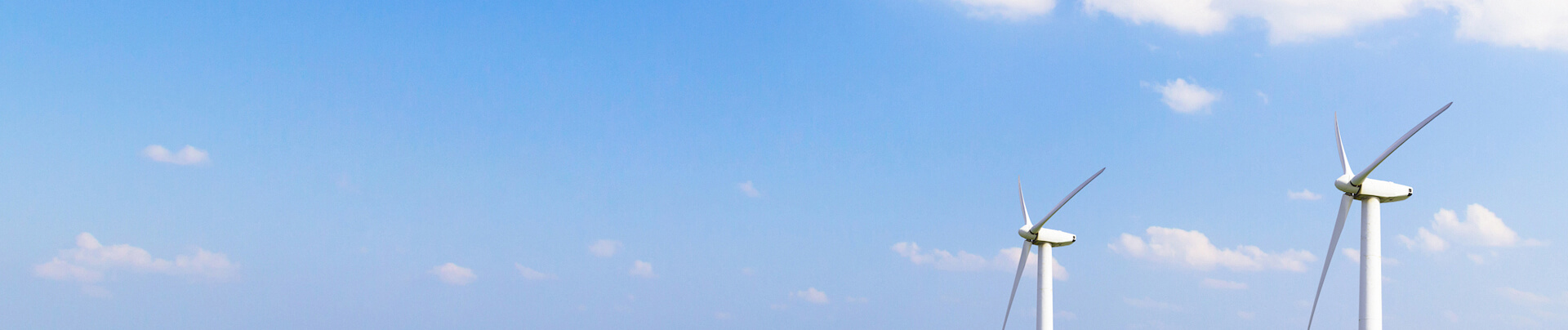
aziendali e a lavorare duramente per
migliorare i benefici dei tuoi progetti
Con l'evoluzione dei sistemi di accumulo di energia verso grandi capacità e un'elevata densità energetica, la progettazione di alloggiamenti per batterie ESS (Electronic Storage Enclosure) e la compatibilità dimensionale sono diventate questioni fondamentali per migliorare l'efficienza e l'affidabilità del sistema. Questo articolo combina i più recenti casi di progettazione ingegneristica, tecnologie brevettate e tendenze del settore per analizzare tre dimensioni: utilizzo dello spazio, compatibilità modulare e progettazione della disposizione e del supporto delle celle.
1- Ottimizzazione dell'utilizzo dello spazio
Il miglioramento dell'utilizzo dello spazio nell'integrazione dei sistemi di accumulo di energia è essenzialmente un processo bidirezionale di iterazione tecnologica e requisiti di scenario. Attraverso l'innovazione collaborativa di tecnologie come le celle per batterie ad alta capacità, l'architettura modulare e l'integrazione del raffreddamento a liquido, il settore sta passando dallo "stacking esteso" al "riutilizzo estremo dello spazio".
a. Applicazione di celle per batterie ad alta capacità: aumento della densità energetica e dell'efficienza
Riepilogo delle idee: L'applicazione di celle per batterie ad alta capacità mira essenzialmente a ridurre il livello strutturale interno del pacco batteria e a migliorare direttamente l'utilizzo dello spazio tra cella e pacco batteria. I pacchi batteria tradizionali adottano una modalità di integrazione a tre livelli: "cella batteria → modulo → pacco batteria", e la struttura del modulo (trave trasversale, trave longitudinale, bulloni, ecc.) riduce l'utilizzo dello spazio. Le celle di batterie ad alta capacità possono saltare direttamente il livello del modulo allungando o aumentando il volume della singola cella e utilizzare la tecnologia CTP (Cell to Pack) per integrare direttamente la cella della batteria nel pacco batteria.
Tecnica di base: utilizzare celle di batterie ultra-large da 600 Ah+ per ridurre il numero di celle e punti di connessione e aumentare la capacità della singola cella.
b. Riutilizzo spaziale e ottimizzazione dei costi: dall'"impilamento dei componenti" al "riutilizzo multidimensionale"
Riepilogo delle idee: Il riutilizzo spaziale e l'ottimizzazione dei costi sono due facce della stessa medaglia e la loro logica di fondo è quella di superare i limiti fisici e di costo dei sistemi di accumulo di energia tradizionali attraverso la semplificazione strutturale, l'integrazione funzionale, l'iterazione dei materiali e la progettazione standardizzata.
Il fulcro del riutilizzo spaziale è la riduzione dei collegamenti intermedi attraverso l'estrema semplificazione del livello strutturale. Ad esempio: il design due in uno della scatola ad alta tensione: la tecnologia brevettata di Jiangsu Trina Energy Storage combina due scatole ad alta tensione in una, condividendo il relè positivo/negativo totale e la connessione elettrica, riducendo l'occupazione dello spazio orizzontale del 30% e il costo dei componenti elettrici del 15%. Riutilizzo interdominio di moduli funzionali, integrazione di componenti strutturali e canali di dissipazione del calore, come l'integrazione della piastra di raffreddamento a liquido con la piastra inferiore del box e la condivisione dello spazio tra il tubo di raffreddamento a liquido e il supporto strutturale, riducendo del 15% i componenti indipendenti di dissipazione del calore; il corpo della batteria come parte strutturale: la batteria a lama di BYD fornisce un supporto robusto grazie alle pareti laterali lunghe e sottili della cella, eliminando il telaio del modulo e aumentando il tasso di utilizzo dello spazio al 60%-80%.
Una profonda ottimizzazione della topologia elettrica, ad esempio la topologia a cascata ad alta tensione, riduce il numero di circuiti paralleli aumentando la capacità e il livello di tensione delle singole celle (come nel caso dell'accumulo di energia a stringa intelligente di Huawei), riducendo lo spazio fisico dello stack di batterie del 20% e accorciando il tempo di risposta del sistema del 50%. Progettazione a relè condiviso: il box ad alta tensione due in uno di Jiangsu Trina Energy Storage consente a due linee di condividere lo stesso relè, riducendo del 50% il numero di relè e la lunghezza dei cavi e migliorando l'efficienza di installazione del 30%.
2- Disposizione delle celle e progettazione del supporto: bilanciamento tra capacità portante, dissipazione del calore e resistenza alle vibrazioni
L'essenza della disposizione delle celle risiede nel gioco tra utilizzo dello spazio, distribuzione del calore e stabilità meccanica. La forma fisica e la direzione di disposizione della cella influiscono direttamente sull'efficienza di riempimento dello spazio:
a. Ottimizzare la disposizione delle celle
Design della cella invertito: ruotare la valvola antideflagrante della cella verso il basso, in modo che lo scarico termico in fuga e lo spazio inferiore a prova di esplosione siano condivisi, liberando lo spazio in altezza della cella e ottenendo un utilizzo del volume ottimale.
Disposizione delle celle disposte orizzontalmente: ottimizzare l'utilizzo dello spazio in altezza del pacco batteria, aumentare la percentuale di materiali attivi e aumentare significativamente il tasso di utilizzo del volume rispetto alla cella verticale.
Celle ultra lunghe e sottili: ridurre il numero di celle per unità di volume grazie alla lunghezza e allo spessore ridotti delle celle, migliorando l'efficienza di raggruppamento.
b. Progettazione combinata di dissipazione del calore e capacità portante: mira a ottenere una duplice ottimizzazione dell'efficienza di dissipazione del calore e della resistenza strutturale attraverso l'innovazione collaborativa di struttura, materiali e processi. Percorso di progettazione strutturale:
Struttura integrata, come la progettazione conforme della piastra di raffreddamento a liquido e della trave di supporto: integrazione del canale di raffreddamento a liquido nella trave di supporto in lega di alluminio per ridurre i componenti indipendenti e migliorare l'utilizzo dello spazio;
Layout a strati e compartimentato, impilando il pacco batteria, il sistema di raffreddamento a liquido e il BMS a strati per ridurre l'interferenza reciproca tra flusso di calore e stress meccanico;
Ottimizzazione della meccanica bionica, come la struttura a nido d'ape/ondulata, progettazione di uno strato di nucleo a nido d'ape o ondulato nel telaio di supporto in lega di alluminio (come la soluzione brevettata Mufeng.com), assorbimento dell'energia delle vibrazioni tramite deformazione e ottimizzazione del percorso di dissipazione del calore.
Percorso di innovazione dei materiali:
Conduzione del calore e supporto del carico integrati, come il materiale composito in fibra di lega di alluminio (conduttività termica ≥ 200 W/m·K, resistenza +30%); materiale intelligente, lo strato di riempimento a cambiamento di fase (PCM) assorbe il calore e lo rilascia lentamente, differenza di temperatura ±1,5℃; smorzamento leggero: il cuscinetto elastico in silicone assorbe le vibrazioni (smorzamento +40%). Percorso di implementazione del processo:
Processo di stampaggio di precisione, come lo stampaggio per estrusione: utilizzato per la produzione di travi in lega di alluminio raffreddate a liquido con canali di flusso complessi;
Tecnologia di trattamento superficiale, come la generazione di uno strato di ossido ceramico sulla superficie della lega di alluminio per migliorare la resistenza alla corrosione (test in nebbia salina ≥1000 ore), migliorando al contempo l'efficienza di dissipazione del calore (emissività superficiale aumentata del 20%);
Processo di assemblaggio intelligente, regolazione dinamica del precarico, come l'integrazione di sensori di pressione e attuatori elettrici per regolare il precarico dei bulloni (5-20 kN) in tempo reale, evitando danni da sovrapressione alla cella della batteria.
c. Progettazione coordinata della resistenza al carico e alle vibrazioni della struttura di supporto: il sistema di supporto deve soddisfare il duplice requisito di resistenza al carico statico (peso della cella della batteria + pressione di impilamento) e di resistenza dinamica alle vibrazioni (trasporto/shock sismico).
3- Modularità e compatibilità: interfaccia standardizzata e architettura scalabile
L'essenza dell'interfaccia standardizzata che si adatta a batterie multi-dimensione è quella di ottenere un'espansione flessibile delle specifiche della batteria su una piattaforma unificata attraverso l'innovazione collaborativa nella gestione meccanica, elettrica e termica. La tecnologia attuale è passata dalla compatibilità statica alla regolazione dinamica e in futuro evolverà verso intelligenza, leggerezza e integrazione multi-scenario.
a. Innovazione collaborativa della struttura meccanica:
Standardizzazione dell'interfaccia meccanica: definire le dimensioni unificate del dispositivo di connessione.
Progettazione modulare di pacchi/armadi batteria: realizzare moduli e armadi batteria scalabili tramite celle di dimensioni standardizzate (come batterie da 280 Ah, 314 Ah), supportando combinazioni flessibili di diversi requisiti di capacità.
Figura 1-Contenitore per batteria ESS da 280 Ah
b. Regolazione dinamica del sistema elettrico
Protocolli e interfacce di comunicazione standardizzati, come la compatibilità con i sistemi BMS: formulare un protocollo di comunicazione BMS (sistema di gestione della batteria) unificato per supportare una connessione fluida con PCS e celle di batteria di diversi produttori; regolazione dinamica della potenza, attraverso il controllo dell'inerzia virtuale e un algoritmo di ottimizzazione multi-scala temporale, per ottenere una regolazione in tempo reale della potenza attiva/reattiva; e progettazione adattiva dell'abbinamento dei parametri elettrici.
c. Adattamento intelligente del sistema di gestione termica
Soluzioni di gestione termica graduali, come l'utilizzo di schiuma ignifuga ad alto rimbalzo, colla termoconduttiva e altri materiali a livello di batteria per bilanciare i requisiti di isolamento e dissipazione del calore e inibire la diffusione del calore; progettazione integrata della piastra di raffreddamento a liquido integrata a livello di modulo e dello strato isolante per migliorare la durata del ciclo; a livello di sistema, la capacità di raffreddamento viene regolata dinamicamente tramite compressori a frequenza variabile e più rami di raffreddamento.
Monitoraggio e previsione intelligenti, fusione multi-sensore. Posizionamento dei sensori di temperatura in punti chiave come i poli della batteria e ampie superfici per ottenere un'acquisizione della temperatura ad alta precisione; La tecnologia Digital Twin ottimizza la strategia di dissipazione del calore in tempo reale tramite monitoraggio cloud e manutenzione predittiva.
4-Riepilogo
L'ottimizzazione dello spazio degli alloggiamenti per batterie ESS è passata da un singolo miglioramento strutturale a un'innovazione collaborativa multidimensionale:
La fusione di materiali, struttura e algoritmi, come la combinazione di alloggiamento in fibra di carbonio + tecnologia CTP + algoritmo di layout basato sull'intelligenza artificiale, diventerà la norma.
La modularizzazione e la standardizzazione stanno accelerando e il design standardizzato, che vede il pacco batteria come unità funzionale più piccola, promuoverà la riduzione dei costi e l'aumento dell'efficienza nel settore.
La stretta correlazione tra gestione termica e utilizzo dello spazio, il raffreddamento a liquido a immersione e la tecnologia di controllo dinamico della temperatura liberano ulteriormente il potenziale dello spazio.
Condivideremo regolarmente aggiornamenti e informazioni su tecniche di progettazione termica e alleggerimento, per la vostra consultazione. Grazie per l'interesse verso Walmate.
Con la crescita esponenziale della potenza di calcolo dell'intelligenza artificiale e il continuo aumento della densità di potenza dei data center, la tradizionale tecnologia di raffreddamento ad aria non è più in grado di soddisfare le esigenze di dissipazione del calore. La tecnologia di raffreddamento a liquido è diventata indispensabile per i suoi vantaggi quali l'efficiente dissipazione del calore, il risparmio energetico e la riduzione dei consumi. Nella tecnologia di raffreddamento a liquido, la concorrenza tra piastra fredda e immersione è particolarmente agguerrita. Questo articolo analizzerà i vantaggi e gli svantaggi di entrambi dal punto di vista delle caratteristiche tecniche, degli scenari applicativi, del rapporto costo-efficacia e delle tendenze future, esplorerà le loro direzioni dominanti in futuro.
1- Confronto delle caratteristiche tecniche: il tipo a piastra fredda ha una forte compatibilità e il tipo a immersione ha una maggiore efficienza di dissipazione del calore
UN. Raffreddamento a liquido a piastra fredda: un "riformista" con transizione graduale
Elevata compatibilità: non è necessario modificare in modo significativo la struttura del server, è compatibile con l'infrastruttura del data center raffreddato ad aria esistente, con bassi costi di modifica e ciclo breve.
Elevata sicurezza: il refrigerante non entra in contatto diretto con i componenti elettronici, il rischio di perdite è basso e può essere ulteriormente ridotto grazie alla progettazione modulare (ad esempio giunti a sgancio rapido e tubi ridondanti).
Elevata maturità: la tecnologia Cold Plate è stata ampiamente utilizzata in scenari quali Alibaba Cloud Qiandao Lake Data Center e progetti di cooperazione Intel, rappresentando il 90% dell'attuale mercato del raffreddamento a liquido.
Limitazioni: il tipo cold plate riesce a coprire solo alcuni componenti ad alta potenza (come CPU e GPU), mentre il resto del calore deve comunque fare affidamento sul raffreddamento ad aria per favorire la dissipazione del calore. Il valore PUE è solitamente compreso tra 1,1 e 1,2, leggermente superiore a quello del tipo a immersione.
B. Raffreddamento a liquido ad immersione: un "innovatore" con efficiente dissipazione del calore
Il raffreddamento a liquido a immersione immerge completamente il server nel refrigerante isolante e consente la completa dissipazione del calore del dispositivo tramite contatto diretto. I suoi principali vantaggi includono:
Efficienza energetica estrema: la conduttività termica del liquido è 20-30 volte superiore a quella dell'aria, il PUE può arrivare fino a 1,05 e l'efficienza di dissipazione del calore aumenta di oltre 3 volte.
Risparmio di spazio: il volume del sistema di raffreddamento è solo 1/3 di quello del raffreddamento ad aria e la densità di potenza di un singolo cabinet può raggiungere più di 50 kW, il che è adatto a scenari ad alta densità come il supercomputing AI.
Silenzioso ed ecologico: non sono necessarie ventole, il rumore è ridotto di oltre il 90% e non c'è inquinamento da polvere, il che prolunga la durata dell'apparecchiatura.
Sfide: l'immersione richiede server personalizzati, il costo del refrigerante può arrivare fino al 60% (ad esempio il liquido fluorurato), l'investimento iniziale è elevato e la compatibilità ecologica deve essere migliorata.
2- Differenziazione dello scenario applicativo: prevale il raffreddamento a liquido a piastra fredda a medio e breve termine, viene liberato il potenziale di raffreddamento a liquido a immersione a lungo termine
UN. Raffreddamento a liquido con piastra fredda: una scelta conveniente per la ristrutturazione di IDC esistenti e la costruzione di nuovi IDC
Ristrutturazione di vecchi data center: il raffreddamento a liquido con piastra fredda può essere adattato rapidamente all'architettura raffreddata ad aria esistente, con un breve ciclo di ristrutturazione e costi controllabili. Ad esempio, la soluzione modulare su cui hanno collaborato Intel e Bich riduce le difficoltà di implementazione tramite una progettazione standardizzata della piastra fredda.
Scenari di elaborazione a media e alta densità: il raffreddamento a liquido cold plate supporta già 130-250 kW di potenza per cabinet (come le GPU NVIDIA serie B), soddisfacendo la maggior parte delle esigenze di formazione dell'intelligenza artificiale.
B. Raffreddamento a liquido a immersione: la soluzione definitiva per supercomputing e data center ecologici
Potenza di calcolo ad altissima densità: la potenza dei cabinet dei chip di prossima generazione (come la serie Rubin di NVIDIA) supererà i 1000 kW e il raffreddamento a liquido a immersione diventerà l'unica soluzione praticabile.
Esigenze di risparmio energetico: il PUE del raffreddamento a liquido a immersione è prossimo a 1,05 e l'efficienza di recupero del calore di scarto raggiunge il 90% (come la soluzione di Lenovo), in linea con la politica di obiettivi "dual carbon".
C. Situazione attuale del mercato
Il raffreddamento a liquido con piastra fredda domina il mercato attuale: nel 2025, il raffreddamento a liquido con piastra fredda rappresenterà l'80%-90% del mercato del raffreddamento a liquido, mentre il raffreddamento a liquido a immersione rappresenterà meno del 10%. Inoltre, sono state create interfacce standardizzate (come il design della piastra fredda OCP di Intel) e le soluzioni di produttori come Inspur e Sugon sono altamente compatibili. Il progetto cinese "East Data West Computing" richiede che il PUE dei data center di nuova costruzione sia ≤1,25 e il raffreddamento a liquido cold plate diventa la prima scelta per la transizione.
Il raffreddamento a liquido a immersione è pronto: la soluzione a immersione con cambio di fase Sugon C8000 raggiunge un PUE di 1,04 e il data center "Kirin" di Alibaba Cloud verifica la fattibilità del raffreddamento a liquido a immersione monofase. I chip ad alta potenza come la GPU NVIDIA B200 (1000 W+) hanno favorito l'uso della tecnologia immersiva, aumentando la densità di potenza di calcolo del raffreddamento a liquido del 30%-50%. L’UE prevede di vietare i liquidi fluorurati nel 2028 e la ricerca e lo sviluppo di refrigeranti nazionali a base di idrocarburi/oli siliconici hanno subito un’accelerazione (come la serie “Kunlun” di Sinopec).
3-Parere autorevole PK
Raffreddamento a liquido con piastra fredda: il raffreddamento a liquido con piastra fredda è il "rompighiaccio" per la diffusione del raffreddamento a liquido. Nei prossimi cinque anni rappresenterà ancora l'80% del mercato incrementale del raffreddamento a liquido. Il raffreddamento a liquido a immersione deve attendere che il consumo energetico del chip superi il punto critico.
Fazione di raffreddamento a liquido a immersione: il raffreddamento a liquido a immersione con cambiamento di fase è la forma definitiva di raffreddamento a liquido, mentre il raffreddamento a liquido con piastra fredda è solo una soluzione transitoria. Quando il consumo energetico di un singolo chip supera gli 800 W, il raffreddamento a liquido a immersione diventa l'unica opzione.
Neutrali: la differenziazione dei percorsi tecnici riflette la stratificazione della domanda di potenza di calcolo. La cold board supporta l'"informatica orientale", mentre l'immersione supporta l'"informatica occidentale". Lo sviluppo parallelo a doppio binario sarà il tema principale del prossimo decennio.
4-Opportunità e strategie del settore
Gioco ecologico e sui costi: il raffreddamento a liquido con piastra fredda avrà la meglio nel breve termine, mentre il raffreddamento a liquido a immersione deve ridurre i costi per uscire dalla situazione di stallo.
Raffreddamento a liquido con piastra fredda: ottimizzazione dei materiali (composito rame-alluminio), miglioramento della precisione di lavorazione (processo a prova di perdite) e promozione di una progettazione modulare e standardizzata.
Raffreddamento a liquido a immersione: sviluppare liquidi di raffreddamento convenienti (ad esempio liquidi a immersione monofase), cabinet compatibili e collaborare con i produttori di chip per personalizzare le soluzioni di raffreddamento.
Riserve tecnologiche: esplorare piastre di raffreddamento a flusso bifase e sistemi di monitoraggio intelligenti (come la regolazione dinamica del flusso tramite intelligenza artificiale) per far fronte alle future elevate richieste di potenza.
5- Conclusion
Breve termine (2025-2027): il raffreddamento a liquido a piastra fredda domina gli scenari generali e il tasso di penetrazione del raffreddamento a liquido a immersione aumenta al 15%-20%; Lungo termine (2030+): il raffreddamento a liquido a immersione con cambiamento di fase diventa la norma nel campo dell'elevata potenza di calcolo, mentre il raffreddamento a liquido a piastra fredda si ritira nel mercato a media e bassa densità.
I fattori decisivi: il costo del refrigerante, la velocità di incremento del consumo energetico dei chip e le politiche internazionali di tutela ambientale.
Condivideremo regolarmente aggiornamenti e informazioni su tecniche di progettazione termica e alleggerimento, per la vostra consultazione. Grazie per l'interesse verso Walmate.
Con il rapido sviluppo di veicoli a nuova energia e dei settori dell'accumulo di energia, leggerezza, elevata sicurezza ed efficiente gestione termica sono diventati requisiti fondamentali. La nostra azienda è profondamente impegnata nel campo della lavorazione di materiali in lega di alluminio. Affidandoci a una selezione avanzata di materiali, processi di formatura e tecnologie di saldatura, ci concentriamo sulla ricerca, sviluppo e produzione di vassoi per batterie, piastre di raffreddamento a liquido, scatole per accumulatori di energia e radiatori. La lega di alluminio è diventata la scelta ideale per la leggerezza e la gestione termica delle nuove apparecchiature energetiche grazie alla sua bassa densità (circa 2,7 g/cm³), all'elevata resistenza, alla resistenza alla corrosione e all'eccellente conduttività termica (conduttività termica di circa 150-220 W/m·K).
1- Selezione del materiale in lega di alluminio e considerazioni chiave
Prodotti diversi presentano requisiti prestazionali significativamente diversi per le leghe di alluminio ed è necessario combinare resistenza, resistenza alla corrosione, saldabilità e adattabilità al processo per una selezione completa dei materiali:
a. Vassoio batteria
Gradi comuni: 6061-T6, 6005A-T6, 6063-T6.
Criteri di selezione:
· Deve soddisfare una resistenza alla trazione ≥ 240 MPa (come il 6061-T6) per superare i test di estrusione, caduta e impatto con sfera standard nazionali;
· Elevati requisiti di saldabilità, è necessario evitare cricche termiche (si preferisce la serie 6xxx rinforzata con Mg/Si);
· La resistenza alla corrosione è migliorata tramite anodizzazione o rivestimento in alluminio.
Figura 1 - Vassoio batteria in lega di alluminio
b. Scatola per accumulatore di energia
Marche comuni: 5083, 6061-T6 (sia per resistenza meccanica che per resistenza alla corrosione).
Criteri di selezione:
· Necessità di resistere a vibrazioni e carichi d'impatto, il limite di snervamento deve essere ≥200 MPa;
· Elevati requisiti di trattamento superficiale per evitare la corrosione elettrochimica.
c. Piastra di raffreddamento a liquido
Marche comuni: 3003, 6061/6063, 6082.
Criteri di selezione:
· Elevata conduttività termica e resistenza alla corrosione;
· Il canale di raffreddamento a liquido richiede uno stampaggio complesso e si preferisce la serie 6xxx con eccellenti prestazioni di estrusione.
2- Differenze nelle prestazioni di processo e difficoltà di lavorazione
La lavorazione delle leghe di alluminio deve adattarsi alle loro proprietà fisiche, in particolare durante il taglio, la lavorazione CNC, la saldatura e il trattamento superficiale:
a. Taglio e lavorazione CNC
Difficoltà:
· La lavorazione di fori ad alta precisione è soggetta a bave o deformazioni (come sporgenze sul bordo dei fori a gradino) a causa della duttilità del materiale;
· Le strutture a pareti sottili (come i canali di flusso delle piastre di raffreddamento a liquido) devono controllare le forze di taglio per evitare deformazioni.
Soluzione:
· Utilizzare utensili con rivestimento diamantato per migliorare l'affilatura dei bordi e ridurre la deformazione da estrusione;
· Ottimizzare i parametri di lavorazione (come alta velocità e basso avanzamento) e collaborare con le apparecchiature CNC generali per ottenere una lavorazione stabile.
b. Processo di saldatura
Sfide principali:
· Il film di ossido (punto di fusione di Al₂O₃ 2050 °C) ostacola la fusione e porta facilmente alla formazione di pori e inclusioni di scorie; · Alcune leghe presentano un'elevata tendenza alla formazione di cricche a caldo, pertanto è necessario controllare l'energia di saldatura e la composizione del filo di saldatura.
Processi preferiti:
· Saldatura TIG (alimentazione a corrente alternata): adatta per lamiere sottili, con rimozione del film di ossido mediante "pulizia catodica";
· Saldatura MIG (alta corrente + miscela di gas elio): elevata efficienza di saldatura per lamiere spesse e apporto termico controllabile.
Figura 2 - Saldatura del vassoio della batteria
c. Trattamento superficiale
· Rivestimento isolante resistente alla pressione: applicato al vassoio batteria e all'interno del contenitore del pacco batteria, deve superare il test di pressione (≥3000 V CC/1 min); lo spessore del rivestimento è di 20-50 μm, per garantire la sicurezza dell'isolamento in ambienti ad alta tensione;
· Rivestimento isolante e deumidificante: per il contenitore del pacco batteria, vengono utilizzati materiali idrofobici (come la resina fluorocarbonica) per ridurre il rischio di condensa interna e il valore dyne è ≥34 per garantire l'adesione;
· Rivestimento di protezione anticollisione: utilizzato per la parete esterna del vassoio batteria, viene selezionato un elastomero poliuretanico (durezza ≥80 Shore A), con una resistenza all'impatto migliorata di oltre il 30%;
· Anodizzazione: trattamento anticorrosione convenzionale, errore di spessore del film ≤3 μm, adatto per strutture complesse.
3- Ispezione di verifica e adattabilità delle apparecchiature
Per soddisfare gli standard del nuovo settore energetico (come GB/T31467.3, UL2580), sono necessari una verifica multidimensionale e un adattamento del processo:
a. Ispezione di verifica
· Resistenza strutturale: verificare le prestazioni di carico, estrusione e impatto con la sfera del vassoio tramite simulazione agli elementi finiti (sollecitazione massima ≤ limite di snervamento del materiale);
· Test di tenuta: il sistema di raffreddamento a liquido utilizza il rilevamento delle perdite con elio (tasso di perdita ≤1×10⁻⁶ mbar·L/s) e un test di pressione ciclica (0,5-1,5 MPa/5000 volte);
· Verifica delle prestazioni del rivestimento:
Test di tensione di tenuta del rivestimento isolante (5000 V CC/60 s senza guasti);
Il rivestimento anticollisione supera il test di impatto con la sfera in caduta (sfera d'acciaio da 1 kg a 1 m di altezza) e il test di nebbia salina (1000 ore senza distacco).
b. Ottimizzazione dell'adattabilità delle apparecchiature
· Trasformazione generale delle apparecchiature CNC: grazie alla progettazione di attrezzature ad alta precisione e all'algoritmo di compensazione dinamica, la deformazione di lavorazione di componenti a pareti sottili può essere ≤0,1 mm;
· Libreria dei parametri di saldatura: definizione di parametri di saldatura standard (come corrente e velocità di avanzamento del filo) per diverse qualità di leghe di alluminio per ridurre il ciclo di debug;
· Spruzzatura automatizzata del rivestimento: grazie all'utilizzo di un robot multiasse per la spruzzatura, combinato con la tecnologia di polimerizzazione a infrarossi, l'errore di uniformità del rivestimento è ≤5%.
Conclusione
L'ampia applicazione delle leghe di alluminio nelle nuove apparecchiature energetiche non è solo una vittoria della scienza dei materiali, ma anche una manifestazione di innovazione di processo. La nostra azienda continuerà a esplorare nuove leghe di alluminio ad alta resistenza, resistenti alla corrosione e facili da lavorare, e a promuovere l'aggiornamento delle prestazioni di prodotti come vassoi per batterie e piastre di raffreddamento a liquido attraverso l'innovazione di processo, aiutando il settore a progredire verso un futuro efficiente e leggero.
Condivideremo regolarmente aggiornamenti e informazioni su tecniche di progettazione termica e alleggerimento, per la vostra consultazione. Grazie per l'interesse verso Walmate.
Con il continuo aumento della densità di potenza dei dispositivi elettronici, la progettazione della dissipazione del calore è diventata un elemento chiave che influenza l'affidabilità e la durata del sistema. In qualità di produttore professionale con 19 anni di esperienza nella gestione termica, combiniamo casi ingegneristici tipici con l'esperienza nella simulazione multifisica sul campo per analizzare a fondo i cinque principali malintesi tecnici che gli ingegneri tendono a trascurare negli scenari ad alta potenza e fornire soluzioni conformi alle prassi del settore.
Equivoco 1: Abuso di materiali ad alta conduttività termica, deviazione di calcolo della resistenza termica di interfaccia
Problema tipico: Ricerca eccessiva di valori teorici per i materiali termoconduttivi, ignorando la realtà ingegneristica della resistenza termica di contatto dell'interfaccia.
Analisi del caso: Un modulo di dissipazione del calore per radar laser per autoveicoli utilizza un substrato di rame puro (conduttività termica 401 W/m·K), ma lo spessore del rivestimento del materiale di interfaccia termica (TIM) non è controllato con precisione (0,1 mm di progetto, fluttuazione effettiva ±0,05 mm) e la resistenza termica di contatto misurata raggiunge 0,6 °C·cm²/W, causando un superamento del 22% della temperatura di giunzione dell'FPGA rispetto allo standard. Dopo il passaggio ai pad termici preformati (tolleranza ±0,02 mm, resistenza termica <0,03 °C·cm²/W) e la combinazione con il processo di sinterizzazione sotto vuoto, la temperatura di giunzione si riduce di 17 °C e l'MTBF (tempo medio tra guasti) aumenta a 100.000 ore.
Piano di ottimizzazione:
Selezione del materiale: secondo lo standard ASTM D5470, viene misurata la resistenza termica del TIM e si preferiscono materiali a cambiamento di fase o elastomeri caricati con metallo.
Controllo di processo: utilizzare apparecchiature di dosaggio automatiche (precisione ±3%) per garantire una tolleranza di spessore <10% ed evitare vuoti d'aria.
Equivoco 2: Incongruenza nell'organizzazione del flusso d'aria nel sistema di raffreddamento ad aria, punti caldi locali fuori controllo
Problema tipico: sovrapposizione cieca del numero di ventole, ignorando l'adattamento di impedenza del canale di flusso e l'effetto di separazione dello strato limite.
Esempio ingegneristico: un cluster GPU di un data center utilizza 4 ventole da 12.038 (volume d'aria 200 CFM), ma a causa di una progettazione non corretta dell'angolo di guida dell'aria (piegatura ad angolo retto di 90°), il volume d'aria effettivo effettivo è solo il 65% del valore nominale e la differenza di temperatura locale raggiunge i 40 °C. Dopo l'ottimizzazione della simulazione CFD, il canale di guida dell'aria viene modificato in un canale di flusso a espansione graduale (angolo di diffusione <7°) e viene adottato un layout a alette sfalsate (il gradiente di spaziatura aumenta da 2 mm a 3,5 mm), la resistenza al vento complessiva viene ridotta del 30% e la differenza di temperatura del punto caldo viene controllata entro 8 °C. Strategia di base:
Progettazione del campo di flusso: i test in galleria del vento vengono eseguiti secondo la norma ISO 5801 per ottimizzare il rapporto tra le aree di ingresso e di uscita (consigliato 1:1,2).
Controllo dinamico: in base alla curva Q-H della ventola PWM, il punto di impedenza del sistema viene abbinato all'intervallo di efficienza più elevato (solitamente 60-80% del volume d'aria massimo).
Equivoco 3: Un difetto nella progettazione della protezione ambientale accelera l'invecchiamento dei materiali
Problema tipico: concentrarsi solo sulle prestazioni iniziali di dissipazione del calore, ignorando gli effetti di stress ambientali a lungo termine come umidità, calore, polvere e nebbia salina.
Analisi del caso: un convertitore eolico offshore utilizza un dissipatore di calore in lega di alluminio 6061 (anodizzato superficialmente). Dopo 6 mesi di funzionamento in un ambiente con nebbia salina, lo strato di ossido si è staccato, causando un aumento del 50% della resistenza termica di contatto e un aumento del tasso di guasto degli IGBT. Passando alla lega di alluminio 5052 (resistenza alla nebbia salina >1000 ore) e applicando una vernice poliuretanica a tripla resistenza (spessore 50 μm, in conformità con lo standard IEC 60068-2-11), il tasso di guasto sul campo a 3 anni è diminuito del 75%. Punti di forza:
Tecnologia di rivestimento: Rivestimento ceramico Al2O3 mediante spruzzatura al plasma (conduttività termica 30 W/m·K, resistenza a temperature >800 °C) utilizzato in scenari ad alta temperatura.
Struttura di tenuta: Grado di protezione IP69K (guarnizione in silicone a doppio passaggio + valvola di sicurezza) per garantire l'assenza di infiltrazioni di polvere/vapore acqueo.
Equivoco 4: Mancanza di modellazione del carico termico transitorio e selezione inadeguata dei materiali a cambiamento di fase
Problema tipico: la soluzione di dissipazione del calore progettata tramite simulazione a stato stazionario non è in grado di gestire impulsi di potenza nell'ordine dei millisecondi.
Dati misurati: un amplificatore di potenza a stato solido è sottoposto a un carico impulsivo di 2 ms a 2000 W in una stazione base 5G. L'aumento di temperatura transitorio della soluzione tradizionale con substrato in alluminio raggiunge i 55 °C, mentre il materiale a cambiamento di fase a microcapsula (composito paraffina/grafene, calore latente del cambiamento di fase 220 J/g), combinato con la simulazione termica transitoria (lunghezza del passo transitorio ANSYS Icepak 1 ms), viene utilizzato per controllare l'aumento di temperatura a 18 °C, soddisfacendo i requisiti del test di impatto MIL-STD-810G.
Tecnologia di gestione dinamica:
Imballaggio a cambiamento di fase: la struttura a nido d'ape viene utilizzata per incapsulare il materiale a cambiamento di fase (porosità >70%) per evitare perdite di liquido e migliorare l'efficienza di diffusione del calore. Calibrazione del modello: le condizioni al contorno della simulazione vengono corrette in base all'imaging termico a infrarossi (frequenza di campionamento 100 Hz) e l'errore è <±1,5 °C
Equivoco 5: la valutazione del TCO è unilaterale e ignora i costi operativi e di manutenzione nascosti.
Problema tipico: viene confrontato solo il costo iniziale dell'hardware e non vengono quantificate le perdite dovute a consumo energetico/manutenzione/fermi macchina.
Confronto dei costi: una fabbrica di semiconduttori utilizzava originariamente armadi raffreddati ad aria (costo iniziale di 500.000 yuan), con una bolletta elettrica annua di 1,2 milioni di yuan (PUE = 1,8). Dopo l'aggiornamento al raffreddamento a liquido a immersione bifase (costo iniziale di 1,8 milioni di yuan), la bolletta elettrica annua è scesa a 450.000 yuan (PUE = 1,05) e, grazie alla riduzione del carico di condizionamento dell'aria della camera bianca, il risparmio annuo complessivo ha raggiunto i 900.000 yuan e l'investimento incrementale può essere recuperato in 2,1 anni (IRR > 25%). Modello decisionale:
Modellazione raffinata: introduzione di una simulazione Monte Carlo per quantificare l'impatto del tasso di guasto delle apparecchiature (distribuzione di Weibull) sul TCO.
Sovrapposizione delle politiche: in combinazione con meccanismi di tassazione del carbonio (come il CBAM dell'UE), le emissioni di carbonio dei sistemi di raffreddamento a liquido durante l'intero ciclo di vita vengono ridotte del 60% e si ottiene un sussidio aggiuntivo del 15%.
Conclusione: Aggiornamento del paradigma di progettazione termica da basato sull'esperienza a basato sui dati.
Processo standardizzato: Introduzione dello standard di test termico JESD51-14 nella fase di progettazione concettuale per evitare rilavorazioni successive (il ciclo di progetto di un determinato modulo ottico si riduce del 30%).
Collaborazione multidisciplinare: Grazie all'accoppiamento di perdite elettromagnetiche (estrazione HFSS) e campo di deformazione termica con COMSOL Multiphysics, l'efficienza di dissipazione del calore di un componente radar TR migliora del 40%.
Operatività e manutenzione intelligenti: Implementazione di sensori di temperatura a reticolo in fibra (accuratezza ±0,1 °C) e piattaforme di digital twin per ottenere la previsione dei guasti (i tempi di inattività imprevisti di un centro di supercalcolo si riducono del 90%).
Grazie a un approccio ingegneristico rigoroso e alla verifica completa dei dati, i progettisti termici possono evitare con precisione i "killer invisibili" e gettare le basi per sistemi ad alta affidabilità. Come professionisti del settore, ci impegniamo a fornire soluzioni a ciclo chiuso, dai materiali ai sistemi, e ad affrontare congiuntamente le sfide di gestione termica con i clienti.
Condivideremo regolarmente aggiornamenti e informazioni su tecniche di progettazione termica e alleggerimento, per la vostra consultazione. Grazie per l'interesse verso Walmate.
1- Requisiti di tolleranza speciali per i componenti chiave
Nella produzione di vassoi batteria per veicoli elettrici e di alloggiamenti per pacchi batteria per accumulo di energia con raffreddamento a liquido, il controllo della tolleranza delle superfici e delle interfacce di collegamento chiave influisce direttamente sulla tenuta, sull'efficienza di dissipazione del calore e sulla precisione di assemblaggio.
a. Superficie di installazione della piastra di raffreddamento a liquido
La piastra di raffreddamento a liquido è il componente principale del sistema di gestione termica della batteria. La planarità della sua superficie di installazione influisce direttamente sulla tenuta del canale di flusso del refrigerante. Se la planarità non rientra nei limiti di tolleranza, causerà una compressione irregolare della guarnizione in silicone, causando perdite localizzate o una maggiore resistenza termica.
b. Disallineamento dei cordoni di saldatura
Il vassoio batteria utilizza spesso una struttura di saldatura in lega di alluminio. Il disallineamento dei cordoni di saldatura causerà una concentrazione di sollecitazioni e ridurrà la durata a fatica. Soprattutto in scenari con elevati requisiti di ermeticità dell'alloggiamento del pacco batteria (come IP67), il disallineamento deve essere rigorosamente controllato.
c. Foro di posizionamento del modulo batteria
Il foro di posizionamento viene utilizzato per fissare con precisione il modulo batteria. Una tolleranza eccessiva causerà il disallineamento del modulo, con conseguenti guasti ai collegamenti elettrici o rischi di vibrazioni meccaniche.
d. Fissaggio della posizione del foro per i bulloni
Il foro per i bulloni viene utilizzato per collegare l'alloggiamento del pacco batteria al telaio. Eventuali deviazioni di posizione causeranno sollecitazioni di assemblaggio e persino la rottura dei bulloni.
e. Rettilineità dei bordi dell'alloggiamento del pacco batteria
La rettilineità dei bordi dell'alloggiamento del pacco batteria influisce sull'assemblaggio dei coperchi superiore e inferiore e sul livello di protezione IP, in particolare per gli alloggiamenti saldati al laser, dove il bordo deve essere utilizzato come riferimento per il tracciamento della testina laser.
2- L'impatto della tolleranza dimensionale sull'efficienza produttiva
L'impatto della tolleranza dimensionale sull'efficienza produttiva si riflette principalmente nel suo equilibrio tra flusso di lavorazione, controllo dei costi e qualità del prodotto. Una progettazione con tolleranze ragionevoli può non solo garantire la funzionalità del prodotto, ma anche ottimizzare il ritmo di produzione. L'impatto di un controllo ragionevole della tolleranza dimensionale sull'efficienza produttiva si riflette principalmente nei seguenti aspetti:
a. Equilibrio tra precisione di lavorazione e costi di produzione
· Sebbene una rigorosa tolleranza dimensionale possa migliorare la precisione di sigillatura e assemblaggio, sono necessarie apparecchiature di lavorazione ad alta precisione e processi complessi, il che aumenta significativamente l'investimento in attrezzature e i tempi di lavorazione.
· Un'eccessiva ricerca della precisione può comportare un aumento dei costi di lavorazione. È necessario impostare tolleranze rigorose nei componenti funzionali chiave e le tolleranze dovrebbero essere opportunamente allentate nelle aree non critiche per ridurre i costi.
b. Controllo del tasso di rilavorazione e del tasso di scarto
· Una progettazione con tolleranze ragionevoli può ridurre le rilavorazioni causate da deviazioni dimensionali.
· La deformazione da saldatura è il problema principale nella produzione di vassoi per batterie. L'utilizzo del processo di saldatura a freddo CMT può ottimizzare l'apporto termico, ridurre la deformazione dopo la saldatura e abbreviare il ciclo di rilavorazione.
c. Produzione modulare e standardizzata
· Grazie ai componenti standardizzati, i requisiti di tolleranza si concentrano su parti sostituibili localmente, riducendo la difficoltà di lavorazione complessiva.
· La progettazione con tolleranze standardizzate può inoltre supportare la compatibilità multi-modello e ridurre la necessità di lavorazioni personalizzate.
3-Standard di settore e applicazioni pratiche del controllo della planarità
Per i vassoi batteria dei veicoli a nuova energia, gli standard di settore prevedono requisiti rigorosi:
a. Standard di planarità: la planarità della superficie di installazione della piastra di raffreddamento a liquido deve essere ≤0,2 mm, la planarità della piastra di supporto inferiore deve essere ≤0,5 mm/m² e l'errore di planarità del telaio dopo la saldatura deve essere ≤0,8 mm6.
b. Ottimizzazione del processo di produzione: la fresatura di precisione CNC, la saldatura a freddo CMT e il trattamento di invecchiamento tramite vibrazioni (VSR), combinati con il rilevamento online tramite interferometro laser, riducono il rischio di deformazione.
c. Selezione del materiale: si consiglia di utilizzare leghe di alluminio ad alta resistenza come la 6061, con un limite di snervamento ≥1180 MPa, tenendo conto sia della leggerezza che della stabilità strutturale.
4- Strategia di adeguamento delle tolleranze basata su materiali e processi
a. L'innovazione nei materiali favorisce l'alleggerimento
Utilizzo di leghe di alluminio leggere ad alta resistenza (come la 6061) e materiali compositi (matrice di alluminio rinforzata con carburo di silicio), combinate con anodizzazione e rivestimento isolante, per ottenere una riduzione del peso del 30% e migliorare la resistenza alla corrosione, adattandosi ai requisiti di dissipazione del calore dei sistemi di raffreddamento a liquido.
b. La collaborazione di processo migliora la precisione di produzione
Lo stampaggio per estrusione monoblocco + la saldatura ad attrito e stiramento (FSW) riducono il numero di saldature, la saldatura a freddo CMT e la saldatura laser controllano la deformazione termica.
c. Simulazione a ciclo chiuso per garantire l'affidabilità
La simulazione CAE ottimizza la disposizione delle nervature di rinforzo, la scansione laser e la tecnologia di rilevamento delle perdite di elio consentono il monitoraggio completo del processo, il design modulare è compatibile con tolleranze di ±5 mm, riducendo i costi e aumentando l'efficienza.
Condivideremo regolarmente aggiornamenti e informazioni su tecniche di progettazione termica e alleggerimento, per la vostra consultazione. Grazie per l'interesse verso Walmate.
1- Caratteristiche del processo di saldatura in lega di alluminio del vassoio batteria/scatola del pacco di accumulo di energia
Nella produzione di nuove scatole del pacco di energia raffreddate a liquido, vassoi batteria e altri prodotti, i canali di raffreddamento a liquido e le strutture multi-cavità sono tipiche caratteristiche di progettazione complesse (come mostrato nella Figura 1). Tali strutture spesso includono le seguenti caratteristiche:
Figura 1: Design tipico di un vassoio per batteria
Interlacciamento spaziale tridimensionale: i canali di flusso sono distribuiti in una forma serpentina, con un gran numero di punti di svolta spaziali;
Collegamento multilivello: la cavità principale e la sottocavità sono collegate da partizioni a parete sottile (spessore 2-3 mm);
Caratteristiche di miniaturizzazione: piccole dimensioni della sezione trasversale del canale di flusso (lo spessore minimo della parete del canale di flusso del profilo in alluminio è 1,2 mm) e scarsa accessibilità alla saldatura.
2- Analisi delle difficoltà di combinare più tecnologie di saldatura nella produzione di vassoi per batterie
Nella pratica della produzione di vassoi per batterie, è necessario combinare più tecnologie di saldatura, come l'applicazione coordinata di saldatura a frizione e agitazione (FSW), saldatura a transizione di metallo freddo (CMT), saldatura a fusione tradizionale (TIG/MIG) e altre tecnologie. Questa combinazione mira a tenere conto di leggerezza, resistenza, tenuta ed efficienza produttiva, ma affronta anche le seguenti difficoltà principali:
a. Il problema dell'apporto di calore coordinato di più processi
Diverse tecnologie di saldatura (come FSW e saldatura laser) presentano grandi differenze nell'apporto di calore, che possono facilmente causare mutazioni delle prestazioni dei materiali e deformazione termica e devono essere risolte ottimizzando la sequenza di saldatura e la regolazione dei parametri.
b. Compatibilità delle apparecchiature e collo di bottiglia dell'efficienza
La commutazione delle apparecchiature è complessa e i requisiti di accuratezza della sincronizzazione dei parametri sono elevati. Sono necessari design di postazioni di lavoro modulari e saldatrici intelligenti per migliorare l'efficienza collaborativa e ridurre i tempi di ciclo.
c. Sfide nel bilanciare resistenza e costi della sigillatura
Il rischio di perdite all'intersezione di più saldature è elevato (rappresenta il 70% dei difetti) ed è richiesta una progettazione ridondante di sigillatura + ottimizzazione della topologia.
3-Pratica ingegneristica: vassoio batteria, raffreddamento a liquido per accumulo di energia, coordinamento del processo di saldatura multipla PACK box
a. Pianificazione della posizione delle cicatrici di saldatura
· Ottimizzazione della posizione di saldatura: nella fase di progettazione del prodotto, la razionalità della posizione di saldatura deve essere pienamente considerata per evitare che appaiano cicatrici di saldatura in parti o aree chiave che influenzano le funzioni del prodotto. Ad esempio, regolare lo spazio tra il telaio anteriore e l'ugello dell'acqua per evitare interferenze con le cicatrici di saldatura; ottimizzare la posizione di saldatura dell'ugello dell'acqua per ridurre l'impatto sulle prestazioni del prodotto.
· Corrispondenza con la struttura del prodotto: la posizione di saldatura deve corrispondere alla struttura del prodotto per garantire che la saldatura possa sopportare vari carichi e sollecitazioni durante l'uso del prodotto. Ad esempio, nel progetto della piastra di raffreddamento a liquido, la stabilità strutturale e l'affidabilità del prodotto vengono migliorate pianificando razionalmente la posizione di saldatura.
· Facile da usare e rilevare: la posizione di saldatura deve essere comoda per gli operatori per eseguire operazioni di saldatura e successive ispezioni di qualità. Ad esempio, evitare di saldare in posizioni difficili da raggiungere o con scarsa visibilità per migliorare l'efficienza e la qualità della saldatura.
b. Controllo della cicatrice di saldatura
· Dimensioni della cicatrice di saldatura: la dimensione della cicatrice di saldatura deve essere rigorosamente controllata. In genere, l'altezza della cicatrice di saldatura deve essere compresa tra 4 e 6 mm e la cicatrice di saldatura non deve superare il piano per garantire l'aspetto e la precisione di assemblaggio del prodotto. Ad esempio, nel progetto della piastra di raffreddamento a liquido, la dimensione della cicatrice di saldatura è stata controllata con successo regolando i parametri e il processo di saldatura, evitando l'impatto della cicatrice di saldatura sulle prestazioni e sulla qualità del prodotto.
· Forma della cicatrice di saldatura: la forma della cicatrice di saldatura deve essere il più regolare possibile per evitare una fusione eccessiva o incompleta. Ottimizzando i parametri di saldatura e le tecniche operative, la forma della cicatrice di saldatura può essere migliorata in modo efficace e la qualità della saldatura può essere migliorata.
· Trattamento di rettifica: per i segni di saldatura concavi prodotti nella posizione di saldatura a frizione, viene utilizzato un trattamento di rettifica per garantire una superficie liscia per soddisfare i requisiti di aspetto e prestazioni del prodotto.
c. Ottimizzazione della sequenza di saldatura
· Saldatura di partizioni: per prodotti di grandi dimensioni, il metodo di saldatura di partizioni può controllare efficacemente la deformazione complessiva. Dividendo il prodotto in più aree e saldandole in sequenza, la concentrazione di calore durante il processo di saldatura può essere ridotta e il rischio di deformazione termica può essere ridotto.
· Correzione passo dopo passo: durante il processo di saldatura, il metodo di correzione passo dopo passo viene utilizzato per regolare la deformazione della saldatura nel tempo. Misurando e correggendo continuamente la deformazione del prodotto durante il processo di saldatura, la precisione dimensionale e la forma del prodotto finale sono garantite per soddisfare i requisiti di progettazione.
· Ottimizzazione del percorso di saldatura: pianificare razionalmente il percorso di saldatura per evitare saldature ripetute nella stessa area e ridurre l'apporto di calore. Ad esempio, nel progetto della piastra di raffreddamento a liquido, l'apporto di calore durante il processo di saldatura è stato ridotto e la qualità della saldatura è stata migliorata ottimizzando il percorso di saldatura.
d. Controllo collaborativo della deformazione
La piastra di raffreddamento a liquido subisce una deformazione termica durante il processo di saldatura, con conseguente diminuzione della precisione dimensionale del prodotto. Misure di ottimizzazione:
· Utilizzare la saldatura di partizione e metodi di correzione passo-passo per controllare la deformazione complessiva.
· Ottimizzare i parametri di saldatura, ridurre corrente e tensione e ridurre l'apporto di calore.
· Utilizzare dispositivi di fissaggio per fissare il prodotto per ridurre il movimento e la deformazione durante la saldatura.
· Utilizzare il metodo di saldatura simmetrico per distribuire uniformemente il calore di saldatura.
Condivideremo regolarmente aggiornamenti e informazioni su tecniche di progettazione termica e alleggerimento, per la vostra consultazione. Grazie per l'interesse verso Walmate.
La tecnologia CTC (Cell-to-Chassis) ha attirato molta attenzione perché può migliorare significativamente l'autonomia e l'efficienza dello spazio dei veicoli elettrici, ma se possa davvero sostituire la tecnologia delle batterie tradizionali è ancora controverso. Il collo di bottiglia principale sul lato della produzione, il processo di saldatura del vassoio della batteria, è diventato la chiave per determinare il futuro di questa tecnologia: progettazione strutturale complessa, compatibilità multi-materiale e rigorosi requisiti di gestione termica hanno messo a dura prova la tecnologia di saldatura tradizionale. Partendo dalla prospettiva degli ingegneri in prima linea, combinando tendenze del settore e pratiche ingegneristiche, questo articolo analizza il potenziale e i limiti della tecnologia CTC ed esplora come la tecnologia di saldatura sia diventata la "pietra di paragone" di questa rivoluzione tecnologica.
1-L'"Ideale e la realtà" della tecnologia CTC
La tecnologia CTC può teoricamente ridurre le parti strutturali ridondanti e migliorare la densità energetica integrando la cella della batteria direttamente nel telaio, ma la fattibilità della sua applicazione su larga scala sta affrontando sfide realistiche:
Radicalismo e cautela delle case automobilistiche: Tesla, BYD e altre aziende leader hanno lanciato soluzioni CTC, ma altri produttori stanno ancora aspettando e osservando. I dati del settore mostrano che a febbraio 2025, i modelli CTC prodotti in serie rappresentano il 15-20% del mondo e la tradizionale tecnologia CTP (Cell-to-Pack) è ancora la tecnologia dominante.
Il "costo" della durata migliorata della batteria: sebbene la CTC possa aumentare la densità energetica del 15%-20%, la complessità della struttura del telaio porta a un aumento dei costi di produzione del 30%-50% (calcolato da un'agenzia di consulenza) e l'equilibrio tra costi e benefici non è ancora chiaro.
Controversia economica sulla manutenzione: il design integrato ha causato un aumento vertiginoso dei costi di manutenzione della batteria. I dati delle compagnie assicurative mostrano che il tasso di sostituzione dei gruppi batteria dopo incidenti dei modelli CTC è pari al 70%, molto più alto del 25% dei modelli tradizionali.
Queste contraddizioni rendono il futuro della tecnologia CTC pieno di variabili. Se il mercato riuscirà a superare il 20% dipenderà da tre variabili principali: il progresso della produzione di massa del Tesla Cybertruck; se la guerra dei prezzi tra le case automobilistiche cinesi costringerà CTC a ridurre i costi; e il grado di compromesso delle normative europee sulla riparabilità delle batterie. Il livello di tecnologia di saldatura sul lato della produzione sarà la chiave per determinare se riuscirà a colmare il divario tra laboratorio e produzione di massa.
2-Tre "barriere di vita e di morte" del processo di saldatura
Per i produttori di vassoi per batterie, l'implementazione della tecnologia CTC deve superare tre problemi fondamentali:
a. Il gioco tra precisione "a livello di micron" ed efficienza
I processi di saldatura tradizionali possono tollerare errori di 0,5 mm, ma i vassoi CTC devono trasportare più batterie e il numero di giunzioni aumenta di oltre 3 volte, e la maggior parte di esse è distribuita su parti curve e irregolari. I test di un produttore mostrano che quando l'errore di posizionamento della saldatura supera 0,15 mm, il tasso di resa dell'assemblaggio delle celle della batteria scenderà drasticamente dal 99% all'82%. Ciò che è più complicato è che il miglioramento della precisione è spesso accompagnato da una diminuzione dell'efficienza: sebbene l'accuratezza della saldatura laser sia elevata, il costo dell'attrezzatura è più di 5 volte superiore a quello della saldatura tradizionale.
b. L'"acqua e il fuoco" dei materiali misti
Per bilanciare leggerezza e resistenza, i vassoi CTC spesso utilizzano una struttura mista di "lega di alluminio + fibra di carbonio + acciaio speciale". La differenza nei coefficienti di dilatazione termica di materiali diversi può arrivare fino a 20 volte (ad esempio alluminio 23μm/m·K contro fibra di carbonio 0,8μm/m·K), il che genera facilmente stress interno durante la saldatura e causa crepe. Quando un'azienda ha provato a collegare alluminio e fibra di carbonio, il tasso di crepe della saldatura era alto fino al 18%, superando di gran lunga la soglia accettabile del settore del 3%.
c. "Killer invisibile" della zona interessata dal calore
L'elevata temperatura di saldatura può danneggiare i materiali isolanti o i circuiti dei sensori attorno alla cella della batteria. Una volta un'azienda automobilistica ha aumentato il tasso di autoscarica del modulo batteria del 50% a causa di un controllo improprio dell'apporto di calore di saldatura. Gli ingegneri devono controllare la fluttuazione della temperatura di saldatura entro ±15℃ entro 0,1 secondi, il che equivale a installare un "freno termico ad alta precisione" sulla pistola per saldatura.
3-La via d'uscita: non esiste una soluzione miracolosa, solo innovazione di sistema
Di fronte a queste sfide, il settore sta esplorando tre percorsi rivoluzionari:
a. "Cocktail therapy" di combinazione di processi
Saldatura ibrida ad arco laser: combinando la precisione della saldatura laser con i vantaggi della penetrazione della saldatura ad arco, la velocità di saldatura della lega di alluminio aumenta del 40%;
Tecnologia di transizione del metallo freddo (CMT): attraverso un controllo preciso dell'apporto di calore, l'area della zona termicamente alterata viene ridotta del 60%;
Sistema di compensazione intelligente del robot: regola automaticamente il percorso della pistola di saldatura in base ai dati di scansione della saldatura in tempo reale e aumenta il tasso qualificato di saldatura di superfici curve complesse dal 75% al 95%.
b. "Pre-compromesso" sul lato del materiale
Alcune aziende hanno iniziato a sviluppare congiuntamente materiali compositi "saldabili" con i fornitori di materiali. Ad esempio, la sensibilità alle crepe di saldatura di una lega di alluminio modificata nazionale (materiale in lega di alluminio regolato con mezzi fisici, chimici o di processo) è stata ridotta dal livello 7 al livello 3 (secondo gli standard ISO). Sebbene sacrifichi il 5% dell'effetto leggero, aumenta la resa della saldatura al 98%.
c. "Digital twin" nella dimensione di rilevamento
Raccogliendo tutti i dati del processo di saldatura (corrente, temperatura, velocità, ecc.), combinati con modelli AI per prevedere la probabilità di difetti. Dopo che una fabbrica ha introdotto questa tecnologia, il tasso di rilevamento online dei difetti di saldatura è aumentato dall'80% al 97% e il costo degli scarti è stato ridotto del 45%.
4- Nuova proposta degli ingegneri: trovare la certezza nell'incertezza
a. La controversia sulla tecnologia CTC è essenzialmente un gioco tra "ottimizzazione del sistema" e "limiti locali":
se la velocità di svolta del processo di saldatura è più lenta delle aspettative di riduzione dei costi delle aziende automobilistiche, la CTC potrebbe diventare una tecnologia di nicchia;
se materiali, processi e tecnologie di collaudo fanno progressi in modo coordinato, ci si aspetta che inaugureranno una nuova era di progettazione strutturale dei veicoli elettrici.
b. Per gli ingegneri, è necessario ricostruire le capacità da due dimensioni:
integrazione delle conoscenze interdisciplinari: comprendere la soglia sensibile delle proprietà elettrochimiche all'apporto di calore di saldatura;
capacità di risposta agile: uno studio di caso di un fornitore europeo mostra che il team che riesce a completare l'ottimizzazione dei parametri di saldatura di nuovi materiali in lega entro una settimana ha una probabilità di ottenere ordini triplicata.
La tecnologia CTC si trova all'incrocio tra "innovazione dirompente" e "trappola della produzione di massa". Potrebbe non sostituire completamente la tecnologia esistente, ma sta costringendo il processo di saldatura a evolversi verso una maggiore precisione, una maggiore compatibilità e un controllo più intelligente. In questa maratona tecnologica, il vero vincitore potrebbe non essere la prima casa automobilistica, ma il team di ingegneri che trasforma le "saldature impossibili" in "interfacce standardizzate" sul lato della produzione.
Condivideremo regolarmente aggiornamenti e informazioni su tecniche di progettazione termica e alleggerimento, per la vostra consultazione. Grazie per l'interesse verso Walmate.
Poiché la tecnologia CTP (Cell to Pack) sovverte completamente la tradizionale struttura del pacco batteria, il "ruolo" del vassoio batteria è passato da supporto passivo del carico a integrazione attiva. La tecnologia di saldatura è diventata il fulcro della sicurezza e delle prestazioni. I requisiti di leggerezza (spessore della parete di soli 1,5 mm), sigillatura a pori zero e integrazione multi-materiale (alluminio/rame/fibra di carbonio) hanno fatto sì che la saldatura tradizionale cadesse nel dilemma della deformazione e dei difetti. Il settore sta facendo progressi attraverso l'innovazione dei materiali, l'ispezione intelligente della qualità e l'iterazione dei processi. Questo articolo analizzerà le sfide dirompenti che la CTP pone alla saldatura ed esplorerà il percorso tecnico verso elevata precisione e elevata affidabilità.
1-Analisi delle modifiche nei requisiti di progettazione strutturale dei vassoi batteria dovuti alla tecnologia CTP
La tecnologia CTP (Cell to Pack) integra direttamente le celle della batteria nel pacco batteria eliminando la struttura del modulo nel pacco batteria tradizionale. Questa innovazione tecnologica propone requisiti di aggiornamento completi e multidimensionali per la progettazione strutturale del vassoio batteria. Di seguito è riportata un'analisi specifica dal punto di vista dei materiali, delle prestazioni, del processo, dell'integrazione, ecc.:
(1) Miglioramento completo della resistenza strutturale e delle prestazioni antiurto
a. Requisiti di cuscinetto meccanico dopo l'eliminazione del modulo:
Dopo che la tecnologia CTP elimina la struttura del modulo, il vassoio batteria deve supportare direttamente le funzioni di supporto, fissaggio e buffering della forza esterna della cella della batteria. Il modulo tradizionale disperde il carico meccanico, mentre il vassoio CTP deve assorbire la deformazione di espansione della cella della batteria durante la carica e la scarica nel suo complesso (ad esempio, la forza di espansione della cella della batteria quadrata può raggiungere 10-20 kN), resistendo al contempo alle vibrazioni, all'estrusione e al carico d'impatto durante la guida del veicolo.
b. Direzione di ottimizzazione strutturale e dei materiali
· Dominanza della lega di alluminio ad alta resistenza: l'acciaio iniziale è stato gradualmente sostituito a causa del suo peso elevato e il 6061-T6 è diventato il mainstream. Ha un'elevata resistenza specifica e una forte resistenza alla corrosione, che può soddisfare i doppi requisiti di leggerezza e alta rigidità.
· Progettazione della struttura composita: ad esempio, la struttura "a trave ad anello a doppio telaio" di Leapmotor migliora la resistenza all'impatto locale attraverso compartimenti trave longitudinali e trasversali, utilizzando al contempo la tecnologia di estrusione per ottimizzare la distribuzione del materiale e ridurre il peso ridondante.
· Esplorazione della lega di magnesio-alluminio e della fibra di carbonio: la lega di magnesio-alluminio è più leggera del 30% rispetto ai tradizionali materiali in alluminio e i materiali compositi in fibra di carbonio hanno caratteristiche sia di elevata resistenza che di leggerezza, ma sono attualmente utilizzati solo nei modelli di fascia alta a causa dei costi e della maturità del processo.
(2) Requisiti per la tenuta all'aria integrata e la gestione termica
a. Miglioramento delle prestazioni di tenuta
Dopo la rimozione del modulo, la circolazione interna del refrigerante e la tenuta del gas del pacco batteria dipendono completamente dal vassoio e i difetti di saldatura (come pori e crepe) possono comportare rischi di perdite.
Figura 1-Test di tenuta all'aria del vassoio della batteria
b. Integrazione delle funzioni di gestione termica
I vassoi CTP devono integrare componenti quali piastre di raffreddamento a liquido e adesivi termoconduttivi. Ad esempio, gli adesivi strutturali vengono utilizzati per fissare le celle della batteria e trasferire lo stress di espansione, mentre gli adesivi termoconduttivi in poliuretano (conduttività termica > 1,5 W/m·K) vengono utilizzati per la conduzione del calore tra le celle della batteria e con i tubi di raffreddamento a liquido. La quantità di adesivo utilizzata in un singolo PACK è superiore di oltre il 50% rispetto a quella delle strutture tradizionali. I canali di flusso devono essere progettati all'interno del vassoio per ottimizzare l'efficienza di raffreddamento evitando al contempo danni alla tenuta causati dalla zona di saldatura interessata dal calore.
(3) Alleggerimento e innovazione dei materiali
a. Tendenze nella selezione dei materiali
Processo di estrusione e pressofusione di leghe di alluminio: i profili in alluminio estruso vengono utilizzati per le strutture del telaio (come il vassoio della batteria 4680 di Tesla) e i processi di pressofusione (come la pressofusione integrata) semplificano il processo di saldatura e riducono il peso del 15%-20%.
Applicazione di materiali compositi in plastica: ad esempio, i materiali PA6 rinforzati con fibra di vetro vengono utilizzati in parti non portanti per ridurre ulteriormente il peso, ma è necessario risolvere il problema di compatibilità con l'interfaccia di collegamento in metallo.
b. Strategia di progettazione leggera
Ottimizzazione della topologia: ridurre i materiali ridondanti tramite simulazione CAE e ridurre il peso del vassoio garantendo al contempo la resistenza.
