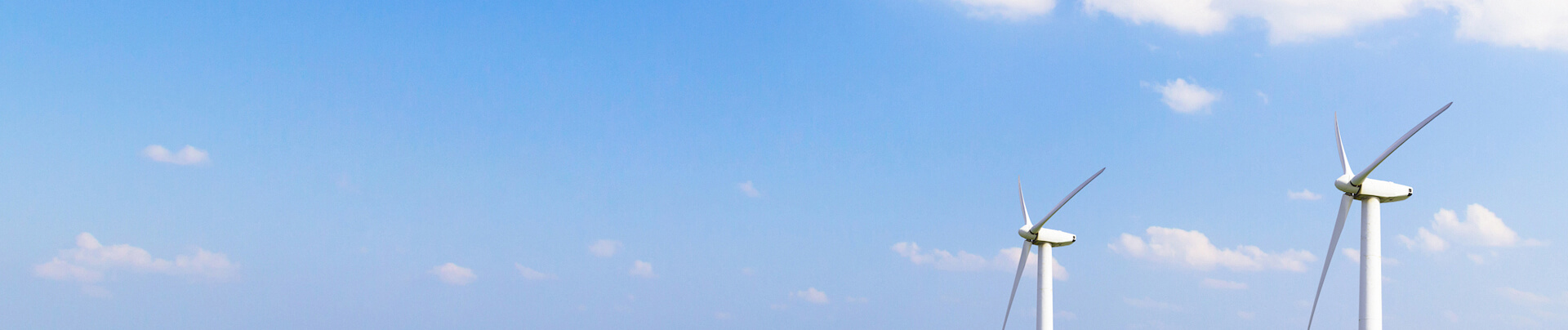
目标并竭力推动您的项目效益提升
随着储能系统向大容量、高能量密度方向演进,储能PACK箱体的尺寸匹配与兼容性设计成为提升系统效率与可靠性的核心课题。本文结合最新工程设计案例、专利技术及行业趋势,从空间利用率、模块化兼容性、电芯排列与支撑设计三个维度展开分析。
1-空间利用率优化
储能系统集成的空间利用率提升,本质是技术迭代与场景需求的双向驱动。通过大容量电芯、模块化架构、液冷集成等技术的协同创新,行业正从“粗放堆叠”迈向“极致空间复用”。
a.大容量电芯应用:能量密度与效率跃升
思路概括:大容量电芯的应用本质是减少电池包内部结构层级,直接提升电芯到电池包的空间利用率。传统电池包采用“电芯→模组→电池包”三级集成模式,模组结构(横梁、纵梁、螺栓等)导致空间利用率低。大容量电芯通过拉长或增大单体体积,可直接跳过模组层级,采用CTP(Cell to Pack)技术将电芯直接集成至电池包。
技术核心:采用600Ah+超大电芯,减少电芯数量与连接点,提升单体容量。
b.空间复用与成本优化:从“组件堆叠”到“多维复用”
思路概括:空间复用与成本优化是一体两面的系统级创新,其底层逻辑在于通过结构简化、功能集成、材料迭代和标准化设计,打破传统储能系统的物理与成本边界。
结构层级的极致简化,空间复用的核心在于减少中间环节。如:高压箱二合一设计:江苏天合储能的专利技术将两个高压箱合并为一个,共享总正/负继电器和电气连接,减少30%的横向空间占用,同时降低15%的电气部件成本。
功能模块的跨域复用,结构件与散热通道一体化,如将液冷板与箱体底板集成,液冷管道与结构支撑共用空间,减少15%的独立散热组件;电芯本体作为结构件:比亚迪刀片电池通过长薄化电芯侧壁提供支撑强度,省去模组框架,空间利用率提升至60%-80%。
电气拓扑的深度优化,如,高压级联拓扑结构通过提高单体电池容量和电压等级(如华为智能组串式储能),减少并联回路数量,使电池堆物理空间缩小20%,系统响应时间缩短50%。;共享式继电器设计,江苏天合储能的二合一高压箱让两条线路共用同一继电器,减少50%的继电器数量和线缆长度,安装效率提升30%
2-电芯排列与支撑设计:承重、散热与抗振平衡
电芯排列的本质是空间利用率、热分布与机械稳定性的博弈,电芯的物理形态和排布方向直接影响空间填充效率:
a.优化电芯排列方式
倒置电芯设计:将电芯防爆阀朝下,使热失控排气与底部防球击空间共用,释放电芯高度空间,体积利用率达。
躺式电芯布局:优化电池包高度方向的空间利用,活性材料占比提升,体积利用率显著高于立式电芯。
超长薄型电芯:通过电芯长薄化设计减少单位体积内的电芯数量,提升成组效率。
b.散热与承重的耦合设计:旨在通过结构、材料、工艺的协同创新,实现高效散热与结构强度的双重优化。
结构设计路径:
集成化结构,如液冷板与支撑梁共形设计:将液冷流道嵌入铝合金支撑梁内部,减少独立组件,空间利用率提升;
分层分舱布局,将电池组、液冷系统、BMS分层堆叠,降低热流与机械应力的相互干扰;
仿生力学优化,如,蜂窝/波纹结构,在铝合金支撑框架中设计蜂窝或波纹芯层(如沐风网专利方案),通过形变吸收振动能量,同时优化散热路径。
材料创新路径:
导热-承重一体化,如,铝合金复合纤维材料(导热≥200 W/m·K,强度+30%);智能材料,相变填充层(PCM)吸热缓释,温差±1.5℃;轻量化阻尼:弹性硅胶垫层吸收振动(阻尼+40%)。
工艺实现路径:
精密成型工艺,如,挤压成型:用于制造复杂流道的铝合金液冷梁;
表面处理技术,如,在铝合金表面生成陶瓷氧化层,提升耐腐蚀性(盐雾测试≥1000h),同时增强散热效率(表面辐射率提高20%);
智能装配工艺,动态预紧力调节,如,集成压力传感器与电动执行器,实时调整螺栓预紧力(5-20kN),避免电芯过压损伤。
c.支撑结构的承重与抗振协同设计:支撑系统需满足静态承重(电芯自重+堆叠压力)与动态抗振(运输/地震冲击)的双重需求。
3-模块化与兼容性:标准化接口与可扩展架构
标准化接口适配多尺寸电芯的本质是通过机械、电气、热管理的协同创新,在统一平台上实现电芯规格的柔性扩展。当前技术已从静态兼容转向动态调节,未来将向智能化、轻量化、跨场景融合方向演进。
a.机械结构协同创新:
机械接口标准化:定义统一的连接装置尺寸。
模块化电池包/柜设计:通过标准化尺寸的电池单元(如280Ah、314Ah电芯)构建可扩展的模组和电池柜,支持不同容量需求的柔性组合。
图1-280Ah 储能PACK箱体
b.电气系统动态调节
标准化通信协议与接口,如,BMS兼容性:制定统一的BMS(电池管理系统)通信协议,支持与不同厂商的PCS、电芯无缝对接;动态功率调节,通过虚拟惯量控制、多时间尺度优化算法,实现有功/无功功率的实时调整;以及自适应电气参数匹配设计。
c.热管理系统的智能化适配
分级热管理方案,如,电芯级采用阻燃高回弹泡棉、导热胶等材料,平衡隔热与散热需求,抑制热扩散;模组级集成液冷板与隔热层的一体化设计,提升循环寿命;系统级通过变频压缩机、多制冷支路动态调节制冷量。
智能化监控与预测,多传感器融合。在电芯极柱、大面等关键位置布置温度传感器,实现高精度温度采集;数字孪生技术通过云端监控和预测性维护,实时优化散热策略。
4-总结
储能Pack箱体空间优化已从单一结构改进转向多维度协同创新:
材料-结构-算法三元融合,如碳纤维箱体+CTP技术+AI排布算法的组合将成为主流。
模块化与标准化加速,以Pack为最小功能单元的标准化设计将推动行业降本增效。
热管理与空间利用深度绑定,浸没式液冷和动态温控技术进一步释放空间潜力。
我们会定期更新有关热设计与轻量化的技术与资讯,与您分享,供您参考,感谢您对迈泰的关注。
随着AI算力爆发式增长和数据中心功率密度持续攀升,传统风冷技术已难以满足散热需求,液冷技术凭借高效散热、节能降耗等优势成为必选项。在液冷技术中,冷板式与浸没式两大路径的竞争尤为激烈。本文将从技术特性、应用场景、成本经济性及未来趋势等角度解析两者的优劣势,并探讨其未来主导方向。
1-技术特性对比:冷板式兼容性强,浸没式散热效率更高
a.冷板式液冷:平滑过渡的“改良派”
兼容性强:无需对服务器结构进行大幅改造,可兼容现有风冷数据中心的基础设施,改造成本低、周期短。
安全性高:冷却液不与电子元件直接接触,泄漏风险较低,且可通过模块化设计(如快换接头、冗余管路)进一步降低风险。
成熟度高:冷板式技术已广泛应用于阿里云千岛湖数据中心、英特尔合作项目等场景,占据当前液冷市场90%的份额。
局限性:冷板式仅能覆盖部分高功耗部件(如CPU、GPU),其余热量仍需依赖风冷辅助散热,PUE值通常在1.1-1.2,略高于浸没式。
b.浸没式液冷:高效散热的“革新派”
浸没式液冷将服务器完全浸没于绝缘冷却液中,通过直接接触实现全器件散热。其核心优势包括:
极致能效:液体导热系数是空气的20-30倍,PUE可低至1.05,散热效率提升3倍以上。
空间节省:冷却系统体积仅为风冷的1/3,单机柜功率密度可达50kW以上,适合AI超算等高密场景。
静音环保:无需风扇,噪音降低90%以上,且无灰尘污染,延长设备寿命。
挑战:浸没式需定制化服务器、冷却液成本占比高达60%(如氟化液),且初期投资较高,生态兼容性待完善。
2-应用场景分化:中短期冷板式主导,长期浸没式潜力释放
a.冷板式:存量改造与新建IDC的“性价比之选”
老旧数据中心改造:冷板式可快速适配现有风冷架构,改造周期短、成本可控。例如,英特尔与比赫合作的模块化方案,通过标准化冷板设计降低部署难度。
中高密度算力场景:冷板式已支持单机柜130-250kW功率(如英伟达B系列GPU),满足多数AI训练需求。
b.浸没式:超算与绿色数据中心的“终极方案”
超高密度算力:下一代芯片(如英伟达Rubin系列)机柜功率将突破1000kW,浸没式成为唯一可行方案。
绿色节能需求:浸没式PUE逼近1.05,余热回收效率达90%(如联想方案),契合“双碳”目标政策。
c.市场格局现状
冷板式主导当前市场:2025年冷板式占液冷市场80%-90%,浸没式不足10%。并且已形成标准化接口(如英特尔的OCP冷板设计),浪潮、中科曙光等厂商方案兼容性强。国内“东数西算”工程要求新建数据中心PUE≤1.25,冷板式成为过渡首选。
浸没式蓄势待发:曙光数创C8000相变浸没方案实现PUE 1.04,阿里云“麒麟”数据中心验证单相浸没可行性。 英伟达B200 GPU(1000W+)等高功耗芯片倒逼浸没式应用,液冷算力密度提升30%-50%。 欧盟计划2028年禁用氟化液,国内碳氢/硅油冷却液研发加速(如中石化“昆仑”系列)。
3-权威观点PK
冷板派:冷板式是液冷普及的‘破冰者’,未来5年仍将承担80%液冷增量市场,浸没式需等待芯片功耗突破临界点。
浸没派:相变浸没是液冷的终极形态,冷板式仅是过渡方案。当单芯片功耗超800W时,浸没式将成为唯一选择。
中立派:技术路线分化反映算力需求分层,冷板服务‘东数’,浸没支撑‘西算’,双轨并行是未来十年主旋律。
4-行业机遇与策略
成本与生态博弈:冷板式短期占优,浸没式需降本破局。
冷板式:优化材料(铜铝复合)、提升加工精度(防泄漏工艺),推动模块化与标准化设计。
浸没式:研发高性价比冷却液(如单相浸没液)、兼容性机柜,联合芯片厂商定制散热方案。
技术储备:探索两相流冷板、智能监控系统(如AI动态调流),应对未来高功率需求。
5-结论
短期(2025-2027):冷板式主导通用场景,浸没式渗透率提升至15%-20%;长期(2030+):相变浸没式在高算力领域成为主流,冷板式退守中低密度市场。
胜负手:冷却液成本、芯片功耗跃升速度、国际环保政策。
我们会定期更新有关热设计与轻量化的技术与资讯,与您分享,供您参考,感谢您对迈泰的关注。
随着新能源汽车与储能产业的快速发展,轻量化、高安全性及高效热管理成为核心诉求。我司深耕铝合金材料加工领域,依托先进的材料选型、成型工艺与焊接技术,专注于电池托盘、液冷板、储能Pack箱及散热器的研发与制造。铝合金因其密度低(约2.7g/cm³)、强度高、耐腐蚀及优异导热性(热导率约150-220 W/m·K),成为新能源装备轻量化与热管理的理想选择。
1-铝合金材料选型及关键考量
不同产品对铝合金的性能需求差异显著,需结合强度、耐蚀性、焊接性及工艺适配性综合选材:
a.电池托盘
常用牌号:6061-T6、6005A-T6、6063-T6。
选型依据:
·需满足抗拉强度≥240 MPa(如6061-T6)以通过国标挤压、跌落及球击测试;
·焊接性要求高,需避免热裂纹(优先选用Mg/Si强化的6xxx系);
·耐腐蚀性通过阳极氧化或包铝工艺提升。
图1-铝合金电池托盘
b.储能Pack箱
常用牌号:5083、6061-T6(兼顾强度与耐蚀性)。
选型依据:
·需承受振动与冲击载荷,屈服强度需≥200 MPa;
·表面处理要求高,避免电化学腐蚀。
c.液冷板
常用牌号:3003、6061/6063、6082。
选型依据:
·高导热性与耐腐蚀性;
·液冷流道需复杂成型,优先挤压性能优的6xxx系。
2-工艺性能差异与加工难点
铝合金的加工需适配其物理特性,尤其在切割、CNC、焊接及表面处理环节:
a.切割与CNC加工
难点:
·高精度孔加工易因材料延展性产生毛刺或变形(如台阶孔边缘突起);
·薄壁结构(如液冷板流道)需控制切削力以防翘曲。
解决方案:
·采用金刚石涂层刀具提升刃口锋利度,减少挤压变形;
·优化加工参数(如高转速、低进给)配合通用CNC设备实现稳定加工。
b.焊接工艺
核心挑战:
·氧化膜(Al₂O₃熔点2050℃)阻碍熔合,易导致气孔与夹渣;
·部分合金热裂纹倾向高,需控制线能量与焊丝成分。
优选工艺:
·TIG焊(交流电源):适用于薄板,通过“阴极清理”破除氧化膜;
·MIG焊(大电流+氦混合气体):厚板焊接效率高,热输入可控。
图2-电池托盘焊接
c.表面处理
·绝缘耐压涂层:应用于电池托盘与Pack箱内部,需通过耐压测试(≥3000V DC/1min),涂层厚度20-50μm,确保高压环境下的绝缘安全性;
·保温除湿涂层:针对储能Pack箱,采用疏水材料(如氟碳树脂)降低内部结露风险,达因值≥34以保证附着力;
·防撞保护涂层:用于电池托盘外壁,选用聚氨酯弹性体(硬度≥80 Shore A),抗冲击性能提升30%以上;
·阳极氧化:常规防腐处理,膜厚误差≤3μm,适配复杂结构。
3-审验性检查与设备适配性
为满足新能源行业标准(如GB/T31467.3、UL2580),需进行多维度验证与工艺适配:
a.审验性检查
·结构强度:通过有限元仿真验证托盘承载、挤压及球击性能(最大应力≤材料屈服强度);
·密封性测试:液冷系统采用氦检漏(泄漏率≤1×10⁻⁶ mbar·L/s)与循环压力测试(0.5-1.5MPa/5000次);
·涂层性能验证:
绝缘涂层耐压测试(5000V DC/60s无击穿);
防撞涂层通过落球冲击(1kg钢球1m高度)与盐雾测试(1000h无剥落)。
b.设备适配性优化
· 通用CNC设备改造:通过高精度夹具设计与动态补偿算法,实现薄壁件加工变形量≤0.1mm;
·焊接参数库:针对不同铝合金牌号建立标准焊接参数(如电流、送丝速度),降低调试周期;
·涂层自动化喷涂:采用多轴机器人喷涂,结合红外固化技术,涂层均匀性误差≤5%。
结语
铝合金在新能源装备中的广泛应用,既是材料科学的胜利,亦是工艺创新的体现。我司将持续探索高强、耐蚀、易加工的新型铝合金,并通过工艺革新推动电池托盘、液冷板等产品的性能升级,助力行业迈向高效、轻量化的未来。
我们会定期更新有关热设计与轻量化的技术与资讯,与您分享,供您参考,感谢您对迈泰的关注。
在电子设备功率密度持续攀升的今天,散热设计已成为影响系统可靠性与寿命的关键环节。作为深耕热管理领域19年的专业制造商,我们结合典型工程案例与多物理场仿真经验,深度解析高功率场景下工程师易忽视的5大技术误区,并提供符合行业实践的解决方案。
误区1:高导热材料滥用,界面热阻计算偏差
典型问题:过度追求导热材料理论值,忽略界面接触热阻的工程实际。
案例解析:某车载激光雷达散热模组采用纯铜基板(导热系数401W/m·K),但未精确控制热界面材料(TIM)的涂覆厚度(设计0.1mm,实际波动±0.05mm),实测接触热阻达0.6°C·cm²/W,导致FPGA结温超标22%。经改用预成型导热垫(公差±0.02mm,热阻<0.03°C·cm²/W)并配合真空烧结工艺,结温降低17°C,MTBF(平均无故障时间)提升至10万小时。
优化方案:
材料选型:根据ASTM D5470标准实测TIM热阻,优先选用相变材料或金属填充弹性体。
工艺控制:采用自动点胶设备(精度±3%),确保厚度公差<10%,避免气隙产生。
误区2:风冷系统气流组织失配,局部热点失控
典型问题:盲目堆叠风扇数量,忽视流道阻抗匹配与边界层分离效应。
工程实例:某数据中心GPU集群采用4台12038风扇(风量200CFM),但因导流罩角度设计不当(90°直角弯折),实际有效风量仅达标称值的65%,局部温差达40°C。经CFD仿真优化,将导流罩改为渐扩式流道(扩散角<7°),并采用交错式鳍片布局(间距梯度从2mm增至3.5mm),整体风阻降低30%,热点温差控制在8°C以内。
核心策略:
流场设计:依据ISO 5801标准进行风洞测试,优化进出口面积比(建议1:1.2)。
动态调控:基于PWM风扇的Q-H曲线,匹配系统阻抗点至最高效率区间(通常为60-80%最大风量)。
误区3:环境防护设计失效,加速材料老化
典型问题:仅关注初始散热性能,忽略湿热/粉尘/盐雾等长期环境应力影响。
案例解析:某海上风电变流器采用6061铝合金散热器(表面阳极氧化处理),在盐雾环境下运行6个月后,氧化层剥落导致接触热阻上升50%,IGBT失效率激增。改用5052铝合金(耐盐雾>1000h)并喷涂聚氨酯三防漆(厚度50μm,符合IEC 60068-2-11标准),3年现场故障率下降75%。
设计要点:
涂层技术:高温场景采用等离子喷涂Al2O3陶瓷涂层(导热系数30W/m·K,耐温>800°C)。
密封结构:IP69K防护等级(双道硅胶密封圈+泄压阀),确保粉尘/水汽零侵入。
误区4:瞬态热负荷建模缺失,相变材料选型不当
典型问题:采用稳态仿真设计散热方案,无法应对毫秒级功率脉冲。
实测数据:某固态功率放大器在5G基站中承受2ms@2000W脉冲负载,传统铝基板方案瞬态温升达55°C,而采用微胶囊相变材料(石蜡/石墨烯复合,相变潜热220J/g)结合瞬态热仿真(ANSYS Icepak瞬态步长1ms),温升控制在18°C,满足MIL-STD-810G冲击测试要求。
动态管理技术:
相变封装:采用蜂窝结构封装相变材料(孔隙率>70%),避免液态泄漏且提升热扩散效率。
模型校准:基于红外热成像(采样率100Hz)修正仿真边界条件,误差<±1.5°C
误区5:TCO评估片面化,忽略隐性运维成本
典型问题:仅对比初期硬件成本,未量化能耗/维护/停机损失。
成本对比:某半导体工厂原采用风冷机柜(初期成本50万元),年电费120万元(PUE=1.8)。升级为两相浸没式液冷后(初期成本180万元),年电费降至45万元(PUE=1.05),且因减少洁净室空调负荷,年综合节支达90万元,2.1年即可收回增量投资(IRR>25%)。
决策模型:
精细化建模:引入蒙特卡洛模拟,量化设备故障率(Weibull分布)对TCO的影响。
政策叠加:结合碳税机制(如欧盟CBAM),液冷系统全生命周期碳排放减少60%,额外获得补贴15%
结语:从经验驱动到数据驱动的热设计范式升级
标准化流程:在概念设计阶段即导入JESD51-14热测试标准,避免后期返工(某光模块项目周期缩短30%)。
多学科协同:通过COMSOL Multiphysics耦合电磁损耗(HFSS提取)与热应变场,某雷达TR组件散热效率提升40%。
智能运维:部署光纤光栅温度传感器(精度±0.1°C)与数字孪生平台,实现故障预测(某超算中心意外停机减少90%)。
通过严谨的工程思维与全链路数据验证,热设计工程师可精准规避“隐形杀手”,为高可靠性系统奠定基础。作为行业实践者,我们致力于提供从材料到系统的闭环解决方案,与客户共同应对热管理挑战。
我们会定期更新有关热设计与轻量化的技术与资讯,与您分享,供您参考,感谢您对迈泰的关注。
1-关键部位的特殊公差要求
在EV电池托盘与储能液冷Pack箱体的制造中,关键连接面与接口的公差控制直接影响密封性、散热效率及装配精度。
a.液冷板安装面
液冷板是电池热管理系统的核心部件,其安装面的平面度直接影响冷却液流道的密封性。若平面度超差,会导致硅胶垫片压缩不均,引发局部泄漏或热阻升高。
b.焊接接缝错边量
电池托盘常采用铝合金焊接结构,焊缝错边会导致应力集中,降低疲劳寿命。尤其对箱体气密性要求高的场景(如IP67),需严控错边。
c.电池模组定位孔
定位孔用于精确固定电池模组,公差过大会导致模组错位,引发电气连接失效或机械振动风险。
d.固定螺栓孔位置度
螺栓孔用于箱体与底盘连接,位置度偏差会导致装配应力,甚至引发螺栓断裂。
e.箱体边缘直线度
箱体边缘直线度影响上下盖装配及IP防护等级,尤其是采用激光焊接的箱体,边缘需作为激光头跟踪基准。
2-尺寸公差对制造效率的影响
尺寸公差对制造效率的影响主要体现在其对加工流程、成本控制及产品质量的平衡上。合理的公差设计既能保证产品功能,又可优化生产节奏。尺寸公差的合理控制对制造效率的影响主要体现在以下几个方面:
a.加工精度与生产成本的平衡
·严格的尺寸公差虽能提升密封性和装配精度,但需采用高精度加工设备和复杂工艺,显著增加设备投入和加工时间。
·过度追求精度可能导致加工成本上升,需在关键功能部位设定严苛公差,非关键区域适当放宽公差以降低成本。
b.返修率与废品率控制
·合理的公差设计可减少因尺寸超差导致的返工。
·焊接变形是电池托盘制造中的主要问题,采用CMT冷焊工艺可优化热输入,减少焊接后变形,缩短返修周期。
c.模组化与标准化生产
·通过标准化组件,公差要求集中于局部可替换部件,降低整体加工难度。
·标准化公差设计还能支持多型号兼容,减少定制化加工需求。
3-平面度控制的行业标准与实际应用
针对新能源汽车电池托盘,行业标准提出严格要求:
a.平面度标准:液冷板安装面平面度需≤0.2mm,底部支撑板平面度≤0.5mm/m²,焊接后框架平面度误差≤0.8mm6。
b.制造工艺优化:采用CNC精铣、CMT冷焊及振动时效处理(VSR),结合激光干涉仪在线检测,降低变形风险。
c.材料选择:推荐使用6061等高强度铝合金,屈服强度≥1180MPa,兼顾轻量化与结构稳定性。
4-材料与工艺驱动的公差调整策略
a.材料创新驱动轻量化
采用轻量化高强铝合金(如6061)及复合材料(碳化硅增强铝基),结合阳极氧化与绝缘涂层,实现减重30%并提升耐腐蚀性,适配液冷系统散热需求。
b.工艺协同提升制造精度
一体挤压成型+搅拌摩擦焊(FSW)减少焊缝数量,CMT冷焊与激光焊接控制热变形。
c.仿真检测闭环保障可靠性
CAE仿真优化加强筋布局,激光扫描与氦检漏技术实现全流程监控,模组化设计兼容±5mm公差,降本增效。
我们会定期更新有关热设计与轻量化的技术与资讯,与您分享,供您参考,感谢您对迈泰的关注。
1-电池托盘/储能Pack箱体铝合金焊接工艺特征
在新能源液冷Pack箱体、电池托盘等产品的制造中,液冷流道与多腔体结构是典型的复杂设计特征(如图1所示)。这类结构往往包含以下特点:
图1:电池托盘典型设计
三维空间交错:流道呈蛇形分布,存在大量空间转折点;
多层级连接:主腔体与子腔体通过薄壁隔板连接(厚度2-3mm);
微型化特征:流道截面尺寸小(铝型材流道壁厚最小1.2mm),焊接可达性差。
2-多焊接技术结合在电池托盘制造中的难点分析
在电池托盘制造实践中,需要采用多焊接技术结合,例如搅拌摩擦焊(FSW)、冷金属过渡焊(CMT)、传统熔化焊(TIG/MIG)等技术的协同应用。这种组合旨在兼顾轻量化、强度、密封性及生产效率,但也面临以下核心难点:
a.多工艺热输入协同难题
不同焊接技术(如FSW、激光焊)热输入差异大,易引发材料性能突变与热变形,需通过优化焊接顺序及参数调节解决。
b.设备兼容性与效率瓶颈
设备切换复杂、参数同步精度要求高,需模块化工作站设计与智能焊机提升协同效率,降低节拍时间。
c.密封强度与成本平衡挑战
多焊缝交汇处泄漏风险高(占缺陷70%),需冗余密封+拓扑优化设计。
