à la surveillance de la résistance de l'isolation (pas moins de 100 MΩ à froid et pas moins de 1 MΩ/kV à chaud) et au contrôle des décharges partielles (moins de 5 pC).
2- Défauts de fabrication courants qui provoquent une défaillance de la tension de tenue d'isolation des plateau de batterie
(1) Étape de construction de la tension de tenue d'isolation
a. Défaillance potentielle et analyse des causes
· Défauts de matériaux :
Cause : Le niveau de tension de tenue du matériau isolant est insuffisant, vieillissement dû à l'humidité ou à une contamination de surface (taches d'huile, débris métalliques).
Performances : Faible résistance d'isolation (< 100 MΩ), courant de fuite supérieur à la norme ou panne directe pendant le test de tension de tenue.
Problèmes de processus :
Cause : Débris métalliques résiduels (processus de soudage/coupe grossier), épaisseur inégale du revêtement isolant ou non durci.
Performances : Décharge partielle, endommagement de la couche isolante provoquant un court-circuit.
Interférence environnementale :
Cause : Une température et une humidité élevées provoquent l'absorption d'humidité du matériau et la corrosion chimique.
Performances : Les performances d'isolation se détériorent avec l'environnement et l'eau condensée provoque un fluage.
Erreurs de test :
Cause : Mauvais réglage de la tension/du temps de test (par exemple non conforme à la norme GB/T 38661), mauvaise mise à la terre.
Performances : Mauvaise évaluation des dommages qualifiés ou dus à une surtension sur les composants.
b. Stratégie de réponse
· Optimisation des matériaux : sélectionner des matériaux résistants à l'humidité (tels que des matériaux composites en fibre de carbone) avec une tension de tenue ≥ 1000 V CC et appliquer un revêtement antisalissure.
· Contrôle du processus : utiliser des équipements de soudage/pulvérisation automatisés et mettre en place un atelier propre.
· Gestion de l'environnement : installer un dispositif de surveillance de la température et de l'humidité et pré-sécher les matériaux avant la construction.
· Spécifications des tests : tests segmentés (pré-test 500 V + test formel 1000 V), étalonner les instruments et enregistrer les données.
(2) Étape d'installation du module
a. Analyse des défaillances potentielles et des causes
· Erreur d'assemblage :
Cause : La doublure isolante est manquante et les boulons sont trop serrés et la couche isolante est endommagée.
Performance : Faible résistance d'isolement entre le module et la coque, et tenue à la rupture de tension.
· Dommages mécaniques
Cause : Rayures sur les outils de manipulation, débris métalliques perçant le film isolant.
Performance : Court-circuit local ou panne soudaine pendant le fonctionnement.
· Compatibilité de conception
Cause : Espace électrique insuffisant en raison de l'écart de taille entre le module et le plateau.
Performance : La capacité parasite provoque une rupture de superposition de tension.
· Risques de connexion électrique :
Cause : Usure et défaillance du joint du connecteur en raison d'un faisceau de câbles non fixé.
Performance : Usure et fuite de la couche isolante du faisceau de câbles haute tension.
b. Contre-mesures
· Conception anti-erreur : Utilisez un outillage de goupille de positionnement pour éviter toute installation manquante et personnalisez la longueur du boulon pour éviter un serrage excessif.
· Opération de nettoyage : nettoyage par aspiration avant l'installation et envelopper les outils avec du silicone anti-rayures.
· Simulation de tolérance : vérifier le degré de correspondance entre le module et le plateau par CAE pour s'assurer que l'écart est ≥ 10 mm.
· Inspection du processus : après l'installation, effectuer une inspection aléatoire avec un mégohmmètre (≥ 100 MΩ) et effectuer un test de tension de tenue segmentée pour localiser le point de défaut.
(3) Phase d'intégration du système
a. Analyse des causes et des défaillances potentielles
· Défaillance de l'interface inter-systèmes :
Cause : les paramètres d'isolation des composants ne correspondent pas (comme les différences de tension nominale de tenue du connecteur).
Performances : panne de connexion de jeu de barres haute tension ou interférence BMS.
· Superposition de capacité parasite :
Cause : la capacité parasite totale augmente après la connexion de plusieurs modules en parallèle, et l'effet d'augmentation de la capacité est significatif.
Performances : le courant de fuite de test au niveau du système dépasse la norme.
· Défaillance due aux contraintes environnementales :
Cause : les vibrations provoquent une fatigue de l'isolation et le liquide de refroidissement s'infiltre dans l'interface haute tension.
Performances : la résistance de l'isolation diminue périodiquement pendant le fonctionnement.
· Angle mort du test :
Cause : échec de simulation des conditions de travail réelles (température élevée/vibrations/humidité).
Performances : réussi en laboratoire mais échec en fonctionnement réel.
b. Contre-mesures
· Conception de compatibilité : unifier les normes des composants des fournisseurs.
· Contrôle de la capacité parasite : ajoutez une couche d'isolation en polyimide et optimisez la disposition grâce à la simulation SPICE.
· Test de simulation des conditions de fonctionnement : effectuez un test composite « cycle de -40 ℃ à 85 ℃ + vibration de 5 Hz à 200 Hz + tension de tenue ».
· Surveillance intelligente : module de surveillance d'isolation en ligne intégré, l'IA prédit les risques potentiels.
3-Test de tenue à la tension d'isolement
Le test de tenue à la tension d'isolement est à la fois une mesure de sécurité et une cause possible de défaillance. Le test de tenue à la tension d'isolement lui-même peut provoquer une défaillance en raison d'un fonctionnement incorrect, de problèmes d'équipement ou de défauts de conception, et même causer des dommages secondaires à l'appareil testé.
(1)Types courants de défaillances pendant le test
(2) Les stratégies de réponse sont les suivantes :
a. Contrôle précis des paramètres de test
· Tension et durée : définies selon les normes ; activer l'algorithme de compensation dynamique pour les charges capacitives (telles que les modules de batterie) afin de supprimer l'effet d'augmentation de la capacité.
· Seuil de courant de fuite : défini selon les spécifications de l'équipement (par exemple ≤ 10 mA) et faire la distinction entre les modes CC/CA (les tests CC nécessitent un seuil inférieur).
b. Spécifications de l'équipement et du fonctionnement
· Étalonnage de l'instrument : le testeur de tension de tenue est étalonné tous les 6 mois et la couche d'isolation de la ligne haute tension est inspectée visuellement quotidiennement.
· Fonctionnement sûr : déconnexion forcée des circuits basse tension avant le test ; utiliser des bras robotisés ou des dispositifs automatiques pour éviter tout contact manuel avec les zones haute tension.
c. Prévention et réparation des pannes
· Tests segmentés : tester des systèmes complexes en modules (par exemple, tester d'abord le bus haute tension, puis tester l'isolation du module) pour localiser le point de panne.
· Réparation des pannes : utiliser de la résine époxy pour combler la zone endommagée après la panne, et après réparation, il est nécessaire de repasser le test de gradient de tension complet (par exemple, pression par paliers de 500 V→1 000 V).
d. Gestion de l'environnement et des données
· Contrôle environnemental : démarrer le déshumidificateur lorsque l'humidité dans la zone de test est supérieure à 75 %, ou retarder le test jusqu'à ce que l'environnement soit conforme à la norme.
· Traçabilité des données : enregistrer la tension de test, la courbe de courant de fuite et les paramètres environnementaux, et utiliser le système MES pour associer le numéro de lot de production.
Nous mettrons régulièrement à jour les informations et technologies relatives à la conception thermique et à l’allègement. Merci de votre intérêt pour Walmate.
Le plateau de batterie utilise des matériaux isolants principalement pour empêcher les fuites de courant, protéger la sécurité du personnel et assurer le fonctionnement normal du système de batterie. Lors de la sélection, il est nécessaire de prendre en compte les propriétés isolantes du matériau, sa résistance à la chaleur, sa stabilité chimique et sa résistance mécanique. Ces facteurs déterminent ensemble l'effet d'application du matériau isolant dans le plateau de batterie, affectant ainsi la sécurité et la fiabilité de l'ensemble du système de batterie.
Partie 2 - Garantie de performance de résistance à la pression
Figure 1 Plateau de batterie pour véhicule électrique
1-Sélection des matériaux isolants et conception de solutions
Lors de la sélection des matériaux isolants pour les Plateau de batterie, l'accent est mis sur les propriétés diélectriques, la tolérance environnementale et les propriétés mécaniques des matériaux. Voici 6 matériaux isolants couramment utilisés dans les plateau de batterie et leurs informations associées :
Lors de la conception d'une solution, nous devons généralement prendre en compte de manière exhaustive les trois facteurs clés du scénario d'application, les exigences de performance et le budget de coût pour sélectionner le matériau isolant approprié. Par exemple :
(1) Sélectionnez en fonction du scénario d'application : dans un système de batterie de stockage d'énergie à haute tension et à courant élevé, si le côté du plateau de batterie nécessite un matériau isolant haute performance, il est recommandé d'utiliser la solution de fixation de film PI ; si les exigences de performance d'isolation ne sont pas élevées, la solution de pulvérisation de poudre isolante peut être sélectionnée. Pour la plaque inférieure du plateau de batterie, si une solution d'isolation à faible coût est recherchée, la solution de pulvérisation de poudre isolante ou de revêtement de peinture isolante est plus adaptée.
(2) Sélectionnez en fonction des exigences de performance : lorsque les exigences de performance d'isolation, de résistance aux hautes températures, de résistance à la corrosion chimique, etc. sont élevées, la solution de fixation de film PI est un meilleur choix ; si ces exigences de performance sont relativement faibles, la solution de pulvérisation de poudre isolante ou de revêtement de peinture isolante peut répondre aux besoins.
(3) Sélectionnez en fonction du budget de coût : lorsque le budget de coût est limité, la solution de pulvérisation de poudre isolante ou de revêtement de peinture isolante est plus économique ; lorsque le budget est suffisant, la solution de fixation du film PI peut être sélectionnée.
2-Exigences techniques pour le film PI pour les plateau de batterie
(1) Matériau : PI, épaisseur du film de base 0,1-0,14 mm, épaisseur de l'adhésif arrière 0,03 mm, conductivité thermique du film PI > 0,3 W/(m·k) ;
(2) Résistance à la pression : AC 3000 V, 60 S, courant de fuite ≤ 0,5 mA ;
(3) (pâte froide) résistance au pelage à 180° ≥ 15 N/24 mm ;
(4) Isolation : DC 1500 V, 60 S, résistance d'isolation > 1000 MΩ ;
(5) Performances d'isolation de résistance à la chaleur et à l'électrolyte : à 500 ℃, tension DC 700 V, ajouter 2 ml d'électrolyte (zone de test 13 000 mm<H>2<H>), conserver pendant 1 h, pas de panne et pas d'étincelles ; (6) Performances thermiques et d'isolation : à 500±2℃, poursuivre la cuisson (four à moufle) pendant 0,5 h, la morphologie globale de l'échantillon change sans combustion spontanée et l'échantillon passe deux fois. Un courant alternatif de 1000 V est appliqué à la surface et la tension est augmentée de 0 V à 3000 pendant 10 S, puis continue pendant 60 S. L'échantillon testé ne présente aucune panne ni aucune étincelle ;
(7) Qualité ignifuge : UL94 V-0 ;
(8) Haute température et humidité élevée : après 1000 heures de test à 85℃ et 85 % d'humidité, l'échantillon ne présente aucune fissure ni déformation, répondant à la norme nationale « GBT 13542.6-2006 Film d'isolation électrique Partie 6 : Film polyimide pour isolation électrique » sur la résistance d'isolation, la valeur de tension de tenue et les exigences de résistance électrique. La résistance à la traction, l'allongement à la rupture et la résistance au pelage sont réduits de moins de 30 % par rapport au matériau non vieilli ;
(9) Choc à chaud et à froid : 85 °C pendant une heure, commuté à -40 °C pendant une heure, puis commuté à 85 °C pour les cycles à haute et basse température. Le temps de commutation est compris dans une heure et le temps de commutation est ≤ 3 min. Après 1 000 heures de cycles à haute et basse température, l'échantillon ne présente aucune fissure ni déformation, répondant à la norme nationale « GBT 13542.6-2006 Film d'isolation électrique Partie 6 : Film polyimide pour isolation électrique » pour la résistance d'isolation, la valeur de tension de tenue et les exigences de résistance électrique. La résistance à la traction, l'allongement à la rupture et la résistance au pelage sont réduits de moins de 30 % par rapport au matériau non vieilli.