Parete sottile e integrata: lo spessore della parete del vassoio è ridotto da 3 mm a 1,5-2 mm e componenti funzionali come staffe BMS e canali di cablaggio sono integrati per ridurre il numero di parti.
(4) Integrazione e progettazione modulare
a. Elevata integrazione dei componenti funzionali
I vassoi CTP devono integrare moduli come il sistema di gestione della batteria (BMS), connettori ad alta tensione e strati di isolamento ignifughi.
b. Progettazione modulare e compatibile
La linea di produzione di saldatura deve supportare la produzione mista di più modelli di vassoi, essere in grado di ottenere un "cambio di tipo con un clic" ed essere compatibile con strutture di vassoi di diverse dimensioni di celle della batteria (come quadrate e cilindriche).
2-Sfide specifiche dell'innovazione della tecnologia CTP per il processo di saldatura
La tecnologia CTP (Cell to Pack) ha migliorato significativamente l'utilizzo dello spazio e la densità energetica, ma ha anche posto sfide senza precedenti al processo di saldatura.
(1) La difficoltà di controllare i difetti di saldatura è aumentata drasticamente
a. Porosità e sfide di sigillatura
Dopo che la tecnologia CTP elimina il modulo, il vassoio della batteria deve assumere direttamente la funzione di sigillatura. I pori di saldatura (un difetto comune nella saldatura delle leghe di alluminio) porteranno direttamente al rischio di perdite di refrigerante o penetrazione di gas.
b. Crepe e compatibilità dei materiali
Le leghe di alluminio ad alto tenore di zinco (come la serie 7) sono soggette a crepe dovute allo stress termico durante la saldatura.
c. Errore di spazio e di assemblaggio
L'integrazione diretta di più celle porta a un aumento del numero di punti di giunzione della struttura del vassoio. L'accumulo di errori di assemblaggio può causare uno spazio di saldatura superiore a ±1 mm.
(2) Problemi di adattamento del processo causati dall'aggiornamento del sistema di materiali
a. Sfide di saldatura di materiali leggeri
Il materiale del vassoio CTP è passato dall'acciaio alla lega di alluminio (6061-T6, 7075-T6), lega di magnesio-alluminio (riduzione del peso del 30%) e materiali compositi in fibra di carbonio. La saldatura della lega di alluminio deve risolvere il problema della penetrazione insufficiente causata dalla difficile fusione del film di ossido e dall'elevata conduttività termica.
b. Tecnologia di collegamento di materiali dissimili
Quando il vassoio integra componenti funzionali come la piastra di raffreddamento a liquido (rame/alluminio) e lo strato ignifugo (materiale composito a matrice ceramica), i composti intermetallici fragili tendono a comparire all'interfaccia di materiali dissimili.
(3) Complessità strutturale migliorata e requisiti di precisione
a. Controllo della deformazione di strutture a parete sottile di grandi dimensioni
Lo spessore della parete del vassoio CTP è ridotto da 3 mm a 1,5-2 mm e la sensibilità della deformazione termica della saldatura aumenta notevolmente.
b. Giunti di saldatura ad alta densità ed efficienza di processo
Il numero di giunti di saldatura su un singolo vassoio è aumentato da 2.000 nei moduli tradizionali a oltre 5.000.
Figura 2- Saldatura del vassoio della batteria
3-Aggiornamento del processo di produzione e del controllo di qualità
La tecnologia CTP promuove la trasformazione della saldatura del vassoio della batteria da "processo singolo" a "collaborazione multi-tecnologica, intelligenza e greening". I produttori devono concentrarsi su tre direzioni principali:
Aggiornamento tecnologico: superare il controllo di difetti come pori e crepe e adattarsi a materiali leggeri;
Transizione intelligente: digitalizzazione completa del processo e ispezione di qualità AI per ottenere una produzione ad alta precisione;
Collaborazione ecologica: creare congiuntamente standard tecnici con fornitori di materiali, fornitori di apparecchiature e OEM.
Condivideremo regolarmente aggiornamenti e informazioni su tecniche di progettazione termica e alleggerimento, per la vostra consultazione. Grazie per l'interesse verso Walmate.
Materiali leggeri come le leghe di alluminio sono diventati mainstream grazie alle loro prestazioni superiori. Tuttavia, sfide come il controllo dell'apporto di calore, la soppressione della deformazione e la stabilità del processo nella saldatura a lamiere sottili pongono ostacoli significativi per le tecnologie di saldatura tradizionali. La saldatura Cold Metal Transfer (CMT), con i suoi vantaggi di basso apporto di calore, trasferimento senza spruzzi e controllo intelligente dei parametri, offre una soluzione innovativa per la produzione di vassoi per batterie.
Questo articolo approfondisce le strategie di controllo di precisione della tecnologia CMT nella saldatura a lamiere sottili per vassoi per batterie, analizzandone l'adattabilità, le sfide del processo e gli scenari applicativi compositi, con l'obiettivo di fornire una guida teorica e pratica per una produzione efficiente e di alta qualità.
Figura 1: Saldatura CMT dell'involucro inferiore di raffreddamento a liquido della batteria di accumulo di energia 104S
1-Requisiti di saldatura del vassoio batteria e adattabilità CMT
La tecnologia CMT, con il suo basso apporto di calore, il trasferimento senza spruzzi e il controllo intelligente dei parametri, si allinea perfettamente con le esigenze di alta precisione, bassa deformazione ed efficienza della saldatura del vassoio batteria.
(1) Requisiti del processo principale per la saldatura del vassoio batteria
a. Compatibilità dei materiali ed esigenze di alleggerimento
I vassoi batteria utilizzano principalmente leghe di alluminio leggere (ad esempio, serie 6xxx, 6061) o compositi in fibra di carbonio per modelli di fascia alta, che richiedono elevata resistenza (resistenza alla trazione del materiale di base 60%-70%) e bassa densità (lega di alluminio: 2,7 g/cm³).
Giunzione di materiali dissimili: per strutture ibride acciaio-alluminio, è necessario tenere conto delle differenze del coefficiente di dilatazione termica per ridurre al minimo la deformazione.
b. Qualità della saldatura e parametri delle prestazioni
Basso apporto di calore e controllo della deformazione: per piastre sottili (0,3-3 mm), la deformazione deve essere ≤2 mm. Le saldature lineari lunghe richiedono una saldatura segmentata o un design anti-deformazione.
Sigillatura e resistenza: le saldature devono essere completamente sigillate per evitare perdite di elettrolita e superare i test di taglio (ad esempio, standard T/CWAN 0027-2022).
Controllo della porosità: la saldatura della lega di alluminio è soggetta a porosità, richiedendo un tasso di porosità ≤0,5%.
c. Efficienza di produzione e requisiti di automazione
La produzione in lotti richiede una velocità di saldatura ≥7 mm/s, riducendo il tempo di saldatura a vassoio singolo a 5-10 minuti.
Le postazioni di lavoro automatizzate devono supportare la progettazione a doppia stazione (assemblaggio e saldatura simultanei) e la collaborazione multi-robot.
(2)Vantaggi principali della CMT per la saldatura dei vassoi delle batterie
a. Controllo preciso dell'apporto di calore ridotto
La CMT riduce l'apporto di calore del 33% rispetto alla saldatura MIG tradizionale, ritraendo il filo di saldatura per interrompere la corrente durante il cortocircuito delle gocce, eliminando i rischi di bruciatura per le piastre ultrasottili (0,3 mm).
I cicli alternati freddo-caldo (riscaldamento dell'arco-trasferimento delle gocce-ritrazione del filo) riducono al minimo l'accumulo di calore, controllando la deformazione a ≤1,5 mm (studi di casi BYD e BAIC).
b. Stabilità del processo e miglioramento della qualità
Saldatura senza spruzzi: la ritrazione meccanica elimina gli spruzzi delle gocce, riducendo le rilavorazioni.
Ottimizzazione della porosità: l'utilizzo del gas di protezione Ar+30%He riduce la porosità del 50% rispetto all'Ar puro, con dimensioni dei pori ≤0,3 mm.
Elevata tolleranza degli spazi: si adatta a spazi di assemblaggio fino a 1,5 mm, riducendo i requisiti di precisione dell'attrezzatura.
c. Integrazione dell'automazione e guadagni di efficienza
Le postazioni di lavoro a doppia stazione (ad esempio, progetti Taixiang Tech) consentono la saldatura e l'assemblaggio paralleli, raddoppiando l'efficienza.
La saldatura robotizzata simmetrica (sincronizzazione a doppio robot) con design anti-deformazione riduce il tempo di ciclo a ≤10 minuti.
2-Sfide nel processo CMT per i vassoi delle batterie
Figura 2: Flusso del processo di saldatura CMT
(1)Proprietà dei materiali e controllo dei difetti di saldatura
a. Sensibilità alla porosità nella saldatura delle leghe di alluminio
I vassoi in lega di alluminio (ad esempio, 6061, 6063) sono inclini alla porosità a causa della rapida solidificazione e dei cambiamenti di solubilità dell'idrogeno. La composizione del gas di protezione è fondamentale: Ar puro determina una porosità di circa il 5%, mentre Ar+30%He riduce la porosità a ≤0,5%. La regolazione dell'induttanza (ad esempio, messa a punto negativa) ottimizza il flusso del bagno fuso, riducendo al minimo le dimensioni dei pori.
b. Cracking a caldo e segregazione della composizione
La segregazione di Mg, Si, ecc. nelle leghe di alluminio può causare fragilità del bordo dei grani. Mentre il basso apporto di calore del CMT riduce la ZTA, è necessario un controllo preciso della velocità di saldatura e dell'alimentazione del filo per evitare una penetrazione insufficiente o un surriscaldamento localizzato.
c. Compatibilità metallurgica nella saldatura di materiali dissimili
Le interfacce nei giunti Al-acciaio o Al-composito (ad esempio, travi di sicurezza e involucri) devono mitigare le fasi fragili (ad esempio, FeAl₃) e l'interferenza del vapore di Zn.
(2)Sfide di ottimizzazione dei parametri di processo
a. Bilanciamento di penetrazione e apporto di calore
Le saldature devono soddisfare gli standard T/CWAN 0027 per la profondità di penetrazione (≥0,8 mm). Il basso apporto di calore del CMT può portare a una penetrazione insufficiente, richiedendo una regolazione della lunghezza dell'arco o una corrente pulsata per migliorare la penetrazione.
b. Compromesso tra velocità e stabilità
Le linee automatizzate richiedono velocità ≥1,2 m/min, ma velocità elevate rischiano l'instabilità dell'arco o un trasferimento irregolare delle gocce.
c. Gap Bridging in saldature complesse
I vassoi spesso presentano ampi spazi (0,5-1,5 mm) o giunti irregolari (ad esempio, giunti a T).
(3) Compatibilità tra progettazione strutturale e processo di fabbricazione
a. Controllo della deformazione della saldatura a piastra sottile
Lo spessore della parete dei pallet in lega di alluminio è solitamente di 2-3 mm. La deformazione della saldatura MAG tradizionale può raggiungere 1,2 mm, mentre la saldatura CMT può ridurre la deformazione a meno di 0,3 mm attraverso un basso apporto di calore. Tuttavia, è necessario collaborare con la progettazione di utensili antideformazione e la saldatura simmetrica robotizzata (postazione di lavoro a doppia stazione) per migliorare ulteriormente la precisione.
b. Continuità e sigillatura di saldature lunghe
La lunghezza della saldatura sigillata del vassoio della batteria può raggiungere diversi metri e devono essere evitate la rottura dell'arco o le fluttuazioni del bagno fuso. La tecnologia CMT garantisce l'uniformità della saldatura attraverso oltre 70 cicli di riaccensione dell'arco al secondo e il tasso di qualificazione della tenuta stagna può essere aumentato al 99% con il sistema di tracciamento laser.
c. Sinergia di applicazioni composite multi-processo
I pallet di fascia alta utilizzano spesso il processo composito CMT+FSW (saldatura a frizione): il CMT viene utilizzato per strutture complesse (come la connessione tra il telaio e la piastra inferiore). Il FSW viene utilizzato in aree ad alto carico (come le travi longitudinali) per migliorare la resistenza. Il problema di corrispondenza dei parametri di connessione dei due processi (come la temperatura di preriscaldamento e il trattamento termico post-saldatura) deve essere risolto.
3-Scenari applicativi tipici del processo CMT nella produzione di vassoi per batterie
(1) Collegamento della struttura principale del vassoio per batterie
a. Saldatura del telaio e della piastra inferiore
Il processo CMT è ampiamente utilizzato nel collegamento tra il telaio e la piastra inferiore dei vassoi per batterie in lega di alluminio, in particolare per saldature lunghe e piastre sottili (spessore 2-3 mm)
b. Collegamento tra trave e piastra inferiore
Nella progettazione dei vassoi per batterie CTP, a causa del numero ridotto di travi e della struttura complessa, il processo CMT viene utilizzato per: Saldatura di posizionamento ad alta precisione: il collegamento locale tra la trave e la piastra inferiore (come il giunto a T) deve evitare una penetrazione insufficiente. CMT raggiunge una penetrazione stabile ≥ 0,8 mm tramite il controllo digitale della lunghezza dell'arco (come la tecnologia Fonis CMT Advanced). Adattamento multi-materiale: se la trave è realizzata in lega di alluminio-magnesio (ad esempio 6061) e la piastra inferiore è in alluminio ad alta resistenza, la CMT può ridurre i pori tramite la protezione con gas misto Ar+He, adattandosi al contempo alle differenze di conduttività termica dei diversi materiali.
(2) Saldatura di piastre sottili e strutture geometriche complesse
a. Saldatura di leghe di alluminio a parete sottile (2-3 mm)
La richiesta di leggerezza per i vassoi batteria promuove l'applicazione di piastre sottili, ma la saldatura MIG tradizionale è soggetta a deformazione. I vantaggi del processo CMT sono:
b. Saldatura di piastre ultrasottili: Taixiang Automation utilizza la tecnologia CMT per ottenere una saldatura senza spruzzi di piastre ultrasottili da 0,3 mm per le strutture di sigillatura dei bordi del vassoio batteria.
c. Bridging di saldature di forma speciale: per strutture di forma speciale come nervature di rinforzo interne e travi anticollisione del vassoio, la modalità CMT Gap Bridging può riempire lo spazio di 0,5-1,5 mm tramite la retrazione del filo e il reindirizzamento dell'arco per evitare difetti non fusi.
d. Saldature con elevati requisiti di tenuta: la sigillatura del vassoio batteria è direttamente correlata alla sicurezza della batteria. Il processo CMT lo garantisce nei seguenti modi:
· Saldature lunghe continue: utilizzando più di 70 cicli di riaccensione dell'arco al secondo (come la tecnologia Fronius LaserHybrid) per garantire la continuità di diversi metri di saldature, con un tasso di passaggio ermetico del 99%.
· Controllo del basso apporto di calore: rispetto alla saldatura laser, la CMT ha un apporto di calore inferiore, il che riduce l'impatto termico delle fluttuazioni del bagno fuso sullo strato sigillante ed è adatta al processo di rivestimento con colla.
(3) Scenario di produzione di compositi multiprocesso
a. Processo composito CMT+FSW
Nelle linee di produzione di vassoi per batterie di fascia alta, CMT è spesso coordinato con la saldatura a frizione e agitazione (FSW):
Divisione del lavoro e cooperazione: CMT è utilizzato per la saldatura flessibile di strutture complesse (come telai e giunti di forma speciale) e FSW è utilizzato per aree ad alto carico (come travi longitudinali) per migliorare la resistenza. Ad esempio, la linea di produzione automatizzata di Shanghai Weisheng utilizza una combinazione di CMT+FSW+CNC per aumentare l'efficienza di produzione del vassoio del 30%.
Ottimizzazione della connessione di processo: la linea di produzione di Huashu Jinming adotta un design modulare e ottiene una connessione senza soluzione di continuità con FSW tramite la corrispondenza dei parametri di preriscaldamento (come il riscaldamento locale a 150 °C dopo la saldatura CMT).
b. In combinazione con la tecnologia di rivettatura FDS/SPR
Nella tecnologia CTP di seconda generazione, CMT è coordinata con la tecnologia di autoserraggio a frizione (FDS) e di rivettatura autoperforante (SPR): Soluzione di connessione ibrida: ad esempio, l'area portante del telaio e la piastra inferiore adottano FSW, mentre le parti staccabili (come piastre di raffreddamento ad acqua e strati isolanti) sono preposizionate dalla saldatura CMT e quindi fissate dalla rivettatura FDS, tenendo conto sia della resistenza che della praticità di manutenzione.
Condivideremo regolarmente aggiornamenti e informazioni su tecniche di progettazione termica e alleggerimento, per la vostra consultazione. Grazie per l'interesse verso Walmate.
Come ingegnere operativo in una fabbrica di produzione di vassoi per batterie, ho partecipato a numerosi progetti per involucri di batterie di veicoli elettrici, sperimentando direttamente il delicato equilibrio tra "leggerezza, sicurezza e costo" nel settore. Questo articolo analizzerà la logica di selezione delle attuali tecnologie e le sfide industriali, suddividendo l’analisi in tre dimensioni: materiali, processi produttivi e tendenze future, con esempi pratici.
1-Percorso dei materiali: Bilanciamento tra leggerezza e costo
La scelta dei materiali per l’involucro della batteria influisce direttamente sulle prestazioni del veicolo e sull’economicità. Le principali opzioni attuali sono leghe di alluminio, acciai ad alta resistenza e materiali compositi, ciascuno con scenari applicativi specifici.
a. Leghe di alluminio: Il pilastro della leggerezza
Profilati in alluminio estruso: Modelli BYD utilizzano profilati estrusi, ottimizzando la forma della sezione per ridurre il peso e aumentare la rigidità strutturale.
Pressofusione integrata: La batteria Tesla 4680 con tecnologia CTC riduce il peso del 50%, ma richiede costi di stampaggio superiori a 200 milioni di RMB, ammortizzabili solo con produzioni annue oltre 500.000 unità, adatto a grandi produttori.
Materiali compositi in alluminio: La Porsche Taycan usa una struttura mista alluminio-fibra di carbonio, riducendo il peso del 15%, ma con un costo incrementale del 30%, limitato ai modelli premium.
b. Acciai ad alta resistenza: La soluzione per mercati sensibili al costo
L’acciaio termoformativo (es. 22MnB5) raggiunge una resistenza a snervamento di 1500 MPa, con una penetrazione del 40% nei veicoli commerciali. Il costo per GWh è inferiore del 40% rispetto all’alluminio, ma la densità energetica si riduce dell’8%. Ideale per modelli sotto i 100.000 RMB, bilanciando costo e sicurezza base.
c. Materiali compositi: Sperimentazioni nel segmento premium
SMC (Sheet Molding Compound): Il guscio superiore della batteria in vetroresina riduce il peso del 30% rispetto all’acciaio, ma richiede spessori maggiori (3mm + rinforzi da 5mm) per compensare la resistenza agli urti.
Fibra di carbonio: L’involucro della BMW i3 è del 50% più leggero dell’alluminio, ma il costo raggiunge 800 RMB/kg, rendendolo adatto solo a modelli di lusso.
Sintesi pratica: La scelta del materiale deve allinearsi al posizionamento del veicolo. Il mercato mid-range (200.000-300.000 RMB) privilegia l’alluminio, quello entry-level l’acciaio, mentre i modelli premium esplorano soluzioni composite.
2-Processi produttivi: Equilibrio tra efficienza e affidabilità
I processi di produzione influenzano direttamente efficienza e affidabilità. Le principali tecnologie includono pressofusione, saldatura di profilati e integrazione strutturale.
a. Pressofusione VS saldatura di profilati
Profilati in alluminio estruso (es. Chevrolet Bolt): Costo unitario ~800 RMB, adatto a grandi volumi, ma processi complessi.
Pressofusione in alluminio (es. NIO ET5): Costo unitario 1500 RMB, ma efficienza produttiva quintuplicata, ideale per produzioni rapide.
Saldatura a attrito (FSW): Riduzione del 50% delle deformazioni rispetto alla saldatura ad arco, con resistenza a fatica migliorata del 30%, ma richiede un investimento in macchinari superiore del 40%, adatto a veicoli commerciali.
b. Tecnologie di integrazione strutturale
CTP (Cell to Pack) - Batteria CATL Qilin: L’utilizzo dello spazio passa dal 72% all’85%, con riduzione dei costi del 15-20%, ma richiede miglioramenti nella protezione termica.
CTC (Cell to Chassis) - Tesla Model Y: Riduzione di 370 componenti, autonomia +54%, ma costi di riparazione +300%, sfidando i sistemi post-vendita.
Confronto dei dati chiave
Esperienza nella linea di produzione: la tecnologia CTP è ancora quella più diffusa grazie alla sua elevata compatibilità; la tecnologia CTC invece richiede una collaborazione approfondita tra le case automobilistiche e i produttori di batterie ed è improbabile che venga diffusa nel breve termine.
3-Tendenze future: Fusione tecnologica e innovazione intelligente
a. Materiali ibridi
Strutture miste alluminio-fibra di carbonio (es. concept Porsche Taycan) riducono il peso del 15% con resistenza a compressione di 800 MPa, ma la stabilità del processo è critica (es. Toyota bZ4X ha una resa del 65%).
b. Integrazione funzionale
Piastre di raffreddamento integrate (es. batteria "Magazine" di GAC): Superficie di contatto +50%, controllo della temperatura entro ±5°C, ma richiede ottimizzazione della saldatura laser per ridurre la porosità.
Sensori a fibra ottica (Continental): Monitoraggio in tempo reale di deformazioni e temperatura, con tempi di risposta BMS +30%, ma necessità di migliorare la durata dei sensori.
c. Sostenibilità e riciclo
La tecnologia BMW di riciclo in ciclo chiuso riduce le emissioni del 60%, ma la perdita di prestazioni dei materiali riciclati deve rimanere sotto il 10%. La pressofusione di grandi componenti (es. pressa da 9000T di LK) richiede controllo termico preciso (±5°C), con la rimozione delle sbavature come collo di bottiglia.
Direzioni di innovazione:
Riduzione del ciclo di formatura dei compositi (es. LGF-PP da 180 a 90 secondi).
Applicazione di gemelli digitali per ridurre l’errore di simulazione da ±20% a ±5%, migliorando l’affidabilità progettuale.
4-Stratificazione del mercato e prospettive
Breve termine (1-3 anni): CTP + profilati in alluminio restano dominanti, con CATL leader (34% di quota).
Medio termine (5-10 anni): CTC e fibra di carbonio accelerano nel premium, raggiungendo il 25% di quota entro il 2030.
Lungo termine: Densità energetica verso 400 Wh/kg, miglioramento della sicurezza oltre gli standard attuali (30 minuti di protezione termica).
5-Conclusione
La scelta del percorso tecnologico per gli involucri delle batterie è una questione di "adattamento allo scenario", bilanciando posizionamento del produttore, soglie di costo e maturità della supply chain. Come ingegneri, dobbiamo abbracciare l’innovazione mantenendo la fattibilità industriale, cercando l’equilibrio dinamico tra leggerezza, sicurezza e costo. Con l’avanzamento di tecnologie intelligenti e sostenibili, gli involucri evolveranno da "protezione passiva" a "sicurezza attiva", supportando la diffusione globale dei veicoli elettrici.
Condivideremo regolarmente aggiornamenti e informazioni su tecniche di progettazione termica e alleggerimento, per la vostra consultazione. Grazie per l'interesse verso Walmate.
Nel processo effettivo di produzione, assemblaggio e utilizzo, si verifica spesso il guasto della tensione di tenuta dell'isolamento dei vassoi batteria, come una barriera corallina nascosta nel rapido sviluppo della nuova industria energetica, che minaccia la sicurezza di guida dei veicoli e il funzionamento affidabile del sistema di accumulo di energia. Questo articolo tenta di analizzare le tipiche modalità di guasto basate sulla pratica di produzione, al fine di fornire alcuni riferimenti superficiali per i professionisti interessati e aiutare i colleghi del settore a esplorare congiuntamente modi efficaci per migliorare le prestazioni della tensione di tenuta dell'isolamento dei vassoi batteria.
Parte 3 - Analisi dei guasti comuni
Figura 1 Prova di tensione di tenuta all'isolamento
1- Analisi dei meccanismi di guasto comuni
Gli scenari applicativi dei vassoi batteria per l'accumulo di energia e dei nuovi veicoli energetici sono diversi, con conseguenti somiglianze e differenze nei requisiti di tensione di tenuta dell'isolamento e nelle condizioni di guasto, come segue:
a. Differenze
Carico dinamico: i nuovi veicoli energetici devono gestire vibrazioni meccaniche ad alta frequenza di 20-2000 Hz, mentre i sistemi di accumulo di energia affrontano principalmente deformazioni statiche a lungo termine, con un tempo di deformazione cumulativo superiore a 10 anni.
Livello di tensione: la tensione di tenuta dell'isolamento dei vassoi batteria dei nuovi veicoli energetici deve raggiungere 3000 V CC e oltre (in base a GB 38031), mentre i sistemi di accumulo di energia richiedono una tensione di tenuta dell'isolamento di 4200 V CA e oltre (in base a IEC 61439).
Fattore di accelerazione del guasto: i nuovi veicoli energetici generano stress termico a causa di oltre 2000 cicli di carica e scarica all'anno, il che accelera il guasto dell'isolamento; i sistemi di accumulo di energia funzionano 24 ore su 24, 7 giorni su 7, con un tempo di funzionamento annuo medio di oltre 8000 ore, con conseguente invecchiamento elettrochimico, che a sua volta accelera il guasto dell'isolamento.
b. Punti comuni
Entrambi devono ottenere un avviso tempestivo del guasto dell'isolamento tramite il monitoraggio della resistenza di isolamento (non inferiore a 100 MΩ a freddo e non inferiore a 1 MΩ/kV a caldo) e il controllo della scarica parziale (inferiore a 5 pC).
2- Comuni difetti di fabbricazione che causano guasti alla tensione di tenuta dell'isolamento dei vassoi batteria
(1) Fase di costruzione della tensione di tenuta dell'isolamento
a. Potenziale guasto e analisi delle cause
· Difetti dei materiali:
Causa: il livello di tensione di tenuta del materiale isolante è insufficiente, invecchiamento dovuto a umidità o contaminazione superficiale (macchie di olio, detriti metallici).
Prestazioni: bassa resistenza di isolamento (<100 MΩ), corrente di dispersione superiore allo standard o guasto diretto durante il test di tensione di tenuta.
· Problemi di processo:
Causa: detriti metallici residui (processo di saldatura/taglio approssimativo), spessore irregolare del rivestimento isolante o non polimerizzato.
Prestazioni: scarica parziale, danni allo strato isolante causano cortocircuito.
· Interferenza ambientale:
Causa: alte temperature e alta umidità causano assorbimento di umidità nel materiale e corrosione chimica.
Prestazioni: le prestazioni di isolamento si deteriorano con l'ambiente e l'acqua di condensa causa dispersione. · Errori di prova:
Causa: impostazione errata della tensione/tempo di prova (ad esempio non conforme allo standard GB/T 38661), messa a terra scadente.
Prestazioni: valutazione errata di danni da sovratensione o qualificazione dei componenti.
b. Strategia di risposta
· Ottimizzazione dei materiali: selezionare materiali a prova di umidità (come materiali compositi in fibra di carbonio) con una tensione di tenuta di ≥1000 V CC e applicare un rivestimento anti-incrostazione.
· Controllo del processo: utilizzare apparecchiature di saldatura/spruzzatura automatizzate e allestire un'officina pulita.
· Gestione ambientale: installare il monitoraggio della temperatura e dell'umidità e pre-essiccare i materiali prima della costruzione.
· Specifiche del test: test segmentati (pre-test 500 V + test formale 1000 V), calibrare gli strumenti e registrare i dati.
(2) Fase di installazione del modulo
a. Analisi di potenziali guasti e cause
· Errore di assemblaggio:
Causa: il rivestimento isolante è mancante e i bulloni sono troppo stretti e lo strato isolante è danneggiato.
Prestazioni: bassa resistenza di isolamento tra il modulo e il guscio e resistenza alla rottura della tensione.
· Danni meccanici
Causa: graffi sugli utensili di movimentazione, detriti metallici che perforano la pellicola isolante.
Prestazioni: cortocircuito locale o guasto improvviso durante il funzionamento.
· Compatibilità di progettazione
Causa: spazio elettrico insufficiente a causa della deviazione delle dimensioni tra il modulo e il vassoio.
Prestazioni: la capacità parassita causa la rottura della sovrapposizione di tensione.
· Pericoli di collegamento elettrico:
Causa: usura e rottura della guarnizione del connettore a causa del cablaggio non fissato.
Prestazioni: usura e perdita dello strato isolante del cablaggio ad alta tensione.
b. Contromisure
· Progettazione a prova di errore: utilizzare utensili con perni di posizionamento per evitare installazioni mancanti e personalizzare la lunghezza del bullone per evitare un serraggio eccessivo.
· Funzionamento pulito: pulire con l'aspirapolvere prima dell'installazione e avvolgere gli utensili con silicone antigraffio.
· Simulazione di tolleranza: verificare il grado di corrispondenza tra il modulo e il vassoio tramite CAE per garantire che lo spazio sia ≥10 mm.
· Ispezione del processo: dopo l'installazione, eseguire un'ispezione casuale con un megaohmetro (≥100 MΩ) ed eseguire un test di tensione di tenuta segmentato per individuare il punto di guasto.
(3) Fase di integrazione del sistema
a. Analisi di potenziali guasti e cause
· Guasto dell'interfaccia tra sistemi:
Causa: i parametri di isolamento dei componenti non corrispondono (ad esempio differenze nella classificazione della tensione di tenuta del connettore).
Prestazioni: rottura della connessione della barra di distribuzione ad alta tensione o interferenza BMS.
· Sovrapposizione di capacità parassita:
Causa: la capacità parassita totale aumenta dopo che più moduli sono collegati in parallelo e l'effetto di aumento della capacità è significativo.
Prestazioni: la corrente di dispersione del test a livello di sistema supera lo standard.
· Guasto da stress ambientale:
Causa: le vibrazioni causano affaticamento dell'isolamento e il refrigerante si infiltra nell'interfaccia ad alta tensione.
Prestazioni: la resistenza dell'isolamento diminuisce periodicamente durante il funzionamento.
· Punto cieco del test:
Causa: mancata simulazione delle condizioni di lavoro reali (alta temperatura/vibrazione/umidità).
Prestazioni: superato in laboratorio ma non superato nel funzionamento effettivo.
b. Contromisure
· Progettazione della compatibilità: unificare gli standard dei componenti del fornitore. · Controllo della capacità parassita: aggiungi uno strato di isolamento in poliimmide e ottimizza il layout tramite simulazione SPICE.
· Test di simulazione delle condizioni di lavoro: esegui il test composito "ciclo -40℃~85℃ + vibrazione 5Hz~200Hz + tensione di tenuta".
· Monitoraggio intelligente: modulo di monitoraggio dell'isolamento online integrato, l'intelligenza artificiale prevede potenziali rischi.
3-Test di tensione di tenuta all'isolamento
Il test di tensione di tenuta all'isolamento è sia una misura di sicurezza che una possibile causa di guasto. Il test di tensione di tenuta all'isolamento stesso può causare guasti dovuti a funzionamento improprio, problemi all'apparecchiatura o difetti di progettazione e persino causare danni secondari al dispositivo sottoposto a test.
(1) Tipi comuni di guasto durante il test
(2) Le strategie di risposta sono le seguenti:
a. Controllo preciso dei parametri di prova
· Tensione e tempo: impostati in base agli standard; abilita l'algoritmo di compensazione dinamica per carichi capacitivi (come i moduli batteria) per sopprimere l'effetto di aumento della capacità.
· Soglia di corrente di dispersione: impostata in base alle specifiche dell'apparecchiatura (come ≤10mA) e distingui tra modalità CC/CA (il test CC richiede una soglia inferiore).
b. Specifiche dell'apparecchiatura e del funzionamento
· Calibrazione dello strumento: il tester di tensione di tenuta viene calibrato ogni 6 mesi e lo strato di isolamento della linea ad alta tensione viene ispezionato visivamente ogni giorno.
· Funzionamento sicuro: disconnessione forzata dei circuiti a bassa tensione prima del test; utilizzare bracci robotici o dispositivi automatici per evitare il contatto manuale con aree ad alta tensione.
c. Prevenzione e riparazione dei guasti
· Test segmentati: testare sistemi complessi in moduli (come testare prima il bus ad alta tensione, quindi testare l'isolamento del modulo) per individuare il punto di guasto. · Riparazione guasti: utilizzare resina epossidica per riempire l'area danneggiata dopo il guasto e, dopo la riparazione, è necessario superare nuovamente il test del gradiente di tensione completo (ad esempio pressione a gradino 500 V→1000 V).
d. Gestione ambiente e dati
· Controllo ambientale: avviare il deumidificatore quando l'umidità nell'area di prova è superiore al 75% o ritardare il test fino a quando l'ambiente non soddisfa lo standard.
· Tracciabilità dei dati: registrare la tensione di prova, la curva della corrente di dispersione e i parametri ambientali e utilizzare il sistema MES per associare il numero del lotto di produzione.
Condivideremo regolarmente aggiornamenti e informazioni su tecniche di progettazione termica e alleggerimento, per la vostra consultazione. Grazie per l'interesse verso Walmate.
Il vassoio della batteria utilizza materiali isolanti principalmente per prevenire perdite di corrente, proteggere la sicurezza del personale e garantire il normale funzionamento del sistema della batteria. Nella selezione, è necessario considerare le proprietà isolanti del materiale, la resistenza al calore, la stabilità chimica e la resistenza meccanica. Questi fattori insieme determinano l'effetto dell'applicazione del materiale isolante nel vassoio della batteria, influenzando così la sicurezza e l'affidabilità dell'intero sistema della batteria.
Sicurezza dell'isolamento elettrico del vassoio batteria | Parte 2 - Garanzia delle prestazioni di resistenza alla pressione
Figura 1 Vassoio della batteria del veicolo elettrico
1-Selezione del materiale isolante e progettazione della soluzione
Nella selezione dei materiali isolanti per i vassoi batteria, l'attenzione è rivolta alle proprietà dielettriche, alla tolleranza ambientale e alle proprietà meccaniche dei materiali. Di seguito sono riportati 6 materiali isolanti comunemente utilizzati nei vassoi batteria e le relative informazioni:
Quando si progetta una soluzione, in genere è necessario considerare in modo completo i tre fattori chiave dello scenario applicativo, dei requisiti di prestazione e del budget dei costi per selezionare il materiale isolante appropriato. Ad esempio:
(1) Selezionare in base allo scenario applicativo: in un sistema di batterie di accumulo di energia ad alta tensione e alta corrente, se il lato del vassoio della batteria richiede materiale isolante ad alte prestazioni, si consiglia di utilizzare la soluzione di fissaggio del film PI; se i requisiti di prestazione dell'isolamento non sono elevati, è possibile selezionare la soluzione di spruzzatura di polvere isolante. Per la piastra inferiore del vassoio della batteria, se si cerca una soluzione di isolamento a basso costo, la soluzione di spruzzatura di polvere isolante o di rivestimento di vernice isolante è più adatta.
(2) Selezionare in base ai requisiti di prestazione: quando i requisiti di prestazione dell'isolamento, resistenza alle alte temperature, resistenza alla corrosione chimica, ecc. sono elevati, la soluzione di fissaggio del film PI è una scelta migliore; se questi requisiti di prestazione sono relativamente bassi, la soluzione di spruzzatura di polvere isolante o di rivestimento di vernice isolante può soddisfare le esigenze.
(3) Selezionare in base al budget dei costi: quando il budget dei costi è limitato, la soluzione di spruzzatura di polvere isolante o di rivestimento di vernice isolante è più economica; quando il budget di spesa è sufficiente, è possibile scegliere la soluzione di fissaggio della pellicola PI.
2-Requisiti tecnici per la pellicola PI per i vassoi delle batterie
(1) Materiale: PI, spessore della pellicola di base 0,1-0,14 mm, spessore adesivo posteriore 0,03 mm, conduttività termica della pellicola PI > 0,3 W/(m·k);
(2) Resistenza alla pressione: CA 3000 V, 60 S, corrente di dispersione ≤ 0,5 mA;
(3) (pasta fredda) resistenza alla pelatura a 180° ≥ 15 N/24 mm;
(4) Isolamento: CC 1500 V, 60 S, resistenza di isolamento > 1000 MΩ;
(5) Prestazioni di isolamento della resistenza al calore e all'elettrolita: a 500 ℃, tensione CC 700 V, aggiungere 2 ml di elettrolita (area di prova 13000 mm<H>2<H>), conservare per 1 ora, nessuna rottura e nessuna scintilla; (6) Prestazioni termiche e di isolamento: a 500±2℃, continuare la cottura (forno a muffola) per 0,5 ore, la morfologia complessiva del campione cambia senza combustione spontanea e il campione passa due volte. CA 1000 V viene applicata alla superficie e la tensione viene aumentata da 0 V a 3000 per 10 S, quindi continuata per 60 S. Il campione testato non presenta rotture e scintille;
(7) Grado ignifugo: UL94 V-0;
(8) Alta temperatura e alta umidità: dopo 1000 ore di test a 85℃ e 85% di umidità, il campione non presenta crepe e deformazioni, soddisfacendo lo standard nazionale "GBT 13542.6-2006 Pellicola isolante elettrica Parte 6: Pellicola in poliimmide per isolamento elettrico" sulla resistenza di isolamento, valore di tensione di tenuta e requisiti di resistenza elettrica. La resistenza alla trazione, l'allungamento a rottura e la resistenza alla pelatura sono ridotte di meno del 30% rispetto al materiale non invecchiato;
(9) Shock caldo e freddo: 85℃ per un'ora, commutato a -40℃ per un'ora, quindi commutato a 85℃ per cicli ad alta e bassa temperatura. Il tempo di commutazione è incluso in un'ora e il tempo di commutazione è ≤3min. Dopo 1000 ore di cicli ad alta e bassa temperatura, il campione non presenta crepe e deformazioni, soddisfacendo lo standard nazionale "GBT 13542.6-2006 Pellicola isolante elettrica Parte 6: Pellicola in poliimmide per isolamento elettrico" per resistenza di isolamento, valore di tensione di tenuta e requisiti di resistenza elettrica. La resistenza alla trazione, l'allungamento a rottura e la resistenza alla pelatura sono ridotte di meno del 30% rispetto al materiale non invecchiato. (10) Prova di nebbia salina: prova di nebbia salina neutra (NSS) secondo lo standard GB/T 10125, temperatura 35℃, umidità ≥85%RH, la soluzione di prova è (5±0,1%) (frazione di massa) NaCl, PH=6,5~7,2, spruzzatura continua per 72 ore. Dopo la prova di nebbia salina, il campione non presenta crepe né deformazioni, soddisfacendo lo standard nazionale "GBT 13542.6-2006 Pellicola isolante elettrica Parte 6: Pellicola in poliimmide per isolamento elettrico" per resistenza di isolamento, valore di tensione di tenuta e requisiti di resistenza elettrica. La resistenza alla trazione, l'allungamento a rottura e la resistenza alla pelatura sono ridotte di meno del 30% rispetto al materiale non invecchiato.
(11) Il prodotto è conforme a RoHS.
Figura 2 Pellicola PI per il vassoio della batteria
3-Metodi di prova della tensione di tenuta dell'isolamento e soluzioni ai problemi comuni
(1) Metodo di prova della tensione di tenuta dell'isolamento
La prova della tensione di tenuta dell'isolamento è un mezzo importante per valutare le prestazioni di isolamento delle apparecchiature elettriche, principalmente tra cui la prova della tensione di tenuta CC e la prova della tensione di tenuta CA. La prova della tensione di tenuta CC rileva se il materiale isolante si rompe entro un tempo specificato applicando alta tensione CC. L'apparecchiatura include un generatore di alta tensione CC, un voltmetro, ecc. I passaggi sono l'applicazione della tensione, il mantenimento della tensione e la riduzione della tensione. La prova della tensione di tenuta CA applica alta tensione CA. L'apparecchiatura e i passaggi sono simili alla prova CC. Entrambi i metodi richiedono una preparazione prima della prova per garantire che l'apparecchiatura sia ben messa a terra e che le condizioni della superficie del materiale isolante siano attentamente osservate durante la prova.
(2) Problemi comuni e soluzioni
I problemi comuni nella prova della tensione di tenuta dell'isolamento includono la rottura dell'isolamento, la corrente di dispersione eccessiva e il guasto dell'apparecchiatura di prova. La rottura dell'isolamento può essere causata da prestazioni insufficienti del materiale isolante, difetti interni o umidità. Le soluzioni includono la selezione di materiali di alta qualità, il rafforzamento della manutenzione e il miglioramento della struttura isolante. Una corrente di dispersione eccessiva può essere causata da una ridotta resistenza di isolamento, contaminazione superficiale o insufficiente accuratezza dell'apparecchiatura di prova. Le soluzioni includono il mantenimento del materiale isolante pulito e asciutto e la calibrazione dell'apparecchiatura di prova. Il guasto dell'apparecchiatura di prova può essere causato dall'invecchiamento dell'apparecchiatura, da una manutenzione impropria o da un funzionamento improprio. Le soluzioni includono una manutenzione regolare, un funzionamento corretto e una riparazione tempestiva.
Condivideremo regolarmente aggiornamenti e informazioni su tecniche di progettazione termica e alleggerimento, per la vostra consultazione. Grazie per l'interesse verso Walmate.
Con il rapido sviluppo dei veicoli a nuova energia e delle tecnologie di accumulo energetico, la sicurezza e l'affidabilità dei sistemi batteria, in qualità di vettori energetici centrali, hanno attirato grande attenzione. Come struttura di supporto e protezione del modulo batteria, le prestazioni di isolamento elettrico del vassoiobatteria sono direttamente collegate alla sicurezza operativa del veicolo, alla durata della batteria e all'incolumità degli utenti.La progettazione della sicurezza elettrica del vassoiobatteria costituisce la base della sicurezza del sistema batteria. Attraverso protezioni multilivello come isolamento, struttura, termica e monitoraggio, garantisce il funzionamento stabile della batteria in condizioni operative complesse, riduce i rischi di incendio, esplosione o folgorazione dovuti a guasti elettrici, prolungando la durata della batteria e migliorando l'affidabilità del sistema.
Questo articolo si concentra sulla sicurezza dell'isolamento elettrico dei vassoi delle batterie, spiegando sistematicamente i suoi principi di progettazione, il metodo di verifica delle prestazioni di resistenza alla pressione e l'analisi delle cause principali e le strategie di miglioramento dei casi di guasto tipici, al fine di fornire supporto teorico e riferimento pratico per la progettazione ad alta sicurezza dei sistemi di batterie.
Capitolo 1 Punti di progettazione
Il nucleo della progettazione della sicurezza elettrica del sistema batteria risiede nella trinità "prevenzione-controllo-emergenza": prevenire i guasti attraverso isolamento, connessioni affidabili e gestione termica; ottenere il controllo in tempo reale mediante sensori e BMS; utilizzare design antincendio e sfiato pressione per situazioni estreme. Tutti i punti chiave devono operare sinergicamente per garantire sicurezza e affidabilità del sistema batteria durante l'intero ciclo vitale, considerando anche manutenibilità e conformità normativa.Il vassoiobatteria non è solo un supporto strutturale nel sistema batteria, ma assolve molteplici funzioni tra cui isolamento elettrico, gestione termica, antiscivolo, protezione meccanica, messa a terra e design modulare, elementi cruciali per la sicurezza elettrica del sistema.
1-Il supporto strutturale garantisce l'affidabilità della connessione elettrica
Il vassoio della batteria garantisce l'affidabilità e la sicurezza dei collegamenti elettrici in condizioni di lavoro complesse fissando i moduli della batteria, riducendo le sollecitazioni meccaniche, resistendo a vibrazioni e urti, mantenendo l'allineamento e integrando protezione ambientale e gestione termica.
Figura 1 Vassoio batteria
A.Il supporto fisico e il fissaggio assicurano l'allineamento preciso dei punti di collegamento elettrico (come barre collettrici, cablaggi e connettori) per evitare un contatto scadente causato da deformazione o spostamento strutturale; forniscono un telaio rigido per fissare i moduli batteria e i connettori per evitare allentamenti o rotture causati da vibrazioni o urti.
B.Isolamento e protezione ambientale: impediscono l'intrusione di vapore acqueo, polvere, nebbia salina, ecc. tramite un design di tenuta (come IP67/IP68), evitano cortocircuiti causati da corrosione o guasti dell'isolamento; bloccano urti meccanici esterni o impatti di corpi estranei per proteggere i componenti di collegamento ad alta tensione.
C.Sinergia di gestione termica: la struttura di dissipazione del calore integrata (come piastra di raffreddamento a liquido, pad termico) bilancia la temperatura per evitare che il surriscaldamento locale causi ossidazione o saldatura dei punti di collegamento; riducono l'interferenza termica tra moduli adiacenti tramite un design di isolamento termico per evitare differenze di espansione del materiale causate da gradienti di temperatura.
D.Supporto per la compatibilità elettromagnetica (EMC): sopprimono l'interferenza elettromagnetica tramite uno strato di schermatura metallica o un rivestimento conduttivo per proteggere le linee di segnale a bassa tensione (come le linee di comunicazione BMS) dalle interferenze del circuito ad alta tensione.
2-La protezione dell'isolamento crea un ambiente di isolamento efficiente
L'obiettivo della progettazione dell'isolamento elettrico della batteria è creare un ambiente in grado di isolare efficacemente l'elettricità ad alta tensione e garantire un funzionamento efficiente del sistema, assicurando che il modulo batteria possa essere imballato in modo sicuro in qualsiasi condizione operativa, impedendo il rilascio accidentale di energia elettrica ed evitando così potenziali rischi elettrici.
A.La struttura del vassoio della batteria tiene conto sia della protezione del carico che dell'isolamento:
l I materiali in lega di alluminio, come la lega di alluminio estrusa, sono preferiti per ottenere leggerezza mantenendo elevata rigidità e resistenza agli urti. Il telaio esterno è utilizzato per sopportare il peso dell'intero sistema di batterie e l'impatto esterno. I profili a sezione chiusa sono utilizzati per migliorare la resistenza strutturale. Il telaio interno è progettato per supportare i moduli della batteria e le piastre raffreddate ad acqua, ecc., per garantirne la stabilità e i requisiti di dissipazione del calore.
l I materiali isolanti sono utilizzati come cuscinetti o rivestimenti per garantire un buon isolamento elettrico tra il modulo della batteria e il vassoio. Il cablaggio ad alta tensione deve avere un percorso di gestione dedicato e una guaina isolante per garantire la distanza di sicurezza elettrica e la distanza di dispersione con il vassoio.
l Le tecnologie di saldatura avanzate come la saldatura a frizione a mescolamento sono utilizzate per migliorare la resistenza della connessione riducendo al contempo le zone interessate dal calore, evitando deformazioni e potenziali crepe. Per le parti che sono scomode da saldare, vengono utilizzati collegamenti a bullone o rivettatura, combinati con sigillanti, per garantire l'affidabilità dei collegamenti meccanici e l'isolamento elettrico.
l Durante la progettazione si tiene conto della modularità per facilitare la sostituzione e la manutenzione delle batterie senza compromettere la stabilità della struttura complessiva.
Figura 2 Diagramma schematico della distanza di isolamento elettrico e della distanza di fuga
B.Punti chiave della progettazione dell'isolamento ad alta e bassa tensione:
l I punti positivo e negativo del sistema della batteria devono essere isolati dal sistema di alimentazione a bassa tensione e dal vassoio della batteria per garantire che vi sia sufficiente distanza di sicurezza elettrica e distanza di dispersione tra il circuito ad alta tensione e il circuito di controllo a bassa tensione per soddisfare gli standard di sicurezza e prevenire perdite di alta tensione nel sistema a bassa tensione.
l La progettazione dell'isolamento ad alta e bassa tensione deve considerare la compatibilità elettromagnetica (EMC) per garantire che le misure di isolamento non introducano interferenze e mantengano il sistema in funzione in modo stabile.
l Collegamento ad alta impedenza, i sistemi ad alta e bassa tensione sono collegati tramite alta impedenza e solo la massa della carrozzeria del veicolo (vassoio della batteria) può limitare il flusso di corrente per garantire che il guasto del sistema ad alta tensione si diffonda al sistema a bassa tensione.
l Misure di isolamento fisico, quando si progetta il vassoio della batteria, i componenti ad alta e bassa tensione possono essere disposti in diverse camere chiuse per ridurre l'influenza reciproca tramite separazione fisica; utilizzare materiali isolanti come cuscinetti tra il modulo della batteria e il vassoio, come polimeri plastici o gomma, per garantire l'isolamento fisico ed elettrico. Durante la progettazione, valutare la manutenibilità delle misure di isolamento per garantire che possano essere riparate o sostituite in modo sicuro quando necessario.
C.Punti chiave della progettazione della protezione dai contatti:
l Gestione del cablaggio ad alta tensione: i cablaggi ad alta tensione devono essere adeguatamente avvolti in guaine isolanti e gestiti in modo ordinato tramite clip di fissaggio o canaline per evitare l'esposizione e ridurre il rischio di contatto diretto.
l Pareti di sicurezza: le partizioni isolanti sono posizionate tra i moduli batteria e tra i moduli batteria e le pareti del vassoio per prevenire il rischio di scosse elettriche indirette causate da perdite di elettrolita quando la batteria è danneggiata.
l Imballaggio dei componenti ad alta tensione: i componenti chiave come i connettori ad alta tensione e i relè sono imballati per garantire che questi componenti non vengano toccati direttamente per errore anche all'interno del vassoio.
l Design chiuso: il vassoio della batteria è progettato come una struttura chiusa nel suo insieme, utilizzando un guscio metallico o composito per garantire che i componenti interni ad alta tensione non siano esposti e il guscio stesso deve anche avere buone proprietà isolanti.
l Meccanismo di bloccaggio: per i punti di collegamento ad alta tensione manutenibili, viene utilizzato un meccanismo di bloccaggio per garantire che non vengano aperti facilmente durante operazioni non professionali, riducendo il rischio di contatto accidentale.
l Applicazione di materiale isolante: i materiali isolanti sono utilizzati come strato isolante tra il vassoio della batteria e il modulo della batteria per garantire che, anche se il vassoio è danneggiato, il corpo umano possa essere impedito di entrare in contatto diretto con le parti sotto tensione. Questi materiali includono, ma non sono limitati a, polimeri plastici, guarnizioni in gomma o rivestimenti.
3-Design del logo elettrico
L'identificazione elettrica del vassoio della batteria può non solo migliorare la sicurezza del funzionamento, ma anche semplificare il processo di manutenzione e ridurre il rischio di funzionamento errato.
A.Identificazione chiara
l Segnare chiaramente i segnali di avvertimento come "Pericolo di alta tensione" e "Non toccare" sul vassoio della batteria e sui componenti ad alta tensione circostanti per garantire una rapida identificazione anche in caso di emergenza.
l Utilizzare una codifica a colori accettata a livello internazionale, come rosso o arancione per contrassegnare le aree ad alta tensione e blu per la corrente continua, per distinguere intuitivamente le diverse caratteristiche elettriche.
l Applicare simboli di sicurezza elettrica standardizzati, come i simboli grafici in IEC 60417, per indicare alta tensione, messa a terra, punti di spegnimento, ecc. per garantire la comprensibilità globale delle informazioni.
l Includere il numero di serie, la data di produzione e le informazioni sul lotto del vassoio della batteria per un facile monitoraggio e gestione del richiamo.
l Selezionare materiali e tecnologie di stampa resistenti all'usura e alla corrosione per garantire che l'etichetta rimanga chiara e leggibile per tutto il ciclo di vita del vassoio della batteria.
B.Segnali di avvertimento
l I pericoli dell'alta tensione sono chiaramente contrassegnati sul vano batteria e nelle aree circostanti per ricordare al personale addetto alla manutenzione di prestare attenzione alla sicurezza elettrica e di rispettare le procedure operative.
l Indicare le distanze operative sicure, in particolare in prossimità di connettori ad alta tensione e posizioni esposte, per ricordare alle persone di mantenere una distanza appropriata.
C.Guida operativa
l Segnare chiaramente i punti di messa a terra del sistema di batterie e del vassoio per garantire la corretta implementazione delle misure di messa a terra.
l Identificare punti di prova sicuri e punti di accesso per la manutenzione, che devono essere progettati per funzionare a bassa tensione o in condizioni di non alimentazione.
l Le istruzioni di base per il funzionamento e la sicurezza possono essere brevemente elencate nelle aree non critiche del vassoio per guidare il corretto processo operativo.
Condivideremo regolarmente aggiornamenti e informazioni su tecniche di progettazione termica e alleggerimento, per la vostra consultazione. Grazie per l'interesse verso Walmate.
I blocchi d'acqua più popolari sono fondamentalmente di tipo microcanale in rame puro. La piastra inferiore in rame è lavorata direttamente con skived e le alette sono integrate con la piastra inferiore per ridurre la resistenza termica. La piastra inferiore e la piastra di copertura sono brasate o diffuse per garantire l'affidabilità della tenuta.
Parte 3: La struttura dei costi principali del blocco dell'acqua elaborato mediante processo di skiving
1- Vantaggi dell'utilizzo del processo di skiving per la produzione di blocchi d'acqua
l Design integrato: il processo di skiving può integrare il pavimento e le alette, il che è utile per ridurre la resistenza termica di contatto e migliorare la conduttività termica. Inoltre, la piastra inferiore integrata e il design delle alette possono anche migliorare la resistenza strutturale.
l Lavorazione ad alta precisione: il processo di skiving può produrre una struttura del dente molto fine e l'altezza del dente, lo spessore del dente e il passo del dente possono essere controllati con precisione, il che rende le alette del dissipatore di calore più dense, l'area di dissipazione del calore più ampia e la dissipazione del calore più efficiente. Allo stesso tempo, può anche soddisfare meglio le esigenze personalizzate di diversi clienti per forma, dimensioni, ecc.
l L'efficienza di produzione è elevata e il processo di skiving può essere prodotto in serie. Rispetto al CNC tradizionale, il processo di skiving può elaborare più pezzi di ingranaggi contemporaneamente, il che migliora notevolmente l'efficienza di produzione.
Figura 1: Base del blocco d'acqua con diverse tecnologie di lavorazione a-Skiving b-CNC c-Forgiatura a freddo
2- Struttura dei costi del blocco di acqua di skiving
l Costi di progettazione e sviluppo: la complessità di progettazione del blocco di acqua di skiving è relativamente elevata, soprattutto quando sono richiesti requisiti di elevate prestazioni di dissipazione del calore, il che richiede una progettazione e un'ottimizzazione complesse del processo.
l Costo del materiale: i materiali utilizzati nel processo di skiving sono principalmente alluminio e lega di rame. La progettazione di una piastra di alluminio e una lega di rame combinate è più comune nella produzione di radiatori e ha un rapporto costi-prestazioni più elevato, quindi la qualità dell'alluminio e del rame influisce direttamente sul costo.
l Costo di lavorazione:
Costo del processo di skiving: il processo di skiving coinvolge attrezzature di lavorazione CNC ad alta precisione, come macchine utensili CNC a tre assi. L'uso di tali attrezzature richiede un elevato costo di investimento e anche i requisiti tecnici per gli operatori sono elevati, il che aumenterà i costi di produzione.
Costo del processo di saldatura: nel processo di produzione di blocchi d'acqua, anche il processo di saldatura è un importante fattore di costo. La brasatura sotto vuoto e la saldatura a diffusione sono due metodi di saldatura comunemente utilizzati. La brasatura può saldare più giunti contemporaneamente, ha un'elevata efficienza di produzione, richiede materiali di brasatura, ha elevati requisiti per le condizioni di processo ed è difficile controllare la qualità; le attrezzature di saldatura a diffusione hanno un grande investimento una tantum e la saldatura a diffusione non richiede riempitivi, ma ha elevati requisiti per la lavorazione superficiale del pezzo.
Costo del trattamento superficiale: i metodi comuni di trattamento superficiale includono anodizzazione, placcatura, ecc. Per i blocchi d'acqua in lega di alluminio, l'anodizzazione può migliorare la durezza superficiale, la resistenza all'usura e la resistenza alla corrosione, aumentando al contempo l'estetica del prodotto; i blocchi d'acqua in rame saranno placcati, come la nichelatura, per prevenire l'ossidazione e la corrosione del rame e aumentare la durata e l'affidabilità del prodotto.
l Altri costi: ispezione e collaudo, imballaggio e trasporto, ecc.
3-Suggerimenti per l'ottimizzazione dei costi
l Ottimizzazione dell'uso dei materiali
Scegli il materiale giusto: ad esempio, il rame ha un'elevata conduttività termica, un'elevata densità unitaria e un prezzo unitario elevato; l'alluminio è leggero, ha un prezzo unitario basso e una conduttività termica leggermente scarsa.
Uso dei materiali: assicurati un uso efficiente dei materiali e riduci gli sprechi di materiale calcolando accuratamente lo spessore e il margine del materiale.
Figura 2: Diagramma schematico del calcolo del consumo di materiale
l Ottimizzazione dei processi di produzione
Semplificare gli stampi: progettare stampi semplici per ridurre la complessità e i costi degli stampi.
Ridurre il tasso di scarto: ridurre il tasso di scarto tramite un controllo preciso del processo e un'ispezione di qualità.
Stampaggio in un unico passaggio: ottimizzare i percorsi di processo, ridurre più fasi di lavorazione e migliorare l'efficienza della produzione.
Condivideremo regolarmente aggiornamenti e informazioni su tecniche di progettazione termica e alleggerimento, per la vostra consultazione. Grazie per l'interesse verso Walmate.
Come componente chiave del sistema di raffreddamento a liquido, la progettazione del water block deve tenere conto di molteplici fattori quali prestazioni di scambio termico, resistenza strutturale, resistenza alla corrosione, resistenza alle perdite e controllo dei costi. Il water block è solitamente progettato con una complessa struttura a fessura per lo scambio termico (ad es., canale di flusso) e la qualità della progettazione del suo canale di flusso interno determina direttamente l'efficienza dello scambio termico dell'intero sistema.
Parte 2: progettazione del blocco dell'acqua, tecnologia di elaborazione e sfide
1-Requisiti di progettazione per blocchi d'acqua in diversi scenari
l High Performance Computing:
I dispositivi di elaborazione ad alte prestazioni (come CPU ad alte prestazioni, GPU, ecc.) generano molto calore durante il funzionamento, quindi il water block deve avere capacità di dissipazione del calore efficienti. Per soddisfare i requisiti di dissipazione del calore ad alta densità di flusso di calore, il water block di solito adotta un design a microcanali ad alta densità per aumentare l'area di scambio termico e migliorare l'efficienza di dissipazione del calore. Inoltre, alcuni design integrano il water block direttamente sulla CPU, eliminando la fase di applicazione del grasso siliconico, che non solo semplifica il processo di assemblaggio, ma migliora anche ulteriormente le prestazioni di dissipazione del calore. In termini di affidabilità, il water block deve avere eccellenti prestazioni di tenuta per prevenire perdite e garantire un funzionamento stabile a lungo termine.
l Raffreddamento della scheda grafica:
Le schede grafiche sono aree che generano molto calore, quindi il waterblock deve avere un design a copertura totale per garantire che tutti i componenti che generano calore sulla scheda grafica possano essere raffreddati in modo efficace. Allo stesso tempo, il raffreddamento della scheda grafica richiede un'elevata portata di refrigerante, quindi la struttura interna del waterblock deve supportare un'elevata portata per rimuovere rapidamente il calore.
l Data Center:
Nei data center, la progettazione strutturale del water block deve soddisfare molteplici requisiti quali efficiente dissipazione del calore, basso rumore, elevata affidabilità, adattabilità ad alta densità di potenza, gestione intelligente e adattabilità ambientale per garantire un funzionamento stabile ed efficiente dissipazione del calore dei data center.
2- Tendenza evolutiva della struttura del blocco d'acqua
La tendenza evolutiva della progettazione strutturale del blocco d'acqua riflette la duplice ricerca di innovazione tecnologica e miglioramento delle prestazioni, che si riflette principalmente nei seguenti aspetti:
l Prestazioni di dissipazione del calore migliorate:
Aumenta l'area di contatto: alcuni design del blocco dell'acqua migliorano le prestazioni di dissipazione del calore aumentando l'area di contatto con l'elemento riscaldante. Ad esempio, un design di base in rame di ampia area può ottenere un buon contatto e conduzione del calore. Ottimizza la struttura interna: ottimizza il canale dell'acqua interno. Un'idea è quella di ottimizzare il flusso del fluido, ad esempio passando da alette ordinarie ad alette di sterzo, presentando un lungo canale di flusso a strisce, promuovendo la separazione dello strato limite del flusso, riducendo lo spessore dello strato limite e migliorando l'efficienza dello scambio termico; un'altra idea è quella di aumentare l'area di capacità termica, ad esempio passando dai tradizionali canali dell'acqua grossolani al design a microcanali, che aumenta significativamente l'area di contatto tra il refrigerante e la piastra di base e migliora l'efficienza di dissipazione del calore. In alcuni design, il refrigerante viene spruzzato sulla piastra di base a microcanali attraverso una piastra guida per aumentare la velocità del flusso locale e la turbolenza, migliorando notevolmente l'efficienza di assorbimento del calore.
l Progettazione integrata e intelligente:
Design integrato: il design integrato integra la pompa dell'acqua, le alette del dissipatore di calore, la base di conduzione del calore e altri componenti insieme per ridurre il numero di punti di connessione e migliorare la stabilità del sistema e l'efficienza di dissipazione del calore.
Integrazione multifunzionale: oltre alle prestazioni di dissipazione del calore, i moderni blocchi d'acqua hanno anche funzioni di visualizzazione e monitoraggio della temperatura.
Design modulare: la struttura della fibbia modulare migliora la praticità e la libertà di organizzazione.
Figura 1: Base del blocco d'acqua con diversi spessori delle alette
l Materiali e finiture ad alte prestazioni:
L'uso di materiali ad alte prestazioni come la base in rame puro, combinati con tecnologie di trattamento superficiale come la nichelatura, migliora la conduttività termica e la resistenza alla corrosione.
3-Tecnologia di elaborazione e sfide
l Le proprietà dei materiali influenzano la lavorazione:
Problemi di durezza e tenacità dei materiali: i radiatori realizzati con materiali diversi, come rame, alluminio e le loro leghe, hanno durezza e tenacità diverse e requisiti diversi per utensili e processi di lavorazione. I materiali con durezza maggiore si usurano più velocemente e richiedono cambi di utensile più frequenti; i materiali con migliore tenacità sono soggetti a deformazioni e sbavature durante il taglio.
La lavorazione di materiali compositi rame-alluminio è complessa: i dissipatori di calore a denti di pala in materiale composito rame-alluminio devono prima essere trasformati in materiali compositi utilizzando la tecnologia di pressatura a stato semi-fuso a colata continua, quindi viene eseguita la lavorazione a denti di pala. Il processo è più complicato e richiede una maggiore precisione per le attrezzature e i processi.
l Elevati requisiti di precisione dimensionale
È difficile garantire la coerenza dell'altezza e dello spessore dei denti: per alcuni dissipatori di calore ad alta densità, l'altezza e lo spessore di ciascun dente devono essere altamente coerenti per garantire le prestazioni e l'uniformità del dissipatore di calore. Se la differenza tra l'altezza e lo spessore dei denti è troppo grande, ciò porterà a un trasferimento di calore non uniforme e influirà sull'effetto di dissipazione del calore. Durante la lavorazione, sono necessarie apparecchiature ad alta precisione e sistemi di controllo automatizzati per garantire che le specifiche di ciascun dente siano coerenti.
È difficile controllare la spaziatura dei denti: quando i denti sul dissipatore di calore sono troppo densi, la loro densità e spaziatura rendono il processo di lavorazione più complicato e l'apparecchiatura di lavorazione deve avere maggiore velocità e precisione per mantenere l'uniformità dei denti. Ad esempio, quando la spaziatura dei denti è troppo piccola, l'utensile è soggetto a interferenze durante il taglio, influendo sulla precisione della lavorazione e sulla qualità della superficie.
l Rigorosi requisiti di qualità della superficie
Problema di sbavature: durante la lavorazione si generano facilmente delle sbavature, che non solo influiscono sull'estetica del radiatore, ma possono anche ostacolare il flusso d'aria e ridurre l'effetto di dissipazione del calore. La generazione di sbavature può essere causata da una bassa precisione di taglio del materiale, dall'usura degli utensili di lavorazione, ecc. e per risolverli è necessario adottare i corrispondenti processi di sbavatura.