3-工程实践:电池托盘、储能液冷PACK箱多焊接工艺协同
a. 焊疤位置规划
· 焊接位置优化:在产品设计阶段,应充分考虑焊接位置的合理性,避免焊疤出现在关键部位或影响产品功能的区域。例如,调整前边框与水嘴的间隙,防止焊疤干涉;优化水嘴焊接位置,减少对产品性能的影响。
· 与产品结构的匹配:焊接位置应与产品结构相匹配,确保焊缝能够承受产品在使用过程中的各种载荷和应力。例如,在液冷板项目中,通过合理规划焊接位置,提高了产品的结构稳定性和可靠性。
· 便于操作和检测:焊接位置应便于操作人员进行焊接操作和后续的质量检测。例如,避免在难以到达或视野不佳的位置进行焊接,以提高焊接效率和质量。
b. 焊疤控制
· 焊疤大小:焊疤大小需严格控制,一般要求焊疤高度在4/6mm范围内,且焊疤不超出平面,以保证产品的外观和装配精度。例如,在液冷板项目中,通过调整焊接参数和工艺,成功控制了焊疤大小,避免了焊疤对产品性能和质量的影响。
· 焊疤形状:焊疤形状应尽量规则,避免出现过度熔化或不完全熔合的情况。通过优化焊接参数和操作技巧,可以有效改善焊疤形状,提高焊缝质量。
· 打磨处理:对于摩擦焊位置产生的下凹焊痕,采用打磨处理方式,确保表面平整,满足产品外观和性能要求。
c. 焊接顺序优化
· 分区焊接:对于大型产品,采用分区焊接的方法,可以有效控制整体变形。通过将产品分成若干区域,依次进行焊接,可以减少焊接过程中的热量集中,降低热变形的风险。
· 逐步校正:在焊接过程中,采用逐步校正的方法,及时调整焊接变形。通过在焊接过程中不断测量和校正产品的变形情况,确保最终产品的尺寸精度和形状符合设计要求。
· 优化焊接路径:合理规划焊接路径,避免在同一个区域反复焊接,减少热量输入。例如,在液冷板项目中,通过优化焊接路径,减少了焊接过程中的热量输入,提高了焊接质量。
d. 变形协同控制
液冷板在焊接过程中出现热变形,导致产品尺寸精度下降。
优化措施:
· 采用分区焊接和逐步校正的方法,控制整体变形。
· 优化焊接参数,降低电流和电压,减少热量输入。
· 使用工装夹具固定产品,减少焊接过程中的移动和变形。
· 采用对称焊接的方法,使焊接热量均匀分布。
我们会定期更新有关热设计与轻量化的技术与资讯,与您分享,供您参考,感谢您对迈泰的关注。
CTC(Cell-to-Chassis)技术因能显著提升电动汽车续航与空间效率而备受关注,但其能否真正取代传统电池技术仍存争议。制造端的核心瓶颈——电池托盘焊接工艺——成为决定这一技术未来的关键:复杂的结构设计、多元材料兼容性、严苛的热管理需求,让传统焊接技术面临巨大考验。本文从一线工程师视角出发,结合行业动态与工程实践,剖析CTC技术的潜力与局限,并探讨焊接工艺如何成为这场技术革命的“试金石”。
1-CTC技术的“理想与现实”
CTC技术通过将电芯直接集成到底盘,理论上可减少冗余结构件、提升能量密度,但其大规模应用的可行性正面临现实拷问:
车企的激进与谨慎:特斯拉、比亚迪等头部企业已推出CTC方案,但更多厂商仍持观望态度。行业数据显示,截止2025年2月全球CTC量产车型占比15-20%,传统CTP(Cell-to-Pack)技术仍是主流。
续航提升的“代价”:CTC虽能提升15%-20%能量密度,但底盘结构复杂度导致制造成本增加30%-50%(某咨询机构测算),成本与收益的平衡尚未明朗。
维修经济性争议:一体化设计使电池维修成本飙升,保险公司数据显示,CTC车型事故后电池总成更换率高达70%,远高于传统车型的25%。
这些矛盾让CTC技术的未来充满变数,市场端能否突破20%取决于三大变量:特斯拉Cybertruck量产爬坡进度;中国车企价格战是否倒逼CTC降本;欧洲法规对电池可维修性的妥协程度。而制造端的焊接工艺水平,将成为决定其能否跨越实验室与量产鸿沟的关键。
2-焊接工艺的三大“生死关”
对于电池托盘制造商而言,CTC技术落地需攻克三个核心难题:
a.“微米级”精度与效率的博弈
传统焊接工艺可容忍0.5mm误差,但CTC托盘因需承载更多电芯,接缝数量增加3倍以上,且多分布于曲面异形部位。某厂商测试表明,当焊接定位误差超过0.15mm时,电芯组装的良品率会从99%骤降至82%。更棘手的是,精度提升往往伴随效率下降——激光焊精度虽高,但设备成本是传统焊接的5倍以上。
b. 材料混搭的“水火不容”
为兼顾轻量化与强度,CTC托盘常采用“铝合金+碳纤维+特种钢”的混合结构。不同材料的热膨胀系数差异可达20倍(如铝23μm/m·K vs. 碳纤维0.8μm/m·K),焊接时易产生内应力导致开裂。某企业尝试铝-碳纤维连接时,焊缝开裂率一度高达18%,远超行业可接受的3%阈值。
c.热影响区的“隐形杀手”
焊接高温可能损伤电芯周边绝缘材料或传感器线路。某车企曾因焊接热输入控制不当,导致电池模组自放电率增加50%。工程师必须在0.1秒内将焊接温度波动控制在±15℃以内——这相当于在焊枪上装一个“高精度温度刹车”。
3-焊接工艺的三大“生死关”
破局之路:没有银弹,唯有系统创新
面对这些挑战,行业正在探索三条突围路径:
a. 工艺组合的“鸡尾酒疗法”
激光电弧复合焊:结合激光焊精度与电弧焊熔深优势,使铝合金焊接速度提升40%;
冷金属过渡技术(CMT):通过精准热输入控制,将热影响区面积缩小60%;
机器人智能补偿系统:基于实时焊缝扫描数据自动调整焊枪路径,将复杂曲面焊接合格率从75%提升至95%。
b. 材料端的“提前妥协”
部分企业开始与材料供应商联合开发“焊接友好型”复合材料。例如,某国产改性铝合金(通过物理、化学或工艺手段调整后的铝合金材料)的焊接裂纹敏感性从7级降至3级(按ISO标准),虽牺牲了5%的轻量化效果,但使焊接良品率提高至98%。
c.检测维度的“数字孪生”
通过焊接过程全数据采集(电流、温度、速度等),结合AI模型预测缺陷概率。某工厂引入该技术后,焊接缺陷的在线检出率从80%提升至97%,报废成本降低45%。
4-工程师的新命题:在不确定中寻找确定性
a.CTC技术的争议本质上是“系统优化”与“局部极限”的博弈:
若焊接工艺突破速度慢于车企降本预期,CTC可能沦为小众技术;
若材料、工艺、检测技术协同突破,则有望开启电动汽车结构设计的新纪元。
b.对于工程师而言,需从两个维度重构能力:
跨领域知识整合:理解电化学性能对焊接热输入的敏感阈值;
敏捷响应能力:某欧洲供应商案例显示,能在一周内完成新合金材料焊接参数优化的团队,订单获取概率提升3倍。
CTC技术站在了“颠覆性创新”与“量产陷阱”的十字路口。它或许不会完全取代现有技术,但正在倒逼焊接工艺向更高精度、更强兼容性、更智能控制的方向进化。这场技术马拉松中,真正的赢家未必是最早出发的车企,而是那些在制造端把“不可能焊缝”变成“标准化接口”的工程师团队。
我们会定期更新有关热设计与轻量化的技术与资讯,与您分享,供您参考,感谢您对迈泰的关注。
随着CTP(Cell to Pack)技术彻底颠覆传统电池包结构,电池托盘的“角色”从被动承载转向主动集成。焊接工艺一跃成为安全与性能的核心命门。轻量化(壁厚仅1.5mm)、零气孔密封、多材料(铝/铜/碳纤维)集成需求,让传统焊接深陷变形与缺陷困局。行业正通过材料革新、智能质检与工艺迭代破局。本文将拆解CTP对焊接的颠覆性挑战,探寻高精度与高可靠性的技术路径。
1-CTP技术对电池托盘结构设计要求的变化分析
CTP(Cell to Pack)技术通过取消传统电池包中的模组结构,直接将电芯集成到电池包中,这一技术革新对电池托盘的结构设计提出了全方位、多维度的升级要求。以下从材料、性能、工艺、集成化等角度展开具体分析:
(1)结构强度与防震性能的全面提升
a.取消模组后的力学承载需求:
CTP技术省去模组结构后,电池托盘需直接承担电芯的支撑、固定及外力缓冲功能。传统模组分散了机械载荷,而CTP托盘需整体吸收充放电过程中电芯的膨胀形变(如方形电芯膨胀力可达10-20kN),同时抵御车辆行驶中的震动、挤压和冲击载荷。
b.材料与结构优化方向
· 高强度铝合金主导:早期钢材因重量大逐渐被替代,6061-T6成为主流,其比强度高、耐腐蚀性强,可满足轻量化与高刚性双重需求。
· 复合结构设计:如零跑汽车的“双骨架环形梁”结构,通过纵横梁隔间增强局部抗冲击性,同时采用挤压工艺优化材料分布,减少冗余重量。
· 镁铝合金与碳纤维探索:镁铝合金比传统铝材减重30%,碳纤维复合材料兼具高强与轻量化特性,但受限于成本与工艺成熟度,目前仅用于高端车型。
(2)气密性与热管理集成要求
a.密封性能升级
取消模组后,电池包内部冷却液循环和气体密封完全依赖托盘,焊接缺陷(如气孔、裂纹)可能导致泄漏风险。
图1-电池托盘气密性检测
b.热管理功能集成
CTP托盘需集成液冷板、导热胶等组件。例如,结构胶用于固定电芯并传递膨胀应力,聚氨酯导热胶(导热系数>1.5 W/m·K)用于电芯间及与液冷管的热传导,单PACK胶黏剂用量较传统结构增加50%以上。托盘内部需设计流道优化冷却效率,同时避免焊接热影响区对密封性的破坏。
(3)轻量化与材料创新
a.材料选择趋势
铝合金挤压与压铸工艺:挤压铝型材用于框架结构(如特斯拉4680电池托盘),压铸工艺(如一体化压铸)简化焊接工序,减重15%-20%。
塑料复合材料应用:例如使用玻纤增强PA6材料,用于非承载部位以进一步减重,但需解决与金属连接界面的兼容性问题。
b.轻量化设计策略
拓扑优化:通过CAE仿真减少冗余材料,在保证强度的前提下降低托盘重量。
薄壁化与集成化:托盘壁厚从3mm降至1.5-2mm,同时集成BMS支架、线束通道等功能部件,减少零件数量。
(4)集成化与模块化设计
a.功能组件的高度集成
CTP托盘需整合电池管理系统(BMS)、高压连接器、防火隔离层等模块。
b.模块化与兼容性设计
焊接产线需要支持多型号托盘混线生产,能够实现“一键换型”,兼容不同电芯尺寸(如方形、圆柱)的托盘结构。
2-CTP技术革新对焊接工艺的具体挑战
CTP(Cell to Pack)技术显著提升了空间利用率和能量密度,但也对焊接工艺提出了前所未有的挑战。
(1)焊接缺陷控制难度激增
a.气孔与密封性挑战
CTP技术取消模组后,电池托盘需直接承担密封功能,焊接气孔(铝合金焊接中常见缺陷)将直接导致冷却液泄漏或气体渗透风险。
b.裂纹与材料兼容性
高锌铝合金(如7系)在焊接时易因热应力产生裂纹。
c.间隙与装配误差
多电芯直接集成导致托盘结构拼接点增加,装配误差累积可能使焊缝间隙超过±1mm。
(2)材料体系升级带来的工艺适配难题
a.轻量化材料的焊接挑战
CTP托盘材料从钢材转向铝合金(6061-T6、7075-T6)、镁铝合金(减重30%)及碳纤维复合材料。铝合金焊接需解决氧化膜难熔、热导率高导致的熔深不足问题。
b.异种材料连接技术
托盘集成液冷板(铜/铝)、防火层(陶瓷基复合材料)等功能组件时,异种材料界面易出现脆性金属间化合物。
(3)结构复杂性与精度要求升级
a.大尺寸薄壁结构变形控制
CTP托盘壁厚从3mm减至1.5-2mm,焊接热变形敏感性激增。
b.高密度焊点与工艺效率
单托盘焊点数量从传统模组的2000个增至5000个以上。
图2-电池托盘焊接
3-生产工艺与质量控制的升级
CTP技术推动电池托盘焊接从“单一工艺”向“多技术协同、智能化、绿色化”转型。制造厂需聚焦三大方向:
技术升级:突破气孔、裂纹等缺陷控制,适配轻量化材料;
智能化跃迁:全流程数字化与AI质检实现高精度生产;
生态协同:联合材料商、设备商、主机厂共建技术标准。
我们会定期更新有关热设计与轻量化的技术与资讯,与您分享,供您参考,感谢您对迈泰的关注。
铝合金等轻质材料因其优异的性能成为主流选择,但薄板焊接中的热输入控制、变形抑制及工艺稳定性等难题对传统焊接技术提出了巨大挑战。冷金属过渡焊(CMT)凭借低热输入、无飞溅过渡及智能化参数控制等优势,为电池托盘制造提供了革新性解决方案。
本文深入探讨CMT技术在电池托盘薄板焊接中的精准控制策略,分析其适配性、工艺难点及复合应用场景,以期为高效、高质生产提供理论支持与实践参考。
图1 104S储能电池液冷下箱体CMT焊接
1-电池托盘焊接的工艺要求与CMT适配性
CMT技术通过低热输入、无飞溅过渡和智能化参数控制,完美适配电池托盘焊接的高精度、低变形与高效率需求。
(1)电池托盘焊接的核心工艺要求
a.材料适配性与轻量化需求
电池托盘多采用轻质铝合金(如6xxx系列、6061等),部分高端车型探索碳纤维复合材料,需满足高强度(抗拉强度达母材60%-70%)与低密度(铝合金密度2.7g/cm³)要求。
异种材料连接需求:例如钢铝混合结构,需克服热膨胀系数差异导致的变形。
b.焊接质量与性能指标
低热输入与变形控制:薄板(0.3-3mm)焊接需确保变形量≤2mm,尤其长直线焊缝需分段焊或反变形设计。
密封性与强度:焊缝需完全密封以防止电解液泄漏,并通过剪切试验(如T/CWAN 0027-2022标准要求)。
气孔率控制:铝合金焊接易产生气孔,需将气孔率控制在0.5%以下。
c.生产效率与自动化要求
批量生产需实现焊接速度≥7mm/s,单托盘焊接时间缩短至5-10分钟。
自动化工作站需兼容双工位设计(装配与焊接同步)和多机器人协同作业。
(2)CMT技术适配电池托盘焊接的关键优势
a.低热输入的精准控制
CMT通过熔滴短路时焊丝回抽切断电流,热输入量比传统MIG焊减少33%,尤其适用于0.3mm超薄板焊接(无烧穿风险)。
冷热交替循环(电弧加热-熔滴过渡-焊丝回抽)减少热积累,焊接变形量可控制在1.5mm以内(比亚迪、北汽案例)。
b.工艺稳定性与质量提升
无飞溅焊接:CMT的机械回抽机制消除熔滴爆断飞溅,减少返工率。
气孔控制优化:采用Ar+30%He混合保护气体,气孔数量比纯Ar减少50%,气孔尺寸缩小至≤0.3mm。
间隙容忍度高:可适应1.5mm装配间隙,降低夹具精度要求。
c.自动化集成与效率提升
双工位工作站(如泰翔科技设计)实现焊接与装配并行,效率提升2倍。
机器人对称焊接(两台机器人同步作业)配合反变形设计,缩短节拍至10分钟内。
2-电池托盘CMT工艺难点分析
图2 CMT焊接工艺过程
(1)材料特性与焊接缺陷控制
a.铝合金焊接的气孔敏感性
铝合金电池托盘(如6061、6063等)在CMT焊接中易因熔池快速凝固、氢溶解度变化等因素形成气孔。保护气体成分对气孔抑制至关重要:纯Ar保护时,气孔率较高(约5%);采用Ar+30%He混合气体可加速气体逸出,气孔率降至0.5%以下。电感修正参数(如负向调节)可优化熔池流动,减少气孔尺寸。
b.热裂纹倾向与成分偏析
铝合金中Mg、Si等元素的偏析易导致焊缝晶界脆化。CMT工艺的低热输入虽能减少热影响区,但需精确控制焊接速度与送丝量,避免熔深不足或局部过热引发裂纹。
c.异种材料焊接的冶金兼容性
若托盘涉及铝-钢或铝-复合材料连接(如防撞梁与箱体),需克服界面脆性相(如FeAl₃)和Zn蒸气干扰。
(2)工艺参数优化挑战
a.熔深与热输入的平衡
电池托盘需满足T/CWAN 0027标准对焊缝熔深(≥0.8mm)的要求。CMT工艺的低热输入特性可能导致熔深不足,需通过调整弧长,利用脉冲电流提升熔池穿透力。
b.焊接速度与稳定性的权衡
自动化产线要求焊接速度≥1.2m/min,但高速下易出现电弧不稳定或熔滴过渡不均。
c.复杂焊缝的搭桥能力
托盘结构常含大间隙(0.5-1.5mm)或异形焊缝(如T型接头)。
(3)结构设计与制造工艺适配性
a.薄板焊接变形控制
铝合金托盘壁厚通常为2-3mm,传统MAG焊变形量可达1.2mm,而CMT焊接通过低热输入可将变形量降至0.3mm以下。但需配合反变形工装设计和机器人对称焊接(双工位工作站)以进一步提升精度。
b.长焊缝的连续性与密封性
电池托盘密封焊缝长度可达数米,需避免断弧或熔池波动。CMT技术通过每秒70次以上的电弧重燃周期,确保焊缝均匀性,配合激光跟踪系统可将气密合格率提升至99%。
c.多工艺复合应用的协同性
高端托盘常采用CMT+FSW(搅拌摩擦焊)复合工艺:CMT用于复杂结构(如边框与底板连接)。FSW用于高载荷区域(如纵梁)以提升强度。需解决两种工艺的衔接参数(如预热温度、焊后热处理)匹配问题。
3-CMT工艺在电池托盘制造中的典型应用场景
(1)电池托盘主体结构的连接
a.边框与底板焊接
CMT工艺广泛应用于铝合金电池托盘的边框与底板连接,尤其适用于 长焊缝、薄板(2-3mm厚度) 场景。
b.横梁与底板连接
在CTP电池托盘设计中,由于横梁数量减少且结构复杂,CMT工艺被用于:高精度定位焊接:横梁与底板的局部连接(如T型接头)需避免熔深不足,CMT通过电弧长度数字化控制(如福尼斯CMT Advanced技术)实现稳定熔深≥0.8mm。多材料适配:若横梁采用铝镁合金(如6061)而底板为高强度铝材,CMT可通过Ar+He混合气体保护减少气孔,同时适应不同材料的导热差异。
(2)薄板与复杂几何结构的焊接
a.薄壁铝合金焊接(2-3mm)
电池托盘的轻量化需求推动薄板应用,但传统MIG焊易导致变形。CMT工艺的优势在于:
b.超薄板焊接:泰翔自动化通过CMT技术实现0.3mm超薄板的无飞溅焊接,用于电池托盘边缘密封结构。
c.异形焊缝搭桥:针对托盘内部加强筋、防撞梁等异形结构,CMT Gap Bridging模式通过焊丝回抽与电弧重定向,可填补0.5-1.5mm间隙,避免未熔合缺陷。
d.密封性要求高的焊缝:电池托盘的密封性直接关系电池安全,CMT工艺通过以下方式保障:
· 连续长焊缝:采用每秒70次以上的电弧重燃周期(如伏能士LaserHybrid技术),确保数米长焊缝的连续性,气密合格率达99%。
· 低热输入控制:相比激光焊,CMT热输入更低,减少熔池波动对密封胶层的热影响,适配涂胶工艺。
(3)多工艺复合制造场景
a.CMT+FSW复合工艺
在高端电池托盘生产线中,CMT常与搅拌摩擦焊(FSW)协同:
分工协作:CMT用于复杂结构(如边框、异形接头)的灵活焊接,FSW用于高载荷区域(如纵梁)以提升强度。例如上海伟晟的自动化生产线通过CMT+FSW+CNC组合,将托盘生产效率提升30%。
工艺衔接优化:华数锦明的生产线采用模块化设计,通过预热参数匹配(如CMT焊后局部加热至150℃)实现与FSW的无缝衔接。
b.与FDS/SPR铆接技术结合
第二代CTP技术中,CMT与摩擦自拧紧(FDS)、自冲铆接(SPR)技术协同:混合连接方案:例如框架与底板的承重区域采用FSW,而可拆卸部件(如水冷板、隔热层)通过CMT焊接预定位,再以FDS铆接固定,兼顾强度与维护便利性。
我们会定期更新有关热设计与轻量化的技术与资讯,与您分享,供您参考,感谢您对迈泰的关注。
新能源汽车及储能的爆发式增长,将电池托盘焊接技术推向了制造工艺的核心战场。面对铝合金轻量化与复杂结构的双重挑战,本文从工艺本质到工程实践,深入解析电池托盘焊接技术,对比传统熔化焊、搅拌摩擦焊与激光焊的工艺原理、性能指标及适用场景。通过热影响区、接头强度、耐腐蚀性等多维度分析,为您呈现焊接技术的优劣势。
1-技术原理对比
a.传统熔化焊
原理:通过电弧、等离子弧等热源将焊接接头局部加热至熔化状态,形成熔池,冷却后凝固形成焊缝。需使用保护气体(如CO₂、氩气)或焊渣防止氧化,可能添加焊丝或焊条作为填充材料。
特点:熔池温度高、冷却快,易形成粗大柱状晶;热影响区(HAZ)宽,冶金过程不充分,易产生气孔、裂纹等缺陷。
b.搅拌摩擦焊(FSW)
原理:利用高速旋转的搅拌头与工件摩擦产热,使材料达到热塑性状态,通过机械搅拌和塑性流动实现固相连接。无熔池形成,无需填充材料。
特点:焊接温度低于材料熔点80%,动态再结晶形成细小晶粒,焊缝致密无气孔,热输入低,变形小。
c.激光焊
原理:高能量密度激光束聚焦于工件表面,通过热传导(功率密度<10⁵ W/cm²)或深熔焊(功率密度≥10⁵ W/cm²,形成匙孔效应)实现材料熔化和连接。
特点:热影响区极窄,熔深大,焊接速度快,可实现精密焊接;但对材料表面反射率敏感,需严格控制工艺参数。
a-传统熔化焊 b-搅拌摩擦焊 c-激光焊
图1 电池托盘常用焊接技术原理
2-性能指标
a.热影响(HAZ)区对比
关键分析:
传统熔化焊:高热量输入导致HAZ宽,晶粒粗化和冶金缺陷(如气孔)显著降低材料性能。
FSW:固态连接避免熔池,HAZ分为TMAZ和HAZ,晶粒细化(NZ)与局部变形(TMAZ)共存。
激光焊:极窄HAZ(约0.1-0.5 mm)得益于高能量密度和快速冷却,但需注意匙孔效应对组织均匀性的影响。
b.接头强度对比
关键分析:
传统熔化焊:快速凝固导致粗晶和缺陷,接头强度显著降低。例如MIG焊铝合金的抗拉强度仅为母材的72.8%。
FSW:动态再结晶形成细晶(NZ),但TMAZ晶粒变形和HAZ强化相溶解可能成为薄弱区。
激光焊:高冷却速率抑制晶粒粗化,焊缝强度接近母材。
c.耐腐蚀性对比
关键分析:
传统熔化焊:粗晶和缺陷导致腐蚀优先发生在HAZ和熔合线。
FSW:NZ因细晶和均质化耐蚀性优,但HAZ晶粒粗化和第二相析出(如含Fe相)可能成为腐蚀敏感区。
激光焊:窄HAZ和均匀组织减少腐蚀活性点,但需注意表面氧化层对耐蚀性的影响。
3-适用场景
a.传统熔化焊
· 适用部位:
框架与底板连接:用于电池托盘主体结构的框架与底板焊接,例如比亚迪、北汽等车型采用间断焊或满焊工艺连接铝型材框架与底板。
边梁及小件补焊:因结构复杂或空间限制,部分边梁、加强筋等小件需配合其他工艺(如FSW)进行补焊。
· 适用焊件:
厚板焊接(如钢制托盘或铝合金厚板)。
非密封性要求的辅助结构(如电池包边角固定件)。
· 适用材料:
铝合金:6系列铝合金(如6061-T6)的厚板焊接,但接头强度较低(母材的70%-80%)。
钢材:钢制电池托盘的框架焊接,成本低但重量较大。
· 局限性:
热输入大导致变形显著,不适用于高精度或薄板焊接。
b.搅拌摩擦焊(FSW)
· 适用部位:
底板拼接:铝合金托盘的底板长焊缝拼接,如水冷通道一体化结构(广东迈泰技术案例)。
密封性要求高的区域:电池托盘与箱体连接处,因FSW焊缝致密无气孔,保障密封性(如吉利、小鹏车型的双面FSW结构)。
复杂型材连接:铝挤压型材的T型接头、中空型材焊接(双轴肩FSW技术可自支撑焊接)。
· 适用焊件:
铝合金挤压型材(如底板厚度10mm、壁厚2mm的双层截面设计)。
异种材料焊接(铝/铜、铝/镁等),但需特殊工艺优化。
· 适用材料:
铝合金:主流材料为6系列(6061-T6、6005A-T6、6063-T6),接头强度达母材80%-90%。