(10) Test au brouillard salin : test au brouillard salin neutre (NSS) selon la norme GB/T 10125, température 35℃, humidité ≥85%RH, solution d'essai (5±0,1%) (fraction massique) NaCl, PH=6,5~7,2, pulvérisation continue pendant 72h. Après le test au brouillard salin, l'échantillon ne présente aucune fissure ni déformation, répondant à la norme nationale « GBT 13542.6-2006 Film d'isolation électrique Partie 6 : Film polyimide pour isolation électrique » pour la résistance d'isolation, la valeur de tension de tenue et les exigences de résistance électrique. La résistance à la traction, l'allongement à la rupture et la résistance au pelage sont réduits de moins de 30 % par rapport au matériau non vieilli.
(11) Le produit est conforme à la directive RoHS.
Figure 2 Film PI pour plateau de batterie
3-Méthodes de test de tension de tenue d'isolement et solutions aux problèmes courants
(1) Méthode de test de tension de tenue d'isolation
Le test de tension de tenue d'isolation est un moyen important d'évaluer les performances d'isolation des équipements électriques, notamment le test de tension de tenue CC et le test de tension de tenue CA. Le test de tension de tenue CC détecte si le matériau isolant se décompose dans un délai spécifié en appliquant une haute tension CC. L'équipement comprend un générateur de haute tension CC, un voltmètre, etc. Les étapes consistent à appliquer la tension, à maintenir la tension et à réduire la tension. Le test de tension de tenue CA applique une haute tension CA. L'équipement et les étapes sont similaires au test CC. Les deux méthodes nécessitent une préparation avant le test pour garantir que l'équipement est bien mis à la terre et que l'état de surface du matériau isolant est étroitement observé pendant le test.
(2) Problèmes courants et solutions
Les problèmes courants dans le test de tension de tenue d'isolation comprennent la rupture d'isolation, le courant de fuite excessif et la défaillance de l'équipement de test. La rupture d'isolation peut être causée par des performances insuffisantes du matériau isolant, des défauts internes ou de l'humidité. Les solutions comprennent la sélection de matériaux de haute qualité, le renforcement de la maintenance et l'amélioration de la structure de l'isolation. Un courant de fuite excessif peut être causé par une résistance d'isolation réduite, une contamination de surface ou une précision insuffisante de l'équipement de test. Les solutions comprennent le maintien du matériau isolant propre et sec et l'étalonnage de l'équipement de test. La défaillance d'un équipement de test peut être causée par son vieillissement, un entretien ou un fonctionnement inadéquat. Les solutions incluent un entretien régulier, un fonctionnement correct et une réparation rapide.
Nous mettrons régulièrement à jour les informations et technologies relatives à la conception thermique et à l’allègement. Merci de votre intérêt pour Walmate.
Avec le développement rapide des véhicules à énergie nouvelle et des technologies de stockage d'énergie, le système de batterie, en tant que vecteur d'énergie central, a attiré une grande attention en termes de sécurité et de fiabilité. Le plateau bac de batterie, en tant que structure de support et de protection des modules de batterie, ses performances d'isolation électrique sont directement liées au fonctionnement en sécurité du véhicule complet, à la durée de vie de la batterie et à la sécurité personnelle des utilisateurs. La conception de la sécurité électrique du plateau bac de batterie est la pierre angulaire de la sécurité du système de batterie. Par des protections multi niveaux, telles que l'isolation, la structure, la chaleur, la surveillance, etc., elle garantit le fonctionnement stable de la batterie dans des conditions de travail complexes, réduit le risque d'incendie, d'explosion ou de choc électrique causé par des pannes électriques, et prolonge en même temps la durée de vie de la batterie et améliore la fiabilité du système.
Cet article, centré sur la sécurité d'isolation électrique du plateau bac de batterie, expose systématiquement ses principes de conception, les méthodes de vérification des performances de résistance à la pression, ainsi que l'analyse de la cause fondamentale et les stratégies d'amélioration des cas typiques de défaillance, en vue de fournir un soutien théorique et une référence pratique pour la conception de haute sécurité du système de batterie.
Part 1: Design Essentials
Le cœur de la conception de la sécurité électrique du système de batterie réside dans la trinité « prévention contrôle urgence » : prévenir les pannes par des mesures telles que l'isolation, la connexion fiable, la gestion de la chaleur, etc. ; réaliser le contrôle en temps réel avec l'aide de capteurs et de BMS ; répondre aux situations extrêmes en utilisant des conceptions telles que la prévention du feu, la décompression, etc. Chaque point doit agir en synergie pour garantir la sécurité et la fiabilité du système de batterie tout au long de son cycle de vie, tout en tenant compte de la maintenabilité et de la conformité. Le plateau bac de batterie dans le système de batterie non seulement supporte la structure, mais assume également de multiples fonctions telles que l'isolation électrique, la gestion de la chaleur, l'anti glissement, la protection mécanique, la mise à la terre et la conception modulaire, ce qui est crucial pour garantir la sécurité électrique du système de batterie.
1-Le support structurel assure la fiabilité de la connexion électrique
Le bac à batterie assure la fiabilité et la sécurité des connexions électriques dans des conditions de travail complexes en fixant les modules de batterie, en réduisant les contraintes mécaniques, en résistant aux vibrations et aux chocs, en maintenant l'alignement et en intégrant la protection de l'environnement et la gestion thermique.
Figure 1 Plateau de batterie
A. Support physique et fixation, assure le positionnement exact des points de connexion électrique (tels que les barres omnibus, les faisceaux de câbles, les connecteurs), évite le mauvais contact causé par la déformation ou le déplacement structurel ; fournit un cadre rigide, fixe les modules de batterie et les pièces de connexion, empêche la desserrage ou la rupture causée par les vibrations ou les chocs.
B.Isolement et protection environnementaux, empêche l'intrusion d'eau vapeur, de poussière, de brouillard salin, etc. par un design d'étanchéité (tels que IP67/IP68), évite le court circuit causé par la corrosion ou l'échec d'isolation ; bloque les chocs mécaniques externes ou les impacts d'objets étrangers, protège les pièces de connexion haute tension.
C. Synergie de la gestion de la chaleur, intègre une structure de dissipation de chaleur (tels que la plaque de refroidissement liquide, le coussin thermoconducteur) pour équilibrer la température, empêche l'oxydation ou le soudage par fusion des points de connexion causés par la surchauffe locale ; réduit les interférences thermiques entre les modules adjacents par un design d'isolation thermique, évite la différence d'expansion des matériaux causée par le gradient de température.
D. Support de la compatibilité électromagnétique (EMC), supprime les interférences électromagnétiques par une couche de blindage métallique ou un revêtement conducteur, protège les lignes de signal basse tension (tels que la ligne de communication BMS) contre les interférences du circuit haute tension.
2-La protection d'isolement crée un environnement d'isolement efficace
La conception d'isolation électrique de la batterie a pour but de construire un environnement capable non seulement d'isoler efficacement l'électricité haute tension, mais aussi de garantir le fonctionnement efficace du système, de sorte que le module de batterie puisse être emballé en toute sécurité dans toutes les conditions de travail, prévenant la libération accidentelle de l'énergie électrique et évitant ainsi les risques électriques potentiels.
A.La structure du plateau bac de batterie tient compte à la fois du support et de la protection par isolation :
l Préférer les matériaux d'aluminium alliage, tels que l'aluminium alliage extrudé, pour réaliser la légèreté tout en maintenant une haute rigidité et une résistance aux chocs. La structure extérieure supporte le poids du système de batterie entier et les chocs externes, utilise des profilés à section fermée pour renforcer la force structurelle, et la structure intérieure est conçue pour supporter les modules de batterie et la plaque de refroidissement à eau, assurant leur stabilité et leurs besoins de dissipation de chaleur.
l Utiliser des matériaux isolants en tant que garnitures ou revêtements pour assurer une bonne isolation électrique entre le module de batterie et le plateau bac, les faisceaux de câbles haute tension doivent avoir un trajet de gestion spécial et une gaine isolante, garantissant la distance d'espacement électrique et la distance de creepage par rapport au plateau bac.
l Utiliser des techniques de soudage avancées telles que le soudage par friction-malaxage, améliorer la force de connexion, en même temps réduire la zone d'influence thermique, éviter la déformation et les fissures potentielles. Pour les parties difficiles à souder, utiliser la connexion par boulons ou le rivetage, combiné avec la colle d'étanchéité, assurer la fiabilité de la connexion mécanique et l'isolation électrique.
l Prendre en compte la modularité lors de la conception, faciliter le remplacement et la maintenance des batteries, sans affecter la stabilité de la structure globale.
Figure 2 Schéma de principe de la distance d'isolement et de fuite dans l'air
B.Points clés de la conception d'isolation haute basse tension :
l Les points de potentiel positif et négatif du système de batterie doivent être isolés du système d'alimentation basse tension et du plateau bac de batterie, assurer une distance d'espacement électrique et une distance de creepage suffisantes entre le circuit haute tension et le circuit de contrôle basse tension, conformément aux normes de sécurité, empêcher la fuite haute tension vers le système basse tension.
l La conception d'isolation haute basse tension doit prendre en compte la compatibilité électromagnétique (EMC), assurer que les mesures d'isolation n'introduisent pas d'interférences, maintenir le fonctionnement stable du système.
l Connexion à haute impédance, les systèmes haute basse sont connectés par une connexion à haute impédance, seulement autorisés à être connectés à la mise à la terre du véhicule (plateau bac de batterie) pour limiter le flux de courant, assurer que la panne du système haute tension ne se propage pas au système basse tension.
l Mesures d'isolation physique, lors de la conception du plateau bac de batterie, on peut disposer les composants haute basse tension dans différentes chambres fermées, réduire l'influence mutuelle par une séparation physique ; utiliser des matériaux isolants en tant que garnitures entre le module de batterie et le plateau bac, tels que des plastiques polymères ou du caoutchouc, pour assurer l'isolation physique et électrique.
l Prendre en compte la maintenabilité des mesures d'isolation lors de la conception, assurer qu'on peut réaliser la réparation ou le remplacement en toute sécurité lorsqu'il y a besoin.
C.Points clés de la conception de protection par contact :
l Gestion des faisceaux de câbles haute tension : les faisceaux de câbles haute tension doivent être bien enveloppés dans une gaine isolante et gérés de manière ordonnée par des pinces de fixation ou des rainures de conducteur, éviter d'être exposés, réduire le risque de contact direct.
l Cloison de sécurité : installer des cloisons isolantes entre les modules de batterie et entre le module de batterie et la paroi du plateau bac, pour prévenir le risque d'électrochoc indirect causé par la fuite d'électrolyte en cas de dommage de la batterie.
l Encapsulation des composants haute tension : effectuer une encapsulation des composants clés tels que les connecteurs haute tension, les relais, etc., assurer que même à l'intérieur du plateau bac, ces composants ne peuvent pas être touchés directement par accident.
l Design fermé : le plateau bac de batterie est conçu en tant que structure fermée, utilise une coque métallique ou composite, assure que les composants haute tension à l'intérieur ne seront pas exposés, et la coque elle même doit également avoir de bonnes performances d'isolation.
l Mécanisme de verrouillage : pour les points de connexion haute tension pouvant être maintenus, utiliser un mécanisme de verrouillage, assurer qu'ils ne s'ouvrent pas facilement lors d'un opération non professionnelle, réduire le risque de toucher par erreur.
l Application des matériaux isolants : utiliser des matériaux isolants en tant que couche d'isolation entre le plateau bac de batterie et le module de batterie, assurer que même en cas de dommage du plateau bac, on peut empêcher le contact direct du corps humain avec la partie sous tension. Ces matériaux comprennent, mais ne sont pas limités à, les plastiques polymères, les rondelles de caoutchouc ou les revêtements.