Rugosità superficiale: la rugosità superficiale del radiatore influisce sulle sue prestazioni di dissipazione del calore e sui successivi effetti del trattamento superficiale. Una rugosità superficiale eccessiva aumenterà la resistenza al flusso d'aria e ridurrà l'efficienza di dissipazione del calore. È necessario un ulteriore trattamento superficiale per ridurre la rugosità, il che aumenta i costi e i tempi di lavorazione.
l Elevati requisiti di apparecchiature e processi di lavorazione
Precisione e stabilità dell'attrezzatura: la pala degli ingranaggi richiede una macchina pala degli ingranaggi ad alta precisione e la precisione dell'attrezzatura influisce direttamente sulla precisione dimensionale e sulla qualità della superficie dei denti. Allo stesso tempo, l'attrezzatura deve avere una buona stabilità per garantire la coerenza dimensionale durante la lavorazione a lungo termine.
Selezione e usura dell'utensile: utensili adatti sono fondamentali per la qualità della lavorazione. Il materiale, i parametri geometrici, ecc. dell'utensile devono essere selezionati in base alle proprietà del materiale. Durante il processo di lavorazione, l'usura dell'utensile comporterà una maggiore forza di taglio, una minore precisione dimensionale e una maggiore rugosità superficiale e l'utensile deve essere regolato o sostituito in tempo.
Velocità di avanzamento e profondità di taglio: impostazioni irragionevoli della velocità di avanzamento e della profondità di taglio possono facilmente portare a difetti di lavorazione. Se la velocità di avanzamento è troppo elevata e la profondità di taglio è troppo grande, l'utensile verrà sovraccaricato, con conseguente strappo dell'utensile, rimbalzo dell'utensile, caduta dell'utensile, ecc., che influiranno sulla precisione della lavorazione e sulla qualità della superficie.
Figura 2: processo di skiving
l Elevati requisiti di personalizzazione
Diversi scenari applicativi hanno requisiti diversi per dimensioni, forma, altezza dei denti, spessore dei denti, spaziatura dei denti e altri parametri del radiatore, che devono essere personalizzati in base a esigenze specifiche. Ciò richiede che il produttore di lavorazione abbia capacità di adattamento del processo flessibili e una vasta esperienza per soddisfare diverse esigenze di personalizzazione.
Condivideremo regolarmente aggiornamenti e informazioni su tecniche di progettazione termica e alleggerimento, per la vostra consultazione. Grazie per l'interesse verso Walmate.
Con la rapida crescita della potenza di calcolo dell'intelligenza artificiale globale e il continuo aumento del consumo di potenza termica di progettazione (TDP) dei chip, la domanda di raffreddamento dei data center sta affrontando sfide senza precedenti. Allo stesso tempo, le politiche sempre più severe di risparmio energetico e riduzione delle emissioni di carbonio in tutto il mondo hanno ulteriormente promosso l'innovazione della tecnologia di raffreddamento. In questo contesto, le tradizionali soluzioni di raffreddamento ad aria sono gradualmente diventate difficili da soddisfare i doppi requisiti di efficiente dissipazione del calore e risparmio energetico. La tecnologia di raffreddamento a liquido sta rapidamente aumentando grazie alle sue eccellenti prestazioni di dissipazione del calore e ai significativi vantaggi di risparmio energetico, diventando la scelta principale per le soluzioni di raffreddamento dei data center. In quanto apparecchiatura principale per l'elaborazione e l'archiviazione dei dati, le prestazioni e la stabilità del server sono direttamente correlate all'efficienza operativa dell'intero sistema. I componenti principali del server, tra cui scheda madre, CPU, memoria, disco rigido e scheda grafica, genereranno molto calore in caso di funzionamento continuo ad alto carico. Se il calore non può essere dissipato in modo tempestivo ed efficace, ciò influirà seriamente sulle prestazioni e sulla durata del server. A tal fine, sono stati introdotti sistemi avanzati di raffreddamento a liquido nelle soluzioni di raffreddamento dei server e installati direttamente sulle principali fonti di calore, come CPU e schede grafiche, per migliorare significativamente l'efficienza della dissipazione del calore.
Parte 1: Struttura e principio di funzionamento del blocco d'acqua
Uno dei componenti principali del sistema di raffreddamento a liquido è il waterblock, che di solito è fatto di materiali in rame o alluminio con elevata conduttività termica ed è progettato con precisi canali per l'acqua e strutture di dissipazione del calore. Questi waterblock si adattano perfettamente alla superficie di fonti di calore come CPU e GPU e assorbono e trasferiscono rapidamente il calore attraverso l'acqua di raffreddamento che circola al suo interno. Il calore viene quindi trasportato al dissipatore di calore, che viene poi fatto circolare attraverso il sistema di raffreddamento ad acqua e infine dissipato nell'aria circostante.
Figura 1: Tendenze del consumo di potenza termica dei chip dei principali produttori di chip
1- Tipi e caratteristiche comuni dei blocchi d'acqua
l Blocco dell'acqua microcanale
Caratteristiche: Il blocco dell'acqua microcanale adotta un design preciso del canale micro-acqua. La struttura del canale dell'acqua è fine e complessa, il che può aumentare significativamente l'area di contatto tra il refrigerante e i componenti che generano calore, migliorando così notevolmente l'efficienza di dissipazione del calore. Il design del canale micro-acqua può anche produrre un forte effetto di turbolenza durante il flusso del refrigerante, migliorando ulteriormente il coefficiente di trasferimento del calore per convezione e ottenendo un trasferimento di calore efficiente.
Scenari di applicazione: è particolarmente adatto per CPU e GPU con elevata generazione di calore, in particolare nell'elaborazione ad alte prestazioni, nell'overclocking e nei data center, che hanno requisiti di dissipazione del calore estremamente elevati.
l Blocco dell'acqua a flusso grande
Caratteristiche: La struttura interna del water block a grande portata è relativamente semplice, solitamente utilizza una piastra di rame o un design con scanalatura incisa, e il costo di produzione è basso. Il suo vantaggio principale è che si basa sul flusso d'acqua ad alta velocità per rimuovere rapidamente il calore ed è adatto per l'uso con un sistema di raffreddamento ad acqua a grande portata. Sebbene la struttura sia semplice, la sua efficiente capacità di dissipazione del calore lo rende una scelta molto conveniente.
Scenario applicativo: Adatto per scenari con determinati requisiti di efficienza di dissipazione del calore ma budget limitato, come sistemi informatici fai da te di fascia medio-alta o cluster di server di piccole e medie dimensioni.
l Blocco dell'acqua di tipo iniezione
Caratteristiche: Il blocco di raffreddamento ad acqua di tipo jet spruzza il refrigerante da un ugello stretto alla piastra inferiore del microcanale ad alta velocità attraverso la piastra di guida, formando un forte effetto turbolenza e migliorando significativamente l'efficienza di dissipazione del calore. Questo design non solo aumenta l'area di contatto tra il refrigerante e la base, ma ottimizza anche ulteriormente le prestazioni di scambio termico attraverso il flusso ad alta velocità.
Scenari applicativi: Adatto per CPU e GPU ad alte prestazioni, in particolare in requisiti di dissipazione del calore elevata e scenari ad alto flusso, come l'elaborazione di overclocking, la formazione dell'intelligenza artificiale e il rendering grafico.
2-Struttura generale del blocco dell'acqua
Un waterblock è un blocco metallico con canali per l'acqua all'interno, solitamente in rame o alluminio. Non entra in contatto con la CPU, la scheda grafica o altri dispositivi che generano calore. Il suo design strutturale determina direttamente la qualità delle prestazioni di dissipazione del calore. Un tipico waterblock è solitamente costituito dalle seguenti parti chiave:
l La base è solitamente realizzata in materiali ad alta conduttività termica come rame o lega di alluminio, e la superficie è finemente lavorata per garantire uno stretto contatto con i componenti che generano calore. La base è dotata di un complesso design del canale di flusso per aumentare l'area di contatto tra il refrigerante e la base.
l La piastra di copertura, insieme alla base, forma una cavità di tenuta del canale di flusso per proteggere il canale di flusso, la guarnizione e altri componenti all'interno del blocco idrico da polvere, impurità e danni fisici esterni.
l L'ingresso e l'uscita dell'acqua sono le interfacce per l'ingresso e l'uscita del refrigerante dalla testa di raffreddamento ad acqua. Sono generalmente progettati sul lato o sulla parte superiore della testa di raffreddamento ad acqua per garantire che il refrigerante possa fluire dentro e fuori senza problemi. La progettazione della posizione deve considerare il percorso di flusso del fluido per ridurre la resistenza al flusso e aumentare la portata del refrigerante.
l Le clip vengono utilizzate per fissare saldamente la testina di raffreddamento ad acqua alla CPU o ad altri componenti che generano calore, per garantire una base solida e ottenere una conduzione efficiente del calore.
Figura 2: Struttura tipica del blocco d'acqua
3- Ottimizzazione completa delle prestazioni di dissipazione del calore
l Ottimizzazione della progettazione del canale di flusso
Aumentare l'area di contatto del canale di flusso: progettando canali di flusso più stretti e densi, l'area di contatto tra il refrigerante e la base può essere notevolmente aumentata, migliorando così il coefficiente di trasferimento di calore convettivo. Ad esempio, il design del microcanale ha una struttura del canale dell'acqua fine. I parametri di progettazione del blocco dell'acqua del microcanale (come larghezza, altezza e spaziatura del canale) hanno un'influenza decisiva sulla sua efficienza di dissipazione del calore: man mano che la larghezza del canale diminuisce, il coefficiente di trasferimento di calore aumenta in modo significativo, grazie all'effetto di turbolenza migliorato del flusso di refrigerante nel canale stretto, migliorando così l'efficienza di scambio termico; l'altezza maggiore del canale aiuta ad aumentare lo spazio di flusso del refrigerante, migliorando così le prestazioni di trasferimento di calore; la spaziatura più piccola del canale può aumentare l'area di contatto tra il refrigerante e la fonte di calore, migliorando così l'efficienza di dissipazione del calore.
Può anche essere ottimizzato ottimizzando il layout del canale di flusso e riducendo le curve del canale di flusso: un layout ragionevole del canale di flusso può garantire che il refrigerante copra uniformemente la superficie dei componenti che generano calore e ridurre la differenza di temperatura locale. Le curve nel canale di flusso aumenteranno la perdita di carico e la resistenza al flusso interno, riducendo così l'efficienza di raffreddamento. Il numero di curve dovrebbe essere ridotto al minimo nella progettazione. Se non può essere evitato, le curve dovrebbero essere progettate come transizioni fluide per ridurre la caduta di pressione e ottimizzare le prestazioni del flusso.
l Materiali ad alta conduttività termica: la base del waterblock è solitamente realizzata in materiali ad alta conduttività termica come rame puro o lega di alluminio. Questi materiali possono trasferire in modo efficiente il calore dalla fonte di calore al refrigerante, migliorando così le prestazioni complessive di dissipazione del calore.
l Ottimizzazione dei parametri strutturali, come spessore del substrato di base, alette, struttura dello spoiler, ecc. L'aumento dello spessore del substrato porterà a un aumento della temperatura massima, quindi il design deve trovare il miglior equilibrio tra effetto di dissipazione del calore e resistenza strutturale; aumentando l'altezza, lo spessore e la spaziatura delle alette, le prestazioni di dissipazione del calore possono essere migliorate, ma allo stesso tempo aumenterà anche la resistenza al flusso. Trova la migliore combinazione di progettazione delle alette per massimizzare le prestazioni di dissipazione del calore. La forma della colonna dello spoiler può migliorare efficacemente l'effetto di turbolenza e migliorare l'efficienza dello scambio termico.
Condivideremo regolarmente aggiornamenti e informazioni su tecniche di progettazione termica e alleggerimento, per la vostra consultazione. Grazie per l'interesse verso Walmate.
Sulla base della produzione effettiva, questo articolo riassume i problemi più comuni, le cause e i metodi di miglioramento nel processo di saldatura ad attrito per vostro riferimento.
1-Difetti superficiali
(1) Scanalature superficiali
l Descrizione del problema: le scanalature superficiali, note anche come difetti di aratura, solitamente si formano sulla superficie superiore della saldatura, tendono verso il bordo di avanzamento della saldatura e hanno la forma di una scanalatura.
l Causa: il flusso di metallo termoplastico attorno alla saldatura è insufficiente e il metallo plastico della saldatura non riesce a riempire completamente la cavità istantanea lasciata dall'ago di agitazione durante il suo movimento.
l Metodo di miglioramento: aumentare il diametro della spalla, aumentare la pressione e ridurre la velocità di saldatura.
Figura 1: Scanalature
(2)Bave sui bordi
l Descrizione del problema: Sul bordo esterno della saldatura si formano delle sbavature di forma ondulata.
l Causa: Corrispondenza non corretta tra velocità di rotazione e velocità di saldatura, pressione verso il basso eccessiva.
l Metodo di miglioramento: ottimizzare i parametri di saldatura e ridurre la quantità di pressione.
Figura 2: Sbavature sui bordi
(3)Peeling superficiale
l Descrizione del problema: sulla superficie della saldatura si formano delle screpolature o delle filettature sotto forma di pellicola o di filo.
l Causa: una grande quantità di calore generato dall'attrito del metallo si accumula sulla superficie metallica della saldatura, facendo sì che il metallo locale sulla superficie raggiunga uno stato fuso.
l Metodo di miglioramento: ottimizzare i parametri di saldatura, ridurre la velocità di rotazione e aumentare la velocità di saldatura.
Figura 3: Peeling superficiale
(4) Nodulo di saldatura posteriore
l Descrizione del problema: si forma un cordone di saldatura sul lato posteriore della saldatura.
l Causa: Controllo improprio della profondità e della pressione della testa di agitazione durante la saldatura.
l Metodo di miglioramento: ottimizzare le impostazioni di profondità e pressione della testa di miscelazione.
2-Difetti interni
(1) Penetrazione incompleta
l Descrizione del problema: un difetto "simile a una crepa" si verifica quando il fondo della saldatura non è collegato o non è completamente collegato.
l Causa: l'ago di agitazione non è sufficientemente lungo, con conseguente agitazione insufficiente del materiale sul fondo della saldatura.
l Metodo di miglioramento: selezionare la lunghezza appropriata dell'ago di agitazione per garantire che il materiale sullo spessore della saldatura possa essere completamente agitato.
Figura 4: Penetrazione incompleta
(2) Fori
l Descrizione del problema: un difetto "simile a una crepa" si verifica quando il fondo della saldatura non è collegato o non è completamente collegato.
l Causa: Durante il processo di saldatura, a causa di un apporto di calore di attrito insufficiente, una quantità insufficiente di materiale raggiunge lo stato plastificato, con conseguente flusso di materiale insufficiente e chiusura incompleta dell'area di saldatura.
l Metodi di miglioramento: ottimizzare i parametri di saldatura, migliorare la progettazione dell'ago di agitazione e controllare la velocità di saldatura e la velocità di rotazione.
Figura 5: Fori
Condivideremo regolarmente aggiornamenti e informazioni su tecniche di progettazione termica e alleggerimento, per la vostra consultazione. Grazie per l'interesse verso Walmate.
Di recente, l'editore ha notato che molte aziende stanno prestando attenzione e pianificando l'accumulo di energia tramite raffreddamento a liquido a immersione. Dopo un periodo di silenzio, la tecnologia di raffreddamento a liquido a immersione ha nuovamente attirato l'attenzione e sembra stia diventando di nuovo popolare. Credo che anche molti colleghi stiano prestando attenzione a questo sviluppo.
1- Caratteristiche della tecnologia di raffreddamento a liquido ad immersione
Le celle di accumulo di energia si stanno muovendo verso 300+Ah e i sistemi di accumulo di energia si stanno muovendo verso 5MWh+. Più grande è la cella, più calore genera, più difficile è dissipare il calore e più difficile è garantire la coerenza della temperatura. Inoltre, il sistema di accumulo di energia è composto da un gran numero di celle impilate e le condizioni operative sono complesse e mutevoli, il che è più probabile che causi una generazione di calore non uniforme e una distribuzione non uniforme della temperatura. Se i problemi di dissipazione del calore e uniformità della temperatura non vengono risolti correttamente, le prestazioni di carica e scarica della batteria, la capacità e la durata diminuiranno, influenzando le prestazioni dell'intero sistema. Inoltre, la sicurezza è sempre stata la "spada di Damocle" che incombe sull'accumulo di energia delle batterie al litio e il modo più comune per migliorare la sicurezza è quello di muoversi verso le tre dimensioni di sicurezza intrinseca, sicurezza attiva e sicurezza passiva. Il raffreddamento a liquido a immersione consiste nell'immergere la cella della batteria in un liquido isolante, non tossico e dissipatore di calore. Il refrigerante ha una maggiore conduttività termica e capacità termica specifica. Questo metodo di contatto diretto può fornire un'efficienza di trasferimento di calore estremamente elevata, migliorando anche una migliore uniformità della temperatura. Inoltre, oltre a essere un mezzo di controllo della temperatura, il refrigerante può anche essere utilizzato come fluido antincendio per sistemi di accumulo di energia, combinando il controllo della temperatura e la protezione antincendio, che è anche una caratteristica significativa della tecnologia di raffreddamento a liquido a immersione. Il raffreddamento a liquido a immersione avrà senza dubbio più vantaggi nel contesto di un settore che richiede prestazioni di dissipazione del calore più elevate e una maggiore sicurezza.
Figura 1: Batteria di accumulo di energia raffreddata a liquido immersa Scatola di imballaggio
2- Soluzione di sistema di accumulo di energia con raffreddamento a liquido immerso
Come ramo della tecnologia di raffreddamento a liquido, la tecnologia di raffreddamento a liquido a immersione non è la prima ad essere utilizzata nel settore dell'accumulo di energia. Inizialmente è stata utilizzata nel campo dell'informatica ad alte prestazioni e in seguito si è gradualmente estesa ai data center, all'intelligenza artificiale, alle criptovalute, ecc.
L'intenzione originale della progettazione del sistema di accumulo di energia con raffreddamento a liquido a immersione è quella di risolvere le carenze del raffreddamento ad aria tradizionale e del raffreddamento a liquido indiretto nell'efficienza di raffreddamento e nel controllo della differenza di temperatura della batteria. La messa in servizio ufficiale del progetto Southern Power Grid Meizhou Baohu segna l'applicazione di successo del raffreddamento a liquido a immersione, una tecnologia all'avanguardia, nel campo della nuova ingegneria dell'accumulo di energia.
l Metodo di raffreddamento e metodo di circolazione del refrigerante
I metodi di raffreddamento sono divisi in monofase e a cambiamento di fase. Viene utilizzato il raffreddamento a liquido a immersione monofase, che include principalmente olio minerale, olio siliconico, estere naturale, ecc. Altri schemi utilizzano il raffreddamento a liquido a immersione bifase, rappresentato principalmente da idrofluoroetere, e utilizzano il calore latente a cambiamento di fase per dissipare il calore e migliorare l'efficienza di dissipazione del calore. Secondo statistiche incomplete, lo schema di "raffreddamento a immersione monofase" è il più comune tra i sistemi di accumulo di energia a raffreddamento a liquido a immersione attualmente rilasciati. In base alla differenza nella modalità di circolazione del refrigerante, ci sono tre percorsi tecnici nel raffreddamento a liquido a immersione monofase: convezione naturale, azionamento della pompa e raffreddamento a liquido a piastra fredda accoppiato a immersione. La convezione naturale utilizza le caratteristiche di espansione del volume del liquido e riduzione della densità dopo il riscaldamento per ottenere il galleggiamento del refrigerante caldo e l'affondamento dopo il raffreddamento, completando così la dissipazione del calore della circolazione; il nucleo del sistema di azionamento della pompa è che l'unità di raffreddamento a liquido aziona il refrigerante per circolare tra la tubazione di raffreddamento a liquido e la scatola di immersione della batteria per completare l'intero processo di dissipazione del calore della circolazione; nello schema di raffreddamento a liquido con piastra accoppiata a immersione, la batteria è immersa nel fluido dielettrico e la piastra fredda a contatto con il fluido dielettrico viene utilizzata per dissipare il calore, evitando l'uso di complessi circuiti secondari per raffreddare il fluido dielettrico.
l Forma del prodotto e soluzione di integrazione
L'iterazione della soluzione di integrazione del sistema di accumulo di energia raffreddato a liquido a immersione è un processo dal tutto alla parte e poi ai dettagli. Ogni passaggio è ottimizzato e migliorato sulla base della fase precedente per ottenere prestazioni e sicurezza più elevate. Dal livello cabina al livello pacco, la tecnologia di integrazione del sistema presenta le caratteristiche della personalizzazione della scena. La diversificazione degli scenari di accumulo di energia rende diversa la domanda di sistemi di accumulo di energia. Un singolo prodotto non può soddisfare la domanda del mercato. Il design modulare consente di ottimizzare ed espandere i prodotti di accumulo di energia in base alla scala e alla domanda di potenza del progetto, consentendo di adattare e distribuire rapidamente le soluzioni di accumulo di energia in base a diversi scenari ed esigenze applicative.
3-Sfide e scenari di implementazione nel processo di industrializzazione
I sistemi di accumulo di energia raffreddati a liquido immersi devono affrontare numerose sfide durante il processo di commercializzazione, tra cui la fattibilità economica, la complessità tecnica, l'accettazione del mercato e la maturità della filiera industriale.
l Complessità tecnica: rispetto ai sistemi di raffreddamento a liquido con piastra fredda, i sistemi di raffreddamento a liquido a immersione sono più complessi da progettare e implementare.
l Maturità della filiera industriale: la filiera industriale della tecnologia di raffreddamento a liquido a immersione non è ancora completamente matura, il che ne limita l'applicazione in una gamma più ampia di campi. La maturità della filiera industriale influisce direttamente sulla promozione e sulla commercializzazione della tecnologia.
l Sfide economiche: il settore dell'accumulo di energia è ancora nelle prime fasi di sviluppo commerciale e la mancanza di redditività rende difficile che i percorsi tecnologici ad alto costo siano favoriti dal mercato. Molte aziende competono con prezzi bassi per ordini temporanei, il che limita la penetrazione del raffreddamento a liquido a immersione.
Attualmente, il mercato principale dell'industria dell'accumulo di energia è ancora dominato dal raffreddamento ad aria e dal raffreddamento a liquido a piastra fredda, e il raffreddamento a liquido a immersione non è ancora stato pienamente accettato dal mercato. Sebbene la penetrazione di mercato e l'accettazione della tecnologia di raffreddamento a liquido a immersione non siano elevate, potrebbe non mostrare un potenziale considerevole in alcuni scenari speciali, come:
l Industria chimica pericolosa: le aziende chimiche pericolose hanno controlli di sicurezza estremamente rigorosi sulle apparecchiature di accumulo di energia, perché la maggior parte delle sostanze chimiche che producono e immagazzinano sono altamente infiammabili, esplosive, tossiche o corrosive. Una volta che si verifica un incidente, non solo causerà gravi perdite all'azienda stessa, ma potrebbe anche causare inquinamento ambientale e danni alle comunità circostanti.
l Stazioni base e data center: le stazioni base e i data center hanno una bassa tolleranza alla fuga termica. I sistemi di accumulo di energia dei data center devono avere batterie con prestazioni stabili e non sono soggetti a fuga termica per garantire la sicurezza del sistema. I requisiti per la qualità dell'alimentazione sono elevati e il sistema di accumulo di energia deve avere una capacità di risposta rapida. In caso di emergenza, come un guasto della rete o un'interruzione di corrente, il sistema di accumulo di energia deve essere in grado di passare direttamente alla modalità di scarica per garantire la continuità e la stabilità dell'alimentazione.
l Stazione di ricarica rapida: quando si carica e si scarica a velocità elevate, la batteria genera una grande quantità di calore in un breve periodo di tempo, il che causerà una temperatura della batteria troppo elevata e irregolare, rappresentando una minaccia per le prestazioni, la durata e la sicurezza della batteria. Ciò significa che la gestione termica della batteria diventa particolarmente importante in scenari di carica e scarica ad alta velocità.
Condivideremo regolarmente aggiornamenti e informazioni su tecniche di progettazione termica e alleggerimento, per la vostra consultazione. Grazie per l'interesse verso Walmate.
La tenuta stagna del pacco batteria è un indicatore cruciale nei veicoli elettrici e nei sistemi di accumulo di energia. Il test di tenuta stagna del pacco batteria viene eseguito principalmente sul guscio del pacco batteria, sull'interfaccia, sul connettore, sul gruppo di raffreddamento, ecc. per garantire che l'interno del pacco batteria non sia contaminato o invaso da impurità come polvere e umidità dall'ambiente esterno e che il gruppo di raffreddamento non perda, in modo da garantire che il pacco batteria mantenga prestazioni e durata normali e non causi incidenti di sicurezza come cortocircuiti o esplosioni.
1- Formulazione standard del test di livello di protezione e tenuta stagna del pacco batteria
International Protection Making (IEC60529), noto anche come livello di protezione da corpi estranei o codice IP. Il sistema di livello di protezione IP (Ingress Protection) è uno standard stabilito dalla Commissione elettrotecnica internazionale (IEC) per classificare il livello di protezione degli alloggiamenti delle apparecchiature elettriche contro l'intrusione di corpi estranei e l'intrusione di acqua. Il livello di tenuta stagna della custodia del pacco batteria è solitamente richiesto per raggiungere IP67 o IP68, il che significa che la custodia del pacco batteria deve essere completamente protetta dall'ingresso di polvere (livello antipolvere 6) e può essere immersa in acqua a una certa pressione per un periodo di tempo senza infiltrazioni d'acqua a un livello dannoso (livello impermeabile 7). Requisiti più rigorosi prevedono che la batteria possa essere immersa in acqua profonda 1 m per 60 minuti senza infiltrazioni d'acqua (livello impermeabile 8). Il livello di protezione IP è solitamente composto da due cifre. Maggiore è il numero, maggiore è il livello di protezione, come mostrato nella Figura 1:
Figura 1: Descrizione del livello di protezione IP
Per garantire che il pacco batteria soddisfi i requisiti IP67 e IP68, il pacco batteria deve essere immerso in acqua. Questo metodo richiede molto tempo, è distruttivo per il pacco batteria e presenta alcuni rischi per la sicurezza. Non è adatto come test offline per le batterie di alimentazione. Pertanto, è diventata una pratica comune nel settore utilizzare test di tenuta stagna per garantire che il pacco batteria soddisfi i requisiti IP67 e IP68. La formulazione di standard di test di tenuta stagna deve considerare la relazione tra valore di caduta di pressione e tasso di perdita, nonché la relazione tra apertura e perdita d'acqua. La formulazione di standard di test di tenuta stagna comporta una serie di passaggi dagli estremi teorici alla verifica sperimentale per ottenere la conversione dal livello IP agli standard di test di tenuta stagna. Ad esempio, prendendo IP68 come esempio:
Figura 2: Fasi per la formulazione di standard di prova di tenuta all'aria
2- Selezione dei metodi di prova di tenuta all'aria e analisi delle difficoltà di prova
La progettazione e la qualità di fabbricazione del pacco batteria sono fattori chiave che influenzano la tenuta all'aria, tra cui la tenacità e la resistenza del coperchio della scatola della batteria, la sigillatura del guscio del pacco batteria, interfacce e connettori, prese d'aria antideflagranti e la sigillatura del connettore elettrico stesso. Inoltre, ci saranno alcuni problemi che influenzano la tenuta all'aria durante l'uso, come problemi di espansione e contrazione termica, invecchiamento del materiale, vibrazioni e urti. Nella produzione e fabbricazione dei gusci del pacco batteria, prestiamo maggiore attenzione alla scarsa tenuta all'aria causata da problemi come punti di saldatura e qualità dei giunti, come punti di saldatura irregolari, saldature deboli o screpolate, fessure d'aria e scarsa tenuta delle connessioni dei giunti. Il test di tenuta all'aria del pacco batteria è principalmente suddiviso nel test di tenuta all'aria del guscio superiore, del guscio inferiore e delle parti di assemblaggio. Il test di tenuta all'aria dei gusci superiore e inferiore deve soddisfare i requisiti di perdita di tenuta all'aria dopo l'assemblaggio. Quando si seleziona il metodo di prova di tenuta all'aria per il pacco batteria, le caratteristiche del pacco batteria, i requisiti di accuratezza del test, l'efficienza di produzione e il costo sono generalmente considerati in modo completo.
I test di tenuta stagna del pacco batteria in ingegneria sono generalmente divisi in test di tenuta stagna di processo e test di tenuta stagna di spedizione. Inoltre, i test di tenuta stagna dei gusci superiore e inferiore devono soddisfare i requisiti di tenuta stagna dopo l'assemblaggio, il che impone requisiti più severi sugli standard di prova. Per garantire che la tenuta stagna soddisfi i requisiti, le seguenti difficoltà devono essere superate nel funzionamento effettivo:
l Stabilità della struttura del prodotto: qualità delle saldature, tra cui saldature a spina, saldature a rubinetto, saldature a trave, saldature della piastra inferiore del telaio, saldature della piastra di copertura anteriore e posteriore del telaio, ecc. I problemi di perdite di saldatura sono concentrati principalmente nei punti di inizio e fine dell'arco e nei difetti causati da bruciature passanti; crepe causate da sollecitazioni di deformazione della saldatura, come la saldatura della parete laterale della cavità della piastra inferiore, la stratificazione del materiale della cavità della piastra inferiore e l'incapacità di resistere alle sollecitazioni di deformazione della saldatura.
l Adattabilità e stabilità di dispositivi di fissaggio ermetici: il design dei dispositivi di fissaggio deve corrispondere fedelmente alla forma e alle dimensioni dei componenti testati, assicurando che i componenti possano essere fissati saldamente ai dispositivi di fissaggio durante il processo di collaudo, riducendo così gli errori di collaudo causati da spostamenti di posizione o vibrazioni. Tuttavia, in pratica, le dimensioni e la forma dei pacchi batteria variano in modo significativo, rendendo necessaria la progettazione e la fabbricazione di più dispositivi di collaudo diversi, il che aumenta i costi e la complessità operativa. Progettare un dispositivo di fissaggio universale complicherebbe ulteriormente il processo di progettazione.
l Ripetibilità dei risultati del test di tenuta all'aria: fattori quali la pressione dell'aria, la temperatura e la secchezza del pezzo/dispositivo di prova influenzeranno i risultati del test di tenuta all'aria.
l Nei pezzi con numerose piccole crepe non penetranti, a causa dell'influenza di fattori quali la precisione dell'apparecchiatura di rilevamento e i parametri di rilevamento, la fonte della perdita potrebbe non essere individuata, con conseguente mancato rilevamento.
Figura 3: Attrezzatura per test di tenuta all'aria
3-Combinazione di soluzioni di rilevamento della tenuta all'aria del pacco batteria comunemente utilizzate in ingegneria
Il test di tenuta all'aria del processo di guscio del pacco batteria generalmente include il test di tenuta all'aria e il test di immersione in acqua. Nel test di tenuta all'aria, il coperchio superiore della scatola della batteria viene sigillato, lasciando solo una porta di collegamento come ingresso dell'aria. La tenuta all'aria del pacco batteria viene valutata controllando la pressione dell'aria e osservando se vi sono perdite d'aria. Il test di immersione in acqua consiste nell'immergere completamente l'intera scatola della batteria in acqua e valutare la sua tenuta all'aria controllando se vi è acqua nella scatola.
Il rilevamento delle perdite di elio è una tecnologia che utilizza l'elio come gas tracciante per rilevare le perdite rilevando la concentrazione di elio nel punto di perdita. Quando l'elio entra all'interno o all'esterno del dispositivo in fase di test dove potrebbe esserci una perdita, se c'è una perdita, l'elio entrerà o uscirà rapidamente dal sistema attraverso la perdita e verrà rilevato dallo spettrometro di massa. Il metodo di rilevamento delle perdite di elio ha un'elevata efficienza di rilevamento, specialmente nel rilevamento di piccole perdite.
Figura 4: Confronto dei metodi di rilevamento delle perdite
Nella produzione effettiva, più metodi di rilevamento vengono solitamente combinati per migliorare l'efficienza e l'accuratezza del rilevamento. Ad esempio, il metodo di rilevamento delle perdite di elio è adatto per il rilevamento di piccole perdite e ad alta precisione, mentre il metodo di pressione differenziale ha le caratteristiche di alta precisione e risposta rapida. Inoltre, sebbene il tradizionale metodo di rilevamento dell'acqua abbia una bassa accuratezza di rilevamento, è intuitivo e poco costoso, ed è un modo conveniente per localizzare le perdite.
Condivideremo regolarmente aggiornamenti e informazioni su tecniche di progettazione termica e alleggerimento, per la vostra consultazione. Grazie per l'interesse verso Walmate.
Il potenziale guasto della tenuta stagna del gruppo di raffreddamento a liquido dell'accumulo di energia coinvolge molteplici aspetti, quali: perdite, corrosione e deposizione, condensa e altre modalità di guasto.
1- Interconnessione e composizione dei fluidi
Nel sistema di raffreddamento a liquido con accumulo di energia, l'interconnessione del fluido è responsabile del trasferimento del refrigerante tra i vari componenti. Attraverso un'efficace interconnessione del fluido, il refrigerante è garantito per circolare in modo efficiente nel sistema, rimuovendo così il calore in eccesso generato durante il processo di carica e scarica della batteria.
Un sistema ben sigillato può prevenire efficacemente la perdita di refrigerante. La perdita non solo porterà alla perdita di refrigerante e richiederà frequenti rifornimenti, ma influenzerà anche le prestazioni di dissipazione del calore e la stabilità del sistema. Nell'accumulo di energia, la perdita di refrigerante può anche causare un cortocircuito della batteria, causando problemi di sicurezza.
2-Progettazione a tenuta stagna del sistema di interconnessione dei fluidi
La progettazione a tenuta stagna del sistema di interconnessione dei fluidi è l'elemento chiave per garantire che il sistema mantenga la tenuta e impedisca perdite di fluido in diverse condizioni operative.
Figura 1: Tipica distribuzione del sistema di raffreddamento a liquido per l'accumulo di energia
(1) Analizzare le possibili fonti di perdite e i punti di rischio nel sistema:
l Proprietà autosigillante dell'assemblaggio di raffreddamento a liquido. Ad esempio, nella progettazione integrata del sistema di canali di raffreddamento a liquido e del Pack box, i componenti sono collegati tramite saldatura. Difetti di qualità della saldatura, saldature scadenti, pori, crepe, ecc. possono tutti portare a problemi di infiltrazione di liquido.
l La progettazione strutturale è irragionevole. Ad esempio, i fori di posizionamento o i fori filettati della scatola di raffreddamento a liquido sono troppo vicini al canale di flusso e le parti saldate male possono facilmente trasformarsi in canali per infiltrazioni di liquido.
l Parti di collegamento: i collegamenti dei tubi, le valvole e i giunti del sistema di raffreddamento a liquido sono punti di perdita comuni. Se la struttura di collegamento non è progettata correttamente o il processo di fabbricazione non è sofisticato, ci sono piccoli difetti all'interno dei giunti e il refrigerante potrebbe anche fuoriuscire da questi difetti.
l Perdite causate da installazione non corretta, invecchiamento o danneggiamento del materiale, ecc.
(2) Progettazione della struttura di tenuta:
l Il PACK raffreddato a liquido utilizza un metodo di raffreddamento a piastra fredda separata a secco e a umido. In normali condizioni di lavoro, le celle della batteria non hanno alcun contatto con il refrigerante, il che può garantire il normale funzionamento delle celle della batteria. Una soluzione per il raffreddatore a liquido per l'accumulo di energia è quella di formarlo tramite un processo di estrusione, integrare il canale di flusso direttamente sulla piastra fredda e quindi utilizzare la lavorazione meccanica per aprire il percorso di circolazione del raffreddamento. In questo processo, la scelta del giusto processo di saldatura è un passaggio importante per garantire la tenuta. Per i dettagli, fare riferimento a "Progettazione del processo di saldatura per la scatola inferiore per l'accumulo di energia".
l Le condotte di raffreddamento a liquido sono utilizzate principalmente per connessioni di tubi morbidi (duri) di transizione tra fonti di raffreddamento a liquido e apparecchiature, tra apparecchiature e tra apparecchiature e condotte. I principali metodi di connessione sono:
Collegamento rapido: uno dei metodi di collegamento per i sistemi di raffreddamento a liquido con accumulo di energia è l'utilizzo del collegamento rapido VDA o CQC.
Collegamento filettato: entrambe le estremità della struttura di collegamento sono collegate in modo scorrevole ai tubi e il collegamento filettato tra l'anello filettato interno e il manicotto filettato aumenta la solidità del collegamento.
Collegamento di tubo di limitazione e dado: un tubo di collegamento è bloccato a un'estremità del tubo e i tubi di limitazione sono installati in modo fisso su entrambi i lati del tubo di collegamento. Rondelle di gomma e anelli convessi sono installati in modo fisso all'interno dei tubi di limitazione e una scanalatura per l'anello di limitazione è aperta sulla superficie della testa del tubo di collegamento. Un dado è collegato in modo rotante alla parte superiore del tubo di limitazione ed è collegato in modo rotante al tubo di limitazione tramite filettature.
Collegamento dell'anello di tenuta: un anello di tenuta è fissato alla parete interna del manicotto filettato mediante una colla forte, e la parete interna dell'anello di tenuta è collegata in modo mobile alla superficie esterna del tubo per evitare perdite durante l'uso.
(3) La piastra di raffreddamento a liquido PACK, l'interfaccia della cabina, la tubazione della cabina, ecc. sono tutte progettate con protezione dalla corrosione a lungo termine in condizioni comuni di refrigerante, temperatura e portata per garantire un funzionamento a lungo termine senza corrosione. Effetto delle condizioni operative sulla tenuta dei liquidi:
l Temperatura. Influenza della temperatura elevata: all'aumentare della temperatura, la viscosità del liquido generalmente diminuisce, il che può causare una diminuzione delle prestazioni di tenuta del liquido, influenzando così la tenuta del liquido. Ad esempio, alcuni materiali di tenuta possono deformarsi o deteriorarsi ad alte temperature, causando perdite. Influenza della bassa temperatura: in un ambiente a bassa temperatura, il liquido può diventare viscoso, aumentando la difficoltà di flusso, ma può anche migliorare le prestazioni del materiale di tenuta, migliorando così la tenuta del liquido in una certa misura.
l Pressione. Ambiente ad alta pressione: ad alta pressione, la densità e la viscosità del liquido possono aumentare, migliorando così le prestazioni di tenuta del liquido. Tuttavia, una pressione eccessiva può anche danneggiare il materiale di tenuta e causare perdite. Ambiente a bassa pressione: a bassa pressione, le prestazioni di tenuta del liquido possono essere relativamente deboli, soprattutto se il materiale di tenuta stesso è difettoso o invecchiato, è più probabile che si verifichino perdite.
l Portata. Portata elevata: quando il liquido scorre ad alta velocità, può produrre una grande forza d'impatto sulla superficie di tenuta, causando usura o deformazione del materiale di tenuta, influenzando così la tenuta del liquido. Portata bassa: a una portata bassa, le prestazioni di tenuta del liquido sono relativamente buone, ma questo può anche mascherare alcuni potenziali problemi di tenuta come piccoli difetti del materiale.
3-Problemi di corrosione e deposizione
l L'impatto del blocco sulla tenuta all'aria:
Particelle, sedimenti o crescita microbica nel refrigerante possono causare ostruzioni all'interno del tubo, compromettendo il flusso del refrigerante e riducendo così l'efficienza del raffreddamento.
Sporcizia e incrostazioni: i minerali nel refrigerante possono formare depositi sulla parete interna del tubo dopo un funzionamento prolungato, il che è chiamato "incrostazione". Lo sporco può anche formarsi a causa della precipitazione di particelle solide, cristallizzazione, corrosione o attività microbica. Questa sporcizia ostruirà tubi e piastre fredde, aumenterà la resistenza al flusso e ridurrà l'efficienza del trasferimento di calore.
Problema di schiuma: potrebbe generarsi schiuma nel sistema di raffreddamento a liquido. La schiuma aderirà alla superficie della piastra fredda, con conseguente diminuzione dell'effetto di trasferimento del calore e potrebbe aumentare la resistenza nel funzionamento del sistema, causare corrosione da cavitazione alla pompa, ecc. e danneggiare l'apparecchiatura.
l L'influenza delle correnti parassite sulla tenuta all'aria:
Quando un fluido scorre in un tubo o in uno spazio, i cambiamenti di velocità possono causare la formazione di vortici, specialmente quando il fluido passa attraverso parti strette o ostacoli, è più probabile che si formino vortici. Anche la viscosità e la densità del fluido influenzano la generazione di vortici. I fluidi con viscosità più elevata hanno maggiori probabilità di formare vortici, mentre i fluidi con densità più elevata possono indebolire la formazione di vortici.
Percorsi di perdita: le correnti parassite formano vortici sulle superfici di contatto, che possono creare piccoli percorsi di perdita in fessure o superfici irregolari, con conseguente perdita di gas o liquido.
Usura superficiale: il flusso vorticoso può causare l'usura delle superfici di contatto, specialmente in condizioni di flusso ad alta velocità. Questa usura può ridurre ulteriormente la tenuta all'aria perché le superfici usurate hanno maggiori probabilità di formare nuovi canali di perdita.
Effetti termici: il flusso di correnti parassite genera calore, che può causare la deformazione o l'espansione termica del materiale della superficie di contatto, compromettendo così la tenuta stagna, soprattutto nei sistemi con grandi variazioni di temperatura.
4-Problema di condensa
In determinate condizioni, nelle linee di raffreddamento del liquido potrebbe formarsi della condensa, che potrebbe danneggiare l'apparecchiatura o ridurne l'efficienza. Guasto dell'isolamento: se il materiale isolante del tubo è danneggiato o invecchiato, il calore verrà perso e l'effetto di raffreddamento sarà compromesso. Soprattutto in ambienti a bassa temperatura, il guasto dell'isolamento può causare la formazione di brina o ghiaccio sulla superficie del tubo. Crepe dovute al gelo: in ambienti freddi, se non vengono prese le misure antigelo appropriate, il refrigerante nei tubi potrebbe congelare e causare la rottura dei tubi.
Soluzioni
l Misure di sigillatura: assicurarsi che l'ingresso e l'uscita della tubazione di raffreddamento a liquido siano completamente bloccati per impedire all'aria umida esterna di entrare nel vano batteria.
l Apparecchiatura di deumidificazione: installare un condizionatore d'aria con funzione di deumidificazione oppure utilizzare la funzione di deumidificazione per mantenere l'umidità nel vano batteria entro un intervallo appropriato.
l Controllo della temperatura: installando sistemi di aria condizionata o ventilazione, è possibile controllare la temperatura e l'umidità dell'ambiente in cui si trova l'armadio di accumulo energetico. Ad esempio, la temperatura può essere mantenuta a 20-25 gradi Celsius e l'umidità relativa può essere controllata al 40%-60%.
l Misure di isolamento: semplice isolamento dei rack delle batterie vuoti per impedire all'umidità di penetrare nel vano contenente il gruppo batterie.
Condivideremo regolarmente aggiornamenti e informazioni su tecniche di progettazione termica e alleggerimento, per la vostra consultazione. Grazie per l'interesse verso Walmate.
Il design completamente sigillato del pacco di accumulo di energia è la chiave per garantirne la sicurezza e il funzionamento stabile a lungo termine. La sigillatura è essenzialmente l'uso di un dispositivo per chiudere (sigillare) uno spazio o rendere un giunto a prova di perdite. Il design completamente sigillato può prevenire efficacemente perdite di liquidi e gas all'interno della cella della batteria, il che è fondamentale per garantire il funzionamento sicuro e stabile del sistema di accumulo di energia. Pertanto, durante la progettazione, devono essere prese in considerazione sia la tenuta all'aria che la sigillatura del mezzo liquido.
Nel funzionamento effettivo, la progettazione della tenuta del pacco di accumulo di energia deve considerare in modo completo molteplici fattori quali materiali, processi, apparecchiature di collaudo, condizioni ambientali e processi di produzione per garantire che le sue prestazioni di tenuta possano soddisfare gli standard previsti. Questo articolo spiega la pratica applicativa e i punti chiave della progettazione della tenuta del pacco di accumulo di energia nell'ingegneria effettiva dagli aspetti di tenuta all'aria della scatola del pacco, tenuta al liquido del ciclo di raffreddamento a liquido e mezzo di raffreddamento a liquido.
Articolo precedente: Progettazione della tenuta stagna della scatola del pacco di accumulo di energia
Il design della tenuta aiuta a mantenere stabili la temperatura e la pressione all'interno del pacco di accumulo di energia, il che svolge un ruolo chiave nel normale funzionamento e nelle prestazioni della batteria; e il design della tenuta può ridurre l'impatto dell'ambiente esterno sulla batteria interna, come umidità, polvere e altri inquinanti, ecc., migliorando così l'affidabilità e la durata del sistema. Inoltre, l'uso di materiali e strutture di tenuta appropriati può migliorare efficacemente la resistenza all'usura e all'invecchiamento delle guarnizioni, aumentare la durata dell'intero sistema di accumulo di energia e ridurre i costi di manutenzione.
L'idea generale della progettazione ermetica è quella di analizzare la struttura della scatola per individuare le aree chiave in cui potrebbero verificarsi perdite e quindi adottare misure mirate in base alle prestazioni specifiche e ai requisiti funzionali delle diverse aree.
1-Analisi della struttura della scatola
La scatola non è solo il supporto fisico dei moduli batteria e dei componenti elettrici, ma anche un'importante garanzia per il funzionamento sicuro e affidabile dell'intero sistema di accumulo di energia. È lo "scheletro" del pacco di accumulo di energia, che è generalmente composto da un coperchio superiore, una scatola inferiore, componenti di supporto e una guarnizione Parti e bulloni, ecc.
Figura 1: Diagramma schematico della scatola del pacco di accumulo di energia e aree chiave su cui concentrarsi nella progettazione della sigillatura (ad esempio, contrassegnate con frecce rosse)
Come mostrato nella figura sopra, scopri dove potrebbero verificarsi potenziali perdite:
l Punti di collegamento di più componenti, quali: l'interfaccia di assemblaggio tra il coperchio superiore e la scatola inferiore, l'interfaccia di installazione tra i connettori ad alta e bassa tensione e la scatola, l'interfaccia di installazione tra i componenti esposti e la scatola della batteria, ecc.
l Se per il collegamento vengono utilizzati bulloni, potrebbe esserci anche il rischio di perdite nel punto di installazione e fissaggio, come l'interfaccia elettrica e l'interfaccia di installazione del pannello frontale della scatola.
l Per garantire la tenuta e la protezione della scatola, non devono esserci fori o fessure nel coperchio superiore e nel corpo inferiore della scatola.
Figura 2: Scatola inferiore di raffreddamento a liquido a immersione (telaio in lamiera + piastra inferiore di raffreddamento a liquido in alluminio)
2- Progettazione della tenuta dell'interfaccia di installazione tra il coperchio superiore e la scatola inferiore
La copertura superiore può essere generalmente divisa in due tipi: tipo piatto e tipo di forma speciale. Anche le loro caratteristiche strutturali sono diverse. Ad esempio, materiale composito SMC, alluminio, indipendentemente dal materiale, al fine di ridurre la complessità della struttura autosigillante, la copertura superiore del guscio della batteria La copertura è solitamente di design monoblocco. Inoltre, i requisiti di apertura della copertura superiore devono anche soddisfare i requisiti dell'interfaccia e devono essere indipendenti dall'interfaccia di tenuta per ridurre l'impatto sulla tenuta del pacco batteria. Il design della guarnizione della copertura superiore generalmente segue i seguenti principi:
l La progettazione di parti integrate è stata adottata per evitare la progettazione di parti separate, garantendo così la stabilità delle prestazioni "autosigillanti" del coperchio superiore.
l I fori di posizionamento e le caratteristiche di posizionamento sono progettati sul bordo del coperchio superiore (all'esterno dell'interfaccia di tenuta tra il coperchio superiore e il vassoio inferiore).
l L'interfaccia di tenuta tra il coperchio superiore e il corpo inferiore della scatola richiede una superficie di corrispondenza che soddisfi i requisiti di tenuta "uniforme" e "continua".
Attualmente, le soluzioni principali per la scatola inferiore del pacco di accumulo di energia sono: scatola in lamiera + piastra di raffreddamento a liquido, scatola pressofusa + piastra di raffreddamento a liquido, scatola integrata nel profilo, scatola integrata pressofusa, ecc. Tra queste, la scatola integrata nel profilo e altre soluzioni Al contrario, presenta i vantaggi di una buona capacità di carico del canale di flusso e di un basso costo di apertura dello stampo, ed è ampiamente utilizzata. La scelta del processo di saldatura ha una grande influenza sulle prestazioni di tenuta. Per saldature di materiali e spessori diversi, la scelta di un metodo di saldatura adatto può migliorare efficacemente la qualità della saldatura per garantire la resistenza complessiva e le prestazioni di tenuta del sistema.
Inoltre, la progettazione della tenuta della scatola inferiore deve seguire i seguenti principi di tenuta:
l Per la costruzione del telaio vengono utilizzati profili a sezione chiusa e nei giunti si impiega la tecnologia di collegamento lineare autosigillante, come la tecnologia di saldatura CMT.
l I vassoi per batterie realizzati con profili in alluminio devono essere progettati con uno o più strati continui di colloide sigillante.
l Nel caso di una piastra di raffreddamento a liquido integrata nella scatola inferiore, è necessario prendere in considerazione l'impiego di guarnizioni colloidali o tecnologie di collegamento lineare autosigillanti, come la tecnologia di saldatura a frizione e agitazione FSW.
l L'interfaccia di tenuta tra il coperchio superiore e il corpo inferiore della scatola necessita della superficie corrispondente per soddisfare i requisiti di tenuta "uniforme" e "continua". Se necessario, l'interfaccia di tenuta deve essere lavorata e lucidata.
Figura 3: Forme di tenuta comuni tra il coperchio superiore e la scatola inferiore
Di solito, il coperchio superiore e la scatola inferiore del Pack box di accumulo di energia adottano una flangia piegata e un design con guarnizione di tenuta, come mostrato nella Figura 2. Il coperchio superiore, il corpo della scatola inferiore e la guarnizione di tenuta sono completamente compattati e accoppiati tramite bulloni di fissaggio per garantire che il Pack box soddisfi i requisiti pertinenti di IP67.
3- Progettazione della tenuta delle interfacce elettriche e di comunicazione e dell'interfaccia di installazione del pannello frontale della scatola inferiore
Il pannello frontale della scatola (come mostrato nella Figura 3) è dotato di fori sul profilo estruso per l'installazione di interfacce elettriche e di comunicazione per realizzare funzioni quali la trasmissione di corrente, l'interazione delle comunicazioni e il controllo di sicurezza.
Figura 4: Interfaccia di installazione elettrica, di comunicazione e del pannello frontale del mobile inferiore
La tenuta all'aria dell'interfaccia di installazione tra la scatola e le interfacce elettriche, di comunicazione e di altro tipo deve seguire i seguenti principi:
l La forma dell'interfaccia è progettata in modo aerodinamico per ridurre la possibilità di accumulo e permeazione di gas e liquidi nell'interfaccia.
l L'allineamento preciso evita spazi vuoti causati dal disallineamento delle interfacce durante l'installazione.
l Sigillare preventivamente l'interfaccia prima dell'installazione e aggiungere cuscinetti antivibranti o sigillanti per migliorare l'effetto di tenuta iniziale o ridurre i guasti di tenuta causati dalle vibrazioni.
Inoltre, in termini di selezione degli elementi di fissaggio, vengono utilizzati elementi di fissaggio ad alta resistenza e coppia elevata, che vengono serrati più volte durante il processo di installazione per garantire la tenuta dell'interfaccia. Ad esempio, se viene utilizzato un dado a saldare di testa, la sua caratteristica è che può essere collegato direttamente al foro della parete della parte collegata (il pannello frontale della scatola) per la saldatura di testa. Questa progettazione strutturale può migliorare significativamente la tenuta stagna della parte di collegamento.
Figura 5: Utilizzo di dadi saldati a testa per aumentare la tenuta stagna
4-Selezione del sigillo
La progettazione e la selezione delle guarnizioni sono fondamentali in quanto influenzano direttamente l'affidabilità e la durata del sistema. Di seguito sono riportati i fattori chiave da considerare quando si progettano e si selezionano le guarnizioni per i sistemi di raffreddamento a liquido per l'accumulo di energia:
l Il materiale di tenuta deve avere una certa compatibilità chimica e di pressione, ed essere in grado di resistere all'intervallo di temperatura di esercizio del sistema, inclusi ambienti ad alta e bassa temperatura. La selezione del materiale della tenuta dipende dall'ambiente di utilizzo e dai requisiti di durata di servizio. I materiali di tenuta comuni includono gomma, politetrafluoroetilene (PTFE), nylon, metallo, ecc.
l Libertà di perdite: la guarnizione deve essere in grado di adattarsi alla leggera deformazione che può verificarsi nel sistema durante il funzionamento per garantire un buon effetto di tenuta in varie condizioni di lavoro. In genere, la deformazione della guarnizione deve essere maggiore del 30% e inferiore al 60% e la pressione dell'interfaccia di tenuta deve essere maggiore di 30 kPa.
Condivideremo regolarmente aggiornamenti e informazioni su tecniche di progettazione termica e alleggerimento, per la vostra consultazione. Grazie per l'interesse verso Walmate.
Nei veicoli elettrici puri, il peso del pacco batteria rappresenta circa il 30% del peso a vuoto. La leggerezza del pacco batteria è di grande importanza per migliorare l'autonomia di crociera del veicolo. Pertanto, la ricerca sull'elevata energia specifica dei pacchi batteria è una delle principali direzioni di ricerca attuali per i veicoli a nuova energia ed è anche il modo principale per ottenere veicoli elettrici leggeri. L'alleggerimento dei pacchi batteria di potenza può essere effettuato in due direzioni: miglioramento delle singole celle La densità energetica del pacco batteria è ottimizzata e gli accessori correlati del pacco batteria sono ottimizzati.
Lo sviluppo di pacchi batteria leggeri multi-materiale mira a ridurre il peso del pacco batteria, aumentare la densità energetica e l'autonomia di crociera, garantendo al contempo sicurezza e affidabilità utilizzando una varietà di materiali leggeri. Tra i componenti principali del pacco batteria, il corpo della cella della batteria ha la massa più elevata, seguito dalla scatola inferiore del pacco, dal coperchio superiore e dai componenti integrati BMS.
1-Design leggero del coperchio del pacco batteria
Il coperchio superiore della scatola della batteria si trova sopra la scatola della batteria di alimentazione e non è influenzato dai lati della scatola della batteria di alimentazione e non influenzerà la qualità dell'intero pacco batteria. Le sue funzioni includono principalmente la sigillatura e la protezione. Per migliorare l'efficienza energetica dell'intero veicolo, verranno presi in considerazione anche materiali leggeri nella progettazione. L'uso di materiali leggeri, come leghe di alluminio e materiali compositi (SMC, FRP, ecc.), può ridurre significativamente il peso del pacco batteria.
Inoltre, la progettazione strutturale della copertura superiore deve anche considerare l'efficienza di produzione e i requisiti di produzione di massa. Quando la struttura è molto irregolare, potrebbe essere difficile utilizzare la formatura o la piegatura e la saldatura su misura. La progettazione della copertura superiore deve anche considerare la connessione e la cooperazione con altri componenti come la scatola inferiore e le parti strutturali di tenuta per garantire la stabilità strutturale e l'affidabilità dell'intera scatola della batteria.
2-Design leggero del guscio inferiore del pacco batteria
La lega di alluminio è un materiale ideale per i gusci dei pacchi batteria grazie alla sua bassa densità, elevata resistenza specifica, buona stabilità termica, forte resistenza alla corrosione, buona conduttività termica, non magnetico, facile stampaggio e alto valore di riciclaggio. I materiali in lega di alluminio comunemente utilizzati includono 6061-T6, 6005A-T6 e 6063-T6. Questi materiali hanno diversi limiti di snervamento e resistenze alla trazione e possono soddisfare diverse esigenze strutturali.
Il guscio del pacco batteria è solitamente composto da un telaio profilato in lega di alluminio e da una piastra inferiore, che viene saldata utilizzando profili estrusi in lega di alluminio serie 6. Fattori come le dimensioni e la complessità della sezione del profilo, lo spessore della parete, ecc. devono essere considerati durante la progettazione per adattarsi a diversi requisiti strutturali e funzionali. Ad esempio, componenti come telai, partizioni centrali, pannelli del pavimento, travi, ecc. possono adottare diversi design di sezione trasversale.
Attraverso una progettazione strutturale ragionevole e metodi di collegamento, la resistenza complessiva del guscio può essere efficacemente garantita, la difficoltà di lavorazione può essere ridotta e il peso del guscio può essere ridotto:
l Pareti sottili: adottando un design a pareti sottili e utilizzando rinforzi per soddisfare i requisiti di resistenza, è possibile ridurre efficacemente il peso del materiale.
l Svuotamento: introduzione di sezioni cave nella progettazione strutturale per ridurre la densità del materiale.
l Ottimizzazione delle dimensioni: ottimizza le dimensioni del pacco batteria per ridurre l'utilizzo non necessario di materiali.
l Ottimizzazione della topologia: ridurre lo spazio occupato dai materiali ottimizzando la disposizione dei componenti interni del pacco batteria.
l Design modulare integrato: integra piastre di raffreddamento, golfari di sollevamento del pacco batteria e altri componenti nella scatola per ridurre il numero e il peso dei singoli componenti.
3-Produzione di tecnologia leggera
l Modellazione del materiale
Attualmente, ci sono tre categorie principali di processi di formatura del materiale della scatola della batteria: stampaggio, pressofusione di lega di alluminio ed estrusione di lega di alluminio. Il flusso di processo complessivo della scatola della batteria di potenza include processi di stampaggio e connessione del materiale, tra cui il processo di stampaggio del materiale è il processo chiave della scatola della batteria di potenza. Attualmente, la cassa superiore è principalmente stampata e i processi principali della cassa inferiore sono lo stampaggio per estrusione e la pressofusione di lega di alluminio.
l tecnologia di connessione
Il processo di collegamento della scatola della batteria è fondamentale nella produzione di nuovi veicoli energetici e prevede una serie di tecnologie e metodi per garantire la resistenza strutturale e la tenuta della scatola della batteria.
La saldatura è il principale processo di collegamento nella lavorazione delle scatole delle batterie ed è ampiamente utilizzato. Include principalmente i seguenti metodi:
① Saldatura a fusione tradizionale: come TIG (saldatura a gas inerte al tungsteno) e MIG (saldatura a gas inerte metallico). La saldatura TIG ha bassa velocità e alta qualità. È adatta per la saldatura a punti e la saldatura a traiettoria complessa. È spesso utilizzata per la saldatura su misura del telaio e la saldatura di piccoli pezzi a trave laterale. La saldatura MIG ha alta velocità e forte capacità di penetrazione ed è adatta per la saldatura a cerchio completo all'interno dell'assemblaggio della piastra inferiore del telaio.
② Saldatura a frizione e agitazione: la saldatura si ottiene generando calore tramite attrito. Ha le caratteristiche di buona qualità del giunto e alta efficienza produttiva.
③Tecnologia di trasferimento del metallo freddo: è adatta per materiali a piastra sottile. Non c'è apporto di calore durante il processo di saldatura, riducendo la deformazione.
④Saldatura laser: alta precisione, alta velocità, adatta per la saldatura di strutture complesse.
⑤ Saldatura a perno e saldatura a proiezione: utilizzata per la connessione rapida di parti specifiche. La saldatura a perno è fissata da perni e dadi, mentre la saldatura a proiezione è collegata mediante protuberanze a pressione.
Il metodo di collegamento meccanico risolve principalmente i problemi di facile saldatura e di slittamento del filo di materiali a piastra sottile durante la saldatura, tra cui:
① Dado per rivetto cieco: utilizzato per collegare la superficie di tenuta del telaio della scatola e la piastra inferiore della cavità interna. Presenta i vantaggi di un'elevata efficienza di fissaggio e di un basso costo di utilizzo. Adatto per collegamenti filettati tra piastre sottili e altri componenti.
②Inserto filettato in filo: utilizzato per rinforzare i fori delle viti in alluminio o altri corpi a bassa resistenza, migliorare la capacità portante delle viti e la distribuzione della forza delle filettature ed è adatto per i fori di montaggio dei moduli batteria e per i fori di montaggio delle superfici di tenuta. Rispetto ai dadi per rivetti ciechi, gli inserti filettati in filo sono più resistenti e facili da riparare, ma generalmente non sono adatti per installazioni a parete sottile.
Condivideremo regolarmente aggiornamenti e informazioni su tecniche di progettazione termica e alleggerimento, per la vostra consultazione. Grazie per l'interesse verso Walmate.
Per far fronte alle richieste del mercato come grandi intervalli, iterazioni rapide e linee di prodotto ricche, garantendo al contempo riduzione dei costi, miglioramento dell'efficienza e garanzia della qualità, per l'industria automobilistica, la standardizzazione dei prodotti - la piattaforma dei veicoli è senza dubbio una buona strategia. Attraverso la piattaforma delle batterie, la stessa soluzione di pacco batteria può essere abbinata a modelli diversi, oppure possono essere abbinate soluzioni di pacchi batteria composte dallo stesso tipo di celle della batteria e strutture simili. Ciò significa che possono essere standardizzate quante più parti possibili, il che può accorciare il ciclo di sviluppo, risparmiare sui costi, semplificare le linee di produzione e migliorare l'efficienza della produzione.
Primo: piattaforma della batteria
La soluzione della piattaforma batteria è favorevole alla pianificazione complessiva dei prodotti, alla riduzione dei costi e all'ottimizzazione della capacità produttiva. In base alla strategia della piattaforma batteria della piattaforma del veicolo, è necessario considerare l'intersezione e la larghezza di banda dei requisiti di ciascun modello della piattaforma e utilizzare il minor numero possibile di batterie e soluzioni di batterie per essere compatibili con il maggior numero possibile di modelli. Nello sviluppo dell'architettura di progetti puramente elettrici, è fondamentale disporre ragionevolmente il pacco batteria di potenza integrato. Gli elementi di lavoro specifici includono requisiti di potenza e prestazioni di potenza, sicurezza in caso di collisione, posizione e spazio di layout, ecc.
1-Confini delle dimensioni spaziali e standardizzazione delle celle della batteria
l Posizioni disponibili per i pacchi batteria
Attualmente, la disposizione della batteria di alimentazione principale è sotto il pavimento, compresi sotto i sedili anteriori, sotto i sedili posteriori, nel canale centrale e nel poggiapiedi. Questa disposizione può massimizzare l'area disponibile, aiutare ad abbassare il baricentro del veicolo, migliorare la stabilità di guida del veicolo e ottimizzare il percorso di trasmissione della forza di collisione.
Figura 1: Disposizione del pacco batteria durante lo sviluppo dei veicoli elettrici
l Evoluzione della disposizione dello spazio del pacco batteria
Pacco batteria diviso: viene adottato un layout dello spazio del pacco batteria diviso, come la serie JAC Tongyue. Il modulo energetico è costituito da due pacchi batteria, uno posizionato nella posizione originale del serbatoio del carburante e l'altro posizionato nel bagagliaio dove è riposta la ruota di scorta.
Inoltre, gli ingegneri stanno esplorando costantemente lo spazio utilizzabile all'interno dell'architettura originale dei veicoli a carburante, con conseguenti disposizioni dei pacchi batteria che assumono le forme di "工" , "T" e "土" .
Questo tipo di design è una modifica minore di un veicolo a carburante tradizionale. Lo spazio è molto limitato e il volume e il peso del pacco batteria che può essere caricato sono molto limitati, quindi la capacità è difficile da aumentare e l'autonomia di crociera non è elevata.
Pacco batteria integrato: si tratta di un nuovo concetto di progettazione del prodotto. Il design dell'intero veicolo ruota attorno al componente principale, il pacco batteria. Il pacco batteria è progettato in modo modulare e disposto in piano sul telaio del veicolo per massimizzare lo spazio disponibile.
l Disposizione del punto di installazione del pacco batteria
La disposizione ragionevole del pacco batteria è fondamentale e i fattori limitanti nella progettazione sono l'altezza da terra, la percorribilità, la sicurezza in caso di collisione, i requisiti di potenza e molti altri aspetti.
Figura 2: Vincoli di progettazione delle dimensioni del pacco batteria
La piattaforma del veicolo deve definire la categoria, il livello e il posizionamento di ciascun modello di veicolo all'interno della piattaforma, quindi determinare le dimensioni e il passo del veicolo. Il layout del veicolo scompone l'involucro delle dimensioni del pacco batteria nelle direzioni X, Y e Z in base allo spazio del veicolo. La batteria deve essere disposta all'interno dell'involucro dato del veicolo per garantire che non vi siano interferenze tra i vari sistemi del veicolo. L'indice di peso a vuoto può scomporre i requisiti di qualità del sistema del pacco batteria.