镁合金:轻量化托盘(如瑞松科技案例),但需控制热输入防止晶粒粗化。
· 技术优势:
固相连接避免熔焊缺陷,适用于轻量化、高密封性场景。
c.激光焊
· 适用部位:
高强钢托盘关键焊缝:如电池托盘与车身连接的高应力区域。
精密密封钉焊接:电池托盘盖板密封钉焊接,速度可达40 mm/s,热影响区极窄。
薄板拼接:铝或钢制托盘的薄板(<3mm)高效拼接,减少变形。
· 适用焊件:
高精度、自动化产线的焊接(如机器人激光焊接系统)。
异形结构(如曲面焊缝),需搭配高动态定位系统。
· 适用材料:
高强钢:抗拉强度≥1000MPa的钢材,激光焊可保留母材95%强度。
铝合金:需表面预处理(如阳极氧化或镀层)降低反射率,成本较高。
· 局限性:
厚板焊接需多道次(如>8mm铝合金),效率低于FSW。
我们会定期更新有关热设计与轻量化的技术与资讯,与您分享,供您参考,感谢您对迈泰的关注。
作为电池托盘制造厂的一线工程师,参与过多个新能源汽车电池壳体项目,深刻体会到行业在“轻量化-安全-成本”三角关系中的博弈。本文将从材料路线、制造工艺及未来趋势三个维度,结合实际案例,解析当前技术路线的选择逻辑与产业化挑战。
1-材料路线:轻量化与成本的权衡
电池壳体材料的选择直接影响整车性能与经济性,目前主流路线可归纳为铝合金、高强钢及复合材料三大类,各有适用场景。
a. 铝合金路线:轻量化的主力军
· 挤压铝型材:BYD的多款车型电池壳体均采用挤压铝型材制造,通过优化截面形状实现减重,同时提升结构刚度。
· 压铸一体化:特斯拉4680电池与CTC技术结合,减重超50%,但模具成本超2亿元,需年产50万件以上摊薄成本,适合头部车企规模化生产。
· 复合铝材:保时捷Taycan采用铝-碳纤维混合结构,进一步减重15%,但成本增加30%,仅限高端车型。
b. 高强钢路线:成本敏感市场的逆袭
热成型钢(如22MnB5)屈服强度达1500MPa,商用车渗透率超40%,单GWh成本比铝低40%,但能量密度牺牲约8%。因此,10万元以下车型普遍采用高强钢,兼顾成本与基础安全性。
c. 复合材料:高端化的试探
· SMC材料:电池包上壳体采用玻璃纤维增强复合材料,比钢减重30%,但需通过增加厚度(3mm+5mm加强筋)弥补抗冲击性短板。
· 碳纤维:宝马i3壳体比铝轻50%,但成本高达800元/kg,量产难度大,目前仅用于豪华车型。
实践总结:材料选择需匹配车型定位。中端市场(20-30万元)以铝基材料为主,低端市场依赖高强钢,而豪华车型则探索碳纤维复合方案。
2-制造工艺:效率与可靠性的平衡术
电池壳体的制造工艺直接影响生产效率和产品可靠性,当前主流技术路线包括压铸、挤压焊接及结构集成技术。
a. 压铸VS挤压焊接
· 挤压铝型材(通用Bolt采用):单件成本约800元,适合大批量生产,但工序复杂。
· 压铸铝(蔚来ET5):单件成本1500元,但生产效率提升5倍,适合快速爬产需求。
· 搅拌摩擦焊(FSW):较传统弧焊变形减少50%,抗疲劳性能提升30%,但设备投资需增加40%,适合对寿命要求高的商用车型。
b. 结构集成技术
· CTP无模组化(宁德时代麒麟电池):空间利用率从72%提升至85%,成本降幅15-20%,但需加强热失控防护设计。
· CTC底盘一体化(特斯拉Model Y):减少370个零件,续航提升54%,但维修成本增加300%,对售后体系提出挑战。
关键数据对比
产线经验:CTP技术因兼容性高,仍是当前主流;而CTC需车企与电池厂深度协同,短期内难以普及。
3-未来趋势:技术融合与智能化升级
a. 材料复合化
铝/碳纤维混合壳体(如保时捷Taycan概念)可减重15%并实现800MPa抗压强度,但界面结合强度需>25MPa(丰田bZ4X量产合格率仅65%),工艺稳定性待突破。
b. 功能集成创新
· 液冷板与壳体一体化(广汽弹匣电池):冷却接触面积增加50%,温差控制<5℃,但铝-铜异种焊接气孔率需通过激光摆动焊优化。
· 嵌入光纤传感器(大陆集团方案):实时监测壳体应变与温度,BMS响应速度提升30%,但需解决传感器耐久性问题。
c. 绿色循环体系
宝马闭环回收再生铝技术将碳排放降低60%,但再生材料性能损失需控制在10%以内。此外,大型薄壁压铸(如力劲9000T压铸机)需精确控制模具温差(±5℃),毛刺清理效率成为量产瓶颈。
工艺突破方向:
· 复合材料成型周期压缩(如LGF-PP注塑周期需从180秒缩短至90秒);
· 数字孪生技术应用,将碰撞仿真误差从±20%降至±5%,提升设计可靠性。
4-市场分层与产业化展望
短期(1-3年):CTP+挤压铝型材仍为主流,宁德时代凭借34%市占率持续领跑;
中期(5-10年):CTC与碳纤维在高端市场加速渗透,预计2030年碳纤维占比达25%;
长期目标:能量密度向400Wh/kg突破,同时在国标30分钟热失控防护基础上,进一步提升安全冗余。
5-结语
电池壳体技术路线的选择本质是“场景化适配”,需综合考虑车企定位、成本阈值及供应链成熟度。作为工程师,我们既要拥抱材料与工艺的创新,也需立足量产可行性,在轻量化、安全与成本的动态平衡中寻找最优解。未来,随着智能化与绿色制造技术的成熟,电池壳体将逐步从“被动防护”转向“主动安全”,为新能源汽车的全面普及提供坚实支撑。
我们会定期更新有关热设计与轻量化的技术与资讯,与您分享,供您参考,感谢您对迈泰的关注。
在实际的生产、组装及使用过程中,电池托盘的绝缘耐压失效问题时有发生,犹如隐藏在新能源产业高速发展的暗礁,威胁着车辆的行驶安全与储能系统的可靠运行,本文试图结合制造实际,对典型失效模式进行分析,以期为相关从业者提供一些粗浅的参考,助力行业同仁共同探索提升电池托盘绝缘耐压性能的有效途径。
下篇-常见失效分析
图1 绝缘耐压测试
1-常见失效产生机理分析
储能与新能源汽车用电池托盘应用场景存在差异,导致绝缘耐压要求及失效情况既有共性也有差异,具体如下:
a.差异点
动态载荷 :新能源汽车需应对 20 - 2000Hz 的高频机械振动,而储能系统主要面临长期静态形变,形变累积时间超 10 年。
电压等级 :新能源汽车电池托盘的绝缘耐压需达 3000VDC 及以上(依据 GB 38031),储能系统则要求绝缘耐压在 4200VAC 及以上(依据 IEC 61439)。
失效加速因子 :新能源汽车因每年超 2000 次的充放电循环产生热应力,加速绝缘失效;储能系统则因 7×24 小时运行,年均运行时长超 8000 小时,导致电化学老化,进而加速绝缘失效。
b.共性要点
两者均需通过绝缘电阻监测(冷态不低于 100MΩ,热态不低于 1MΩ/kV)以及局部放电量控制(小于 5pC),来实现绝缘失效的预警。
2-常见的制造缺陷引发的电池托盘绝缘耐压失效
(1)绝缘耐压施工阶段
a.潜在失效与原因分析
· 材料缺陷:
原因:绝缘材料耐压等级不足、受潮老化或表面污染(油污、金属碎屑)。
表现:绝缘电阻低(<100MΩ)、耐压测试漏电流超标或直接击穿。
· 工艺问题:
原因:金属碎屑残留(焊接/切割工艺粗糙)、绝缘涂层厚度不均或未固化。
表现:局部放电、绝缘层破损引发短路。
· 环境干扰:
原因:高温高湿导致材料吸潮、化学腐蚀。
表现:绝缘性能随环境恶化,冷凝水引发爬电。
· 测试失误:
原因:测试电压/时间设置错误(如未按GB/T 38661标准)、接地不良。
表现:误判合格或过压损坏部件。
b.应对策略
· 材料优化:选用耐压≥1000V DC的防潮材料(如碳纤维复合材料),涂覆防污涂层。
· 工艺管控:采用自动化焊接/喷涂设备,设置洁净车间。
· 环境管理:安装温湿度监控,施工前预烘干材料。
· 测试规范:分段测试(500V预检 + 1000V正式测试),校准仪器并记录数据。
(2)模组安装阶段
a.潜在失效与原因分析
· 装配误差:
原因:绝缘衬垫漏装、螺栓过紧压损绝缘层。
表现:模组与壳体间绝缘电阻低,耐压击穿。
· 机械损伤
原因:搬运工具划伤、金属碎屑刺穿绝缘膜。
表现:局部短路或运行中突发失效。
· 设计兼容性
原因:模组与托盘尺寸偏差导致电气间隙不足。
表现:寄生电容引发电压叠加击穿。
· 电气连接隐患:
原因:线束未固定导致磨损、连接器密封失效。
表现:高压线束绝缘层磨损漏电。
b.应对策略
· 防错设计:使用定位销工装防漏装,定制螺栓长度防过紧。
· 洁净操作:安装前吸尘清理,工具包裹防刮擦硅胶。
· 公差仿真:通过CAE验证模组与托盘的匹配度,确保间隙≥10mm。
· 过程检验:安装后兆欧表抽检(≥100MΩ),分段耐压测试定位故障点。
(3)系统集成阶段
a.潜在失效与原因分析
· 跨系统接口失效:
原因:部件绝缘参数不匹配(如连接器耐压等级差异)。
表现:高压母线连接处击穿或BMS受干扰。
· 寄生电容叠加:
原因:多模组并联后总寄生电容增大,容升效应显著。
表现:系统级测试漏电流超标。
· 环境应力失效:
原因:振动导致绝缘疲劳、冷却液渗入高压接口。
表现:运行中绝缘电阻周期性下降。
· 测试盲区:
原因:未模拟真实工况(高温/振动/湿度)。
表现:实验室通过但实际运行失效。
b.应对策略
· 兼容性设计:统一供应商部件标准。
· 寄生电容控制:增加聚酰亚胺隔离层,SPICE仿真优化布局。
· 工况模拟测试:执行“-40℃~85℃循环+5Hz~200Hz振动+耐压”复合测试。
· 智能监测:集成在线绝缘监测模块,AI预测潜在风险。
3-绝缘耐压测试
绝缘耐压测试既是安全保障手段,也可能成为失效诱因。绝缘耐压测试本身可能因操作不当、设备问题或设计缺陷引发失效,甚至对被测设备造成二次损伤。
(1)测试过程中常见的失效类型
(2)应对策略如下:
a.测试参数精准控制
· 电压与时间:按标准设定;对容性负载(如电池模组)启用动态补偿算法,抑制容升效应。
· 漏电流阈值:根据设备规格设定(如≤10mA),并区分直流/交流模式(DC测试需更低阈值)。
b.设备与操作规范
· 仪器校准:耐压测试仪每6个月校准一次,高压线绝缘层每日目视检查。
· 安全操作:测试前强制断开低压电路;采用机械臂或自动夹具避免人工接触高压区域。
c.失效预防与修复
· 分段测试:对复杂系统分模块测试(如先测高压母线,再测模组绝缘),定位击穿点。
· 失效修复:击穿后使用环氧树脂填补破损处,修复后需重新通过全电压梯度测试(如500V→1000V阶梯加压)。
d.环境与数据管理
· 环境控制:测试区湿度>75%时启动除湿机,或延迟测试至环境达标。
· 数据追溯:记录测试电压、漏电流曲线、环境参数,利用MES系统关联生产批次号。
我们会定期更新有关热设计与轻量化的技术与资讯,与您分享,供您参考,感谢您对迈泰的关注。
电池托盘使用绝缘材料主要是为了防止电流泄漏,保护人员安全,同时确保电池系统的正常运行。在选型时,需要考虑材料的绝缘性能、耐热性、化学稳定性和机械强度。这些因素共同决定了绝缘材料在电池托盘中的应用效果,从而影响整个电池系统的安全性和可靠性。
电池托盘电气绝缘安全丨中篇-耐压性能保障
图1 电动汽车电池托盘
1-绝缘材料选型与方案设计
在电池托盘绝缘材料的选型中,重点关注材料的介电性能、环境耐受性和机械性能。以下是电池托盘中常用的 6种绝缘材料及其相关信息:
方案设计时我们一般需综合考虑应用场景、性能要求及成本预算三大关键因素来选择合适的绝缘材料。如:
(1)根据应用场景选择:在像高压、大电流的储能电池系统中,电池托盘侧边若需要高性能绝缘材料,建议采用PI膜贴附方案;若绝缘性能要求不高,绝缘粉喷涂方案可供选择。对于电池托盘底板,若追求低成本绝缘方案,绝缘粉喷涂或绝缘漆涂覆方案较为合适。
(2)根据性能要求选择:当对绝缘性能、耐高温性能、耐化学腐蚀性能等要求较高时,PI膜贴附方案是较好的选择;若这些性能要求相对较低,绝缘粉喷涂或绝缘漆涂覆方案可满足需求。
(3)根据成本预算选择:成本预算有限时,绝缘粉喷涂或绝缘漆涂覆方案更经济;成本预算充足的情况下,可选择PI膜贴附方案。
2-电池托盘选用PI膜技术要求
(1)材料:PI,基膜厚0.1-0.14mm,背胶胶厚0.03mm,PI膜导热系数>0.3W/(m·k);
(2)耐压性:AC 3000V,60S,漏电流≤0.5mA;
(3)(冷贴)180°剥离强度≥15N/24mm;
(4)绝缘性:DC 1500V,60S,绝缘电阻>1000MΩ;
(5)耐温耐电解液绝缘性能:在500℃、700V DC电压,滴加2ml电解液下(测试面积13000mm<H>2<H>),保持1h,无击穿无跳火;
(6)耐温绝缘性能:500±2℃下,持续烘烤(马弗炉)0.5h,样品整体形态变化过程无自燃,且试样两过。表面施加AC 1000V,从0V到3000升压时间10S,继续持续60S,被测样品无击穿、无跳火;
(7)阻燃等级:UL94 V-0;
(8)高温高湿:1000小时85℃和85%湿度试验后,样品无开裂、无变形,满足国标《GBT 13542.6-2006 电气绝缘用薄膜 第6部分:电气绝缘用聚酰亚胺薄膜》中关于绝缘电阻、耐电压值、电气强度要求,拉伸强度、断裂伸长率、剥离强度相比本物料未老化时下降<30%;
(9)冷热冲击:85℃持续一小时切换至-40℃持续一小时,再切换至85℃这样高低温循环。切换时间包含在一小时内,切换时间≤3min。样件在高低温循环1000小时后,样品无开裂、无变形,满足国标《GBT 13542.6-2006 电气绝缘用薄膜 第6部分:电气绝缘用聚酰亚胺薄膜》中关于绝缘电阻、耐电压值、电气强度要求,拉伸强度、断裂伸长率、剥离强度相比本物料未老化时下降<30%。
(10)盐雾试验:GB/T 10125标准中的中性盐雾试验(NSS)测试,温度为35℃、湿度≥85%RH,试验溶液为(5±0.1%)(质量分数)NaCl ,PH=6.5~7.2,连续喷雾72h,盐雾试验后,样品无开裂、无变形,满足国标《GBT 13542.6-2006 电气绝缘用薄膜 第6部分:电气绝缘用聚酰亚胺薄膜》中关于绝缘电阻、耐电压值、电气强度要求,拉伸强度、断裂伸长率、剥离强度相比本物料未老化时下降<30%。
(11)产品符合RoHS。
图2 电池托盘用PI膜
3-绝缘耐压测试方法及常见问题解决方案
(1)绝缘耐压测试方法
绝缘耐压测试是评估电气设备绝缘性能的重要手段,主要包括直流耐压测试和交流耐压测试。直流耐压测试通过施加直流高电压,检测绝缘材料在规定时间内是否击穿,设备包括直流高压发生器、电压表等,步骤为施加电压、保持电压和降低电压。交流耐压测试则施加交流高电压,设备和步骤与直流测试类似。两种方法均需在测试前做好准备工作,确保设备接地良好,并在测试过程中密切观察绝缘材料的表面状况。
(2)常见问题及解决方案
绝缘耐压测试中常见的问题包括绝缘击穿、泄漏电流过大和测试设备故障。绝缘击穿可能由绝缘材料性能不足、内部缺陷或受潮引起,解决方案包括选择优质材料、加强维护和改进绝缘结构。泄漏电流过大可能由绝缘电阻降低、表面污染或测试设备精度不够导致,解决方案包括保持绝缘材料清洁、干燥和校准测试设备。测试设备故障可能由设备老化、维护不当或操作不当引起,解决方案包括定期维护、正确操作和及时维修。
我们会定期更新有关热设计与轻量化的技术与资讯,与您分享,供您参考,感谢您对迈泰的关注。
随着新能源汽车和储能技术的快速发展,电池系统作为核心能量载体,其安全性与可靠性备受关注。电池托盘作为电池模组的承载与防护结构,其电气绝缘性能直接关系到整车的安全运行、电池寿命及用户人身安全。电池托盘的电安全设计是电池系统安全性的基石,通过多层次防护,如:绝缘、结构、热、监测等,在复杂工况下保障电池稳定运行,降低因电气故障引发的火灾、爆炸或触电风险,同时延长电池寿命并提升系统可靠性。
本文围绕电池托盘的电气绝缘安全,系统阐述其设计原则、耐压性能的验证方法,以及典型失效案例的根因分析与改进策略,以期为电池系统的高安全设计提供理论支撑与实践参考。
上篇-设计要点
电池系统的电安全设计的核心在于“预防-控制-应急”三位一体:通过绝缘隔离、可靠连接、热管理等措施预防故障;借助传感器和BMS实现实时控制;利用防火、泄压等设计应对极端情况。各要点需协同作用,确保电池系统在全生命周期内的安全可靠,同时兼顾可维护性与合规性。电池托盘在电池系统中不仅是结构支撑,还承担电气隔离、热管理、防滑、机械保护、接地和模块化设计等多重功能,对保障电池系统的电气安全至关重要。
1-结构支撑确保电气连接可靠性
电池托盘通过固定电池模块、减少机械应力、抗振抗冲击、保持对齐、环境防护和热管理集成等,确保在复杂工况下电气连接的可靠性和安全性。
图1 电池托盘
A.物理支撑与固定,确保电气连接点(如汇流排、线束、接插件)的精确对位,避免因结构变形或位移导致的接触不良;提供刚性框架,固定电池模组和连接件,防止振动或冲击引起的松脱或断裂。
B.环境隔离与防护,通过密封设计(如IP67/IP68)防止水汽、灰尘、盐雾等侵入,避免腐蚀或绝缘失效导致的短路;阻隔外部机械冲击或异物撞击,保护高压连接部件。
C.热管理协同,集成散热结构(如液冷板、导热垫)均衡温度,防止局部过热导致连接点氧化或熔焊;通过隔热设计减少相邻模组间的热干扰,避免温度梯度引发的材料膨胀差异。
D.电磁兼容(EMC)支持,通过金属屏蔽层或导电涂层抑制电磁干扰,保护低压信号线路(如BMS通信线)免受高压回路干扰。
2-隔离防护构建高效隔离环境
电池电气隔离设计重点在于构建一个既能有效隔绝高压电、又能确保系统高效运行的环境,确保电池模块在任何工况下都能被安全地封装,防止电气能量意外释放,从而规避潜在的电气风险。
A.电池托盘结构兼顾承载和隔离防护:
l 优选铝合金材料,如挤压铝合金,以实现轻量化同时保持高刚性和抗冲击性,外框以承受整个电池系统的重量和外部冲击,采用封闭截面型材增强结构强度,内框设计用于支撑电池模组和水冷板等,确保它们的稳定性和散热需求。
l 使用绝缘材料作为衬垫或涂层,确保电池模块与托盘之间有良好的电气隔离,高压线束应有专门的管理路径和绝缘护套,保证与托盘的电气间隙和爬电距离。
l 采用搅拌摩擦焊等先进焊接技术,提高连接强度,同时减少热影响区,避免变形和潜在的裂纹,对于不便焊接的部分,使用螺栓连接或铆接,结合密封胶,确保机械连接的可靠性和电气隔离。
l 设计时考虑模块化,便于电池的更换和维护,同时不影响整体结构的稳定性。
图2 电气间隙与爬电距离示意
B.高低压隔离设计要点:
l 电池系统的正负点位必须与低压供电系统隔离,并且与电池托盘隔离,确保高压电路与低压控制电路之间有足够的电气间隙和爬电距离,以符合安全标准,防止高压泄露至低压系统
l 高低压隔离设计需考虑电磁兼容(EMC),确保隔离措施不会引入干扰,保持系统稳定运行。
l 高阻抗连接,高低系统之间通过高阻抗连接,只允许接到车身接地(电池托盘)以限制电流流动,确保高压系统故障蔓延至低压系统。
l 物理隔离措施,设计电池托盘时,可以将高压和低压组件布置在不同的封闭腔室内,通过物理分隔减少相互影响;在电池模组与托盘之间使用绝缘材料作为衬垫,如高分子塑料或橡胶,以确保物理和电气上的隔离。
l 设计时考虑隔离措施的可维护性,确保在需要时能够安全地进行维修或更换。
C.接触防护设计要点:
l 高压线束管理:高压线束应被妥善包裹在绝缘护套内,并通过固定夹或导线槽进行有序管理,避免裸露,减少直接接触的风险。
l 安全隔板:在电池模组之间和电池模组与托盘壁之间设置绝缘隔板,以防止在电池损坏时电解液泄露导致的间接电击风险。
l 高压部件封装:对高压连接器、继电器等关键部件进行封装处理,确保即使在托盘内部,这些部件也不会因意外而被直接触及。
l 封闭式设计:电池托盘整体设计为封闭结构,使用金属或复合材料外壳,确保内部高压组件不会外露,同时外壳本身也需具备良好的绝缘性能。
l 锁定机制:对于可维护的高压连接点,采用锁定机制,确保在非专业操作时不会轻易打开,减少误触风险。
l 绝缘材料应用:使用绝缘材料作为电池托盘与电池模块之间的隔离层,确保即使在托盘受损的情况下,也能防止人体直接接触带电部分。这些材料包括但不限于高分子塑料、橡胶垫片或涂层。
3-电气标识设计
电池托盘的电气标识不仅能够提升操作的安全性,还能简化维护流程,减少错误操作的风险。
A.明确标识
l 在电池托盘及周边高压组件上清晰标注“高压危险”、“勿接触”等警告标识,确保即使在紧急情况下也能快速识别。
l 使用国际通用的颜色编码,如红色或橙色标识高压区域,蓝色代表直流电,以直观区分不同电气特性。
l 应用标准化的电气安全符号,如IEC 60417中的图形符号,来表示高压、接地、断电点等,确保信息的全球可理解性。
l 包含电池托盘的序列号、生产日期和批次信息,便于追踪和召回管理。
l 选用耐磨损、耐腐蚀的材料和印刷技术,确保标识在电池托盘的整个生命周期内保持清晰可读。
B.警告标识
l 在电池托盘及周边区域明确标识高压危险,提醒维修人员注意电气安全,遵守操作规程。
l 指示安全操作距离,尤其是在高压连接器和裸露导体附近,提醒保持适当距离。
C.操作指引
l 明确标出电池系统和托盘的接地位置,确保正确实施接地措施。
l 标识出安全的测试点和维护接入点,这些点应设计为低电压或非带电状态下的操作点。
l 可以在托盘的非关键区域简要列出基本操作和安全指南,引导正确操作流程。
我们会定期更新有关热设计与轻量化的技术与资讯,与您分享,供您参考,感谢您对迈泰的关注。
目前比较流行的水冷头,基本上采用纯铜微通道型。铜底板直接进行铲齿加工,鳍片与底板一体,减少热阻。底板与盖板之间则采用钎焊或者扩散焊的方式,确保密封的可靠性。
下篇:铲齿工艺加工水冷头主要成本构成
1-铲齿工艺制造水冷头的优势
l 一体化设计:铲齿工艺可以将地板和鳍片进行一体化加工,有利于减少接触热阻,提升热传导性能。此外一体化的底板和鳍片设计还可以提升结构强度。
l 高精度加工:铲齿工艺可以加工出非常精细的齿片结构,齿高、齿厚和齿距可以精确控制,这使得散热鳍片密度更高,散热面积更大,进而更高效散热。同时也能更好的满足不同客户对形状、尺寸等个性化的需求。
l 生产效率高,铲齿工艺可以批量生产,与传统的CNC相比,铲齿工艺可以同时加工多个齿片,大大提高了生产效率。
图1:不同加工工艺的水冷头底座 a-铲齿 b-CNC c-冷锻
2-铲齿工艺水冷头成本构成
l 设计与开发成本:铲齿工艺水冷头的设计复杂度较高,尤其是在散热性能要求较高的情况下,需要进行复杂的工艺设计和优化。
l 材料成本:铲齿工艺中使用的材料主要是铝和铜合金。铝板与铜合金结合的设计方式在散热器制造中较为常见,且性价比较高,因此铝和铜的质量直接影响成本.