3-Conception des identifications électriques
Les identifications électriques du plateau bac de batterie peuvent non seulement améliorer la sécurité des opérations, mais aussi simplifier le processus de maintenance, réduire le risque d'opérations erronées.
A.Identification claire
l Marquer clairement des avertissements tels que « Danger haute tension », « Ne pas toucher » sur le plateau bac de batterie et les composants haute tension environnants, assurer qu'ils peuvent être rapidement identifiés même en cas d'urgence.
l Utiliser le codage de couleur internationalement reconnu, par exemple, utiliser le rouge ou l'orange pour identifier la zone haute tension, le bleu pour représenter le courant continu, pour distinguer intuitivement les différentes caractéristiques électriques.
l Appliquer des symboles de sécurité électrique standardisés, tels que les symboles graphiques dans l'IEC 60417, pour représenter la haute tension, la mise à la terre, les points de coupure d'alimentation, etc., assurer la compréhensibilité mondiale des informations.
l Inclure le numéro de série, la date de production et l'information de lot du plateau bac de batterie, faciliter le suivi et la gestion du rappel.
l Sélectionner des matériaux et des techniques d'impression résistants à l'usure et à la corrosion, assurer que les identifications restent claires et lisibles tout au long du cycle de vie du plateau bac de batterie.
B.Avertissements d'identification
l Identifier clairement le danger haute tension sur le plateau bac de batterie et dans la région environnante, rappeler aux techniciens de maintenance d'attacher attention à la sécurité électrique et de respecter les procédures d'opération.
l Indiquer la distance de sécurité d'opération, en particulier près des connecteurs haute tension et des conducteurs nus, rappeler de maintenir une distance appropriée.
C.Guide d'opération
l Marquer clairement la position de mise à la terre du système de batterie et du plateau bac, assurer la mise en œuvre correcte des mesures de mise à la terre.
l Identifier les points de test en sécurité et les points d'accès de maintenance, ces points doivent être conçus en tant que points d'opération sous basse tension ou non sous tension.
l On peut également énumérer brièvement les opérations de base et les guides de sécurité dans la région non critique du plateau bac, guider le processus d'opération correct.
Nous mettrons régulièrement à jour les informations et technologies relatives à la conception thermique et à l’allègement. Merci de votre intérêt pour Walmate.
Les blocs d'eau les plus populaires sont essentiellement de type microcanal en cuivre pur. La plaque inférieure en cuivre est directement traitée avec un racloir et les ailettes sont intégrées à la plaque inférieure pour réduire la résistance thermique. La plaque inférieure et la plaque de recouvrement sont brasées ou diffusées pour assurer la fiabilité de l'étanchéité.
Partie 3 : La principale structure de coût du bloc d'eau traité par le processus de découpage
1- Avantages de l'utilisation du procédé de skiving pour la fabrication de blocs d'eau
l Conception intégrée : le processus de découpe peut intégrer le fond et les ailettes, ce qui permet de réduire la résistance thermique de contact et d'améliorer la conductivité thermique. De plus, la conception intégrée de la plaque inférieure et des ailettes peut également améliorer la résistance structurelle.
l Traitement de haute précision : le processus de découpe peut produire une structure de dent très fine, et la hauteur, l'épaisseur et le pas des dents peuvent être contrôlés avec précision, ce qui rend les ailettes du dissipateur thermique plus denses, la zone de dissipation thermique plus grande et la dissipation thermique plus efficace. En même temps, il peut également mieux répondre aux besoins personnalisés des différents clients en termes de forme, de taille, etc.
l L'efficacité de la production est élevée et le processus de découpe peut être produit en série. Par rapport à la CNC traditionnelle, le processus de découpe peut traiter plusieurs pièces d'engrenage en même temps, ce qui améliore considérablement l'efficacité de la production.
Figure 1 : Base de bloc d'eau avec différentes technologies de traitement a-Skiving b-CNC c-Forgeage à froid
2- Structure des coûts du bloc d'eau de skiving
l Coûts de conception et de développement : La complexité de conception du bloc d'eau de découpage est relativement élevée, en particulier lorsque des exigences élevées en matière de performances de dissipation thermique sont requises, ce qui nécessite une conception et une optimisation complexes du processus.
l Coût des matériaux : Les matériaux utilisés dans le processus de découpage sont principalement de l'aluminium et un alliage de cuivre. La conception combinant une plaque d'aluminium et un alliage de cuivre est plus courante dans la fabrication de radiateurs et présente un rapport coût-performance plus élevé, de sorte que la qualité de l'aluminium et du cuivre affecte directement le coût.
l Coût de traitement :
Coût du processus de découpage : Le processus de découpage implique des équipements d'usinage CNC de haute précision, tels que des machines-outils CNC à trois axes. L'utilisation de tels équipements nécessite un coût d'investissement élevé et les exigences techniques pour les opérateurs sont également élevées, ce qui augmentera les coûts de production.
Coût du processus de soudage : Dans le processus de fabrication des blocs d'eau, le processus de soudage est également un facteur de coût important. Le brasage sous vide et le soudage par diffusion sont deux méthodes de soudage couramment utilisées. Le brasage peut souder plusieurs joints en même temps, a une efficacité de production élevée, nécessite des matériaux de brasage, a des exigences élevées pour les conditions de processus et est difficile à contrôler la qualité ; l'équipement de soudage par diffusion a un investissement ponctuel important et le soudage par diffusion ne nécessite pas de charges, mais a des exigences élevées pour le traitement de surface de la pièce.
Coût du traitement de surface : Les méthodes de traitement de surface courantes comprennent l'anodisation, le placage, etc. Pour les blocs d'eau en alliage d'aluminium, l'anodisation peut améliorer la dureté de surface, la résistance à l'usure et la résistance à la corrosion, tout en augmentant l'esthétique du produit ; les blocs d'eau en cuivre seront plaqués, comme le nickelage, pour empêcher l'oxydation et la corrosion du cuivre, et augmenter la durée de vie et la fiabilité du produit.
l Autres coûts : inspection et tests, emballage et transport, etc.
3-Suggestions d'optimisation des coûts
l Optimisation de l'utilisation des matériaux:
Choisissez le bon matériau : par exemple, le cuivre présente une conductivité thermique élevée, une densité unitaire élevée et un prix unitaire élevé ; l'aluminium est léger, a un prix unitaire faible et une conductivité thermique légèrement médiocre.
Utilisation des matériaux : assurez une utilisation efficace des matériaux et réduisez le gaspillage de matériaux en calculant avec précision l'épaisseur et la marge des matériaux.
Figure 2 : Schéma de principe du calcul de la consommation de matériaux
l Optimisation des processus de production
Simplification des moules : Concevez des moules simples pour réduire la complexité et le coût des moules.
Réduction du taux de rebut : Réduisez le taux de rebut grâce à un contrôle précis des processus et à une inspection de la qualité.
Moulage en une seule étape : Optimisez les itinéraires de processus, réduisez les étapes de traitement multiples et améliorez l'efficacité de la production.
Nous mettrons régulièrement à jour les informations et technologies relatives à la conception thermique et à l’allègement. Merci de votre intérêt pour Walmate.
En tant que composant clé du système de refroidissement liquide, la conception du bloc d'eau doit prendre en compte de multiples facteurs tels que les performances d'échange thermique, la résistance structurelle, la résistance à la corrosion, la résistance aux fuites et le contrôle des coûts. Le bloc d'eau est généralement conçu avec une structure complexe de fentes d'échange thermique (c'est-à-dire un canal d'écoulement), et la qualité de la conception de son canal d'écoulement interne détermine directement l'efficacité de l'échange thermique de l'ensemble du système.
Partie 2 : Conception de blocs d'eau, technologie de traitement et défis
1-Exigences de conception pour les blocs d'eau dans différents scénarios
Les appareils de calcul haute performance (tels que les processeurs haute performance, les GPU, etc.) génèrent beaucoup de chaleur pendant leur fonctionnement, de sorte que le bloc d'eau doit avoir des capacités de dissipation thermique efficaces. Afin de répondre aux exigences de dissipation thermique à haute densité de flux thermique, le bloc d'eau adopte généralement une conception de microcanaux haute densité pour augmenter la zone d'échange thermique et améliorer l'efficacité de la dissipation thermique. De plus, certaines conceptions intègrent le bloc d'eau directement sur le processeur, éliminant ainsi l'étape d'application de graisse silicone, ce qui simplifie non seulement le processus d'assemblage, mais améliore également encore les performances de dissipation thermique. En termes de fiabilité, le bloc d'eau doit avoir d'excellentes performances d'étanchéité pour éviter les fuites et assurer un fonctionnement stable à long terme.
l Refroidissement de la carte graphique :
Les cartes graphiques sont des zones à forte production de chaleur, le bloc d'eau doit donc être entièrement recouvert pour garantir que tous les composants générateurs de chaleur de la carte graphique peuvent être refroidis efficacement. Dans le même temps, le refroidissement de la carte graphique nécessite un débit élevé de liquide de refroidissement, de sorte que la structure interne du bloc d'eau doit prendre en charge un débit élevé pour évacuer rapidement la chaleur.
l Centre de données :
Dans les centres de données, la conception structurelle du bloc d'eau doit répondre à de multiples exigences telles qu'une dissipation thermique efficace, un faible bruit, une fiabilité élevée, une adaptabilité à une densité de puissance élevée, une gestion intelligente et une adaptabilité environnementale pour assurer un fonctionnement stable et une dissipation thermique efficace des centres de données.
2- Tendance évolutive de la structure des blocs d'eau
La tendance évolutive de la conception structurelle des blocs d'eau reflète la double recherche d'innovation technologique et d'amélioration des performances, qui se reflète principalement dans les aspects suivants :
l Amélioration des performances de dissipation thermique :
Augmentation de la surface de contact : Certaines conceptions de blocs d'eau améliorent les performances de dissipation thermique en augmentant la surface de contact avec l'élément chauffant. Par exemple, une conception de base en cuivre de grande surface peut obtenir un bon contact et une bonne conduction thermique.
Optimisation de la structure interne : Optimisation du canal d'eau interne. Une idée consiste à optimiser l'écoulement du fluide, par exemple en passant d'ailettes ordinaires à des ailettes de direction, en présentant un canal d'écoulement à longue bande, en favorisant la séparation de la couche limite d'écoulement, en réduisant l'épaisseur de la couche limite et en améliorant l'efficacité de l'échange thermique ; une autre idée consiste à augmenter la zone de capacité thermique, par exemple en passant des canaux d'eau grossiers traditionnels à une conception à microcanaux, ce qui augmente considérablement la surface de contact entre le liquide de refroidissement et la plaque de base et améliore l'efficacité de la dissipation thermique. Dans certaines conceptions, le liquide de refroidissement est pulvérisé sur la plaque de base à microcanaux via une plaque de guidage pour augmenter la vitesse d'écoulement locale et la turbulence, améliorant ainsi considérablement l'efficacité d'absorption thermique.
l Conception intégrée et intelligente :
Conception intégrée : La conception intégrée intègre la pompe à eau, les ailettes du dissipateur thermique, la base de conduction thermique et d'autres composants ensemble pour réduire le nombre de points de connexion et améliorer la stabilité du système et l'efficacité de la dissipation thermique.
Intégration multifonctionnelle : En plus des performances de dissipation thermique, les blocs d'eau modernes ont également des fonctions d'affichage et de surveillance de la température.
Conception modulaire : La structure de boucle modulaire améliore la commodité et la liberté d'organisation.
Figure 1 : Base du bloc d'eau avec différentes épaisseurs d'ailettes
l Matériaux et finitions hautes performances :
L'utilisation de matériaux hautes performances tels que la base en cuivre pur, combinée à des technologies de traitement de surface telles que le nickelage, améliore la conductivité thermique et la résistance à la corrosion.