In termini di dimensioni della batteria, la progettazione dei pacchi batteria di potenza non può evitare rigidi indicatori di riferimento come lo spazio del veicolo e il peso a vuoto, il che significa che esiste una soglia per la progettazione delle celle della batteria. Vincolata da questa soglia, la dimensione della cella della batteria sarà concentrata in un certo intervallo, come: la lunghezza delle celle della batteria quadrate varia da 150-220 mm, la larghezza varia da 20-80 mm e l'altezza varia intorno ai 100 mm. La tendenza mutevole delle specifiche delle dimensioni delle celle della batteria è il risultato della relazione complementare tra la piattaforma del veicolo e la standardizzazione della batteria.
Tuttavia, le strategie della piattaforma della batteria, i modelli dei veicoli e la comprensione della standardizzazione di vari produttori di automobili sono diversi, con conseguenti differenze significative nelle attuali soluzioni di prodotto. Ad esempio, la strategia di standardizzazione di BYD è quella di sostituire completamente la batteria blade, la cui dimensione è bloccata a 960*13,5 (14)*90 (102) mm e la tensione della singola cella è 3,2/3,3 V.
2- Sviluppo di limiti di resistenza e soluzioni di capacità della batteria
La batteria di potenza fornisce energia per il viaggio del veicolo: la capacità della batteria, la profondità di scarica e la densità di energia influenzano la quantità di potenza disponibile. Per soddisfare le esigenze di diversi modelli, la differenza nel consumo di energia dei modelli è diventata una preoccupazione importante. L'autonomia di crociera del veicolo sarà influenzata da fattori quali la trazione elettrica, la batteria, il peso a vuoto, la resistenza al vento, la resistenza meccanica, il consumo di energia a bassa tensione e il recupero di energia. La possibilità di condividere soluzioni di batteria tra modelli con grandi differenze nel consumo di energia è debole, quindi è necessario sviluppare soluzioni di alimentazione della batteria personalizzate, tra cui dimensioni della batteria, qualità, potenza e ottimizzazione delle prestazioni di potenza per soddisfare i requisiti delle prestazioni di crociera.
In base ai vincoli dell'autonomia elettrica pura della piattaforma di produzione del veicolo, la scarica netta richiesta dalla batteria sarà influenzata dal consumo di energia di diversi modelli. È necessario confermare la distribuzione del consumo di energia di ciascun modello sulla piattaforma per convertire ulteriormente la larghezza di banda del consumo di energia nella distribuzione della domanda della batteria, quindi determinare il piano di alimentazione della batteria richiesto dalla piattaforma.
3-Limite di prestazione di potenza
Le prestazioni dinamiche del veicolo completo includono le performance in termini di accelerazione, velocità costante e modalità di risparmio energetico a diversi livelli di SOC (State of Charge) e temperature ambientali. Questo si traduce, a livello di batteria, nelle caratteristiche potenza-tensione della batteria stessa a diversi SOC e temperature. La potenza della batteria corrisponde alla richiesta di potenza del sistema di propulsione del veicolo, mentre la tensione corrisponde alla tensione nominale richiesta dal motore di trazione.
In genere, la valutazione delle soluzioni per le batterie per l'intera piattaforma del veicolo inizia dal tempo di accelerazione di 100 chilometri a temperatura normale e potenza elevata e dalla decomposizione dell'indicatore della batteria, e si estende gradualmente alla decomposizione dell'indicatore della batteria sull'intera autonomia e in tutte le condizioni operative.
SECONDO: Sviluppo della scatola della batteria
1-Integrazione e modularizzazione della batteria
Ottimizzare la progettazione dei moduli batteria, migliorare l'integrazione e la modularità dei pacchi batteria, ridurre i componenti inattivi e aumentare la densità energetica dei pacchi batteria.
Le tecnologie di integrazione dei pacchi batteria attualmente più diffuse includono CTP, CTB, CTC e altre forme. La forma, il materiale e la combinazione delle parti sono cambiati con l'avanzamento della tecnologia di integrazione. La direzione generale è integrazione e integrazione. Riducendo il numero di parti indipendenti e utilizzando una parte grande per sostituire più parti, si formano componenti più grandi e più funzionali.
2-Progettazione della scatola della batteria
La custodia della batteria è il supporto dell'assemblaggio del sistema di batterie di potenza, svolge un ruolo chiave nel funzionamento sicuro e nella protezione del prodotto e influisce direttamente sulla sicurezza dell'intero veicolo. La progettazione strutturale della custodia della batteria include principalmente la selezione dei materiali del guscio per il guscio superiore, il guscio inferiore e altri componenti della custodia della batteria e la selezione delle soluzioni del processo di fabbricazione. Il coperchio superiore della custodia della batteria svolge principalmente un ruolo di tenuta e non è soggetto a molta forza; la custodia inferiore della custodia della batteria è il supporto dell'intero prodotto del sistema di batterie di potenza e il modulo della batteria è principalmente disposto nella custodia inferiore. Pertanto, devono esserci misure strutturali come scanalature e deflettori incorporati all'interno della custodia della batteria per garantire che il modulo della batteria sia fissato in modo affidabile quando il veicolo è in marcia e non vi sia alcun movimento nelle direzioni anteriore, posteriore, sinistra, destra, su e giù, in modo da evitare impatti sulle pareti laterali e sul coperchio superiore e influire sulla durata della custodia della batteria.
Figura 3: Soluzione scatola inferiore batteria, telaio a-skin, saldatura b-FSW + telaio, saldatura c-FSW + telaio
l Progettazione della struttura del punto di installazione del pacco batteria e fissaggio della connessione
Il punto di installazione del pacco batteria di solito adotta una struttura a trave di montaggio, che attraversa la parte anteriore e posteriore, e l'estremità anteriore è collegata alla trave longitudinale della cabina anteriore per formare una struttura a trave chiusa efficace e coerente. I punti di installazione sono ragionevolmente disposti in base alla distribuzione del peso del pacco batteria. Il pacco batteria e il veicolo sono fissati in vari modi, tra cui fissaggio tramite bulloni, fissaggio meccanico + collegamento ibrido con giunto adesivo, collegamento a scatto, ecc.
Figura 4: Disposizione del pacco batteria e sezione di installazione
I pacchi batterie di potenza sono generalmente installati sul veicolo tramite più strutture di ganci. La lavorazione dei ganci deve sopportare non solo il peso considerevole del pacco batterie, ma anche le sollecitazioni generate dalla marcia dell'auto su strade irregolari, come ciottoli e buche profonde. Queste condizioni di durata e di uso improprio pongono requisiti più elevati sulla resistenza della struttura dei ganci.
Figura 5: Diverse soluzioni di collegamento del gancio di sollevamento: a Gancio di sollevamento saldato b Gancio di sollevamento con telaio estruso in alluminio
l Struttura di sicurezza e protezione della scatola della batteria
Resistenza meccanica e protezione: la scatola della batteria deve avere una resistenza meccanica sufficiente a proteggere le batterie al suo interno da urti e impatti meccanici. La scatola della batteria deve essere in grado di resistere a vibrazioni, estrusione e urti meccanici per garantire la sicurezza della batteria in varie condizioni.
Protezione dalle collisioni: la progettazione della custodia della batteria deve tenere in considerazione la sicurezza dalle collisioni, in particolare per le collisioni laterali e inferiori. Di solito è realizzata in alluminio o acciaio e collegata al vassoio inferiore tramite un telaio esterno per fornire rigidità strutturale e migliorare le capacità di assorbimento dell'energia di collisione. Inoltre, devono essere progettate strutture di assorbimento delle collisioni appropriate per prevenire la deformazione della custodia della batteria e danni alle celle della batteria.
Impermeabile, antipolvere e resistente alla corrosione: la scatola della batteria deve essere impermeabile e antipolvere e solitamente utilizza guarnizioni di tenuta di livello IP67 per garantire la tenuta stagna. Inoltre, dovrebbero essere prese in considerazione anche misure anticorrosione, come la spruzzatura di rivestimento in PVC all'esterno per migliorare la resistenza alla corrosione.
Progettazione antideflagrante e di scarico della pressione: quando una batteria esplode, l'energia deve essere rilasciata in modo concentrato e direzionale tramite dispositivi quali valvole antideflagranti bilanciate per evitare di entrare nella cabina del cliente. Inoltre, devono essere adottate misure antideflagranti (quali la parziale distruzione strutturale) per impedire la rottura complessiva dell'apparecchiatura.
l Design sigillato
Il design della superficie di tenuta tra il coperchio superiore e la cassa inferiore della scatola della batteria svolge un ruolo importante nelle prestazioni di tenuta e il suo design deve essere progettato insieme alla struttura della scatola della batteria e all'anello di tenuta. La superficie di tenuta deve essere mantenuta sullo stesso piano il più possibile per evitare troppe strutture curve. Poiché il coperchio superiore e la cassa inferiore sono collegati da bulloni, viene utilizzato un gran numero di bulloni, quindi è particolarmente importante garantire la coassialità dei fori. Mentre si dispongono ragionevolmente le posizioni dei fori dei bulloni, le dimensioni della posizione devono essere il più possibile rotonde e disposte simmetricamente nelle direzioni X e Y. La selezione del numero di bulloni di collegamento deve essere considerata in modo completo in base al livello di tenuta e alla quantità di carico di lavoro di smontaggio e montaggio.
Figura 6: Progettazione della tenuta della scatola superiore e inferiore, 1-coperchio superiore della batteria 2-guarnizione di tenuta 3-coperchio inferiore della batteria 4-condotto metallico
l Sicurezza elettrica e protezione da cortocircuito
Affidabilità della connessione: i connettori all'interno del vano batteria devono avere la corretta polarità per garantire la capacità di sovracorrente del vano batteria e l'affidabilità dei collegamenti elettrici/meccanici, comprese le misure di rilassamento, ecc.
Progettazione di isolamento elettrico e resistenza alla tensione: la progettazione del modulo adotta una doppia protezione di isolamento. La cella della batteria stessa ha uno strato di pellicola blu della cella della batteria e una toppa superiore della cella della batteria per soddisfare i requisiti di isolamento e resistenza alla tensione. La protezione di isolamento e resistenza alla tensione è impostata tra la piastra terminale/laterale e la cella della batteria e tra la cella della batteria e la superficie di montaggio inferiore.
l Progettazione della gestione termica
Lo sviluppo della gestione termica della batteria attraversa l'intero ciclo di progettazione e sviluppo del sistema del pacco batteria, inclusa la progettazione del controllo della temperatura della batteria, della piastra fredda, del sistema di tubazioni, ecc. L'obiettivo principale della progettazione del sistema di gestione termica della batteria è garantire che il sistema della batteria funzioni a una temperatura di esercizio relativamente adatta tramite il controllo del riscaldamento o del raffreddamento, tenendo conto della disposizione dello spazio, dei costi di progettazione, della leggerezza, ecc., riducendo al contempo la differenza di temperatura tra le celle per garantire la coerenza.
Condivideremo regolarmente aggiornamenti e informazioni su tecniche di progettazione termica e alleggerimento, per la vostra consultazione. Grazie per l'interesse verso Walmate.
Il pacco batteria è la fonte energetica principale dei nuovi veicoli energetici, che fornisce potenza motrice all'intero veicolo. In genere valutiamo i vantaggi e gli svantaggi della tecnologia del pacco batteria in base alle dimensioni di efficienza (densità energetica), sicurezza, costi di produzione e manutenzione.
Nella progettazione delle batterie, la tensione di una singola cella è di soli 3-4 V circa, mentre la tensione richiesta dai veicoli elettrici è di almeno 100 V. Le nuove auto ora hanno persino una tensione di 700 V/800 V e la potenza in uscita è generalmente di 200 W, quindi la batteria deve essere potenziata. Per soddisfare i requisiti di corrente e tensione dei veicoli elettrici, è necessario collegare celle diverse in serie o in parallelo.
Il pacco batteria è composto da celle, sistemi elettronici ed elettrici, sistemi di gestione termica, ecc., che sono racchiusi da una struttura del telaio della batteria: piastra di base (vassoio), telaio (telaio metallico), piastra di copertura superiore, bulloni, ecc. Come "confezionare" questi componenti e sistemi in un tutto in modo più efficiente e sicuro è sempre stato un argomento di continua ricerca ed esplorazione per l'intero settore.
Articolo precedente: Innovazione e sviluppo della tecnologia di integrazione delle batterie
L'origine della tecnologia dei gruppi di batterie di potenza può essere fatta risalire agli anni '50, e ha avuto origine nell'ex Unione Sovietica e in alcuni paesi europei. Questa tecnologia è stata originariamente utilizzata come concetto di ingegneria e produzione per determinare le somiglianze fisiche delle parti (percorsi di processo universali) e stabilire la loro produzione efficiente.
Il fulcro della Group Technology (GT) è identificare ed esplorare le somiglianze di cose correlate nelle attività di produzione, classificare problemi simili in gruppi e cercare soluzioni ottimali relativamente unificate per risolvere questo gruppo di problemi per ottenere benefici economici. Nel campo delle batterie di potenza, la group technology riguarda principalmente la tecnologia di integrazione delle batterie da singole celle in pacchi batteria (Pack), tra cui struttura, gestione termica, progettazione della connessione elettrica e tecnologia del sistema di gestione della batteria (BMS).
La prima tecnologia di raggruppamento nel campo automobilistico è MTP (Module To Pack), il che significa che le celle vengono prima integrate nei moduli e poi i moduli vengono integrati nei Pack. Questa tecnologia è caratterizzata da moduli staccabili e sostituibili, che hanno una buona manutenibilità, ma l'efficienza di raggruppamento è bassa. Con lo sviluppo della tecnologia, la tecnologia di raggruppamento ha subito una trasformazione da MTP a CTP (Cell To Pack). La tecnologia CTP si riferisce alla tecnologia di integrazione diretta delle celle nei Pack, eliminando la tradizionale struttura del modulo e migliorando l'efficienza di raggruppamento e l'efficienza di produzione. Negli ultimi anni, il settore sta anche esplorando tecnologie di raggruppamento come CTC (Cell To Chassis), CTB (Cell To Body & Bracket) e MTB (Module To Body) con maggiore efficienza di integrazione.
Nel campo delle batterie di potenza e dell'accumulo di energia elettrochimica, i principali progressi tecnologici delle batterie al litio derivano dall'innovazione strutturale e dall'innovazione dei materiali. Il primo consiste nell'ottimizzare la struttura di "cella-modulo-pacco batteria" a livello fisico per raggiungere l'obiettivo di migliorare sia la densità di energia del volume del pacco batteria sia la riduzione dei costi; il secondo consiste nell'esplorare i materiali delle batterie a livello chimico per raggiungere l'obiettivo di migliorare sia le prestazioni delle singole celle sia la riduzione dei costi. Questo articolo si concentra sull'impatto delle diverse tecnologie di integrazione strutturale sulla tecnologia di produzione del pacco batteria e sulla direzione dello sviluppo innovativo dal punto di vista dell'integrazione strutturale del pacco batteria. Le attuali tecnologie chiave per l'integrazione delle batterie di potenza sono illustrate nella figura seguente:
1-MTP è stato eliminato
All'inizio dell'attuale ondata di sviluppo di veicoli elettrici, sono stati lanciati molti modelli di veicoli a nuova energia da petrolio a elettrico. Essi continuano la disposizione spaziale e il design stilistico dei tradizionali veicoli a benzina. Gli ingegneri hanno assemblato un modulo di celle di batteria relativamente grande collegando un certo numero di singole celle di batteria in serie/parallelo, e poi hanno posizionato diversi di tali moduli di celle di batteria nel pacco batteria, che è il familiare pacco batteria "MTP". Poiché il pacco batteria deve essere "confezionato" più di due volte, il numero di componenti richiesti è estremamente elevato e il pacco batteria appare come "tre strati all'interno e tre strati all'esterno", con troppe parti ridondanti che occupano più volume e peso del sistema, con conseguente scarsa densità di energia volumetrica e densità di energia gravimetrica del pacco batteria "MTP". Inoltre, poiché la progettazione dei veicoli a benzina non ha specificamente riservato spazio per la batteria, il sistema di batterie può essere solo "schiacciato dove si adatta", con conseguente scarsa competitività del prodotto ed esperienza utente.
Dal lancio delle nuove piattaforme di veicoli elettrici intelligenti rappresentate da Tesla, i veicoli elettrici puri nativi hanno consentito di installare pacchi batteria in posizioni spaziali ideali in modo più efficiente e regolare, i sistemi tri-elettrici possono essere disposti in modo più ragionevole e l'architettura elettronica ed elettrica del veicolo e la progettazione della gestione termica possono essere integrate in modo più efficiente. La forza del prodotto del veicolo in termini di efficienza energetica, resistenza e intelligenza è stata notevolmente migliorata.
2-Era della tecnologia integrata 2.0——CTP
Il pacco batteria con struttura MTP presenta un problema significativo di utilizzo dello spazio. L'utilizzo dello spazio della cella della batteria rispetto al modulo è dell'80%, l'utilizzo dello spazio del modulo rispetto al pacco batteria è del 50% e l'utilizzo complessivo dello spazio è solo del 40%. Il costo dell'hardware del modulo rappresenta circa il 14% del costo totale della batteria. Questa struttura a basso utilizzo dello spazio non può soddisfare i requisiti di sviluppo dei nuovi veicoli energetici. Nell'ambito dell'idea di integrazione cella della batteria → modulo → pacco batteria → carrozzeria, se il veicolo desidera caricare quanta più potenza possibile nello spazio limitato del telaio e migliorare l'utilizzo del volume, è necessario considerare la standardizzazione di ogni fase di integrazione. Poiché la domanda di mercato per l'autonomia di guida continua ad aumentare, il volume di un singolo modulo batteria continua ad aumentare, il che porta indirettamente all'emergere della soluzione CTP.
La tecnologia della struttura CTP è nata per tenere in considerazione la sicurezza, la complessità del packaging, la riduzione dei costi, ecc. Con la premessa di garantire la sicurezza della cella della batteria, la tecnologia CTP riduce i cavi interni e le parti strutturali. Rispetto alla tecnologia MTP, la tecnologia CTP non ha una struttura modulare e confeziona direttamente la cella della batteria in un pacco batteria prima di installarlo sul veicolo.
Attualmente ci sono due idee principali. Una è quella di considerare il Pack come un grande modulo completo che sostituisce la struttura di più piccoli moduli al suo interno, rappresentata da CATL; l'altra è quella di considerare l'utilizzo di una soluzione senza modulo durante la progettazione e progettare la batteria stessa come partecipante alla forza, come la batteria blade di BYD.
Il punto centrale della tecnologia CTP è l'eliminazione del design del modulo, con le celle della batteria che si combinano direttamente con il guscio, riducendo l'uso delle piastre terminali e dei separatori. I problemi che ne derivano riguardano il fissaggio del pacco batteria e la gestione termica.
In effetti, il prodotto originale del pacco batteria CTP non era un progetto completamente privo di moduli, ma un progetto che univa i piccoli moduli originali in tre moduli grandi e due moduli medi, e c'erano anche piastre terminali in alluminio ad entrambe le estremità, quindi in teoria è ancora MTP, ma ci sono davvero grandi miglioramenti nella struttura.
Dopo l'introduzione di CTP 3.0, CATL ha presentato un metodo di produzione più avanzato, ottenendo un design completamente privo di moduli. Le celle della batteria sono state modificate da un orientamento verticale lungo l'altezza a una posizione orizzontale. Inoltre, è stata implementata una nuova soluzione di raffreddamento tra le celle della batteria, che non solo dissipa il calore ma fornisce anche funzioni di supporto, ammortizzazione, isolamento e controllo della temperatura. Anche il guscio inferiore è stato progettato con una funzione di fissaggio limitante.
Figura 1: Confronto tra la batteria CATL Kirin CTP2.0 e CTP3.0
3-Tecnologia integrata 3.0 Era—CTB, CTC
l Tecnologia CTB
La tecnologia CTP è un importante passo avanti nell'innovazione della struttura della batteria, ma non ha fatto una svolta nel pacco batteria stesso. Nella tecnologia CTP, il pacco batteria è ancora un componente indipendente. Rispetto alla strategia semplificata di CTP per i pacchi batteria, la tecnologia CTB combina il pannello del pavimento della carrozzeria e il coperchio del pacco batteria in uno. La superficie di tenuta piatta formata dal coperchio della batteria, dalla soglia della portiera e dalle travi anteriore e posteriore sigilla l'abitacolo passeggeri con sigillante e il fondo è assemblato con la carrozzeria attraverso il punto di installazione. Quando si progetta e si produce il pacco batteria, il sistema della batteria è integrato con la carrozzeria nel suo insieme, i requisiti di tenuta e impermeabilità della batteria stessa possono essere soddisfatti e la sigillatura della batteria e dell'abitacolo passeggeri è relativamente semplice e i rischi sono controllabili.
In questo modo, la struttura a sandwich originale di "coperchio pacco batteria-cella batteria-vassoio" si trasforma in una struttura a sandwich di "coperchio pacco batteria integrato sottoscocca-cella batteria-vassoio", riducendo la perdita di spazio causata dalla connessione tra carrozzeria e coperchio batteria. In questa modalità strutturale, il pacco batteria non è solo una fonte di energia, ma partecipa anche alla forza e alla trasmissione dell'intero veicolo come struttura.
Figura 2: Schema della struttura della tecnologia CTB
l Tecnologia CTC
Dopo aver adottato il metodo CTC, il pacco batteria non è più un assemblaggio indipendente, ma è integrato nella carrozzeria del veicolo, il che ottimizza la progettazione del prodotto e il processo di produzione, riduce il numero di parti del veicolo, in particolare riduce le parti strutturali interne e i connettori della batteria, ha il vantaggio intrinseco della leggerezza, massimizza l'utilizzo dello spazio e fornisce spazio per aumentare il numero di batterie e migliorare l'autonomia di guida. A condizione che il sistema elettrochimico stesso rimanga invariato, l'autonomia di guida può essere aumentata aumentando il numero di batterie.
Figura 3: Diagramma della struttura della tecnologia Tesla CTC
Ad esempio, Tesla e altre case automobilistiche hanno lanciato in successione modelli di tecnologia CTC. A livello di cella, possono utilizzare strutture sandwich elastiche multifunzionali e tecnologia di raffreddamento ad acqua di grandi dimensioni e sovrapporre la tecnologia di riutilizzo dello spazio anti-collisione nella parte inferiore del pacco batteria apportata dallo sviluppo integrato, tenendo conto dell'efficienza di raggruppamento, della dissipazione del calore e della sicurezza e promuovendo l'applicazione della tecnologia CTC dalle due dimensioni di ottimizzazione delle celle e protezione della struttura del veicolo. A livello di sviluppo integrato del veicolo, la cella della batteria è direttamente integrata nel telaio, eliminando i collegamenti di moduli e pacchi batteria. L'integrazione dei tre principali sistemi elettrici (motore, controllo elettronico, batteria), i tre sistemi elettrici minori (CC/CC, OBC, PDU), il sistema del telaio (sistema di trasmissione, sistema di guida, sistema di sterzo, sistema di frenata) e moduli correlati alla guida autonoma è realizzata e la distribuzione di potenza è ottimizzata e il consumo di energia è ridotto tramite il controller di dominio di potenza intelligente.
4-Modifiche ai requisiti specifici per i box batteria per le tecnologie CTP, CTB e CTC
Nella struttura tradizionale del pacco batteria, il modulo batteria svolge il ruolo di supporto, fissaggio e protezione della cella della batteria, mentre il corpo del box batteria sopporta principalmente la forza di estrusione esterna. L'applicazione delle tecnologie CTP, CTB e CTC propone nuovi requisiti per i box batteria, che si riflettono specificamente in:
I requisiti di resistenza del corpo della scatola della batteria sono migliorati: poiché il collegamento del modulo è ridotto o eliminato nelle strutture CTP, CTB e CTC, il corpo della scatola della batteria non deve solo resistere alla forza di estrusione esterna, ma anche alla forza di espansione della cella della batteria originariamente sopportata dal modulo. Pertanto, i requisiti di resistenza del corpo della scatola della batteria sono più elevati.
Capacità di protezione dalle collisioni: dopo aver utilizzato la tecnologia CTP per rimuovere le travi laterali del pacco batteria, la batteria subirà direttamente l'impatto della collisione, pertanto il pacco batteria CTP deve avere una resistenza alle collisioni sufficiente.
Requisiti di isolamento, isolamento e dissipazione del calore: le strutture CTP o CTB e CTC modificano il profilo della piastra inferiore in una piastra raffreddata ad acqua basata sulla scatola strutturale portante del telaio. La scatola della batteria non solo sopporta il peso delle celle della batteria, ma fornisce anche gestione termica e altre funzioni per la batteria. La struttura è più compatta, il processo di produzione è ottimizzato e il grado di automazione è più elevato.
Manutenibilità ridotta: il design altamente integrato rende complicata la sostituzione del pacco batteria. Ad esempio, nella struttura CTC, le celle della batteria sono riempite con materiale in resina, il che rende difficile la sostituzione delle celle della batteria e quasi impossibile la riparazione.
5- Impatto dell'integrazione del pacco batteria sull'infrastruttura di ricarica dei veicoli elettrici
La scelta di diverse tecnologie di integrazione del pacco batteria implica anche la scelta di diversi metodi di compensazione. CTP tende a essere la sostituzione della batteria, mentre CTB/CTC, più altamente integrato, tende a essere la ricarica rapida.
Un'elevata integrazione significa che più batterie possono essere ospitate nello stesso spazio, aumentando così l'autonomia dei veicoli elettrici. Gli utenti potrebbero non aver più bisogno di caricare frequentemente per brevi distanze, ma potrebbero preferire caricare rapidamente durante i lunghi viaggi. Pertanto, la pianificazione dell'infrastruttura di ricarica deve tenere conto di questi cambiamenti per garantire che possa soddisfare le esigenze degli utenti.
Con l'aumento dell'integrazione dei pacchi batteria, le dimensioni fisiche e la struttura dei pacchi batteria potrebbero cambiare, il che potrebbe influire sulla progettazione dell'interfaccia di ricarica e sulla compatibilità dell'apparecchiatura di ricarica.
Inoltre, la maggiore integrazione dei pacchi batteria potrebbe anche influire sulla velocità e l'efficienza della ricarica. Potrebbe essere necessario sviluppare e implementare sistemi di gestione della batteria e tecnologie di ricarica più efficienti per garantire un processo di ricarica rapido e sicuro.
Condivideremo regolarmente aggiornamenti e informazioni su tecniche di progettazione termica e alleggerimento, per la vostra consultazione. Grazie per l'interesse verso Walmate.
Nel processo di produzione di vassoi batteria e scatole fredde di accumulo di energia per veicoli a nuova energia, il trattamento superficiale necessario e appropriato è un passaggio fondamentale, come: l'uso di rivestimento, trattamento di ossidazione, ecc. per formare uno strato protettivo sulla superficie metallica per resistere all'erosione di mezzi corrosivi; i componenti che richiedono isolamento elettrico, come celle batteria, piastre di raffreddamento ad acqua, pareti del modulo, ecc., devono stabilire una pellicola protettiva isolante. L'isolamento è generalmente ottenuto spruzzando polvere isolante o vernice isolante. La scelta della tecnologia di trattamento superficiale appropriata può non solo migliorare le prestazioni del vassoio/scatola di raffreddamento a liquido, ma anche la durata e la sicurezza possono soddisfare le esigenze di diversi scenari applicativi. Questo articolo riassume le comuni tecnologie di trattamento superficiale come riferimento.
1-Pulizia e lucidatura
Durante il processo di produzione, sulla superficie del pallet possono accumularsi impurità come olio di lavorazione, residui di olio motore, polvere e polvere. Queste impurità non solo influiscono sulla durata utile del vassoio della batteria, ma possono anche influire negativamente sulle prestazioni e sulla sicurezza della batteria. Tramite pulizia e lucidatura, queste impurità possono essere rimosse efficacemente per garantire la pulizia della superficie del pallet. La pulizia e la molatura possono rimuovere efficacemente impurità superficiali, sbavature e scorie di saldatura, rendendo la superficie liscia e piatta, migliorando così la qualità complessiva del vassoio/scatola della batteria.
l pulizia chimica
Pulizia alcalina: la pulizia alcalina utilizza principalmente soluzioni alcaline (come idrossido di sodio, carbonato di sodio, ecc.) per rimuovere grasso, sporco e altre sostanze organiche dalla superficie delle leghe di alluminio. Il lavaggio alcalino rimuove il grasso tramite saponificazione, emulsificazione e penetrazione e bagnatura e allo stesso tempo genera precipitati solubili in acqua, ottenendo così un effetto pulente. La pulizia alcalina è solitamente utilizzata per rimuovere grasso, polvere e contaminanti organici dalla superficie delle leghe di alluminio.
Decapaggio: il decapaggio utilizza soluzioni acide (come acido nitrico, acido cloridrico, ecc.) per rimuovere incrostazioni di ossido, ruggine e altri depositi inorganici sulla superficie delle leghe di alluminio. Il decapaggio converte gli ossidi sulla superficie del metallo in sali solubili attraverso la reazione dell'acido con gli ossidi sulla superficie del metallo, rimuovendo così le impurità superficiali. Il decapaggio è utilizzato principalmente per rimuovere la pellicola di ossido, la ruggine e le incrostazioni di sale inorganico sulla superficie delle leghe di alluminio. Il decapaggio è spesso utilizzato per il trattamento finale delle superfici metalliche per migliorarne la finitura e la planarità.
l Rettifica meccanica
Durante la produzione, il processo di rettifica può rimuovere le tolleranze di lavorazione, correggere errori di forma, garantire la levigatezza e la precisione della superficie del pallet/scatola, soddisfare i requisiti di assemblaggio e quindi migliorare le prestazioni complessive e la durata utile.
La superficie pulita e levigata può migliorare il trattamento dei materiali di rivestimento o di altri materiali, ed è molto importante per l'applicazione successiva di rivestimenti anticorrosivi, sigillanti, conduttori di calore, isolanti e materiali di isolamento. Questo svolge un ruolo chiave nell'assicurare una solida adesione di questi materiali al pallet o al contenitore.
2-Stabilimento del rivestimento e della pellicola protettiva
Oltre alla pulizia e alla lucidatura di base, la produzione di pallet/scatole utilizza un processo di spruzzatura per il trattamento superficiale, al fine di formare uno strato protettivo che prevenga l'ossidazione e la corrosione e soddisfi le esigenze di diversi scenari, quali isolamento termico, isolamento e resistenza alla tensione.
l Isolamento termico
L'isolamento termico e anticondensa dei vassoi delle batterie può essere ottenuto mediante una progettazione completa di sistemi di isolamento termico, l'uso di materiali isolanti ad alta efficienza, l'applicazione di aerogel, la progettazione dell'isolamento del pacco batteria e la spruzzatura di materiali isolanti in schiuma.
Superficie inferiore spruzzata con PVC e materiale espanso
l Tensione di tenuta all'isolamento
L'isolamento dell'involucro del pacco batteria e dei componenti di raffreddamento a liquido serve principalmente a prevenire perdite di corrente, proteggere il personale da scosse elettriche e garantire il normale funzionamento del sistema di batterie. L'isolamento è in genere ottenuto tramite due metodi principali: spruzzatura a polvere e laminazione a pellicola. I principali processi di laminazione a pellicola includono laminazione a temperatura ambiente, pressatura a caldo ed esposizione ai raggi UV.
Spruzzatura interna di polvere isolante e vernice isolante
3-Loghi e segnaletica
Una targhetta o un'etichetta viene posizionata in una posizione ben visibile sul vassoio della batteria, generalmente tramite laser, incisione meccanica, ecc. Questi loghi sono solitamente realizzati con materiali resistenti all'usura e alla corrosione, per garantire che non vengano cancellati facilmente durante l'intera durata di servizio.
Condivideremo regolarmente aggiornamenti e informazioni su tecniche di progettazione termica e alleggerimento, per la vostra consultazione. Grazie per l'interesse verso Walmate.
In quanto apparecchiatura principale del sistema di accumulo di energia, il convertitore di accumulo di energia è uno strumento importante per la conversione di potenza, la gestione dell'energia, la garanzia della stabilità della rete, il miglioramento dell'efficienza energetica, ecc. Man mano che l'unità di potenza del convertitore di accumulo di energia si sposta verso un'elevata integrazione e un'elevata efficienza, lo sviluppo di frequenza e grande capacità pone requisiti sempre più elevati sulla dissipazione del calore.
1-Cambiamenti nei requisiti di raffreddamento
l Grazie alla cabina CC più grande, la capacità del convertitore continua ad aumentare e l'efficiente tecnologia di dissipazione del calore garantisce l'affidabilità dell'apparecchiatura.
Man mano che la capacità delle celle di accumulo di energia diventa sempre più grande, anche la capacità dei sistemi di accumulo di energia si sta espandendo simultaneamente. All'inizio del 2023, la capacità standard della batteria a cella singola da 20 piedi sul mercato era di soli 3,35 MWh. Nella seconda metà dell'anno, molte aziende di celle per batterie hanno lanciato prodotti di accumulo di energia da 310+Ah e la capacità della batteria a cella singola da 20 piedi è stata ampliata anche a 5 MWh. Tuttavia, meno di sei mesi dopo l'aggiornamento del modello da 5 MWh, alcuni importanti sistemi di accumulo di energia hanno rilasciato sistemi da 6 MWh e 8 MWh. Secondo l'esperienza generale, il convertitore di accumulo di energia è configurato a 1,2 volte la capacità di carico. La capacità della singola unità di un sistema di accumulo di energia da 5 MWh deve essere superiore a 2,5 MW. L'elevata potenza richiede una tecnologia di raffreddamento più efficiente per garantire un funzionamento stabile dell'apparecchiatura sotto carichi elevati sostenuti.
Evoluzione iterativa dello schema di topologia di integrazione del sistema di accumulo di energia
l L'applicazione della tecnologia ad alta tensione CC richiede che i dispositivi abbiano livelli di tensione di tenuta e resistenza dell'isolamento più elevati, inoltre la dissipazione del calore dei dispositivi di potenza è notevole.
Per adattarsi al sistema di accumulo di energia di grande capacità, la tecnologia ad alta tensione CC è diventata una tendenza tecnica. Attraverso l'aumento del livello di tensione, è possibile ottenere risparmio energetico, efficienza e miglioramento delle prestazioni. L'aggiornamento della tensione a 1500 V ha avuto origine dal fotovoltaico e ora il fotovoltaico è coinvolto nell'accumulo di energia. Tuttavia, l'evoluzione ad alta tensione del PCS di accumulo di energia ha ancora molta strada da fare e alcuni produttori hanno iniziato a ottimizzarla e spingerla a 2000 V. L'applicazione della tecnologia ad alta tensione CC costringe i dispositivi elettronici di potenza nei convertitori di accumulo di energia ad avere livelli di tensione di tenuta più elevati e una maggiore resistenza di isolamento per adattarsi agli ambienti di lavoro ad alta tensione. Negli ambienti ad alta tensione, la progettazione della dissipazione del calore dei dispositivi di potenza diventa più importante. La temperatura di giunzione pn dei dispositivi di potenza generalmente non può superare i 125 °C e la temperatura del guscio del pacchetto non supera gli 85 °C.
l I sistemi di accumulo di energia in rete richiedono algoritmi di controllo complessi, progetti di circuiti e convertitori di accumulo di energia ad alta densità di potenza
A differenza delle caratteristiche essenziali delle fonti di corrente nei sistemi di accumulo di energia grid-forming, i sistemi di accumulo di energia grid-forming sono essenzialmente fonti di tensione che possono impostare internamente parametri di tensione per generare tensione e frequenza stabili. Pertanto, è necessario che i convertitori grid-forming simulino le caratteristiche dei generatori sincroni, fornendo supporto per tensione e frequenza per migliorare la stabilità del sistema di alimentazione. Questa strategia di controllo richiede che i convertitori possiedano una maggiore densità di potenza e algoritmi di controllo più complessi, nonché dispositivi di alimentazione ad alte prestazioni e progetti di circuiti più intricati per implementare la strategia di controllo. Gestire efficacemente il calore generato da un'elevata densità di potenza e strategie di controllo complesse, riducendo al contempo le dimensioni e il costo del sistema di raffreddamento senza compromettere le prestazioni, è diventata una nuova sfida nella progettazione termica.
2- Confronto delle soluzioni di raffreddamento comuni
Negli ultimi anni la soluzione di raffreddamento per gli inverter con accumulo di energia ha subito una significativa evoluzione iterativa, che si riflette principalmente nella transizione della tecnologia di raffreddamento dal tradizionale raffreddamento ad aria a quella a liquido.
l Soluzione di raffreddamento ad aria
Il raffreddamento ad aria è la forma di controllo della temperatura utilizzata nella fase iniziale dei convertitori di accumulo di energia. Utilizza l'aria come mezzo e dissipa il calore tramite ventole e radiatori. La soluzione di raffreddamento ad aria migliora l'efficienza di dissipazione del calore riducendo costantemente il consumo di energia, ottimizzando la struttura e migliorando i materiali di dissipazione del calore. Al livello di potenza di 2,5 MW, il raffreddamento ad aria può ancora soddisfare i requisiti.
l Soluzione di raffreddamento a liquido
Poiché la densità di potenza e la densità energetica dei sistemi di accumulo di energia continuano ad aumentare, il PCS raffreddato a liquido utilizza un refrigerante con elevata conduttività termica come mezzo. Il refrigerante è azionato da una pompa dell'acqua per circolare nella piastra fredda e non è influenzato da fattori quali altitudine e pressione dell'aria. Il sistema di raffreddamento a liquido ha un'efficienza di dissipazione del calore più efficiente rispetto al sistema di raffreddamento ad aria. La soluzione di raffreddamento a liquido ha un grado di corrispondenza più elevato e ha iniziato a essere esplorata e resa popolare negli ultimi uno o due anni.
Oltre alla soluzione di accumulo di energia con raffreddamento a liquido completo, alcuni produttori hanno lanciato macchine di raffreddamento diretto con accumulo di energia, che utilizzano il raffreddamento diretto a cambiamento di fase e nessuna circolazione d'acqua. Anche le soluzioni di raffreddamento diretto stanno entrando nel campo dell'accumulo di energia.
Condivideremo regolarmente aggiornamenti e informazioni su tecniche di progettazione termica e alleggerimento, per la vostra consultazione. Grazie per l'interesse verso Walmate.
Il pacco batteria è un componente chiave dei nuovi veicoli energetici, degli armadietti e dei contenitori per l'accumulo di energia. È una fonte di energia attraverso l'involucro del guscio, che fornisce energia ai veicoli elettrici e fornisce capacità di consumo per gli armadietti e i contenitori per l'accumulo di energia. In combinazione con le effettive esigenze ingegneristiche, questo articolo riassume i punti chiave della progettazione del profilo per i pacchi batteria analizzando i requisiti di resistenza meccanica, sicurezza, gestione termica e leggerezza dei pacchi batteria.
1-Requisiti di progettazione dell'alloggiamento del pacco batteria
l Resistenza meccanica, resistenza alle vibrazioni e resistenza agli urti. Dopo il test, non dovrebbero esserci danni meccanici, deformazioni o allentamenti del fissaggio e il meccanismo di bloccaggio non dovrebbe essere danneggiato.
l Sigillatura: la sigillatura del pacco batteria influisce direttamente sulla sicurezza di funzionamento del sistema di batterie. Di solito è necessario raggiungere il livello di protezione IP67 per garantire che il pacco batteria sia sigillato e impermeabile.
l La progettazione dell'involucro del pacco batteria deve tenere in considerazione le prestazioni di gestione termica e garantire che la batteria funzioni entro un intervallo appropriato mediante un'adeguata progettazione della gestione termica.
l Per l'installazione e il fissaggio, la struttura deve avere spazio per la targhetta e i segnali di sicurezza e deve riservare spazio sufficiente e fondamenta fisse per l'installazione di linee di acquisizione, vari elementi sensori, ecc.
l Tutti i connettori, i terminali e i contatti elettrici con isolamento di base non polare devono soddisfare i requisiti del livello di protezione corrispondente quando combinati.
l Alleggerimento: l'alleggerimento del guscio è di grande importanza per migliorare la densità energetica del pacco batteria. La lega di alluminio è leggera e di alta qualità, il che la rende la scelta più fattibile al momento. Il livello di alleggerimento può essere migliorato tramite un design estremo appropriato in combinazione con applicazioni reali.
l Durata: la durata di vita del guscio del pacco batteria non deve essere inferiore alla durata di vita del prodotto complessivo. Non deve verificarsi alcuna deformazione plastica evidente durante il ciclo di utilizzo. Il livello di protezione e le prestazioni di isolamento non devono essere ridotti. La struttura deve essere facile da manutenere, inclusa la disposizione delle targhette e dei segnali di sicurezza e la protezione dei connettori.
Figura 1 Tipico guscio del pacco batteria saldato in lega di alluminio
2-Tipica soluzione con guscio per pacco batteria in lega di alluminio
I materiali in lega di alluminio comunemente usati per i gusci dei pacchi batteria includono 6061-T6, 6005A-T6 e 6063-T6, ecc. Questi materiali hanno diversi limiti di snervamento e resistenze alla trazione per soddisfare diversi requisiti strutturali. La resistenza di questi materiali è: 6061-T6>6005A-T6>6063-T6.
Attualmente, le soluzioni di formatura del guscio del pacco batteria includono la saldatura di profili in alluminio, la fusione di lega di alluminio, la fusione di alluminio più profili in alluminio, la saldatura di piastre in alluminio stampato, ecc. La soluzione di saldatura di profili in alluminio è diventata la scelta principale grazie alla sua flessibilità e praticità di lavorazione. Come mostrato nella Figura 1, il guscio è composto principalmente da un telaio di profili in lega di alluminio e da una piastra inferiore di profili in lega di alluminio, che vengono saldati utilizzando profili estrusi in lega di alluminio serie 6. La soluzione di fusione di lega di alluminio è considerata la futura direzione di sviluppo grazie al suo processo semplificato e al potenziale di riduzione dei costi.
3- Progettazione della sezione del profilo
l Dimensioni e complessità della sezione: la dimensione della sezione del profilo è misurata dal cerchio circoscritto. Più grande è il cerchio circoscritto, maggiore è la pressione di estrusione richiesta. La sezione del profilo è solitamente composta da più cavità per migliorare la rigidità e la resistenza strutturale. Solitamente, il telaio, la partizione centrale, la piastra inferiore, la trave, ecc. adottano diversi design di sezione per adattarsi a diversi requisiti strutturali e funzionali.
Figura 2 Sezione tipica del profilo in lega di alluminio
l Spessore della parete del profilo in alluminio: lo spessore minimo della parete di uno specifico profilo in alluminio è correlato al raggio del cerchio circoscritto del profilo, alla forma e alla composizione della lega. Ad esempio, quando lo spessore della parete della lega di alluminio 6063 è di 1 mm, lo spessore della parete della lega di alluminio 6061 dovrebbe essere di circa 1,5 mm. La difficoltà di estrusione della stessa sezione è: 6061-T6>6005A-T6>6063-T6. Nella progettazione dei profili del pacco batteria, il profilo del telaio è solitamente realizzato in materiale in lega di alluminio 6061-T6 e la sua sezione tipica è composta da più cavità e lo spessore della parete più sottile è di circa 2 mm; anche il profilo della piastra inferiore è composto da più cavità e il materiale è generalmente 6061-T6, 6065A-T6 e anche lo spessore della parete più sottile è di circa 2 mm; Inoltre, nella progettazione del vassoio portante della piastra inferiore e dell'integrazione del raffreddamento a liquido della piastra inferiore, la piastra inferiore adotta generalmente una struttura bifacciale, lo spessore della piastra inferiore è generalmente di 10 mm e lo spessore della parete e della parete interna della cavità sono di circa 2 mm.
l Tolleranza delle dimensioni trasversali del profilo: la tolleranza delle dimensioni trasversali deve essere determinata in base alla tolleranza di lavorazione del profilo in alluminio, alle condizioni di utilizzo, alla difficoltà di estrusione del profilo e alla forma del profilo. Per alcuni profili in alluminio difficili da estrudere, la forma può essere modificata o la tolleranza di lavorazione e la tolleranza dimensionale possono essere aumentate per ridurre la difficoltà di estrusione ed estrudere prodotti di profili in alluminio che sono vicini ai requisiti, e quindi possono essere rimodellati o lavorati per soddisfare i requisiti di utilizzo.
Inoltre, quando si progetta la sezione del profilo, è necessario considerare i requisiti specifici dei diversi processi di saldatura per giunti, scanalature, spessore delle pareti, ecc.
Condivideremo regolarmente aggiornamenti e informazioni su tecniche di progettazione termica e alleggerimento, per la vostra consultazione. Grazie per l'interesse verso Walmate.
La tenuta stagna del pacco batteria è un fattore chiave per garantire la qualità e la sicurezza del pacco batteria. È correlata alla sicurezza, all'affidabilità e alla durata del pacco batteria. Il test di tenuta stagna del pacco batteria deve essere eseguito non solo durante il processo di produzione, ma anche durante la manutenzione e l'ispezione della batteria.
1-Requisiti di tenuta stagna del pacco batteria
Nella produzione effettiva, la tenuta stagna del pacco batteria deve soddisfare i seguenti requisiti:
Prestazioni di tenuta: l'involucro del pacco batteria, l'interfaccia e i connettori devono avere buone prestazioni di tenuta per impedire a polvere, vapore acqueo e altre impurità esterne di entrare nel pacco batteria, il che può essere ottenuto tramite saldatura, sigillanti, materiali impermeabili, ecc.
Prestazioni impermeabili, per impedire all'umidità di entrare nella batteria, causando cortocircuiti, corrosione e altri problemi. Secondo lo standard nazionale GB38031-2020 "Requisiti di sicurezza per batterie di alimentazione per veicoli elettrici", le prestazioni di tenuta delle batterie e dei loro componenti devono soddisfare lo standard IP67. La maggior parte dei nuovi veicoli energetici ha requisiti di prestazioni di tenuta più elevati per le batterie e i loro componenti e deve soddisfare lo standard IP68, ovvero il pacco batteria può impedire all'acqua di entrare entro la profondità dell'acqua e il tempo di immersione specificati.
I metodi tradizionali di prova di tenuta all'aria includono il metodo di pressione e il metodo di immersione (prova in acqua). Il metodo di immersione consiste nell'immergere la piastra di raffreddamento a liquido in acqua e osservare se vengono generate bolle per giudicare la tenuta.
Piastra di raffreddamento a liquido Canale dell'acqua Serbatoio di prova di tenuta dell'aria
Sebbene lo standard IP68 sia più rigoroso, nelle applicazioni reali, il metodo della caduta di pressione è spesso utilizzato come metodo di rilevamento principale per soddisfare i requisiti IP68 impostando standard di rilevamento della tenuta stagna appropriati. Il metodo della caduta di pressione determina la tenuta stagna del pacco batteria misurando la variazione di pressione all'interno del pacco batteria. Quando si eseguono test di tenuta stagna, è necessario prestare attenzione a più parametri, come pressione di gonfiaggio, tempo di gonfiaggio, tempo di stabilizzazione della pressione e tasso di perdita.
(lato sinistro)Diagramma del principio di base della pressione differenziale
(lato destro)Diagramma del principio di base della pressione diretta
2-Analisi del problema di perdita della piastra di raffreddamento a liquido
Con il continuo aggiornamento della domanda di mercato per veicoli a batteria, sistemi di accumulo di energia a batteria, ecc., vengono ampiamente utilizzati pacchi batteria con densità di energia e densità di potenza più elevate. A causa delle caratteristiche termiche delle batterie, per garantire il funzionamento stabile delle apparecchiature principali come le batterie e migliorare l'efficienza di utilizzo dell'energia, la tecnologia di raffreddamento a liquido è una delle principali vie tecniche per la gestione termica dell'accumulo di energia e il test di tenuta all'aria del sistema di raffreddamento a liquido è diventato un collegamento chiave.
La perdita dalla piastra di raffreddamento a liquido è un problema serio: la perdita ostacolerà il normale flusso del refrigerante, comprometterà l'effetto di dissipazione del calore della piastra di raffreddamento a liquido e ridurrà le prestazioni dell'apparecchiatura; la perdita può anche causare l'invecchiamento e il danneggiamento dei componenti del sistema, riducendone l'affidabilità; la perdita può anche corrodere i componenti e i circuiti elettronici, aumentando il rischio di guasti e incendi dell'apparecchiatura.
Perché il problema delle perdite si verifica ancora dopo rigorosi test di tenuta all'aria durante il processo di produzione e fabbricazione della piastra di raffreddamento a liquido?
Processo di prova di tenuta all'aria del sistema di raffreddamento a liquido
Le infiltrazioni di liquidi possono essere causate da diversi fattori:
l Piccole crepe e difetti:I test di tenuta all'aria del paesaggio possono rilevare grandi canali di perdita, ma piccole crepe e difetti possono comunque esistere. Queste piccole crepe possono espandersi sotto la pressione del liquido o in un ambiente ad alta temperatura, causando infiltrazioni di liquido.
l Differenze di tensione superficiale e bagnabilità del refrigerante: quando la tensione superficiale del refrigerante è bassa, è più facile penetrare attraverso piccole fessure. Se la progettazione della tensione superficiale della piastra fredda del liquido non è ragionevole o il refrigerante non è selezionato correttamente, il problema di infiltrazione del liquido potrebbe aggravarsi.
Differenze di bagnabilità: diversi refrigeranti hanno una diversa bagnabilità sulle superfici solide. Se la rugosità superficiale del materiale della piastra fredda liquida è elevata o ci sono difetti microstrutturali, il refrigerante potrebbe penetrare più facilmente.
l Problemi di installazione o di processo: se il processo di installazione della piastra di raffreddamento del liquido non è sufficientemente accurato o se sono presenti difetti nella saldatura, nel collegamento e in altri processi, ciò potrebbe causare una scarsa tenuta e aumentare la possibilità di infiltrazioni di liquido.
l Condizioni ambientali: i cambiamenti di temperatura, specialmente in ambienti ad alta pressione, possono influenzare la permeabilità del refrigerante. Sebbene questi fattori ambientali possano non essere considerati durante i test di tenuta all'aria, nel funzionamento effettivo, le fluttuazioni di temperatura possono causare guasti alla guarnizione.
l Invecchiamento o affaticamento del materiale: se il materiale della piastra di raffreddamento del liquido viene utilizzato per troppo tempo, potrebbe invecchiare o affaticarsi, deteriorando le sue prestazioni di tenuta e aumentando così il rischio di perdite di liquido.
3-Misure preventive per perdite della piastra di raffreddamento a liquido
l Migliorare la progettazione della piastra di raffreddamento a liquido: ottimizzando la struttura e la progettazione della piastra di raffreddamento a liquido, ridurre piccole crepe e difetti e migliorare le sue prestazioni di tenuta. Ad esempio, quando si salda la trave di installazione del modulo sulla superficie del canale di flusso, adottare misure anti-perdita per evitare perdite di refrigerante.
l Migliorare il livello del processo di produzione: nel processo di produzione della piastra di raffreddamento a liquido, vengono utilizzati processi di saldatura e materiali di alta qualità per garantire che il refrigerante non sia facile da penetrare. Allo stesso tempo, durante il processo di assemblaggio, seguire rigorosamente le procedure operative per evitare allentamenti o installazioni errate.
l Ottimizza la combinazione di metodi di rilevamento per garantire l'efficienza del rilevamento migliorando al contempo la precisione del rilevamento e riducendo il tasso di rilevamento mancato. Il metodo di immersione e il metodo di caduta di pressione vengono utilizzati per il rilevamento della tenuta all'aria, che è semplice da utilizzare, economico ed efficiente ed è adatto per esigenze di rilevamento di routine su larga scala. Tuttavia, la precisione di rilevamento dei due metodi è bassa. La precisione di rilevamento del metodo di caduta di pressione è generalmente una velocità di perdita di 1×10-4Pa·m³/s e la precisione dei risultati di rilevamento è facilmente influenzata da fattori quali temperatura, umidità, pulizia e pressione. Utilizzare apparecchiature di rilevamento con una maggiore precisione di rilevamento e un effetto migliore per aumentare la precisione di rilevamento a 1×10-6Pa·m³/s, migliorando così l'effetto di rilevamento.
Oltre alle misure preventive per la piastra di raffreddamento a liquido stessa, è anche necessario adottare strategie di risposta appropriate sotto molteplici aspetti, come la scelta del refrigerante, la scelta della guarnizione e l'ambiente di lavoro dell'apparecchiatura.
Condivideremo regolarmente aggiornamenti e informazioni su tecniche di progettazione termica e alleggerimento, per la vostra consultazione. Grazie per l'interesse verso Walmate.
Nella progettazione della dissipazione del calore, l'adozione di metodi efficaci di riduzione dei costi può migliorare l'affidabilità e l'efficienza del sistema complessivo, riducendo al contempo i costi inutili.
1-Il design di derating riduce i costi
Il design di derating è un metodo di progettazione che riduce intenzionalmente gli stress elettrici, termici e meccanici a cui sono sottoposti componenti o prodotti durante il funzionamento. Negli scenari di produzione e utilizzo effettivi, la stabilità delle apparecchiature elettroniche può essere migliorata riducendo lo stress sopportato dai componenti.
Diagramma schematico dei percorsi di dissipazione del calore per imballaggi 2D e 3D
l Riduzione dello stress lavorativo: durante la progettazione e il funzionamento del prodotto, lo stress lavorativo dei componenti può essere ridotto riducendo il carico di lavoro, controllando la frequenza operativa, limitando la corrente e la tensione, ecc.
l Ridurre lo stress ambientale: ridurre lo stress ambientale selezionando tipologie di componenti, layout e forme di imballaggio appropriate, ad esempio selezionando componenti con un ampio margine di temperatura o utilizzando forme di imballaggio con una buona tenuta per ridurre gli effetti della temperatura, dell'umidità e della pressione sui componenti.
l Applicazione dell'ingegneria dell'affidabilità: progettazione ridondante ragionevole, rilevamento e isolamento dei guasti, ecc., riducono ulteriormente il rischio di guasto dei componenti.
Riducendo lo stress sui componenti durante il funzionamento, è possibile ridurre il loro consumo di energia e la generazione di calore. Quando i dispositivi di potenza funzionano in condizioni di stress inferiori allo stress nominale, è possibile ridurre il loro consumo di energia e la generazione di calore, il che aiuta a migliorare l'efficienza energetica e l'affidabilità del sistema. A lungo termine, la progettazione del derating aumenta efficacemente la durata dei componenti, riduce i tassi di guasto, riduce il carico di lavoro di manutenzione e quindi riduce i costi.
2-Ottimizzare il layout
L'efficienza di funzionamento del radiatore può essere notevolmente migliorata mediante una disposizione ragionevole dei componenti termici; una strategia di disposizione dei componenti ragionevole può raggiungere un equilibrio tra prestazioni del prodotto e costi.
l Distribuire i componenti di dissipazione del calore: disperdere i componenti che generano grandi quantità di calore per ridurre il carico termico per unità di superficie.
l Posizione che favorisca la dissipazione del calore: posizionare l'elemento riscaldante in una posizione che favorisca la dissipazione del calore, ad esempio vicino a una presa d'aria o al bordo del dispositivo.
l Disposizione sfalsata: durante la disposizione, sfalsare i componenti riscaldanti rispetto agli altri componenti generali e cercare di rendere i componenti riscaldanti principalmente sensibili alla temperatura per ridurre il loro impatto sui componenti sensibili al calore.
l Miglioramento del flusso d'aria: modificando la progettazione della direzione e la disposizione dei componenti, il percorso del flusso d'aria viene ottimizzato, la portata aumenta e il coefficiente di trasferimento del calore viene migliorato.
Raccomandazioni sulla spaziatura tra i componenti
3-Scelta del metodo di raffreddamento
Man mano che le prestazioni dei componenti elettronici migliorano e il grado di integrazione aumenta, la densità di potenza continua ad aumentare, con conseguente aumento significativo del calore generato dai componenti elettronici durante il funzionamento. Quando si sceglie un metodo di dissipazione del calore per i componenti elettronici, i requisiti di controllo della temperatura includono principalmente i seguenti aspetti:
l Intervallo di temperatura: diversi componenti hanno diversi intervalli di tolleranza della temperatura. Ad esempio, i chip ad alte prestazioni come le CPU hanno requisiti di temperatura di esercizio compresi tra 85 e 100 °C, mentre alcuni dispositivi a bassa potenza possono tollerare temperature più elevate, quindi il sistema di raffreddamento deve garantire che i componenti funzionino entro un intervallo di temperatura sicuro.
l Precisione del controllo della temperatura: in alcuni scenari con severi requisiti di controllo della temperatura, è necessario adottare una soluzione di dissipazione del calore in grado di controllare accuratamente la temperatura per evitare il degrado delle prestazioni dei componenti o addirittura danni causati da temperature eccessivamente alte o basse.
l Temperatura ambiente: l'effetto di dissipazione del calore delle apparecchiature elettroniche non dipende solo dalla capacità di dissipazione del calore del dispositivo stesso, ma è anche influenzato dalla temperatura ambiente circostante. La progettazione della dissipazione del calore deve considerare le variazioni della temperatura ambiente e cercare di mantenere il dispositivo entro un intervallo di temperatura adeguato tramite mezzi di dissipazione del calore.
l Consumo energetico e affidabilità: alcuni componenti elettronici a bassa potenza possono utilizzare la dissipazione naturale del calore quando generano poco calore. Per le apparecchiature ad alto consumo energetico, è necessario attendere la tecnologia di dissipazione del calore delle università per garantire che mantenga prestazioni normali e prolunghi il funzionamento sotto carichi elevati durata di servizio.
l Sigillatura e densità: nei dispositivi assemblati sigillati e ad alta densità, se la generazione di calore non è elevata, è possibile fare affidamento sulla dissipazione naturale del calore. Quando i componenti sono densamente imballati e generano grandi quantità di calore, sono necessarie tecnologie di dissipazione del calore più efficaci come la dissipazione del calore forzata o il raffreddamento a liquido. Il raffreddamento a liquido e la tecnologia heat pipe sono utilizzati in scenari con elevato consumo energetico e grande generazione di calore, come componenti elettronici ad alta potenza come tubi a onda progressiva, magnetron e tubi amplificatori di potenza, server e apparecchiature ad alto consumo energetico e sistemi trielettrici di veicoli a nuova energia. I suoi vantaggi applicativi unici.
(lato sinistro)Modulo di raffreddamento dell'aria della pila di carica
(lato destro)Modulo di raffreddamento a liquido della pila di carica
Quando si sceglie un metodo di raffreddamento per componenti elettronici, è necessario considerare in modo completo fattori quali generazione di calore e flusso di calore, temperatura ambiente e temperatura di esercizio, vincoli di spazio e requisiti di isolamento termico, nonché costi e fattibilità. Utilizzando una tecnologia di raffreddamento e dispositivi di raffreddamento appropriati per garantire che i componenti funzionino a una temperatura adatta, il costo di sostituzione e manutenzione del sistema può essere ridotto in modo efficace. Inoltre, riutilizzare progetti storici è anche una strategia efficace per ridurre i costi di sviluppo e produzione e migliorare l'affidabilità.
Condivideremo regolarmente aggiornamenti e informazioni su tecniche di progettazione termica e alleggerimento, per la vostra consultazione. Grazie per l'interesse verso Walmate.
I vassoi batteria, noti anche come scatole batteria o scatole PACK, sono sempre più apprezzati come un componente molto importante nello sviluppo di nuovi veicoli energetici. La progettazione dei vassoi batteria deve bilanciare la relazione tra fattori quali peso, sicurezza, costo e prestazioni dei materiali. Le leghe di alluminio sono ampiamente utilizzate nell'ingegneria leggera automobilistica per la loro bassa densità e l'elevata resistenza specifica, che può garantire rigidità assicurando al contempo le prestazioni della carrozzeria del veicolo.
1- Posizione di saldatura del vassoio della batteria e selezione del metodo
I vassoi per batterie in alluminio sono realizzati con profili in alluminio estruso e i vari componenti vengono uniti in un tutto tramite saldatura per formare una struttura di telaio completa. Strutture simili sono ampiamente utilizzate anche nelle scatole per pacchi di accumulo di energia.
Le parti di saldatura del vassoio della batteria solitamente includono la giunzione della piastra inferiore, la connessione tra la piastra inferiore e il lato, la connessione tra il telaio laterale, le travi orizzontali e verticali, la saldatura dei componenti del sistema di raffreddamento a liquido e la saldatura di accessori come staffe e orecchie pendenti. Quando si selezionano i metodi di saldatura, verranno selezionati diversi metodi di saldatura in base ai diversi requisiti strutturali e dei materiali, vedere la tabella seguente:
2-Analisi dell'influenza della deformazione termica della saldatura
La saldatura è un metodo di lavorazione con riscaldamento locale. Poiché la fonte di calore è concentrata sulla saldatura, la distribuzione della temperatura sulla saldatura è irregolare, il che alla fine porta alla deformazione della saldatura e allo stress della saldatura all'interno della struttura saldata. La deformazione termica della saldatura è il fenomeno per cui la forma e le dimensioni delle parti saldate cambiano a causa dell'apporto e dell'emissione di calore irregolari durante il processo di saldatura. In combinazione con l'esperienza effettiva del progetto di ingegneria, le parti che sono soggette a deformazione termica della saldatura e i fattori che influenzano sono riassunti:
a.Area di saldatura lunga e dritta
Nella produzione effettiva, la piastra inferiore del vassoio della batteria è generalmente realizzata con 2-4 profili in lega di alluminio uniti insieme mediante saldatura a frizione. Le saldature sono lunghe e ci sono anche lunghe saldature tra la piastra inferiore e la piastra laterale e tra la piastra inferiore e la trave distanziatrice. Le saldature lunghe sono soggette a surriscaldamento locale nell'area di saldatura a causa dell'apporto di calore concentrato, con conseguente deformazione termica.
Saldatura del telaio del vassoio della batteria
b.Giunti multicomponente
È causato dal riscaldamento locale ad alta temperatura e dal successivo raffreddamento durante il processo di saldatura nella saldatura multicomponente. Durante il processo di saldatura, la saldatura è soggetta a un apporto di calore non uniforme, con conseguente differenza di temperatura significativa tra l'area di saldatura e il materiale madre circostante, che causa effetti di espansione e contrazione termica, causando la deformazione delle parti saldate. L'estremità dell'installazione elettrica della scatola del pacco di accumulo di energia è solitamente dotata di un ugello per l'acqua, una staffa per cablaggio, una trave, ecc. e le saldature sono dense e molto facili da deformare.
Nella zona ad alta intensità di saldatura, il lato anteriore del pallet è deformato e deformato
c.Parete laterale del canale della piastra fredda
Nel vassoio batteria con design integrato della piastra di raffreddamento a liquido, le parti con minore rigidità strutturale, come piastre sottili e strutture di tubi, non possono resistere bene alla deformazione termica durante la saldatura e sono soggette a deformazione. Ad esempio, la parete laterale del canale di flusso della piastra di raffreddamento a liquido è molto sottile, generalmente solo circa 2 mm. Quando si saldano travi, staffe del cablaggio e altre parti sulla superficie di montaggio del modulo, è facile causare crepe e pieghe di deformazione sulla parete laterale del canale di flusso, influenzando le prestazioni complessive.
Difetti di crepe termiche sulla parete del canale di raffreddamento del liquido causati dalla saldatura a trave
3-Metodo di controllo della deformazione termica della saldatura
a.Saldatura a segmenti, saldatura bilaterale
Per le parti con requisiti di resistenza relativamente bassi, viene adottata la saldatura segmentata e il processo di saldatura viene suddiviso in più piccole sezioni. Le saldature sono disposte simmetricamente e le saldature sono disposte simmetricamente vicino all'asse neutro nella sezione di costruzione, in modo che le deformazioni causate dalle saldature possano compensarsi a vicenda. Allo stesso tempo, la lunghezza e il numero di saldature sono ridotti al minimo e si evita un'eccessiva concentrazione o incrocio di saldature, il che può ridurre il gradiente di temperatura di saldatura e quindi ridurre la deformazione della saldatura. Per le parti con requisiti di resistenza elevati come la piastra inferiore, la piastra inferiore e il telaio laterale, viene adottata la saldatura bifacciale per aumentare la resistenza riducendo al contempo la deformazione da flessione causata da parti di grandi dimensioni e lunghe saldature.
b.Ottimizzazione della sequenza di saldatura
Controllare la deformazione della saldatura, utilizzare giunti con rigidità inferiore, evitare saldature intersecanti bidirezionali e tridirezionali ed evitare aree ad alto stress. Ottimizzare la sequenza di saldatura, saldare prima le aree con rigidità più debole e per ultime quelle con rigidità migliore, ad esempio saldare prima le saldature a filetto, poi le saldature corte e infine le saldature lunghe; saldare prima le saldature trasversali, poi quelle longitudinali. Una sequenza di saldatura ragionevole può controllare efficacemente la deformazione della saldatura, controllando così le dimensioni della saldatura.
c.Regolazione dei parametri di saldatura
Controllare i parametri e i processi di saldatura e impostare ragionevolmente la velocità di saldatura, il numero di strati di saldatura e lo spessore di ogni saldatura. Per saldature più spesse, utilizzare metodi di saldatura multistrato e multicanale e lo spessore di ogni strato di saldatura non deve superare i 4 mm. La saldatura multistrato può ridurre la microstruttura strutturale e migliorare le prestazioni del giunto. Controllare accuratamente i parametri di saldatura e selezionare ragionevolmente parametri quali corrente di saldatura, tensione, modello di elettrodo e velocità di saldatura per garantire forma e dimensioni coerenti del bagno fuso, evitando così errori causati da una selezione impropria dei parametri.
d.Miglioramento delle capacità di saldatura
Migliorare le capacità operative del saldatore (utilizzare lavorazioni meccaniche per componenti di grandi dimensioni o nodi con requisiti rigorosi) per garantire coerenza e standardizzazione delle azioni durante la saldatura e ridurre i problemi dimensionali causati da fattori umani.