l 加工工艺成本:
铲齿工艺成本:铲齿工艺涉及高精度的数控加工设备,如三轴线轨数控机床。这种设备的使用需要较高的投入成本,同时对操作人员的技术要求也较高,这些都会增加生产成本。
焊接工艺成本:在水冷头的制造过程中,焊接工艺也是一个重要的成本因素。真空钎焊和扩散焊是两种常用的焊接方法。钎焊可以同时焊接多个接头、生产效率高,需要钎料,对工艺条件的要求较,质量控制难度大;扩散焊设备一次性投资较大,扩散焊不需要填料,但对工件表面的加工要求高。
表面处理成本:常见的表面处理方式有阳极氧化、镀层处理等。对于铝合金水冷头,阳极氧化处理可以提高表面硬度、耐磨性和耐腐蚀性,同时增加产品的美观度;对于铜质水冷头会进行镀层处理,如镀镍等,以防止铜的氧化和腐蚀,提供产品的使用寿命和可靠性。
l 其他成本:检验检测、包装运输等。
3-成本优化建议
l 优化材料使用:
选择合适的材料:如,铜的导热系数高,单密度大,单价高;铝的质量轻,单价低,导热系数稍差。
材料用量:通过精确计算材料厚度和余量,确保材料的高效利用,减少材料浪费。
图2:材料用量计算示意
l 优化生产流程
简化模具:设计简单的模具,减少模具的复杂度和成本。
减少废品率:通过精确的工艺控制和质量检测,减少废品率。
一次成型:优化工艺路线,减少多次加工工序,提高生产效率。
我们会定期更新有关热设计与轻量化的技术与资讯,与您分享,供您参考,感谢您对迈泰的关注。
水冷头作为液冷散热系统的关键部件,其设计需兼顾换热性能、结构强度、防腐蚀性、防泄漏性以及成本控制等多方面因素。水冷头内部通常设计有复杂的换热槽结构(即流道),其内部流道设计的优劣直接决定了整个系统的换热效率。
中篇:水冷头设计、加工工艺及挑战
1-不同场景对水冷头的设计要求
l 高性能计算:
高性能计算设备(如高性能CPU、GPU等)在运行过程中会产生大量热量,因此需要水冷头具备高效的散热能力。为了应对高热流密度散热需求,水冷头通常采用高密度微流道设计,以增大换热面积,提高散热效率。此外,一些设计将水冷头直接集成到CPU上,省去了涂抹硅脂的步骤,不仅简化了组装过程,还进一步提升了散热性能。可靠性方面,水冷头必须具备出色的密封性能,以防止泄漏,确保长期稳定运行。
l 显卡散热:
显卡是高热量产生区域,因此需要水冷头具备全覆盖设计,以确保显卡上各个发热部件均能得到有效散热。同时,显卡散热对冷却液的流量要求较高,需要水冷头内部结构设计支持高流量通过,以便快速带走热量。
l 数据中心:
在数据中心中,水冷头的结构设计需要满足高效散热、低噪音、高可靠性、适应高功率密度、智能化管理和环境适应性等多方面的要求,以确保数据中心的稳定运行和高效散热。
2-水冷头结构演化趋势
水冷头结构设计的演化趋势体现了技术创新和性能提升的双重追求,主要体现在以下几个方面:
l 散热性能提升:
增大接触面积:一些水冷头设计通过增加与发热元件的接触面积,提高散热性能。如,采用大面积铜底座设计,可以实现良好的接触和热传导。
优化内部结构:对内部水道进行优化,一种思路以优化流体流动为目标,如,由普通Fin片改为转向Fin片风格,呈现长条形流道,促进流动边界层分离,减少边界层厚度,提升热交换效率;另一种思路以增大热容面积为目标,如,从传统的粗水道向微流道设计转变,显著提高了冷却液与底板的接触面积,增强了散热效率。还有些设计中通过导流板将冷却液喷射至微水道底板,提升局部流速和乱流,大幅提高吸热效率。
l 集成化和智能化设计:
一体化设计:通过一体化设计将水泵、散热鳍片、导热底座等部件集成到一起,减少连接点,提高系统稳定性和散热效率。
多功能集成:除了散热性能,现代水冷头还具备温显、监测功能。
模块化设计:通过组合式扣具结构,提高组织的便利性和自由度。
图1:不同Fin厚水冷头底座
l 高性能材料和表面处理:
采用纯铜底座等高性能材料,结合镀镍等表面处理技术,提升导热效率和抗腐蚀性能。
3-加工工艺及挑战
l 材料特性影响加工:
材料硬度与韧性问题:不同材质的散热器,如铜、铝及其合金,硬度和韧性不同,对加工刀具和工艺的要求也不同。硬度较高的材料,刀具磨损加快,需更频繁地更换刀具;韧性好的材料,切削时易产生变形和毛刺。
铜铝复合材料加工复杂:铜铝复合材料铲齿散热片,需先采用连续铸造半熔态压制成型技术制成复合材料,再进行铲齿加工,工艺流程更复杂,对设备和工艺的精度要求更高。
l 尺寸精度要求高
齿高齿厚一致性难保证:对于一些高密齿散热器,其要求每个齿的高度和厚度都高度一致,以确保散热片的性能和均匀性。若齿高齿厚差异过大,会导致热传递不均匀,影响散热效果。加工过程中,需使用高精度设备和自动化控制系统,才能确保每个齿的规格一致。
齿间距控制难度大:散热片上的齿过于密集时,其密度和间距使得加工过程更加复杂,加工设备需具备更高的速度和精度,才能保持齿的均匀性。例如,当齿间距过小,刀具在切削时容易产生干涉,影响加工精度和表面质量。
l 表面质量要求严格
毛刺问题:加工过程中易产生毛刺,这不仅影响散热器的美观度,还可能阻碍空气流动,降低散热效果。毛刺的产生可能由材料切削精度低、加工工具刀具磨损等原因引起,需采取相应的去毛刺工艺来解决。
表面粗糙度:散热器的表面粗糙度影响其散热性能和后续的表面处理效果。过高的表面粗糙度会增加空气流动的阻力,降低散热效率,还需进行额外的表面处理来降低粗糙度,增加了加工成本和时间。
l 加工设备与工艺要求高
设备精度与稳定性:铲齿加工需要高精度的铲齿机,设备的精度直接影响齿的尺寸精度和表面质量。同时,设备需具备良好的稳定性,以保证长时间加工过程中尺寸的一致性。
刀具选择与磨损:合适的刀具对加工质量至关重要。刀具的材质、几何参数等需根据材料特性进行选择。加工过程中,刀具磨损会导致切削力增大、尺寸精度下降和表面粗糙度增加,需及时调整或更换刀具。
进给速度与切削深度:进给速度和切削深度的不合理设置,易导致加工缺陷。如进给速度过快,切削深度过大,会使刀具承受过大负荷,出现抢刀、弹刀、掉刀等现象,影响加工精度和表面质量。
图2:铲齿工艺
l 定制化需求高
不同的应用场景对散热器的尺寸、形状、齿高、齿厚、齿间距等参数有不同的要求,需根据具体需求进行定制化设计和加工。这要求加工厂家具备灵活的工艺调整能力和丰富的经验,以满足多样化的定制需求。
我们会定期更新有关热设计与轻量化的技术与资讯,与您分享,供您参考,感谢您对迈泰的关注。
随着全球人工智能算力的迅猛增长,以及芯片热设计功耗(TDP)的持续攀升,数据中心的冷却需求正面临前所未有的挑战。与此同时,全球范围内节能降碳政策的日益严格,进一步推动了冷却技术的革新。在这一背景下,传统的风冷方案已逐渐难以满足高效散热与节能的双重要求,液冷技术因其卓越的散热性能和显著的节能优势,正迅速崛起,成为数据中心冷却方案的主流选择。服务器作为数据处理和存储的核心设备,其性能与稳定性直接关系到整个系统的运行效率。服务器的核心组件——包括主板、CPU、内存、硬盘和显卡等——在持续高负荷运作下会产生大量热量,若不能及时有效地散热,将严重影响服务器的性能和寿命。为此,先进的液冷系统被引入到服务器散热解决方案中,直接安装在主要热源如CPU和显卡上,以显著提升散热效能。
上篇:水冷块结构及工作原理
液冷系统的核心部件之一是水冷块,它通常由高导热性的铜或铝材料制成,设计有精密的水道和散热片结构。这些水冷块紧密贴合在CPU、GPU等热源表面,通过内部流通的冷却水迅速吸收并转移热量。随后,热量被输送至散热片,通过水冷系统的循环,最终将热量散发到周围空气中。
图1:主流芯片制造商芯片热功耗趋势
1-常见水冷块类型及特点
l 微通道水冷头
特点:微通道水冷头采用精密的微小水道设计,水道结构细密且复杂,能够显著增加冷却液与发热部件的接触面积,从而大幅提升散热效率。微水道设计还能够在冷却液流动过程中产生强烈的湍流效应,进一步增强对流换热系数,实现高效的热量转移。
应用场景:特别适用于高发热量的CPU和GPU,尤其在高性能计算、超频以及数据中心等对散热要求极高的场景中表现卓越。
l 大流量水冷头
特点:大流量水冷头的内部结构相对简单,通常采用铜板或蚀刻凹槽设计,制造成本较低。其核心优势在于依靠高速水流快速带走热量,适合搭配大流量的水冷系统使用。虽然结构简单,但其高效的散热能力使其成为性价比极高的选择。
应用场景:适用于对散热效率有一定要求但预算有限的场景,例如中高端的DIY电脑系统或中小型服务器集群。
l 喷射型水冷头
特点:喷射型水冷头通过导流板将冷却液从狭小的喷嘴高速喷射到微水道底板上,形成强烈的湍流效应,显著提升散热效率。这种设计不仅增加了冷却液与底座的接触面积,还通过高速流动进一步优化了热交换性能。
应用场景:适用于高性能CPU和GPU,尤其在高散热需求和高流量场景中表现突出,例如超频计算、人工智能训练以及图形渲染等领域。
2-水冷块一般结构
水冷块是一个内部留有水道的金属块,通常由铜或铝制成,与CPU、显卡或其他发热不见接触,其结构设计直接决定了散热性能的优劣,典型的水冷块通常由以下几个关键部分构成:
l 底座,通常由高导热材料,如铜或铝合金,表面经过精细加工,以确保与发热部件的紧密接触。底座内部设有复杂的流道设计,以增加冷却液与底座的接触面积。
l 盖板,与底座一起形成流道密封腔,保护水冷块内部的流道、密封等组件,防止灰尘、杂质和外界物理损伤。
l 进出水口,进出水口是冷却液进出水冷头的接口,一般设计在水冷头侧面或顶部,要确保冷却液能够顺利的流入流出,其位置设计需要考虑流体的流动路径,以减少流阻,提高冷却液流动速度。
l 扣具,扣具是将水冷头牢固地固定在CPU或其他发热部件上,确保紧密基础,实现高效热传导。
图2:水冷块典型构造
3-散热性能综合优化
l 流道设计优化
增加流道接触面积:通过设计更窄、更密集的流道,可以显著增加冷却液与底座的接触面积,从而提高对流换热系数。例如,微水道设计通过其细密的水道结构,微通道水冷块的设计参数(如通道宽度、高度、间距)对其散热效率具有决定性影响:随着通道宽度的减小,换热系数显著增加,得益于窄通道内冷却液流动的湍流效应增强,从而提高了热交换效率;较高的通道高度有助于增加冷却液的流动空间,从而提升换热性能;较小的通道间距能够增加冷却液与热源的接触面积,从而提高散热效率。
还可以通过优化流道布局及减少流道弯道进行优化:合理的流道布局能够确保冷却液均匀覆盖发热部件的表面,减少局部温差。而流道中的弯道会增加水头损失和内部流阻,从而降低冷却效率。在设计中应尽量减少弯道数量,若无法避免,则需将弯道设计为圆滑过渡,以降低压降并优化流动性能。
l 高导热材料:水冷块的底座通常采用纯铜或铝合金等高导热材料,这些材料能够高效地将热量从热源传导至冷却液,从而提升整体散热性能。
l 结构参数优化,如:底座基板厚度、Fin片、扰流结构等。基板厚度的增加会导致最高温度上升,因此在设计中需要在散热效果与结构强度之间找到最佳平衡点;通过增加肋片的高度、厚度和间距,可以提升散热性能,但同时也会增加流阻,找到最佳的肋片设计组合,从而实现散热性能的最大化。扰流柱的形状能够有效增强湍流效应并提升热交换效率。
我们会定期更新有关热设计与轻量化的技术与资讯,与您分享,供您参考,感谢您对迈泰的关注。
本文从生产实际出发,总结了搅拌摩擦焊焊接过程中常见的问题、产生原因及改善方法,供大家参考。
1-表面缺陷
(1)表面沟槽
l 问题描述:表面沟槽又称犁沟缺陷,通常出现在焊缝的上表面,偏向于焊缝的前进边,呈沟槽状。
l 产生原因:焊缝周围的热塑性金属流动不充分,焊缝的塑性金属无法充分填充搅拌针行进过程中留下的瞬时空腔。
l 改善方法:增大轴肩直径,增大压力,降低焊接速度。
图1: 沟槽
(2)飞边毛刺
l 问题描述:飞边毛刺出现在焊缝的外边缘,呈波浪形。
l 产生原因:旋转速度和焊接速度的匹配不当,下压量过大。
l 改善方法:优化焊接参数,减少下压量。
图2:飞边毛刺
(3)表面起皮
l 问题描述:表面起皮或起丝呈皮状或丝状出现在焊缝的表面。
l 产生原因:大量的金属摩擦产热积累于焊缝的表层金属,使得表层的局部金属达到熔化状态。
l 改善方法:优化焊接参数,降低转速,提高焊速度。
图3:表面起皮
(4)背部焊瘤
l 问题描述:在焊缝的背面形成焊瘤。
l 产生原因:焊接过程中搅拌头的深度和压力控制不当。
l 改善方法:优化搅拌头的深度和压力设置。
2-内部缺陷
(1)未焊透
l 问题描述:焊缝底部未形成连接或者不完全连接而出现的“裂纹状”缺陷。
l 产生原因:搅拌针长度不足,导致焊缝下部的材料未能充分搅拌。
l 改善方法:选择合适的搅拌针长度,确保焊缝厚度上的材料能够被充分搅拌。
图4:未焊透
(2)孔洞
l 问题描述:焊缝底部未形成连接或者不完全连接而出现的“裂纹状”缺陷。
l 产生原因:焊接过程中,由于摩擦热量输入不够,使达到塑化状态的材料不足,造成不充分的材料流动,导致焊缝区未完全闭合的。
l 改善方法:优化焊接参数,改进搅拌针设计,控制焊接速度和转速。
图5:孔洞
我们会定期更新有关热设计与轻量化的技术与资讯,与您分享,供您参考,感谢您对迈泰的关注。
近段时间,小编注意到多家企业都在关注和布局浸没式液冷储能,浸没液冷技术在沉寂一段时间后再次受到关注,似乎又有“变火”的趋势,相信很多同行也都在关注这一进展。
1-浸没式液冷技术特点
储能电芯走向300+Ah、储能系统纷纷走向5MWh+,电芯越大产热越多、越难散热、越难保证温度一致性,并且储能系统由大量电芯堆叠组成,运行工况复杂多变,更容易造成产热不均、温度分布不均。散热、均温的问题若不能妥善解决,会导致电池的充放电性能、容量和寿命的下降,影响整个系统的性能。此外,安全一直是悬在锂电储能头上的“达摩克利斯之剑”,而提升安全的最普遍做法是向本征安全、主动安全、被动安全三个维度进发。
浸没式液冷是将电芯浸没在在一种绝缘、无毒、可散热的液体中,冷却液具有更高的导热率和比热容,这种直接的接触方式在提供极高的热传递效率的同时,也能够提高更好的均温性。并且,冷却液在作为温度控制的介质外,还可以作为储能系统消防液使用,使得温度控制与消防合二为一,也是浸没式液冷技术的显著特点。浸没式液冷在面对更高散热性能、更强安全性要求的产业背景下,无疑会更具优势。
图1:浸没式液冷储能电池Pack箱
2-浸没式液冷储能系统方案
浸没式液冷技术作为液冷技术一个分支,并非储能行业首创,最初是在高性能计算领域得到应用的,后来逐渐扩展到数据中心、人工智能、加密货币等。
浸没式液冷储能系统的设计初衷是为了解决传统风冷和间接液冷在冷却效率和电池温差控制方面的不足。南方电网梅州宝湖项目正式投运标志着浸没式液冷这一前沿技术在新型储能工程领域的成功应用。
l 冷却方式及冷却液循环方式
冷却方式分为单相和相变两种方式,采用单相浸没液冷,主要包括矿物油、硅油、天然酯等。而另一些方案则采用两相浸没液冷,以氢氟醚为主要代表,利用相变潜热进行散热,提高散热效率。据不完全统计,当前发布的浸没式液冷储能系统中以“单相浸没冷却”的方案居多。
据冷却液的循环方式的差异,在单相浸没液冷又有三条技术路线:自然对流、泵驱动、浸没式耦合冷板式液冷。自然对流利用液体受热后体积膨胀、密度减小的特性,实现热冷却液的上浮和冷却后的下沉,从而完成循环散热;泵驱动系统的核心是液冷机组驱动冷却液在液冷管路及电池浸没箱之间循环流动,完成整个循环散热过程;而浸没式耦合板式液冷的方案中,电池浸没在介电流体中,与介电流体接触的冷板用来带走热量,避免使用复杂的二次回路来冷却介电流体。
l 产品形态与集成方案
浸没式液冷储能系统的集成方案迭代是一个从整体到局部、再到细节的过程,每一步都在前一阶段的基础上进行优化和改进,以实现更高的性能和安全性。
从舱级到Pack级,系统集成技术呈现出场景定制特点。储能场景的多元化使得对储能系统的需求各一,单一产品与无法满足市场需求,模块化设计使得储能产品可以根据项目的规模和电力需求进行优化和扩容,允许根据不同的应用场景和需求快速调整和部署储能解决方案。
3-产业化进程中的挑战及落地场景
浸没式液冷储能系统在商业化过程中面临经济性、技术复杂性、市场接受度、产业链成熟度等多方面的挑战。
l 技术复杂性:相较于冷板式液冷系统,浸没式液冷系统的设计和实施更为复杂。
l 产业链成熟度:浸没式液冷技术的产业链尚未完全成熟,这限制了其在更广泛领域的应用。产业链的成熟度直接影响到技术的推广和商业化进程。
l 经济性挑战:在当前储能行业仍处于商业化发展的初期阶段,盈利性不足使得高成本的技术路线难以受到市场青睐。许多企业在为了一时订单而进行低价竞争,导致浸没式液冷的渗透率受到限制。
当前,储能行业的主要市场仍以风冷和冷板式液冷为主,浸没式液冷尚未完全被市场所接受。尽管浸没式液冷技术的市场渗透率与接受度不高,但在一些特殊的场景下可能展现不出可观的潜力,比如:
l 危化品行业:危化品企业对于储能设备的安全管控极为严格,因为其生产和存储的化学品大多具有高度易燃、易爆、有毒或腐蚀性,一旦发生事故,不仅会对企业自身造成严重损失,还可能引发环境污染和对周边社区造成危害。
l 基站、数据中心:基站、数据中心对热失控容忍度低,数据中心储能系统需保证性能稳定、不易发生热失控的电池,以确保系统的安全性。对电能质量的要求高,需要储能系统具有快速的响应能力,在电网发生故障或停电等紧急情况先,储能系统需能够直接切换至放电模式,以保证电力的连续性和稳定性。
l 快充电站:高倍率充放电时,电池在短时间内产生大量热量,会导致电池温度过高和温度不均,对电池的性能、寿命和安全性构成威胁,就意味着高倍率充放电场景下,电池的热管理变得尤为重要。
我们会定期更新有关热设计与轻量化的技术与资讯,与您分享,供您参考,感谢您对迈泰的关注。
电池包的气密性是电动汽车及储能系统中至关重要的指标,电池包的气密性检测主要针对电池包壳体、接口、连接件、冷却组件等进行检测,以保证电池包内部不受外界环境的灰尘、水气等杂质污染或侵入,冷却组件不发生漏液,确保电池包维持正常的性能和寿命,不发生短路或爆炸等安全事故。
1-电池包的防护等级与气密性检测标准的制定
国际防护等级认证(International Protection Making,IEC60529),也称作异物防护等级或IP代码(IP Code)。IP(Ingress Protection)防护等级系统是有国际电工委员会(IEC)制定的,用于对电气设备外壳对异物侵入和水侵入的防护等级进行分类的标准。电池包箱体的气密等级通常要求达到IP67或IP68,这就意味着电池包箱体需要完全防止灰尘进入(防尘等级6),并且能够在一定压力的水中浸泡一段时间,外壳进水量不致达到有害程度(防水等级7),更严格的要求电池包在1m深的水下浸泡60min而无水进入(防水等级8)。IP防护等级通常由两位数字组成,数字越大,表示防护等级越高,见图1:
图1:IP防护等级说明示意
为了确保电池包IP67、IP68的要求,电池包需要进行沉水测试,此方法耗时较长,对动力电池包具有破坏性,且具有一定的安全风险,并不适合作为动力电池的下线检测。因此使用气密检测来保证电池包满足IP67、IP68的要求成为行业通用做法。气密检测标准的制定需要考虑压降值与泄漏率之间的关系,以及孔径与漏水的关系。气密性检测标准制定时涉及从理论极端到实验验证的一系列步骤,以实现IP等级到气密性检测标准的转换。如,以IP68为例:
图2:气密检测标准制定步骤
2-气密性检测方法选择及检测难点分析
电池包设计和制造质量是影响气密性的关键要素,包括电池箱上盖的韧性和强度、电池包壳体、接口和连接件等部位的密封及防爆透气阀、电气接插件本身的密封性等。此外,使用过程中也会带来一些问题影响气密性,如:热膨胀收缩问题、材料老化及振动冲击影响等。在电池包壳体生产制造中我们更关注焊点和接头质量等问题造成的气密不良,比如焊点不均匀、不牢固或存在裂缝、气隙,接头连接部位密封不良等。
电池包气密性检测主要分为上壳体、下壳体、总装件的气密性测试,上下壳体的气密性测试必须满足总装后的气密性泄漏要求。选择电池包气密性测试方法时,一般会综合考虑电池包的特性、测试精度要求、生产效率以及成本等因素。
工程中电池包壳体测试一般会分为制程气密检测、出货气密检测。并且上下壳体的气密性测试必须满足总装后的气密性泄漏要求,对检测标准提出了更严格的要求。要保证气密性满足要求,实操中必须克服以下困难:
l 产品结构稳定性:焊缝的质量,包括塞块焊缝、水嘴焊缝、横梁焊缝、边框底板焊缝、边框前后封板焊缝等,焊缝漏气问题主要集中在起弧、收弧处及因烧穿导致的不良等;焊接变形应力造成的开裂,如底板腔体侧壁焊接、底板腔体材料分层,无法承受焊接变形应力等。
l 气密工装的适配性与稳定性:工装设计应紧密贴合被测件的外形和尺寸,确保在检测过程中被测件能够稳固的固定在工装上,减少因为位置偏移或晃动导致的测试误差。然而,实际上电池包尺寸和形状差异较大,就需要设计和制造多种不同的测试工装,增加成本和操作复杂性,如果设计一种通用型工装,这又会加大设计复杂度。
l 气密性检测结果的可重复性:气压、温度、测试工件/夹具的干燥状态等因素都会影响气密检测结果。
l 对于工件存在较多不贯穿的微小裂纹,受检测设备精度、检测参数等因素的影响,可能存在泄漏源未能发现,出现漏检现象。
图3:气密检测工装
3-工程中常用的电池包气密检测方案组合
电池包壳体制程气密测试一般会做气密性试验和浸水试验,在气密性试验中,电池箱上盖被密封,只留一个插接件口作为进气口。通过控制气压并观察是否漏气来判断电池包的气密性。而浸水试验则是将整个电池箱体完全浸入水中,通过检查箱体内是否浸水来判断其气密性。
氦气检漏法是一种利用氦气作为示踪气体,通过检测泄漏点的氦气浓度来实现泄漏检测的技术。当氦气进入被检测设备的内部或外部可能存在泄漏的部位时,如果存在漏孔,氦气会迅速通过漏孔进入或逸出系统,并被质谱仪检测到。氦气检漏法的检测效率较高,尤其是在检测微小泄漏方面。
图4:泄露检测方法比较
在实际生产中,通常会结合多种检测方法以提高检测效率和准确性。例如,氦气检漏法适用于高精度和微小泄漏检测,而压差法则具有高精度和快速响应的特点。此外,传统的水检法虽然检测精度低,但是直观且成本低,是定位泄漏点的便捷方式。
我们会定期更新有关热设计与轻量化的技术与资讯,与您分享,供您参考,感谢您对迈泰的关注。
储能液冷Pack的液密潜在失效会涉及多个方面,如:泄漏、腐蚀和沉积、冷凝水等故障模式。
1-流体互联及组成