3-Technologie de traitement et défis
l Les propriétés des matériaux affectent le traitement :
Problèmes de dureté et de ténacité des matériaux : les radiateurs fabriqués à partir de différents matériaux, tels que le cuivre, l'aluminium et leurs alliages, ont une dureté et une ténacité différentes, ainsi que des exigences différentes en matière d'outils et de processus de traitement. Les matériaux ayant une dureté plus élevée s'usent plus rapidement et nécessitent des changements d'outils plus fréquents ; les matériaux ayant une meilleure ténacité sont sujets à la déformation et aux bavures lors de la coupe.
Le traitement des matériaux composites cuivre-aluminium est complexe : les dissipateurs thermiques à dents de pelle en matériaux composites cuivre-aluminium doivent d'abord être transformés en matériaux composites à l'aide de la technologie de pressage à l'état semi-fondu par coulée continue, puis le traitement à dents de pelle est effectué. Le processus est plus compliqué et nécessite une plus grande précision pour les équipements et les processus.
l Exigences élevées en matière de précision dimensionnelle :
Il est difficile de garantir la cohérence de la hauteur et de l'épaisseur des dents : pour certains dissipateurs thermiques à dents haute densité, la hauteur et l'épaisseur de chaque dent doivent être très cohérentes pour garantir les performances et l'uniformité du dissipateur thermique. Si la différence de hauteur et d'épaisseur des dents est trop importante, cela entraînera un transfert de chaleur inégal et affectera l'effet de dissipation thermique. Pendant le traitement, des équipements de haute précision et des systèmes de contrôle automatisés sont nécessaires pour garantir la cohérence des spécifications de chaque dent.
Il est difficile de contrôler l'espacement des dents : lorsque les dents du dissipateur thermique sont trop denses, leur densité et leur espacement compliquent le processus de traitement, et l'équipement de traitement doit avoir une vitesse et une précision plus élevées pour maintenir l'uniformité des dents. Par exemple, lorsque l'espacement des dents est trop petit, l'outil est sujet à des interférences pendant la coupe, ce qui affecte la précision de traitement et la qualité de surface.
l Exigences strictes en matière de qualité de surface
Problème de bavures : des bavures se forment facilement pendant le traitement, ce qui affecte non seulement l'esthétique du radiateur, mais peut également gêner le flux d'air et réduire l'effet de dissipation thermique. La génération de bavures peut être causée par une faible précision de coupe du matériau, l'usure des outils de traitement, etc., et des processus d'ébavurage correspondants doivent être adoptés pour les résoudre.
Rugosité de surface : la rugosité de surface du radiateur affecte ses performances de dissipation thermique et les effets du traitement de surface ultérieur. Une rugosité de surface excessive augmentera la résistance au flux d'air et réduira l'efficacité de la dissipation thermique. Un traitement de surface supplémentaire est nécessaire pour réduire la rugosité, ce qui augmente les coûts et le temps de traitement.
l Équipements de traitement et exigences de processus élevés
Précision et stabilité de l'équipement : le pelletage des engrenages nécessite une pelleteuse de haute précision, et la précision de l'équipement affecte directement la précision dimensionnelle et la qualité de surface des dents. Dans le même temps, l'équipement doit avoir une bonne stabilité pour assurer la cohérence dimensionnelle pendant le traitement à long terme.
Sélection et usure des outils : des outils appropriés sont essentiels à la qualité du traitement. Le matériau, les paramètres géométriques, etc. de l'outil doivent être sélectionnés en fonction des propriétés du matériau. Pendant le processus de traitement, l'usure de l'outil entraînera une augmentation de la force de coupe, une diminution de la précision dimensionnelle et une augmentation de la rugosité de la surface, et l'outil devra être ajusté ou remplacé à temps.
Vitesse d'avance et profondeur de coupe : des réglages déraisonnables de la vitesse d'avance et de la profondeur de coupe peuvent facilement entraîner des défauts de traitement. Si la vitesse d'avance est trop rapide et la profondeur de coupe trop importante, l'outil sera surchargé, ce qui entraînera un arrachement de l'outil, un rebond de l'outil, une chute de l'outil, etc., affectant la précision de traitement et la qualité de surface.
Figure 2 : Processus de coupe des dents
l Exigences de personnalisation élevées
Différents scénarios d'application ont des exigences différentes en matière de taille, de forme, de hauteur de dent, d'épaisseur de dent, d'espacement de dent et d'autres paramètres du radiateur, qui doivent être personnalisés en fonction des besoins spécifiques. Cela nécessite que le fabricant de traitement dispose de capacités d'ajustement de processus flexibles et d'une riche expérience pour répondre aux divers besoins de personnalisation.
Nous mettrons régulièrement à jour les informations et technologies relatives à la conception thermique et à l’allègement. Merci de votre intérêt pour Walmate.
Avec la croissance rapide de la puissance de calcul de l'intelligence artificielle mondiale et l'augmentation continue de la consommation d'énergie thermique (TDP) des puces, la demande de refroidissement des centres de données est confrontée à des défis sans précédent. Dans le même temps, les politiques de plus en plus strictes en matière d'économie d'énergie et de réduction des émissions de carbone dans le monde entier ont encore favorisé l'innovation en matière de technologie de refroidissement. Dans ce contexte, les solutions de refroidissement par air traditionnelles sont progressivement devenues difficiles à satisfaire à la double exigence de dissipation thermique efficace et d'économie d'énergie. La technologie de refroidissement liquide progresse rapidement en raison de ses excellentes performances de dissipation thermique et de ses avantages significatifs en matière d'économie d'énergie, devenant le choix dominant pour les solutions de refroidissement des centres de données. En tant qu'équipement de base pour le traitement et le stockage des données, les performances et la stabilité du serveur sont directement liées à l'efficacité de fonctionnement de l'ensemble du système. Les composants de base du serveur, notamment la carte mère, le processeur, la mémoire, le disque dur et la carte graphique, génèrent beaucoup de chaleur en fonctionnement continu à forte charge. Si la chaleur ne peut pas être dissipée de manière opportune et efficace, cela affectera gravement les performances et la durée de vie du serveur. À cette fin, des systèmes de refroidissement liquide avancés ont été introduits dans les solutions de refroidissement des serveurs et installés directement sur les principales sources de chaleur telles que les processeurs et les cartes graphiques pour améliorer considérablement l'efficacité de la dissipation thermique.
Partie 1 : Structure et principe de fonctionnement du bloc d'eau
L'un des composants principaux du système de refroidissement liquide est le bloc d'eau, qui est généralement constitué de matériaux en cuivre ou en aluminium à haute conductivité thermique et est conçu avec des canaux d'eau précis et des structures de dissipateur de chaleur. Ces blocs d'eau s'adaptent parfaitement à la surface des sources de chaleur telles que les processeurs et les GPU, et absorbent et transfèrent rapidement la chaleur grâce à l'eau de refroidissement qui circule à l'intérieur. La chaleur est ensuite transportée vers le dissipateur de chaleur, qui circule ensuite dans le système de refroidissement par eau et finit par se dissiper dans l'air ambiant.
Figure 1 : Tendances de la consommation d'énergie thermique des principaux fabricants de puces
1- Types et caractéristiques courantes des blocs d'eau
l Bloc d'eau à microcanaux
Caractéristiques : Le bloc d'eau à microcanaux adopte une conception précise de micro-canaux d'eau. La structure du canal d'eau est fine et complexe, ce qui peut augmenter considérablement la zone de contact entre le liquide de refroidissement et les composants générateurs de chaleur, améliorant ainsi considérablement l'efficacité de la dissipation thermique. La conception du micro-canal d'eau peut également produire un fort effet de turbulence pendant l'écoulement du liquide de refroidissement, améliorant encore le coefficient de transfert de chaleur par convection et obtenant un transfert de chaleur efficace.
Scénarios d'application : Il est particulièrement adapté aux processeurs et aux GPU à forte génération de chaleur, en particulier dans le calcul haute performance, l'overclocking et les centres de données, qui ont des exigences de dissipation thermique extrêmement élevées.
l Bloc d'eau à grand débit
Caractéristiques : La structure interne du bloc d'eau à grand débit est relativement simple, utilisant généralement une plaque de cuivre ou une conception de rainure gravée, et le coût de fabrication est faible. Son principal avantage est qu'il s'appuie sur un débit d'eau à grande vitesse pour évacuer rapidement la chaleur et qu'il convient à une utilisation avec un système de refroidissement par eau à grand débit. Bien que la structure soit simple, sa capacité de dissipation thermique efficace en fait un choix très rentable.
Scénario d'application : Convient aux scénarios avec certaines exigences en matière d'efficacité de dissipation thermique mais un budget limité, tels que les systèmes informatiques DIY de milieu à haut de gamme ou les clusters de serveurs de petite et moyenne taille.
l Bloc d'eau de type injection
Caractéristiques : Le bloc de refroidissement à eau de type jet pulvérise le liquide de refroidissement d'une buse étroite vers la plaque inférieure à micro-canaux à grande vitesse à travers la plaque de guidage, formant un fort effet de turbulence et améliorant considérablement l'efficacité de la dissipation thermique. Cette conception augmente non seulement la surface de contact entre le liquide de refroidissement et la base, mais optimise également davantage les performances d'échange thermique grâce à un flux à grande vitesse.
Scénarios d'application : Convient aux processeurs et GPU hautes performances, en particulier dans les scénarios à forte dissipation thermique et à haut débit, tels que l'overclocking, la formation à l'intelligence artificielle et le rendu graphique.
2-Structure générale du bloc d'eau
Un waterblock est un bloc métallique contenant des canaux d'eau à l'intérieur, généralement en cuivre ou en aluminium. Il n'entre pas en contact avec le processeur, la carte graphique ou d'autres appareils générateurs de chaleur. Sa conception structurelle détermine directement la qualité des performances de dissipation de chaleur. Un waterblock typique se compose généralement des éléments clés suivants :
l La base est généralement constituée de matériaux à haute conductivité thermique tels que le cuivre ou l'alliage d'aluminium, et la surface est finement traitée pour assurer un contact étroit avec les composants générateurs de chaleur. La base est équipée d'une conception de canal d'écoulement complexe pour augmenter la surface de contact entre le liquide de refroidissement et la base.
l La plaque de recouvrement, avec la base, forme une cavité d'étanchéité du canal d'écoulement pour protéger le canal d'écoulement, le joint et les autres composants à l'intérieur du bloc d'eau de la poussière, des impuretés et des dommages physiques externes.
l L'entrée et la sortie d'eau sont les interfaces permettant au liquide de refroidissement d'entrer et de sortir de la tête de refroidissement par eau. Elles sont généralement conçues sur le côté ou sur le dessus de la tête de refroidissement par eau pour garantir que le liquide de refroidissement puisse entrer et sortir en douceur. La conception de la position doit tenir compte du trajet d'écoulement du fluide pour réduire la résistance à l'écoulement et augmenter le débit du liquide de refroidissement.
l Les clips sont utilisés pour fixer fermement la tête de refroidissement par eau au processeur ou à d'autres composants générateurs de chaleur afin de garantir une base solide et d'obtenir une conduction thermique efficace.
Figure 2 : Structure typique d'un bloc d'eau
3- Optimisation complète des performances de dissipation thermique
l Optimisation de la conception des canaux d'écoulement
Augmenter la surface de contact du canal d'écoulement : En concevant des canaux d'écoulement plus étroits et plus denses, la surface de contact entre le liquide de refroidissement et la base peut être considérablement augmentée, améliorant ainsi le coefficient de transfert de chaleur par convection. Par exemple, la conception du microcanal présente une structure de canal d'eau fine. Les paramètres de conception du bloc d'eau à microcanaux (tels que la largeur, la hauteur et l'espacement du canal) ont une influence décisive sur son efficacité de dissipation thermique : à mesure que la largeur du canal diminue, le coefficient de transfert de chaleur augmente considérablement, grâce à l'effet de turbulence amélioré du flux de liquide de refroidissement dans le canal étroit, améliorant ainsi l'efficacité de l'échange thermique ; la hauteur de canal plus élevée contribue à augmenter l'espace d'écoulement du liquide de refroidissement, améliorant ainsi les performances de transfert de chaleur ; l'espacement plus petit des canaux peut augmenter la surface de contact entre le liquide de refroidissement et la source de chaleur, améliorant ainsi l'efficacité de dissipation thermique.