Condivideremo regolarmente aggiornamenti e informazioni su tecniche di progettazione termica e alleggerimento, per la vostra consultazione. Grazie per l'interesse verso Walmate.
Con l'evoluzione dei sistemi di accumulo di energia verso grandi capacità e un'elevata densità energetica, la progettazione di alloggiamenti per batterie ESS (Electronic Storage Enclosure) e la compatibilità dimensionale sono diventate questioni fondamentali per migliorare l'efficienza e l'affidabilità del sistema. Questo articolo combina i più recenti casi di progettazione ingegneristica, tecnologie brevettate e tendenze del settore per analizzare tre dimensioni: utilizzo dello spazio, compatibilità modulare e progettazione della disposizione e del supporto delle celle.
1- Ottimizzazione dell'utilizzo dello spazio
Il miglioramento dell'utilizzo dello spazio nell'integrazione dei sistemi di accumulo di energia è essenzialmente un processo bidirezionale di iterazione tecnologica e requisiti di scenario. Attraverso l'innovazione collaborativa di tecnologie come le celle per batterie ad alta capacità, l'architettura modulare e l'integrazione del raffreddamento a liquido, il settore sta passando dallo "stacking esteso" al "riutilizzo estremo dello spazio".
a. Applicazione di celle per batterie ad alta capacità: aumento della densità energetica e dell'efficienza
Riepilogo delle idee: L'applicazione di celle per batterie ad alta capacità mira essenzialmente a ridurre il livello strutturale interno del pacco batteria e a migliorare direttamente l'utilizzo dello spazio tra cella e pacco batteria. I pacchi batteria tradizionali adottano una modalità di integrazione a tre livelli: "cella batteria → modulo → pacco batteria", e la struttura del modulo (trave trasversale, trave longitudinale, bulloni, ecc.) riduce l'utilizzo dello spazio. Le celle di batterie ad alta capacità possono saltare direttamente il livello del modulo allungando o aumentando il volume della singola cella e utilizzare la tecnologia CTP (Cell to Pack) per integrare direttamente la cella della batteria nel pacco batteria.
Tecnica di base: utilizzare celle di batterie ultra-large da 600 Ah+ per ridurre il numero di celle e punti di connessione e aumentare la capacità della singola cella.
b. Riutilizzo spaziale e ottimizzazione dei costi: dall'"impilamento dei componenti" al "riutilizzo multidimensionale"
Riepilogo delle idee: Il riutilizzo spaziale e l'ottimizzazione dei costi sono due facce della stessa medaglia e la loro logica di fondo è quella di superare i limiti fisici e di costo dei sistemi di accumulo di energia tradizionali attraverso la semplificazione strutturale, l'integrazione funzionale, l'iterazione dei materiali e la progettazione standardizzata.
Il fulcro del riutilizzo spaziale è la riduzione dei collegamenti intermedi attraverso l'estrema semplificazione del livello strutturale. Ad esempio: il design due in uno della scatola ad alta tensione: la tecnologia brevettata di Jiangsu Trina Energy Storage combina due scatole ad alta tensione in una, condividendo il relè positivo/negativo totale e la connessione elettrica, riducendo l'occupazione dello spazio orizzontale del 30% e il costo dei componenti elettrici del 15%. Riutilizzo interdominio di moduli funzionali, integrazione di componenti strutturali e canali di dissipazione del calore, come l'integrazione della piastra di raffreddamento a liquido con la piastra inferiore del box e la condivisione dello spazio tra il tubo di raffreddamento a liquido e il supporto strutturale, riducendo del 15% i componenti indipendenti di dissipazione del calore; il corpo della batteria come parte strutturale: la batteria a lama di BYD fornisce un supporto robusto grazie alle pareti laterali lunghe e sottili della cella, eliminando il telaio del modulo e aumentando il tasso di utilizzo dello spazio al 60%-80%.
Una profonda ottimizzazione della topologia elettrica, ad esempio la topologia a cascata ad alta tensione, riduce il numero di circuiti paralleli aumentando la capacità e il livello di tensione delle singole celle (come nel caso dell'accumulo di energia a stringa intelligente di Huawei), riducendo lo spazio fisico dello stack di batterie del 20% e accorciando il tempo di risposta del sistema del 50%. Progettazione a relè condiviso: il box ad alta tensione due in uno di Jiangsu Trina Energy Storage consente a due linee di condividere lo stesso relè, riducendo del 50% il numero di relè e la lunghezza dei cavi e migliorando l'efficienza di installazione del 30%.
2- Disposizione delle celle e progettazione del supporto: bilanciamento tra capacità portante, dissipazione del calore e resistenza alle vibrazioni
L'essenza della disposizione delle celle risiede nel gioco tra utilizzo dello spazio, distribuzione del calore e stabilità meccanica. La forma fisica e la direzione di disposizione della cella influiscono direttamente sull'efficienza di riempimento dello spazio:
a. Ottimizzare la disposizione delle celle
Design della cella invertito: ruotare la valvola antideflagrante della cella verso il basso, in modo che lo scarico termico in fuga e lo spazio inferiore a prova di esplosione siano condivisi, liberando lo spazio in altezza della cella e ottenendo un utilizzo del volume ottimale.
Disposizione delle celle disposte orizzontalmente: ottimizzare l'utilizzo dello spazio in altezza del pacco batteria, aumentare la percentuale di materiali attivi e aumentare significativamente il tasso di utilizzo del volume rispetto alla cella verticale.
Celle ultra lunghe e sottili: ridurre il numero di celle per unità di volume grazie alla lunghezza e allo spessore ridotti delle celle, migliorando l'efficienza di raggruppamento.
b. Progettazione combinata di dissipazione del calore e capacità portante: mira a ottenere una duplice ottimizzazione dell'efficienza di dissipazione del calore e della resistenza strutturale attraverso l'innovazione collaborativa di struttura, materiali e processi. Percorso di progettazione strutturale:
Struttura integrata, come la progettazione conforme della piastra di raffreddamento a liquido e della trave di supporto: integrazione del canale di raffreddamento a liquido nella trave di supporto in lega di alluminio per ridurre i componenti indipendenti e migliorare l'utilizzo dello spazio;
Layout a strati e compartimentato, impilando il pacco batteria, il sistema di raffreddamento a liquido e il BMS a strati per ridurre l'interferenza reciproca tra flusso di calore e stress meccanico;
Ottimizzazione della meccanica bionica, come la struttura a nido d'ape/ondulata, progettazione di uno strato di nucleo a nido d'ape o ondulato nel telaio di supporto in lega di alluminio (come la soluzione brevettata Mufeng.com), assorbimento dell'energia delle vibrazioni tramite deformazione e ottimizzazione del percorso di dissipazione del calore.
Percorso di innovazione dei materiali:
Conduzione del calore e supporto del carico integrati, come il materiale composito in fibra di lega di alluminio (conduttività termica ≥ 200 W/m·K, resistenza +30%); materiale intelligente, lo strato di riempimento a cambiamento di fase (PCM) assorbe il calore e lo rilascia lentamente, differenza di temperatura ±1,5℃; smorzamento leggero: il cuscinetto elastico in silicone assorbe le vibrazioni (smorzamento +40%). Percorso di implementazione del processo:
Processo di stampaggio di precisione, come lo stampaggio per estrusione: utilizzato per la produzione di travi in lega di alluminio raffreddate a liquido con canali di flusso complessi;
Tecnologia di trattamento superficiale, come la generazione di uno strato di ossido ceramico sulla superficie della lega di alluminio per migliorare la resistenza alla corrosione (test in nebbia salina ≥1000 ore), migliorando al contempo l'efficienza di dissipazione del calore (emissività superficiale aumentata del 20%);
Processo di assemblaggio intelligente, regolazione dinamica del precarico, come l'integrazione di sensori di pressione e attuatori elettrici per regolare il precarico dei bulloni (5-20 kN) in tempo reale, evitando danni da sovrapressione alla cella della batteria.
c. Progettazione coordinata della resistenza al carico e alle vibrazioni della struttura di supporto: il sistema di supporto deve soddisfare il duplice requisito di resistenza al carico statico (peso della cella della batteria + pressione di impilamento) e di resistenza dinamica alle vibrazioni (trasporto/shock sismico).
3- Modularità e compatibilità: interfaccia standardizzata e architettura scalabile
L'essenza dell'interfaccia standardizzata che si adatta a batterie multi-dimensione è quella di ottenere un'espansione flessibile delle specifiche della batteria su una piattaforma unificata attraverso l'innovazione collaborativa nella gestione meccanica, elettrica e termica. La tecnologia attuale è passata dalla compatibilità statica alla regolazione dinamica e in futuro evolverà verso intelligenza, leggerezza e integrazione multi-scenario.
a. Innovazione collaborativa della struttura meccanica:
Standardizzazione dell'interfaccia meccanica: definire le dimensioni unificate del dispositivo di connessione.
Progettazione modulare di pacchi/armadi batteria: realizzare moduli e armadi batteria scalabili tramite celle di dimensioni standardizzate (come batterie da 280 Ah, 314 Ah), supportando combinazioni flessibili di diversi requisiti di capacità.
Figura 1-Contenitore per batteria ESS da 280 Ah
b. Regolazione dinamica del sistema elettrico
Protocolli e interfacce di comunicazione standardizzati, come la compatibilità con i sistemi BMS: formulare un protocollo di comunicazione BMS (sistema di gestione della batteria) unificato per supportare una connessione fluida con PCS e celle di batteria di diversi produttori; regolazione dinamica della potenza, attraverso il controllo dell'inerzia virtuale e un algoritmo di ottimizzazione multi-scala temporale, per ottenere una regolazione in tempo reale della potenza attiva/reattiva; e progettazione adattiva dell'abbinamento dei parametri elettrici.
c. Adattamento intelligente del sistema di gestione termica
Soluzioni di gestione termica graduali, come l'utilizzo di schiuma ignifuga ad alto rimbalzo, colla termoconduttiva e altri materiali a livello di batteria per bilanciare i requisiti di isolamento e dissipazione del calore e inibire la diffusione del calore; progettazione integrata della piastra di raffreddamento a liquido integrata a livello di modulo e dello strato isolante per migliorare la durata del ciclo; a livello di sistema, la capacità di raffreddamento viene regolata dinamicamente tramite compressori a frequenza variabile e più rami di raffreddamento.
Monitoraggio e previsione intelligenti, fusione multi-sensore. Posizionamento dei sensori di temperatura in punti chiave come i poli della batteria e ampie superfici per ottenere un'acquisizione della temperatura ad alta precisione; La tecnologia Digital Twin ottimizza la strategia di dissipazione del calore in tempo reale tramite monitoraggio cloud e manutenzione predittiva.
4-Riepilogo
L'ottimizzazione dello spazio degli alloggiamenti per batterie ESS è passata da un singolo miglioramento strutturale a un'innovazione collaborativa multidimensionale:
La fusione di materiali, struttura e algoritmi, come la combinazione di alloggiamento in fibra di carbonio + tecnologia CTP + algoritmo di layout basato sull'intelligenza artificiale, diventerà la norma.
La modularizzazione e la standardizzazione stanno accelerando e il design standardizzato, che vede il pacco batteria come unità funzionale più piccola, promuoverà la riduzione dei costi e l'aumento dell'efficienza nel settore.
La stretta correlazione tra gestione termica e utilizzo dello spazio, il raffreddamento a liquido a immersione e la tecnologia di controllo dinamico della temperatura liberano ulteriormente il potenziale dello spazio.
Condivideremo regolarmente aggiornamenti e informazioni su tecniche di progettazione termica e alleggerimento, per la vostra consultazione. Grazie per l'interesse verso Walmate.
Con la crescita esponenziale della potenza di calcolo dell'intelligenza artificiale e il continuo aumento della densità di potenza dei data center, la tradizionale tecnologia di raffreddamento ad aria non è più in grado di soddisfare le esigenze di dissipazione del calore. La tecnologia di raffreddamento a liquido è diventata indispensabile per i suoi vantaggi quali l'efficiente dissipazione del calore, il risparmio energetico e la riduzione dei consumi. Nella tecnologia di raffreddamento a liquido, la concorrenza tra piastra fredda e immersione è particolarmente agguerrita. Questo articolo analizzerà i vantaggi e gli svantaggi di entrambi dal punto di vista delle caratteristiche tecniche, degli scenari applicativi, del rapporto costo-efficacia e delle tendenze future, esplorerà le loro direzioni dominanti in futuro.
1- Confronto delle caratteristiche tecniche: il tipo a piastra fredda ha una forte compatibilità e il tipo a immersione ha una maggiore efficienza di dissipazione del calore
UN. Raffreddamento a liquido a piastra fredda: un "riformista" con transizione graduale
Elevata compatibilità: non è necessario modificare in modo significativo la struttura del server, è compatibile con l'infrastruttura del data center raffreddato ad aria esistente, con bassi costi di modifica e ciclo breve.
Elevata sicurezza: il refrigerante non entra in contatto diretto con i componenti elettronici, il rischio di perdite è basso e può essere ulteriormente ridotto grazie alla progettazione modulare (ad esempio giunti a sgancio rapido e tubi ridondanti).
Elevata maturità: la tecnologia Cold Plate è stata ampiamente utilizzata in scenari quali Alibaba Cloud Qiandao Lake Data Center e progetti di cooperazione Intel, rappresentando il 90% dell'attuale mercato del raffreddamento a liquido.
Limitazioni: il tipo cold plate riesce a coprire solo alcuni componenti ad alta potenza (come CPU e GPU), mentre il resto del calore deve comunque fare affidamento sul raffreddamento ad aria per favorire la dissipazione del calore. Il valore PUE è solitamente compreso tra 1,1 e 1,2, leggermente superiore a quello del tipo a immersione.
B. Raffreddamento a liquido ad immersione: un "innovatore" con efficiente dissipazione del calore
Il raffreddamento a liquido a immersione immerge completamente il server nel refrigerante isolante e consente la completa dissipazione del calore del dispositivo tramite contatto diretto. I suoi principali vantaggi includono:
Efficienza energetica estrema: la conduttività termica del liquido è 20-30 volte superiore a quella dell'aria, il PUE può arrivare fino a 1,05 e l'efficienza di dissipazione del calore aumenta di oltre 3 volte.
Risparmio di spazio: il volume del sistema di raffreddamento è solo 1/3 di quello del raffreddamento ad aria e la densità di potenza di un singolo cabinet può raggiungere più di 50 kW, il che è adatto a scenari ad alta densità come il supercomputing AI.
Silenzioso ed ecologico: non sono necessarie ventole, il rumore è ridotto di oltre il 90% e non c'è inquinamento da polvere, il che prolunga la durata dell'apparecchiatura.
Sfide: l'immersione richiede server personalizzati, il costo del refrigerante può arrivare fino al 60% (ad esempio il liquido fluorurato), l'investimento iniziale è elevato e la compatibilità ecologica deve essere migliorata.
2- Differenziazione dello scenario applicativo: prevale il raffreddamento a liquido a piastra fredda a medio e breve termine, viene liberato il potenziale di raffreddamento a liquido a immersione a lungo termine
UN. Raffreddamento a liquido con piastra fredda: una scelta conveniente per la ristrutturazione di IDC esistenti e la costruzione di nuovi IDC
Ristrutturazione di vecchi data center: il raffreddamento a liquido con piastra fredda può essere adattato rapidamente all'architettura raffreddata ad aria esistente, con un breve ciclo di ristrutturazione e costi controllabili. Ad esempio, la soluzione modulare su cui hanno collaborato Intel e Bich riduce le difficoltà di implementazione tramite una progettazione standardizzata della piastra fredda.
Scenari di elaborazione a media e alta densità: il raffreddamento a liquido cold plate supporta già 130-250 kW di potenza per cabinet (come le GPU NVIDIA serie B), soddisfacendo la maggior parte delle esigenze di formazione dell'intelligenza artificiale.
B. Raffreddamento a liquido a immersione: la soluzione definitiva per supercomputing e data center ecologici
Potenza di calcolo ad altissima densità: la potenza dei cabinet dei chip di prossima generazione (come la serie Rubin di NVIDIA) supererà i 1000 kW e il raffreddamento a liquido a immersione diventerà l'unica soluzione praticabile.
Esigenze di risparmio energetico: il PUE del raffreddamento a liquido a immersione è prossimo a 1,05 e l'efficienza di recupero del calore di scarto raggiunge il 90% (come la soluzione di Lenovo), in linea con la politica di obiettivi "dual carbon".
C. Situazione attuale del mercato
Il raffreddamento a liquido con piastra fredda domina il mercato attuale: nel 2025, il raffreddamento a liquido con piastra fredda rappresenterà l'80%-90% del mercato del raffreddamento a liquido, mentre il raffreddamento a liquido a immersione rappresenterà meno del 10%. Inoltre, sono state create interfacce standardizzate (come il design della piastra fredda OCP di Intel) e le soluzioni di produttori come Inspur e Sugon sono altamente compatibili. Il progetto cinese "East Data West Computing" richiede che il PUE dei data center di nuova costruzione sia ≤1,25 e il raffreddamento a liquido cold plate diventa la prima scelta per la transizione.
Il raffreddamento a liquido a immersione è pronto: la soluzione a immersione con cambio di fase Sugon C8000 raggiunge un PUE di 1,04 e il data center "Kirin" di Alibaba Cloud verifica la fattibilità del raffreddamento a liquido a immersione monofase. I chip ad alta potenza come la GPU NVIDIA B200 (1000 W+) hanno favorito l'uso della tecnologia immersiva, aumentando la densità di potenza di calcolo del raffreddamento a liquido del 30%-50%. L’UE prevede di vietare i liquidi fluorurati nel 2028 e la ricerca e lo sviluppo di refrigeranti nazionali a base di idrocarburi/oli siliconici hanno subito un’accelerazione (come la serie “Kunlun” di Sinopec).
3-Parere autorevole PK
Raffreddamento a liquido con piastra fredda: il raffreddamento a liquido con piastra fredda è il "rompighiaccio" per la diffusione del raffreddamento a liquido. Nei prossimi cinque anni rappresenterà ancora l'80% del mercato incrementale del raffreddamento a liquido. Il raffreddamento a liquido a immersione deve attendere che il consumo energetico del chip superi il punto critico.
Fazione di raffreddamento a liquido a immersione: il raffreddamento a liquido a immersione con cambiamento di fase è la forma definitiva di raffreddamento a liquido, mentre il raffreddamento a liquido con piastra fredda è solo una soluzione transitoria. Quando il consumo energetico di un singolo chip supera gli 800 W, il raffreddamento a liquido a immersione diventa l'unica opzione.
Neutrali: la differenziazione dei percorsi tecnici riflette la stratificazione della domanda di potenza di calcolo. La cold board supporta l'"informatica orientale", mentre l'immersione supporta l'"informatica occidentale". Lo sviluppo parallelo a doppio binario sarà il tema principale del prossimo decennio.
4-Opportunità e strategie del settore
Gioco ecologico e sui costi: il raffreddamento a liquido con piastra fredda avrà la meglio nel breve termine, mentre il raffreddamento a liquido a immersione deve ridurre i costi per uscire dalla situazione di stallo.
Raffreddamento a liquido con piastra fredda: ottimizzazione dei materiali (composito rame-alluminio), miglioramento della precisione di lavorazione (processo a prova di perdite) e promozione di una progettazione modulare e standardizzata.
Raffreddamento a liquido a immersione: sviluppare liquidi di raffreddamento convenienti (ad esempio liquidi a immersione monofase), cabinet compatibili e collaborare con i produttori di chip per personalizzare le soluzioni di raffreddamento.
Riserve tecnologiche: esplorare piastre di raffreddamento a flusso bifase e sistemi di monitoraggio intelligenti (come la regolazione dinamica del flusso tramite intelligenza artificiale) per far fronte alle future elevate richieste di potenza.
5- Conclusion
Breve termine (2025-2027): il raffreddamento a liquido a piastra fredda domina gli scenari generali e il tasso di penetrazione del raffreddamento a liquido a immersione aumenta al 15%-20%; Lungo termine (2030+): il raffreddamento a liquido a immersione con cambiamento di fase diventa la norma nel campo dell'elevata potenza di calcolo, mentre il raffreddamento a liquido a piastra fredda si ritira nel mercato a media e bassa densità.
I fattori decisivi: il costo del refrigerante, la velocità di incremento del consumo energetico dei chip e le politiche internazionali di tutela ambientale.
Condivideremo regolarmente aggiornamenti e informazioni su tecniche di progettazione termica e alleggerimento, per la vostra consultazione. Grazie per l'interesse verso Walmate.
Con il rapido sviluppo di veicoli a nuova energia e dei settori dell'accumulo di energia, leggerezza, elevata sicurezza ed efficiente gestione termica sono diventati requisiti fondamentali. La nostra azienda è profondamente impegnata nel campo della lavorazione di materiali in lega di alluminio. Affidandoci a una selezione avanzata di materiali, processi di formatura e tecnologie di saldatura, ci concentriamo sulla ricerca, sviluppo e produzione di vassoi per batterie, piastre di raffreddamento a liquido, scatole per accumulatori di energia e radiatori. La lega di alluminio è diventata la scelta ideale per la leggerezza e la gestione termica delle nuove apparecchiature energetiche grazie alla sua bassa densità (circa 2,7 g/cm³), all'elevata resistenza, alla resistenza alla corrosione e all'eccellente conduttività termica (conduttività termica di circa 150-220 W/m·K).
1- Selezione del materiale in lega di alluminio e considerazioni chiave
Prodotti diversi presentano requisiti prestazionali significativamente diversi per le leghe di alluminio ed è necessario combinare resistenza, resistenza alla corrosione, saldabilità e adattabilità al processo per una selezione completa dei materiali:
a. Vassoio batteria
Gradi comuni: 6061-T6, 6005A-T6, 6063-T6.
Criteri di selezione:
· Deve soddisfare una resistenza alla trazione ≥ 240 MPa (come il 6061-T6) per superare i test di estrusione, caduta e impatto con sfera standard nazionali;
· Elevati requisiti di saldabilità, è necessario evitare cricche termiche (si preferisce la serie 6xxx rinforzata con Mg/Si);
· La resistenza alla corrosione è migliorata tramite anodizzazione o rivestimento in alluminio.
Figura 1 - Vassoio batteria in lega di alluminio
b. Scatola per accumulatore di energia
Marche comuni: 5083, 6061-T6 (sia per resistenza meccanica che per resistenza alla corrosione).
Criteri di selezione:
· Necessità di resistere a vibrazioni e carichi d'impatto, il limite di snervamento deve essere ≥200 MPa;
· Elevati requisiti di trattamento superficiale per evitare la corrosione elettrochimica.
c. Piastra di raffreddamento a liquido
Marche comuni: 3003, 6061/6063, 6082.
Criteri di selezione:
· Elevata conduttività termica e resistenza alla corrosione;
· Il canale di raffreddamento a liquido richiede uno stampaggio complesso e si preferisce la serie 6xxx con eccellenti prestazioni di estrusione.
2- Differenze nelle prestazioni di processo e difficoltà di lavorazione
La lavorazione delle leghe di alluminio deve adattarsi alle loro proprietà fisiche, in particolare durante il taglio, la lavorazione CNC, la saldatura e il trattamento superficiale:
a. Taglio e lavorazione CNC
Difficoltà:
· La lavorazione di fori ad alta precisione è soggetta a bave o deformazioni (come sporgenze sul bordo dei fori a gradino) a causa della duttilità del materiale;
· Le strutture a pareti sottili (come i canali di flusso delle piastre di raffreddamento a liquido) devono controllare le forze di taglio per evitare deformazioni.
Soluzione:
· Utilizzare utensili con rivestimento diamantato per migliorare l'affilatura dei bordi e ridurre la deformazione da estrusione;
· Ottimizzare i parametri di lavorazione (come alta velocità e basso avanzamento) e collaborare con le apparecchiature CNC generali per ottenere una lavorazione stabile.
b. Processo di saldatura
Sfide principali:
· Il film di ossido (punto di fusione di Al₂O₃ 2050 °C) ostacola la fusione e porta facilmente alla formazione di pori e inclusioni di scorie; · Alcune leghe presentano un'elevata tendenza alla formazione di cricche a caldo, pertanto è necessario controllare l'energia di saldatura e la composizione del filo di saldatura.
Processi preferiti:
· Saldatura TIG (alimentazione a corrente alternata): adatta per lamiere sottili, con rimozione del film di ossido mediante "pulizia catodica";
· Saldatura MIG (alta corrente + miscela di gas elio): elevata efficienza di saldatura per lamiere spesse e apporto termico controllabile.
Figura 2 - Saldatura del vassoio della batteria
c. Trattamento superficiale
· Rivestimento isolante resistente alla pressione: applicato al vassoio batteria e all'interno del contenitore del pacco batteria, deve superare il test di pressione (≥3000 V CC/1 min); lo spessore del rivestimento è di 20-50 μm, per garantire la sicurezza dell'isolamento in ambienti ad alta tensione;
· Rivestimento isolante e deumidificante: per il contenitore del pacco batteria, vengono utilizzati materiali idrofobici (come la resina fluorocarbonica) per ridurre il rischio di condensa interna e il valore dyne è ≥34 per garantire l'adesione;
· Rivestimento di protezione anticollisione: utilizzato per la parete esterna del vassoio batteria, viene selezionato un elastomero poliuretanico (durezza ≥80 Shore A), con una resistenza all'impatto migliorata di oltre il 30%;
· Anodizzazione: trattamento anticorrosione convenzionale, errore di spessore del film ≤3 μm, adatto per strutture complesse.
3- Ispezione di verifica e adattabilità delle apparecchiature
Per soddisfare gli standard del nuovo settore energetico (come GB/T31467.3, UL2580), sono necessari una verifica multidimensionale e un adattamento del processo:
a. Ispezione di verifica
· Resistenza strutturale: verificare le prestazioni di carico, estrusione e impatto con la sfera del vassoio tramite simulazione agli elementi finiti (sollecitazione massima ≤ limite di snervamento del materiale);
· Test di tenuta: il sistema di raffreddamento a liquido utilizza il rilevamento delle perdite con elio (tasso di perdita ≤1×10⁻⁶ mbar·L/s) e un test di pressione ciclica (0,5-1,5 MPa/5000 volte);
· Verifica delle prestazioni del rivestimento:
Test di tensione di tenuta del rivestimento isolante (5000 V CC/60 s senza guasti);
Il rivestimento anticollisione supera il test di impatto con la sfera in caduta (sfera d'acciaio da 1 kg a 1 m di altezza) e il test di nebbia salina (1000 ore senza distacco).
b. Ottimizzazione dell'adattabilità delle apparecchiature
· Trasformazione generale delle apparecchiature CNC: grazie alla progettazione di attrezzature ad alta precisione e all'algoritmo di compensazione dinamica, la deformazione di lavorazione di componenti a pareti sottili può essere ≤0,1 mm;
· Libreria dei parametri di saldatura: definizione di parametri di saldatura standard (come corrente e velocità di avanzamento del filo) per diverse qualità di leghe di alluminio per ridurre il ciclo di debug;
· Spruzzatura automatizzata del rivestimento: grazie all'utilizzo di un robot multiasse per la spruzzatura, combinato con la tecnologia di polimerizzazione a infrarossi, l'errore di uniformità del rivestimento è ≤5%.
Conclusione
L'ampia applicazione delle leghe di alluminio nelle nuove apparecchiature energetiche non è solo una vittoria della scienza dei materiali, ma anche una manifestazione di innovazione di processo. La nostra azienda continuerà a esplorare nuove leghe di alluminio ad alta resistenza, resistenti alla corrosione e facili da lavorare, e a promuovere l'aggiornamento delle prestazioni di prodotti come vassoi per batterie e piastre di raffreddamento a liquido attraverso l'innovazione di processo, aiutando il settore a progredire verso un futuro efficiente e leggero.
Condivideremo regolarmente aggiornamenti e informazioni su tecniche di progettazione termica e alleggerimento, per la vostra consultazione. Grazie per l'interesse verso Walmate.
Con il continuo aumento della densità di potenza dei dispositivi elettronici, la progettazione della dissipazione del calore è diventata un elemento chiave che influenza l'affidabilità e la durata del sistema. In qualità di produttore professionale con 19 anni di esperienza nella gestione termica, combiniamo casi ingegneristici tipici con l'esperienza nella simulazione multifisica sul campo per analizzare a fondo i cinque principali malintesi tecnici che gli ingegneri tendono a trascurare negli scenari ad alta potenza e fornire soluzioni conformi alle prassi del settore.
Equivoco 1: Abuso di materiali ad alta conduttività termica, deviazione di calcolo della resistenza termica di interfaccia
Problema tipico: Ricerca eccessiva di valori teorici per i materiali termoconduttivi, ignorando la realtà ingegneristica della resistenza termica di contatto dell'interfaccia.
Analisi del caso: Un modulo di dissipazione del calore per radar laser per autoveicoli utilizza un substrato di rame puro (conduttività termica 401 W/m·K), ma lo spessore del rivestimento del materiale di interfaccia termica (TIM) non è controllato con precisione (0,1 mm di progetto, fluttuazione effettiva ±0,05 mm) e la resistenza termica di contatto misurata raggiunge 0,6 °C·cm²/W, causando un superamento del 22% della temperatura di giunzione dell'FPGA rispetto allo standard. Dopo il passaggio ai pad termici preformati (tolleranza ±0,02 mm, resistenza termica <0,03 °C·cm²/W) e la combinazione con il processo di sinterizzazione sotto vuoto, la temperatura di giunzione si riduce di 17 °C e l'MTBF (tempo medio tra guasti) aumenta a 100.000 ore.
Piano di ottimizzazione:
Selezione del materiale: secondo lo standard ASTM D5470, viene misurata la resistenza termica del TIM e si preferiscono materiali a cambiamento di fase o elastomeri caricati con metallo.
Controllo di processo: utilizzare apparecchiature di dosaggio automatiche (precisione ±3%) per garantire una tolleranza di spessore <10% ed evitare vuoti d'aria.
Equivoco 2: Incongruenza nell'organizzazione del flusso d'aria nel sistema di raffreddamento ad aria, punti caldi locali fuori controllo
Problema tipico: sovrapposizione cieca del numero di ventole, ignorando l'adattamento di impedenza del canale di flusso e l'effetto di separazione dello strato limite.
Esempio ingegneristico: un cluster GPU di un data center utilizza 4 ventole da 12.038 (volume d'aria 200 CFM), ma a causa di una progettazione non corretta dell'angolo di guida dell'aria (piegatura ad angolo retto di 90°), il volume d'aria effettivo effettivo è solo il 65% del valore nominale e la differenza di temperatura locale raggiunge i 40 °C. Dopo l'ottimizzazione della simulazione CFD, il canale di guida dell'aria viene modificato in un canale di flusso a espansione graduale (angolo di diffusione <7°) e viene adottato un layout a alette sfalsate (il gradiente di spaziatura aumenta da 2 mm a 3,5 mm), la resistenza al vento complessiva viene ridotta del 30% e la differenza di temperatura del punto caldo viene controllata entro 8 °C. Strategia di base:
Progettazione del campo di flusso: i test in galleria del vento vengono eseguiti secondo la norma ISO 5801 per ottimizzare il rapporto tra le aree di ingresso e di uscita (consigliato 1:1,2).
Controllo dinamico: in base alla curva Q-H della ventola PWM, il punto di impedenza del sistema viene abbinato all'intervallo di efficienza più elevato (solitamente 60-80% del volume d'aria massimo).
Equivoco 3: Un difetto nella progettazione della protezione ambientale accelera l'invecchiamento dei materiali
Problema tipico: concentrarsi solo sulle prestazioni iniziali di dissipazione del calore, ignorando gli effetti di stress ambientali a lungo termine come umidità, calore, polvere e nebbia salina.
Analisi del caso: un convertitore eolico offshore utilizza un dissipatore di calore in lega di alluminio 6061 (anodizzato superficialmente). Dopo 6 mesi di funzionamento in un ambiente con nebbia salina, lo strato di ossido si è staccato, causando un aumento del 50% della resistenza termica di contatto e un aumento del tasso di guasto degli IGBT. Passando alla lega di alluminio 5052 (resistenza alla nebbia salina >1000 ore) e applicando una vernice poliuretanica a tripla resistenza (spessore 50 μm, in conformità con lo standard IEC 60068-2-11), il tasso di guasto sul campo a 3 anni è diminuito del 75%. Punti di forza:
Tecnologia di rivestimento: Rivestimento ceramico Al2O3 mediante spruzzatura al plasma (conduttività termica 30 W/m·K, resistenza a temperature >800 °C) utilizzato in scenari ad alta temperatura.
Struttura di tenuta: Grado di protezione IP69K (guarnizione in silicone a doppio passaggio + valvola di sicurezza) per garantire l'assenza di infiltrazioni di polvere/vapore acqueo.
Equivoco 4: Mancanza di modellazione del carico termico transitorio e selezione inadeguata dei materiali a cambiamento di fase
Problema tipico: la soluzione di dissipazione del calore progettata tramite simulazione a stato stazionario non è in grado di gestire impulsi di potenza nell'ordine dei millisecondi.
Dati misurati: un amplificatore di potenza a stato solido è sottoposto a un carico impulsivo di 2 ms a 2000 W in una stazione base 5G. L'aumento di temperatura transitorio della soluzione tradizionale con substrato in alluminio raggiunge i 55 °C, mentre il materiale a cambiamento di fase a microcapsula (composito paraffina/grafene, calore latente del cambiamento di fase 220 J/g), combinato con la simulazione termica transitoria (lunghezza del passo transitorio ANSYS Icepak 1 ms), viene utilizzato per controllare l'aumento di temperatura a 18 °C, soddisfacendo i requisiti del test di impatto MIL-STD-810G.
Tecnologia di gestione dinamica:
Imballaggio a cambiamento di fase: la struttura a nido d'ape viene utilizzata per incapsulare il materiale a cambiamento di fase (porosità >70%) per evitare perdite di liquido e migliorare l'efficienza di diffusione del calore. Calibrazione del modello: le condizioni al contorno della simulazione vengono corrette in base all'imaging termico a infrarossi (frequenza di campionamento 100 Hz) e l'errore è <±1,5 °C
Equivoco 5: la valutazione del TCO è unilaterale e ignora i costi operativi e di manutenzione nascosti.
Problema tipico: viene confrontato solo il costo iniziale dell'hardware e non vengono quantificate le perdite dovute a consumo energetico/manutenzione/fermi macchina.
Confronto dei costi: una fabbrica di semiconduttori utilizzava originariamente armadi raffreddati ad aria (costo iniziale di 500.000 yuan), con una bolletta elettrica annua di 1,2 milioni di yuan (PUE = 1,8). Dopo l'aggiornamento al raffreddamento a liquido a immersione bifase (costo iniziale di 1,8 milioni di yuan), la bolletta elettrica annua è scesa a 450.000 yuan (PUE = 1,05) e, grazie alla riduzione del carico di condizionamento dell'aria della camera bianca, il risparmio annuo complessivo ha raggiunto i 900.000 yuan e l'investimento incrementale può essere recuperato in 2,1 anni (IRR > 25%). Modello decisionale:
Modellazione raffinata: introduzione di una simulazione Monte Carlo per quantificare l'impatto del tasso di guasto delle apparecchiature (distribuzione di Weibull) sul TCO.
Sovrapposizione delle politiche: in combinazione con meccanismi di tassazione del carbonio (come il CBAM dell'UE), le emissioni di carbonio dei sistemi di raffreddamento a liquido durante l'intero ciclo di vita vengono ridotte del 60% e si ottiene un sussidio aggiuntivo del 15%.
Conclusione: Aggiornamento del paradigma di progettazione termica da basato sull'esperienza a basato sui dati.
Processo standardizzato: Introduzione dello standard di test termico JESD51-14 nella fase di progettazione concettuale per evitare rilavorazioni successive (il ciclo di progetto di un determinato modulo ottico si riduce del 30%).
Collaborazione multidisciplinare: Grazie all'accoppiamento di perdite elettromagnetiche (estrazione HFSS) e campo di deformazione termica con COMSOL Multiphysics, l'efficienza di dissipazione del calore di un componente radar TR migliora del 40%.
Operatività e manutenzione intelligenti: Implementazione di sensori di temperatura a reticolo in fibra (accuratezza ±0,1 °C) e piattaforme di digital twin per ottenere la previsione dei guasti (i tempi di inattività imprevisti di un centro di supercalcolo si riducono del 90%).
Grazie a un approccio ingegneristico rigoroso e alla verifica completa dei dati, i progettisti termici possono evitare con precisione i "killer invisibili" e gettare le basi per sistemi ad alta affidabilità. Come professionisti del settore, ci impegniamo a fornire soluzioni a ciclo chiuso, dai materiali ai sistemi, e ad affrontare congiuntamente le sfide di gestione termica con i clienti.
Condivideremo regolarmente aggiornamenti e informazioni su tecniche di progettazione termica e alleggerimento, per la vostra consultazione. Grazie per l'interesse verso Walmate.
1- Requisiti di tolleranza speciali per i componenti chiave
Nella produzione di vassoi batteria per veicoli elettrici e di alloggiamenti per pacchi batteria per accumulo di energia con raffreddamento a liquido, il controllo della tolleranza delle superfici e delle interfacce di collegamento chiave influisce direttamente sulla tenuta, sull'efficienza di dissipazione del calore e sulla precisione di assemblaggio.
a. Superficie di installazione della piastra di raffreddamento a liquido
La piastra di raffreddamento a liquido è il componente principale del sistema di gestione termica della batteria. La planarità della sua superficie di installazione influisce direttamente sulla tenuta del canale di flusso del refrigerante. Se la planarità non rientra nei limiti di tolleranza, causerà una compressione irregolare della guarnizione in silicone, causando perdite localizzate o una maggiore resistenza termica.
b. Disallineamento dei cordoni di saldatura
Il vassoio batteria utilizza spesso una struttura di saldatura in lega di alluminio. Il disallineamento dei cordoni di saldatura causerà una concentrazione di sollecitazioni e ridurrà la durata a fatica. Soprattutto in scenari con elevati requisiti di ermeticità dell'alloggiamento del pacco batteria (come IP67), il disallineamento deve essere rigorosamente controllato.
c. Foro di posizionamento del modulo batteria
Il foro di posizionamento viene utilizzato per fissare con precisione il modulo batteria. Una tolleranza eccessiva causerà il disallineamento del modulo, con conseguenti guasti ai collegamenti elettrici o rischi di vibrazioni meccaniche.
d. Fissaggio della posizione del foro per i bulloni
Il foro per i bulloni viene utilizzato per collegare l'alloggiamento del pacco batteria al telaio. Eventuali deviazioni di posizione causeranno sollecitazioni di assemblaggio e persino la rottura dei bulloni.
e. Rettilineità dei bordi dell'alloggiamento del pacco batteria
La rettilineità dei bordi dell'alloggiamento del pacco batteria influisce sull'assemblaggio dei coperchi superiore e inferiore e sul livello di protezione IP, in particolare per gli alloggiamenti saldati al laser, dove il bordo deve essere utilizzato come riferimento per il tracciamento della testina laser.
2- L'impatto della tolleranza dimensionale sull'efficienza produttiva
L'impatto della tolleranza dimensionale sull'efficienza produttiva si riflette principalmente nel suo equilibrio tra flusso di lavorazione, controllo dei costi e qualità del prodotto. Una progettazione con tolleranze ragionevoli può non solo garantire la funzionalità del prodotto, ma anche ottimizzare il ritmo di produzione. L'impatto di un controllo ragionevole della tolleranza dimensionale sull'efficienza produttiva si riflette principalmente nei seguenti aspetti:
a. Equilibrio tra precisione di lavorazione e costi di produzione
· Sebbene una rigorosa tolleranza dimensionale possa migliorare la precisione di sigillatura e assemblaggio, sono necessarie apparecchiature di lavorazione ad alta precisione e processi complessi, il che aumenta significativamente l'investimento in attrezzature e i tempi di lavorazione.
· Un'eccessiva ricerca della precisione può comportare un aumento dei costi di lavorazione. È necessario impostare tolleranze rigorose nei componenti funzionali chiave e le tolleranze dovrebbero essere opportunamente allentate nelle aree non critiche per ridurre i costi.
b. Controllo del tasso di rilavorazione e del tasso di scarto
· Una progettazione con tolleranze ragionevoli può ridurre le rilavorazioni causate da deviazioni dimensionali.
· La deformazione da saldatura è il problema principale nella produzione di vassoi per batterie. L'utilizzo del processo di saldatura a freddo CMT può ottimizzare l'apporto termico, ridurre la deformazione dopo la saldatura e abbreviare il ciclo di rilavorazione.
c. Produzione modulare e standardizzata
· Grazie ai componenti standardizzati, i requisiti di tolleranza si concentrano su parti sostituibili localmente, riducendo la difficoltà di lavorazione complessiva.
· La progettazione con tolleranze standardizzate può inoltre supportare la compatibilità multi-modello e ridurre la necessità di lavorazioni personalizzate.
3-Standard di settore e applicazioni pratiche del controllo della planarità
Per i vassoi batteria dei veicoli a nuova energia, gli standard di settore prevedono requisiti rigorosi:
a. Standard di planarità: la planarità della superficie di installazione della piastra di raffreddamento a liquido deve essere ≤0,2 mm, la planarità della piastra di supporto inferiore deve essere ≤0,5 mm/m² e l'errore di planarità del telaio dopo la saldatura deve essere ≤0,8 mm6.
b. Ottimizzazione del processo di produzione: la fresatura di precisione CNC, la saldatura a freddo CMT e il trattamento di invecchiamento tramite vibrazioni (VSR), combinati con il rilevamento online tramite interferometro laser, riducono il rischio di deformazione.
c. Selezione del materiale: si consiglia di utilizzare leghe di alluminio ad alta resistenza come la 6061, con un limite di snervamento ≥1180 MPa, tenendo conto sia della leggerezza che della stabilità strutturale.
4- Strategia di adeguamento delle tolleranze basata su materiali e processi
a. L'innovazione nei materiali favorisce l'alleggerimento
Utilizzo di leghe di alluminio leggere ad alta resistenza (come la 6061) e materiali compositi (matrice di alluminio rinforzata con carburo di silicio), combinate con anodizzazione e rivestimento isolante, per ottenere una riduzione del peso del 30% e migliorare la resistenza alla corrosione, adattandosi ai requisiti di dissipazione del calore dei sistemi di raffreddamento a liquido.
b. La collaborazione di processo migliora la precisione di produzione
Lo stampaggio per estrusione monoblocco + la saldatura ad attrito e stiramento (FSW) riducono il numero di saldature, la saldatura a freddo CMT e la saldatura laser controllano la deformazione termica.
c. Simulazione a ciclo chiuso per garantire l'affidabilità
La simulazione CAE ottimizza la disposizione delle nervature di rinforzo, la scansione laser e la tecnologia di rilevamento delle perdite di elio consentono il monitoraggio completo del processo, il design modulare è compatibile con tolleranze di ±5 mm, riducendo i costi e aumentando l'efficienza.
Condivideremo regolarmente aggiornamenti e informazioni su tecniche di progettazione termica e alleggerimento, per la vostra consultazione. Grazie per l'interesse verso Walmate.
1- Caratteristiche del processo di saldatura in lega di alluminio del vassoio batteria/scatola del pacco di accumulo di energia
Nella produzione di nuove scatole del pacco di energia raffreddate a liquido, vassoi batteria e altri prodotti, i canali di raffreddamento a liquido e le strutture multi-cavità sono tipiche caratteristiche di progettazione complesse (come mostrato nella Figura 1). Tali strutture spesso includono le seguenti caratteristiche:
Figura 1: Design tipico di un vassoio per batteria
Interlacciamento spaziale tridimensionale: i canali di flusso sono distribuiti in una forma serpentina, con un gran numero di punti di svolta spaziali;
Collegamento multilivello: la cavità principale e la sottocavità sono collegate da partizioni a parete sottile (spessore 2-3 mm);
Caratteristiche di miniaturizzazione: piccole dimensioni della sezione trasversale del canale di flusso (lo spessore minimo della parete del canale di flusso del profilo in alluminio è 1,2 mm) e scarsa accessibilità alla saldatura.
2- Analisi delle difficoltà di combinare più tecnologie di saldatura nella produzione di vassoi per batterie
Nella pratica della produzione di vassoi per batterie, è necessario combinare più tecnologie di saldatura, come l'applicazione coordinata di saldatura a frizione e agitazione (FSW), saldatura a transizione di metallo freddo (CMT), saldatura a fusione tradizionale (TIG/MIG) e altre tecnologie. Questa combinazione mira a tenere conto di leggerezza, resistenza, tenuta ed efficienza produttiva, ma affronta anche le seguenti difficoltà principali:
a. Il problema dell'apporto di calore coordinato di più processi
Diverse tecnologie di saldatura (come FSW e saldatura laser) presentano grandi differenze nell'apporto di calore, che possono facilmente causare mutazioni delle prestazioni dei materiali e deformazione termica e devono essere risolte ottimizzando la sequenza di saldatura e la regolazione dei parametri.
b. Compatibilità delle apparecchiature e collo di bottiglia dell'efficienza
La commutazione delle apparecchiature è complessa e i requisiti di accuratezza della sincronizzazione dei parametri sono elevati. Sono necessari design di postazioni di lavoro modulari e saldatrici intelligenti per migliorare l'efficienza collaborativa e ridurre i tempi di ciclo.
c. Sfide nel bilanciare resistenza e costi della sigillatura
Il rischio di perdite all'intersezione di più saldature è elevato (rappresenta il 70% dei difetti) ed è richiesta una progettazione ridondante di sigillatura + ottimizzazione della topologia.
3-Pratica ingegneristica: vassoio batteria, raffreddamento a liquido per accumulo di energia, coordinamento del processo di saldatura multipla PACK box
a. Pianificazione della posizione delle cicatrici di saldatura
· Ottimizzazione della posizione di saldatura: nella fase di progettazione del prodotto, la razionalità della posizione di saldatura deve essere pienamente considerata per evitare che appaiano cicatrici di saldatura in parti o aree chiave che influenzano le funzioni del prodotto. Ad esempio, regolare lo spazio tra il telaio anteriore e l'ugello dell'acqua per evitare interferenze con le cicatrici di saldatura; ottimizzare la posizione di saldatura dell'ugello dell'acqua per ridurre l'impatto sulle prestazioni del prodotto.
· Corrispondenza con la struttura del prodotto: la posizione di saldatura deve corrispondere alla struttura del prodotto per garantire che la saldatura possa sopportare vari carichi e sollecitazioni durante l'uso del prodotto. Ad esempio, nel progetto della piastra di raffreddamento a liquido, la stabilità strutturale e l'affidabilità del prodotto vengono migliorate pianificando razionalmente la posizione di saldatura.
· Facile da usare e rilevare: la posizione di saldatura deve essere comoda per gli operatori per eseguire operazioni di saldatura e successive ispezioni di qualità. Ad esempio, evitare di saldare in posizioni difficili da raggiungere o con scarsa visibilità per migliorare l'efficienza e la qualità della saldatura.
b. Controllo della cicatrice di saldatura
· Dimensioni della cicatrice di saldatura: la dimensione della cicatrice di saldatura deve essere rigorosamente controllata. In genere, l'altezza della cicatrice di saldatura deve essere compresa tra 4 e 6 mm e la cicatrice di saldatura non deve superare il piano per garantire l'aspetto e la precisione di assemblaggio del prodotto. Ad esempio, nel progetto della piastra di raffreddamento a liquido, la dimensione della cicatrice di saldatura è stata controllata con successo regolando i parametri e il processo di saldatura, evitando l'impatto della cicatrice di saldatura sulle prestazioni e sulla qualità del prodotto.
· Forma della cicatrice di saldatura: la forma della cicatrice di saldatura deve essere il più regolare possibile per evitare una fusione eccessiva o incompleta. Ottimizzando i parametri di saldatura e le tecniche operative, la forma della cicatrice di saldatura può essere migliorata in modo efficace e la qualità della saldatura può essere migliorata.
· Trattamento di rettifica: per i segni di saldatura concavi prodotti nella posizione di saldatura a frizione, viene utilizzato un trattamento di rettifica per garantire una superficie liscia per soddisfare i requisiti di aspetto e prestazioni del prodotto.
c. Ottimizzazione della sequenza di saldatura
· Saldatura di partizioni: per prodotti di grandi dimensioni, il metodo di saldatura di partizioni può controllare efficacemente la deformazione complessiva. Dividendo il prodotto in più aree e saldandole in sequenza, la concentrazione di calore durante il processo di saldatura può essere ridotta e il rischio di deformazione termica può essere ridotto.
· Correzione passo dopo passo: durante il processo di saldatura, il metodo di correzione passo dopo passo viene utilizzato per regolare la deformazione della saldatura nel tempo. Misurando e correggendo continuamente la deformazione del prodotto durante il processo di saldatura, la precisione dimensionale e la forma del prodotto finale sono garantite per soddisfare i requisiti di progettazione.
· Ottimizzazione del percorso di saldatura: pianificare razionalmente il percorso di saldatura per evitare saldature ripetute nella stessa area e ridurre l'apporto di calore. Ad esempio, nel progetto della piastra di raffreddamento a liquido, l'apporto di calore durante il processo di saldatura è stato ridotto e la qualità della saldatura è stata migliorata ottimizzando il percorso di saldatura.
d. Controllo collaborativo della deformazione
La piastra di raffreddamento a liquido subisce una deformazione termica durante il processo di saldatura, con conseguente diminuzione della precisione dimensionale del prodotto. Misure di ottimizzazione:
· Utilizzare la saldatura di partizione e metodi di correzione passo-passo per controllare la deformazione complessiva.
· Ottimizzare i parametri di saldatura, ridurre corrente e tensione e ridurre l'apporto di calore.
· Utilizzare dispositivi di fissaggio per fissare il prodotto per ridurre il movimento e la deformazione durante la saldatura.
· Utilizzare il metodo di saldatura simmetrico per distribuire uniformemente il calore di saldatura.
Condivideremo regolarmente aggiornamenti e informazioni su tecniche di progettazione termica e alleggerimento, per la vostra consultazione. Grazie per l'interesse verso Walmate.
La tecnologia CTC (Cell-to-Chassis) ha attirato molta attenzione perché può migliorare significativamente l'autonomia e l'efficienza dello spazio dei veicoli elettrici, ma se possa davvero sostituire la tecnologia delle batterie tradizionali è ancora controverso. Il collo di bottiglia principale sul lato della produzione, il processo di saldatura del vassoio della batteria, è diventato la chiave per determinare il futuro di questa tecnologia: progettazione strutturale complessa, compatibilità multi-materiale e rigorosi requisiti di gestione termica hanno messo a dura prova la tecnologia di saldatura tradizionale. Partendo dalla prospettiva degli ingegneri in prima linea, combinando tendenze del settore e pratiche ingegneristiche, questo articolo analizza il potenziale e i limiti della tecnologia CTC ed esplora come la tecnologia di saldatura sia diventata la "pietra di paragone" di questa rivoluzione tecnologica.
1-L'"Ideale e la realtà" della tecnologia CTC
La tecnologia CTC può teoricamente ridurre le parti strutturali ridondanti e migliorare la densità energetica integrando la cella della batteria direttamente nel telaio, ma la fattibilità della sua applicazione su larga scala sta affrontando sfide realistiche:
Radicalismo e cautela delle case automobilistiche: Tesla, BYD e altre aziende leader hanno lanciato soluzioni CTC, ma altri produttori stanno ancora aspettando e osservando. I dati del settore mostrano che a febbraio 2025, i modelli CTC prodotti in serie rappresentano il 15-20% del mondo e la tradizionale tecnologia CTP (Cell-to-Pack) è ancora la tecnologia dominante.
Il "costo" della durata migliorata della batteria: sebbene la CTC possa aumentare la densità energetica del 15%-20%, la complessità della struttura del telaio porta a un aumento dei costi di produzione del 30%-50% (calcolato da un'agenzia di consulenza) e l'equilibrio tra costi e benefici non è ancora chiaro.
Controversia economica sulla manutenzione: il design integrato ha causato un aumento vertiginoso dei costi di manutenzione della batteria. I dati delle compagnie assicurative mostrano che il tasso di sostituzione dei gruppi batteria dopo incidenti dei modelli CTC è pari al 70%, molto più alto del 25% dei modelli tradizionali.
Queste contraddizioni rendono il futuro della tecnologia CTC pieno di variabili. Se il mercato riuscirà a superare il 20% dipenderà da tre variabili principali: il progresso della produzione di massa del Tesla Cybertruck; se la guerra dei prezzi tra le case automobilistiche cinesi costringerà CTC a ridurre i costi; e il grado di compromesso delle normative europee sulla riparabilità delle batterie. Il livello di tecnologia di saldatura sul lato della produzione sarà la chiave per determinare se riuscirà a colmare il divario tra laboratorio e produzione di massa.
2-Tre "barriere di vita e di morte" del processo di saldatura
Per i produttori di vassoi per batterie, l'implementazione della tecnologia CTC deve superare tre problemi fondamentali:
a. Il gioco tra precisione "a livello di micron" ed efficienza
I processi di saldatura tradizionali possono tollerare errori di 0,5 mm, ma i vassoi CTC devono trasportare più batterie e il numero di giunzioni aumenta di oltre 3 volte, e la maggior parte di esse è distribuita su parti curve e irregolari. I test di un produttore mostrano che quando l'errore di posizionamento della saldatura supera 0,15 mm, il tasso di resa dell'assemblaggio delle celle della batteria scenderà drasticamente dal 99% all'82%. Ciò che è più complicato è che il miglioramento della precisione è spesso accompagnato da una diminuzione dell'efficienza: sebbene l'accuratezza della saldatura laser sia elevata, il costo dell'attrezzatura è più di 5 volte superiore a quello della saldatura tradizionale.
b. L'"acqua e il fuoco" dei materiali misti
Per bilanciare leggerezza e resistenza, i vassoi CTC spesso utilizzano una struttura mista di "lega di alluminio + fibra di carbonio + acciaio speciale". La differenza nei coefficienti di dilatazione termica di materiali diversi può arrivare fino a 20 volte (ad esempio alluminio 23μm/m·K contro fibra di carbonio 0,8μm/m·K), il che genera facilmente stress interno durante la saldatura e causa crepe. Quando un'azienda ha provato a collegare alluminio e fibra di carbonio, il tasso di crepe della saldatura era alto fino al 18%, superando di gran lunga la soglia accettabile del settore del 3%.
c. "Killer invisibile" della zona interessata dal calore
L'elevata temperatura di saldatura può danneggiare i materiali isolanti o i circuiti dei sensori attorno alla cella della batteria. Una volta un'azienda automobilistica ha aumentato il tasso di autoscarica del modulo batteria del 50% a causa di un controllo improprio dell'apporto di calore di saldatura. Gli ingegneri devono controllare la fluttuazione della temperatura di saldatura entro ±15℃ entro 0,1 secondi, il che equivale a installare un "freno termico ad alta precisione" sulla pistola per saldatura.
3-La via d'uscita: non esiste una soluzione miracolosa, solo innovazione di sistema
Di fronte a queste sfide, il settore sta esplorando tre percorsi rivoluzionari:
a. "Cocktail therapy" di combinazione di processi
Saldatura ibrida ad arco laser: combinando la precisione della saldatura laser con i vantaggi della penetrazione della saldatura ad arco, la velocità di saldatura della lega di alluminio aumenta del 40%;
Tecnologia di transizione del metallo freddo (CMT): attraverso un controllo preciso dell'apporto di calore, l'area della zona termicamente alterata viene ridotta del 60%;
Sistema di compensazione intelligente del robot: regola automaticamente il percorso della pistola di saldatura in base ai dati di scansione della saldatura in tempo reale e aumenta il tasso qualificato di saldatura di superfici curve complesse dal 75% al 95%.
b. "Pre-compromesso" sul lato del materiale
Alcune aziende hanno iniziato a sviluppare congiuntamente materiali compositi "saldabili" con i fornitori di materiali. Ad esempio, la sensibilità alle crepe di saldatura di una lega di alluminio modificata nazionale (materiale in lega di alluminio regolato con mezzi fisici, chimici o di processo) è stata ridotta dal livello 7 al livello 3 (secondo gli standard ISO). Sebbene sacrifichi il 5% dell'effetto leggero, aumenta la resa della saldatura al 98%.
c. "Digital twin" nella dimensione di rilevamento
Raccogliendo tutti i dati del processo di saldatura (corrente, temperatura, velocità, ecc.), combinati con modelli AI per prevedere la probabilità di difetti. Dopo che una fabbrica ha introdotto questa tecnologia, il tasso di rilevamento online dei difetti di saldatura è aumentato dall'80% al 97% e il costo degli scarti è stato ridotto del 45%.
4- Nuova proposta degli ingegneri: trovare la certezza nell'incertezza
a. La controversia sulla tecnologia CTC è essenzialmente un gioco tra "ottimizzazione del sistema" e "limiti locali":
se la velocità di svolta del processo di saldatura è più lenta delle aspettative di riduzione dei costi delle aziende automobilistiche, la CTC potrebbe diventare una tecnologia di nicchia;
se materiali, processi e tecnologie di collaudo fanno progressi in modo coordinato, ci si aspetta che inaugureranno una nuova era di progettazione strutturale dei veicoli elettrici.
b. Per gli ingegneri, è necessario ricostruire le capacità da due dimensioni:
integrazione delle conoscenze interdisciplinari: comprendere la soglia sensibile delle proprietà elettrochimiche all'apporto di calore di saldatura;
capacità di risposta agile: uno studio di caso di un fornitore europeo mostra che il team che riesce a completare l'ottimizzazione dei parametri di saldatura di nuovi materiali in lega entro una settimana ha una probabilità di ottenere ordini triplicata.
La tecnologia CTC si trova all'incrocio tra "innovazione dirompente" e "trappola della produzione di massa". Potrebbe non sostituire completamente la tecnologia esistente, ma sta costringendo il processo di saldatura a evolversi verso una maggiore precisione, una maggiore compatibilità e un controllo più intelligente. In questa maratona tecnologica, il vero vincitore potrebbe non essere la prima casa automobilistica, ma il team di ingegneri che trasforma le "saldature impossibili" in "interfacce standardizzate" sul lato della produzione.
Condivideremo regolarmente aggiornamenti e informazioni su tecniche di progettazione termica e alleggerimento, per la vostra consultazione. Grazie per l'interesse verso Walmate.
Poiché la tecnologia CTP (Cell to Pack) sovverte completamente la tradizionale struttura del pacco batteria, il "ruolo" del vassoio batteria è passato da supporto passivo del carico a integrazione attiva. La tecnologia di saldatura è diventata il fulcro della sicurezza e delle prestazioni. I requisiti di leggerezza (spessore della parete di soli 1,5 mm), sigillatura a pori zero e integrazione multi-materiale (alluminio/rame/fibra di carbonio) hanno fatto sì che la saldatura tradizionale cadesse nel dilemma della deformazione e dei difetti. Il settore sta facendo progressi attraverso l'innovazione dei materiali, l'ispezione intelligente della qualità e l'iterazione dei processi. Questo articolo analizzerà le sfide dirompenti che la CTP pone alla saldatura ed esplorerà il percorso tecnico verso elevata precisione e elevata affidabilità.
1-Analisi delle modifiche nei requisiti di progettazione strutturale dei vassoi batteria dovuti alla tecnologia CTP
La tecnologia CTP (Cell to Pack) integra direttamente le celle della batteria nel pacco batteria eliminando la struttura del modulo nel pacco batteria tradizionale. Questa innovazione tecnologica propone requisiti di aggiornamento completi e multidimensionali per la progettazione strutturale del vassoio batteria. Di seguito è riportata un'analisi specifica dal punto di vista dei materiali, delle prestazioni, del processo, dell'integrazione, ecc.:
(1) Miglioramento completo della resistenza strutturale e delle prestazioni antiurto
a. Requisiti di cuscinetto meccanico dopo l'eliminazione del modulo:
Dopo che la tecnologia CTP elimina la struttura del modulo, il vassoio batteria deve supportare direttamente le funzioni di supporto, fissaggio e buffering della forza esterna della cella della batteria. Il modulo tradizionale disperde il carico meccanico, mentre il vassoio CTP deve assorbire la deformazione di espansione della cella della batteria durante la carica e la scarica nel suo complesso (ad esempio, la forza di espansione della cella della batteria quadrata può raggiungere 10-20 kN), resistendo al contempo alle vibrazioni, all'estrusione e al carico d'impatto durante la guida del veicolo.
b. Direzione di ottimizzazione strutturale e dei materiali
· Dominanza della lega di alluminio ad alta resistenza: l'acciaio iniziale è stato gradualmente sostituito a causa del suo peso elevato e il 6061-T6 è diventato il mainstream. Ha un'elevata resistenza specifica e una forte resistenza alla corrosione, che può soddisfare i doppi requisiti di leggerezza e alta rigidità.
· Progettazione della struttura composita: ad esempio, la struttura "a trave ad anello a doppio telaio" di Leapmotor migliora la resistenza all'impatto locale attraverso compartimenti trave longitudinali e trasversali, utilizzando al contempo la tecnologia di estrusione per ottimizzare la distribuzione del materiale e ridurre il peso ridondante.
· Esplorazione della lega di magnesio-alluminio e della fibra di carbonio: la lega di magnesio-alluminio è più leggera del 30% rispetto ai tradizionali materiali in alluminio e i materiali compositi in fibra di carbonio hanno caratteristiche sia di elevata resistenza che di leggerezza, ma sono attualmente utilizzati solo nei modelli di fascia alta a causa dei costi e della maturità del processo.
(2) Requisiti per la tenuta all'aria integrata e la gestione termica
a. Miglioramento delle prestazioni di tenuta
Dopo la rimozione del modulo, la circolazione interna del refrigerante e la tenuta del gas del pacco batteria dipendono completamente dal vassoio e i difetti di saldatura (come pori e crepe) possono comportare rischi di perdite.
Figura 1-Test di tenuta all'aria del vassoio della batteria
b. Integrazione delle funzioni di gestione termica
I vassoi CTP devono integrare componenti quali piastre di raffreddamento a liquido e adesivi termoconduttivi. Ad esempio, gli adesivi strutturali vengono utilizzati per fissare le celle della batteria e trasferire lo stress di espansione, mentre gli adesivi termoconduttivi in poliuretano (conduttività termica > 1,5 W/m·K) vengono utilizzati per la conduzione del calore tra le celle della batteria e con i tubi di raffreddamento a liquido. La quantità di adesivo utilizzata in un singolo PACK è superiore di oltre il 50% rispetto a quella delle strutture tradizionali. I canali di flusso devono essere progettati all'interno del vassoio per ottimizzare l'efficienza di raffreddamento evitando al contempo danni alla tenuta causati dalla zona di saldatura interessata dal calore.
(3) Alleggerimento e innovazione dei materiali
a. Tendenze nella selezione dei materiali
Processo di estrusione e pressofusione di leghe di alluminio: i profili in alluminio estruso vengono utilizzati per le strutture del telaio (come il vassoio della batteria 4680 di Tesla) e i processi di pressofusione (come la pressofusione integrata) semplificano il processo di saldatura e riducono il peso del 15%-20%.
Applicazione di materiali compositi in plastica: ad esempio, i materiali PA6 rinforzati con fibra di vetro vengono utilizzati in parti non portanti per ridurre ulteriormente il peso, ma è necessario risolvere il problema di compatibilità con l'interfaccia di collegamento in metallo.
b. Strategia di progettazione leggera
Ottimizzazione della topologia: ridurre i materiali ridondanti tramite simulazione CAE e ridurre il peso del vassoio garantendo al contempo la resistenza.
Parete sottile e integrata: lo spessore della parete del vassoio è ridotto da 3 mm a 1,5-2 mm e componenti funzionali come staffe BMS e canali di cablaggio sono integrati per ridurre il numero di parti.
(4) Integrazione e progettazione modulare
a. Elevata integrazione dei componenti funzionali
I vassoi CTP devono integrare moduli come il sistema di gestione della batteria (BMS), connettori ad alta tensione e strati di isolamento ignifughi.
b. Progettazione modulare e compatibile
La linea di produzione di saldatura deve supportare la produzione mista di più modelli di vassoi, essere in grado di ottenere un "cambio di tipo con un clic" ed essere compatibile con strutture di vassoi di diverse dimensioni di celle della batteria (come quadrate e cilindriche).