在储能液冷系统中,流体互连负责在各个组件之间传输冷却液,通过有效的流体互连,确保冷却液在系统中的高效循环,从而带走电池充放电过程中产生的多余热量。
密封性良好的系统可以有效防止冷却液的泄露,泄漏不仅会导致冷却液的损失,需要频繁补充,还会影响系统的散热性能和稳定稳定性,在储能中冷却液泄露还可能会造成电池短路,引发安全问题。
2-流体互连系统液密设计
流体互连系统的液密设计是确保系统在各种操作条件下保持密封性和防止流体泄露的关键环节。
图1:储能液冷系统典型部署
(1)分析系统中可能的泄漏源与风险点:
l 液冷组件的自密封性,如,在液冷流道系统与Pack箱一体设计中,部件通过焊接进行连接,焊接质量缺陷,焊合不良、气孔、裂纹等,都可能导致渗液问题。
l 结构设计不合理,如液冷箱的定位孔或螺纹孔距离流道过近,焊合不良的部位容易成为渗液的通道。
l 连接部位:液冷系统的管道连接、阀门和接头等部位是常见的泄露点,若连接结构设计不合理或制造工艺不精良,接头内部存在微小缺陷,冷却液也可能从这些缺陷处泄漏出来。
l 由于安装不当、材料老化或损伤等原因导致的泄露。
(2)密封结构设计:
l 液冷PACK使用干湿分离式冷板冷却方式,在正常工作情况下,电芯与冷却液无接触,可保障电芯正常工作。储能液冷箱一种方案是通过挤压工艺成型,流道直接集成在冷板上,然后机械加工打通冷却循环路径。在这个过程中,选择合适的焊接工艺是确保密封性的重要步骤。具体详见《储能用下箱体拼焊工艺设计》。
l 液冷管路主要用于连接液冷源与设备之间、设备之间、设备与管路之间的过渡软(硬)管连接。主要连接方式有:
快插连接:储能液冷系统的连接方式之一是采用VDA或CQC快插连。
螺纹连接:连接结构的两端均滑动连接有管道,内螺纹圈与螺纹套的螺纹连接,增加了连接的牢固性。
限位管和螺母连接:管道一端卡接有连接管路,连接管路两侧固定安装有限位管,限位管内部固定安装有橡胶垫圈和凸圈,连接管头表面开设有限位圈槽,限位管顶部转动连接有螺母,通过螺纹与限位管进行转动连接。
密封圈连接:螺纹套的内壁通过强力胶粘附有密封圈,密封圈的内壁与管道的外表面活动连接,以防止使用过程中漏液。
(3)PACK液冷板、舱内接口、舱内管路等,均考虑在常用冷却液、常用温度、流速条件下的长期防腐蚀,可保障长时间工作不出现腐蚀。操作条件对液密性的影响:
l 温度。高温影响,随着温度的升高,液体的粘度通常会降低,这可能导致液体的密封性能下降,从而影响液密性。例如,某些密封材料在高温下可能会发生变形或老化,导致泄漏。低温影响,在低温环境下,液体可能会变得粘稠,增加了流动的难度,但也可能提高密封材料的性能,从而在一定程度上增强液密性。
l 压力。 高压环境,在高压下,液体的密度和粘度可能会增加,从而提高液体的密封性能。然而,过高的压力也可能对密封材料造成损坏,导致泄漏。低压环境,在低压下,液体的密封性能可能相对较弱,特别是如果密封材料本身存在缺陷或老化,更容易发生泄漏。
l 流速。高流速,液体在高速流动时,可能会对密封面产生较大的冲击力,导致密封材料的磨损或变形,从而影响液密性。低流速,在低流速下,液体的密封性能相对较好,但这也可能掩盖一些潜在的密封问题,如微小的材料缺陷。
3-腐蚀与沉积问题
l 堵塞对秘密性的影响:
冷却液中的颗粒物、沉淀物或微生物生长都可能导致管道内部堵塞,影响冷却液的流通性,进而降低冷却效率。
污垢和结垢:冷却液中的矿物质在长时间运行后可能会在管道内壁形成沉积物,即所谓的“水垢”;也可能会因为固体颗粒沉淀、结晶、腐蚀或微生物活动而形成污垢,这些污垢会堵塞管道和冷板,增加流动阻力,降低传热效率。
泡沫问题:液冷系统中可能会产生泡沫,泡沫会附着在冷板表面,导致传热效果下降,并可能增大系统运行中的阻力,对泵造成气穴腐蚀等,损坏设备。
l 涡流对气密性的影响:
当流体在管道或缝隙中流动时,速度变化会导致涡流产生,特别是在流体经过狭窄部分或障碍物时,涡流更容易形成。流体的粘度和密度也会影响涡流的产生。粘性较高的流体更容易形成涡流,而密度较大的流体可能减弱涡流的形成。
泄漏通道:涡流会在接触表面形成旋涡,这些旋涡可能会在缝隙或不规则表面形成微小的泄漏通道,从而导致气体或液体的泄露。
表面磨损:涡流流动会导致接触表面磨损,特别是在高速流动的情况下,这种磨损会进一步降低气密性,因为磨损的表面更容易形成新的泄漏通道。
热效应:涡流流动会产生热量,这可能会导致接触面材料的变形或热膨胀,从而影响气密性,特别是在温度变化较大的系统中。
4-冷凝水问题
在某些条件下,液冷管路可能会形成冷凝水,这可能会导致设备损坏或效率降低。保温失效:如果管道的保温材料破损或老化,会导致热量散失,影响冷却效果。特别是在低温环境下,保温失效会使管道表面结霜或结冰。冻裂:在寒冷环境中,如果没有采取适当的防冻措施,管道内的冷却液可能会冻结,导致管道破裂。
解决方案
l 密封措施:确保液冷管路的进/出水管口完全封堵,防止外界潮湿空气进入电池舱。
l 除湿设备:安装除湿空调或使用除湿功能,维持电池舱内的湿度在合适范围。
l 温度控制:通过安装空调或通风系统,控制储能柜所在环境的温度和湿度,例如将温度保持在20-25摄氏度,相对湿度控制在40%-60%。
l 隔离措施:对空着的电池架进行简易隔绝,防止湿气进入装有电池簇的舱室。
我们会定期更新有关热设计与轻量化的技术与资讯,与您分享,供您参考,感谢您对迈泰的关注。
储能Pack的全密封设计是确保其安全性和长期稳定运行的关键,密封本质上是用一种装置来密闭(密封)一个缝隙或使一处接合不漏流体(气体或液体)的。全密封计设能够有效防止电池单元内的液体和气体泄漏,这对于保证储能系统的安全和稳定运行至关重要。因此,设计时既要考虑气密性也要保证液体介质的密封性。
储能Pack密封设计在实际操作中需要综合考虑材料、工艺、检测设备、环境条件以及制造过程中的多个因素,以确保其密封性能能达到预期标准。本文从Pack箱体气密、液冷循环液密及液冷工质等方面阐述储能Pack密封设计在实际工程的应用实践及注意要点。
上篇:储能Pack箱体气密性设计
密封设计有助于维持储能Pack内部的温度和压力稳定,这对电池的正常工作和性能发挥起到关键作用;并且密封设计可以减少外界环境对电池内部的影响,比如湿气、尘埃和其他污染物等,从而提高系统的可靠性和使用寿命。此外,采用合适的密封材料和结构可以有效提高密封件的耐磨性和抗老化性能,增强整个储能系统的耐久性,减少维护成本。
气密设计的一般思路是通过箱体结构分析,找出可能存在泄漏的重点区域,然后针对不同区域具体性能、功能需求采取针对性的措施。
1-箱体结构分析
箱体不仅是电池模组、电气件等的物理载体,更是整个储能系统安全、可靠运行的重要保障,是储能Pack的“骨架,一般由上盖、下箱体、支撑组件、密封件及螺栓等组成。
图1:储能pack箱体示意图及密封设计重点关注区域(如,红色箭头标注)
如上图,找出潜在泄漏点可能出现区域:
l 多个零件连接处,如:箱体上盖与下箱体装配界面、高低压连接器与箱体安装界面、外露器件与电池箱体安装接口等。
l 如果采用螺栓固定连接,安装固定处亦可能存在泄漏风险,如,电气接口与箱体前面板安装界面。
l 箱体的上盖、下箱体不能出现漏洞、缝隙,确保箱体的密封性和防护性能。
图2:浸没式液冷下箱体(钣金边框+铝型材液冷底板)
2-上盖与下箱体安装界面密封设计
上盖一般可以分为平板式和异型式两种,它们的结构特点也各不相同,比如SMC复合材料、铝制,无论是何种材质,为了减少自密封结构的复杂性,电池壳的上盖通常采用整体式设计。此外,上盖的开孔要求也应符合接口的要求,并且应将其独立于密封界面,以减少对电池包密封的影响。上盖密封设计一般遵循以下原则:
l 采用一体式零件设计,避免分件设计,确保上盖“自密封”性能的稳定。
l 定位孔、定位特征设计在上盖边缘(上盖和下托盘密封界面外侧)。
l 上盖与下箱体密封界面,需要匹配面满足“均匀”、“连续”的密封要求。
目前储能Pack下箱体主流方案有:钣金箱体+液冷板、压铸箱体+液冷板、型材一体式箱体、压铸一体式箱体等,其中型材一体式箱体与其他方案对比,具备流道承重能力好、开模成本较低等优点,应用广泛。焊接工艺的选择对密封性能影响很大,对于不同材料、厚度的焊件,选择合适的焊接方法能有效提升焊缝的质量,以保证系统的整体强度和密封性能。
另外,下箱体密封设计应当遵循如下密封原则:
l 采用封闭截面型材进行框架的搭建,接头处采用自密封的线性连接技术,如CMT焊接技术。
l 铝型材拼接的电池托盘需要设计有连续的一道或多道密封胶体。
l 下箱体集成液冷板的情况下,需要考虑使用胶体密封或采用自密封的线性连接技术,如FSW搅拌摩擦焊技术。
l 上盖与下箱体密封界面,需要匹配面满足“均匀”、“连续”的密封要求,必要时进行机加工对密封界面进行打磨处理。
图3:箱体上盖与下箱体常见密封形式
通常,储能Pack箱上盖下箱体采用折弯翻边加密封垫设计,见图2。利用紧固螺栓使上盖、下箱体与密封垫充分压实耦合,保证Pack箱满足IP67的相关要求。
3-电气、通信接口与下箱体前面板安装界面密封设计
箱体前面板(如图3),在挤出成型的型材上进行机加工开孔,用于安装电气、通信等接口,实现电流传递、通讯交互、安全控制等功能。
图4:电气、通信接口与下箱体前面板安装界面
箱体与电气、通信等接口安装界面气密性遵循以下原则:
l 接口形状设计成流线型以减少气体和液体在接口处的积聚和渗透可能性。
l 精确对位,避免接口在安装时错位导致的缝隙。
l 安装前对接口进行预密封处理,增加防震垫或密封胶,以增强初始密封效果或减少因振动导致的密封失效。
另外,紧固件的选择方面,使用高强度、高扭矩的紧固件,并在安装过程中进行多次紧固,以确保接口的紧密性。如使用碰焊螺母,其特点是能够直接连接与被连接件(箱体前面板)的壁孔进行碰焊,这种结构设计能够显著提高连接部位的气密性。
图5:使用碰焊螺母增加气密性
4-密封件选择
密封件设计和选择至关重要,因为它们直接影响到系统的可靠性和使用寿命。以下是在设计和选择储能液冷系统密封件时应考虑的关键因素:
l 密封材料必须有一定的化学、压力兼容性,同时能够耐受系统工作温度范围,包括高温和低温环境。密封件的材料选择取决于使用环境和使用寿命要求。常见的密封件材料包括橡胶、聚四氟乙烯(PTFE)、尼龙、金属等。
l 泄漏自由度:密封件必须能够适应系统在工作过程中可能出现的微小变形,以确保在各种工况下均保持良好的密封效果。一般密封垫的变形量要大于30%,小于60%,密封界面压力大于30kPa。
我们会定期更新有关热设计与轻量化的技术与资讯,与您分享,供您参考,感谢您对迈泰的关注。
在纯电动汽车中,电池包的重量约占整备质量的30%左右,电池包轻量化,对于提升整车续航里程有着重大意义。因此,对电池包高比能量的研究是新能源汽车目前的主要研究方向之一,也是实现电动汽车轻量化的主要途径,实现动力电池包轻量化可从两个方向开展:提高单体电芯的能量密度,对电池包相关辅件进行优化设计。
多材料轻量化电池包开发旨在通过采用多种轻质材料,降低电池包的重量,提高能量密度和续航里程,同时保证安全性和可靠性。电池Pack各主要部件中,质量最大的是电芯本体,其次为Pack下箱体、上盖、BMS集成部件等。
1-电池包上盖轻量化
电池箱的上盖位于动力电池箱体的上方,不受动力电池箱体侧面的影响,也不会影响整个电池组的质量,其功能主要包括密封、保护等作用。为了提高整车能效,在设计中也会考虑轻量化,采用轻质材料,如铝合金、复合材料(SMC、FRP等),可以显著减轻电池包的重量。
此外,上盖的结构设计还需要考虑制造效率和批量化要求,在结构非常异形的情况下,采用冲压成型或折弯拼焊可能较为困难。上盖的设计还需要考虑到与下箱体、密封结构件等其他部件的连接与配合,确保整个电池箱体的结构稳定性和可靠性。
2-电池包下壳体轻量化
铝合金是电池包壳体制作的理想材料,因其密度低、比强度高、热稳定性好、耐腐蚀性强、导热性好、无磁性、成型容易以及回收价值高等诸多优点。常用的铝合金材料包括6061-T6、6005A-T6和6063-T6等,这些材料具有不同的屈服强度和抗拉强度,可以满足不同的结构需求。
电池包壳体通常由铝合金型材边框和底板构成,采用6系铝合金挤压型材拼焊而成。设计时需要考虑型材断面大小及复杂性、壁厚等因素,以适应不同的结构和功能要求。例如,边框、中间隔板、底板、横梁等部件可能会采用不同的断面设计。
通过合理的结构设计和连接方式,可以有效保证壳体整体强度,降低加工难度,实现壳体减重:
l 薄壁化:通过采用薄壁设计,配合加强筋来满足强度要求,可以有效减轻材料重量。
l 中空化:在结构设计中引入中空部分,以降低材料密度。
l 尺寸优化:优化电池包的尺寸,减少不必要的材料使用。
l 拓扑优化:通过优化电池包内部组件的布局,减少材料占用空间。
l 集成模块化设计:将冷却板、电池包吊耳等部件集成在箱体中,减少单独部件的数量和重量。
3-制造轻量化技术
l 材料成型
目前电池箱材料成型工艺主要有三类:冲压、铝合金压铸和铝合金挤压成型。动力电池箱整体工艺流程包括材料成型及连接工艺,其中材料成型工艺是动力电池箱体的关键工艺。当前上壳体以冲压为主,下壳体主要工艺为挤压成型及铝合金压铸成型两种方式。
l 连接技术
电池箱体连接工艺在新能源汽车制造中至关重要,涉及多种技术和方法,以确保电池箱的结构强度和密封性。
焊接是电池箱体加工中的主要连接工艺,应用广泛。主要包括以下几种方法:
①传统熔焊:如TIG(钨极惰性气体保护焊)和MIG(金属惰性气体保护焊)。TIG焊接速度低,质量高,适用于点固焊和复杂轨迹焊接,常用于边框拼焊和边梁小件焊接。MIG焊接速度高,熔透能力强,适用于边框底板总成内部整圈焊接。
②搅拌摩擦焊:通过摩擦产生热量实现焊接,具有接头质量好、生产效率高等特点。
③冷金属过渡技术:适用于薄板材料,焊接过程无热输入,减少变形。
④激光焊:高精度、高速度,适用于复杂结构焊接。
⑤螺柱焊和凸焊:用于特定部位的快速连接,螺柱焊通过螺柱和螺母实现紧固,凸焊则通过凸点压紧实现连接。
机械连接方式主要解决薄板材料在焊接中的易焊穿和螺纹滑牙问题,包括:
①拉铆螺母:用于箱体边框密封面和内腔底板的连接,具有紧固效率高、使用成本低等优点。适用于薄板与其他部件的螺纹联接。
②钢丝螺套:用于加强铝或其他低强度机体的螺孔,提高螺钉的承载能力和螺纹的受力分布,适用于电池模组安装孔和密封面安装孔。相对于拉铆螺母,钢丝螺套强度更高且易于修复,但一般不适用于薄壁安装。
我们会定期更新有关热设计与轻量化的技术与资讯,与您分享,供您参考,感谢您对迈泰的关注。
要应对大跨度、快迭代、丰富产品线等市场需求,还要保证降本增效保质,对汽车行业而言,通过产品标准化——造车平台化无疑是项不错的策略,通过电池平台化为不同的车型匹配同一个电池包方案,或者匹配由同一种电芯组成且结构相近的电池包方案,这就意味着尽可能的多零件通用化,可以缩短开发周期、节约成本、精简产线与提高生产效率。
一、电池平台化
电池平台化方案有利于产品的统筹规划、成本的降低和产能的优化。根据整车平台的电池平台化策略,需要考虑平台各车型需求的交集与带宽,用尽量少的电池与电池方案兼容尽可能多的车型。在纯电动项目的架构开发中,合理布置集成动力电池包是至关重要的,具体工作要素包括电量与动力性能需求、碰撞安全、布置位置与空间等。
1-空间尺寸边界与电芯标准化
l 电池包可用布置位置
目前主流的动力电池布置位置为地板下方,包含前座椅下方、后座椅下方、中通道位置及脚踏位置。这种布置方式能够最大限度的获得可用面积,并且有助于降低车身重心、提高整车操纵稳定性和优化碰撞传力路径。
图1:电动车发展过中电池包布置位置
l 电池包空间布置形式演化
分体式电池包:采用分体式的电池包空间布局形式,如江淮同悦系列,能量模块由两个电池包组成,一个放在原来油箱位置,一个放在车尾箱存放备胎位置。
此外,工程师们在燃油车原来架构上不断发掘可利用空间,电池包布局出现了“工”字形、“T”字形、“土”字形的形式。
此类设计是在传统燃油车基础上做较小的改动,空间非常有限,能够装载的电池包体积和重量都很受限,因此容量也很难提升,续航里程不高。
一体式电池包:这是一种全新的产品设计思路,整车设计围绕核心零部件——电池包展开,将电池包进行模块化设计,平铺在车辆底盘上,以最大限度获得可用空间。
l 电池包安装点布置
合理布置电池包至关重要,限制要素设计离地间隙、通过性、碰撞安全和电量需求等诸多方面。
图2:电池包尺寸设计约束
整车平台需定义平台内各车型的类别、级别与定位,进而确定了车辆的大小、轴距,整车布置根据整车空间分解出电池包在X、Y、Z方向的尺寸包络,电池需要在整车给定的包络内进行布置,保证整车各系统间不出现干涉,而整备质量指标可分解出电池包的系统质量要求。
在电池尺寸这一指标上,动力电池包的设计绕不开整车空间、整备质量等硬性参考指标,这就意味着电芯的设计存在阈值,受到这个阈值的约束,电芯尺寸就会往某个特定的区间进行集中,如:方形电芯长度范围150-220mm,宽度范围在20-80mm,高度范围在100mm左右徘徊。电芯尺寸规格的变化趋势正是造车平台化与电池标准化相辅相成的结果。
然而,各车企电池平台策略、承载车型及对标准化的理解也有所差别,致使当前所呈现出来的产品方案仍有较大差异。如比亚迪的标准化策略是全面更换刀片电池,刀片电池的尺寸标准锁定为960*13.5(14)*90(102)mm,单体电压3.2/3.3V。
2-续航边界与电池电量方案开发
动力电池为整车行驶提供能量:电池容量、放电深度、能量密度影响可供电量。为满足不同车型的需求,车型的电耗差异成为重要关注项目,车辆的续航里程会受电驱、电池、整备质量、风阻、机械阻力、低压电耗及能量回收等因素的影响。电耗差别大的车型间共用电池方案的可能性弱,就需要针对性的开发个性化的电池电量方案,包括电池尺寸、质量、电量及做功率性能优化,以满足续航性能的要求。
在造车平台纯电续航里程的约束下,电池需求净放电量会受不同车型电耗的影响,需要确认平台各车型的电耗分布,才能进一步将该电耗带宽转化为电池的需求电量分布,进而确定平台所需电池电量方案。
3-动力性能边界
整车的动力性包括不同SOC、不同环境温度下的加速工况、等速工况和保电工况下的动力表现,对应到电池的变量就是电池在不同SOC和温度下的功率-电压特性,电池的功率对应整车动力系统的功率要求,电压对应驱动电机的额定电压需求。
一般对整车平台电池方案评估从常温高电量下的百公里加速时间及其电池指标分解,逐步延伸到全域全工况的电池指标分解。
二、电池箱体开发
1-电池集成与模块化
优化电池模块的设计,提高电池组的集成度和模块化,减少非活性组件,提升电池组的能量密度。
当前流行的电池包集成技术有CTP、CTB、CTC等各种形式,零件的外形、材质和组合形式等都伴随集成技术的进步发生了改变,整体方向是一体化、集成化,通过减少独立零件数量、使用一个大零件替代几个零件,形成尺寸更大、功能更多的组件。
2-电池箱体方案设计
电池箱体是动力电池系统总成的载体,对产品的安全运行和防护起着关键作用,直接影响整车的安全性。电池箱体的结构设计主要包括电池箱上壳体、下壳体等部件的壳体材料选择,制造工艺方案选择等。电池箱体上盖主要起密封作用,受力不大;电池箱体下箱体是整个动力电池系统产品的承载件,电池模组主要布置在下箱体里面,因此电池箱体内部要有嵌槽、挡板等结构措施,使电池模组在车辆行驶的状况下可靠固定,在前后、左右、上下各个方向上均不发生窜动,避免对侧壁和上盖造成冲击,影响电池箱体寿命。
图3:电池下箱体方案,a-蒙皮框架、 b-FSW焊接+围框、c-FSW焊接+围框
l 电池包安装点结构设计与连接固定
电池包安装点通常采用安装梁结构,这种结构前后贯通,前端与前舱纵梁连接,形成有效、连贯的封闭梁结构,并根据电池包重量分布,合理布置安装点。电池包与整车的固定方式包括螺栓固定、机械固定+胶接混合连接、卡扣连接等。
图4:电池包布置与安装断面
动力电池包一般通过多个吊耳结构安装至整车上,吊耳处理要承受动力电池包自身较大的自重外,还要承受汽车行进时带来的路面激励,如石块路和深坑等,此类耐久工况和误用工况对吊耳结构的强度提出更高的要求。
图5:不同吊耳连接方案:a焊接吊耳 b铝挤边框吊耳
l 电池箱体安全与保护结构
机械强度和防护:电池箱体应具备足够的机械强度,以确保其内部电池免受机械撞击和冲击。电池箱体需要能够承受振动、挤压和机械冲击等,以确保在各种条件下电池的安全性。
碰撞保护:电池箱体的设计必须考虑碰撞安全性,特别是针对侧向碰撞和底部碰撞的情况。通常采用铝制或钢制材料,并通过外框架连接到下部托盘,以提供结构刚度并增强碰撞能量吸收能力。此外,还应设计适当的碰撞吸收结构,以防止电池外壳变形和电池单元损坏。
防水防尘和防腐蚀:电池箱体需要具备防水防尘功能,通常采用IP67级别的密封胶垫来保证气密性能。此外,还应考虑防腐蚀措施,如在外部喷涂PVC涂层以增强耐腐蚀性。
防爆和泄压设计:当电池发生爆炸时,应通过平衡防爆阀等装置使能量集中定向泄放,避免进入客户舱。此外,还应采取防爆措施(如部分破坏结构)以防止设备整体破裂。
l 密封设计
电池箱体上盖与下箱体之间密封面的设计对密封性起重要作用,其设计需要配合电池箱体结构和密封圈一起设计。密封面应尽可能保持在同一个平面,避免出现较多的曲面结构。由于上盖和下箱体是通过螺栓连接,所用螺栓数目较多,因此保证孔的同轴度尤其重要,需在合理布置螺栓孔位置的同时,位置尺寸尽量圆整,且在X、Y向呈对称布置。连接螺栓数目的选择需根据密封性高低和拆装工作量大小两方面综合考虑。
图6:上下箱体密封设计方案,1-电池上盖 2-密封垫 3-电池下盖 4-金属导管
l 电气安全和短路保护
连接可靠性:电池箱体内的连接器应具有正确的极性连接,确保电池箱体的过流能力和电气/机械连接的可靠性,包括放松措施等。
电气绝缘耐压设计:模组设计采用双重绝缘防护电芯本身有一层电芯蓝膜及电芯顶帖片可以满足绝缘耐压要求,端/侧板与电芯间、电芯与底部安装面间设置绝缘耐压防护。
l 热管理设计
电池热管理开发贯穿于电池包系统设计开发全周期,包含电池温度控制、冷板、管路系统等的设计。电池热管理系统设计的主要目标是在考虑空间布置、设计成本、轻量化等条件下,通过加热或冷却控制,保证电池系统工作在相对适宜的工作温度,同时减小单体间温差,保证一致性。