Il peut également être optimisé en optimisant la disposition des canaux d'écoulement et en réduisant les coudes des canaux d'écoulement : une disposition raisonnable des canaux d'écoulement peut garantir que le liquide de refroidissement recouvre uniformément la surface des composants générateurs de chaleur et réduire la différence de température locale. Les coudes dans le canal d'écoulement augmentent la perte de charge et la résistance interne à l'écoulement, réduisant ainsi l'efficacité du refroidissement. Le nombre de coudes doit être réduit au minimum lors de la conception. Si cela ne peut être évité, les coudes doivent être conçus comme des transitions douces pour réduire la chute de pression et optimiser les performances d'écoulement.
l Matériaux à haute conductivité thermique : La base du bloc d'eau est généralement constituée de matériaux à haute conductivité thermique tels que le cuivre pur ou l'alliage d'aluminium. Ces matériaux peuvent transférer efficacement la chaleur de la source de chaleur au liquide de refroidissement, améliorant ainsi les performances globales de dissipation thermique.
l Optimisation des paramètres structurels, tels que l'épaisseur du substrat de base, les ailettes, la structure du spoiler, etc. L'augmentation de l'épaisseur du substrat entraînera une augmentation de la température maximale, de sorte que la conception doit trouver le meilleur équilibre entre l'effet de dissipation thermique et la résistance structurelle ; en augmentant la hauteur, l'épaisseur et l'espacement des ailettes, les performances de dissipation thermique peuvent être améliorées, mais en même temps, la résistance à l'écoulement augmentera également. Trouvez la meilleure combinaison de conception d'ailettes pour maximiser les performances de dissipation thermique. La forme de la colonne de spoiler peut améliorer efficacement l'effet de turbulence et améliorer l'efficacité de l'échange thermique.
Nous mettrons régulièrement à jour les informations et technologies relatives à la conception thermique et à l’allègement. Merci de votre intérêt pour Walmate.
Basé sur la production réelle, cet article résume les problèmes courants, les causes et les méthodes d'amélioration du processus de soudage par friction-malaxage pour votre référence.
1-Défauts de surface
(1) Rainures de surface
l Description du problème : Les rainures de surface, également appelées défauts de labour, apparaissent généralement sur la surface supérieure de la soudure, tendant vers le bord avancé de la soudure, et ont la forme de rainures.
l Cause : Le flux de métal thermoplastique autour de la soudure est insuffisant et le métal plastique de la soudure ne peut pas remplir complètement la cavité instantanée laissée par l'aiguille d'agitation pendant son mouvement.
l Méthode d'amélioration : augmenter le diamètre de l'épaulement, augmenter la pression et réduire la vitesse de soudage.
Figure 1 : Rainures
(2)Bavures de bord
l Description du problème : Des bavures apparaissent sur le bord extérieur de la soudure et sont de forme ondulée.
l Cause : Mauvaise adaptation de la vitesse de rotation et de la vitesse de soudage, pression vers le bas excessive.
l Méthode d'amélioration : Optimiser les paramètres de soudage et réduire la quantité de pression.
Figure 2 : Bavures de bord
(3)Décapage de surface
l Description du problème : Un pelage ou un filetage superficiel apparaît à la surface de la soudure sous forme de peau ou de filetage.
l Cause : Une grande quantité de chaleur générée par le frottement du métal s'accumule dans la surface du métal de la soudure, ce qui fait que le métal local à la surface atteint un état de fusion.
l Méthode d’amélioration : optimiser les paramètres de soudage, réduire la vitesse de rotation et augmenter la vitesse de soudage.
Figure 3 : Peeling de surface
(4) Cicatrice de soudure au dos
l Description du problème : Un cordon de soudure se forme à l'arrière de la soudure.
l Cause : Contrôle incorrect de la profondeur et de la pression de la tête d'agitation pendant le soudage.
l Méthode d'amélioration : Optimiser les réglages de profondeur et de pression de la tête de mélange.
2-Défauts internes
(1) Pénétration incomplète
l Description du problème : Un défaut de type « fissure » se produit lorsque le fond de la soudure n'est pas connecté ou n'est pas complètement connecté.
l Cause : L'aiguille d'agitation n'est pas assez longue, ce qui entraîne une agitation insuffisante du matériau au fond de la soudure.
l Méthode d'amélioration : Sélectionnez la longueur d'aiguille d'agitation appropriée pour garantir que le matériau sur l'épaisseur de la soudure puisse être entièrement agité.
Figure 4 : Pénétration incomplète
(2) Trous
l Description du problème : Un défaut de type « fissure » se produit lorsque le fond de la soudure n'est pas connecté ou n'est pas complètement connecté.
l Cause : Pendant le processus de soudage, en raison d'un apport de chaleur par friction insuffisant, une quantité insuffisante de matériau atteint l'état plastifié, ce qui entraîne un flux de matériau insuffisant et une fermeture incomplète de la zone de soudure.
l Méthodes d'amélioration : optimiser les paramètres de soudage, améliorer la conception de l'aiguille d'agitation et contrôler la vitesse de soudage et la vitesse de rotation.
Figure 5 : Trous
Nous mettrons régulièrement à jour les informations et technologies relatives à la conception thermique et à l’allègement. Merci de votre intérêt pour Walmate.
Récemment, l'éditeur a remarqué que de nombreuses entreprises s'intéressent au stockage d'énergie par refroidissement liquide par immersion et planifient ce type de stockage. Après une période de silence, la technologie du refroidissement liquide par immersion a de nouveau attiré l'attention et semble redevenir populaire. Je pense que de nombreux pairs prêtent également attention à cette évolution.
1- Caractéristiques de la technologie de refroidissement liquide par immersion
Les cellules de stockage d'énergie évoluent vers 300+Ah, et les systèmes de stockage d'énergie évoluent vers 5MWh+. Plus la cellule est grande, plus elle génère de chaleur, plus il est difficile de dissiper la chaleur et plus il est difficile d'assurer la cohérence de la température. De plus, le système de stockage d'énergie est composé d'un grand nombre de cellules empilées et les conditions de fonctionnement sont complexes et changeantes, ce qui est plus susceptible de provoquer une génération de chaleur inégale et une distribution de température inégale. Si les problèmes de dissipation de chaleur et d'uniformité de température ne sont pas correctement résolus, les performances de charge et de décharge, la capacité et la durée de vie de la batterie diminueront, affectant les performances de l'ensemble du système. De plus, la sécurité a toujours été l'« épée de Damoclès » suspendue au-dessus du stockage d'énergie des batteries au lithium, et le moyen le plus courant d'améliorer la sécurité est de s'orienter vers les trois dimensions de la sécurité intrinsèque, de la sécurité active et de la sécurité passive.
Le refroidissement liquide par immersion consiste à immerger la cellule de la batterie dans un liquide isolant, non toxique et dissipant la chaleur. Le liquide de refroidissement a une conductivité thermique et une capacité thermique spécifique plus élevées. Cette méthode de contact direct peut fournir une efficacité de transfert de chaleur extrêmement élevée tout en améliorant une meilleure uniformité de température. De plus, en plus d'être un moyen de contrôle de la température, le liquide de refroidissement peut également être utilisé comme fluide anti-incendie pour les systèmes de stockage d'énergie, combinant contrôle de la température et protection contre l'incendie, ce qui est également une caractéristique importante de la technologie de refroidissement par liquide par immersion. Le refroidissement par liquide par immersion présentera sans aucun doute plus d'avantages dans le contexte d'une industrie qui exige des performances de dissipation thermique plus élevées et une sécurité renforcée.
Figure 1 : Boîtier de batterie Pack à refroidissement liquide immersif
2- Solution de stockage d'énergie par refroidissement liquide immergé
En tant que branche de la technologie de refroidissement liquide, la technologie de refroidissement liquide par immersion n'est pas la première à être utilisée dans l'industrie du stockage d'énergie. Elle a été initialement utilisée dans le domaine du calcul haute performance, puis progressivement étendue aux centres de données, à l'intelligence artificielle, à la crypto-monnaie, etc.
L'intention initiale de la conception du système de stockage d'énergie par refroidissement liquide par immersion est de résoudre les lacunes du refroidissement par air traditionnel et du refroidissement liquide indirect en termes d'efficacité de refroidissement et de contrôle de la différence de température de la batterie. La mise en service officielle du projet Southern Power Grid Meizhou Baohu marque l'application réussie du refroidissement liquide par immersion, une technologie de pointe, dans le domaine de la nouvelle ingénierie de stockage d'énergie.
l Méthode de refroidissement et méthode de circulation du liquide de refroidissement
Les méthodes de refroidissement sont divisées en monophasé et à changement de phase. Le refroidissement liquide par immersion monophasé est utilisé, comprenant principalement de l'huile minérale, de l'huile de silicone, de l'ester naturel, etc. D'autres schémas utilisent le refroidissement liquide par immersion biphasé, principalement représenté par l'hydrofluoroéther, et utilisent la chaleur latente à changement de phase pour dissiper la chaleur et améliorer l'efficacité de la dissipation thermique. Selon des statistiques incomplètes, le schéma de « refroidissement par immersion monophasé » est le plus courant parmi les systèmes de stockage d'énergie par refroidissement liquide par immersion actuellement commercialisés.
Selon la différence de mode de circulation du liquide de refroidissement, il existe trois voies techniques dans le refroidissement liquide par immersion monophasé : la convection naturelle, l'entraînement par pompe et le refroidissement liquide par plaque froide couplée par immersion. La convection naturelle utilise les caractéristiques de dilatation du volume du liquide et de réduction de la densité après chauffage pour obtenir la flottaison du liquide de refroidissement chaud et son affaissement après refroidissement, complétant ainsi la dissipation thermique par circulation ; le cœur du système d'entraînement par pompe est que l'unité de refroidissement liquide entraîne le liquide de refroidissement à circuler entre la canalisation de refroidissement liquide et le boîtier d'immersion de la batterie pour compléter l'ensemble du processus de dissipation thermique par circulation ; et dans le schéma de refroidissement liquide à plaques couplées par immersion, la batterie est immergée dans le fluide diélectrique, et la plaque froide en contact avec le fluide diélectrique est utilisée pour évacuer la chaleur, évitant l'utilisation de circuits secondaires complexes pour refroidir le fluide diélectrique.
l Forme du produit et solution d'intégration
L'itération de la solution d'intégration du système de stockage d'énergie refroidi par liquide par immersion est un processus allant de l'ensemble à la partie puis aux détails. Chaque étape est optimisée et améliorée sur la base de l'étape précédente pour obtenir des performances et une sécurité supérieures.
Du niveau de la cabine au niveau du pack, la technologie d'intégration du système présente les caractéristiques de la personnalisation de la scène. La diversification des scénarios de stockage d'énergie rend la demande de systèmes de stockage d'énergie différente. Un seul produit ne peut pas répondre à la demande du marché. La conception modulaire permet d'optimiser et d'étendre les produits de stockage d'énergie en fonction de l'échelle et de la demande de puissance du projet, ce qui permet d'ajuster et de déployer rapidement les solutions de stockage d'énergie en fonction de différents scénarios d'application et besoins.