2-Sfide specifiche dell'innovazione della tecnologia CTP per il processo di saldatura
La tecnologia CTP (Cell to Pack) ha migliorato significativamente l'utilizzo dello spazio e la densità energetica, ma ha anche posto sfide senza precedenti al processo di saldatura.
(1) La difficoltà di controllare i difetti di saldatura è aumentata drasticamente
a. Porosità e sfide di sigillatura
Dopo che la tecnologia CTP elimina il modulo, il vassoio della batteria deve assumere direttamente la funzione di sigillatura. I pori di saldatura (un difetto comune nella saldatura delle leghe di alluminio) porteranno direttamente al rischio di perdite di refrigerante o penetrazione di gas.
b. Crepe e compatibilità dei materiali
Le leghe di alluminio ad alto tenore di zinco (come la serie 7) sono soggette a crepe dovute allo stress termico durante la saldatura.
c. Errore di spazio e di assemblaggio
L'integrazione diretta di più celle porta a un aumento del numero di punti di giunzione della struttura del vassoio. L'accumulo di errori di assemblaggio può causare uno spazio di saldatura superiore a ±1 mm.
(2) Problemi di adattamento del processo causati dall'aggiornamento del sistema di materiali
a. Sfide di saldatura di materiali leggeri
Il materiale del vassoio CTP è passato dall'acciaio alla lega di alluminio (6061-T6, 7075-T6), lega di magnesio-alluminio (riduzione del peso del 30%) e materiali compositi in fibra di carbonio. La saldatura della lega di alluminio deve risolvere il problema della penetrazione insufficiente causata dalla difficile fusione del film di ossido e dall'elevata conduttività termica.
b. Tecnologia di collegamento di materiali dissimili
Quando il vassoio integra componenti funzionali come la piastra di raffreddamento a liquido (rame/alluminio) e lo strato ignifugo (materiale composito a matrice ceramica), i composti intermetallici fragili tendono a comparire all'interfaccia di materiali dissimili.
(3) Complessità strutturale migliorata e requisiti di precisione
a. Controllo della deformazione di strutture a parete sottile di grandi dimensioni
Lo spessore della parete del vassoio CTP è ridotto da 3 mm a 1,5-2 mm e la sensibilità della deformazione termica della saldatura aumenta notevolmente.
b. Giunti di saldatura ad alta densità ed efficienza di processo
Il numero di giunti di saldatura su un singolo vassoio è aumentato da 2.000 nei moduli tradizionali a oltre 5.000.
Figura 2- Saldatura del vassoio della batteria
3-Aggiornamento del processo di produzione e del controllo di qualità
La tecnologia CTP promuove la trasformazione della saldatura del vassoio della batteria da "processo singolo" a "collaborazione multi-tecnologica, intelligenza e greening". I produttori devono concentrarsi su tre direzioni principali:
Aggiornamento tecnologico: superare il controllo di difetti come pori e crepe e adattarsi a materiali leggeri;
Transizione intelligente: digitalizzazione completa del processo e ispezione di qualità AI per ottenere una produzione ad alta precisione;
Collaborazione ecologica: creare congiuntamente standard tecnici con fornitori di materiali, fornitori di apparecchiature e OEM.
Condivideremo regolarmente aggiornamenti e informazioni su tecniche di progettazione termica e alleggerimento, per la vostra consultazione. Grazie per l'interesse verso Walmate.
Materiali leggeri come le leghe di alluminio sono diventati mainstream grazie alle loro prestazioni superiori. Tuttavia, sfide come il controllo dell'apporto di calore, la soppressione della deformazione e la stabilità del processo nella saldatura a lamiere sottili pongono ostacoli significativi per le tecnologie di saldatura tradizionali. La saldatura Cold Metal Transfer (CMT), con i suoi vantaggi di basso apporto di calore, trasferimento senza spruzzi e controllo intelligente dei parametri, offre una soluzione innovativa per la produzione di vassoi per batterie.
Questo articolo approfondisce le strategie di controllo di precisione della tecnologia CMT nella saldatura a lamiere sottili per vassoi per batterie, analizzandone l'adattabilità, le sfide del processo e gli scenari applicativi compositi, con l'obiettivo di fornire una guida teorica e pratica per una produzione efficiente e di alta qualità.
Figura 1: Saldatura CMT dell'involucro inferiore di raffreddamento a liquido della batteria di accumulo di energia 104S
1-Requisiti di saldatura del vassoio batteria e adattabilità CMT
La tecnologia CMT, con il suo basso apporto di calore, il trasferimento senza spruzzi e il controllo intelligente dei parametri, si allinea perfettamente con le esigenze di alta precisione, bassa deformazione ed efficienza della saldatura del vassoio batteria.
(1) Requisiti del processo principale per la saldatura del vassoio batteria
a. Compatibilità dei materiali ed esigenze di alleggerimento
I vassoi batteria utilizzano principalmente leghe di alluminio leggere (ad esempio, serie 6xxx, 6061) o compositi in fibra di carbonio per modelli di fascia alta, che richiedono elevata resistenza (resistenza alla trazione del materiale di base 60%-70%) e bassa densità (lega di alluminio: 2,7 g/cm³).
Giunzione di materiali dissimili: per strutture ibride acciaio-alluminio, è necessario tenere conto delle differenze del coefficiente di dilatazione termica per ridurre al minimo la deformazione.
b. Qualità della saldatura e parametri delle prestazioni
Basso apporto di calore e controllo della deformazione: per piastre sottili (0,3-3 mm), la deformazione deve essere ≤2 mm. Le saldature lineari lunghe richiedono una saldatura segmentata o un design anti-deformazione.
Sigillatura e resistenza: le saldature devono essere completamente sigillate per evitare perdite di elettrolita e superare i test di taglio (ad esempio, standard T/CWAN 0027-2022).
Controllo della porosità: la saldatura della lega di alluminio è soggetta a porosità, richiedendo un tasso di porosità ≤0,5%.
c. Efficienza di produzione e requisiti di automazione
La produzione in lotti richiede una velocità di saldatura ≥7 mm/s, riducendo il tempo di saldatura a vassoio singolo a 5-10 minuti.
Le postazioni di lavoro automatizzate devono supportare la progettazione a doppia stazione (assemblaggio e saldatura simultanei) e la collaborazione multi-robot.
(2)Vantaggi principali della CMT per la saldatura dei vassoi delle batterie
a. Controllo preciso dell'apporto di calore ridotto
La CMT riduce l'apporto di calore del 33% rispetto alla saldatura MIG tradizionale, ritraendo il filo di saldatura per interrompere la corrente durante il cortocircuito delle gocce, eliminando i rischi di bruciatura per le piastre ultrasottili (0,3 mm).
I cicli alternati freddo-caldo (riscaldamento dell'arco-trasferimento delle gocce-ritrazione del filo) riducono al minimo l'accumulo di calore, controllando la deformazione a ≤1,5 mm (studi di casi BYD e BAIC).
b. Stabilità del processo e miglioramento della qualità
Saldatura senza spruzzi: la ritrazione meccanica elimina gli spruzzi delle gocce, riducendo le rilavorazioni.
Ottimizzazione della porosità: l'utilizzo del gas di protezione Ar+30%He riduce la porosità del 50% rispetto all'Ar puro, con dimensioni dei pori ≤0,3 mm.
Elevata tolleranza degli spazi: si adatta a spazi di assemblaggio fino a 1,5 mm, riducendo i requisiti di precisione dell'attrezzatura.
c. Integrazione dell'automazione e guadagni di efficienza
Le postazioni di lavoro a doppia stazione (ad esempio, progetti Taixiang Tech) consentono la saldatura e l'assemblaggio paralleli, raddoppiando l'efficienza.
La saldatura robotizzata simmetrica (sincronizzazione a doppio robot) con design anti-deformazione riduce il tempo di ciclo a ≤10 minuti.
2-Sfide nel processo CMT per i vassoi delle batterie
Figura 2: Flusso del processo di saldatura CMT
(1)Proprietà dei materiali e controllo dei difetti di saldatura
a. Sensibilità alla porosità nella saldatura delle leghe di alluminio
I vassoi in lega di alluminio (ad esempio, 6061, 6063) sono inclini alla porosità a causa della rapida solidificazione e dei cambiamenti di solubilità dell'idrogeno. La composizione del gas di protezione è fondamentale: Ar puro determina una porosità di circa il 5%, mentre Ar+30%He riduce la porosità a ≤0,5%. La regolazione dell'induttanza (ad esempio, messa a punto negativa) ottimizza il flusso del bagno fuso, riducendo al minimo le dimensioni dei pori.
b. Cracking a caldo e segregazione della composizione
La segregazione di Mg, Si, ecc. nelle leghe di alluminio può causare fragilità del bordo dei grani. Mentre il basso apporto di calore del CMT riduce la ZTA, è necessario un controllo preciso della velocità di saldatura e dell'alimentazione del filo per evitare una penetrazione insufficiente o un surriscaldamento localizzato.
c. Compatibilità metallurgica nella saldatura di materiali dissimili
Le interfacce nei giunti Al-acciaio o Al-composito (ad esempio, travi di sicurezza e involucri) devono mitigare le fasi fragili (ad esempio, FeAl₃) e l'interferenza del vapore di Zn.
(2)Sfide di ottimizzazione dei parametri di processo
a. Bilanciamento di penetrazione e apporto di calore
Le saldature devono soddisfare gli standard T/CWAN 0027 per la profondità di penetrazione (≥0,8 mm). Il basso apporto di calore del CMT può portare a una penetrazione insufficiente, richiedendo una regolazione della lunghezza dell'arco o una corrente pulsata per migliorare la penetrazione.
b. Compromesso tra velocità e stabilità
Le linee automatizzate richiedono velocità ≥1,2 m/min, ma velocità elevate rischiano l'instabilità dell'arco o un trasferimento irregolare delle gocce.
c. Gap Bridging in saldature complesse
I vassoi spesso presentano ampi spazi (0,5-1,5 mm) o giunti irregolari (ad esempio, giunti a T).
(3) Compatibilità tra progettazione strutturale e processo di fabbricazione
a. Controllo della deformazione della saldatura a piastra sottile
Lo spessore della parete dei pallet in lega di alluminio è solitamente di 2-3 mm. La deformazione della saldatura MAG tradizionale può raggiungere 1,2 mm, mentre la saldatura CMT può ridurre la deformazione a meno di 0,3 mm attraverso un basso apporto di calore. Tuttavia, è necessario collaborare con la progettazione di utensili antideformazione e la saldatura simmetrica robotizzata (postazione di lavoro a doppia stazione) per migliorare ulteriormente la precisione.
b. Continuità e sigillatura di saldature lunghe
La lunghezza della saldatura sigillata del vassoio della batteria può raggiungere diversi metri e devono essere evitate la rottura dell'arco o le fluttuazioni del bagno fuso. La tecnologia CMT garantisce l'uniformità della saldatura attraverso oltre 70 cicli di riaccensione dell'arco al secondo e il tasso di qualificazione della tenuta stagna può essere aumentato al 99% con il sistema di tracciamento laser.
c. Sinergia di applicazioni composite multi-processo
I pallet di fascia alta utilizzano spesso il processo composito CMT+FSW (saldatura a frizione): il CMT viene utilizzato per strutture complesse (come la connessione tra il telaio e la piastra inferiore). Il FSW viene utilizzato in aree ad alto carico (come le travi longitudinali) per migliorare la resistenza. Il problema di corrispondenza dei parametri di connessione dei due processi (come la temperatura di preriscaldamento e il trattamento termico post-saldatura) deve essere risolto.
3-Scenari applicativi tipici del processo CMT nella produzione di vassoi per batterie
(1) Collegamento della struttura principale del vassoio per batterie
a. Saldatura del telaio e della piastra inferiore
Il processo CMT è ampiamente utilizzato nel collegamento tra il telaio e la piastra inferiore dei vassoi per batterie in lega di alluminio, in particolare per saldature lunghe e piastre sottili (spessore 2-3 mm)
b. Collegamento tra trave e piastra inferiore
Nella progettazione dei vassoi per batterie CTP, a causa del numero ridotto di travi e della struttura complessa, il processo CMT viene utilizzato per: Saldatura di posizionamento ad alta precisione: il collegamento locale tra la trave e la piastra inferiore (come il giunto a T) deve evitare una penetrazione insufficiente. CMT raggiunge una penetrazione stabile ≥ 0,8 mm tramite il controllo digitale della lunghezza dell'arco (come la tecnologia Fonis CMT Advanced). Adattamento multi-materiale: se la trave è realizzata in lega di alluminio-magnesio (ad esempio 6061) e la piastra inferiore è in alluminio ad alta resistenza, la CMT può ridurre i pori tramite la protezione con gas misto Ar+He, adattandosi al contempo alle differenze di conduttività termica dei diversi materiali.
(2) Saldatura di piastre sottili e strutture geometriche complesse
a. Saldatura di leghe di alluminio a parete sottile (2-3 mm)
La richiesta di leggerezza per i vassoi batteria promuove l'applicazione di piastre sottili, ma la saldatura MIG tradizionale è soggetta a deformazione. I vantaggi del processo CMT sono:
b. Saldatura di piastre ultrasottili: Taixiang Automation utilizza la tecnologia CMT per ottenere una saldatura senza spruzzi di piastre ultrasottili da 0,3 mm per le strutture di sigillatura dei bordi del vassoio batteria.
c. Bridging di saldature di forma speciale: per strutture di forma speciale come nervature di rinforzo interne e travi anticollisione del vassoio, la modalità CMT Gap Bridging può riempire lo spazio di 0,5-1,5 mm tramite la retrazione del filo e il reindirizzamento dell'arco per evitare difetti non fusi.
d. Saldature con elevati requisiti di tenuta: la sigillatura del vassoio batteria è direttamente correlata alla sicurezza della batteria. Il processo CMT lo garantisce nei seguenti modi:
· Saldature lunghe continue: utilizzando più di 70 cicli di riaccensione dell'arco al secondo (come la tecnologia Fronius LaserHybrid) per garantire la continuità di diversi metri di saldature, con un tasso di passaggio ermetico del 99%.
· Controllo del basso apporto di calore: rispetto alla saldatura laser, la CMT ha un apporto di calore inferiore, il che riduce l'impatto termico delle fluttuazioni del bagno fuso sullo strato sigillante ed è adatta al processo di rivestimento con colla.
(3) Scenario di produzione di compositi multiprocesso
a. Processo composito CMT+FSW
Nelle linee di produzione di vassoi per batterie di fascia alta, CMT è spesso coordinato con la saldatura a frizione e agitazione (FSW):
Divisione del lavoro e cooperazione: CMT è utilizzato per la saldatura flessibile di strutture complesse (come telai e giunti di forma speciale) e FSW è utilizzato per aree ad alto carico (come travi longitudinali) per migliorare la resistenza. Ad esempio, la linea di produzione automatizzata di Shanghai Weisheng utilizza una combinazione di CMT+FSW+CNC per aumentare l'efficienza di produzione del vassoio del 30%.
Ottimizzazione della connessione di processo: la linea di produzione di Huashu Jinming adotta un design modulare e ottiene una connessione senza soluzione di continuità con FSW tramite la corrispondenza dei parametri di preriscaldamento (come il riscaldamento locale a 150 °C dopo la saldatura CMT).
b. In combinazione con la tecnologia di rivettatura FDS/SPR
Nella tecnologia CTP di seconda generazione, CMT è coordinata con la tecnologia di autoserraggio a frizione (FDS) e di rivettatura autoperforante (SPR): Soluzione di connessione ibrida: ad esempio, l'area portante del telaio e la piastra inferiore adottano FSW, mentre le parti staccabili (come piastre di raffreddamento ad acqua e strati isolanti) sono preposizionate dalla saldatura CMT e quindi fissate dalla rivettatura FDS, tenendo conto sia della resistenza che della praticità di manutenzione.
Condivideremo regolarmente aggiornamenti e informazioni su tecniche di progettazione termica e alleggerimento, per la vostra consultazione. Grazie per l'interesse verso Walmate.
Come ingegnere operativo in una fabbrica di produzione di vassoi per batterie, ho partecipato a numerosi progetti per involucri di batterie di veicoli elettrici, sperimentando direttamente il delicato equilibrio tra "leggerezza, sicurezza e costo" nel settore. Questo articolo analizzerà la logica di selezione delle attuali tecnologie e le sfide industriali, suddividendo l’analisi in tre dimensioni: materiali, processi produttivi e tendenze future, con esempi pratici.
1-Percorso dei materiali: Bilanciamento tra leggerezza e costo
La scelta dei materiali per l’involucro della batteria influisce direttamente sulle prestazioni del veicolo e sull’economicità. Le principali opzioni attuali sono leghe di alluminio, acciai ad alta resistenza e materiali compositi, ciascuno con scenari applicativi specifici.
a. Leghe di alluminio: Il pilastro della leggerezza
Profilati in alluminio estruso: Modelli BYD utilizzano profilati estrusi, ottimizzando la forma della sezione per ridurre il peso e aumentare la rigidità strutturale.
Pressofusione integrata: La batteria Tesla 4680 con tecnologia CTC riduce il peso del 50%, ma richiede costi di stampaggio superiori a 200 milioni di RMB, ammortizzabili solo con produzioni annue oltre 500.000 unità, adatto a grandi produttori.
Materiali compositi in alluminio: La Porsche Taycan usa una struttura mista alluminio-fibra di carbonio, riducendo il peso del 15%, ma con un costo incrementale del 30%, limitato ai modelli premium.
b. Acciai ad alta resistenza: La soluzione per mercati sensibili al costo
L’acciaio termoformativo (es. 22MnB5) raggiunge una resistenza a snervamento di 1500 MPa, con una penetrazione del 40% nei veicoli commerciali. Il costo per GWh è inferiore del 40% rispetto all’alluminio, ma la densità energetica si riduce dell’8%. Ideale per modelli sotto i 100.000 RMB, bilanciando costo e sicurezza base.
c. Materiali compositi: Sperimentazioni nel segmento premium
SMC (Sheet Molding Compound): Il guscio superiore della batteria in vetroresina riduce il peso del 30% rispetto all’acciaio, ma richiede spessori maggiori (3mm + rinforzi da 5mm) per compensare la resistenza agli urti.
Fibra di carbonio: L’involucro della BMW i3 è del 50% più leggero dell’alluminio, ma il costo raggiunge 800 RMB/kg, rendendolo adatto solo a modelli di lusso.
Sintesi pratica: La scelta del materiale deve allinearsi al posizionamento del veicolo. Il mercato mid-range (200.000-300.000 RMB) privilegia l’alluminio, quello entry-level l’acciaio, mentre i modelli premium esplorano soluzioni composite.
2-Processi produttivi: Equilibrio tra efficienza e affidabilità
I processi di produzione influenzano direttamente efficienza e affidabilità. Le principali tecnologie includono pressofusione, saldatura di profilati e integrazione strutturale.
a. Pressofusione VS saldatura di profilati
Profilati in alluminio estruso (es. Chevrolet Bolt): Costo unitario ~800 RMB, adatto a grandi volumi, ma processi complessi.
Pressofusione in alluminio (es. NIO ET5): Costo unitario 1500 RMB, ma efficienza produttiva quintuplicata, ideale per produzioni rapide.
Saldatura a attrito (FSW): Riduzione del 50% delle deformazioni rispetto alla saldatura ad arco, con resistenza a fatica migliorata del 30%, ma richiede un investimento in macchinari superiore del 40%, adatto a veicoli commerciali.
b. Tecnologie di integrazione strutturale
CTP (Cell to Pack) - Batteria CATL Qilin: L’utilizzo dello spazio passa dal 72% all’85%, con riduzione dei costi del 15-20%, ma richiede miglioramenti nella protezione termica.
CTC (Cell to Chassis) - Tesla Model Y: Riduzione di 370 componenti, autonomia +54%, ma costi di riparazione +300%, sfidando i sistemi post-vendita.
Confronto dei dati chiave
Esperienza nella linea di produzione: la tecnologia CTP è ancora quella più diffusa grazie alla sua elevata compatibilità; la tecnologia CTC invece richiede una collaborazione approfondita tra le case automobilistiche e i produttori di batterie ed è improbabile che venga diffusa nel breve termine.
3-Tendenze future: Fusione tecnologica e innovazione intelligente
a. Materiali ibridi
Strutture miste alluminio-fibra di carbonio (es. concept Porsche Taycan) riducono il peso del 15% con resistenza a compressione di 800 MPa, ma la stabilità del processo è critica (es. Toyota bZ4X ha una resa del 65%).
b. Integrazione funzionale
Piastre di raffreddamento integrate (es. batteria "Magazine" di GAC): Superficie di contatto +50%, controllo della temperatura entro ±5°C, ma richiede ottimizzazione della saldatura laser per ridurre la porosità.
Sensori a fibra ottica (Continental): Monitoraggio in tempo reale di deformazioni e temperatura, con tempi di risposta BMS +30%, ma necessità di migliorare la durata dei sensori.
c. Sostenibilità e riciclo
La tecnologia BMW di riciclo in ciclo chiuso riduce le emissioni del 60%, ma la perdita di prestazioni dei materiali riciclati deve rimanere sotto il 10%. La pressofusione di grandi componenti (es. pressa da 9000T di LK) richiede controllo termico preciso (±5°C), con la rimozione delle sbavature come collo di bottiglia.
Direzioni di innovazione:
Riduzione del ciclo di formatura dei compositi (es. LGF-PP da 180 a 90 secondi).
Applicazione di gemelli digitali per ridurre l’errore di simulazione da ±20% a ±5%, migliorando l’affidabilità progettuale.
4-Stratificazione del mercato e prospettive
Breve termine (1-3 anni): CTP + profilati in alluminio restano dominanti, con CATL leader (34% di quota).
Medio termine (5-10 anni): CTC e fibra di carbonio accelerano nel premium, raggiungendo il 25% di quota entro il 2030.
Lungo termine: Densità energetica verso 400 Wh/kg, miglioramento della sicurezza oltre gli standard attuali (30 minuti di protezione termica).
5-Conclusione
La scelta del percorso tecnologico per gli involucri delle batterie è una questione di "adattamento allo scenario", bilanciando posizionamento del produttore, soglie di costo e maturità della supply chain. Come ingegneri, dobbiamo abbracciare l’innovazione mantenendo la fattibilità industriale, cercando l’equilibrio dinamico tra leggerezza, sicurezza e costo. Con l’avanzamento di tecnologie intelligenti e sostenibili, gli involucri evolveranno da "protezione passiva" a "sicurezza attiva", supportando la diffusione globale dei veicoli elettrici.
Condivideremo regolarmente aggiornamenti e informazioni su tecniche di progettazione termica e alleggerimento, per la vostra consultazione. Grazie per l'interesse verso Walmate.
Nel processo effettivo di produzione, assemblaggio e utilizzo, si verifica spesso il guasto della tensione di tenuta dell'isolamento dei vassoi batteria, come una barriera corallina nascosta nel rapido sviluppo della nuova industria energetica, che minaccia la sicurezza di guida dei veicoli e il funzionamento affidabile del sistema di accumulo di energia. Questo articolo tenta di analizzare le tipiche modalità di guasto basate sulla pratica di produzione, al fine di fornire alcuni riferimenti superficiali per i professionisti interessati e aiutare i colleghi del settore a esplorare congiuntamente modi efficaci per migliorare le prestazioni della tensione di tenuta dell'isolamento dei vassoi batteria.
Parte 3 - Analisi dei guasti comuni
Figura 1 Prova di tensione di tenuta all'isolamento
1- Analisi dei meccanismi di guasto comuni
Gli scenari applicativi dei vassoi batteria per l'accumulo di energia e dei nuovi veicoli energetici sono diversi, con conseguenti somiglianze e differenze nei requisiti di tensione di tenuta dell'isolamento e nelle condizioni di guasto, come segue:
a. Differenze
Carico dinamico: i nuovi veicoli energetici devono gestire vibrazioni meccaniche ad alta frequenza di 20-2000 Hz, mentre i sistemi di accumulo di energia affrontano principalmente deformazioni statiche a lungo termine, con un tempo di deformazione cumulativo superiore a 10 anni.
Livello di tensione: la tensione di tenuta dell'isolamento dei vassoi batteria dei nuovi veicoli energetici deve raggiungere 3000 V CC e oltre (in base a GB 38031), mentre i sistemi di accumulo di energia richiedono una tensione di tenuta dell'isolamento di 4200 V CA e oltre (in base a IEC 61439).
Fattore di accelerazione del guasto: i nuovi veicoli energetici generano stress termico a causa di oltre 2000 cicli di carica e scarica all'anno, il che accelera il guasto dell'isolamento; i sistemi di accumulo di energia funzionano 24 ore su 24, 7 giorni su 7, con un tempo di funzionamento annuo medio di oltre 8000 ore, con conseguente invecchiamento elettrochimico, che a sua volta accelera il guasto dell'isolamento.
b. Punti comuni
Entrambi devono ottenere un avviso tempestivo del guasto dell'isolamento tramite il monitoraggio della resistenza di isolamento (non inferiore a 100 MΩ a freddo e non inferiore a 1 MΩ/kV a caldo) e il controllo della scarica parziale (inferiore a 5 pC).
2- Comuni difetti di fabbricazione che causano guasti alla tensione di tenuta dell'isolamento dei vassoi batteria
(1) Fase di costruzione della tensione di tenuta dell'isolamento
a. Potenziale guasto e analisi delle cause
· Difetti dei materiali:
Causa: il livello di tensione di tenuta del materiale isolante è insufficiente, invecchiamento dovuto a umidità o contaminazione superficiale (macchie di olio, detriti metallici).
Prestazioni: bassa resistenza di isolamento (<100 MΩ), corrente di dispersione superiore allo standard o guasto diretto durante il test di tensione di tenuta.
· Problemi di processo:
Causa: detriti metallici residui (processo di saldatura/taglio approssimativo), spessore irregolare del rivestimento isolante o non polimerizzato.
Prestazioni: scarica parziale, danni allo strato isolante causano cortocircuito.
· Interferenza ambientale:
Causa: alte temperature e alta umidità causano assorbimento di umidità nel materiale e corrosione chimica.
Prestazioni: le prestazioni di isolamento si deteriorano con l'ambiente e l'acqua di condensa causa dispersione. · Errori di prova:
Causa: impostazione errata della tensione/tempo di prova (ad esempio non conforme allo standard GB/T 38661), messa a terra scadente.
Prestazioni: valutazione errata di danni da sovratensione o qualificazione dei componenti.
b. Strategia di risposta
· Ottimizzazione dei materiali: selezionare materiali a prova di umidità (come materiali compositi in fibra di carbonio) con una tensione di tenuta di ≥1000 V CC e applicare un rivestimento anti-incrostazione.
· Controllo del processo: utilizzare apparecchiature di saldatura/spruzzatura automatizzate e allestire un'officina pulita.
· Gestione ambientale: installare il monitoraggio della temperatura e dell'umidità e pre-essiccare i materiali prima della costruzione.
· Specifiche del test: test segmentati (pre-test 500 V + test formale 1000 V), calibrare gli strumenti e registrare i dati.
(2) Fase di installazione del modulo
a. Analisi di potenziali guasti e cause
· Errore di assemblaggio:
Causa: il rivestimento isolante è mancante e i bulloni sono troppo stretti e lo strato isolante è danneggiato.
Prestazioni: bassa resistenza di isolamento tra il modulo e il guscio e resistenza alla rottura della tensione.
· Danni meccanici
Causa: graffi sugli utensili di movimentazione, detriti metallici che perforano la pellicola isolante.
Prestazioni: cortocircuito locale o guasto improvviso durante il funzionamento.
· Compatibilità di progettazione
Causa: spazio elettrico insufficiente a causa della deviazione delle dimensioni tra il modulo e il vassoio.
Prestazioni: la capacità parassita causa la rottura della sovrapposizione di tensione.
· Pericoli di collegamento elettrico:
Causa: usura e rottura della guarnizione del connettore a causa del cablaggio non fissato.
Prestazioni: usura e perdita dello strato isolante del cablaggio ad alta tensione.
b. Contromisure
· Progettazione a prova di errore: utilizzare utensili con perni di posizionamento per evitare installazioni mancanti e personalizzare la lunghezza del bullone per evitare un serraggio eccessivo.
· Funzionamento pulito: pulire con l'aspirapolvere prima dell'installazione e avvolgere gli utensili con silicone antigraffio.
· Simulazione di tolleranza: verificare il grado di corrispondenza tra il modulo e il vassoio tramite CAE per garantire che lo spazio sia ≥10 mm.
· Ispezione del processo: dopo l'installazione, eseguire un'ispezione casuale con un megaohmetro (≥100 MΩ) ed eseguire un test di tensione di tenuta segmentato per individuare il punto di guasto.
(3) Fase di integrazione del sistema
a. Analisi di potenziali guasti e cause
· Guasto dell'interfaccia tra sistemi:
Causa: i parametri di isolamento dei componenti non corrispondono (ad esempio differenze nella classificazione della tensione di tenuta del connettore).
Prestazioni: rottura della connessione della barra di distribuzione ad alta tensione o interferenza BMS.
· Sovrapposizione di capacità parassita:
Causa: la capacità parassita totale aumenta dopo che più moduli sono collegati in parallelo e l'effetto di aumento della capacità è significativo.
Prestazioni: la corrente di dispersione del test a livello di sistema supera lo standard.
· Guasto da stress ambientale:
Causa: le vibrazioni causano affaticamento dell'isolamento e il refrigerante si infiltra nell'interfaccia ad alta tensione.
Prestazioni: la resistenza dell'isolamento diminuisce periodicamente durante il funzionamento.
· Punto cieco del test:
Causa: mancata simulazione delle condizioni di lavoro reali (alta temperatura/vibrazione/umidità).
Prestazioni: superato in laboratorio ma non superato nel funzionamento effettivo.
b. Contromisure
· Progettazione della compatibilità: unificare gli standard dei componenti del fornitore. · Controllo della capacità parassita: aggiungi uno strato di isolamento in poliimmide e ottimizza il layout tramite simulazione SPICE.
· Test di simulazione delle condizioni di lavoro: esegui il test composito "ciclo -40℃~85℃ + vibrazione 5Hz~200Hz + tensione di tenuta".
· Monitoraggio intelligente: modulo di monitoraggio dell'isolamento online integrato, l'intelligenza artificiale prevede potenziali rischi.
3-Test di tensione di tenuta all'isolamento
Il test di tensione di tenuta all'isolamento è sia una misura di sicurezza che una possibile causa di guasto. Il test di tensione di tenuta all'isolamento stesso può causare guasti dovuti a funzionamento improprio, problemi all'apparecchiatura o difetti di progettazione e persino causare danni secondari al dispositivo sottoposto a test.
(1) Tipi comuni di guasto durante il test
(2) Le strategie di risposta sono le seguenti:
a. Controllo preciso dei parametri di prova
· Tensione e tempo: impostati in base agli standard; abilita l'algoritmo di compensazione dinamica per carichi capacitivi (come i moduli batteria) per sopprimere l'effetto di aumento della capacità.
· Soglia di corrente di dispersione: impostata in base alle specifiche dell'apparecchiatura (come ≤10mA) e distingui tra modalità CC/CA (il test CC richiede una soglia inferiore).
b. Specifiche dell'apparecchiatura e del funzionamento
· Calibrazione dello strumento: il tester di tensione di tenuta viene calibrato ogni 6 mesi e lo strato di isolamento della linea ad alta tensione viene ispezionato visivamente ogni giorno.
· Funzionamento sicuro: disconnessione forzata dei circuiti a bassa tensione prima del test; utilizzare bracci robotici o dispositivi automatici per evitare il contatto manuale con aree ad alta tensione.
c. Prevenzione e riparazione dei guasti
· Test segmentati: testare sistemi complessi in moduli (come testare prima il bus ad alta tensione, quindi testare l'isolamento del modulo) per individuare il punto di guasto. · Riparazione guasti: utilizzare resina epossidica per riempire l'area danneggiata dopo il guasto e, dopo la riparazione, è necessario superare nuovamente il test del gradiente di tensione completo (ad esempio pressione a gradino 500 V→1000 V).
d. Gestione ambiente e dati
· Controllo ambientale: avviare il deumidificatore quando l'umidità nell'area di prova è superiore al 75% o ritardare il test fino a quando l'ambiente non soddisfa lo standard.
· Tracciabilità dei dati: registrare la tensione di prova, la curva della corrente di dispersione e i parametri ambientali e utilizzare il sistema MES per associare il numero del lotto di produzione.
Condivideremo regolarmente aggiornamenti e informazioni su tecniche di progettazione termica e alleggerimento, per la vostra consultazione. Grazie per l'interesse verso Walmate.
Il vassoio della batteria utilizza materiali isolanti principalmente per prevenire perdite di corrente, proteggere la sicurezza del personale e garantire il normale funzionamento del sistema della batteria. Nella selezione, è necessario considerare le proprietà isolanti del materiale, la resistenza al calore, la stabilità chimica e la resistenza meccanica. Questi fattori insieme determinano l'effetto dell'applicazione del materiale isolante nel vassoio della batteria, influenzando così la sicurezza e l'affidabilità dell'intero sistema della batteria.
Sicurezza dell'isolamento elettrico del vassoio batteria | Parte 2 - Garanzia delle prestazioni di resistenza alla pressione
Figura 1 Vassoio della batteria del veicolo elettrico
1-Selezione del materiale isolante e progettazione della soluzione
Nella selezione dei materiali isolanti per i vassoi batteria, l'attenzione è rivolta alle proprietà dielettriche, alla tolleranza ambientale e alle proprietà meccaniche dei materiali. Di seguito sono riportati 6 materiali isolanti comunemente utilizzati nei vassoi batteria e le relative informazioni:
Quando si progetta una soluzione, in genere è necessario considerare in modo completo i tre fattori chiave dello scenario applicativo, dei requisiti di prestazione e del budget dei costi per selezionare il materiale isolante appropriato. Ad esempio:
(1) Selezionare in base allo scenario applicativo: in un sistema di batterie di accumulo di energia ad alta tensione e alta corrente, se il lato del vassoio della batteria richiede materiale isolante ad alte prestazioni, si consiglia di utilizzare la soluzione di fissaggio del film PI; se i requisiti di prestazione dell'isolamento non sono elevati, è possibile selezionare la soluzione di spruzzatura di polvere isolante. Per la piastra inferiore del vassoio della batteria, se si cerca una soluzione di isolamento a basso costo, la soluzione di spruzzatura di polvere isolante o di rivestimento di vernice isolante è più adatta.
(2) Selezionare in base ai requisiti di prestazione: quando i requisiti di prestazione dell'isolamento, resistenza alle alte temperature, resistenza alla corrosione chimica, ecc. sono elevati, la soluzione di fissaggio del film PI è una scelta migliore; se questi requisiti di prestazione sono relativamente bassi, la soluzione di spruzzatura di polvere isolante o di rivestimento di vernice isolante può soddisfare le esigenze.
(3) Selezionare in base al budget dei costi: quando il budget dei costi è limitato, la soluzione di spruzzatura di polvere isolante o di rivestimento di vernice isolante è più economica; quando il budget di spesa è sufficiente, è possibile scegliere la soluzione di fissaggio della pellicola PI.
2-Requisiti tecnici per la pellicola PI per i vassoi delle batterie
(1) Materiale: PI, spessore della pellicola di base 0,1-0,14 mm, spessore adesivo posteriore 0,03 mm, conduttività termica della pellicola PI > 0,3 W/(m·k);
(2) Resistenza alla pressione: CA 3000 V, 60 S, corrente di dispersione ≤ 0,5 mA;
(3) (pasta fredda) resistenza alla pelatura a 180° ≥ 15 N/24 mm;
(4) Isolamento: CC 1500 V, 60 S, resistenza di isolamento > 1000 MΩ;
(5) Prestazioni di isolamento della resistenza al calore e all'elettrolita: a 500 ℃, tensione CC 700 V, aggiungere 2 ml di elettrolita (area di prova 13000 mm<H>2<H>), conservare per 1 ora, nessuna rottura e nessuna scintilla; (6) Prestazioni termiche e di isolamento: a 500±2℃, continuare la cottura (forno a muffola) per 0,5 ore, la morfologia complessiva del campione cambia senza combustione spontanea e il campione passa due volte. CA 1000 V viene applicata alla superficie e la tensione viene aumentata da 0 V a 3000 per 10 S, quindi continuata per 60 S. Il campione testato non presenta rotture e scintille;
(7) Grado ignifugo: UL94 V-0;
(8) Alta temperatura e alta umidità: dopo 1000 ore di test a 85℃ e 85% di umidità, il campione non presenta crepe e deformazioni, soddisfacendo lo standard nazionale "GBT 13542.6-2006 Pellicola isolante elettrica Parte 6: Pellicola in poliimmide per isolamento elettrico" sulla resistenza di isolamento, valore di tensione di tenuta e requisiti di resistenza elettrica. La resistenza alla trazione, l'allungamento a rottura e la resistenza alla pelatura sono ridotte di meno del 30% rispetto al materiale non invecchiato;
(9) Shock caldo e freddo: 85℃ per un'ora, commutato a -40℃ per un'ora, quindi commutato a 85℃ per cicli ad alta e bassa temperatura. Il tempo di commutazione è incluso in un'ora e il tempo di commutazione è ≤3min. Dopo 1000 ore di cicli ad alta e bassa temperatura, il campione non presenta crepe e deformazioni, soddisfacendo lo standard nazionale "GBT 13542.6-2006 Pellicola isolante elettrica Parte 6: Pellicola in poliimmide per isolamento elettrico" per resistenza di isolamento, valore di tensione di tenuta e requisiti di resistenza elettrica. La resistenza alla trazione, l'allungamento a rottura e la resistenza alla pelatura sono ridotte di meno del 30% rispetto al materiale non invecchiato. (10) Prova di nebbia salina: prova di nebbia salina neutra (NSS) secondo lo standard GB/T 10125, temperatura 35℃, umidità ≥85%RH, la soluzione di prova è (5±0,1%) (frazione di massa) NaCl, PH=6,5~7,2, spruzzatura continua per 72 ore. Dopo la prova di nebbia salina, il campione non presenta crepe né deformazioni, soddisfacendo lo standard nazionale "GBT 13542.6-2006 Pellicola isolante elettrica Parte 6: Pellicola in poliimmide per isolamento elettrico" per resistenza di isolamento, valore di tensione di tenuta e requisiti di resistenza elettrica. La resistenza alla trazione, l'allungamento a rottura e la resistenza alla pelatura sono ridotte di meno del 30% rispetto al materiale non invecchiato.
(11) Il prodotto è conforme a RoHS.
Figura 2 Pellicola PI per il vassoio della batteria
3-Metodi di prova della tensione di tenuta dell'isolamento e soluzioni ai problemi comuni
(1) Metodo di prova della tensione di tenuta dell'isolamento
La prova della tensione di tenuta dell'isolamento è un mezzo importante per valutare le prestazioni di isolamento delle apparecchiature elettriche, principalmente tra cui la prova della tensione di tenuta CC e la prova della tensione di tenuta CA. La prova della tensione di tenuta CC rileva se il materiale isolante si rompe entro un tempo specificato applicando alta tensione CC. L'apparecchiatura include un generatore di alta tensione CC, un voltmetro, ecc. I passaggi sono l'applicazione della tensione, il mantenimento della tensione e la riduzione della tensione. La prova della tensione di tenuta CA applica alta tensione CA. L'apparecchiatura e i passaggi sono simili alla prova CC. Entrambi i metodi richiedono una preparazione prima della prova per garantire che l'apparecchiatura sia ben messa a terra e che le condizioni della superficie del materiale isolante siano attentamente osservate durante la prova.
(2) Problemi comuni e soluzioni
I problemi comuni nella prova della tensione di tenuta dell'isolamento includono la rottura dell'isolamento, la corrente di dispersione eccessiva e il guasto dell'apparecchiatura di prova. La rottura dell'isolamento può essere causata da prestazioni insufficienti del materiale isolante, difetti interni o umidità. Le soluzioni includono la selezione di materiali di alta qualità, il rafforzamento della manutenzione e il miglioramento della struttura isolante. Una corrente di dispersione eccessiva può essere causata da una ridotta resistenza di isolamento, contaminazione superficiale o insufficiente accuratezza dell'apparecchiatura di prova. Le soluzioni includono il mantenimento del materiale isolante pulito e asciutto e la calibrazione dell'apparecchiatura di prova. Il guasto dell'apparecchiatura di prova può essere causato dall'invecchiamento dell'apparecchiatura, da una manutenzione impropria o da un funzionamento improprio. Le soluzioni includono una manutenzione regolare, un funzionamento corretto e una riparazione tempestiva.
Condivideremo regolarmente aggiornamenti e informazioni su tecniche di progettazione termica e alleggerimento, per la vostra consultazione. Grazie per l'interesse verso Walmate.
Con il rapido sviluppo dei veicoli a nuova energia e delle tecnologie di accumulo energetico, la sicurezza e l'affidabilità dei sistemi batteria, in qualità di vettori energetici centrali, hanno attirato grande attenzione. Come struttura di supporto e protezione del modulo batteria, le prestazioni di isolamento elettrico del vassoiobatteria sono direttamente collegate alla sicurezza operativa del veicolo, alla durata della batteria e all'incolumità degli utenti.La progettazione della sicurezza elettrica del vassoiobatteria costituisce la base della sicurezza del sistema batteria. Attraverso protezioni multilivello come isolamento, struttura, termica e monitoraggio, garantisce il funzionamento stabile della batteria in condizioni operative complesse, riduce i rischi di incendio, esplosione o folgorazione dovuti a guasti elettrici, prolungando la durata della batteria e migliorando l'affidabilità del sistema.
Questo articolo si concentra sulla sicurezza dell'isolamento elettrico dei vassoi delle batterie, spiegando sistematicamente i suoi principi di progettazione, il metodo di verifica delle prestazioni di resistenza alla pressione e l'analisi delle cause principali e le strategie di miglioramento dei casi di guasto tipici, al fine di fornire supporto teorico e riferimento pratico per la progettazione ad alta sicurezza dei sistemi di batterie.
Capitolo 1 Punti di progettazione
Il nucleo della progettazione della sicurezza elettrica del sistema batteria risiede nella trinità "prevenzione-controllo-emergenza": prevenire i guasti attraverso isolamento, connessioni affidabili e gestione termica; ottenere il controllo in tempo reale mediante sensori e BMS; utilizzare design antincendio e sfiato pressione per situazioni estreme. Tutti i punti chiave devono operare sinergicamente per garantire sicurezza e affidabilità del sistema batteria durante l'intero ciclo vitale, considerando anche manutenibilità e conformità normativa.Il vassoiobatteria non è solo un supporto strutturale nel sistema batteria, ma assolve molteplici funzioni tra cui isolamento elettrico, gestione termica, antiscivolo, protezione meccanica, messa a terra e design modulare, elementi cruciali per la sicurezza elettrica del sistema.
1-Il supporto strutturale garantisce l'affidabilità della connessione elettrica
Il vassoio della batteria garantisce l'affidabilità e la sicurezza dei collegamenti elettrici in condizioni di lavoro complesse fissando i moduli della batteria, riducendo le sollecitazioni meccaniche, resistendo a vibrazioni e urti, mantenendo l'allineamento e integrando protezione ambientale e gestione termica.
Figura 1 Vassoio batteria
A.Il supporto fisico e il fissaggio assicurano l'allineamento preciso dei punti di collegamento elettrico (come barre collettrici, cablaggi e connettori) per evitare un contatto scadente causato da deformazione o spostamento strutturale; forniscono un telaio rigido per fissare i moduli batteria e i connettori per evitare allentamenti o rotture causati da vibrazioni o urti.
B.Isolamento e protezione ambientale: impediscono l'intrusione di vapore acqueo, polvere, nebbia salina, ecc. tramite un design di tenuta (come IP67/IP68), evitano cortocircuiti causati da corrosione o guasti dell'isolamento; bloccano urti meccanici esterni o impatti di corpi estranei per proteggere i componenti di collegamento ad alta tensione.
C.Sinergia di gestione termica: la struttura di dissipazione del calore integrata (come piastra di raffreddamento a liquido, pad termico) bilancia la temperatura per evitare che il surriscaldamento locale causi ossidazione o saldatura dei punti di collegamento; riducono l'interferenza termica tra moduli adiacenti tramite un design di isolamento termico per evitare differenze di espansione del materiale causate da gradienti di temperatura.
D.Supporto per la compatibilità elettromagnetica (EMC): sopprimono l'interferenza elettromagnetica tramite uno strato di schermatura metallica o un rivestimento conduttivo per proteggere le linee di segnale a bassa tensione (come le linee di comunicazione BMS) dalle interferenze del circuito ad alta tensione.
2-La protezione dell'isolamento crea un ambiente di isolamento efficiente
L'obiettivo della progettazione dell'isolamento elettrico della batteria è creare un ambiente in grado di isolare efficacemente l'elettricità ad alta tensione e garantire un funzionamento efficiente del sistema, assicurando che il modulo batteria possa essere imballato in modo sicuro in qualsiasi condizione operativa, impedendo il rilascio accidentale di energia elettrica ed evitando così potenziali rischi elettrici.
A.La struttura del vassoio della batteria tiene conto sia della protezione del carico che dell'isolamento:
l I materiali in lega di alluminio, come la lega di alluminio estrusa, sono preferiti per ottenere leggerezza mantenendo elevata rigidità e resistenza agli urti. Il telaio esterno è utilizzato per sopportare il peso dell'intero sistema di batterie e l'impatto esterno. I profili a sezione chiusa sono utilizzati per migliorare la resistenza strutturale. Il telaio interno è progettato per supportare i moduli della batteria e le piastre raffreddate ad acqua, ecc., per garantirne la stabilità e i requisiti di dissipazione del calore.
l I materiali isolanti sono utilizzati come cuscinetti o rivestimenti per garantire un buon isolamento elettrico tra il modulo della batteria e il vassoio. Il cablaggio ad alta tensione deve avere un percorso di gestione dedicato e una guaina isolante per garantire la distanza di sicurezza elettrica e la distanza di dispersione con il vassoio.
l Le tecnologie di saldatura avanzate come la saldatura a frizione a mescolamento sono utilizzate per migliorare la resistenza della connessione riducendo al contempo le zone interessate dal calore, evitando deformazioni e potenziali crepe. Per le parti che sono scomode da saldare, vengono utilizzati collegamenti a bullone o rivettatura, combinati con sigillanti, per garantire l'affidabilità dei collegamenti meccanici e l'isolamento elettrico.
l Durante la progettazione si tiene conto della modularità per facilitare la sostituzione e la manutenzione delle batterie senza compromettere la stabilità della struttura complessiva.
Figura 2 Diagramma schematico della distanza di isolamento elettrico e della distanza di fuga
B.Punti chiave della progettazione dell'isolamento ad alta e bassa tensione:
l I punti positivo e negativo del sistema della batteria devono essere isolati dal sistema di alimentazione a bassa tensione e dal vassoio della batteria per garantire che vi sia sufficiente distanza di sicurezza elettrica e distanza di dispersione tra il circuito ad alta tensione e il circuito di controllo a bassa tensione per soddisfare gli standard di sicurezza e prevenire perdite di alta tensione nel sistema a bassa tensione.
l La progettazione dell'isolamento ad alta e bassa tensione deve considerare la compatibilità elettromagnetica (EMC) per garantire che le misure di isolamento non introducano interferenze e mantengano il sistema in funzione in modo stabile.
l Collegamento ad alta impedenza, i sistemi ad alta e bassa tensione sono collegati tramite alta impedenza e solo la massa della carrozzeria del veicolo (vassoio della batteria) può limitare il flusso di corrente per garantire che il guasto del sistema ad alta tensione si diffonda al sistema a bassa tensione.
l Misure di isolamento fisico, quando si progetta il vassoio della batteria, i componenti ad alta e bassa tensione possono essere disposti in diverse camere chiuse per ridurre l'influenza reciproca tramite separazione fisica; utilizzare materiali isolanti come cuscinetti tra il modulo della batteria e il vassoio, come polimeri plastici o gomma, per garantire l'isolamento fisico ed elettrico. Durante la progettazione, valutare la manutenibilità delle misure di isolamento per garantire che possano essere riparate o sostituite in modo sicuro quando necessario.
C.Punti chiave della progettazione della protezione dai contatti:
l Gestione del cablaggio ad alta tensione: i cablaggi ad alta tensione devono essere adeguatamente avvolti in guaine isolanti e gestiti in modo ordinato tramite clip di fissaggio o canaline per evitare l'esposizione e ridurre il rischio di contatto diretto.
l Pareti di sicurezza: le partizioni isolanti sono posizionate tra i moduli batteria e tra i moduli batteria e le pareti del vassoio per prevenire il rischio di scosse elettriche indirette causate da perdite di elettrolita quando la batteria è danneggiata.
l Imballaggio dei componenti ad alta tensione: i componenti chiave come i connettori ad alta tensione e i relè sono imballati per garantire che questi componenti non vengano toccati direttamente per errore anche all'interno del vassoio.
l Design chiuso: il vassoio della batteria è progettato come una struttura chiusa nel suo insieme, utilizzando un guscio metallico o composito per garantire che i componenti interni ad alta tensione non siano esposti e il guscio stesso deve anche avere buone proprietà isolanti.
l Meccanismo di bloccaggio: per i punti di collegamento ad alta tensione manutenibili, viene utilizzato un meccanismo di bloccaggio per garantire che non vengano aperti facilmente durante operazioni non professionali, riducendo il rischio di contatto accidentale.
l Applicazione di materiale isolante: i materiali isolanti sono utilizzati come strato isolante tra il vassoio della batteria e il modulo della batteria per garantire che, anche se il vassoio è danneggiato, il corpo umano possa essere impedito di entrare in contatto diretto con le parti sotto tensione. Questi materiali includono, ma non sono limitati a, polimeri plastici, guarnizioni in gomma o rivestimenti.
3-Design del logo elettrico
L'identificazione elettrica del vassoio della batteria può non solo migliorare la sicurezza del funzionamento, ma anche semplificare il processo di manutenzione e ridurre il rischio di funzionamento errato.
A.Identificazione chiara
l Segnare chiaramente i segnali di avvertimento come "Pericolo di alta tensione" e "Non toccare" sul vassoio della batteria e sui componenti ad alta tensione circostanti per garantire una rapida identificazione anche in caso di emergenza.
l Utilizzare una codifica a colori accettata a livello internazionale, come rosso o arancione per contrassegnare le aree ad alta tensione e blu per la corrente continua, per distinguere intuitivamente le diverse caratteristiche elettriche.
l Applicare simboli di sicurezza elettrica standardizzati, come i simboli grafici in IEC 60417, per indicare alta tensione, messa a terra, punti di spegnimento, ecc. per garantire la comprensibilità globale delle informazioni.
l Includere il numero di serie, la data di produzione e le informazioni sul lotto del vassoio della batteria per un facile monitoraggio e gestione del richiamo.
l Selezionare materiali e tecnologie di stampa resistenti all'usura e alla corrosione per garantire che l'etichetta rimanga chiara e leggibile per tutto il ciclo di vita del vassoio della batteria.
B.Segnali di avvertimento
l I pericoli dell'alta tensione sono chiaramente contrassegnati sul vano batteria e nelle aree circostanti per ricordare al personale addetto alla manutenzione di prestare attenzione alla sicurezza elettrica e di rispettare le procedure operative.
l Indicare le distanze operative sicure, in particolare in prossimità di connettori ad alta tensione e posizioni esposte, per ricordare alle persone di mantenere una distanza appropriata.
C.Guida operativa
l Segnare chiaramente i punti di messa a terra del sistema di batterie e del vassoio per garantire la corretta implementazione delle misure di messa a terra.
l Identificare punti di prova sicuri e punti di accesso per la manutenzione, che devono essere progettati per funzionare a bassa tensione o in condizioni di non alimentazione.
l Le istruzioni di base per il funzionamento e la sicurezza possono essere brevemente elencate nelle aree non critiche del vassoio per guidare il corretto processo operativo.
Condivideremo regolarmente aggiornamenti e informazioni su tecniche di progettazione termica e alleggerimento, per la vostra consultazione. Grazie per l'interesse verso Walmate.
I blocchi d'acqua più popolari sono fondamentalmente di tipo microcanale in rame puro. La piastra inferiore in rame è lavorata direttamente con skived e le alette sono integrate con la piastra inferiore per ridurre la resistenza termica. La piastra inferiore e la piastra di copertura sono brasate o diffuse per garantire l'affidabilità della tenuta.
Parte 3: La struttura dei costi principali del blocco dell'acqua elaborato mediante processo di skiving
1- Vantaggi dell'utilizzo del processo di skiving per la produzione di blocchi d'acqua
l Design integrato: il processo di skiving può integrare il pavimento e le alette, il che è utile per ridurre la resistenza termica di contatto e migliorare la conduttività termica. Inoltre, la piastra inferiore integrata e il design delle alette possono anche migliorare la resistenza strutturale.
l Lavorazione ad alta precisione: il processo di skiving può produrre una struttura del dente molto fine e l'altezza del dente, lo spessore del dente e il passo del dente possono essere controllati con precisione, il che rende le alette del dissipatore di calore più dense, l'area di dissipazione del calore più ampia e la dissipazione del calore più efficiente. Allo stesso tempo, può anche soddisfare meglio le esigenze personalizzate di diversi clienti per forma, dimensioni, ecc.
l L'efficienza di produzione è elevata e il processo di skiving può essere prodotto in serie. Rispetto al CNC tradizionale, il processo di skiving può elaborare più pezzi di ingranaggi contemporaneamente, il che migliora notevolmente l'efficienza di produzione.
Figura 1: Base del blocco d'acqua con diverse tecnologie di lavorazione a-Skiving b-CNC c-Forgiatura a freddo
2- Struttura dei costi del blocco di acqua di skiving
l Costi di progettazione e sviluppo: la complessità di progettazione del blocco di acqua di skiving è relativamente elevata, soprattutto quando sono richiesti requisiti di elevate prestazioni di dissipazione del calore, il che richiede una progettazione e un'ottimizzazione complesse del processo.
l Costo del materiale: i materiali utilizzati nel processo di skiving sono principalmente alluminio e lega di rame. La progettazione di una piastra di alluminio e una lega di rame combinate è più comune nella produzione di radiatori e ha un rapporto costi-prestazioni più elevato, quindi la qualità dell'alluminio e del rame influisce direttamente sul costo.
l Costo di lavorazione:
Costo del processo di skiving: il processo di skiving coinvolge attrezzature di lavorazione CNC ad alta precisione, come macchine utensili CNC a tre assi. L'uso di tali attrezzature richiede un elevato costo di investimento e anche i requisiti tecnici per gli operatori sono elevati, il che aumenterà i costi di produzione.
Costo del processo di saldatura: nel processo di produzione di blocchi d'acqua, anche il processo di saldatura è un importante fattore di costo. La brasatura sotto vuoto e la saldatura a diffusione sono due metodi di saldatura comunemente utilizzati. La brasatura può saldare più giunti contemporaneamente, ha un'elevata efficienza di produzione, richiede materiali di brasatura, ha elevati requisiti per le condizioni di processo ed è difficile controllare la qualità; le attrezzature di saldatura a diffusione hanno un grande investimento una tantum e la saldatura a diffusione non richiede riempitivi, ma ha elevati requisiti per la lavorazione superficiale del pezzo.
Costo del trattamento superficiale: i metodi comuni di trattamento superficiale includono anodizzazione, placcatura, ecc. Per i blocchi d'acqua in lega di alluminio, l'anodizzazione può migliorare la durezza superficiale, la resistenza all'usura e la resistenza alla corrosione, aumentando al contempo l'estetica del prodotto; i blocchi d'acqua in rame saranno placcati, come la nichelatura, per prevenire l'ossidazione e la corrosione del rame e aumentare la durata e l'affidabilità del prodotto.
l Altri costi: ispezione e collaudo, imballaggio e trasporto, ecc.
3-Suggerimenti per l'ottimizzazione dei costi
l Ottimizzazione dell'uso dei materiali
Scegli il materiale giusto: ad esempio, il rame ha un'elevata conduttività termica, un'elevata densità unitaria e un prezzo unitario elevato; l'alluminio è leggero, ha un prezzo unitario basso e una conduttività termica leggermente scarsa.
Uso dei materiali: assicurati un uso efficiente dei materiali e riduci gli sprechi di materiale calcolando accuratamente lo spessore e il margine del materiale.
Figura 2: Diagramma schematico del calcolo del consumo di materiale
l Ottimizzazione dei processi di produzione
Semplificare gli stampi: progettare stampi semplici per ridurre la complessità e i costi degli stampi.
Ridurre il tasso di scarto: ridurre il tasso di scarto tramite un controllo preciso del processo e un'ispezione di qualità.
Stampaggio in un unico passaggio: ottimizzare i percorsi di processo, ridurre più fasi di lavorazione e migliorare l'efficienza della produzione.
Condivideremo regolarmente aggiornamenti e informazioni su tecniche di progettazione termica e alleggerimento, per la vostra consultazione. Grazie per l'interesse verso Walmate.
Come componente chiave del sistema di raffreddamento a liquido, la progettazione del water block deve tenere conto di molteplici fattori quali prestazioni di scambio termico, resistenza strutturale, resistenza alla corrosione, resistenza alle perdite e controllo dei costi. Il water block è solitamente progettato con una complessa struttura a fessura per lo scambio termico (ad es., canale di flusso) e la qualità della progettazione del suo canale di flusso interno determina direttamente l'efficienza dello scambio termico dell'intero sistema.
Parte 2: progettazione del blocco dell'acqua, tecnologia di elaborazione e sfide
1-Requisiti di progettazione per blocchi d'acqua in diversi scenari
l High Performance Computing:
I dispositivi di elaborazione ad alte prestazioni (come CPU ad alte prestazioni, GPU, ecc.) generano molto calore durante il funzionamento, quindi il water block deve avere capacità di dissipazione del calore efficienti. Per soddisfare i requisiti di dissipazione del calore ad alta densità di flusso di calore, il water block di solito adotta un design a microcanali ad alta densità per aumentare l'area di scambio termico e migliorare l'efficienza di dissipazione del calore. Inoltre, alcuni design integrano il water block direttamente sulla CPU, eliminando la fase di applicazione del grasso siliconico, che non solo semplifica il processo di assemblaggio, ma migliora anche ulteriormente le prestazioni di dissipazione del calore. In termini di affidabilità, il water block deve avere eccellenti prestazioni di tenuta per prevenire perdite e garantire un funzionamento stabile a lungo termine.
l Raffreddamento della scheda grafica:
Le schede grafiche sono aree che generano molto calore, quindi il waterblock deve avere un design a copertura totale per garantire che tutti i componenti che generano calore sulla scheda grafica possano essere raffreddati in modo efficace. Allo stesso tempo, il raffreddamento della scheda grafica richiede un'elevata portata di refrigerante, quindi la struttura interna del waterblock deve supportare un'elevata portata per rimuovere rapidamente il calore.
l Data Center:
Nei data center, la progettazione strutturale del water block deve soddisfare molteplici requisiti quali efficiente dissipazione del calore, basso rumore, elevata affidabilità, adattabilità ad alta densità di potenza, gestione intelligente e adattabilità ambientale per garantire un funzionamento stabile ed efficiente dissipazione del calore dei data center.
2- Tendenza evolutiva della struttura del blocco d'acqua
La tendenza evolutiva della progettazione strutturale del blocco d'acqua riflette la duplice ricerca di innovazione tecnologica e miglioramento delle prestazioni, che si riflette principalmente nei seguenti aspetti:
l Prestazioni di dissipazione del calore migliorate:
Aumenta l'area di contatto: alcuni design del blocco dell'acqua migliorano le prestazioni di dissipazione del calore aumentando l'area di contatto con l'elemento riscaldante. Ad esempio, un design di base in rame di ampia area può ottenere un buon contatto e conduzione del calore. Ottimizza la struttura interna: ottimizza il canale dell'acqua interno. Un'idea è quella di ottimizzare il flusso del fluido, ad esempio passando da alette ordinarie ad alette di sterzo, presentando un lungo canale di flusso a strisce, promuovendo la separazione dello strato limite del flusso, riducendo lo spessore dello strato limite e migliorando l'efficienza dello scambio termico; un'altra idea è quella di aumentare l'area di capacità termica, ad esempio passando dai tradizionali canali dell'acqua grossolani al design a microcanali, che aumenta significativamente l'area di contatto tra il refrigerante e la piastra di base e migliora l'efficienza di dissipazione del calore. In alcuni design, il refrigerante viene spruzzato sulla piastra di base a microcanali attraverso una piastra guida per aumentare la velocità del flusso locale e la turbolenza, migliorando notevolmente l'efficienza di assorbimento del calore.
l Progettazione integrata e intelligente:
Design integrato: il design integrato integra la pompa dell'acqua, le alette del dissipatore di calore, la base di conduzione del calore e altri componenti insieme per ridurre il numero di punti di connessione e migliorare la stabilità del sistema e l'efficienza di dissipazione del calore.
Integrazione multifunzionale: oltre alle prestazioni di dissipazione del calore, i moderni blocchi d'acqua hanno anche funzioni di visualizzazione e monitoraggio della temperatura.
Design modulare: la struttura della fibbia modulare migliora la praticità e la libertà di organizzazione.
Figura 1: Base del blocco d'acqua con diversi spessori delle alette
l Materiali e finiture ad alte prestazioni:
L'uso di materiali ad alte prestazioni come la base in rame puro, combinati con tecnologie di trattamento superficiale come la nichelatura, migliora la conduttività termica e la resistenza alla corrosione.
3-Tecnologia di elaborazione e sfide
l Le proprietà dei materiali influenzano la lavorazione:
Problemi di durezza e tenacità dei materiali: i radiatori realizzati con materiali diversi, come rame, alluminio e le loro leghe, hanno durezza e tenacità diverse e requisiti diversi per utensili e processi di lavorazione. I materiali con durezza maggiore si usurano più velocemente e richiedono cambi di utensile più frequenti; i materiali con migliore tenacità sono soggetti a deformazioni e sbavature durante il taglio.
La lavorazione di materiali compositi rame-alluminio è complessa: i dissipatori di calore a denti di pala in materiale composito rame-alluminio devono prima essere trasformati in materiali compositi utilizzando la tecnologia di pressatura a stato semi-fuso a colata continua, quindi viene eseguita la lavorazione a denti di pala. Il processo è più complicato e richiede una maggiore precisione per le attrezzature e i processi.
l Elevati requisiti di precisione dimensionale
È difficile garantire la coerenza dell'altezza e dello spessore dei denti: per alcuni dissipatori di calore ad alta densità, l'altezza e lo spessore di ciascun dente devono essere altamente coerenti per garantire le prestazioni e l'uniformità del dissipatore di calore. Se la differenza tra l'altezza e lo spessore dei denti è troppo grande, ciò porterà a un trasferimento di calore non uniforme e influirà sull'effetto di dissipazione del calore. Durante la lavorazione, sono necessarie apparecchiature ad alta precisione e sistemi di controllo automatizzati per garantire che le specifiche di ciascun dente siano coerenti.
È difficile controllare la spaziatura dei denti: quando i denti sul dissipatore di calore sono troppo densi, la loro densità e spaziatura rendono il processo di lavorazione più complicato e l'apparecchiatura di lavorazione deve avere maggiore velocità e precisione per mantenere l'uniformità dei denti. Ad esempio, quando la spaziatura dei denti è troppo piccola, l'utensile è soggetto a interferenze durante il taglio, influendo sulla precisione della lavorazione e sulla qualità della superficie.
l Rigorosi requisiti di qualità della superficie
Problema di sbavature: durante la lavorazione si generano facilmente delle sbavature, che non solo influiscono sull'estetica del radiatore, ma possono anche ostacolare il flusso d'aria e ridurre l'effetto di dissipazione del calore. La generazione di sbavature può essere causata da una bassa precisione di taglio del materiale, dall'usura degli utensili di lavorazione, ecc. e per risolverli è necessario adottare i corrispondenti processi di sbavatura.
Rugosità superficiale: la rugosità superficiale del radiatore influisce sulle sue prestazioni di dissipazione del calore e sui successivi effetti del trattamento superficiale. Una rugosità superficiale eccessiva aumenterà la resistenza al flusso d'aria e ridurrà l'efficienza di dissipazione del calore. È necessario un ulteriore trattamento superficiale per ridurre la rugosità, il che aumenta i costi e i tempi di lavorazione.
l Elevati requisiti di apparecchiature e processi di lavorazione
Precisione e stabilità dell'attrezzatura: la pala degli ingranaggi richiede una macchina pala degli ingranaggi ad alta precisione e la precisione dell'attrezzatura influisce direttamente sulla precisione dimensionale e sulla qualità della superficie dei denti. Allo stesso tempo, l'attrezzatura deve avere una buona stabilità per garantire la coerenza dimensionale durante la lavorazione a lungo termine.
Selezione e usura dell'utensile: utensili adatti sono fondamentali per la qualità della lavorazione. Il materiale, i parametri geometrici, ecc. dell'utensile devono essere selezionati in base alle proprietà del materiale. Durante il processo di lavorazione, l'usura dell'utensile comporterà una maggiore forza di taglio, una minore precisione dimensionale e una maggiore rugosità superficiale e l'utensile deve essere regolato o sostituito in tempo.