我们会定期更新有关热设计与轻量化的技术与资讯,与您分享,供您参考,感谢您对迈泰的关注。
电池包是新能源汽车的核心能量源,为整车提供驱动电能。我们一般会从效率(能量密度)、安全、制造及维修成本等维度评价电池包技术的优劣。
在电池设计中,单个电芯的电压只有3-4V左右,而电动车所需的电压最低都要100V以上,现在的新车甚至有700V/800V的电压,输出功率一般也在200W,所以就需要给电池升压。为了满足电动车的电流和电压需求,就需要将不同的电芯通过串联、并联组合的方式相连。
电池包是将电芯、电子电气系统、热管理系统等通过电池框架结构——底板(托盘)、框架(金属框)、上盖板、螺栓等包络构成的,一直以来,如何将这些部件、系统更高效更安全的“打包”成为一个整体,是整个行业持续不断研究探索的议题。
上篇:电池集成技术创新与发展
动力电池成组技术的由来可以追溯到20世纪50年代,起源于前苏联与欧洲等一些国家。这项技术最初是作为一种工程和制造理念,用于确定零件的物理相似性(通用工艺路线),并建立其有效生产。
成组技术(Group Technology, GT)的核心在于通过识别和发掘生产活动中有关事物的相似性,将相似的问题归类成组,寻求解决这一组问题的相对统一的最优方案,以取得经济效益。在动力电池领域,成组技术主要涉及将电池由单体集成为电池包(Pack)的技术,包括结构、热管理、电连接设计和电池管理系统(BMS)技术。
汽车领域较早的成组技术为MTP(Module To Pack),即先由电芯集成为模组,再由模组集成为Pack。这种技术的特征是模组可拆卸和更换,具有较好的可维护性,但成组效率较低。随着技术的发展,成组技术经历了从MTP到CTP(Cell To Pack)的转变,CTP技术指将电芯直接集成到Pack的技术,取消了传统的模组结构,提升了成组效率和生产效率。近年来,行业还在探索更高集成效率的CTC(Cell To Chassis)、CTB(Cell To Body & Bracket)和MTB(Module To Body)等成组技术。
在动力电池及电化学储能领域,锂电池主要的技术进步来源于结构创新和材料创新,前者是在物理层面对“电芯—模组—电池包”进行结构优化,达到兼顾提高电池包体积能量密度与降低成本的目的;后者是在化学层面对电池材料进行探索,达到兼顾提高单体电池性能与降低成本的目的。本文注重从电池包结构集成视角探讨不同结构集成技术对电池包制造技术的影响及创新发展方向,当前动力电池集成关键技术,见下图:
1-已被淘汰的MTP
在当前这波电动汽车发展潮流的伊始,很多油改电新能源车型上市,它们延续传统油车的空间布局与造型设计,工程师们将一定数量的电芯单体通过串/并联的方式,组成一个相对较大的电芯模组,然后再将几个这样的电芯模组布置到电池包中,也就是我们熟悉的“MTP”电池包,由于电池包需要“打包”两次以上,因此需要的零部件数量十分庞大,电池包也以“里三层外三层”的形象示人,过多冗余部件也占据更多的系统体积空间和重量,使得“MTP”电池包在体积能量密度、质量能量密度表现差;并且因为燃油车设计过程并没有专门为电池预留空间,电池系统只能“见缝插针”地塞进车内,产品力低下,用户体验欠佳。
自以特斯拉为代表的全新智能化电动车平台推出以后,原生纯电动车使得电池包以更高效、规整的安装在理想的空间位置上,三电系统可以更合理的布局,整车的电子电器架构及热管理设计实现更高效的集成,车辆的能效、续航、智能化维度的产品力极大加强。
2-集成技术2.0时代——CTP
MTP结构的电池包存在显著的空间利用率问题,电芯对模组的空间利用率为80%,模组对电池包的空间利用率为50%,整体空间利用率仅为40%,模组硬件费用约占电池电池总成本的14%,这种低空间利用率结构无法满足新能源汽车的发展要求。在电芯→模组→电池包→车身集成思路的框架下,整车想要在有限的底盘空间内尽可能装载更多电量,提高体积利用率,就要考虑每个集成步骤的标准化,随着市场对续航里程需求的不断攀升,单个电池模组的体积不断增大,间接带动了CTP方案的出现。
出于安全、封装复杂程度、降本等方面的考虑,CTP结构技术应运而生。在保证电芯安全的前提下,CTP技术减少了内部线缆和结构件,相比MTP技术,CTP技术没有模组结构,直接由电芯封装成电池包再安装到车上。
目前主要有两种思路,一是将Pack看成是一个完整大模组替代内部多个小模组的结构,以宁德时代为代表;二是设计时即考虑采用无模组方案,以电池本身作为强度的参与件去设计,例如比亚迪刀片电池。
CTP技术的核心点就是取消了模组设计,电芯直接与壳体相结合,减少了端板与隔板的使用,随之而来的问题是电池组的固定以及热管理问题。
实际上CTP电池包的最初产品并非是纯无模组的设计,而是将原有的小模组合并为3个大模组和2个中模组的设计,并且两端同样存在铝制端板,所以理论上依然是MTP,但结构上确有很大的进步。
而到CTP3.0之后,宁德时代给出了更为先进的制造方式,实现了彻底的无模组设计,电芯从原来的沿高度方向立置改为侧置,同时提盒电芯间采用了全新的冷却方案,除却散热外,冷板还承担了支撑、缓冲、隔热、温控等多种功能;底壳也做了限位固定设计。
图1:宁德时代麒麟电池CTP2.0与CTP3.0对比
3-集成技术3.0时代——CTB、CTC
a. CTB技术
CTP技术是电池结构创新的一大进步,却没有突破电池包本身,在CTP技术中,电池包仍然是一个独立的零部件,相较于CTP对电池包的精简策略,CTB技术把车身底板面板与电池包上盖合二为一,电池上盖与门槛及前后横梁形成的平整密封面,通过密封胶密封乘员舱,底部通过安装点与车身组装。在设计制造电池包的时候,把电池系统作为一个整体与车身集成,电池本身的密封及防水要求可以满足,电池与乘员舱的密封相对简单,风险可控。
这样将原来的“电池包上盖-电芯-托盘”的三明治结构转化成“车身底板集成电池包上盖-电芯-托盘”的整车三明治结构,减少了因车身与电池盖连接而产生的空间损失。这种结构模式下,电池包不仅仅是能量源,同时也作为结构体参与整车的受力与传力。
图2:CTB技术结构示意
b. CTC技术
采用CTC方式后,电池包不再是一个独立的总成,而是融合为车身的一部分,优化了产品设计和生产工艺,减少整车零件数量,特别是减少了电池内部结构件与连接件,具备轻量化的先天优势,最大程度提升空间利用率,为增加电池数量、提升续驶里程提供了空间。在电化学体系本身技术不变的条件下,能够通过提升电池数量增加续驶里程。
图3:特斯拉CTC技术结构示意
如,特斯拉等车企先后推出CTC技术车型,在电芯层面可采用多功能弹性夹层结构、大面积水冷技术,叠加一体化开发带来的电池包底部防撞击空间复用技术,兼顾了成组效率、散热性和安全性,从电芯优化和整车结构防护两个维度,推进CTC技术的应用。在整车一体化开发层面,将电芯直接集成到底盘,省去模组和电池包的环节。实现大三电系统(电机、电控、电池)、小三电系统(DC/DC、OBC、PDU)、底盘系统(传动系统、驾驶系统、转向系统、制动系统)以及自动驾驶相关模块的集成,并通过智能化动力域控制器优化动力分配和降低能耗。
4-CTP、CTB和CTC技术对电池盒的具体要求变化
在传统电池包结构中,电池模组起到支撑、固定和保护电芯的作用,而电池盒箱体主要承受外部的挤压力。CTP、CTB和CTC技术的应用对电池盒的提出新的要求,具体体现在:
电池盒箱体强度要求提升:由于CTP或CTB及CTC结构中减少了或取消了模组环节,电池盒箱体不仅要承受外部的挤压力,还需要承担原本由模组承担的来自电芯的膨胀力,因此对电池盒箱体的强度要求更高。
碰撞防护能力:利用CTP技术去除电池组的侧梁后,电池将直接承受碰撞的影响,因此CTP电池组需要具备足够的抗碰撞能力。
保温、绝缘和散热需求:CTP或CTB及CTC结构在底盘承载式结构箱体的基础上,把底板型材更改为水冷板,电池盒箱体不仅要承载电芯重量,还要为电池提供热管理等功能,结构更加紧凑、制造工艺优化、自动化程度较高。
维修性便利性降低:高度集成度设计使得电池包的更换变得复杂,如在CTC结构中,电池内部电芯间充填树脂材料,导致难易更换电芯,几乎不能进行维修。
5-电池包集成度提升对电动汽车充电基础设施的影响
选择不同的电池包集成技术同时隐含选择了不同的补偿方式,CTP倾向于换电,而集成化更高的CTB/CTC则倾向于快充。
高度集成化意味着在相同的空间内可以容纳更多的电池,从而增加了电动汽车的续航里程。用户可能不再需要频繁地进行短距离充电,而是更倾向于在长途旅行中进行快速充电。因此,充电基础设施的规划需要考虑到这些变化,以确保能够满足用户的需求。
由于电池包集成度的提升,电池包的物理尺寸和结构可能发生变化,这可能影响充电接口的设计和充电设备的兼容性。
此外,电池包集成度的提升也可能影响充电速度和效率。更高效的电池管理系统和充电技术可能需要被开发和部署,以确保快速且安全的充电过程。
我们会定期更新有关热设计与轻量化的技术与资讯,与您分享,供您参考,感谢您对迈泰的关注。
新能源汽车用电池托盘和储能液冷箱在生产过程中,必要适当的表面处理是一个关键步骤,如:采用涂装、氧化处理等在金属表面形成保护层,抵御腐蚀介质的侵蚀;对需要电气隔离的组件,如电芯、水冷板、模组壁等需要建立绝缘保护膜,一般通过喷涂绝缘粉末或绝缘漆来实现绝缘;选择合适的表面处理技术不仅能够提升托盘/液冷箱的耐用性和安全性,还能满足不同应用场景的需求。本文对常见表面处理技术进行整理,以供参考。
1-清洁、打磨
在生产过程中,托盘表面可能会积累加工油污、机油残留、粉屑、灰尘等杂质。这些杂质不仅会影响电池托盘的使用寿命,还可能对电池的性能和安全造成不利影响。通过清洁打磨,可以有效去除这些杂质,确保托盘表面的洁净。清洁打磨可以有效去除表面杂质、毛刺、焊渣,使其表面光滑、平整,从而提高电池托盘/箱体的整体质量。
a.化学清洗
碱洗:碱洗主要是利用碱性溶液(如氢氧化钠、碳酸钠等)去除铝合金表面的油脂、污垢和其他有机物。碱洗通过皂化作用、乳化作用和浸透润湿作用来去除油脂,同时生成可溶于水的沉淀物,从而达到清洁的效果。碱洗通常用于去除铝合金表面的油脂、灰尘和有机污染物。
酸洗:酸洗则是利用酸性溶液(如硝酸、盐酸等)去除铝合金表面的氧化皮、锈蚀和其他无机沉积物。酸洗通过酸与金属表面的氧化物反应,将其转化为可溶性盐类,从而去除表面杂质。酸洗主要用于去除铝合金表面的氧化皮膜、锈蚀和无机盐垢。酸洗常用于金属表面的最终处理,以提高其光洁度和平整度。
b.机械打磨
生产中,通过打磨工序可以去除加工余量、修正形状误差,确保托盘/箱体表面的平滑度和精度、满足装配要求,进而提高整体性能和使用寿命。
经过清洁打磨后的表面能增加涂装材料或其他材料的处理,对后续的防腐、密封、导热、绝缘、保温等涂层的施工非常重要,对这些材料牢固的附着在托盘/箱体起到关键作用。
2-涂覆与防护膜建立
除了基础的清洁、打磨外,托盘/箱体生产中通过会采用喷涂工艺进行表面处理用以形成保护层,防止氧化、腐蚀以及满足保温隔热、绝缘耐压等不同场景的需要。
a.保温隔热
电池托盘的防凝露和保温隔热可以通过综合设计隔热保温系统、使用高效保温隔热材料、应用气凝胶、进行电池包保温设计以及喷涂发泡保温材料等路径实现。
底面喷涂PVC、发泡材料
b.绝缘耐压
电池包箱体绝缘、液冷组件绝缘,主要是防止电流泄漏,保护人员免受电击,确保电池系统的正常工作。绝缘的实现通常采用喷粉和覆膜两种方案,主流的覆膜工艺包括:室温贴膜、热压、UV光照等。
内部喷涂绝缘粉、绝缘漆
3-标志、标识
在电池托盘的显著位置设置铭牌或标签,一般通过镭射、机械雕刻等方法实现。这些标识通常采用耐磨损、耐腐蚀的介质进行制作,以保证其在整个使用期内不易磨灭。
我们会定期更新有关热设计与轻量化的技术与资讯,与您分享,供您参考,感谢您对迈泰的关注。
储能变流器作为储能系统的核心设备,是电能转换、能量管理、确保电网稳定性,提高能源使用效率等的重要工具,随着储能变流器功率单元向着高度集成化、高工作频率和大容量的发展,对散热要求越来越高。
1-散热需求变化
a.匹配更大直流舱,变流器容量不断变大,高效散热技术确保设备可靠
伴随储能电芯单体容量愈来愈大,储能系统单机容量也在同步扩大。2023年初,市面上标准20呎单舱电池容量仅为3.35MWh,进入下半年多家电芯企业相继推出310+Ah储能产品,20呎单舱的电容量也扩容至5MWh。然而,5MWh模式更新不到半年,一些头部储能紧接着又发布6MWh、8MWh系统。根据一般经验,储能变流器按负荷容量的1.2倍配置,5MWh储能系统单机容量就必须大于2.5MW,大功率需要更高效的散热技术来确保设备在持续高负载下稳定运行。
储能系统集成拓扑方案迭代演化
b.直流高压技术的应用要求器件具备更高的耐压等级和绝缘强度,功率器件散热严峻
为匹配大容量储能系统,直流高压技术成为一种技术趋势,通过电压等级的提高,实现节能增效和性能提升,1500V电压升级源于光伏,现由光伏切入储能。然而,储能PCS高压演进之路还很长,一些厂商优化开始推向2000V。直流高压技术的应用迫使储能变流器中的电力电子器件需要具备更高的耐压等级、更高的绝缘强度以适应高压工作环境。高压环境下,功率器件的散热设计变得更为重要,功率器件的pn结温度一般不能超过125℃,封装外壳的温度不超过85℃。
c.构网型储能系统需要具备复杂的控制算法、电路设计及高功率密度储能变流器
不同于跟网型储能系统电流源的本质属性,构网型储能系统本质上是电压源,能够内部设定电压参数,输出稳定的电压与频率。因此要求构网型变流器模拟同步发电机的特性,提供电压和频率的支撑,增强电力系统的稳定性,这种控制策略要求变流器具备更高的功率密度和更加复杂的控制算法,并且需要更高性能的功率器件和更复杂的电路设计来实现控制策略。如何有效地管理由于高功率密度、复杂控制策略产生的热量,在保持高性能的同时减少散热系统体积和成本成为热设计的新挑战。
2-常用散热方案比较
储能变流器的散热方案在近年来经历了显著的迭代演化,主要体现在散热技术从传统的风冷向液冷技术的转变。
a.风冷方案
风冷是储能变流器初期采用的温控形式,以空气为介质,通过风扇和散热器来实现热量的散发。风冷方案通过不断降低能耗、优化结构、改进散热材料等途径提升散热效率。在2.5MW功率等级下,风冷仍能满足要求。
b.液冷方案
随着储能系统的功率密度和能量密度不断增加,液冷PCS因为采用了高导热系数的冷却液作为介质,通过水泵驱动冷却液在冷板内循环流动,并且不受海拔和气压等因素的影响,液冷系统拥有比风冷系统更高效的散热效率,液冷方案的匹配度更高,近一两年开始探索,普及。
除全液冷储能方案外,一些厂家推出储能直冷机,采用相变直冷,无水循环。直冷方案也正在进入储能领域。
我们会定期更新有关热设计与轻量化的技术与资讯,与您分享,供您参考,感谢您对迈泰的关注。
电池包是新能源汽车、储能一体柜及集装箱的关键部件,它是通过壳体包络构成能量源,为电动汽车提供动力,为储能柜与集装箱提供消纳能力。本文结合实际工程需要,通过分析电池包机械强度、安全性、热管理及轻量化等多方面要求,对电池包用型材设计要点进行总结说明。
1-电池包壳体设计要求
a.机械强度,耐振动强度和耐冲击强度,在试验后不能有机械损坏、变形及紧固不见松动的现象,锁止机构不应收到损坏。
b.密封性,电池包的密封性直接影响到电池系统的工作安全,通常要求达到IP67防护等级,以确保电池包密封防水。
c.电池包壳体设计需要考虑热管理性能,通过适当的热管理设计,保证电池在适合的范围内工作。
d.安装固定,壳体应留有铭牌和安全标志布置位置,并为采集线、各种传感元件等安装预留足够空间和固定基础。
e.所有无极基本绝缘的连接件、端子、电触头结合后应满足相应的防护等级需求。
f.轻量化,壳体轻量化对于提升电池包能量密度有着重大意义,铝合金质轻质优是当下最可行的选择,结合实际应用通过适当的极限设计提升轻量化水平。
g.耐久性,电池包壳体的设计寿命不得低于整体产品使用寿命,使用周期内不应发生明显的塑性变形,防护等级、绝缘性能不应降低;结构具备维护方便性,包括铭牌与安全标志布置、连接件防护等。
图1典型铝合金拼焊电池包壳体
2-典型铝合金电池包壳体方案
电池包壳体常用的铝合金材料有6061-T6、6005A-T6和6063-T6等,这些材料具有不同的屈服强度和抗拉强度,可以满足不同的结构需求。这几种材料的强度大小:6061-T6>6005A-T6>6063-T6。
当前电池包壳体成型方案有铝型材焊接、铝合金铸造、铸铝加型材铝、冲压铝板焊接等,铝型材拼焊方案因其灵活性和加工方便性成为主流选择,如图1,壳体主要有铝合金型材边框、铝合金型材底板构成,采用6系铝合金挤压型材拼焊而成。铝合金铸造方案因其简化工艺和降本潜力被视为未来发展方向。
3-型材断面设计
a.断面大小及复杂性:型材断面大小用外接圆来衡量,外接圆越大,所需要的挤压力就越大;型材断面通常由多个空腔组成,以提高结构刚度和强度,通常边框、中间隔板、底板、横梁等采用不同的断面设计以适应不同的结构和功能要求。
图2典型铝合金型材断面
b.铝型材壁厚:某一特定铝型材的壁厚最小值与型材外接圆半径、形状及合金成分有关,如,6063铝合金壁厚取为1mm时,6061铝合金就要取为1.5mm左右,同等断面挤压难度:6061-T6>6005A-T6>6063-T6。电池包用型材设计中,边框型材通常选用6061-T6铝合金材料,其典型断面由多个空腔组成,壁厚最薄处约为2mm左右;底板型材也由多个空腔组成,材质一般为6061-T6、6065A-T6,起壁厚最薄处也为2mm左右;另外,在底板承重的托盘及底板液冷集成的设计方案中,一般底板均采用双面结构,底板厚度一般为10mm,壁厚及腔体内壁约为2mm。
c.型材断面尺寸公差:断面尺寸公差应根据铝型材的加工余量、使用条件、型材挤压难易程度、形状的部位来确定,对一些挤压难度大的铝型材可以改变形状或增大工艺余量、尺寸公差,来减小挤压难度,挤压出近似要求的铝型材制品,然后通过或整形或者加工满足使用要求。
此外,进行型材断面设计时需要考虑不同焊接工艺对接头、坡口、壁厚等具体要求。
我们会定期更新有关热设计与轻量化的技术与资讯,与您分享,供您参考,感谢您对迈泰的关注。
电池托盘又称电池盒或PACK箱体等,作为新能源汽车开发中十分重要的部件日益受到重视,电池托盘的设计需要平衡重量、安全、成本、材料性能等因素之间的关系。铝合金由于其密度低、强度高等优点,在保证车身性能时仍能保证其刚性,在汽车轻量化工程中得到广泛应用。
1-电池托盘焊接部位及方法选择
铝制电池托盘以挤压铝型材为基础材料,通过焊接方式将各个部件组合为一个整体,形成完整的框架结构。类似的结构在储能Pack箱中也得到了广泛的应用。
电池托盘的焊接部位通常包括底板拼接、底板与侧边的连接、侧边框的连接、横纵梁、液冷系统组件焊接及支架、吊耳等配件的焊接。在焊接方法选择时,会根据不同的材料和结构要求选择不同的焊接方法,参见下表:
2-焊接热变形影响分析
焊接作为一种局部加热的加工方法,由于热源集中在焊缝处加热,因而造成焊件上温度分布不均匀,最终导致在焊接结构内部产生了焊接变形与焊接应力。焊接热变形就是在焊接过程中由于不均匀的热输入和热输出,导致被焊件的形状和尺寸发生改变的现象。结合实际的工程项目经验,对易产生焊接热变形的部位及影响因素进行了归纳总结:
a.长直线焊接部位
实际生产中,电池托盘底板一般由2~4块铝合金型材采用搅拌摩擦焊拼接而成,焊缝较长,底板与侧板、底板与间隔梁之间连接也有较长的焊缝。长焊缝由于热输入集中,容易导致焊接区域的局部过热,从而产生热变形。
电池托盘边框焊接
b.多部件拼接处
在多部件焊接处由于焊接过程中局部高温加热和随后的冷却导致的。在焊接过程中,焊件受到不均匀的热输入,使得焊缝区域与周围母材之间的温度差异显著,从而引起热膨胀和冷缩效应,引起被焊件变形。储能Pack箱电气安装端通常设有水嘴、线束支架、横梁等,焊缝密集,极易发生变形。
焊缝密集区,托盘前侧翘起变形
c.冷板流道侧壁
液冷板一体化集成设计的电池托盘中,结构刚度较小的部位,如薄板、管道结构等,在焊接过程中不能很好的抵抗热变形,容易发生变形,如:液冷板流道侧壁很薄,一般只有2mm左右,模组安装面焊接横梁、线束支架等零件时,容易造成流道侧壁有裂纹和变形褶皱,影响整体性能。
横梁焊接导致的液冷流道腔壁热裂纹缺陷
3-焊接热变形控制方法
a.分段焊、双面焊
对于强度要求相对较低的部件采取分段焊,将焊接过程分解成多个小段进行,对称布置焊缝,将焊缝对称地布置在构建截面中中和轴附近,以使焊缝产生的变形有可能互相抵消。同时,尽量减少焊缝长度和数量,避免焊缝过度集中或交叉,可以减小焊接温度梯度,从而减少焊接变形。对于底板、底板与侧面框等强度要求高的部位,采取双面焊,增加强度的同时减少因零件较大,焊道较长产生的弯曲变形。
b.优化焊接顺序
控制焊接变形,使用刚性较小的接头形式、避免双向、三向相交的焊缝位置,以及避开高应力区。优化焊接顺序,先焊刚度较弱的区域,最后焊刚度较好的区域,例如先焊角焊缝、再焊短焊缝、后焊长焊缝;先焊横焊缝、后焊纵焊缝。合理的焊接顺序可以有效控制焊接变形,从而控制焊缝外形尺寸。
c.焊接参数调整
控制焊接参数和流程,合理设置焊接速度、焊接层数和每层焊缝的厚度。对较厚的焊缝,采用多层多通道焊接方法,每层焊缝的厚度不大于4mm,多层焊能够减小结构显微组织,提高接头性能。精确控制焊接参数,合理选择焊接电流、电压、焊条型号和焊接速度等参数,可以确保熔池形状和大小一致,从而避免因参数选择不当造成的误差。
d.焊接技能提升
提高焊工操作技术水平(大型构件或要求严格节点采用机械加工),确保焊接过程中动作一致性和规范性,减少人为因素导致的尺寸问题。
我们会定期更新有关热设计与轻量化的技术与资讯,与您分享,供您参考,感谢您对迈泰的关注。
铝合金是工业中应用最广泛的一类有色金属结构材料,尤其在材料导热性能备受关注的场景下,在需要高效热传导的场合,如电子设备散热、电动汽车三电散热、电池储能系统散热以及航空航天领域,通常被用作制造散热器、导热板、电子元件等高效传热设备。
导热率也叫导热系数,是表征材料导热性能的参数指标,它表明单位时间、单位面积、负的温度梯度下的导热量,单位为W/m·K或W/m·℃。铝合金是一种由铝和其他金属组成的合金材料,其导热性能非常优异,导热系数通常在140-200W/(m•K)之间,铝作为地壳中含量最高的金属,因热传导系数较高、密度小、价格低而受到青睐。