3-Défis et scénarios de mise en œuvre dans le processus d'industrialisation
Les systèmes de stockage d’énergie refroidis par liquide immergés sont confrontés à de nombreux défis au cours du processus de commercialisation, notamment la faisabilité économique, la complexité technique, l’acceptation du marché et la maturité de la chaîne industrielle.
l Complexité technique : Comparés aux systèmes de refroidissement liquide à plaque froide, les systèmes de refroidissement liquide par immersion sont plus complexes à concevoir et à mettre en œuvre.
l Maturité de la chaîne industrielle : La chaîne industrielle de la technologie du refroidissement liquide par immersion n'est pas encore totalement mature, ce qui limite son application à un plus large éventail de domaines. La maturité de la chaîne industrielle affecte directement la promotion et la commercialisation de la technologie.
l Défis économiques : L'industrie du stockage d'énergie en est encore aux premiers stades de son développement commercial et le manque de rentabilité rend difficile la promotion des technologies à coût élevé par le marché. De nombreuses entreprises rivalisent avec des prix bas pour des commandes temporaires, ce qui limite la pénétration du refroidissement liquide par immersion.
À l'heure actuelle, le marché principal de l'industrie du stockage d'énergie est toujours dominé par le refroidissement par air et le refroidissement par liquide à plaque froide, et le refroidissement par liquide par immersion n'est pas encore pleinement accepté par le marché. Bien que la pénétration du marché et l'acceptation de la technologie de refroidissement par liquide par immersion ne soient pas élevées, elle peut ne pas montrer un potentiel considérable dans certains scénarios particuliers, tels que :
l Industrie des produits chimiques dangereux : les entreprises de produits chimiques dangereux appliquent des contrôles de sécurité extrêmement stricts sur les équipements de stockage d'énergie, car la plupart des produits chimiques qu'elles produisent et stockent sont hautement inflammables, explosifs, toxiques ou corrosifs. En cas d'accident, celui-ci entraînera non seulement de graves pertes pour l'entreprise elle-même, mais pourra également entraîner une pollution de l'environnement et des dommages aux communautés environnantes.
l Stations de base et centres de données : les stations de base et les centres de données ont une faible tolérance à l'emballement thermique. Les systèmes de stockage d'énergie des centres de données doivent disposer de batteries aux performances stables et ne sont pas sujets à l'emballement thermique pour garantir la sécurité du système. Les exigences en matière de qualité de l'énergie sont élevées et le système de stockage d'énergie doit avoir une capacité de réponse rapide. En cas d'urgence telle qu'une panne de réseau ou une coupure de courant, le système de stockage d'énergie doit pouvoir passer directement en mode décharge pour assurer la continuité et la stabilité de l'alimentation électrique.
l Station de charge rapide : lors d'une charge et d'une décharge à des vitesses élevées, la batterie génère une grande quantité de chaleur en peu de temps, ce qui entraîne une température trop élevée et inégale de la batterie, ce qui constitue une menace pour les performances, la durée de vie et la sécurité de la batterie. Cela signifie que la gestion thermique de la batterie devient particulièrement importante dans les scénarios de charge et de décharge à vitesse élevée.
Nous mettrons régulièrement à jour les informations et technologies relatives à la conception thermique et à l’allègement. Merci de votre intérêt pour Walmate.
L'étanchéité à l'air du pack de batteries est un indicateur crucial dans les véhicules électriques et les systèmes de stockage d'énergie. Le test d'étanchéité à l'air du pack de batteries est principalement effectué sur la coque du pack de batteries, l'interface, le connecteur, l'ensemble de refroidissement, etc. pour garantir que l'intérieur du pack de batteries n'est pas contaminé ou envahi par des impuretés telles que la poussière et l'humidité de l'environnement extérieur, et que l'ensemble de refroidissement ne fuit pas, afin de garantir que le pack de batteries conserve des performances et une durée de vie normales, et ne provoque pas d'accidents de sécurité tels qu'un court-circuit ou une explosion.
1-Formulation standard des tests de niveau de protection et d'étanchéité des batteries
Norme de protection internationale (IEC60529), également connue sous le nom de niveau de protection contre les corps étrangers ou code IP. Le système de niveaux de protection IP (Ingress Protection) est une norme établie par la Commission électrotechnique internationale (IEC) pour classer le niveau de protection des boîtiers d'équipements électriques contre l'intrusion de corps étrangers et l'intrusion d'eau. Le niveau d'étanchéité à l'air du boîtier de la batterie doit généralement atteindre IP67 ou IP68, ce qui signifie que le boîtier de la batterie doit être complètement protégé contre la pénétration de poussière (niveau d'étanchéité à la poussière 6) et peut être immergé dans l'eau à une certaine pression pendant une période de temps sans pénétration d'eau à un niveau nocif (niveau d'étanchéité 7). Des exigences plus strictes prévoient que la batterie puisse être immergée dans de l'eau de 1 m de profondeur pendant 60 minutes sans pénétration d'eau (niveau d'étanchéité 8). Le niveau de protection IP se compose généralement de deux chiffres. Plus le nombre est élevé, plus le niveau de protection est élevé, comme le montre la figure 1 :
Figure 1 : Description du niveau de protection IP
Afin de garantir que le bloc-batterie répond aux exigences IP67 et IP68, le bloc-batterie doit être immergé dans l'eau. Cette méthode prend du temps, détruit le bloc-batterie et présente certains risques pour la sécurité. Elle ne convient pas comme test hors ligne pour les batteries d'alimentation. Par conséquent, il est devenu une pratique courante dans l'industrie d'utiliser des tests d'étanchéité à l'air pour garantir que le bloc-batterie répond aux exigences IP67 et IP68. La formulation des normes de test d'étanchéité à l'air doit prendre en compte la relation entre la valeur de chute de pression et le taux de fuite, ainsi que la relation entre l'ouverture et la fuite d'eau. La formulation des normes de test d'étanchéité à l'air implique une série d'étapes allant des extrêmes théoriques à la vérification expérimentale pour parvenir à la conversion du niveau IP aux normes de test d'étanchéité à l'air. Par exemple, en prenant l'IP68 comme exemple :
Figure 2 : Étapes de formulation des normes d'essai d'étanchéité à l'air
2- Sélection des méthodes d'essais d'étanchéité à l'air et analyse des difficultés d'essai
La conception et la qualité de fabrication du bloc-batterie sont des facteurs clés affectant l'étanchéité à l'air, notamment la solidité et la résistance du couvercle du boîtier de la batterie, l'étanchéité de la coque du bloc-batterie, les interfaces et les connecteurs, les évents antidéflagrants et l'étanchéité du connecteur électrique lui-même. De plus, certains problèmes affecteront l'étanchéité à l'air pendant l'utilisation, tels que les problèmes de dilatation et de contraction thermiques, le vieillissement du matériau, les vibrations et les impacts. Dans la production et la fabrication de coques de blocs-batteries, nous accordons plus d'attention à la mauvaise étanchéité à l'air causée par des problèmes tels que les points de soudure et la qualité des joints, tels que les points de soudure irréguliers, les soudures faibles ou fissurées, les entrefers et la mauvaise étanchéité des connexions de joint.
Le test d'étanchéité à l'air du bloc-batterie est principalement divisé en test d'étanchéité à l'air de la coque supérieure, de la coque inférieure et des pièces d'assemblage. Le test d'étanchéité à l'air des coques supérieure et inférieure doit répondre aux exigences de fuite d'étanchéité à l'air après l'assemblage. Lors de la sélection de la méthode de test d'étanchéité à l'air pour le bloc-batterie, les caractéristiques du bloc-batterie, les exigences de précision des tests, l'efficacité de la production et le coût sont généralement pris en compte de manière exhaustive.
En ingénierie, les tests de coque de batterie sont généralement divisés en tests d'étanchéité à l'air de processus et tests d'étanchéité à l'air d'expédition. De plus, les tests d'étanchéité à l'air des coques supérieure et inférieure doivent répondre aux exigences d'étanchéité à l'air après l'assemblage, ce qui impose des exigences plus strictes en matière de normes de test. Pour garantir que l'étanchéité à l'air répond aux exigences, les difficultés suivantes doivent être surmontées en fonctionnement réel :
l Stabilité de la structure du produit : la qualité des soudures, y compris les soudures en bouchon, les soudures au robinet, les soudures de poutre, les soudures de la plaque inférieure du cadre, les soudures des plaques de recouvrement avant et arrière du cadre, etc. Les problèmes de fuite de soudure sont principalement concentrés aux points de démarrage et de fin d'arc et les défauts causés par le brûlage ; les fissures causées par la contrainte de déformation de soudure, telles que le soudage des parois latérales de la cavité de la plaque inférieure, la stratification du matériau de la cavité de la plaque inférieure et l'incapacité à résister à la contrainte de déformation de soudure.
l Adaptabilité et stabilité des dispositifs de test étanches : la conception des dispositifs de test doit correspondre étroitement à la forme et aux dimensions des composants testés, garantissant que les composants peuvent être solidement fixés aux dispositifs de test pendant le processus de test, réduisant ainsi les erreurs de test causées par des décalages de position ou des vibrations. Cependant, dans la pratique, la taille et la forme des blocs-batteries varient considérablement, ce qui nécessite la conception et la fabrication de plusieurs dispositifs de test différents, ce qui augmente les coûts et la complexité opérationnelle. La conception d'un dispositif universel compliquerait encore davantage le processus de conception.
l Répétabilité des résultats des tests d'étanchéité à l'air : des facteurs tels que la pression de l'air, la température et la sécheresse de la pièce/du dispositif d'essai affecteront les résultats des tests d'étanchéité à l'air.
l Pour les pièces présentant de nombreuses petites fissures non pénétrantes, en raison de l'influence de facteurs tels que la précision de l'équipement de détection et les paramètres de détection, la source de fuite peut ne pas être découverte, ce qui entraîne une détection manquée.
Figure 3 : Outillage de test d'étanchéité à l'air
3-Combinaison de solutions de détection d'étanchéité à l'air des packs de batteries couramment utilisées en ingénierie
Le test d'étanchéité à l'air du processus de coque de la batterie comprend généralement un test d'étanchéité à l'air et un test d'immersion dans l'eau. Dans le test d'étanchéité à l'air, le couvercle supérieur du boîtier de la batterie est scellé, ne laissant qu'un port de connecteur comme entrée d'air. L'étanchéité à l'air de la batterie est jugée en contrôlant la pression d'air et en observant s'il y a des fuites d'air. Le test d'immersion dans l'eau consiste à immerger complètement l'ensemble du boîtier de batterie dans l'eau et à juger de son étanchéité à l'air en vérifiant s'il y a de l'eau dans le boîtier.
La détection des fuites d'hélium est une technologie qui utilise l'hélium comme gaz traceur pour détecter les fuites en détectant la concentration d'hélium au point de fuite. Lorsque l'hélium pénètre à l'intérieur ou à l'extérieur de l'appareil testé où il peut y avoir une fuite, s'il y a une fuite, l'hélium entrera ou s'échappera rapidement du système par la fuite et sera détecté par le spectromètre de masse. La méthode de détection des fuites d'hélium a une efficacité de détection élevée, en particulier pour détecter les petites fuites.
Figure 4 : Comparaison des méthodes de détection des fuites
En production réelle, plusieurs méthodes de détection sont généralement combinées pour améliorer l'efficacité et la précision de la détection. Par exemple, la méthode de détection des fuites à l'hélium convient à la détection de fuites de haute précision et de petite taille, tandis que la méthode de pression différentielle présente les caractéristiques d'une haute précision et d'une réponse rapide. De plus, bien que la méthode traditionnelle de détection de l'eau ait une faible précision de détection, elle est intuitive et peu coûteuse, et constitue un moyen pratique de localiser les fuites.
Nous mettrons régulièrement à jour les informations et technologies relatives à la conception thermique et à l’allègement. Merci de votre intérêt pour Walmate.
La défaillance potentielle de l'étanchéité au liquide du pack de refroidissement liquide de stockage d'énergie implique de multiples aspects, tels que : les fuites, la corrosion et le dépôt, l'eau de condensation et d'autres modes de défaillance.
1- Interconnexion et composition des fluides
Dans le système de refroidissement liquide de stockage d'énergie, l'interconnexion des fluides est responsable du transfert du liquide de refroidissement entre les différents composants. Grâce à une interconnexion efficace des fluides, le liquide de refroidissement circule efficacement dans le système, éliminant ainsi l'excès de chaleur généré pendant le processus de charge et de décharge de la batterie.