Velocità di avanzamento e profondità di taglio: impostazioni irragionevoli della velocità di avanzamento e della profondità di taglio possono facilmente portare a difetti di lavorazione. Se la velocità di avanzamento è troppo elevata e la profondità di taglio è troppo grande, l'utensile verrà sovraccaricato, con conseguente strappo dell'utensile, rimbalzo dell'utensile, caduta dell'utensile, ecc., che influiranno sulla precisione della lavorazione e sulla qualità della superficie.
Figura 2: processo di skiving
l Elevati requisiti di personalizzazione
Diversi scenari applicativi hanno requisiti diversi per dimensioni, forma, altezza dei denti, spessore dei denti, spaziatura dei denti e altri parametri del radiatore, che devono essere personalizzati in base a esigenze specifiche. Ciò richiede che il produttore di lavorazione abbia capacità di adattamento del processo flessibili e una vasta esperienza per soddisfare diverse esigenze di personalizzazione.
Condivideremo regolarmente aggiornamenti e informazioni su tecniche di progettazione termica e alleggerimento, per la vostra consultazione. Grazie per l'interesse verso Walmate.
Con la rapida crescita della potenza di calcolo dell'intelligenza artificiale globale e il continuo aumento del consumo di potenza termica di progettazione (TDP) dei chip, la domanda di raffreddamento dei data center sta affrontando sfide senza precedenti. Allo stesso tempo, le politiche sempre più severe di risparmio energetico e riduzione delle emissioni di carbonio in tutto il mondo hanno ulteriormente promosso l'innovazione della tecnologia di raffreddamento. In questo contesto, le tradizionali soluzioni di raffreddamento ad aria sono gradualmente diventate difficili da soddisfare i doppi requisiti di efficiente dissipazione del calore e risparmio energetico. La tecnologia di raffreddamento a liquido sta rapidamente aumentando grazie alle sue eccellenti prestazioni di dissipazione del calore e ai significativi vantaggi di risparmio energetico, diventando la scelta principale per le soluzioni di raffreddamento dei data center. In quanto apparecchiatura principale per l'elaborazione e l'archiviazione dei dati, le prestazioni e la stabilità del server sono direttamente correlate all'efficienza operativa dell'intero sistema. I componenti principali del server, tra cui scheda madre, CPU, memoria, disco rigido e scheda grafica, genereranno molto calore in caso di funzionamento continuo ad alto carico. Se il calore non può essere dissipato in modo tempestivo ed efficace, ciò influirà seriamente sulle prestazioni e sulla durata del server. A tal fine, sono stati introdotti sistemi avanzati di raffreddamento a liquido nelle soluzioni di raffreddamento dei server e installati direttamente sulle principali fonti di calore, come CPU e schede grafiche, per migliorare significativamente l'efficienza della dissipazione del calore.
Parte 1: Struttura e principio di funzionamento del blocco d'acqua
Uno dei componenti principali del sistema di raffreddamento a liquido è il waterblock, che di solito è fatto di materiali in rame o alluminio con elevata conduttività termica ed è progettato con precisi canali per l'acqua e strutture di dissipazione del calore. Questi waterblock si adattano perfettamente alla superficie di fonti di calore come CPU e GPU e assorbono e trasferiscono rapidamente il calore attraverso l'acqua di raffreddamento che circola al suo interno. Il calore viene quindi trasportato al dissipatore di calore, che viene poi fatto circolare attraverso il sistema di raffreddamento ad acqua e infine dissipato nell'aria circostante.
Figura 1: Tendenze del consumo di potenza termica dei chip dei principali produttori di chip
1- Tipi e caratteristiche comuni dei blocchi d'acqua
l Blocco dell'acqua microcanale
Caratteristiche: Il blocco dell'acqua microcanale adotta un design preciso del canale micro-acqua. La struttura del canale dell'acqua è fine e complessa, il che può aumentare significativamente l'area di contatto tra il refrigerante e i componenti che generano calore, migliorando così notevolmente l'efficienza di dissipazione del calore. Il design del canale micro-acqua può anche produrre un forte effetto di turbolenza durante il flusso del refrigerante, migliorando ulteriormente il coefficiente di trasferimento del calore per convezione e ottenendo un trasferimento di calore efficiente.
Scenari di applicazione: è particolarmente adatto per CPU e GPU con elevata generazione di calore, in particolare nell'elaborazione ad alte prestazioni, nell'overclocking e nei data center, che hanno requisiti di dissipazione del calore estremamente elevati.
l Blocco dell'acqua a flusso grande
Caratteristiche: La struttura interna del water block a grande portata è relativamente semplice, solitamente utilizza una piastra di rame o un design con scanalatura incisa, e il costo di produzione è basso. Il suo vantaggio principale è che si basa sul flusso d'acqua ad alta velocità per rimuovere rapidamente il calore ed è adatto per l'uso con un sistema di raffreddamento ad acqua a grande portata. Sebbene la struttura sia semplice, la sua efficiente capacità di dissipazione del calore lo rende una scelta molto conveniente.
Scenario applicativo: Adatto per scenari con determinati requisiti di efficienza di dissipazione del calore ma budget limitato, come sistemi informatici fai da te di fascia medio-alta o cluster di server di piccole e medie dimensioni.
l Blocco dell'acqua di tipo iniezione
Caratteristiche: Il blocco di raffreddamento ad acqua di tipo jet spruzza il refrigerante da un ugello stretto alla piastra inferiore del microcanale ad alta velocità attraverso la piastra di guida, formando un forte effetto turbolenza e migliorando significativamente l'efficienza di dissipazione del calore. Questo design non solo aumenta l'area di contatto tra il refrigerante e la base, ma ottimizza anche ulteriormente le prestazioni di scambio termico attraverso il flusso ad alta velocità.
Scenari applicativi: Adatto per CPU e GPU ad alte prestazioni, in particolare in requisiti di dissipazione del calore elevata e scenari ad alto flusso, come l'elaborazione di overclocking, la formazione dell'intelligenza artificiale e il rendering grafico.
2-Struttura generale del blocco dell'acqua
Un waterblock è un blocco metallico con canali per l'acqua all'interno, solitamente in rame o alluminio. Non entra in contatto con la CPU, la scheda grafica o altri dispositivi che generano calore. Il suo design strutturale determina direttamente la qualità delle prestazioni di dissipazione del calore. Un tipico waterblock è solitamente costituito dalle seguenti parti chiave:
l La base è solitamente realizzata in materiali ad alta conduttività termica come rame o lega di alluminio, e la superficie è finemente lavorata per garantire uno stretto contatto con i componenti che generano calore. La base è dotata di un complesso design del canale di flusso per aumentare l'area di contatto tra il refrigerante e la base.
l La piastra di copertura, insieme alla base, forma una cavità di tenuta del canale di flusso per proteggere il canale di flusso, la guarnizione e altri componenti all'interno del blocco idrico da polvere, impurità e danni fisici esterni.
l L'ingresso e l'uscita dell'acqua sono le interfacce per l'ingresso e l'uscita del refrigerante dalla testa di raffreddamento ad acqua. Sono generalmente progettati sul lato o sulla parte superiore della testa di raffreddamento ad acqua per garantire che il refrigerante possa fluire dentro e fuori senza problemi. La progettazione della posizione deve considerare il percorso di flusso del fluido per ridurre la resistenza al flusso e aumentare la portata del refrigerante.
l Le clip vengono utilizzate per fissare saldamente la testina di raffreddamento ad acqua alla CPU o ad altri componenti che generano calore, per garantire una base solida e ottenere una conduzione efficiente del calore.
Figura 2: Struttura tipica del blocco d'acqua
3- Ottimizzazione completa delle prestazioni di dissipazione del calore
l Ottimizzazione della progettazione del canale di flusso
Aumentare l'area di contatto del canale di flusso: progettando canali di flusso più stretti e densi, l'area di contatto tra il refrigerante e la base può essere notevolmente aumentata, migliorando così il coefficiente di trasferimento di calore convettivo. Ad esempio, il design del microcanale ha una struttura del canale dell'acqua fine. I parametri di progettazione del blocco dell'acqua del microcanale (come larghezza, altezza e spaziatura del canale) hanno un'influenza decisiva sulla sua efficienza di dissipazione del calore: man mano che la larghezza del canale diminuisce, il coefficiente di trasferimento di calore aumenta in modo significativo, grazie all'effetto di turbolenza migliorato del flusso di refrigerante nel canale stretto, migliorando così l'efficienza di scambio termico; l'altezza maggiore del canale aiuta ad aumentare lo spazio di flusso del refrigerante, migliorando così le prestazioni di trasferimento di calore; la spaziatura più piccola del canale può aumentare l'area di contatto tra il refrigerante e la fonte di calore, migliorando così l'efficienza di dissipazione del calore.
Può anche essere ottimizzato ottimizzando il layout del canale di flusso e riducendo le curve del canale di flusso: un layout ragionevole del canale di flusso può garantire che il refrigerante copra uniformemente la superficie dei componenti che generano calore e ridurre la differenza di temperatura locale. Le curve nel canale di flusso aumenteranno la perdita di carico e la resistenza al flusso interno, riducendo così l'efficienza di raffreddamento. Il numero di curve dovrebbe essere ridotto al minimo nella progettazione. Se non può essere evitato, le curve dovrebbero essere progettate come transizioni fluide per ridurre la caduta di pressione e ottimizzare le prestazioni del flusso.
l Materiali ad alta conduttività termica: la base del waterblock è solitamente realizzata in materiali ad alta conduttività termica come rame puro o lega di alluminio. Questi materiali possono trasferire in modo efficiente il calore dalla fonte di calore al refrigerante, migliorando così le prestazioni complessive di dissipazione del calore.
l Ottimizzazione dei parametri strutturali, come spessore del substrato di base, alette, struttura dello spoiler, ecc. L'aumento dello spessore del substrato porterà a un aumento della temperatura massima, quindi il design deve trovare il miglior equilibrio tra effetto di dissipazione del calore e resistenza strutturale; aumentando l'altezza, lo spessore e la spaziatura delle alette, le prestazioni di dissipazione del calore possono essere migliorate, ma allo stesso tempo aumenterà anche la resistenza al flusso. Trova la migliore combinazione di progettazione delle alette per massimizzare le prestazioni di dissipazione del calore. La forma della colonna dello spoiler può migliorare efficacemente l'effetto di turbolenza e migliorare l'efficienza dello scambio termico.
Condivideremo regolarmente aggiornamenti e informazioni su tecniche di progettazione termica e alleggerimento, per la vostra consultazione. Grazie per l'interesse verso Walmate.
Sulla base della produzione effettiva, questo articolo riassume i problemi più comuni, le cause e i metodi di miglioramento nel processo di saldatura ad attrito per vostro riferimento.
1-Difetti superficiali
(1) Scanalature superficiali
l Descrizione del problema: le scanalature superficiali, note anche come difetti di aratura, solitamente si formano sulla superficie superiore della saldatura, tendono verso il bordo di avanzamento della saldatura e hanno la forma di una scanalatura.
l Causa: il flusso di metallo termoplastico attorno alla saldatura è insufficiente e il metallo plastico della saldatura non riesce a riempire completamente la cavità istantanea lasciata dall'ago di agitazione durante il suo movimento.
l Metodo di miglioramento: aumentare il diametro della spalla, aumentare la pressione e ridurre la velocità di saldatura.
Figura 1: Scanalature
(2)Bave sui bordi
l Descrizione del problema: Sul bordo esterno della saldatura si formano delle sbavature di forma ondulata.
l Causa: Corrispondenza non corretta tra velocità di rotazione e velocità di saldatura, pressione verso il basso eccessiva.
l Metodo di miglioramento: ottimizzare i parametri di saldatura e ridurre la quantità di pressione.
Figura 2: Sbavature sui bordi
(3)Peeling superficiale
l Descrizione del problema: sulla superficie della saldatura si formano delle screpolature o delle filettature sotto forma di pellicola o di filo.
l Causa: una grande quantità di calore generato dall'attrito del metallo si accumula sulla superficie metallica della saldatura, facendo sì che il metallo locale sulla superficie raggiunga uno stato fuso.
l Metodo di miglioramento: ottimizzare i parametri di saldatura, ridurre la velocità di rotazione e aumentare la velocità di saldatura.
Figura 3: Peeling superficiale
(4) Nodulo di saldatura posteriore
l Descrizione del problema: si forma un cordone di saldatura sul lato posteriore della saldatura.
l Causa: Controllo improprio della profondità e della pressione della testa di agitazione durante la saldatura.
l Metodo di miglioramento: ottimizzare le impostazioni di profondità e pressione della testa di miscelazione.
2-Difetti interni
(1) Penetrazione incompleta
l Descrizione del problema: un difetto "simile a una crepa" si verifica quando il fondo della saldatura non è collegato o non è completamente collegato.
l Causa: l'ago di agitazione non è sufficientemente lungo, con conseguente agitazione insufficiente del materiale sul fondo della saldatura.
l Metodo di miglioramento: selezionare la lunghezza appropriata dell'ago di agitazione per garantire che il materiale sullo spessore della saldatura possa essere completamente agitato.
Figura 4: Penetrazione incompleta
(2) Fori
l Descrizione del problema: un difetto "simile a una crepa" si verifica quando il fondo della saldatura non è collegato o non è completamente collegato.
l Causa: Durante il processo di saldatura, a causa di un apporto di calore di attrito insufficiente, una quantità insufficiente di materiale raggiunge lo stato plastificato, con conseguente flusso di materiale insufficiente e chiusura incompleta dell'area di saldatura.
l Metodi di miglioramento: ottimizzare i parametri di saldatura, migliorare la progettazione dell'ago di agitazione e controllare la velocità di saldatura e la velocità di rotazione.
Figura 5: Fori
Condivideremo regolarmente aggiornamenti e informazioni su tecniche di progettazione termica e alleggerimento, per la vostra consultazione. Grazie per l'interesse verso Walmate.
Di recente, l'editore ha notato che molte aziende stanno prestando attenzione e pianificando l'accumulo di energia tramite raffreddamento a liquido a immersione. Dopo un periodo di silenzio, la tecnologia di raffreddamento a liquido a immersione ha nuovamente attirato l'attenzione e sembra stia diventando di nuovo popolare. Credo che anche molti colleghi stiano prestando attenzione a questo sviluppo.
1- Caratteristiche della tecnologia di raffreddamento a liquido ad immersione
Le celle di accumulo di energia si stanno muovendo verso 300+Ah e i sistemi di accumulo di energia si stanno muovendo verso 5MWh+. Più grande è la cella, più calore genera, più difficile è dissipare il calore e più difficile è garantire la coerenza della temperatura. Inoltre, il sistema di accumulo di energia è composto da un gran numero di celle impilate e le condizioni operative sono complesse e mutevoli, il che è più probabile che causi una generazione di calore non uniforme e una distribuzione non uniforme della temperatura. Se i problemi di dissipazione del calore e uniformità della temperatura non vengono risolti correttamente, le prestazioni di carica e scarica della batteria, la capacità e la durata diminuiranno, influenzando le prestazioni dell'intero sistema. Inoltre, la sicurezza è sempre stata la "spada di Damocle" che incombe sull'accumulo di energia delle batterie al litio e il modo più comune per migliorare la sicurezza è quello di muoversi verso le tre dimensioni di sicurezza intrinseca, sicurezza attiva e sicurezza passiva. Il raffreddamento a liquido a immersione consiste nell'immergere la cella della batteria in un liquido isolante, non tossico e dissipatore di calore. Il refrigerante ha una maggiore conduttività termica e capacità termica specifica. Questo metodo di contatto diretto può fornire un'efficienza di trasferimento di calore estremamente elevata, migliorando anche una migliore uniformità della temperatura. Inoltre, oltre a essere un mezzo di controllo della temperatura, il refrigerante può anche essere utilizzato come fluido antincendio per sistemi di accumulo di energia, combinando il controllo della temperatura e la protezione antincendio, che è anche una caratteristica significativa della tecnologia di raffreddamento a liquido a immersione. Il raffreddamento a liquido a immersione avrà senza dubbio più vantaggi nel contesto di un settore che richiede prestazioni di dissipazione del calore più elevate e una maggiore sicurezza.
Figura 1: Batteria di accumulo di energia raffreddata a liquido immersa Scatola di imballaggio
2- Soluzione di sistema di accumulo di energia con raffreddamento a liquido immerso
Come ramo della tecnologia di raffreddamento a liquido, la tecnologia di raffreddamento a liquido a immersione non è la prima ad essere utilizzata nel settore dell'accumulo di energia. Inizialmente è stata utilizzata nel campo dell'informatica ad alte prestazioni e in seguito si è gradualmente estesa ai data center, all'intelligenza artificiale, alle criptovalute, ecc.
L'intenzione originale della progettazione del sistema di accumulo di energia con raffreddamento a liquido a immersione è quella di risolvere le carenze del raffreddamento ad aria tradizionale e del raffreddamento a liquido indiretto nell'efficienza di raffreddamento e nel controllo della differenza di temperatura della batteria. La messa in servizio ufficiale del progetto Southern Power Grid Meizhou Baohu segna l'applicazione di successo del raffreddamento a liquido a immersione, una tecnologia all'avanguardia, nel campo della nuova ingegneria dell'accumulo di energia.
l Metodo di raffreddamento e metodo di circolazione del refrigerante
I metodi di raffreddamento sono divisi in monofase e a cambiamento di fase. Viene utilizzato il raffreddamento a liquido a immersione monofase, che include principalmente olio minerale, olio siliconico, estere naturale, ecc. Altri schemi utilizzano il raffreddamento a liquido a immersione bifase, rappresentato principalmente da idrofluoroetere, e utilizzano il calore latente a cambiamento di fase per dissipare il calore e migliorare l'efficienza di dissipazione del calore. Secondo statistiche incomplete, lo schema di "raffreddamento a immersione monofase" è il più comune tra i sistemi di accumulo di energia a raffreddamento a liquido a immersione attualmente rilasciati. In base alla differenza nella modalità di circolazione del refrigerante, ci sono tre percorsi tecnici nel raffreddamento a liquido a immersione monofase: convezione naturale, azionamento della pompa e raffreddamento a liquido a piastra fredda accoppiato a immersione. La convezione naturale utilizza le caratteristiche di espansione del volume del liquido e riduzione della densità dopo il riscaldamento per ottenere il galleggiamento del refrigerante caldo e l'affondamento dopo il raffreddamento, completando così la dissipazione del calore della circolazione; il nucleo del sistema di azionamento della pompa è che l'unità di raffreddamento a liquido aziona il refrigerante per circolare tra la tubazione di raffreddamento a liquido e la scatola di immersione della batteria per completare l'intero processo di dissipazione del calore della circolazione; nello schema di raffreddamento a liquido con piastra accoppiata a immersione, la batteria è immersa nel fluido dielettrico e la piastra fredda a contatto con il fluido dielettrico viene utilizzata per dissipare il calore, evitando l'uso di complessi circuiti secondari per raffreddare il fluido dielettrico.
l Forma del prodotto e soluzione di integrazione
L'iterazione della soluzione di integrazione del sistema di accumulo di energia raffreddato a liquido a immersione è un processo dal tutto alla parte e poi ai dettagli. Ogni passaggio è ottimizzato e migliorato sulla base della fase precedente per ottenere prestazioni e sicurezza più elevate. Dal livello cabina al livello pacco, la tecnologia di integrazione del sistema presenta le caratteristiche della personalizzazione della scena. La diversificazione degli scenari di accumulo di energia rende diversa la domanda di sistemi di accumulo di energia. Un singolo prodotto non può soddisfare la domanda del mercato. Il design modulare consente di ottimizzare ed espandere i prodotti di accumulo di energia in base alla scala e alla domanda di potenza del progetto, consentendo di adattare e distribuire rapidamente le soluzioni di accumulo di energia in base a diversi scenari ed esigenze applicative.
3-Sfide e scenari di implementazione nel processo di industrializzazione
I sistemi di accumulo di energia raffreddati a liquido immersi devono affrontare numerose sfide durante il processo di commercializzazione, tra cui la fattibilità economica, la complessità tecnica, l'accettazione del mercato e la maturità della filiera industriale.
l Complessità tecnica: rispetto ai sistemi di raffreddamento a liquido con piastra fredda, i sistemi di raffreddamento a liquido a immersione sono più complessi da progettare e implementare.
l Maturità della filiera industriale: la filiera industriale della tecnologia di raffreddamento a liquido a immersione non è ancora completamente matura, il che ne limita l'applicazione in una gamma più ampia di campi. La maturità della filiera industriale influisce direttamente sulla promozione e sulla commercializzazione della tecnologia.
l Sfide economiche: il settore dell'accumulo di energia è ancora nelle prime fasi di sviluppo commerciale e la mancanza di redditività rende difficile che i percorsi tecnologici ad alto costo siano favoriti dal mercato. Molte aziende competono con prezzi bassi per ordini temporanei, il che limita la penetrazione del raffreddamento a liquido a immersione.
Attualmente, il mercato principale dell'industria dell'accumulo di energia è ancora dominato dal raffreddamento ad aria e dal raffreddamento a liquido a piastra fredda, e il raffreddamento a liquido a immersione non è ancora stato pienamente accettato dal mercato. Sebbene la penetrazione di mercato e l'accettazione della tecnologia di raffreddamento a liquido a immersione non siano elevate, potrebbe non mostrare un potenziale considerevole in alcuni scenari speciali, come:
l Industria chimica pericolosa: le aziende chimiche pericolose hanno controlli di sicurezza estremamente rigorosi sulle apparecchiature di accumulo di energia, perché la maggior parte delle sostanze chimiche che producono e immagazzinano sono altamente infiammabili, esplosive, tossiche o corrosive. Una volta che si verifica un incidente, non solo causerà gravi perdite all'azienda stessa, ma potrebbe anche causare inquinamento ambientale e danni alle comunità circostanti.
l Stazioni base e data center: le stazioni base e i data center hanno una bassa tolleranza alla fuga termica. I sistemi di accumulo di energia dei data center devono avere batterie con prestazioni stabili e non sono soggetti a fuga termica per garantire la sicurezza del sistema. I requisiti per la qualità dell'alimentazione sono elevati e il sistema di accumulo di energia deve avere una capacità di risposta rapida. In caso di emergenza, come un guasto della rete o un'interruzione di corrente, il sistema di accumulo di energia deve essere in grado di passare direttamente alla modalità di scarica per garantire la continuità e la stabilità dell'alimentazione.
l Stazione di ricarica rapida: quando si carica e si scarica a velocità elevate, la batteria genera una grande quantità di calore in un breve periodo di tempo, il che causerà una temperatura della batteria troppo elevata e irregolare, rappresentando una minaccia per le prestazioni, la durata e la sicurezza della batteria. Ciò significa che la gestione termica della batteria diventa particolarmente importante in scenari di carica e scarica ad alta velocità.
Condivideremo regolarmente aggiornamenti e informazioni su tecniche di progettazione termica e alleggerimento, per la vostra consultazione. Grazie per l'interesse verso Walmate.
La tenuta stagna del pacco batteria è un indicatore cruciale nei veicoli elettrici e nei sistemi di accumulo di energia. Il test di tenuta stagna del pacco batteria viene eseguito principalmente sul guscio del pacco batteria, sull'interfaccia, sul connettore, sul gruppo di raffreddamento, ecc. per garantire che l'interno del pacco batteria non sia contaminato o invaso da impurità come polvere e umidità dall'ambiente esterno e che il gruppo di raffreddamento non perda, in modo da garantire che il pacco batteria mantenga prestazioni e durata normali e non causi incidenti di sicurezza come cortocircuiti o esplosioni.
1- Formulazione standard del test di livello di protezione e tenuta stagna del pacco batteria
International Protection Making (IEC60529), noto anche come livello di protezione da corpi estranei o codice IP. Il sistema di livello di protezione IP (Ingress Protection) è uno standard stabilito dalla Commissione elettrotecnica internazionale (IEC) per classificare il livello di protezione degli alloggiamenti delle apparecchiature elettriche contro l'intrusione di corpi estranei e l'intrusione di acqua. Il livello di tenuta stagna della custodia del pacco batteria è solitamente richiesto per raggiungere IP67 o IP68, il che significa che la custodia del pacco batteria deve essere completamente protetta dall'ingresso di polvere (livello antipolvere 6) e può essere immersa in acqua a una certa pressione per un periodo di tempo senza infiltrazioni d'acqua a un livello dannoso (livello impermeabile 7). Requisiti più rigorosi prevedono che la batteria possa essere immersa in acqua profonda 1 m per 60 minuti senza infiltrazioni d'acqua (livello impermeabile 8). Il livello di protezione IP è solitamente composto da due cifre. Maggiore è il numero, maggiore è il livello di protezione, come mostrato nella Figura 1:
Figura 1: Descrizione del livello di protezione IP
Per garantire che il pacco batteria soddisfi i requisiti IP67 e IP68, il pacco batteria deve essere immerso in acqua. Questo metodo richiede molto tempo, è distruttivo per il pacco batteria e presenta alcuni rischi per la sicurezza. Non è adatto come test offline per le batterie di alimentazione. Pertanto, è diventata una pratica comune nel settore utilizzare test di tenuta stagna per garantire che il pacco batteria soddisfi i requisiti IP67 e IP68. La formulazione di standard di test di tenuta stagna deve considerare la relazione tra valore di caduta di pressione e tasso di perdita, nonché la relazione tra apertura e perdita d'acqua. La formulazione di standard di test di tenuta stagna comporta una serie di passaggi dagli estremi teorici alla verifica sperimentale per ottenere la conversione dal livello IP agli standard di test di tenuta stagna. Ad esempio, prendendo IP68 come esempio:
Figura 2: Fasi per la formulazione di standard di prova di tenuta all'aria
2- Selezione dei metodi di prova di tenuta all'aria e analisi delle difficoltà di prova
La progettazione e la qualità di fabbricazione del pacco batteria sono fattori chiave che influenzano la tenuta all'aria, tra cui la tenacità e la resistenza del coperchio della scatola della batteria, la sigillatura del guscio del pacco batteria, interfacce e connettori, prese d'aria antideflagranti e la sigillatura del connettore elettrico stesso. Inoltre, ci saranno alcuni problemi che influenzano la tenuta all'aria durante l'uso, come problemi di espansione e contrazione termica, invecchiamento del materiale, vibrazioni e urti. Nella produzione e fabbricazione dei gusci del pacco batteria, prestiamo maggiore attenzione alla scarsa tenuta all'aria causata da problemi come punti di saldatura e qualità dei giunti, come punti di saldatura irregolari, saldature deboli o screpolate, fessure d'aria e scarsa tenuta delle connessioni dei giunti. Il test di tenuta all'aria del pacco batteria è principalmente suddiviso nel test di tenuta all'aria del guscio superiore, del guscio inferiore e delle parti di assemblaggio. Il test di tenuta all'aria dei gusci superiore e inferiore deve soddisfare i requisiti di perdita di tenuta all'aria dopo l'assemblaggio. Quando si seleziona il metodo di prova di tenuta all'aria per il pacco batteria, le caratteristiche del pacco batteria, i requisiti di accuratezza del test, l'efficienza di produzione e il costo sono generalmente considerati in modo completo.
I test di tenuta stagna del pacco batteria in ingegneria sono generalmente divisi in test di tenuta stagna di processo e test di tenuta stagna di spedizione. Inoltre, i test di tenuta stagna dei gusci superiore e inferiore devono soddisfare i requisiti di tenuta stagna dopo l'assemblaggio, il che impone requisiti più severi sugli standard di prova. Per garantire che la tenuta stagna soddisfi i requisiti, le seguenti difficoltà devono essere superate nel funzionamento effettivo:
l Stabilità della struttura del prodotto: qualità delle saldature, tra cui saldature a spina, saldature a rubinetto, saldature a trave, saldature della piastra inferiore del telaio, saldature della piastra di copertura anteriore e posteriore del telaio, ecc. I problemi di perdite di saldatura sono concentrati principalmente nei punti di inizio e fine dell'arco e nei difetti causati da bruciature passanti; crepe causate da sollecitazioni di deformazione della saldatura, come la saldatura della parete laterale della cavità della piastra inferiore, la stratificazione del materiale della cavità della piastra inferiore e l'incapacità di resistere alle sollecitazioni di deformazione della saldatura.
l Adattabilità e stabilità di dispositivi di fissaggio ermetici: il design dei dispositivi di fissaggio deve corrispondere fedelmente alla forma e alle dimensioni dei componenti testati, assicurando che i componenti possano essere fissati saldamente ai dispositivi di fissaggio durante il processo di collaudo, riducendo così gli errori di collaudo causati da spostamenti di posizione o vibrazioni. Tuttavia, in pratica, le dimensioni e la forma dei pacchi batteria variano in modo significativo, rendendo necessaria la progettazione e la fabbricazione di più dispositivi di collaudo diversi, il che aumenta i costi e la complessità operativa. Progettare un dispositivo di fissaggio universale complicherebbe ulteriormente il processo di progettazione.
l Ripetibilità dei risultati del test di tenuta all'aria: fattori quali la pressione dell'aria, la temperatura e la secchezza del pezzo/dispositivo di prova influenzeranno i risultati del test di tenuta all'aria.
l Nei pezzi con numerose piccole crepe non penetranti, a causa dell'influenza di fattori quali la precisione dell'apparecchiatura di rilevamento e i parametri di rilevamento, la fonte della perdita potrebbe non essere individuata, con conseguente mancato rilevamento.
Figura 3: Attrezzatura per test di tenuta all'aria
3-Combinazione di soluzioni di rilevamento della tenuta all'aria del pacco batteria comunemente utilizzate in ingegneria
Il test di tenuta all'aria del processo di guscio del pacco batteria generalmente include il test di tenuta all'aria e il test di immersione in acqua. Nel test di tenuta all'aria, il coperchio superiore della scatola della batteria viene sigillato, lasciando solo una porta di collegamento come ingresso dell'aria. La tenuta all'aria del pacco batteria viene valutata controllando la pressione dell'aria e osservando se vi sono perdite d'aria. Il test di immersione in acqua consiste nell'immergere completamente l'intera scatola della batteria in acqua e valutare la sua tenuta all'aria controllando se vi è acqua nella scatola.
Il rilevamento delle perdite di elio è una tecnologia che utilizza l'elio come gas tracciante per rilevare le perdite rilevando la concentrazione di elio nel punto di perdita. Quando l'elio entra all'interno o all'esterno del dispositivo in fase di test dove potrebbe esserci una perdita, se c'è una perdita, l'elio entrerà o uscirà rapidamente dal sistema attraverso la perdita e verrà rilevato dallo spettrometro di massa. Il metodo di rilevamento delle perdite di elio ha un'elevata efficienza di rilevamento, specialmente nel rilevamento di piccole perdite.
Figura 4: Confronto dei metodi di rilevamento delle perdite
Nella produzione effettiva, più metodi di rilevamento vengono solitamente combinati per migliorare l'efficienza e l'accuratezza del rilevamento. Ad esempio, il metodo di rilevamento delle perdite di elio è adatto per il rilevamento di piccole perdite e ad alta precisione, mentre il metodo di pressione differenziale ha le caratteristiche di alta precisione e risposta rapida. Inoltre, sebbene il tradizionale metodo di rilevamento dell'acqua abbia una bassa accuratezza di rilevamento, è intuitivo e poco costoso, ed è un modo conveniente per localizzare le perdite.
Condivideremo regolarmente aggiornamenti e informazioni su tecniche di progettazione termica e alleggerimento, per la vostra consultazione. Grazie per l'interesse verso Walmate.
Il potenziale guasto della tenuta stagna del gruppo di raffreddamento a liquido dell'accumulo di energia coinvolge molteplici aspetti, quali: perdite, corrosione e deposizione, condensa e altre modalità di guasto.
1- Interconnessione e composizione dei fluidi
Nel sistema di raffreddamento a liquido con accumulo di energia, l'interconnessione del fluido è responsabile del trasferimento del refrigerante tra i vari componenti. Attraverso un'efficace interconnessione del fluido, il refrigerante è garantito per circolare in modo efficiente nel sistema, rimuovendo così il calore in eccesso generato durante il processo di carica e scarica della batteria.
Un sistema ben sigillato può prevenire efficacemente la perdita di refrigerante. La perdita non solo porterà alla perdita di refrigerante e richiederà frequenti rifornimenti, ma influenzerà anche le prestazioni di dissipazione del calore e la stabilità del sistema. Nell'accumulo di energia, la perdita di refrigerante può anche causare un cortocircuito della batteria, causando problemi di sicurezza.
2-Progettazione a tenuta stagna del sistema di interconnessione dei fluidi
La progettazione a tenuta stagna del sistema di interconnessione dei fluidi è l'elemento chiave per garantire che il sistema mantenga la tenuta e impedisca perdite di fluido in diverse condizioni operative.
Figura 1: Tipica distribuzione del sistema di raffreddamento a liquido per l'accumulo di energia
(1) Analizzare le possibili fonti di perdite e i punti di rischio nel sistema:
l Proprietà autosigillante dell'assemblaggio di raffreddamento a liquido. Ad esempio, nella progettazione integrata del sistema di canali di raffreddamento a liquido e del Pack box, i componenti sono collegati tramite saldatura. Difetti di qualità della saldatura, saldature scadenti, pori, crepe, ecc. possono tutti portare a problemi di infiltrazione di liquido.
l La progettazione strutturale è irragionevole. Ad esempio, i fori di posizionamento o i fori filettati della scatola di raffreddamento a liquido sono troppo vicini al canale di flusso e le parti saldate male possono facilmente trasformarsi in canali per infiltrazioni di liquido.
l Parti di collegamento: i collegamenti dei tubi, le valvole e i giunti del sistema di raffreddamento a liquido sono punti di perdita comuni. Se la struttura di collegamento non è progettata correttamente o il processo di fabbricazione non è sofisticato, ci sono piccoli difetti all'interno dei giunti e il refrigerante potrebbe anche fuoriuscire da questi difetti.
l Perdite causate da installazione non corretta, invecchiamento o danneggiamento del materiale, ecc.
(2) Progettazione della struttura di tenuta:
l Il PACK raffreddato a liquido utilizza un metodo di raffreddamento a piastra fredda separata a secco e a umido. In normali condizioni di lavoro, le celle della batteria non hanno alcun contatto con il refrigerante, il che può garantire il normale funzionamento delle celle della batteria. Una soluzione per il raffreddatore a liquido per l'accumulo di energia è quella di formarlo tramite un processo di estrusione, integrare il canale di flusso direttamente sulla piastra fredda e quindi utilizzare la lavorazione meccanica per aprire il percorso di circolazione del raffreddamento. In questo processo, la scelta del giusto processo di saldatura è un passaggio importante per garantire la tenuta. Per i dettagli, fare riferimento a "Progettazione del processo di saldatura per la scatola inferiore per l'accumulo di energia".
l Le condotte di raffreddamento a liquido sono utilizzate principalmente per connessioni di tubi morbidi (duri) di transizione tra fonti di raffreddamento a liquido e apparecchiature, tra apparecchiature e tra apparecchiature e condotte. I principali metodi di connessione sono:
Collegamento rapido: uno dei metodi di collegamento per i sistemi di raffreddamento a liquido con accumulo di energia è l'utilizzo del collegamento rapido VDA o CQC.
Collegamento filettato: entrambe le estremità della struttura di collegamento sono collegate in modo scorrevole ai tubi e il collegamento filettato tra l'anello filettato interno e il manicotto filettato aumenta la solidità del collegamento.
Collegamento di tubo di limitazione e dado: un tubo di collegamento è bloccato a un'estremità del tubo e i tubi di limitazione sono installati in modo fisso su entrambi i lati del tubo di collegamento. Rondelle di gomma e anelli convessi sono installati in modo fisso all'interno dei tubi di limitazione e una scanalatura per l'anello di limitazione è aperta sulla superficie della testa del tubo di collegamento. Un dado è collegato in modo rotante alla parte superiore del tubo di limitazione ed è collegato in modo rotante al tubo di limitazione tramite filettature.
Collegamento dell'anello di tenuta: un anello di tenuta è fissato alla parete interna del manicotto filettato mediante una colla forte, e la parete interna dell'anello di tenuta è collegata in modo mobile alla superficie esterna del tubo per evitare perdite durante l'uso.
(3) La piastra di raffreddamento a liquido PACK, l'interfaccia della cabina, la tubazione della cabina, ecc. sono tutte progettate con protezione dalla corrosione a lungo termine in condizioni comuni di refrigerante, temperatura e portata per garantire un funzionamento a lungo termine senza corrosione. Effetto delle condizioni operative sulla tenuta dei liquidi:
l Temperatura. Influenza della temperatura elevata: all'aumentare della temperatura, la viscosità del liquido generalmente diminuisce, il che può causare una diminuzione delle prestazioni di tenuta del liquido, influenzando così la tenuta del liquido. Ad esempio, alcuni materiali di tenuta possono deformarsi o deteriorarsi ad alte temperature, causando perdite. Influenza della bassa temperatura: in un ambiente a bassa temperatura, il liquido può diventare viscoso, aumentando la difficoltà di flusso, ma può anche migliorare le prestazioni del materiale di tenuta, migliorando così la tenuta del liquido in una certa misura.
l Pressione. Ambiente ad alta pressione: ad alta pressione, la densità e la viscosità del liquido possono aumentare, migliorando così le prestazioni di tenuta del liquido. Tuttavia, una pressione eccessiva può anche danneggiare il materiale di tenuta e causare perdite. Ambiente a bassa pressione: a bassa pressione, le prestazioni di tenuta del liquido possono essere relativamente deboli, soprattutto se il materiale di tenuta stesso è difettoso o invecchiato, è più probabile che si verifichino perdite.
l Portata. Portata elevata: quando il liquido scorre ad alta velocità, può produrre una grande forza d'impatto sulla superficie di tenuta, causando usura o deformazione del materiale di tenuta, influenzando così la tenuta del liquido. Portata bassa: a una portata bassa, le prestazioni di tenuta del liquido sono relativamente buone, ma questo può anche mascherare alcuni potenziali problemi di tenuta come piccoli difetti del materiale.
3-Problemi di corrosione e deposizione
l L'impatto del blocco sulla tenuta all'aria:
Particelle, sedimenti o crescita microbica nel refrigerante possono causare ostruzioni all'interno del tubo, compromettendo il flusso del refrigerante e riducendo così l'efficienza del raffreddamento.
Sporcizia e incrostazioni: i minerali nel refrigerante possono formare depositi sulla parete interna del tubo dopo un funzionamento prolungato, il che è chiamato "incrostazione". Lo sporco può anche formarsi a causa della precipitazione di particelle solide, cristallizzazione, corrosione o attività microbica. Questa sporcizia ostruirà tubi e piastre fredde, aumenterà la resistenza al flusso e ridurrà l'efficienza del trasferimento di calore.
Problema di schiuma: potrebbe generarsi schiuma nel sistema di raffreddamento a liquido. La schiuma aderirà alla superficie della piastra fredda, con conseguente diminuzione dell'effetto di trasferimento del calore e potrebbe aumentare la resistenza nel funzionamento del sistema, causare corrosione da cavitazione alla pompa, ecc. e danneggiare l'apparecchiatura.
l L'influenza delle correnti parassite sulla tenuta all'aria:
Quando un fluido scorre in un tubo o in uno spazio, i cambiamenti di velocità possono causare la formazione di vortici, specialmente quando il fluido passa attraverso parti strette o ostacoli, è più probabile che si formino vortici. Anche la viscosità e la densità del fluido influenzano la generazione di vortici. I fluidi con viscosità più elevata hanno maggiori probabilità di formare vortici, mentre i fluidi con densità più elevata possono indebolire la formazione di vortici.
Percorsi di perdita: le correnti parassite formano vortici sulle superfici di contatto, che possono creare piccoli percorsi di perdita in fessure o superfici irregolari, con conseguente perdita di gas o liquido.
Usura superficiale: il flusso vorticoso può causare l'usura delle superfici di contatto, specialmente in condizioni di flusso ad alta velocità. Questa usura può ridurre ulteriormente la tenuta all'aria perché le superfici usurate hanno maggiori probabilità di formare nuovi canali di perdita.
Effetti termici: il flusso di correnti parassite genera calore, che può causare la deformazione o l'espansione termica del materiale della superficie di contatto, compromettendo così la tenuta stagna, soprattutto nei sistemi con grandi variazioni di temperatura.
4-Problema di condensa
In determinate condizioni, nelle linee di raffreddamento del liquido potrebbe formarsi della condensa, che potrebbe danneggiare l'apparecchiatura o ridurne l'efficienza. Guasto dell'isolamento: se il materiale isolante del tubo è danneggiato o invecchiato, il calore verrà perso e l'effetto di raffreddamento sarà compromesso. Soprattutto in ambienti a bassa temperatura, il guasto dell'isolamento può causare la formazione di brina o ghiaccio sulla superficie del tubo. Crepe dovute al gelo: in ambienti freddi, se non vengono prese le misure antigelo appropriate, il refrigerante nei tubi potrebbe congelare e causare la rottura dei tubi.
Soluzioni
l Misure di sigillatura: assicurarsi che l'ingresso e l'uscita della tubazione di raffreddamento a liquido siano completamente bloccati per impedire all'aria umida esterna di entrare nel vano batteria.
l Apparecchiatura di deumidificazione: installare un condizionatore d'aria con funzione di deumidificazione oppure utilizzare la funzione di deumidificazione per mantenere l'umidità nel vano batteria entro un intervallo appropriato.
l Controllo della temperatura: installando sistemi di aria condizionata o ventilazione, è possibile controllare la temperatura e l'umidità dell'ambiente in cui si trova l'armadio di accumulo energetico. Ad esempio, la temperatura può essere mantenuta a 20-25 gradi Celsius e l'umidità relativa può essere controllata al 40%-60%.
l Misure di isolamento: semplice isolamento dei rack delle batterie vuoti per impedire all'umidità di penetrare nel vano contenente il gruppo batterie.
Condivideremo regolarmente aggiornamenti e informazioni su tecniche di progettazione termica e alleggerimento, per la vostra consultazione. Grazie per l'interesse verso Walmate.
Il design completamente sigillato del pacco di accumulo di energia è la chiave per garantirne la sicurezza e il funzionamento stabile a lungo termine. La sigillatura è essenzialmente l'uso di un dispositivo per chiudere (sigillare) uno spazio o rendere un giunto a prova di perdite. Il design completamente sigillato può prevenire efficacemente perdite di liquidi e gas all'interno della cella della batteria, il che è fondamentale per garantire il funzionamento sicuro e stabile del sistema di accumulo di energia. Pertanto, durante la progettazione, devono essere prese in considerazione sia la tenuta all'aria che la sigillatura del mezzo liquido.
Nel funzionamento effettivo, la progettazione della tenuta del pacco di accumulo di energia deve considerare in modo completo molteplici fattori quali materiali, processi, apparecchiature di collaudo, condizioni ambientali e processi di produzione per garantire che le sue prestazioni di tenuta possano soddisfare gli standard previsti. Questo articolo spiega la pratica applicativa e i punti chiave della progettazione della tenuta del pacco di accumulo di energia nell'ingegneria effettiva dagli aspetti di tenuta all'aria della scatola del pacco, tenuta al liquido del ciclo di raffreddamento a liquido e mezzo di raffreddamento a liquido.
Articolo precedente: Progettazione della tenuta stagna della scatola del pacco di accumulo di energia
Il design della tenuta aiuta a mantenere stabili la temperatura e la pressione all'interno del pacco di accumulo di energia, il che svolge un ruolo chiave nel normale funzionamento e nelle prestazioni della batteria; e il design della tenuta può ridurre l'impatto dell'ambiente esterno sulla batteria interna, come umidità, polvere e altri inquinanti, ecc., migliorando così l'affidabilità e la durata del sistema. Inoltre, l'uso di materiali e strutture di tenuta appropriati può migliorare efficacemente la resistenza all'usura e all'invecchiamento delle guarnizioni, aumentare la durata dell'intero sistema di accumulo di energia e ridurre i costi di manutenzione.
L'idea generale della progettazione ermetica è quella di analizzare la struttura della scatola per individuare le aree chiave in cui potrebbero verificarsi perdite e quindi adottare misure mirate in base alle prestazioni specifiche e ai requisiti funzionali delle diverse aree.
1-Analisi della struttura della scatola
La scatola non è solo il supporto fisico dei moduli batteria e dei componenti elettrici, ma anche un'importante garanzia per il funzionamento sicuro e affidabile dell'intero sistema di accumulo di energia. È lo "scheletro" del pacco di accumulo di energia, che è generalmente composto da un coperchio superiore, una scatola inferiore, componenti di supporto e una guarnizione Parti e bulloni, ecc.
Figura 1: Diagramma schematico della scatola del pacco di accumulo di energia e aree chiave su cui concentrarsi nella progettazione della sigillatura (ad esempio, contrassegnate con frecce rosse)
Come mostrato nella figura sopra, scopri dove potrebbero verificarsi potenziali perdite:
l Punti di collegamento di più componenti, quali: l'interfaccia di assemblaggio tra il coperchio superiore e la scatola inferiore, l'interfaccia di installazione tra i connettori ad alta e bassa tensione e la scatola, l'interfaccia di installazione tra i componenti esposti e la scatola della batteria, ecc.
l Se per il collegamento vengono utilizzati bulloni, potrebbe esserci anche il rischio di perdite nel punto di installazione e fissaggio, come l'interfaccia elettrica e l'interfaccia di installazione del pannello frontale della scatola.
l Per garantire la tenuta e la protezione della scatola, non devono esserci fori o fessure nel coperchio superiore e nel corpo inferiore della scatola.
Figura 2: Scatola inferiore di raffreddamento a liquido a immersione (telaio in lamiera + piastra inferiore di raffreddamento a liquido in alluminio)
2- Progettazione della tenuta dell'interfaccia di installazione tra il coperchio superiore e la scatola inferiore
La copertura superiore può essere generalmente divisa in due tipi: tipo piatto e tipo di forma speciale. Anche le loro caratteristiche strutturali sono diverse. Ad esempio, materiale composito SMC, alluminio, indipendentemente dal materiale, al fine di ridurre la complessità della struttura autosigillante, la copertura superiore del guscio della batteria La copertura è solitamente di design monoblocco. Inoltre, i requisiti di apertura della copertura superiore devono anche soddisfare i requisiti dell'interfaccia e devono essere indipendenti dall'interfaccia di tenuta per ridurre l'impatto sulla tenuta del pacco batteria. Il design della guarnizione della copertura superiore generalmente segue i seguenti principi:
l La progettazione di parti integrate è stata adottata per evitare la progettazione di parti separate, garantendo così la stabilità delle prestazioni "autosigillanti" del coperchio superiore.
l I fori di posizionamento e le caratteristiche di posizionamento sono progettati sul bordo del coperchio superiore (all'esterno dell'interfaccia di tenuta tra il coperchio superiore e il vassoio inferiore).
l L'interfaccia di tenuta tra il coperchio superiore e il corpo inferiore della scatola richiede una superficie di corrispondenza che soddisfi i requisiti di tenuta "uniforme" e "continua".
Attualmente, le soluzioni principali per la scatola inferiore del pacco di accumulo di energia sono: scatola in lamiera + piastra di raffreddamento a liquido, scatola pressofusa + piastra di raffreddamento a liquido, scatola integrata nel profilo, scatola integrata pressofusa, ecc. Tra queste, la scatola integrata nel profilo e altre soluzioni Al contrario, presenta i vantaggi di una buona capacità di carico del canale di flusso e di un basso costo di apertura dello stampo, ed è ampiamente utilizzata. La scelta del processo di saldatura ha una grande influenza sulle prestazioni di tenuta. Per saldature di materiali e spessori diversi, la scelta di un metodo di saldatura adatto può migliorare efficacemente la qualità della saldatura per garantire la resistenza complessiva e le prestazioni di tenuta del sistema.
Inoltre, la progettazione della tenuta della scatola inferiore deve seguire i seguenti principi di tenuta:
l Per la costruzione del telaio vengono utilizzati profili a sezione chiusa e nei giunti si impiega la tecnologia di collegamento lineare autosigillante, come la tecnologia di saldatura CMT.
l I vassoi per batterie realizzati con profili in alluminio devono essere progettati con uno o più strati continui di colloide sigillante.
l Nel caso di una piastra di raffreddamento a liquido integrata nella scatola inferiore, è necessario prendere in considerazione l'impiego di guarnizioni colloidali o tecnologie di collegamento lineare autosigillanti, come la tecnologia di saldatura a frizione e agitazione FSW.
l L'interfaccia di tenuta tra il coperchio superiore e il corpo inferiore della scatola necessita della superficie corrispondente per soddisfare i requisiti di tenuta "uniforme" e "continua". Se necessario, l'interfaccia di tenuta deve essere lavorata e lucidata.
Figura 3: Forme di tenuta comuni tra il coperchio superiore e la scatola inferiore
Di solito, il coperchio superiore e la scatola inferiore del Pack box di accumulo di energia adottano una flangia piegata e un design con guarnizione di tenuta, come mostrato nella Figura 2. Il coperchio superiore, il corpo della scatola inferiore e la guarnizione di tenuta sono completamente compattati e accoppiati tramite bulloni di fissaggio per garantire che il Pack box soddisfi i requisiti pertinenti di IP67.
3- Progettazione della tenuta delle interfacce elettriche e di comunicazione e dell'interfaccia di installazione del pannello frontale della scatola inferiore
Il pannello frontale della scatola (come mostrato nella Figura 3) è dotato di fori sul profilo estruso per l'installazione di interfacce elettriche e di comunicazione per realizzare funzioni quali la trasmissione di corrente, l'interazione delle comunicazioni e il controllo di sicurezza.
Figura 4: Interfaccia di installazione elettrica, di comunicazione e del pannello frontale del mobile inferiore
La tenuta all'aria dell'interfaccia di installazione tra la scatola e le interfacce elettriche, di comunicazione e di altro tipo deve seguire i seguenti principi:
l La forma dell'interfaccia è progettata in modo aerodinamico per ridurre la possibilità di accumulo e permeazione di gas e liquidi nell'interfaccia.
l L'allineamento preciso evita spazi vuoti causati dal disallineamento delle interfacce durante l'installazione.
l Sigillare preventivamente l'interfaccia prima dell'installazione e aggiungere cuscinetti antivibranti o sigillanti per migliorare l'effetto di tenuta iniziale o ridurre i guasti di tenuta causati dalle vibrazioni.
Inoltre, in termini di selezione degli elementi di fissaggio, vengono utilizzati elementi di fissaggio ad alta resistenza e coppia elevata, che vengono serrati più volte durante il processo di installazione per garantire la tenuta dell'interfaccia. Ad esempio, se viene utilizzato un dado a saldare di testa, la sua caratteristica è che può essere collegato direttamente al foro della parete della parte collegata (il pannello frontale della scatola) per la saldatura di testa. Questa progettazione strutturale può migliorare significativamente la tenuta stagna della parte di collegamento.
Figura 5: Utilizzo di dadi saldati a testa per aumentare la tenuta stagna
4-Selezione del sigillo
La progettazione e la selezione delle guarnizioni sono fondamentali in quanto influenzano direttamente l'affidabilità e la durata del sistema. Di seguito sono riportati i fattori chiave da considerare quando si progettano e si selezionano le guarnizioni per i sistemi di raffreddamento a liquido per l'accumulo di energia:
l Il materiale di tenuta deve avere una certa compatibilità chimica e di pressione, ed essere in grado di resistere all'intervallo di temperatura di esercizio del sistema, inclusi ambienti ad alta e bassa temperatura. La selezione del materiale della tenuta dipende dall'ambiente di utilizzo e dai requisiti di durata di servizio. I materiali di tenuta comuni includono gomma, politetrafluoroetilene (PTFE), nylon, metallo, ecc.
l Libertà di perdite: la guarnizione deve essere in grado di adattarsi alla leggera deformazione che può verificarsi nel sistema durante il funzionamento per garantire un buon effetto di tenuta in varie condizioni di lavoro. In genere, la deformazione della guarnizione deve essere maggiore del 30% e inferiore al 60% e la pressione dell'interfaccia di tenuta deve essere maggiore di 30 kPa.
Condivideremo regolarmente aggiornamenti e informazioni su tecniche di progettazione termica e alleggerimento, per la vostra consultazione. Grazie per l'interesse verso Walmate.
Nei veicoli elettrici puri, il peso del pacco batteria rappresenta circa il 30% del peso a vuoto. La leggerezza del pacco batteria è di grande importanza per migliorare l'autonomia di crociera del veicolo. Pertanto, la ricerca sull'elevata energia specifica dei pacchi batteria è una delle principali direzioni di ricerca attuali per i veicoli a nuova energia ed è anche il modo principale per ottenere veicoli elettrici leggeri. L'alleggerimento dei pacchi batteria di potenza può essere effettuato in due direzioni: miglioramento delle singole celle La densità energetica del pacco batteria è ottimizzata e gli accessori correlati del pacco batteria sono ottimizzati.
Lo sviluppo di pacchi batteria leggeri multi-materiale mira a ridurre il peso del pacco batteria, aumentare la densità energetica e l'autonomia di crociera, garantendo al contempo sicurezza e affidabilità utilizzando una varietà di materiali leggeri. Tra i componenti principali del pacco batteria, il corpo della cella della batteria ha la massa più elevata, seguito dalla scatola inferiore del pacco, dal coperchio superiore e dai componenti integrati BMS.
1-Design leggero del coperchio del pacco batteria
Il coperchio superiore della scatola della batteria si trova sopra la scatola della batteria di alimentazione e non è influenzato dai lati della scatola della batteria di alimentazione e non influenzerà la qualità dell'intero pacco batteria. Le sue funzioni includono principalmente la sigillatura e la protezione. Per migliorare l'efficienza energetica dell'intero veicolo, verranno presi in considerazione anche materiali leggeri nella progettazione. L'uso di materiali leggeri, come leghe di alluminio e materiali compositi (SMC, FRP, ecc.), può ridurre significativamente il peso del pacco batteria.
Inoltre, la progettazione strutturale della copertura superiore deve anche considerare l'efficienza di produzione e i requisiti di produzione di massa. Quando la struttura è molto irregolare, potrebbe essere difficile utilizzare la formatura o la piegatura e la saldatura su misura. La progettazione della copertura superiore deve anche considerare la connessione e la cooperazione con altri componenti come la scatola inferiore e le parti strutturali di tenuta per garantire la stabilità strutturale e l'affidabilità dell'intera scatola della batteria.
2-Design leggero del guscio inferiore del pacco batteria
La lega di alluminio è un materiale ideale per i gusci dei pacchi batteria grazie alla sua bassa densità, elevata resistenza specifica, buona stabilità termica, forte resistenza alla corrosione, buona conduttività termica, non magnetico, facile stampaggio e alto valore di riciclaggio. I materiali in lega di alluminio comunemente utilizzati includono 6061-T6, 6005A-T6 e 6063-T6. Questi materiali hanno diversi limiti di snervamento e resistenze alla trazione e possono soddisfare diverse esigenze strutturali.
Il guscio del pacco batteria è solitamente composto da un telaio profilato in lega di alluminio e da una piastra inferiore, che viene saldata utilizzando profili estrusi in lega di alluminio serie 6. Fattori come le dimensioni e la complessità della sezione del profilo, lo spessore della parete, ecc. devono essere considerati durante la progettazione per adattarsi a diversi requisiti strutturali e funzionali. Ad esempio, componenti come telai, partizioni centrali, pannelli del pavimento, travi, ecc. possono adottare diversi design di sezione trasversale.
Attraverso una progettazione strutturale ragionevole e metodi di collegamento, la resistenza complessiva del guscio può essere efficacemente garantita, la difficoltà di lavorazione può essere ridotta e il peso del guscio può essere ridotto:
l Pareti sottili: adottando un design a pareti sottili e utilizzando rinforzi per soddisfare i requisiti di resistenza, è possibile ridurre efficacemente il peso del materiale.
l Svuotamento: introduzione di sezioni cave nella progettazione strutturale per ridurre la densità del materiale.
l Ottimizzazione delle dimensioni: ottimizza le dimensioni del pacco batteria per ridurre l'utilizzo non necessario di materiali.
l Ottimizzazione della topologia: ridurre lo spazio occupato dai materiali ottimizzando la disposizione dei componenti interni del pacco batteria.
l Design modulare integrato: integra piastre di raffreddamento, golfari di sollevamento del pacco batteria e altri componenti nella scatola per ridurre il numero e il peso dei singoli componenti.
3-Produzione di tecnologia leggera
l Modellazione del materiale
Attualmente, ci sono tre categorie principali di processi di formatura del materiale della scatola della batteria: stampaggio, pressofusione di lega di alluminio ed estrusione di lega di alluminio. Il flusso di processo complessivo della scatola della batteria di potenza include processi di stampaggio e connessione del materiale, tra cui il processo di stampaggio del materiale è il processo chiave della scatola della batteria di potenza. Attualmente, la cassa superiore è principalmente stampata e i processi principali della cassa inferiore sono lo stampaggio per estrusione e la pressofusione di lega di alluminio.
l tecnologia di connessione
Il processo di collegamento della scatola della batteria è fondamentale nella produzione di nuovi veicoli energetici e prevede una serie di tecnologie e metodi per garantire la resistenza strutturale e la tenuta della scatola della batteria.
La saldatura è il principale processo di collegamento nella lavorazione delle scatole delle batterie ed è ampiamente utilizzato. Include principalmente i seguenti metodi:
① Saldatura a fusione tradizionale: come TIG (saldatura a gas inerte al tungsteno) e MIG (saldatura a gas inerte metallico). La saldatura TIG ha bassa velocità e alta qualità. È adatta per la saldatura a punti e la saldatura a traiettoria complessa. È spesso utilizzata per la saldatura su misura del telaio e la saldatura di piccoli pezzi a trave laterale. La saldatura MIG ha alta velocità e forte capacità di penetrazione ed è adatta per la saldatura a cerchio completo all'interno dell'assemblaggio della piastra inferiore del telaio.
② Saldatura a frizione e agitazione: la saldatura si ottiene generando calore tramite attrito. Ha le caratteristiche di buona qualità del giunto e alta efficienza produttiva.
③Tecnologia di trasferimento del metallo freddo: è adatta per materiali a piastra sottile. Non c'è apporto di calore durante il processo di saldatura, riducendo la deformazione.
④Saldatura laser: alta precisione, alta velocità, adatta per la saldatura di strutture complesse.
⑤ Saldatura a perno e saldatura a proiezione: utilizzata per la connessione rapida di parti specifiche. La saldatura a perno è fissata da perni e dadi, mentre la saldatura a proiezione è collegata mediante protuberanze a pressione.
Il metodo di collegamento meccanico risolve principalmente i problemi di facile saldatura e di slittamento del filo di materiali a piastra sottile durante la saldatura, tra cui:
① Dado per rivetto cieco: utilizzato per collegare la superficie di tenuta del telaio della scatola e la piastra inferiore della cavità interna. Presenta i vantaggi di un'elevata efficienza di fissaggio e di un basso costo di utilizzo. Adatto per collegamenti filettati tra piastre sottili e altri componenti.
②Inserto filettato in filo: utilizzato per rinforzare i fori delle viti in alluminio o altri corpi a bassa resistenza, migliorare la capacità portante delle viti e la distribuzione della forza delle filettature ed è adatto per i fori di montaggio dei moduli batteria e per i fori di montaggio delle superfici di tenuta. Rispetto ai dadi per rivetti ciechi, gli inserti filettati in filo sono più resistenti e facili da riparare, ma generalmente non sono adatti per installazioni a parete sottile.
Condivideremo regolarmente aggiornamenti e informazioni su tecniche di progettazione termica e alleggerimento, per la vostra consultazione. Grazie per l'interesse verso Walmate.
Per far fronte alle richieste del mercato come grandi intervalli, iterazioni rapide e linee di prodotto ricche, garantendo al contempo riduzione dei costi, miglioramento dell'efficienza e garanzia della qualità, per l'industria automobilistica, la standardizzazione dei prodotti - la piattaforma dei veicoli è senza dubbio una buona strategia. Attraverso la piattaforma delle batterie, la stessa soluzione di pacco batteria può essere abbinata a modelli diversi, oppure possono essere abbinate soluzioni di pacchi batteria composte dallo stesso tipo di celle della batteria e strutture simili. Ciò significa che possono essere standardizzate quante più parti possibili, il che può accorciare il ciclo di sviluppo, risparmiare sui costi, semplificare le linee di produzione e migliorare l'efficienza della produzione.
Primo: piattaforma della batteria
La soluzione della piattaforma batteria è favorevole alla pianificazione complessiva dei prodotti, alla riduzione dei costi e all'ottimizzazione della capacità produttiva. In base alla strategia della piattaforma batteria della piattaforma del veicolo, è necessario considerare l'intersezione e la larghezza di banda dei requisiti di ciascun modello della piattaforma e utilizzare il minor numero possibile di batterie e soluzioni di batterie per essere compatibili con il maggior numero possibile di modelli. Nello sviluppo dell'architettura di progetti puramente elettrici, è fondamentale disporre ragionevolmente il pacco batteria di potenza integrato. Gli elementi di lavoro specifici includono requisiti di potenza e prestazioni di potenza, sicurezza in caso di collisione, posizione e spazio di layout, ecc.
1-Confini delle dimensioni spaziali e standardizzazione delle celle della batteria
l Posizioni disponibili per i pacchi batteria
Attualmente, la disposizione della batteria di alimentazione principale è sotto il pavimento, compresi sotto i sedili anteriori, sotto i sedili posteriori, nel canale centrale e nel poggiapiedi. Questa disposizione può massimizzare l'area disponibile, aiutare ad abbassare il baricentro del veicolo, migliorare la stabilità di guida del veicolo e ottimizzare il percorso di trasmissione della forza di collisione.
Figura 1: Disposizione del pacco batteria durante lo sviluppo dei veicoli elettrici
l Evoluzione della disposizione dello spazio del pacco batteria
Pacco batteria diviso: viene adottato un layout dello spazio del pacco batteria diviso, come la serie JAC Tongyue. Il modulo energetico è costituito da due pacchi batteria, uno posizionato nella posizione originale del serbatoio del carburante e l'altro posizionato nel bagagliaio dove è riposta la ruota di scorta.
Inoltre, gli ingegneri stanno esplorando costantemente lo spazio utilizzabile all'interno dell'architettura originale dei veicoli a carburante, con conseguenti disposizioni dei pacchi batteria che assumono le forme di "工" , "T" e "土" .
Questo tipo di design è una modifica minore di un veicolo a carburante tradizionale. Lo spazio è molto limitato e il volume e il peso del pacco batteria che può essere caricato sono molto limitati, quindi la capacità è difficile da aumentare e l'autonomia di crociera non è elevata.
Pacco batteria integrato: si tratta di un nuovo concetto di progettazione del prodotto. Il design dell'intero veicolo ruota attorno al componente principale, il pacco batteria. Il pacco batteria è progettato in modo modulare e disposto in piano sul telaio del veicolo per massimizzare lo spazio disponibile.
l Disposizione del punto di installazione del pacco batteria
La disposizione ragionevole del pacco batteria è fondamentale e i fattori limitanti nella progettazione sono l'altezza da terra, la percorribilità, la sicurezza in caso di collisione, i requisiti di potenza e molti altri aspetti.
Figura 2: Vincoli di progettazione delle dimensioni del pacco batteria
La piattaforma del veicolo deve definire la categoria, il livello e il posizionamento di ciascun modello di veicolo all'interno della piattaforma, quindi determinare le dimensioni e il passo del veicolo. Il layout del veicolo scompone l'involucro delle dimensioni del pacco batteria nelle direzioni X, Y e Z in base allo spazio del veicolo. La batteria deve essere disposta all'interno dell'involucro dato del veicolo per garantire che non vi siano interferenze tra i vari sistemi del veicolo. L'indice di peso a vuoto può scomporre i requisiti di qualità del sistema del pacco batteria.
In termini di dimensioni della batteria, la progettazione dei pacchi batteria di potenza non può evitare rigidi indicatori di riferimento come lo spazio del veicolo e il peso a vuoto, il che significa che esiste una soglia per la progettazione delle celle della batteria. Vincolata da questa soglia, la dimensione della cella della batteria sarà concentrata in un certo intervallo, come: la lunghezza delle celle della batteria quadrate varia da 150-220 mm, la larghezza varia da 20-80 mm e l'altezza varia intorno ai 100 mm. La tendenza mutevole delle specifiche delle dimensioni delle celle della batteria è il risultato della relazione complementare tra la piattaforma del veicolo e la standardizzazione della batteria.
Tuttavia, le strategie della piattaforma della batteria, i modelli dei veicoli e la comprensione della standardizzazione di vari produttori di automobili sono diversi, con conseguenti differenze significative nelle attuali soluzioni di prodotto. Ad esempio, la strategia di standardizzazione di BYD è quella di sostituire completamente la batteria blade, la cui dimensione è bloccata a 960*13,5 (14)*90 (102) mm e la tensione della singola cella è 3,2/3,3 V.