1-铝合金材料的导热原理
当材料的相邻区域存在温度差时,热量就会从高温区域经接触部位流向低温区域,产生热传导。金属材料内有着大量的自由电子存在,自由电子可以在金属中快速运动,可以快速实现热量的传递,晶格振动是金属热传递的另一种方式,但相对自由电子传递方式来说处于次要地位。
金属与非金属的热传导方式对比
2-影响铝合金导热性的因素
a.合金化是影响热导率的主要因素之一。合金元素通过固溶原子、析出相和中间相形式存在,这些形式会带来晶体缺陷,如空位、位错和晶格畸变,这些缺陷会增加电子散射的几率,导致自由电子数量减少,从而降低合金的热导性。不同合金元素对Al基体产生晶格畸变程度不同,对热导率的影响也不同。这种差异是由合金元素的化合价、原子体积差异、核外电子排布、凝固反应类型等多因素共同作用的结果。
b.热处理是铝合金加工过程中非常重要的环节,通过改变铝合金微观结构和相变,可以显著影响其热导性。固溶处理是将铝合金加热到一定温度,使其溶质原子充分溶解于基体中,然后快速冷却,以获得均匀的固溶体。这种处理方式可以提高材料的力学性能,但通常会降低其热导率。时效处理是通过在固溶处理后进行适当的冷变形和再加热,可以优化合金的微观组织,提高其综合性能。时效处理兼顾了合金的力学性能和热导率,使合金在保持较高强度的同时,也具有较好的导热性。退火处理通过在较低温度下保温,使合金中的第二相析出并重新分布,从而改善合金的微观组织。退火处理可以提高铝合金的塑性和韧性,但对热导率的影响因具体情况而异。
Al-Cu合金在时效过程中的晶体结构变化示意图
c.其他因素影响,杂质和第二相粒子:铝合金中的杂质和第二相粒子(如氧化物、碳化物等)会散射热载流子(电子和声子),从而降低热导率。杂质含量越高,第二相粒子越粗大,热导率通常越低。铝合金的晶粒尺寸也会影响热导率。一般来说,晶粒尺寸越小,晶界越多,热导率越低。此外,铝合金的加工方式(如轧制、挤压、锻造等)会影响其微观结构和残余应力状态,进而影响热导率。加工硬化和残余应力会降低热导率。
综上,铝合金是高导热材料的理想选择,铝合金中合金元素类型及其存在形式、热处理方式、杂质情况、晶粒大小及成型方式等因素均会影响铝合金材料的热导率,在进行材料成分设计及工艺规划时应该综合考虑。
我们会定期更新有关热设计与轻量化的技术与资讯,与您分享,供您参考,感谢您对迈泰的关注。
随着储能系统向大容量、高能量密度方向演进,储能PACK箱体的尺寸匹配与兼容性设计成为提升系统效率与可靠性的核心课题。本文结合最新工程设计案例、专利技术及行业趋势,从空间利用率、模块化兼容性、电芯排列与支撑设计三个维度展开分析。
1-空间利用率优化
储能系统集成的空间利用率提升,本质是技术迭代与场景需求的双向驱动。通过大容量电芯、模块化架构、液冷集成等技术的协同创新,行业正从“粗放堆叠”迈向“极致空间复用”。
a.大容量电芯应用:能量密度与效率跃升
思路概括:大容量电芯的应用本质是减少电池包内部结构层级,直接提升电芯到电池包的空间利用率。传统电池包采用“电芯→模组→电池包”三级集成模式,模组结构(横梁、纵梁、螺栓等)导致空间利用率低。大容量电芯通过拉长或增大单体体积,可直接跳过模组层级,采用CTP(Cell to Pack)技术将电芯直接集成至电池包。
技术核心:采用600Ah+超大电芯,减少电芯数量与连接点,提升单体容量。
b.空间复用与成本优化:从“组件堆叠”到“多维复用”
思路概括:空间复用与成本优化是一体两面的系统级创新,其底层逻辑在于通过结构简化、功能集成、材料迭代和标准化设计,打破传统储能系统的物理与成本边界。
结构层级的极致简化,空间复用的核心在于减少中间环节。如:高压箱二合一设计:江苏天合储能的专利技术将两个高压箱合并为一个,共享总正/负继电器和电气连接,减少30%的横向空间占用,同时降低15%的电气部件成本。
功能模块的跨域复用,结构件与散热通道一体化,如将液冷板与箱体底板集成,液冷管道与结构支撑共用空间,减少15%的独立散热组件;电芯本体作为结构件:比亚迪刀片电池通过长薄化电芯侧壁提供支撑强度,省去模组框架,空间利用率提升至60%-80%。
电气拓扑的深度优化,如,高压级联拓扑结构通过提高单体电池容量和电压等级(如华为智能组串式储能),减少并联回路数量,使电池堆物理空间缩小20%,系统响应时间缩短50%。;共享式继电器设计,江苏天合储能的二合一高压箱让两条线路共用同一继电器,减少50%的继电器数量和线缆长度,安装效率提升30%
2-电芯排列与支撑设计:承重、散热与抗振平衡
电芯排列的本质是空间利用率、热分布与机械稳定性的博弈,电芯的物理形态和排布方向直接影响空间填充效率:
a.优化电芯排列方式
倒置电芯设计:将电芯防爆阀朝下,使热失控排气与底部防球击空间共用,释放电芯高度空间,体积利用率达。
躺式电芯布局:优化电池包高度方向的空间利用,活性材料占比提升,体积利用率显著高于立式电芯。
超长薄型电芯:通过电芯长薄化设计减少单位体积内的电芯数量,提升成组效率。
b.散热与承重的耦合设计:旨在通过结构、材料、工艺的协同创新,实现高效散热与结构强度的双重优化。
结构设计路径:
集成化结构,如液冷板与支撑梁共形设计:将液冷流道嵌入铝合金支撑梁内部,减少独立组件,空间利用率提升;
分层分舱布局,将电池组、液冷系统、BMS分层堆叠,降低热流与机械应力的相互干扰;
仿生力学优化,如,蜂窝/波纹结构,在铝合金支撑框架中设计蜂窝或波纹芯层(如沐风网专利方案),通过形变吸收振动能量,同时优化散热路径。
材料创新路径:
导热-承重一体化,如,铝合金复合纤维材料(导热≥200 W/m·K,强度+30%);智能材料,相变填充层(PCM)吸热缓释,温差±1.5℃;轻量化阻尼:弹性硅胶垫层吸收振动(阻尼+40%)。
工艺实现路径:
精密成型工艺,如,挤压成型:用于制造复杂流道的铝合金液冷梁;
表面处理技术,如,在铝合金表面生成陶瓷氧化层,提升耐腐蚀性(盐雾测试≥1000h),同时增强散热效率(表面辐射率提高20%);
智能装配工艺,动态预紧力调节,如,集成压力传感器与电动执行器,实时调整螺栓预紧力(5-20kN),避免电芯过压损伤。
c.支撑结构的承重与抗振协同设计:支撑系统需满足静态承重(电芯自重+堆叠压力)与动态抗振(运输/地震冲击)的双重需求。
3-模块化与兼容性:标准化接口与可扩展架构
标准化接口适配多尺寸电芯的本质是通过机械、电气、热管理的协同创新,在统一平台上实现电芯规格的柔性扩展。当前技术已从静态兼容转向动态调节,未来将向智能化、轻量化、跨场景融合方向演进。
a.机械结构协同创新:
机械接口标准化:定义统一的连接装置尺寸。
模块化电池包/柜设计:通过标准化尺寸的电池单元(如280Ah、314Ah电芯)构建可扩展的模组和电池柜,支持不同容量需求的柔性组合。
图1-280Ah 储能PACK箱体
b.电气系统动态调节
标准化通信协议与接口,如,BMS兼容性:制定统一的BMS(电池管理系统)通信协议,支持与不同厂商的PCS、电芯无缝对接;动态功率调节,通过虚拟惯量控制、多时间尺度优化算法,实现有功/无功功率的实时调整;以及自适应电气参数匹配设计。
c.热管理系统的智能化适配
分级热管理方案,如,电芯级采用阻燃高回弹泡棉、导热胶等材料,平衡隔热与散热需求,抑制热扩散;模组级集成液冷板与隔热层的一体化设计,提升循环寿命;系统级通过变频压缩机、多制冷支路动态调节制冷量。
智能化监控与预测,多传感器融合。在电芯极柱、大面等关键位置布置温度传感器,实现高精度温度采集;数字孪生技术通过云端监控和预测性维护,实时优化散热策略。
4-总结
储能Pack箱体空间优化已从单一结构改进转向多维度协同创新:
材料-结构-算法三元融合,如碳纤维箱体+CTP技术+AI排布算法的组合将成为主流。
模块化与标准化加速,以Pack为最小功能单元的标准化设计将推动行业降本增效。
热管理与空间利用深度绑定,浸没式液冷和动态温控技术进一步释放空间潜力。
我们会定期更新有关热设计与轻量化的技术与资讯,与您分享,供您参考,感谢您对迈泰的关注。
随着AI算力爆发式增长和数据中心功率密度持续攀升,传统风冷技术已难以满足散热需求,液冷技术凭借高效散热、节能降耗等优势成为必选项。在液冷技术中,冷板式与浸没式两大路径的竞争尤为激烈。本文将从技术特性、应用场景、成本经济性及未来趋势等角度解析两者的优劣势,并探讨其未来主导方向。
1-技术特性对比:冷板式兼容性强,浸没式散热效率更高
a.冷板式液冷:平滑过渡的“改良派”
兼容性强:无需对服务器结构进行大幅改造,可兼容现有风冷数据中心的基础设施,改造成本低、周期短。
安全性高:冷却液不与电子元件直接接触,泄漏风险较低,且可通过模块化设计(如快换接头、冗余管路)进一步降低风险。
成熟度高:冷板式技术已广泛应用于阿里云千岛湖数据中心、英特尔合作项目等场景,占据当前液冷市场90%的份额。
局限性:冷板式仅能覆盖部分高功耗部件(如CPU、GPU),其余热量仍需依赖风冷辅助散热,PUE值通常在1.1-1.2,略高于浸没式。
b.浸没式液冷:高效散热的“革新派”
浸没式液冷将服务器完全浸没于绝缘冷却液中,通过直接接触实现全器件散热。其核心优势包括:
极致能效:液体导热系数是空气的20-30倍,PUE可低至1.05,散热效率提升3倍以上。
空间节省:冷却系统体积仅为风冷的1/3,单机柜功率密度可达50kW以上,适合AI超算等高密场景。
静音环保:无需风扇,噪音降低90%以上,且无灰尘污染,延长设备寿命。
挑战:浸没式需定制化服务器、冷却液成本占比高达60%(如氟化液),且初期投资较高,生态兼容性待完善。
2-应用场景分化:中短期冷板式主导,长期浸没式潜力释放
a.冷板式:存量改造与新建IDC的“性价比之选”
老旧数据中心改造:冷板式可快速适配现有风冷架构,改造周期短、成本可控。例如,英特尔与比赫合作的模块化方案,通过标准化冷板设计降低部署难度。
中高密度算力场景:冷板式已支持单机柜130-250kW功率(如英伟达B系列GPU),满足多数AI训练需求。
b.浸没式:超算与绿色数据中心的“终极方案”
超高密度算力:下一代芯片(如英伟达Rubin系列)机柜功率将突破1000kW,浸没式成为唯一可行方案。
绿色节能需求:浸没式PUE逼近1.05,余热回收效率达90%(如联想方案),契合“双碳”目标政策。
c.市场格局现状
冷板式主导当前市场:2025年冷板式占液冷市场80%-90%,浸没式不足10%。并且已形成标准化接口(如英特尔的OCP冷板设计),浪潮、中科曙光等厂商方案兼容性强。国内“东数西算”工程要求新建数据中心PUE≤1.25,冷板式成为过渡首选。
浸没式蓄势待发:曙光数创C8000相变浸没方案实现PUE 1.04,阿里云“麒麟”数据中心验证单相浸没可行性。 英伟达B200 GPU(1000W+)等高功耗芯片倒逼浸没式应用,液冷算力密度提升30%-50%。 欧盟计划2028年禁用氟化液,国内碳氢/硅油冷却液研发加速(如中石化“昆仑”系列)。
3-权威观点PK
冷板派:冷板式是液冷普及的‘破冰者’,未来5年仍将承担80%液冷增量市场,浸没式需等待芯片功耗突破临界点。
浸没派:相变浸没是液冷的终极形态,冷板式仅是过渡方案。当单芯片功耗超800W时,浸没式将成为唯一选择。
中立派:技术路线分化反映算力需求分层,冷板服务‘东数’,浸没支撑‘西算’,双轨并行是未来十年主旋律。
4-行业机遇与策略
成本与生态博弈:冷板式短期占优,浸没式需降本破局。
冷板式:优化材料(铜铝复合)、提升加工精度(防泄漏工艺),推动模块化与标准化设计。
浸没式:研发高性价比冷却液(如单相浸没液)、兼容性机柜,联合芯片厂商定制散热方案。
技术储备:探索两相流冷板、智能监控系统(如AI动态调流),应对未来高功率需求。
5-结论
短期(2025-2027):冷板式主导通用场景,浸没式渗透率提升至15%-20%;长期(2030+):相变浸没式在高算力领域成为主流,冷板式退守中低密度市场。
胜负手:冷却液成本、芯片功耗跃升速度、国际环保政策。
我们会定期更新有关热设计与轻量化的技术与资讯,与您分享,供您参考,感谢您对迈泰的关注。
随着新能源汽车与储能产业的快速发展,轻量化、高安全性及高效热管理成为核心诉求。我司深耕铝合金材料加工领域,依托先进的材料选型、成型工艺与焊接技术,专注于电池托盘、液冷板、储能Pack箱及散热器的研发与制造。铝合金因其密度低(约2.7g/cm³)、强度高、耐腐蚀及优异导热性(热导率约150-220 W/m·K),成为新能源装备轻量化与热管理的理想选择。
1-铝合金材料选型及关键考量
不同产品对铝合金的性能需求差异显著,需结合强度、耐蚀性、焊接性及工艺适配性综合选材:
a.电池托盘
常用牌号:6061-T6、6005A-T6、6063-T6。
选型依据:
·需满足抗拉强度≥240 MPa(如6061-T6)以通过国标挤压、跌落及球击测试;
·焊接性要求高,需避免热裂纹(优先选用Mg/Si强化的6xxx系);
·耐腐蚀性通过阳极氧化或包铝工艺提升。
图1-铝合金电池托盘
b.储能Pack箱
常用牌号:5083、6061-T6(兼顾强度与耐蚀性)。
选型依据:
·需承受振动与冲击载荷,屈服强度需≥200 MPa;
·表面处理要求高,避免电化学腐蚀。
c.液冷板
常用牌号:3003、6061/6063、6082。
选型依据:
·高导热性与耐腐蚀性;
·液冷流道需复杂成型,优先挤压性能优的6xxx系。
2-工艺性能差异与加工难点
铝合金的加工需适配其物理特性,尤其在切割、CNC、焊接及表面处理环节:
a.切割与CNC加工
难点:
·高精度孔加工易因材料延展性产生毛刺或变形(如台阶孔边缘突起);
·薄壁结构(如液冷板流道)需控制切削力以防翘曲。
解决方案:
·采用金刚石涂层刀具提升刃口锋利度,减少挤压变形;
·优化加工参数(如高转速、低进给)配合通用CNC设备实现稳定加工。
b.焊接工艺
核心挑战:
·氧化膜(Al₂O₃熔点2050℃)阻碍熔合,易导致气孔与夹渣;
·部分合金热裂纹倾向高,需控制线能量与焊丝成分。
优选工艺:
·TIG焊(交流电源):适用于薄板,通过“阴极清理”破除氧化膜;
·MIG焊(大电流+氦混合气体):厚板焊接效率高,热输入可控。
图2-电池托盘焊接
c.表面处理
·绝缘耐压涂层:应用于电池托盘与Pack箱内部,需通过耐压测试(≥3000V DC/1min),涂层厚度20-50μm,确保高压环境下的绝缘安全性;
·保温除湿涂层:针对储能Pack箱,采用疏水材料(如氟碳树脂)降低内部结露风险,达因值≥34以保证附着力;
·防撞保护涂层:用于电池托盘外壁,选用聚氨酯弹性体(硬度≥80 Shore A),抗冲击性能提升30%以上;
·阳极氧化:常规防腐处理,膜厚误差≤3μm,适配复杂结构。
3-审验性检查与设备适配性
为满足新能源行业标准(如GB/T31467.3、UL2580),需进行多维度验证与工艺适配:
a.审验性检查
·结构强度:通过有限元仿真验证托盘承载、挤压及球击性能(最大应力≤材料屈服强度);
·密封性测试:液冷系统采用氦检漏(泄漏率≤1×10⁻⁶ mbar·L/s)与循环压力测试(0.5-1.5MPa/5000次);
·涂层性能验证:
绝缘涂层耐压测试(5000V DC/60s无击穿);
防撞涂层通过落球冲击(1kg钢球1m高度)与盐雾测试(1000h无剥落)。
b.设备适配性优化
· 通用CNC设备改造:通过高精度夹具设计与动态补偿算法,实现薄壁件加工变形量≤0.1mm;
·焊接参数库:针对不同铝合金牌号建立标准焊接参数(如电流、送丝速度),降低调试周期;
·涂层自动化喷涂:采用多轴机器人喷涂,结合红外固化技术,涂层均匀性误差≤5%。
结语
铝合金在新能源装备中的广泛应用,既是材料科学的胜利,亦是工艺创新的体现。我司将持续探索高强、耐蚀、易加工的新型铝合金,并通过工艺革新推动电池托盘、液冷板等产品的性能升级,助力行业迈向高效、轻量化的未来。
我们会定期更新有关热设计与轻量化的技术与资讯,与您分享,供您参考,感谢您对迈泰的关注。
在电子设备功率密度持续攀升的今天,散热设计已成为影响系统可靠性与寿命的关键环节。作为深耕热管理领域19年的专业制造商,我们结合典型工程案例与多物理场仿真经验,深度解析高功率场景下工程师易忽视的5大技术误区,并提供符合行业实践的解决方案。
误区1:高导热材料滥用,界面热阻计算偏差
典型问题:过度追求导热材料理论值,忽略界面接触热阻的工程实际。
案例解析:某车载激光雷达散热模组采用纯铜基板(导热系数401W/m·K),但未精确控制热界面材料(TIM)的涂覆厚度(设计0.1mm,实际波动±0.05mm),实测接触热阻达0.6°C·cm²/W,导致FPGA结温超标22%。经改用预成型导热垫(公差±0.02mm,热阻<0.03°C·cm²/W)并配合真空烧结工艺,结温降低17°C,MTBF(平均无故障时间)提升至10万小时。
优化方案:
材料选型:根据ASTM D5470标准实测TIM热阻,优先选用相变材料或金属填充弹性体。
工艺控制:采用自动点胶设备(精度±3%),确保厚度公差<10%,避免气隙产生。
误区2:风冷系统气流组织失配,局部热点失控
典型问题:盲目堆叠风扇数量,忽视流道阻抗匹配与边界层分离效应。
工程实例:某数据中心GPU集群采用4台12038风扇(风量200CFM),但因导流罩角度设计不当(90°直角弯折),实际有效风量仅达标称值的65%,局部温差达40°C。经CFD仿真优化,将导流罩改为渐扩式流道(扩散角<7°),并采用交错式鳍片布局(间距梯度从2mm增至3.5mm),整体风阻降低30%,热点温差控制在8°C以内。
核心策略:
流场设计:依据ISO 5801标准进行风洞测试,优化进出口面积比(建议1:1.2)。
动态调控:基于PWM风扇的Q-H曲线,匹配系统阻抗点至最高效率区间(通常为60-80%最大风量)。
误区3:环境防护设计失效,加速材料老化
典型问题:仅关注初始散热性能,忽略湿热/粉尘/盐雾等长期环境应力影响。
案例解析:某海上风电变流器采用6061铝合金散热器(表面阳极氧化处理),在盐雾环境下运行6个月后,氧化层剥落导致接触热阻上升50%,IGBT失效率激增。改用5052铝合金(耐盐雾>1000h)并喷涂聚氨酯三防漆(厚度50μm,符合IEC 60068-2-11标准),3年现场故障率下降75%。
设计要点:
涂层技术:高温场景采用等离子喷涂Al2O3陶瓷涂层(导热系数30W/m·K,耐温>800°C)。
密封结构:IP69K防护等级(双道硅胶密封圈+泄压阀),确保粉尘/水汽零侵入。
误区4:瞬态热负荷建模缺失,相变材料选型不当
典型问题:采用稳态仿真设计散热方案,无法应对毫秒级功率脉冲。
实测数据:某固态功率放大器在5G基站中承受2ms@2000W脉冲负载,传统铝基板方案瞬态温升达55°C,而采用微胶囊相变材料(石蜡/石墨烯复合,相变潜热220J/g)结合瞬态热仿真(ANSYS Icepak瞬态步长1ms),温升控制在18°C,满足MIL-STD-810G冲击测试要求。
动态管理技术:
相变封装:采用蜂窝结构封装相变材料(孔隙率>70%),避免液态泄漏且提升热扩散效率。
模型校准:基于红外热成像(采样率100Hz)修正仿真边界条件,误差<±1.5°C
误区5:TCO评估片面化,忽略隐性运维成本
典型问题:仅对比初期硬件成本,未量化能耗/维护/停机损失。
成本对比:某半导体工厂原采用风冷机柜(初期成本50万元),年电费120万元(PUE=1.8)。升级为两相浸没式液冷后(初期成本180万元),年电费降至45万元(PUE=1.05),且因减少洁净室空调负荷,年综合节支达90万元,2.1年即可收回增量投资(IRR>25%)。
决策模型:
精细化建模:引入蒙特卡洛模拟,量化设备故障率(Weibull分布)对TCO的影响。
政策叠加:结合碳税机制(如欧盟CBAM),液冷系统全生命周期碳排放减少60%,额外获得补贴15%
结语:从经验驱动到数据驱动的热设计范式升级
标准化流程:在概念设计阶段即导入JESD51-14热测试标准,避免后期返工(某光模块项目周期缩短30%)。
多学科协同:通过COMSOL Multiphysics耦合电磁损耗(HFSS提取)与热应变场,某雷达TR组件散热效率提升40%。
智能运维:部署光纤光栅温度传感器(精度±0.1°C)与数字孪生平台,实现故障预测(某超算中心意外停机减少90%)。
通过严谨的工程思维与全链路数据验证,热设计工程师可精准规避“隐形杀手”,为高可靠性系统奠定基础。作为行业实践者,我们致力于提供从材料到系统的闭环解决方案,与客户共同应对热管理挑战。
我们会定期更新有关热设计与轻量化的技术与资讯,与您分享,供您参考,感谢您对迈泰的关注。
1-关键部位的特殊公差要求
在EV电池托盘与储能液冷Pack箱体的制造中,关键连接面与接口的公差控制直接影响密封性、散热效率及装配精度。
a.液冷板安装面
液冷板是电池热管理系统的核心部件,其安装面的平面度直接影响冷却液流道的密封性。若平面度超差,会导致硅胶垫片压缩不均,引发局部泄漏或热阻升高。
b.焊接接缝错边量
电池托盘常采用铝合金焊接结构,焊缝错边会导致应力集中,降低疲劳寿命。尤其对箱体气密性要求高的场景(如IP67),需严控错边。
c.电池模组定位孔
定位孔用于精确固定电池模组,公差过大会导致模组错位,引发电气连接失效或机械振动风险。
d.固定螺栓孔位置度
螺栓孔用于箱体与底盘连接,位置度偏差会导致装配应力,甚至引发螺栓断裂。
e.箱体边缘直线度
箱体边缘直线度影响上下盖装配及IP防护等级,尤其是采用激光焊接的箱体,边缘需作为激光头跟踪基准。
2-尺寸公差对制造效率的影响
尺寸公差对制造效率的影响主要体现在其对加工流程、成本控制及产品质量的平衡上。合理的公差设计既能保证产品功能,又可优化生产节奏。尺寸公差的合理控制对制造效率的影响主要体现在以下几个方面:
a.加工精度与生产成本的平衡
·严格的尺寸公差虽能提升密封性和装配精度,但需采用高精度加工设备和复杂工艺,显著增加设备投入和加工时间。
·过度追求精度可能导致加工成本上升,需在关键功能部位设定严苛公差,非关键区域适当放宽公差以降低成本。
b.返修率与废品率控制