Un système bien scellé peut empêcher efficacement les fuites de liquide de refroidissement. Les fuites entraîneront non seulement une perte de liquide de refroidissement et nécessiteront un réapprovisionnement fréquent, mais affecteront également les performances de dissipation thermique et la stabilité du système. Dans le stockage d'énergie, les fuites de liquide de refroidissement peuvent également provoquer un court-circuit de la batterie, ce qui entraîne des problèmes de sécurité.
2-Conception étanche du système d'interconnexion des fluides
La conception étanche du système d'interconnexion de fluides est le lien clé pour garantir que le système maintient l'étanchéité et empêche les fuites de fluide dans diverses conditions de fonctionnement.
Figure 1 : Déploiement typique d'un système de refroidissement liquide de stockage d'énergie
(1) Analyser les sources de fuite possibles et les points de risque dans le système :
l La propriété d'auto-étanchéité de l'ensemble de refroidissement liquide. Par exemple, dans la conception intégrée du système de canaux de refroidissement liquide et du boîtier d'emballage, les composants sont reliés par soudage. Les défauts de qualité de soudage, les soudures médiocres, les pores, les fissures, etc. peuvent tous entraîner des problèmes d'infiltration de liquide.
l La conception structurelle est déraisonnable. Par exemple, les trous de positionnement ou les trous filetés du boîtier de refroidissement liquide sont trop proches du canal d'écoulement et les pièces mal soudées peuvent facilement devenir des canaux d'infiltration de liquide.
l Pièces de raccordement : Les raccords de tuyaux, les vannes et les joints du système de refroidissement liquide sont des points de fuite courants. Si la structure de raccordement n'est pas conçue correctement ou si le processus de fabrication n'est pas sophistiqué, de minuscules défauts se forment à l'intérieur des joints et le liquide de refroidissement peut également fuir à partir de ces défauts.
l Fuite causée par une mauvaise installation, le vieillissement ou l'endommagement du matériel, etc.
(2) Conception de la structure d'étanchéité :
l Le PACK refroidi par liquide utilise une méthode de refroidissement par plaque froide séparée sèche-humide. Dans des conditions de fonctionnement normales, les cellules de la batterie n'ont aucun contact avec le liquide de refroidissement, ce qui peut assurer le fonctionnement normal des cellules de la batterie. Une solution pour le refroidisseur liquide de stockage d'énergie consiste à le former par un processus d'extrusion, à intégrer le canal d'écoulement directement sur la plaque froide, puis à utiliser un traitement mécanique pour ouvrir le chemin de circulation du refroidissement. Dans ce processus, le choix du bon procédé de soudage est une étape importante pour assurer l'étanchéité. Pour plus de détails, veuillez vous référer à « Conception du procédé de soudage pour le boîtier inférieur pour le stockage d'énergie ».
l Les conduites de refroidissement liquide sont principalement utilisées pour les raccordements de tuyaux souples (rigides) de transition entre les sources de refroidissement liquide et les équipements, entre les équipements et entre les équipements et les conduites. Les principales méthodes de raccordement sont les suivantes :
Connexion rapide : L’une des méthodes de connexion pour les systèmes de refroidissement liquide de stockage d’énergie consiste à utiliser une connexion rapide VDA ou CQC.
Connexion filetée : les deux extrémités de la structure de connexion sont connectées de manière coulissante aux tuyaux, et la connexion filetée entre la bague filetée interne et le manchon fileté augmente la fermeté de la connexion.
Raccordement du tube de limitation et de l'écrou : un tube de raccordement est serré à une extrémité du tube et des tubes de limitation sont installés de manière fixe des deux côtés du tube de raccordement. Des rondelles en caoutchouc et des bagues convexes sont installées de manière fixe à l'intérieur des tubes de limitation et une rainure de bague de limitation est ouverte sur la surface de la tête du tube de raccordement. Un écrou est relié de manière rotative au sommet du tube de limitation et est relié de manière rotative au tube de limitation par des filetages.
Connexion de bague d'étanchéité : une bague d'étanchéité est collée à la paroi intérieure du manchon fileté par une colle forte, et la paroi intérieure de la bague d'étanchéité est reliée de manière mobile à la surface extérieure du tuyau pour éviter les fuites pendant l'utilisation.
(3) La plaque de refroidissement liquide PACK, l'interface de cabine, la tuyauterie de cabine, etc. sont toutes conçues avec une protection anticorrosion à long terme dans des conditions de liquide de refroidissement, de température et de débit communes pour assurer un fonctionnement à long terme sans corrosion. Effet des conditions de fonctionnement sur l'étanchéité au liquide :
l Température. Influence de la température élevée : lorsque la température augmente, la viscosité du liquide diminue généralement, ce qui peut entraîner une diminution des performances d'étanchéité du liquide, affectant ainsi l'étanchéité du liquide. Par exemple, certains matériaux d'étanchéité peuvent se déformer ou se détériorer à des températures élevées, provoquant des fuites. Influence de la basse température : dans un environnement à basse température, le liquide peut devenir visqueux, augmentant la difficulté d'écoulement, mais il peut également améliorer les performances du matériau d'étanchéité, améliorant ainsi l'étanchéité du liquide dans une certaine mesure.
l Pression. Environnement haute pression : sous haute pression, la densité et la viscosité du liquide peuvent augmenter, améliorant ainsi les performances d'étanchéité du liquide. Cependant, une pression excessive peut également endommager le matériau d'étanchéité et provoquer des fuites. Environnement basse pression : sous basse pression, les performances d'étanchéité du liquide peuvent être relativement faibles, en particulier si le matériau d'étanchéité lui-même est défectueux ou vieilli, il est plus susceptible de fuir.
l Débit. Débit élevé : lorsque le liquide s'écoule à grande vitesse, il peut produire une force d'impact importante sur la surface d'étanchéité, provoquant une usure ou une déformation du matériau d'étanchéité, affectant ainsi l'étanchéité du liquide. Faible débit : à faible débit, les performances d'étanchéité du liquide sont relativement bonnes, mais cela peut également masquer certains problèmes d'étanchéité potentiels tels que des défauts mineurs du matériau.
3-Problèmes de corrosion et de dépôt
l L'impact du blocage sur l'étanchéité à l'air :
Le liquide de refroidissement, les dépôts ou la croissance de la chaudière peuvent provoquer des blocages internes, un mauvais débit de liquide de refroidissement et une efficacité de refroidissement réduite.
Encrassement et tartre : les minéraux présents dans le liquide de refroidissement peuvent former des dépôts sur la paroi intérieure du tuyau après un fonctionnement à long terme, ce que l'on appelle « tartre ». L'encrassement peut également se former en raison de la précipitation de particules solides, de la cristallisation, de la corrosion ou de l'activité microbienne. Ces saletés obstruent les tuyaux et les plaques froides, augmentent la résistance à l'écoulement et réduisent l'efficacité du transfert de chaleur.
Problème de mousse : de la mousse peut se former dans le système de refroidissement liquide. La mousse adhère à la surface de la plaque froide, ce qui entraîne une diminution de l'effet de transfert de chaleur et peut augmenter la résistance au fonctionnement du système, provoquer une corrosion par cavitation de la pompe, etc., et endommager l'équipement.
l L'influence des courants de Foucault sur l'étanchéité à l'air :
Lorsqu'un fluide s'écoule dans un tuyau ou un espace, les changements de vitesse peuvent provoquer la formation de tourbillons, en particulier lorsque le fluide traverse des parties étroites ou des obstacles, des tourbillons sont plus susceptibles de se former. La viscosité et la densité du fluide affectent également la génération de tourbillons. Les fluides ayant une viscosité plus élevée sont plus susceptibles de former des tourbillons, tandis que les fluides ayant une densité plus élevée peuvent affaiblir la formation de tourbillons.
Chemins de fuite : les courants de Foucault forment des tourbillons sur les surfaces de contact, qui peuvent former de minuscules chemins de fuite dans des espaces ou des surfaces irrégulières, entraînant une fuite de gaz ou de liquide.
Usure de surface : l'écoulement tourbillonnaire peut provoquer l'usure des surfaces de contact, en particulier dans des conditions d'écoulement à grande vitesse. Cette usure peut réduire encore davantage l'étanchéité à l'air, car les surfaces usées sont plus susceptibles de former de nouveaux canaux de fuite.
Effets thermiques : Le flux de courants de Foucault génère de la chaleur, ce qui peut provoquer une déformation ou une dilatation thermique du matériau de la surface de contact, affectant ainsi l'étanchéité à l'air, en particulier dans les systèmes soumis à de grandes variations de température.
4-Problème d'eau de condensation
Français Dans certaines conditions, de la condensation peut se former dans les conduites de refroidissement liquide, ce qui peut endommager l'équipement ou réduire l'efficacité. Défaillance de l'isolation : Si le matériau isolant du tuyau est endommagé ou vieilli, de la chaleur sera perdue et l'effet de refroidissement sera affecté. En particulier dans les environnements à basse température, une défaillance de l'isolation peut provoquer la formation de givre ou de glace à la surface du tuyau. Fissuration par le gel : Dans les environnements froids, si des mesures antigel appropriées ne sont pas prises, le liquide de refroidissement dans les tuyaux peut geler et provoquer la rupture des tuyaux.
Solutions
l Mesures d'étanchéité : Assurez-vous que l'entrée et la sortie du tuyau de refroidissement liquide sont complètement bloquées pour empêcher l'air humide extérieur de pénétrer dans le compartiment de la batterie.
l Équipement de déshumidification : Installez un climatiseur déshumidifiant ou utilisez la fonction de déshumidification pour maintenir l'humidité dans le compartiment de la batterie dans une plage appropriée.
l Contrôle de la température : En installant des systèmes de climatisation ou de ventilation, la température et l'humidité de l'environnement dans lequel se trouve l'armoire de stockage d'énergie peuvent être contrôlées. Par exemple, la température peut être maintenue à 20-25 degrés Celsius et l'humidité relative peut être contrôlée à 40-60 %.
l Isolation measures: Simple isolation of empty battery racks to prevent moisture from entering the compartment containing the battery cluster.
Nous mettrons régulièrement à jour les informations et technologies relatives à la conception thermique et à l’allègement. Merci de votre intérêt pour Walmate.
La conception entièrement étanche du pack de stockage d'énergie est la clé pour assurer sa sécurité et son fonctionnement stable à long terme. L'étanchéité consiste essentiellement à utiliser un dispositif pour fermer (sceller) un espace ou rendre un joint étanche. La conception entièrement étanche peut empêcher efficacement les fuites de liquide et de gaz à l'intérieur de la cellule de batterie, ce qui est essentiel pour assurer le fonctionnement sûr et stable du système de stockage d'énergie. Par conséquent, lors de la conception, l'étanchéité à l'air et l'étanchéité du milieu liquide doivent être prises en compte.
En fonctionnement réel, la conception de l'étanchéité du pack de stockage d'énergie doit prendre en compte de manière exhaustive de nombreux facteurs tels que les matériaux, les processus, les équipements de test, les conditions environnementales et les processus de fabrication pour garantir que ses performances d'étanchéité peuvent répondre aux normes attendues. Cet article explique la pratique d'application et les points clés de la conception de l'étanchéité du pack de stockage d'énergie dans l'ingénierie réelle sous les aspects de l'étanchéité à l'air du boîtier du pack, de l'étanchéité au liquide du cycle de refroidissement liquide et du fluide de refroidissement liquide.
Partie supérieure : Conception de l'étanchéité du boîtier de pack de stockage d'énergie
La conception de l'étanchéité permet de maintenir la température et la pression à l'intérieur du bloc de stockage d'énergie stables, ce qui joue un rôle clé dans le fonctionnement normal et les performances de la batterie. De plus, la conception de l'étanchéité peut réduire l'impact de l'environnement externe sur la batterie interne, comme l'humidité, la poussière et d'autres polluants, etc., améliorant ainsi la fiabilité et la durée de vie du système. De plus, l'utilisation de matériaux et de structures d'étanchéité appropriés peut améliorer efficacement la résistance à l'usure et au vieillissement des joints, améliorer la durabilité de l'ensemble du système de stockage d'énergie et réduire les coûts de maintenance.