2- Sviluppo di limiti di resistenza e soluzioni di capacità della batteria
La batteria di potenza fornisce energia per il viaggio del veicolo: la capacità della batteria, la profondità di scarica e la densità di energia influenzano la quantità di potenza disponibile. Per soddisfare le esigenze di diversi modelli, la differenza nel consumo di energia dei modelli è diventata una preoccupazione importante. L'autonomia di crociera del veicolo sarà influenzata da fattori quali la trazione elettrica, la batteria, il peso a vuoto, la resistenza al vento, la resistenza meccanica, il consumo di energia a bassa tensione e il recupero di energia. La possibilità di condividere soluzioni di batteria tra modelli con grandi differenze nel consumo di energia è debole, quindi è necessario sviluppare soluzioni di alimentazione della batteria personalizzate, tra cui dimensioni della batteria, qualità, potenza e ottimizzazione delle prestazioni di potenza per soddisfare i requisiti delle prestazioni di crociera.
In base ai vincoli dell'autonomia elettrica pura della piattaforma di produzione del veicolo, la scarica netta richiesta dalla batteria sarà influenzata dal consumo di energia di diversi modelli. È necessario confermare la distribuzione del consumo di energia di ciascun modello sulla piattaforma per convertire ulteriormente la larghezza di banda del consumo di energia nella distribuzione della domanda della batteria, quindi determinare il piano di alimentazione della batteria richiesto dalla piattaforma.
3-Limite di prestazione di potenza
Le prestazioni dinamiche del veicolo completo includono le performance in termini di accelerazione, velocità costante e modalità di risparmio energetico a diversi livelli di SOC (State of Charge) e temperature ambientali. Questo si traduce, a livello di batteria, nelle caratteristiche potenza-tensione della batteria stessa a diversi SOC e temperature. La potenza della batteria corrisponde alla richiesta di potenza del sistema di propulsione del veicolo, mentre la tensione corrisponde alla tensione nominale richiesta dal motore di trazione.
In genere, la valutazione delle soluzioni per le batterie per l'intera piattaforma del veicolo inizia dal tempo di accelerazione di 100 chilometri a temperatura normale e potenza elevata e dalla decomposizione dell'indicatore della batteria, e si estende gradualmente alla decomposizione dell'indicatore della batteria sull'intera autonomia e in tutte le condizioni operative.
SECONDO: Sviluppo della scatola della batteria
1-Integrazione e modularizzazione della batteria
Ottimizzare la progettazione dei moduli batteria, migliorare l'integrazione e la modularità dei pacchi batteria, ridurre i componenti inattivi e aumentare la densità energetica dei pacchi batteria.
Le tecnologie di integrazione dei pacchi batteria attualmente più diffuse includono CTP, CTB, CTC e altre forme. La forma, il materiale e la combinazione delle parti sono cambiati con l'avanzamento della tecnologia di integrazione. La direzione generale è integrazione e integrazione. Riducendo il numero di parti indipendenti e utilizzando una parte grande per sostituire più parti, si formano componenti più grandi e più funzionali.
2-Progettazione della scatola della batteria
La custodia della batteria è il supporto dell'assemblaggio del sistema di batterie di potenza, svolge un ruolo chiave nel funzionamento sicuro e nella protezione del prodotto e influisce direttamente sulla sicurezza dell'intero veicolo. La progettazione strutturale della custodia della batteria include principalmente la selezione dei materiali del guscio per il guscio superiore, il guscio inferiore e altri componenti della custodia della batteria e la selezione delle soluzioni del processo di fabbricazione. Il coperchio superiore della custodia della batteria svolge principalmente un ruolo di tenuta e non è soggetto a molta forza; la custodia inferiore della custodia della batteria è il supporto dell'intero prodotto del sistema di batterie di potenza e il modulo della batteria è principalmente disposto nella custodia inferiore. Pertanto, devono esserci misure strutturali come scanalature e deflettori incorporati all'interno della custodia della batteria per garantire che il modulo della batteria sia fissato in modo affidabile quando il veicolo è in marcia e non vi sia alcun movimento nelle direzioni anteriore, posteriore, sinistra, destra, su e giù, in modo da evitare impatti sulle pareti laterali e sul coperchio superiore e influire sulla durata della custodia della batteria.
Figura 3: Soluzione scatola inferiore batteria, telaio a-skin, saldatura b-FSW + telaio, saldatura c-FSW + telaio
l Progettazione della struttura del punto di installazione del pacco batteria e fissaggio della connessione
Il punto di installazione del pacco batteria di solito adotta una struttura a trave di montaggio, che attraversa la parte anteriore e posteriore, e l'estremità anteriore è collegata alla trave longitudinale della cabina anteriore per formare una struttura a trave chiusa efficace e coerente. I punti di installazione sono ragionevolmente disposti in base alla distribuzione del peso del pacco batteria. Il pacco batteria e il veicolo sono fissati in vari modi, tra cui fissaggio tramite bulloni, fissaggio meccanico + collegamento ibrido con giunto adesivo, collegamento a scatto, ecc.
Figura 4: Disposizione del pacco batteria e sezione di installazione
I pacchi batterie di potenza sono generalmente installati sul veicolo tramite più strutture di ganci. La lavorazione dei ganci deve sopportare non solo il peso considerevole del pacco batterie, ma anche le sollecitazioni generate dalla marcia dell'auto su strade irregolari, come ciottoli e buche profonde. Queste condizioni di durata e di uso improprio pongono requisiti più elevati sulla resistenza della struttura dei ganci.
Figura 5: Diverse soluzioni di collegamento del gancio di sollevamento: a Gancio di sollevamento saldato b Gancio di sollevamento con telaio estruso in alluminio
l Struttura di sicurezza e protezione della scatola della batteria
Resistenza meccanica e protezione: la scatola della batteria deve avere una resistenza meccanica sufficiente a proteggere le batterie al suo interno da urti e impatti meccanici. La scatola della batteria deve essere in grado di resistere a vibrazioni, estrusione e urti meccanici per garantire la sicurezza della batteria in varie condizioni.
Protezione dalle collisioni: la progettazione della custodia della batteria deve tenere in considerazione la sicurezza dalle collisioni, in particolare per le collisioni laterali e inferiori. Di solito è realizzata in alluminio o acciaio e collegata al vassoio inferiore tramite un telaio esterno per fornire rigidità strutturale e migliorare le capacità di assorbimento dell'energia di collisione. Inoltre, devono essere progettate strutture di assorbimento delle collisioni appropriate per prevenire la deformazione della custodia della batteria e danni alle celle della batteria.
Impermeabile, antipolvere e resistente alla corrosione: la scatola della batteria deve essere impermeabile e antipolvere e solitamente utilizza guarnizioni di tenuta di livello IP67 per garantire la tenuta stagna. Inoltre, dovrebbero essere prese in considerazione anche misure anticorrosione, come la spruzzatura di rivestimento in PVC all'esterno per migliorare la resistenza alla corrosione.
Progettazione antideflagrante e di scarico della pressione: quando una batteria esplode, l'energia deve essere rilasciata in modo concentrato e direzionale tramite dispositivi quali valvole antideflagranti bilanciate per evitare di entrare nella cabina del cliente. Inoltre, devono essere adottate misure antideflagranti (quali la parziale distruzione strutturale) per impedire la rottura complessiva dell'apparecchiatura.
l Design sigillato
Il design della superficie di tenuta tra il coperchio superiore e la cassa inferiore della scatola della batteria svolge un ruolo importante nelle prestazioni di tenuta e il suo design deve essere progettato insieme alla struttura della scatola della batteria e all'anello di tenuta. La superficie di tenuta deve essere mantenuta sullo stesso piano il più possibile per evitare troppe strutture curve. Poiché il coperchio superiore e la cassa inferiore sono collegati da bulloni, viene utilizzato un gran numero di bulloni, quindi è particolarmente importante garantire la coassialità dei fori. Mentre si dispongono ragionevolmente le posizioni dei fori dei bulloni, le dimensioni della posizione devono essere il più possibile rotonde e disposte simmetricamente nelle direzioni X e Y. La selezione del numero di bulloni di collegamento deve essere considerata in modo completo in base al livello di tenuta e alla quantità di carico di lavoro di smontaggio e montaggio.
Figura 6: Progettazione della tenuta della scatola superiore e inferiore, 1-coperchio superiore della batteria 2-guarnizione di tenuta 3-coperchio inferiore della batteria 4-condotto metallico
l Sicurezza elettrica e protezione da cortocircuito
Affidabilità della connessione: i connettori all'interno del vano batteria devono avere la corretta polarità per garantire la capacità di sovracorrente del vano batteria e l'affidabilità dei collegamenti elettrici/meccanici, comprese le misure di rilassamento, ecc.
Progettazione di isolamento elettrico e resistenza alla tensione: la progettazione del modulo adotta una doppia protezione di isolamento. La cella della batteria stessa ha uno strato di pellicola blu della cella della batteria e una toppa superiore della cella della batteria per soddisfare i requisiti di isolamento e resistenza alla tensione. La protezione di isolamento e resistenza alla tensione è impostata tra la piastra terminale/laterale e la cella della batteria e tra la cella della batteria e la superficie di montaggio inferiore.
l Progettazione della gestione termica
Lo sviluppo della gestione termica della batteria attraversa l'intero ciclo di progettazione e sviluppo del sistema del pacco batteria, inclusa la progettazione del controllo della temperatura della batteria, della piastra fredda, del sistema di tubazioni, ecc. L'obiettivo principale della progettazione del sistema di gestione termica della batteria è garantire che il sistema della batteria funzioni a una temperatura di esercizio relativamente adatta tramite il controllo del riscaldamento o del raffreddamento, tenendo conto della disposizione dello spazio, dei costi di progettazione, della leggerezza, ecc., riducendo al contempo la differenza di temperatura tra le celle per garantire la coerenza.
Condivideremo regolarmente aggiornamenti e informazioni su tecniche di progettazione termica e alleggerimento, per la vostra consultazione. Grazie per l'interesse verso Walmate.
Il pacco batteria è la fonte energetica principale dei nuovi veicoli energetici, che fornisce potenza motrice all'intero veicolo. In genere valutiamo i vantaggi e gli svantaggi della tecnologia del pacco batteria in base alle dimensioni di efficienza (densità energetica), sicurezza, costi di produzione e manutenzione.
Nella progettazione delle batterie, la tensione di una singola cella è di soli 3-4 V circa, mentre la tensione richiesta dai veicoli elettrici è di almeno 100 V. Le nuove auto ora hanno persino una tensione di 700 V/800 V e la potenza in uscita è generalmente di 200 W, quindi la batteria deve essere potenziata. Per soddisfare i requisiti di corrente e tensione dei veicoli elettrici, è necessario collegare celle diverse in serie o in parallelo.
Il pacco batteria è composto da celle, sistemi elettronici ed elettrici, sistemi di gestione termica, ecc., che sono racchiusi da una struttura del telaio della batteria: piastra di base (vassoio), telaio (telaio metallico), piastra di copertura superiore, bulloni, ecc. Come "confezionare" questi componenti e sistemi in un tutto in modo più efficiente e sicuro è sempre stato un argomento di continua ricerca ed esplorazione per l'intero settore.
Articolo precedente: Innovazione e sviluppo della tecnologia di integrazione delle batterie
L'origine della tecnologia dei gruppi di batterie di potenza può essere fatta risalire agli anni '50, e ha avuto origine nell'ex Unione Sovietica e in alcuni paesi europei. Questa tecnologia è stata originariamente utilizzata come concetto di ingegneria e produzione per determinare le somiglianze fisiche delle parti (percorsi di processo universali) e stabilire la loro produzione efficiente.
Il fulcro della Group Technology (GT) è identificare ed esplorare le somiglianze di cose correlate nelle attività di produzione, classificare problemi simili in gruppi e cercare soluzioni ottimali relativamente unificate per risolvere questo gruppo di problemi per ottenere benefici economici. Nel campo delle batterie di potenza, la group technology riguarda principalmente la tecnologia di integrazione delle batterie da singole celle in pacchi batteria (Pack), tra cui struttura, gestione termica, progettazione della connessione elettrica e tecnologia del sistema di gestione della batteria (BMS).
La prima tecnologia di raggruppamento nel campo automobilistico è MTP (Module To Pack), il che significa che le celle vengono prima integrate nei moduli e poi i moduli vengono integrati nei Pack. Questa tecnologia è caratterizzata da moduli staccabili e sostituibili, che hanno una buona manutenibilità, ma l'efficienza di raggruppamento è bassa. Con lo sviluppo della tecnologia, la tecnologia di raggruppamento ha subito una trasformazione da MTP a CTP (Cell To Pack). La tecnologia CTP si riferisce alla tecnologia di integrazione diretta delle celle nei Pack, eliminando la tradizionale struttura del modulo e migliorando l'efficienza di raggruppamento e l'efficienza di produzione. Negli ultimi anni, il settore sta anche esplorando tecnologie di raggruppamento come CTC (Cell To Chassis), CTB (Cell To Body & Bracket) e MTB (Module To Body) con maggiore efficienza di integrazione.
Nel campo delle batterie di potenza e dell'accumulo di energia elettrochimica, i principali progressi tecnologici delle batterie al litio derivano dall'innovazione strutturale e dall'innovazione dei materiali. Il primo consiste nell'ottimizzare la struttura di "cella-modulo-pacco batteria" a livello fisico per raggiungere l'obiettivo di migliorare sia la densità di energia del volume del pacco batteria sia la riduzione dei costi; il secondo consiste nell'esplorare i materiali delle batterie a livello chimico per raggiungere l'obiettivo di migliorare sia le prestazioni delle singole celle sia la riduzione dei costi. Questo articolo si concentra sull'impatto delle diverse tecnologie di integrazione strutturale sulla tecnologia di produzione del pacco batteria e sulla direzione dello sviluppo innovativo dal punto di vista dell'integrazione strutturale del pacco batteria. Le attuali tecnologie chiave per l'integrazione delle batterie di potenza sono illustrate nella figura seguente:
1-MTP è stato eliminato
All'inizio dell'attuale ondata di sviluppo di veicoli elettrici, sono stati lanciati molti modelli di veicoli a nuova energia da petrolio a elettrico. Essi continuano la disposizione spaziale e il design stilistico dei tradizionali veicoli a benzina. Gli ingegneri hanno assemblato un modulo di celle di batteria relativamente grande collegando un certo numero di singole celle di batteria in serie/parallelo, e poi hanno posizionato diversi di tali moduli di celle di batteria nel pacco batteria, che è il familiare pacco batteria "MTP". Poiché il pacco batteria deve essere "confezionato" più di due volte, il numero di componenti richiesti è estremamente elevato e il pacco batteria appare come "tre strati all'interno e tre strati all'esterno", con troppe parti ridondanti che occupano più volume e peso del sistema, con conseguente scarsa densità di energia volumetrica e densità di energia gravimetrica del pacco batteria "MTP". Inoltre, poiché la progettazione dei veicoli a benzina non ha specificamente riservato spazio per la batteria, il sistema di batterie può essere solo "schiacciato dove si adatta", con conseguente scarsa competitività del prodotto ed esperienza utente.
Dal lancio delle nuove piattaforme di veicoli elettrici intelligenti rappresentate da Tesla, i veicoli elettrici puri nativi hanno consentito di installare pacchi batteria in posizioni spaziali ideali in modo più efficiente e regolare, i sistemi tri-elettrici possono essere disposti in modo più ragionevole e l'architettura elettronica ed elettrica del veicolo e la progettazione della gestione termica possono essere integrate in modo più efficiente. La forza del prodotto del veicolo in termini di efficienza energetica, resistenza e intelligenza è stata notevolmente migliorata.
2-Era della tecnologia integrata 2.0——CTP
Il pacco batteria con struttura MTP presenta un problema significativo di utilizzo dello spazio. L'utilizzo dello spazio della cella della batteria rispetto al modulo è dell'80%, l'utilizzo dello spazio del modulo rispetto al pacco batteria è del 50% e l'utilizzo complessivo dello spazio è solo del 40%. Il costo dell'hardware del modulo rappresenta circa il 14% del costo totale della batteria. Questa struttura a basso utilizzo dello spazio non può soddisfare i requisiti di sviluppo dei nuovi veicoli energetici. Nell'ambito dell'idea di integrazione cella della batteria → modulo → pacco batteria → carrozzeria, se il veicolo desidera caricare quanta più potenza possibile nello spazio limitato del telaio e migliorare l'utilizzo del volume, è necessario considerare la standardizzazione di ogni fase di integrazione. Poiché la domanda di mercato per l'autonomia di guida continua ad aumentare, il volume di un singolo modulo batteria continua ad aumentare, il che porta indirettamente all'emergere della soluzione CTP.
La tecnologia della struttura CTP è nata per tenere in considerazione la sicurezza, la complessità del packaging, la riduzione dei costi, ecc. Con la premessa di garantire la sicurezza della cella della batteria, la tecnologia CTP riduce i cavi interni e le parti strutturali. Rispetto alla tecnologia MTP, la tecnologia CTP non ha una struttura modulare e confeziona direttamente la cella della batteria in un pacco batteria prima di installarlo sul veicolo.
Attualmente ci sono due idee principali. Una è quella di considerare il Pack come un grande modulo completo che sostituisce la struttura di più piccoli moduli al suo interno, rappresentata da CATL; l'altra è quella di considerare l'utilizzo di una soluzione senza modulo durante la progettazione e progettare la batteria stessa come partecipante alla forza, come la batteria blade di BYD.
Il punto centrale della tecnologia CTP è l'eliminazione del design del modulo, con le celle della batteria che si combinano direttamente con il guscio, riducendo l'uso delle piastre terminali e dei separatori. I problemi che ne derivano riguardano il fissaggio del pacco batteria e la gestione termica.
In effetti, il prodotto originale del pacco batteria CTP non era un progetto completamente privo di moduli, ma un progetto che univa i piccoli moduli originali in tre moduli grandi e due moduli medi, e c'erano anche piastre terminali in alluminio ad entrambe le estremità, quindi in teoria è ancora MTP, ma ci sono davvero grandi miglioramenti nella struttura.
Dopo l'introduzione di CTP 3.0, CATL ha presentato un metodo di produzione più avanzato, ottenendo un design completamente privo di moduli. Le celle della batteria sono state modificate da un orientamento verticale lungo l'altezza a una posizione orizzontale. Inoltre, è stata implementata una nuova soluzione di raffreddamento tra le celle della batteria, che non solo dissipa il calore ma fornisce anche funzioni di supporto, ammortizzazione, isolamento e controllo della temperatura. Anche il guscio inferiore è stato progettato con una funzione di fissaggio limitante.
Figura 1: Confronto tra la batteria CATL Kirin CTP2.0 e CTP3.0
3-Tecnologia integrata 3.0 Era—CTB, CTC
l Tecnologia CTB
La tecnologia CTP è un importante passo avanti nell'innovazione della struttura della batteria, ma non ha fatto una svolta nel pacco batteria stesso. Nella tecnologia CTP, il pacco batteria è ancora un componente indipendente. Rispetto alla strategia semplificata di CTP per i pacchi batteria, la tecnologia CTB combina il pannello del pavimento della carrozzeria e il coperchio del pacco batteria in uno. La superficie di tenuta piatta formata dal coperchio della batteria, dalla soglia della portiera e dalle travi anteriore e posteriore sigilla l'abitacolo passeggeri con sigillante e il fondo è assemblato con la carrozzeria attraverso il punto di installazione. Quando si progetta e si produce il pacco batteria, il sistema della batteria è integrato con la carrozzeria nel suo insieme, i requisiti di tenuta e impermeabilità della batteria stessa possono essere soddisfatti e la sigillatura della batteria e dell'abitacolo passeggeri è relativamente semplice e i rischi sono controllabili.
In questo modo, la struttura a sandwich originale di "coperchio pacco batteria-cella batteria-vassoio" si trasforma in una struttura a sandwich di "coperchio pacco batteria integrato sottoscocca-cella batteria-vassoio", riducendo la perdita di spazio causata dalla connessione tra carrozzeria e coperchio batteria. In questa modalità strutturale, il pacco batteria non è solo una fonte di energia, ma partecipa anche alla forza e alla trasmissione dell'intero veicolo come struttura.
Figura 2: Schema della struttura della tecnologia CTB
l Tecnologia CTC
Dopo aver adottato il metodo CTC, il pacco batteria non è più un assemblaggio indipendente, ma è integrato nella carrozzeria del veicolo, il che ottimizza la progettazione del prodotto e il processo di produzione, riduce il numero di parti del veicolo, in particolare riduce le parti strutturali interne e i connettori della batteria, ha il vantaggio intrinseco della leggerezza, massimizza l'utilizzo dello spazio e fornisce spazio per aumentare il numero di batterie e migliorare l'autonomia di guida. A condizione che il sistema elettrochimico stesso rimanga invariato, l'autonomia di guida può essere aumentata aumentando il numero di batterie.
Figura 3: Diagramma della struttura della tecnologia Tesla CTC
Ad esempio, Tesla e altre case automobilistiche hanno lanciato in successione modelli di tecnologia CTC. A livello di cella, possono utilizzare strutture sandwich elastiche multifunzionali e tecnologia di raffreddamento ad acqua di grandi dimensioni e sovrapporre la tecnologia di riutilizzo dello spazio anti-collisione nella parte inferiore del pacco batteria apportata dallo sviluppo integrato, tenendo conto dell'efficienza di raggruppamento, della dissipazione del calore e della sicurezza e promuovendo l'applicazione della tecnologia CTC dalle due dimensioni di ottimizzazione delle celle e protezione della struttura del veicolo. A livello di sviluppo integrato del veicolo, la cella della batteria è direttamente integrata nel telaio, eliminando i collegamenti di moduli e pacchi batteria. L'integrazione dei tre principali sistemi elettrici (motore, controllo elettronico, batteria), i tre sistemi elettrici minori (CC/CC, OBC, PDU), il sistema del telaio (sistema di trasmissione, sistema di guida, sistema di sterzo, sistema di frenata) e moduli correlati alla guida autonoma è realizzata e la distribuzione di potenza è ottimizzata e il consumo di energia è ridotto tramite il controller di dominio di potenza intelligente.
4-Modifiche ai requisiti specifici per i box batteria per le tecnologie CTP, CTB e CTC
Nella struttura tradizionale del pacco batteria, il modulo batteria svolge il ruolo di supporto, fissaggio e protezione della cella della batteria, mentre il corpo del box batteria sopporta principalmente la forza di estrusione esterna. L'applicazione delle tecnologie CTP, CTB e CTC propone nuovi requisiti per i box batteria, che si riflettono specificamente in:
I requisiti di resistenza del corpo della scatola della batteria sono migliorati: poiché il collegamento del modulo è ridotto o eliminato nelle strutture CTP, CTB e CTC, il corpo della scatola della batteria non deve solo resistere alla forza di estrusione esterna, ma anche alla forza di espansione della cella della batteria originariamente sopportata dal modulo. Pertanto, i requisiti di resistenza del corpo della scatola della batteria sono più elevati.
Capacità di protezione dalle collisioni: dopo aver utilizzato la tecnologia CTP per rimuovere le travi laterali del pacco batteria, la batteria subirà direttamente l'impatto della collisione, pertanto il pacco batteria CTP deve avere una resistenza alle collisioni sufficiente.
Requisiti di isolamento, isolamento e dissipazione del calore: le strutture CTP o CTB e CTC modificano il profilo della piastra inferiore in una piastra raffreddata ad acqua basata sulla scatola strutturale portante del telaio. La scatola della batteria non solo sopporta il peso delle celle della batteria, ma fornisce anche gestione termica e altre funzioni per la batteria. La struttura è più compatta, il processo di produzione è ottimizzato e il grado di automazione è più elevato.
Manutenibilità ridotta: il design altamente integrato rende complicata la sostituzione del pacco batteria. Ad esempio, nella struttura CTC, le celle della batteria sono riempite con materiale in resina, il che rende difficile la sostituzione delle celle della batteria e quasi impossibile la riparazione.
5- Impatto dell'integrazione del pacco batteria sull'infrastruttura di ricarica dei veicoli elettrici
La scelta di diverse tecnologie di integrazione del pacco batteria implica anche la scelta di diversi metodi di compensazione. CTP tende a essere la sostituzione della batteria, mentre CTB/CTC, più altamente integrato, tende a essere la ricarica rapida.
Un'elevata integrazione significa che più batterie possono essere ospitate nello stesso spazio, aumentando così l'autonomia dei veicoli elettrici. Gli utenti potrebbero non aver più bisogno di caricare frequentemente per brevi distanze, ma potrebbero preferire caricare rapidamente durante i lunghi viaggi. Pertanto, la pianificazione dell'infrastruttura di ricarica deve tenere conto di questi cambiamenti per garantire che possa soddisfare le esigenze degli utenti.
Con l'aumento dell'integrazione dei pacchi batteria, le dimensioni fisiche e la struttura dei pacchi batteria potrebbero cambiare, il che potrebbe influire sulla progettazione dell'interfaccia di ricarica e sulla compatibilità dell'apparecchiatura di ricarica.
Inoltre, la maggiore integrazione dei pacchi batteria potrebbe anche influire sulla velocità e l'efficienza della ricarica. Potrebbe essere necessario sviluppare e implementare sistemi di gestione della batteria e tecnologie di ricarica più efficienti per garantire un processo di ricarica rapido e sicuro.
Condivideremo regolarmente aggiornamenti e informazioni su tecniche di progettazione termica e alleggerimento, per la vostra consultazione. Grazie per l'interesse verso Walmate.
Nel processo di produzione di vassoi batteria e scatole fredde di accumulo di energia per veicoli a nuova energia, il trattamento superficiale necessario e appropriato è un passaggio fondamentale, come: l'uso di rivestimento, trattamento di ossidazione, ecc. per formare uno strato protettivo sulla superficie metallica per resistere all'erosione di mezzi corrosivi; i componenti che richiedono isolamento elettrico, come celle batteria, piastre di raffreddamento ad acqua, pareti del modulo, ecc., devono stabilire una pellicola protettiva isolante. L'isolamento è generalmente ottenuto spruzzando polvere isolante o vernice isolante. La scelta della tecnologia di trattamento superficiale appropriata può non solo migliorare le prestazioni del vassoio/scatola di raffreddamento a liquido, ma anche la durata e la sicurezza possono soddisfare le esigenze di diversi scenari applicativi. Questo articolo riassume le comuni tecnologie di trattamento superficiale come riferimento.
1-Pulizia e lucidatura
Durante il processo di produzione, sulla superficie del pallet possono accumularsi impurità come olio di lavorazione, residui di olio motore, polvere e polvere. Queste impurità non solo influiscono sulla durata utile del vassoio della batteria, ma possono anche influire negativamente sulle prestazioni e sulla sicurezza della batteria. Tramite pulizia e lucidatura, queste impurità possono essere rimosse efficacemente per garantire la pulizia della superficie del pallet. La pulizia e la molatura possono rimuovere efficacemente impurità superficiali, sbavature e scorie di saldatura, rendendo la superficie liscia e piatta, migliorando così la qualità complessiva del vassoio/scatola della batteria.
l pulizia chimica
Pulizia alcalina: la pulizia alcalina utilizza principalmente soluzioni alcaline (come idrossido di sodio, carbonato di sodio, ecc.) per rimuovere grasso, sporco e altre sostanze organiche dalla superficie delle leghe di alluminio. Il lavaggio alcalino rimuove il grasso tramite saponificazione, emulsificazione e penetrazione e bagnatura e allo stesso tempo genera precipitati solubili in acqua, ottenendo così un effetto pulente. La pulizia alcalina è solitamente utilizzata per rimuovere grasso, polvere e contaminanti organici dalla superficie delle leghe di alluminio.
Decapaggio: il decapaggio utilizza soluzioni acide (come acido nitrico, acido cloridrico, ecc.) per rimuovere incrostazioni di ossido, ruggine e altri depositi inorganici sulla superficie delle leghe di alluminio. Il decapaggio converte gli ossidi sulla superficie del metallo in sali solubili attraverso la reazione dell'acido con gli ossidi sulla superficie del metallo, rimuovendo così le impurità superficiali. Il decapaggio è utilizzato principalmente per rimuovere la pellicola di ossido, la ruggine e le incrostazioni di sale inorganico sulla superficie delle leghe di alluminio. Il decapaggio è spesso utilizzato per il trattamento finale delle superfici metalliche per migliorarne la finitura e la planarità.
l Rettifica meccanica
Durante la produzione, il processo di rettifica può rimuovere le tolleranze di lavorazione, correggere errori di forma, garantire la levigatezza e la precisione della superficie del pallet/scatola, soddisfare i requisiti di assemblaggio e quindi migliorare le prestazioni complessive e la durata utile.
La superficie pulita e levigata può migliorare il trattamento dei materiali di rivestimento o di altri materiali, ed è molto importante per l'applicazione successiva di rivestimenti anticorrosivi, sigillanti, conduttori di calore, isolanti e materiali di isolamento. Questo svolge un ruolo chiave nell'assicurare una solida adesione di questi materiali al pallet o al contenitore.
2-Stabilimento del rivestimento e della pellicola protettiva
Oltre alla pulizia e alla lucidatura di base, la produzione di pallet/scatole utilizza un processo di spruzzatura per il trattamento superficiale, al fine di formare uno strato protettivo che prevenga l'ossidazione e la corrosione e soddisfi le esigenze di diversi scenari, quali isolamento termico, isolamento e resistenza alla tensione.
l Isolamento termico
L'isolamento termico e anticondensa dei vassoi delle batterie può essere ottenuto mediante una progettazione completa di sistemi di isolamento termico, l'uso di materiali isolanti ad alta efficienza, l'applicazione di aerogel, la progettazione dell'isolamento del pacco batteria e la spruzzatura di materiali isolanti in schiuma.
Superficie inferiore spruzzata con PVC e materiale espanso
l Tensione di tenuta all'isolamento
L'isolamento dell'involucro del pacco batteria e dei componenti di raffreddamento a liquido serve principalmente a prevenire perdite di corrente, proteggere il personale da scosse elettriche e garantire il normale funzionamento del sistema di batterie. L'isolamento è in genere ottenuto tramite due metodi principali: spruzzatura a polvere e laminazione a pellicola. I principali processi di laminazione a pellicola includono laminazione a temperatura ambiente, pressatura a caldo ed esposizione ai raggi UV.
Spruzzatura interna di polvere isolante e vernice isolante
3-Loghi e segnaletica
Una targhetta o un'etichetta viene posizionata in una posizione ben visibile sul vassoio della batteria, generalmente tramite laser, incisione meccanica, ecc. Questi loghi sono solitamente realizzati con materiali resistenti all'usura e alla corrosione, per garantire che non vengano cancellati facilmente durante l'intera durata di servizio.
Condivideremo regolarmente aggiornamenti e informazioni su tecniche di progettazione termica e alleggerimento, per la vostra consultazione. Grazie per l'interesse verso Walmate.
In quanto apparecchiatura principale del sistema di accumulo di energia, il convertitore di accumulo di energia è uno strumento importante per la conversione di potenza, la gestione dell'energia, la garanzia della stabilità della rete, il miglioramento dell'efficienza energetica, ecc. Man mano che l'unità di potenza del convertitore di accumulo di energia si sposta verso un'elevata integrazione e un'elevata efficienza, lo sviluppo di frequenza e grande capacità pone requisiti sempre più elevati sulla dissipazione del calore.
1-Cambiamenti nei requisiti di raffreddamento
l Grazie alla cabina CC più grande, la capacità del convertitore continua ad aumentare e l'efficiente tecnologia di dissipazione del calore garantisce l'affidabilità dell'apparecchiatura.
Man mano che la capacità delle celle di accumulo di energia diventa sempre più grande, anche la capacità dei sistemi di accumulo di energia si sta espandendo simultaneamente. All'inizio del 2023, la capacità standard della batteria a cella singola da 20 piedi sul mercato era di soli 3,35 MWh. Nella seconda metà dell'anno, molte aziende di celle per batterie hanno lanciato prodotti di accumulo di energia da 310+Ah e la capacità della batteria a cella singola da 20 piedi è stata ampliata anche a 5 MWh. Tuttavia, meno di sei mesi dopo l'aggiornamento del modello da 5 MWh, alcuni importanti sistemi di accumulo di energia hanno rilasciato sistemi da 6 MWh e 8 MWh. Secondo l'esperienza generale, il convertitore di accumulo di energia è configurato a 1,2 volte la capacità di carico. La capacità della singola unità di un sistema di accumulo di energia da 5 MWh deve essere superiore a 2,5 MW. L'elevata potenza richiede una tecnologia di raffreddamento più efficiente per garantire un funzionamento stabile dell'apparecchiatura sotto carichi elevati sostenuti.
Evoluzione iterativa dello schema di topologia di integrazione del sistema di accumulo di energia
l L'applicazione della tecnologia ad alta tensione CC richiede che i dispositivi abbiano livelli di tensione di tenuta e resistenza dell'isolamento più elevati, inoltre la dissipazione del calore dei dispositivi di potenza è notevole.
Per adattarsi al sistema di accumulo di energia di grande capacità, la tecnologia ad alta tensione CC è diventata una tendenza tecnica. Attraverso l'aumento del livello di tensione, è possibile ottenere risparmio energetico, efficienza e miglioramento delle prestazioni. L'aggiornamento della tensione a 1500 V ha avuto origine dal fotovoltaico e ora il fotovoltaico è coinvolto nell'accumulo di energia. Tuttavia, l'evoluzione ad alta tensione del PCS di accumulo di energia ha ancora molta strada da fare e alcuni produttori hanno iniziato a ottimizzarla e spingerla a 2000 V. L'applicazione della tecnologia ad alta tensione CC costringe i dispositivi elettronici di potenza nei convertitori di accumulo di energia ad avere livelli di tensione di tenuta più elevati e una maggiore resistenza di isolamento per adattarsi agli ambienti di lavoro ad alta tensione. Negli ambienti ad alta tensione, la progettazione della dissipazione del calore dei dispositivi di potenza diventa più importante. La temperatura di giunzione pn dei dispositivi di potenza generalmente non può superare i 125 °C e la temperatura del guscio del pacchetto non supera gli 85 °C.
l I sistemi di accumulo di energia in rete richiedono algoritmi di controllo complessi, progetti di circuiti e convertitori di accumulo di energia ad alta densità di potenza
A differenza delle caratteristiche essenziali delle fonti di corrente nei sistemi di accumulo di energia grid-forming, i sistemi di accumulo di energia grid-forming sono essenzialmente fonti di tensione che possono impostare internamente parametri di tensione per generare tensione e frequenza stabili. Pertanto, è necessario che i convertitori grid-forming simulino le caratteristiche dei generatori sincroni, fornendo supporto per tensione e frequenza per migliorare la stabilità del sistema di alimentazione. Questa strategia di controllo richiede che i convertitori possiedano una maggiore densità di potenza e algoritmi di controllo più complessi, nonché dispositivi di alimentazione ad alte prestazioni e progetti di circuiti più intricati per implementare la strategia di controllo. Gestire efficacemente il calore generato da un'elevata densità di potenza e strategie di controllo complesse, riducendo al contempo le dimensioni e il costo del sistema di raffreddamento senza compromettere le prestazioni, è diventata una nuova sfida nella progettazione termica.
2- Confronto delle soluzioni di raffreddamento comuni
Negli ultimi anni la soluzione di raffreddamento per gli inverter con accumulo di energia ha subito una significativa evoluzione iterativa, che si riflette principalmente nella transizione della tecnologia di raffreddamento dal tradizionale raffreddamento ad aria a quella a liquido.
l Soluzione di raffreddamento ad aria
Il raffreddamento ad aria è la forma di controllo della temperatura utilizzata nella fase iniziale dei convertitori di accumulo di energia. Utilizza l'aria come mezzo e dissipa il calore tramite ventole e radiatori. La soluzione di raffreddamento ad aria migliora l'efficienza di dissipazione del calore riducendo costantemente il consumo di energia, ottimizzando la struttura e migliorando i materiali di dissipazione del calore. Al livello di potenza di 2,5 MW, il raffreddamento ad aria può ancora soddisfare i requisiti.
l Soluzione di raffreddamento a liquido
Poiché la densità di potenza e la densità energetica dei sistemi di accumulo di energia continuano ad aumentare, il PCS raffreddato a liquido utilizza un refrigerante con elevata conduttività termica come mezzo. Il refrigerante è azionato da una pompa dell'acqua per circolare nella piastra fredda e non è influenzato da fattori quali altitudine e pressione dell'aria. Il sistema di raffreddamento a liquido ha un'efficienza di dissipazione del calore più efficiente rispetto al sistema di raffreddamento ad aria. La soluzione di raffreddamento a liquido ha un grado di corrispondenza più elevato e ha iniziato a essere esplorata e resa popolare negli ultimi uno o due anni.
Oltre alla soluzione di accumulo di energia con raffreddamento a liquido completo, alcuni produttori hanno lanciato macchine di raffreddamento diretto con accumulo di energia, che utilizzano il raffreddamento diretto a cambiamento di fase e nessuna circolazione d'acqua. Anche le soluzioni di raffreddamento diretto stanno entrando nel campo dell'accumulo di energia.
Condivideremo regolarmente aggiornamenti e informazioni su tecniche di progettazione termica e alleggerimento, per la vostra consultazione. Grazie per l'interesse verso Walmate.
Il pacco batteria è un componente chiave dei nuovi veicoli energetici, degli armadietti e dei contenitori per l'accumulo di energia. È una fonte di energia attraverso l'involucro del guscio, che fornisce energia ai veicoli elettrici e fornisce capacità di consumo per gli armadietti e i contenitori per l'accumulo di energia. In combinazione con le effettive esigenze ingegneristiche, questo articolo riassume i punti chiave della progettazione del profilo per i pacchi batteria analizzando i requisiti di resistenza meccanica, sicurezza, gestione termica e leggerezza dei pacchi batteria.
1-Requisiti di progettazione dell'alloggiamento del pacco batteria
l Resistenza meccanica, resistenza alle vibrazioni e resistenza agli urti. Dopo il test, non dovrebbero esserci danni meccanici, deformazioni o allentamenti del fissaggio e il meccanismo di bloccaggio non dovrebbe essere danneggiato.
l Sigillatura: la sigillatura del pacco batteria influisce direttamente sulla sicurezza di funzionamento del sistema di batterie. Di solito è necessario raggiungere il livello di protezione IP67 per garantire che il pacco batteria sia sigillato e impermeabile.
l La progettazione dell'involucro del pacco batteria deve tenere in considerazione le prestazioni di gestione termica e garantire che la batteria funzioni entro un intervallo appropriato mediante un'adeguata progettazione della gestione termica.
l Per l'installazione e il fissaggio, la struttura deve avere spazio per la targhetta e i segnali di sicurezza e deve riservare spazio sufficiente e fondamenta fisse per l'installazione di linee di acquisizione, vari elementi sensori, ecc.
l Tutti i connettori, i terminali e i contatti elettrici con isolamento di base non polare devono soddisfare i requisiti del livello di protezione corrispondente quando combinati.
l Alleggerimento: l'alleggerimento del guscio è di grande importanza per migliorare la densità energetica del pacco batteria. La lega di alluminio è leggera e di alta qualità, il che la rende la scelta più fattibile al momento. Il livello di alleggerimento può essere migliorato tramite un design estremo appropriato in combinazione con applicazioni reali.
l Durata: la durata di vita del guscio del pacco batteria non deve essere inferiore alla durata di vita del prodotto complessivo. Non deve verificarsi alcuna deformazione plastica evidente durante il ciclo di utilizzo. Il livello di protezione e le prestazioni di isolamento non devono essere ridotti. La struttura deve essere facile da manutenere, inclusa la disposizione delle targhette e dei segnali di sicurezza e la protezione dei connettori.
Figura 1 Tipico guscio del pacco batteria saldato in lega di alluminio
2-Tipica soluzione con guscio per pacco batteria in lega di alluminio
I materiali in lega di alluminio comunemente usati per i gusci dei pacchi batteria includono 6061-T6, 6005A-T6 e 6063-T6, ecc. Questi materiali hanno diversi limiti di snervamento e resistenze alla trazione per soddisfare diversi requisiti strutturali. La resistenza di questi materiali è: 6061-T6>6005A-T6>6063-T6.
Attualmente, le soluzioni di formatura del guscio del pacco batteria includono la saldatura di profili in alluminio, la fusione di lega di alluminio, la fusione di alluminio più profili in alluminio, la saldatura di piastre in alluminio stampato, ecc. La soluzione di saldatura di profili in alluminio è diventata la scelta principale grazie alla sua flessibilità e praticità di lavorazione. Come mostrato nella Figura 1, il guscio è composto principalmente da un telaio di profili in lega di alluminio e da una piastra inferiore di profili in lega di alluminio, che vengono saldati utilizzando profili estrusi in lega di alluminio serie 6. La soluzione di fusione di lega di alluminio è considerata la futura direzione di sviluppo grazie al suo processo semplificato e al potenziale di riduzione dei costi.
3- Progettazione della sezione del profilo
l Dimensioni e complessità della sezione: la dimensione della sezione del profilo è misurata dal cerchio circoscritto. Più grande è il cerchio circoscritto, maggiore è la pressione di estrusione richiesta. La sezione del profilo è solitamente composta da più cavità per migliorare la rigidità e la resistenza strutturale. Solitamente, il telaio, la partizione centrale, la piastra inferiore, la trave, ecc. adottano diversi design di sezione per adattarsi a diversi requisiti strutturali e funzionali.
Figura 2 Sezione tipica del profilo in lega di alluminio
l Spessore della parete del profilo in alluminio: lo spessore minimo della parete di uno specifico profilo in alluminio è correlato al raggio del cerchio circoscritto del profilo, alla forma e alla composizione della lega. Ad esempio, quando lo spessore della parete della lega di alluminio 6063 è di 1 mm, lo spessore della parete della lega di alluminio 6061 dovrebbe essere di circa 1,5 mm. La difficoltà di estrusione della stessa sezione è: 6061-T6>6005A-T6>6063-T6. Nella progettazione dei profili del pacco batteria, il profilo del telaio è solitamente realizzato in materiale in lega di alluminio 6061-T6 e la sua sezione tipica è composta da più cavità e lo spessore della parete più sottile è di circa 2 mm; anche il profilo della piastra inferiore è composto da più cavità e il materiale è generalmente 6061-T6, 6065A-T6 e anche lo spessore della parete più sottile è di circa 2 mm; Inoltre, nella progettazione del vassoio portante della piastra inferiore e dell'integrazione del raffreddamento a liquido della piastra inferiore, la piastra inferiore adotta generalmente una struttura bifacciale, lo spessore della piastra inferiore è generalmente di 10 mm e lo spessore della parete e della parete interna della cavità sono di circa 2 mm.
l Tolleranza delle dimensioni trasversali del profilo: la tolleranza delle dimensioni trasversali deve essere determinata in base alla tolleranza di lavorazione del profilo in alluminio, alle condizioni di utilizzo, alla difficoltà di estrusione del profilo e alla forma del profilo. Per alcuni profili in alluminio difficili da estrudere, la forma può essere modificata o la tolleranza di lavorazione e la tolleranza dimensionale possono essere aumentate per ridurre la difficoltà di estrusione ed estrudere prodotti di profili in alluminio che sono vicini ai requisiti, e quindi possono essere rimodellati o lavorati per soddisfare i requisiti di utilizzo.
Inoltre, quando si progetta la sezione del profilo, è necessario considerare i requisiti specifici dei diversi processi di saldatura per giunti, scanalature, spessore delle pareti, ecc.
Condivideremo regolarmente aggiornamenti e informazioni su tecniche di progettazione termica e alleggerimento, per la vostra consultazione. Grazie per l'interesse verso Walmate.
La tenuta stagna del pacco batteria è un fattore chiave per garantire la qualità e la sicurezza del pacco batteria. È correlata alla sicurezza, all'affidabilità e alla durata del pacco batteria. Il test di tenuta stagna del pacco batteria deve essere eseguito non solo durante il processo di produzione, ma anche durante la manutenzione e l'ispezione della batteria.
1-Requisiti di tenuta stagna del pacco batteria
Nella produzione effettiva, la tenuta stagna del pacco batteria deve soddisfare i seguenti requisiti:
Prestazioni di tenuta: l'involucro del pacco batteria, l'interfaccia e i connettori devono avere buone prestazioni di tenuta per impedire a polvere, vapore acqueo e altre impurità esterne di entrare nel pacco batteria, il che può essere ottenuto tramite saldatura, sigillanti, materiali impermeabili, ecc.
Prestazioni impermeabili, per impedire all'umidità di entrare nella batteria, causando cortocircuiti, corrosione e altri problemi. Secondo lo standard nazionale GB38031-2020 "Requisiti di sicurezza per batterie di alimentazione per veicoli elettrici", le prestazioni di tenuta delle batterie e dei loro componenti devono soddisfare lo standard IP67. La maggior parte dei nuovi veicoli energetici ha requisiti di prestazioni di tenuta più elevati per le batterie e i loro componenti e deve soddisfare lo standard IP68, ovvero il pacco batteria può impedire all'acqua di entrare entro la profondità dell'acqua e il tempo di immersione specificati.
I metodi tradizionali di prova di tenuta all'aria includono il metodo di pressione e il metodo di immersione (prova in acqua). Il metodo di immersione consiste nell'immergere la piastra di raffreddamento a liquido in acqua e osservare se vengono generate bolle per giudicare la tenuta.
Piastra di raffreddamento a liquido Canale dell'acqua Serbatoio di prova di tenuta dell'aria
Sebbene lo standard IP68 sia più rigoroso, nelle applicazioni reali, il metodo della caduta di pressione è spesso utilizzato come metodo di rilevamento principale per soddisfare i requisiti IP68 impostando standard di rilevamento della tenuta stagna appropriati. Il metodo della caduta di pressione determina la tenuta stagna del pacco batteria misurando la variazione di pressione all'interno del pacco batteria. Quando si eseguono test di tenuta stagna, è necessario prestare attenzione a più parametri, come pressione di gonfiaggio, tempo di gonfiaggio, tempo di stabilizzazione della pressione e tasso di perdita.
(lato sinistro)Diagramma del principio di base della pressione differenziale
(lato destro)Diagramma del principio di base della pressione diretta
2-Analisi del problema di perdita della piastra di raffreddamento a liquido
Con il continuo aggiornamento della domanda di mercato per veicoli a batteria, sistemi di accumulo di energia a batteria, ecc., vengono ampiamente utilizzati pacchi batteria con densità di energia e densità di potenza più elevate. A causa delle caratteristiche termiche delle batterie, per garantire il funzionamento stabile delle apparecchiature principali come le batterie e migliorare l'efficienza di utilizzo dell'energia, la tecnologia di raffreddamento a liquido è una delle principali vie tecniche per la gestione termica dell'accumulo di energia e il test di tenuta all'aria del sistema di raffreddamento a liquido è diventato un collegamento chiave.
La perdita dalla piastra di raffreddamento a liquido è un problema serio: la perdita ostacolerà il normale flusso del refrigerante, comprometterà l'effetto di dissipazione del calore della piastra di raffreddamento a liquido e ridurrà le prestazioni dell'apparecchiatura; la perdita può anche causare l'invecchiamento e il danneggiamento dei componenti del sistema, riducendone l'affidabilità; la perdita può anche corrodere i componenti e i circuiti elettronici, aumentando il rischio di guasti e incendi dell'apparecchiatura.
Perché il problema delle perdite si verifica ancora dopo rigorosi test di tenuta all'aria durante il processo di produzione e fabbricazione della piastra di raffreddamento a liquido?
Processo di prova di tenuta all'aria del sistema di raffreddamento a liquido
Le infiltrazioni di liquidi possono essere causate da diversi fattori:
l Piccole crepe e difetti:I test di tenuta all'aria del paesaggio possono rilevare grandi canali di perdita, ma piccole crepe e difetti possono comunque esistere. Queste piccole crepe possono espandersi sotto la pressione del liquido o in un ambiente ad alta temperatura, causando infiltrazioni di liquido.
l Differenze di tensione superficiale e bagnabilità del refrigerante: quando la tensione superficiale del refrigerante è bassa, è più facile penetrare attraverso piccole fessure. Se la progettazione della tensione superficiale della piastra fredda del liquido non è ragionevole o il refrigerante non è selezionato correttamente, il problema di infiltrazione del liquido potrebbe aggravarsi.
Differenze di bagnabilità: diversi refrigeranti hanno una diversa bagnabilità sulle superfici solide. Se la rugosità superficiale del materiale della piastra fredda liquida è elevata o ci sono difetti microstrutturali, il refrigerante potrebbe penetrare più facilmente.
l Problemi di installazione o di processo: se il processo di installazione della piastra di raffreddamento del liquido non è sufficientemente accurato o se sono presenti difetti nella saldatura, nel collegamento e in altri processi, ciò potrebbe causare una scarsa tenuta e aumentare la possibilità di infiltrazioni di liquido.
l Condizioni ambientali: i cambiamenti di temperatura, specialmente in ambienti ad alta pressione, possono influenzare la permeabilità del refrigerante. Sebbene questi fattori ambientali possano non essere considerati durante i test di tenuta all'aria, nel funzionamento effettivo, le fluttuazioni di temperatura possono causare guasti alla guarnizione.
l Invecchiamento o affaticamento del materiale: se il materiale della piastra di raffreddamento del liquido viene utilizzato per troppo tempo, potrebbe invecchiare o affaticarsi, deteriorando le sue prestazioni di tenuta e aumentando così il rischio di perdite di liquido.
3-Misure preventive per perdite della piastra di raffreddamento a liquido
l Migliorare la progettazione della piastra di raffreddamento a liquido: ottimizzando la struttura e la progettazione della piastra di raffreddamento a liquido, ridurre piccole crepe e difetti e migliorare le sue prestazioni di tenuta. Ad esempio, quando si salda la trave di installazione del modulo sulla superficie del canale di flusso, adottare misure anti-perdita per evitare perdite di refrigerante.
l Migliorare il livello del processo di produzione: nel processo di produzione della piastra di raffreddamento a liquido, vengono utilizzati processi di saldatura e materiali di alta qualità per garantire che il refrigerante non sia facile da penetrare. Allo stesso tempo, durante il processo di assemblaggio, seguire rigorosamente le procedure operative per evitare allentamenti o installazioni errate.
l Ottimizza la combinazione di metodi di rilevamento per garantire l'efficienza del rilevamento migliorando al contempo la precisione del rilevamento e riducendo il tasso di rilevamento mancato. Il metodo di immersione e il metodo di caduta di pressione vengono utilizzati per il rilevamento della tenuta all'aria, che è semplice da utilizzare, economico ed efficiente ed è adatto per esigenze di rilevamento di routine su larga scala. Tuttavia, la precisione di rilevamento dei due metodi è bassa. La precisione di rilevamento del metodo di caduta di pressione è generalmente una velocità di perdita di 1×10-4Pa·m³/s e la precisione dei risultati di rilevamento è facilmente influenzata da fattori quali temperatura, umidità, pulizia e pressione. Utilizzare apparecchiature di rilevamento con una maggiore precisione di rilevamento e un effetto migliore per aumentare la precisione di rilevamento a 1×10-6Pa·m³/s, migliorando così l'effetto di rilevamento.
Oltre alle misure preventive per la piastra di raffreddamento a liquido stessa, è anche necessario adottare strategie di risposta appropriate sotto molteplici aspetti, come la scelta del refrigerante, la scelta della guarnizione e l'ambiente di lavoro dell'apparecchiatura.
Condivideremo regolarmente aggiornamenti e informazioni su tecniche di progettazione termica e alleggerimento, per la vostra consultazione. Grazie per l'interesse verso Walmate.
Nella progettazione della dissipazione del calore, l'adozione di metodi efficaci di riduzione dei costi può migliorare l'affidabilità e l'efficienza del sistema complessivo, riducendo al contempo i costi inutili.
1-Il design di derating riduce i costi
Il design di derating è un metodo di progettazione che riduce intenzionalmente gli stress elettrici, termici e meccanici a cui sono sottoposti componenti o prodotti durante il funzionamento. Negli scenari di produzione e utilizzo effettivi, la stabilità delle apparecchiature elettroniche può essere migliorata riducendo lo stress sopportato dai componenti.
Diagramma schematico dei percorsi di dissipazione del calore per imballaggi 2D e 3D
l Riduzione dello stress lavorativo: durante la progettazione e il funzionamento del prodotto, lo stress lavorativo dei componenti può essere ridotto riducendo il carico di lavoro, controllando la frequenza operativa, limitando la corrente e la tensione, ecc.
l Ridurre lo stress ambientale: ridurre lo stress ambientale selezionando tipologie di componenti, layout e forme di imballaggio appropriate, ad esempio selezionando componenti con un ampio margine di temperatura o utilizzando forme di imballaggio con una buona tenuta per ridurre gli effetti della temperatura, dell'umidità e della pressione sui componenti.
l Applicazione dell'ingegneria dell'affidabilità: progettazione ridondante ragionevole, rilevamento e isolamento dei guasti, ecc., riducono ulteriormente il rischio di guasto dei componenti.
Riducendo lo stress sui componenti durante il funzionamento, è possibile ridurre il loro consumo di energia e la generazione di calore. Quando i dispositivi di potenza funzionano in condizioni di stress inferiori allo stress nominale, è possibile ridurre il loro consumo di energia e la generazione di calore, il che aiuta a migliorare l'efficienza energetica e l'affidabilità del sistema. A lungo termine, la progettazione del derating aumenta efficacemente la durata dei componenti, riduce i tassi di guasto, riduce il carico di lavoro di manutenzione e quindi riduce i costi.
2-Ottimizzare il layout
L'efficienza di funzionamento del radiatore può essere notevolmente migliorata mediante una disposizione ragionevole dei componenti termici; una strategia di disposizione dei componenti ragionevole può raggiungere un equilibrio tra prestazioni del prodotto e costi.
l Distribuire i componenti di dissipazione del calore: disperdere i componenti che generano grandi quantità di calore per ridurre il carico termico per unità di superficie.
l Posizione che favorisca la dissipazione del calore: posizionare l'elemento riscaldante in una posizione che favorisca la dissipazione del calore, ad esempio vicino a una presa d'aria o al bordo del dispositivo.
l Disposizione sfalsata: durante la disposizione, sfalsare i componenti riscaldanti rispetto agli altri componenti generali e cercare di rendere i componenti riscaldanti principalmente sensibili alla temperatura per ridurre il loro impatto sui componenti sensibili al calore.
l Miglioramento del flusso d'aria: modificando la progettazione della direzione e la disposizione dei componenti, il percorso del flusso d'aria viene ottimizzato, la portata aumenta e il coefficiente di trasferimento del calore viene migliorato.
Raccomandazioni sulla spaziatura tra i componenti
3-Scelta del metodo di raffreddamento
Man mano che le prestazioni dei componenti elettronici migliorano e il grado di integrazione aumenta, la densità di potenza continua ad aumentare, con conseguente aumento significativo del calore generato dai componenti elettronici durante il funzionamento. Quando si sceglie un metodo di dissipazione del calore per i componenti elettronici, i requisiti di controllo della temperatura includono principalmente i seguenti aspetti:
l Intervallo di temperatura: diversi componenti hanno diversi intervalli di tolleranza della temperatura. Ad esempio, i chip ad alte prestazioni come le CPU hanno requisiti di temperatura di esercizio compresi tra 85 e 100 °C, mentre alcuni dispositivi a bassa potenza possono tollerare temperature più elevate, quindi il sistema di raffreddamento deve garantire che i componenti funzionino entro un intervallo di temperatura sicuro.
l Precisione del controllo della temperatura: in alcuni scenari con severi requisiti di controllo della temperatura, è necessario adottare una soluzione di dissipazione del calore in grado di controllare accuratamente la temperatura per evitare il degrado delle prestazioni dei componenti o addirittura danni causati da temperature eccessivamente alte o basse.
l Temperatura ambiente: l'effetto di dissipazione del calore delle apparecchiature elettroniche non dipende solo dalla capacità di dissipazione del calore del dispositivo stesso, ma è anche influenzato dalla temperatura ambiente circostante. La progettazione della dissipazione del calore deve considerare le variazioni della temperatura ambiente e cercare di mantenere il dispositivo entro un intervallo di temperatura adeguato tramite mezzi di dissipazione del calore.
l Consumo energetico e affidabilità: alcuni componenti elettronici a bassa potenza possono utilizzare la dissipazione naturale del calore quando generano poco calore. Per le apparecchiature ad alto consumo energetico, è necessario attendere la tecnologia di dissipazione del calore delle università per garantire che mantenga prestazioni normali e prolunghi il funzionamento sotto carichi elevati durata di servizio.
l Sigillatura e densità: nei dispositivi assemblati sigillati e ad alta densità, se la generazione di calore non è elevata, è possibile fare affidamento sulla dissipazione naturale del calore. Quando i componenti sono densamente imballati e generano grandi quantità di calore, sono necessarie tecnologie di dissipazione del calore più efficaci come la dissipazione del calore forzata o il raffreddamento a liquido. Il raffreddamento a liquido e la tecnologia heat pipe sono utilizzati in scenari con elevato consumo energetico e grande generazione di calore, come componenti elettronici ad alta potenza come tubi a onda progressiva, magnetron e tubi amplificatori di potenza, server e apparecchiature ad alto consumo energetico e sistemi trielettrici di veicoli a nuova energia. I suoi vantaggi applicativi unici.
(lato sinistro)Modulo di raffreddamento dell'aria della pila di carica
(lato destro)Modulo di raffreddamento a liquido della pila di carica
Quando si sceglie un metodo di raffreddamento per componenti elettronici, è necessario considerare in modo completo fattori quali generazione di calore e flusso di calore, temperatura ambiente e temperatura di esercizio, vincoli di spazio e requisiti di isolamento termico, nonché costi e fattibilità. Utilizzando una tecnologia di raffreddamento e dispositivi di raffreddamento appropriati per garantire che i componenti funzionino a una temperatura adatta, il costo di sostituzione e manutenzione del sistema può essere ridotto in modo efficace. Inoltre, riutilizzare progetti storici è anche una strategia efficace per ridurre i costi di sviluppo e produzione e migliorare l'affidabilità.
Condivideremo regolarmente aggiornamenti e informazioni su tecniche di progettazione termica e alleggerimento, per la vostra consultazione. Grazie per l'interesse verso Walmate.
I vassoi batteria, noti anche come scatole batteria o scatole PACK, sono sempre più apprezzati come un componente molto importante nello sviluppo di nuovi veicoli energetici. La progettazione dei vassoi batteria deve bilanciare la relazione tra fattori quali peso, sicurezza, costo e prestazioni dei materiali. Le leghe di alluminio sono ampiamente utilizzate nell'ingegneria leggera automobilistica per la loro bassa densità e l'elevata resistenza specifica, che può garantire rigidità assicurando al contempo le prestazioni della carrozzeria del veicolo.
1- Posizione di saldatura del vassoio della batteria e selezione del metodo
I vassoi per batterie in alluminio sono realizzati con profili in alluminio estruso e i vari componenti vengono uniti in un tutto tramite saldatura per formare una struttura di telaio completa. Strutture simili sono ampiamente utilizzate anche nelle scatole per pacchi di accumulo di energia.
Le parti di saldatura del vassoio della batteria solitamente includono la giunzione della piastra inferiore, la connessione tra la piastra inferiore e il lato, la connessione tra il telaio laterale, le travi orizzontali e verticali, la saldatura dei componenti del sistema di raffreddamento a liquido e la saldatura di accessori come staffe e orecchie pendenti. Quando si selezionano i metodi di saldatura, verranno selezionati diversi metodi di saldatura in base ai diversi requisiti strutturali e dei materiali, vedere la tabella seguente:
2-Analisi dell'influenza della deformazione termica della saldatura
La saldatura è un metodo di lavorazione con riscaldamento locale. Poiché la fonte di calore è concentrata sulla saldatura, la distribuzione della temperatura sulla saldatura è irregolare, il che alla fine porta alla deformazione della saldatura e allo stress della saldatura all'interno della struttura saldata. La deformazione termica della saldatura è il fenomeno per cui la forma e le dimensioni delle parti saldate cambiano a causa dell'apporto e dell'emissione di calore irregolari durante il processo di saldatura. In combinazione con l'esperienza effettiva del progetto di ingegneria, le parti che sono soggette a deformazione termica della saldatura e i fattori che influenzano sono riassunti:
a.Area di saldatura lunga e dritta
Nella produzione effettiva, la piastra inferiore del vassoio della batteria è generalmente realizzata con 2-4 profili in lega di alluminio uniti insieme mediante saldatura a frizione. Le saldature sono lunghe e ci sono anche lunghe saldature tra la piastra inferiore e la piastra laterale e tra la piastra inferiore e la trave distanziatrice. Le saldature lunghe sono soggette a surriscaldamento locale nell'area di saldatura a causa dell'apporto di calore concentrato, con conseguente deformazione termica.
Saldatura del telaio del vassoio della batteria
b.Giunti multicomponente
È causato dal riscaldamento locale ad alta temperatura e dal successivo raffreddamento durante il processo di saldatura nella saldatura multicomponente. Durante il processo di saldatura, la saldatura è soggetta a un apporto di calore non uniforme, con conseguente differenza di temperatura significativa tra l'area di saldatura e il materiale madre circostante, che causa effetti di espansione e contrazione termica, causando la deformazione delle parti saldate. L'estremità dell'installazione elettrica della scatola del pacco di accumulo di energia è solitamente dotata di un ugello per l'acqua, una staffa per cablaggio, una trave, ecc. e le saldature sono dense e molto facili da deformare.
Nella zona ad alta intensità di saldatura, il lato anteriore del pallet è deformato e deformato
c.Parete laterale del canale della piastra fredda
Nel vassoio batteria con design integrato della piastra di raffreddamento a liquido, le parti con minore rigidità strutturale, come piastre sottili e strutture di tubi, non possono resistere bene alla deformazione termica durante la saldatura e sono soggette a deformazione. Ad esempio, la parete laterale del canale di flusso della piastra di raffreddamento a liquido è molto sottile, generalmente solo circa 2 mm. Quando si saldano travi, staffe del cablaggio e altre parti sulla superficie di montaggio del modulo, è facile causare crepe e pieghe di deformazione sulla parete laterale del canale di flusso, influenzando le prestazioni complessive.
Difetti di crepe termiche sulla parete del canale di raffreddamento del liquido causati dalla saldatura a trave
3-Metodo di controllo della deformazione termica della saldatura
a.Saldatura a segmenti, saldatura bilaterale
Per le parti con requisiti di resistenza relativamente bassi, viene adottata la saldatura segmentata e il processo di saldatura viene suddiviso in più piccole sezioni. Le saldature sono disposte simmetricamente e le saldature sono disposte simmetricamente vicino all'asse neutro nella sezione di costruzione, in modo che le deformazioni causate dalle saldature possano compensarsi a vicenda. Allo stesso tempo, la lunghezza e il numero di saldature sono ridotti al minimo e si evita un'eccessiva concentrazione o incrocio di saldature, il che può ridurre il gradiente di temperatura di saldatura e quindi ridurre la deformazione della saldatura. Per le parti con requisiti di resistenza elevati come la piastra inferiore, la piastra inferiore e il telaio laterale, viene adottata la saldatura bifacciale per aumentare la resistenza riducendo al contempo la deformazione da flessione causata da parti di grandi dimensioni e lunghe saldature.
b.Ottimizzazione della sequenza di saldatura
Controllare la deformazione della saldatura, utilizzare giunti con rigidità inferiore, evitare saldature intersecanti bidirezionali e tridirezionali ed evitare aree ad alto stress. Ottimizzare la sequenza di saldatura, saldare prima le aree con rigidità più debole e per ultime quelle con rigidità migliore, ad esempio saldare prima le saldature a filetto, poi le saldature corte e infine le saldature lunghe; saldare prima le saldature trasversali, poi quelle longitudinali. Una sequenza di saldatura ragionevole può controllare efficacemente la deformazione della saldatura, controllando così le dimensioni della saldatura.
c.Regolazione dei parametri di saldatura
Controllare i parametri e i processi di saldatura e impostare ragionevolmente la velocità di saldatura, il numero di strati di saldatura e lo spessore di ogni saldatura. Per saldature più spesse, utilizzare metodi di saldatura multistrato e multicanale e lo spessore di ogni strato di saldatura non deve superare i 4 mm. La saldatura multistrato può ridurre la microstruttura strutturale e migliorare le prestazioni del giunto. Controllare accuratamente i parametri di saldatura e selezionare ragionevolmente parametri quali corrente di saldatura, tensione, modello di elettrodo e velocità di saldatura per garantire forma e dimensioni coerenti del bagno fuso, evitando così errori causati da una selezione impropria dei parametri.
d.Miglioramento delle capacità di saldatura
Migliorare le capacità operative del saldatore (utilizzare lavorazioni meccaniche per componenti di grandi dimensioni o nodi con requisiti rigorosi) per garantire coerenza e standardizzazione delle azioni durante la saldatura e ridurre i problemi dimensionali causati da fattori umani.
Condivideremo regolarmente aggiornamenti e informazioni su tecniche di progettazione termica e alleggerimento, per la vostra consultazione. Grazie per l'interesse verso Walmate.