L'idée générale de la conception étanche à l'air est d'analyser la structure de la boîte pour découvrir les zones clés où des fuites peuvent exister, puis de prendre des mesures ciblées en fonction des performances spécifiques et des exigences fonctionnelles des différentes zones.
1-analyse de la structure de la boîte
Le boîtier n'est pas seulement le support physique des modules de batterie et des composants électriques, mais aussi une garantie importante pour le fonctionnement sûr et fiable de l'ensemble du système de stockage d'énergie. Il s'agit du « squelette » du pack de stockage d'énergie, qui est généralement composé d'un couvercle supérieur, d'un boîtier inférieur, de composants de support, de pièces d'étanchéité et de boulons, etc.
Figure 1 : Schéma du boîtier de stockage d'énergie et zones clés sur lesquelles se concentrer dans la conception de l'étanchéité (par exemple, indiquées par des flèches rouges)
Comme le montre la figure ci-dessus, déterminez où des fuites potentielles peuvent se produire :
l Points de connexion de plusieurs pièces, tels que : l'interface d'assemblage entre le couvercle supérieur et le boîtier inférieur, l'interface d'installation entre les connecteurs haute et basse tension et le boîtier, l'interface d'installation entre les composants exposés et le boîtier de batterie, etc.
l Si des boulons sont utilisés pour la connexion, il peut également y avoir un risque de fuite au niveau du point d'installation et de fixation, comme l'interface électrique et l'interface d'installation du panneau avant du boîtier.
l Il ne doit y avoir aucun trou ni espace dans le couvercle supérieur et le corps inférieur de la boîte pour assurer l'étanchéité et les performances de protection de la boîte.
Figure 2 : Boîtier inférieur de refroidissement liquide par immersion (cadre en tôle + plaque inférieure de refroidissement liquide en aluminium)
2- Conception d'étanchéité de l'interface d'installation entre le couvercle supérieur et le boîtier inférieur
Le couvercle supérieur peut généralement être divisé en deux types : type plat et type de forme spéciale. Leurs caractéristiques structurelles sont également différentes. Par exemple, matériau composite SMC, aluminium, quel que soit le matériau, afin de réduire la complexité de la structure auto-obturante, le couvercle supérieur de la coque de la batterie Le couvercle est généralement de conception monobloc. De plus, les exigences d'ouverture du couvercle supérieur doivent également répondre aux exigences de l'interface et doivent être indépendantes de l'interface d'étanchéité pour réduire l'impact sur l'étanchéité du bloc-batterie. La conception du joint du couvercle supérieur suit généralement les principes suivants :
l La conception des pièces intégrées est adoptée pour éviter la conception de pièces séparées, garantissant ainsi la stabilité des performances « auto-obturantes » du couvercle supérieur.
l Les trous de positionnement et les dispositifs de positionnement sont conçus sur le bord du couvercle supérieur (à l'extérieur de l'interface d'étanchéité entre le couvercle supérieur et le plateau inférieur).
l L'interface d'étanchéité entre le couvercle supérieur et le corps inférieur du boîtier nécessite une surface correspondante pour répondre aux exigences d'étanchéité « uniforme » et « continue ».
Actuellement, les solutions courantes pour le boîtier inférieur du pack de stockage d'énergie sont : boîtier en tôle + plaque de refroidissement liquide, boîtier moulé sous pression + plaque de refroidissement liquide, boîtier intégré profilé, boîtier intégré moulé sous pression, etc. Parmi elles, le boîtier intégré profilé et d'autres solutions En revanche, il présente les avantages d'une bonne capacité portante du canal d'écoulement et d'un faible coût d'ouverture du moule, et est largement utilisé. Le choix du procédé de soudage a une grande influence sur les performances d'étanchéité. Pour les soudures de différents matériaux et épaisseurs, le choix d'une méthode de soudage appropriée peut améliorer efficacement la qualité de la soudure pour garantir la résistance globale et les performances d'étanchéité du système.
De plus, la conception de l'étanchéité du boîtier inférieur doit suivre les principes d'étanchéité suivants :
l Pour la construction du cadre, on utilise des profilés à section fermée et au niveau des joints, on utilise une technologie de connexion linéaire auto-étanche, telle que la technologie de soudage CMT.
l Les plateaux de batteries constitués de profilés en aluminium doivent être conçus avec une ou plusieurs couches continues de colloïde d'étanchéité.
l Dans le cas d'une plaque de refroidissement liquide intégrée dans le boîtier inférieur, il est nécessaire d'envisager l'utilisation de joints colloïdaux ou de technologies de connexion linéaire auto-obturantes, telles que la technologie de soudage par friction-malaxage FSW.
l L'interface d'étanchéité entre le couvercle supérieur et le corps inférieur du boîtier doit être dotée d'une surface adaptée pour répondre aux exigences d'étanchéité « uniforme » et « continue ». Si nécessaire, l'interface d'étanchéité doit être usinée et polie.
Figure 3 : Formes d'étanchéité courantes entre le couvercle supérieur et le boîtier inférieur
Habituellement, le couvercle supérieur et le boîtier inférieur du boîtier de stockage d'énergie adoptent une conception à bride courbée et à joint d'étanchéité, comme illustré dans la figure 2. Le couvercle supérieur, le corps du boîtier inférieur et le joint d'étanchéité sont entièrement compactés et couplés par des boulons de fixation pour garantir que le boîtier de stockage d'énergie répond aux exigences pertinentes de l'IP67.
3- Conception d'étanchéité des interfaces électriques et de communication et de l'interface d'installation du panneau avant du boîtier inférieur
Le panneau avant du boîtier (comme illustré dans la figure 3) est usiné avec des trous sur le profil extrudé pour l'installation d'interfaces électriques et de communication afin de réaliser des fonctions telles que la transmission de courant, l'interaction de communication et le contrôle de sécurité.
Figure 4 : Interface électrique, interface de communication et interface d'installation du panneau avant de l'armoire inférieure
L'étanchéité à l'air de l'interface d'installation entre le boîtier et les interfaces électriques, de communication et autres doit suivre les principes suivants :
l La forme de l’interface est conçue pour être profilée afin de réduire la possibilité d’accumulation et de pénétration de gaz et de liquide à l’interface.
l L'alignement précis évite les écarts causés par un mauvais alignement des interfaces lors de l'installation.
l Pré-sceller l'interface avant l'installation et ajouter des tampons anti-vibrations ou des produits d'étanchéité pour améliorer l'effet d'étanchéité initial ou réduire les défaillances d'étanchéité causées par les vibrations.
De plus, en termes de sélection des fixations, des fixations à haute résistance et à couple élevé sont utilisées et elles sont serrées plusieurs fois pendant le processus d'installation pour assurer l'étanchéité de l'interface. Par exemple, si un écrou à souder bout à bout est utilisé, sa caractéristique est qu'il peut être directement connecté au trou de paroi de la partie connectée (le panneau avant du boîtier) pour le soudage bout à bout. Cette conception structurelle peut améliorer considérablement l'étanchéité à l'air de la partie de connexion.
Figure 5 : Utilisation d'écrous soudés bout à bout pour augmenter l'étanchéité à l'air
4-Choix des joints d'étanchéité
La conception et la sélection des joints sont essentielles car elles affectent directement la fiabilité et la durée de vie du système. Voici les facteurs clés à prendre en compte lors de la conception et de la sélection des joints pour les systèmes de refroidissement liquide de stockage d'énergie :
l Le matériau d'étanchéité doit avoir une certaine compatibilité chimique et de pression et être capable de résister à la plage de températures de fonctionnement du système, y compris les environnements à haute et basse température. Le choix du matériau du joint dépend de l'environnement d'utilisation et des exigences de durée de vie. Les matériaux d'étanchéité courants comprennent le caoutchouc, le polytétrafluoroéthylène (PTFE), le nylon, le métal, etc.
l Absence de fuite : le joint doit pouvoir s'adapter à la légère déformation qui peut survenir dans le système pendant le fonctionnement afin de garantir une bonne étanchéité dans diverses conditions de travail. En général, la déformation du joint doit être supérieure à 30 % et inférieure à 60 %, et la pression de l'interface d'étanchéité doit être supérieure à 30 kPa.
Nous mettrons régulièrement à jour les informations et technologies relatives à la conception thermique et à l’allègement. Merci de votre intérêt pour Walmate.
SIMULATION FLUIDE
Utilisation de logiciels de simulation pour analyser les performances thermiques des radiateurs et des plaques froides.
Scénario d'application
Technologie: Soudure sur mesure de profils en aluminium
Disposition et installation: Refroidissement liquide par le bas
Application typique: Personnalisation client
Caractéristique: poids léger, bon effet de refroidissement
Scénario d'application
Technologie: Soudure sur mesure de profils en aluminium
Disposition et installation: Refroidissement liquide par le bas
Application typique: Personnalisation client
Caractéristique: poids léger, bon effet de refroidissement
Le liquide de refroidissement circule à travers les tuyaux entraîné par une pompe. Lorsque le liquide de refroidissement circule à travers l'échangeur de chaleur à l'intérieur du serveur, il échange de la chaleur avec des composants à haute température (comme le CPU et le GPU) pour évacuer la chaleur.
Lori is a heat sink manufacturer of design and manufacturing high power heat sink, we have provided innovative thermal solutions for many high power industry device such as Aerospace industry,Medical, Communication server, Consumer Electronics etc. Our solutions include high power heat pipe thermal mould, liquid cooling system, staked fin heat sink solution etc.
Lori is a heat sink manufacturer of design and manufacturing high power heat sink, we have provided innovative thermal solutions for many high power industry device such as Aerospace industry,Medical, Communication server, Consumer Electronics etc. Our solutions include high power heat pipe thermal mould, liquid cooling system, staked fin heat sink solution etc.
Lori is a heat sink manufacturer of design and manufacturing high power heat sink, we have provided innovative thermal solutions for many high power industry device such as Aerospace industry,Medical, Communication server, Consumer Electronics etc. Our solutions include high power heat pipe thermal mould, liquid cooling system, staked fin heat sink solution etc.
Principe de base de la solution de refroidissement liquide : Le refroidissement liquide utilise un liquide comme réfrigérant, utilisant le flux de liquide pour transférer la chaleur générée par les composants internes de l'équipement informatique du centre de données vers l'extérieur de l'équipement, de sorte que les composants chauffants de l'équipement informatique les équipements peuvent être refroidis, ce qui permet une technologie qui garantit le fonctionnement sûr des équipements informatiques.
Avantages du refroidissement liquide : Le refroidissement liquide offre une efficacité énergétique ultra-élevée et une densité thermique ultra-élevée, permettant une dissipation de chaleur efficace qui n'est pas affectée par l'altitude, la localisation ou les variations de température.
La solution de refroidissement liquide à plaque froide de transfert de chaleur de Walmate:
Le refroidissement liquide à plaque froide est une forme de dissipation de chaleur qui transfère indirectement la chaleur des dispositifs chauffants à un liquide de refroidissement enfermé dans un circuit de circulation, à travers des plaques de refroidissement liquide (généralement en métaux thermiquement conducteurs comme le cuivre ou l'aluminium). Le liquide de refroidissement évacue ensuite la chaleur. La solution de refroidissement liquide à plaque froide présente le plus haut niveau de maturité technologique. C'est une solution efficace pour déployer des équipements à forte puissance, améliorer l'efficacité énergétique, réduire les coûts de fonctionnement du refroidissement et diminuer le TCO (Coût Total de Possession).
La haute consommation d'énergie et la haute densité représentent l'avenir des centres de données, et le refroidissement liquide deviendra la solution principale pour le refroidissement des serveurs IA.