·合理的公差设计可减少因尺寸超差导致的返工。
·焊接变形是电池托盘制造中的主要问题,采用CMT冷焊工艺可优化热输入,减少焊接后变形,缩短返修周期。
c.模组化与标准化生产
·通过标准化组件,公差要求集中于局部可替换部件,降低整体加工难度。
·标准化公差设计还能支持多型号兼容,减少定制化加工需求。
3-平面度控制的行业标准与实际应用
针对新能源汽车电池托盘,行业标准提出严格要求:
a.平面度标准:液冷板安装面平面度需≤0.2mm,底部支撑板平面度≤0.5mm/m²,焊接后框架平面度误差≤0.8mm6。
b.制造工艺优化:采用CNC精铣、CMT冷焊及振动时效处理(VSR),结合激光干涉仪在线检测,降低变形风险。
c.材料选择:推荐使用6061等高强度铝合金,屈服强度≥1180MPa,兼顾轻量化与结构稳定性。
4-材料与工艺驱动的公差调整策略
a.材料创新驱动轻量化
采用轻量化高强铝合金(如6061)及复合材料(碳化硅增强铝基),结合阳极氧化与绝缘涂层,实现减重30%并提升耐腐蚀性,适配液冷系统散热需求。
b.工艺协同提升制造精度
一体挤压成型+搅拌摩擦焊(FSW)减少焊缝数量,CMT冷焊与激光焊接控制热变形。
c.仿真检测闭环保障可靠性
CAE仿真优化加强筋布局,激光扫描与氦检漏技术实现全流程监控,模组化设计兼容±5mm公差,降本增效。
我们会定期更新有关热设计与轻量化的技术与资讯,与您分享,供您参考,感谢您对迈泰的关注。
1-电池托盘/储能Pack箱体铝合金焊接工艺特征
在新能源液冷Pack箱体、电池托盘等产品的制造中,液冷流道与多腔体结构是典型的复杂设计特征(如图1所示)。这类结构往往包含以下特点:
图1:电池托盘典型设计
三维空间交错:流道呈蛇形分布,存在大量空间转折点;
多层级连接:主腔体与子腔体通过薄壁隔板连接(厚度2-3mm);
微型化特征:流道截面尺寸小(铝型材流道壁厚最小1.2mm),焊接可达性差。
2-多焊接技术结合在电池托盘制造中的难点分析
在电池托盘制造实践中,需要采用多焊接技术结合,例如搅拌摩擦焊(FSW)、冷金属过渡焊(CMT)、传统熔化焊(TIG/MIG)等技术的协同应用。这种组合旨在兼顾轻量化、强度、密封性及生产效率,但也面临以下核心难点:
a.多工艺热输入协同难题
不同焊接技术(如FSW、激光焊)热输入差异大,易引发材料性能突变与热变形,需通过优化焊接顺序及参数调节解决。
b.设备兼容性与效率瓶颈
设备切换复杂、参数同步精度要求高,需模块化工作站设计与智能焊机提升协同效率,降低节拍时间。
c.密封强度与成本平衡挑战
多焊缝交汇处泄漏风险高(占缺陷70%),需冗余密封+拓扑优化设计。
3-工程实践:电池托盘、储能液冷PACK箱多焊接工艺协同
a. 焊疤位置规划
· 焊接位置优化:在产品设计阶段,应充分考虑焊接位置的合理性,避免焊疤出现在关键部位或影响产品功能的区域。例如,调整前边框与水嘴的间隙,防止焊疤干涉;优化水嘴焊接位置,减少对产品性能的影响。
· 与产品结构的匹配:焊接位置应与产品结构相匹配,确保焊缝能够承受产品在使用过程中的各种载荷和应力。例如,在液冷板项目中,通过合理规划焊接位置,提高了产品的结构稳定性和可靠性。
· 便于操作和检测:焊接位置应便于操作人员进行焊接操作和后续的质量检测。例如,避免在难以到达或视野不佳的位置进行焊接,以提高焊接效率和质量。
b. 焊疤控制
· 焊疤大小:焊疤大小需严格控制,一般要求焊疤高度在4/6mm范围内,且焊疤不超出平面,以保证产品的外观和装配精度。例如,在液冷板项目中,通过调整焊接参数和工艺,成功控制了焊疤大小,避免了焊疤对产品性能和质量的影响。
· 焊疤形状:焊疤形状应尽量规则,避免出现过度熔化或不完全熔合的情况。通过优化焊接参数和操作技巧,可以有效改善焊疤形状,提高焊缝质量。
· 打磨处理:对于摩擦焊位置产生的下凹焊痕,采用打磨处理方式,确保表面平整,满足产品外观和性能要求。
c. 焊接顺序优化
· 分区焊接:对于大型产品,采用分区焊接的方法,可以有效控制整体变形。通过将产品分成若干区域,依次进行焊接,可以减少焊接过程中的热量集中,降低热变形的风险。
· 逐步校正:在焊接过程中,采用逐步校正的方法,及时调整焊接变形。通过在焊接过程中不断测量和校正产品的变形情况,确保最终产品的尺寸精度和形状符合设计要求。
· 优化焊接路径:合理规划焊接路径,避免在同一个区域反复焊接,减少热量输入。例如,在液冷板项目中,通过优化焊接路径,减少了焊接过程中的热量输入,提高了焊接质量。
d. 变形协同控制
液冷板在焊接过程中出现热变形,导致产品尺寸精度下降。
优化措施:
· 采用分区焊接和逐步校正的方法,控制整体变形。
· 优化焊接参数,降低电流和电压,减少热量输入。
· 使用工装夹具固定产品,减少焊接过程中的移动和变形。
· 采用对称焊接的方法,使焊接热量均匀分布。
我们会定期更新有关热设计与轻量化的技术与资讯,与您分享,供您参考,感谢您对迈泰的关注。
CTC(Cell-to-Chassis)技术因能显著提升电动汽车续航与空间效率而备受关注,但其能否真正取代传统电池技术仍存争议。制造端的核心瓶颈——电池托盘焊接工艺——成为决定这一技术未来的关键:复杂的结构设计、多元材料兼容性、严苛的热管理需求,让传统焊接技术面临巨大考验。本文从一线工程师视角出发,结合行业动态与工程实践,剖析CTC技术的潜力与局限,并探讨焊接工艺如何成为这场技术革命的“试金石”。
1-CTC技术的“理想与现实”
CTC技术通过将电芯直接集成到底盘,理论上可减少冗余结构件、提升能量密度,但其大规模应用的可行性正面临现实拷问:
车企的激进与谨慎:特斯拉、比亚迪等头部企业已推出CTC方案,但更多厂商仍持观望态度。行业数据显示,截止2025年2月全球CTC量产车型占比15-20%,传统CTP(Cell-to-Pack)技术仍是主流。
续航提升的“代价”:CTC虽能提升15%-20%能量密度,但底盘结构复杂度导致制造成本增加30%-50%(某咨询机构测算),成本与收益的平衡尚未明朗。
维修经济性争议:一体化设计使电池维修成本飙升,保险公司数据显示,CTC车型事故后电池总成更换率高达70%,远高于传统车型的25%。
这些矛盾让CTC技术的未来充满变数,市场端能否突破20%取决于三大变量:特斯拉Cybertruck量产爬坡进度;中国车企价格战是否倒逼CTC降本;欧洲法规对电池可维修性的妥协程度。而制造端的焊接工艺水平,将成为决定其能否跨越实验室与量产鸿沟的关键。
2-焊接工艺的三大“生死关”
对于电池托盘制造商而言,CTC技术落地需攻克三个核心难题:
a.“微米级”精度与效率的博弈
传统焊接工艺可容忍0.5mm误差,但CTC托盘因需承载更多电芯,接缝数量增加3倍以上,且多分布于曲面异形部位。某厂商测试表明,当焊接定位误差超过0.15mm时,电芯组装的良品率会从99%骤降至82%。更棘手的是,精度提升往往伴随效率下降——激光焊精度虽高,但设备成本是传统焊接的5倍以上。
b. 材料混搭的“水火不容”
为兼顾轻量化与强度,CTC托盘常采用“铝合金+碳纤维+特种钢”的混合结构。不同材料的热膨胀系数差异可达20倍(如铝23μm/m·K vs. 碳纤维0.8μm/m·K),焊接时易产生内应力导致开裂。某企业尝试铝-碳纤维连接时,焊缝开裂率一度高达18%,远超行业可接受的3%阈值。
c.热影响区的“隐形杀手”
焊接高温可能损伤电芯周边绝缘材料或传感器线路。某车企曾因焊接热输入控制不当,导致电池模组自放电率增加50%。工程师必须在0.1秒内将焊接温度波动控制在±15℃以内——这相当于在焊枪上装一个“高精度温度刹车”。
3-焊接工艺的三大“生死关”
破局之路:没有银弹,唯有系统创新
面对这些挑战,行业正在探索三条突围路径:
a. 工艺组合的“鸡尾酒疗法”
激光电弧复合焊:结合激光焊精度与电弧焊熔深优势,使铝合金焊接速度提升40%;
冷金属过渡技术(CMT):通过精准热输入控制,将热影响区面积缩小60%;
机器人智能补偿系统:基于实时焊缝扫描数据自动调整焊枪路径,将复杂曲面焊接合格率从75%提升至95%。
b. 材料端的“提前妥协”
部分企业开始与材料供应商联合开发“焊接友好型”复合材料。例如,某国产改性铝合金(通过物理、化学或工艺手段调整后的铝合金材料)的焊接裂纹敏感性从7级降至3级(按ISO标准),虽牺牲了5%的轻量化效果,但使焊接良品率提高至98%。
c.检测维度的“数字孪生”
通过焊接过程全数据采集(电流、温度、速度等),结合AI模型预测缺陷概率。某工厂引入该技术后,焊接缺陷的在线检出率从80%提升至97%,报废成本降低45%。
4-工程师的新命题:在不确定中寻找确定性
a.CTC技术的争议本质上是“系统优化”与“局部极限”的博弈:
若焊接工艺突破速度慢于车企降本预期,CTC可能沦为小众技术;
若材料、工艺、检测技术协同突破,则有望开启电动汽车结构设计的新纪元。
b.对于工程师而言,需从两个维度重构能力:
跨领域知识整合:理解电化学性能对焊接热输入的敏感阈值;
敏捷响应能力:某欧洲供应商案例显示,能在一周内完成新合金材料焊接参数优化的团队,订单获取概率提升3倍。
CTC技术站在了“颠覆性创新”与“量产陷阱”的十字路口。它或许不会完全取代现有技术,但正在倒逼焊接工艺向更高精度、更强兼容性、更智能控制的方向进化。这场技术马拉松中,真正的赢家未必是最早出发的车企,而是那些在制造端把“不可能焊缝”变成“标准化接口”的工程师团队。
我们会定期更新有关热设计与轻量化的技术与资讯,与您分享,供您参考,感谢您对迈泰的关注。
随着CTP(Cell to Pack)技术彻底颠覆传统电池包结构,电池托盘的“角色”从被动承载转向主动集成。焊接工艺一跃成为安全与性能的核心命门。轻量化(壁厚仅1.5mm)、零气孔密封、多材料(铝/铜/碳纤维)集成需求,让传统焊接深陷变形与缺陷困局。行业正通过材料革新、智能质检与工艺迭代破局。本文将拆解CTP对焊接的颠覆性挑战,探寻高精度与高可靠性的技术路径。
1-CTP技术对电池托盘结构设计要求的变化分析
CTP(Cell to Pack)技术通过取消传统电池包中的模组结构,直接将电芯集成到电池包中,这一技术革新对电池托盘的结构设计提出了全方位、多维度的升级要求。以下从材料、性能、工艺、集成化等角度展开具体分析:
(1)结构强度与防震性能的全面提升
a.取消模组后的力学承载需求:
CTP技术省去模组结构后,电池托盘需直接承担电芯的支撑、固定及外力缓冲功能。传统模组分散了机械载荷,而CTP托盘需整体吸收充放电过程中电芯的膨胀形变(如方形电芯膨胀力可达10-20kN),同时抵御车辆行驶中的震动、挤压和冲击载荷。
b.材料与结构优化方向
· 高强度铝合金主导:早期钢材因重量大逐渐被替代,6061-T6成为主流,其比强度高、耐腐蚀性强,可满足轻量化与高刚性双重需求。
· 复合结构设计:如零跑汽车的“双骨架环形梁”结构,通过纵横梁隔间增强局部抗冲击性,同时采用挤压工艺优化材料分布,减少冗余重量。
· 镁铝合金与碳纤维探索:镁铝合金比传统铝材减重30%,碳纤维复合材料兼具高强与轻量化特性,但受限于成本与工艺成熟度,目前仅用于高端车型。
(2)气密性与热管理集成要求
a.密封性能升级
取消模组后,电池包内部冷却液循环和气体密封完全依赖托盘,焊接缺陷(如气孔、裂纹)可能导致泄漏风险。
图1-电池托盘气密性检测
b.热管理功能集成
CTP托盘需集成液冷板、导热胶等组件。例如,结构胶用于固定电芯并传递膨胀应力,聚氨酯导热胶(导热系数>1.5 W/m·K)用于电芯间及与液冷管的热传导,单PACK胶黏剂用量较传统结构增加50%以上。托盘内部需设计流道优化冷却效率,同时避免焊接热影响区对密封性的破坏。
(3)轻量化与材料创新
a.材料选择趋势
铝合金挤压与压铸工艺:挤压铝型材用于框架结构(如特斯拉4680电池托盘),压铸工艺(如一体化压铸)简化焊接工序,减重15%-20%。
塑料复合材料应用:例如使用玻纤增强PA6材料,用于非承载部位以进一步减重,但需解决与金属连接界面的兼容性问题。
b.轻量化设计策略
拓扑优化:通过CAE仿真减少冗余材料,在保证强度的前提下降低托盘重量。
薄壁化与集成化:托盘壁厚从3mm降至1.5-2mm,同时集成BMS支架、线束通道等功能部件,减少零件数量。
(4)集成化与模块化设计
a.功能组件的高度集成
CTP托盘需整合电池管理系统(BMS)、高压连接器、防火隔离层等模块。
b.模块化与兼容性设计
焊接产线需要支持多型号托盘混线生产,能够实现“一键换型”,兼容不同电芯尺寸(如方形、圆柱)的托盘结构。
2-CTP技术革新对焊接工艺的具体挑战
CTP(Cell to Pack)技术显著提升了空间利用率和能量密度,但也对焊接工艺提出了前所未有的挑战。
(1)焊接缺陷控制难度激增
a.气孔与密封性挑战
CTP技术取消模组后,电池托盘需直接承担密封功能,焊接气孔(铝合金焊接中常见缺陷)将直接导致冷却液泄漏或气体渗透风险。
b.裂纹与材料兼容性
高锌铝合金(如7系)在焊接时易因热应力产生裂纹。
c.间隙与装配误差
多电芯直接集成导致托盘结构拼接点增加,装配误差累积可能使焊缝间隙超过±1mm。
(2)材料体系升级带来的工艺适配难题
a.轻量化材料的焊接挑战
CTP托盘材料从钢材转向铝合金(6061-T6、7075-T6)、镁铝合金(减重30%)及碳纤维复合材料。铝合金焊接需解决氧化膜难熔、热导率高导致的熔深不足问题。
b.异种材料连接技术
托盘集成液冷板(铜/铝)、防火层(陶瓷基复合材料)等功能组件时,异种材料界面易出现脆性金属间化合物。
(3)结构复杂性与精度要求升级
a.大尺寸薄壁结构变形控制
CTP托盘壁厚从3mm减至1.5-2mm,焊接热变形敏感性激增。
b.高密度焊点与工艺效率
单托盘焊点数量从传统模组的2000个增至5000个以上。
图2-电池托盘焊接
3-生产工艺与质量控制的升级
CTP技术推动电池托盘焊接从“单一工艺”向“多技术协同、智能化、绿色化”转型。制造厂需聚焦三大方向:
技术升级:突破气孔、裂纹等缺陷控制,适配轻量化材料;
智能化跃迁:全流程数字化与AI质检实现高精度生产;
生态协同:联合材料商、设备商、主机厂共建技术标准。
我们会定期更新有关热设计与轻量化的技术与资讯,与您分享,供您参考,感谢您对迈泰的关注。
铝合金等轻质材料因其优异的性能成为主流选择,但薄板焊接中的热输入控制、变形抑制及工艺稳定性等难题对传统焊接技术提出了巨大挑战。冷金属过渡焊(CMT)凭借低热输入、无飞溅过渡及智能化参数控制等优势,为电池托盘制造提供了革新性解决方案。
本文深入探讨CMT技术在电池托盘薄板焊接中的精准控制策略,分析其适配性、工艺难点及复合应用场景,以期为高效、高质生产提供理论支持与实践参考。
图1 104S储能电池液冷下箱体CMT焊接
1-电池托盘焊接的工艺要求与CMT适配性
CMT技术通过低热输入、无飞溅过渡和智能化参数控制,完美适配电池托盘焊接的高精度、低变形与高效率需求。
(1)电池托盘焊接的核心工艺要求
a.材料适配性与轻量化需求
电池托盘多采用轻质铝合金(如6xxx系列、6061等),部分高端车型探索碳纤维复合材料,需满足高强度(抗拉强度达母材60%-70%)与低密度(铝合金密度2.7g/cm³)要求。
异种材料连接需求:例如钢铝混合结构,需克服热膨胀系数差异导致的变形。
b.焊接质量与性能指标
低热输入与变形控制:薄板(0.3-3mm)焊接需确保变形量≤2mm,尤其长直线焊缝需分段焊或反变形设计。
密封性与强度:焊缝需完全密封以防止电解液泄漏,并通过剪切试验(如T/CWAN 0027-2022标准要求)。
气孔率控制:铝合金焊接易产生气孔,需将气孔率控制在0.5%以下。
c.生产效率与自动化要求
批量生产需实现焊接速度≥7mm/s,单托盘焊接时间缩短至5-10分钟。
自动化工作站需兼容双工位设计(装配与焊接同步)和多机器人协同作业。
(2)CMT技术适配电池托盘焊接的关键优势
a.低热输入的精准控制
CMT通过熔滴短路时焊丝回抽切断电流,热输入量比传统MIG焊减少33%,尤其适用于0.3mm超薄板焊接(无烧穿风险)。
冷热交替循环(电弧加热-熔滴过渡-焊丝回抽)减少热积累,焊接变形量可控制在1.5mm以内(比亚迪、北汽案例)。
b.工艺稳定性与质量提升
无飞溅焊接:CMT的机械回抽机制消除熔滴爆断飞溅,减少返工率。
气孔控制优化:采用Ar+30%He混合保护气体,气孔数量比纯Ar减少50%,气孔尺寸缩小至≤0.3mm。
间隙容忍度高:可适应1.5mm装配间隙,降低夹具精度要求。
c.自动化集成与效率提升
双工位工作站(如泰翔科技设计)实现焊接与装配并行,效率提升2倍。
机器人对称焊接(两台机器人同步作业)配合反变形设计,缩短节拍至10分钟内。
2-电池托盘CMT工艺难点分析
图2 CMT焊接工艺过程
(1)材料特性与焊接缺陷控制
a.铝合金焊接的气孔敏感性
铝合金电池托盘(如6061、6063等)在CMT焊接中易因熔池快速凝固、氢溶解度变化等因素形成气孔。保护气体成分对气孔抑制至关重要:纯Ar保护时,气孔率较高(约5%);采用Ar+30%He混合气体可加速气体逸出,气孔率降至0.5%以下。电感修正参数(如负向调节)可优化熔池流动,减少气孔尺寸。
b.热裂纹倾向与成分偏析
铝合金中Mg、Si等元素的偏析易导致焊缝晶界脆化。CMT工艺的低热输入虽能减少热影响区,但需精确控制焊接速度与送丝量,避免熔深不足或局部过热引发裂纹。
c.异种材料焊接的冶金兼容性
若托盘涉及铝-钢或铝-复合材料连接(如防撞梁与箱体),需克服界面脆性相(如FeAl₃)和Zn蒸气干扰。
(2)工艺参数优化挑战
a.熔深与热输入的平衡
电池托盘需满足T/CWAN 0027标准对焊缝熔深(≥0.8mm)的要求。CMT工艺的低热输入特性可能导致熔深不足,需通过调整弧长,利用脉冲电流提升熔池穿透力。
b.焊接速度与稳定性的权衡
自动化产线要求焊接速度≥1.2m/min,但高速下易出现电弧不稳定或熔滴过渡不均。
c.复杂焊缝的搭桥能力
托盘结构常含大间隙(0.5-1.5mm)或异形焊缝(如T型接头)。
(3)结构设计与制造工艺适配性
a.薄板焊接变形控制
铝合金托盘壁厚通常为2-3mm,传统MAG焊变形量可达1.2mm,而CMT焊接通过低热输入可将变形量降至0.3mm以下。但需配合反变形工装设计和机器人对称焊接(双工位工作站)以进一步提升精度。
b.长焊缝的连续性与密封性
电池托盘密封焊缝长度可达数米,需避免断弧或熔池波动。CMT技术通过每秒70次以上的电弧重燃周期,确保焊缝均匀性,配合激光跟踪系统可将气密合格率提升至99%。
c.多工艺复合应用的协同性
高端托盘常采用CMT+FSW(搅拌摩擦焊)复合工艺:CMT用于复杂结构(如边框与底板连接)。FSW用于高载荷区域(如纵梁)以提升强度。需解决两种工艺的衔接参数(如预热温度、焊后热处理)匹配问题。
3-CMT工艺在电池托盘制造中的典型应用场景
(1)电池托盘主体结构的连接
a.边框与底板焊接
CMT工艺广泛应用于铝合金电池托盘的边框与底板连接,尤其适用于 长焊缝、薄板(2-3mm厚度) 场景。
b.横梁与底板连接
在CTP电池托盘设计中,由于横梁数量减少且结构复杂,CMT工艺被用于:高精度定位焊接:横梁与底板的局部连接(如T型接头)需避免熔深不足,CMT通过电弧长度数字化控制(如福尼斯CMT Advanced技术)实现稳定熔深≥0.8mm。多材料适配:若横梁采用铝镁合金(如6061)而底板为高强度铝材,CMT可通过Ar+He混合气体保护减少气孔,同时适应不同材料的导热差异。
(2)薄板与复杂几何结构的焊接
a.薄壁铝合金焊接(2-3mm)
电池托盘的轻量化需求推动薄板应用,但传统MIG焊易导致变形。CMT工艺的优势在于:
b.超薄板焊接:泰翔自动化通过CMT技术实现0.3mm超薄板的无飞溅焊接,用于电池托盘边缘密封结构。
c.异形焊缝搭桥:针对托盘内部加强筋、防撞梁等异形结构,CMT Gap Bridging模式通过焊丝回抽与电弧重定向,可填补0.5-1.5mm间隙,避免未熔合缺陷。
d.密封性要求高的焊缝:电池托盘的密封性直接关系电池安全,CMT工艺通过以下方式保障:
· 连续长焊缝:采用每秒70次以上的电弧重燃周期(如伏能士LaserHybrid技术),确保数米长焊缝的连续性,气密合格率达99%。
· 低热输入控制:相比激光焊,CMT热输入更低,减少熔池波动对密封胶层的热影响,适配涂胶工艺。
(3)多工艺复合制造场景
a.CMT+FSW复合工艺
在高端电池托盘生产线中,CMT常与搅拌摩擦焊(FSW)协同:
分工协作:CMT用于复杂结构(如边框、异形接头)的灵活焊接,FSW用于高载荷区域(如纵梁)以提升强度。例如上海伟晟的自动化生产线通过CMT+FSW+CNC组合,将托盘生产效率提升30%。
工艺衔接优化:华数锦明的生产线采用模块化设计,通过预热参数匹配(如CMT焊后局部加热至150℃)实现与FSW的无缝衔接。
b.与FDS/SPR铆接技术结合
第二代CTP技术中,CMT与摩擦自拧紧(FDS)、自冲铆接(SPR)技术协同:混合连接方案:例如框架与底板的承重区域采用FSW,而可拆卸部件(如水冷板、隔热层)通过CMT焊接预定位,再以FDS铆接固定,兼顾强度与维护便利性。
我们会定期更新有关热设计与轻量化的技术与资讯,与您分享,供您参考,感谢您对迈泰的关注。
新能源汽车及储能的爆发式增长,将电池托盘焊接技术推向了制造工艺的核心战场。面对铝合金轻量化与复杂结构的双重挑战,本文从工艺本质到工程实践,深入解析电池托盘焊接技术,对比传统熔化焊、搅拌摩擦焊与激光焊的工艺原理、性能指标及适用场景。通过热影响区、接头强度、耐腐蚀性等多维度分析,为您呈现焊接技术的优劣势。
1-技术原理对比
a.传统熔化焊
原理:通过电弧、等离子弧等热源将焊接接头局部加热至熔化状态,形成熔池,冷却后凝固形成焊缝。需使用保护气体(如CO₂、氩气)或焊渣防止氧化,可能添加焊丝或焊条作为填充材料。
特点:熔池温度高、冷却快,易形成粗大柱状晶;热影响区(HAZ)宽,冶金过程不充分,易产生气孔、裂纹等缺陷。
b.搅拌摩擦焊(FSW)
原理:利用高速旋转的搅拌头与工件摩擦产热,使材料达到热塑性状态,通过机械搅拌和塑性流动实现固相连接。无熔池形成,无需填充材料。
特点:焊接温度低于材料熔点80%,动态再结晶形成细小晶粒,焊缝致密无气孔,热输入低,变形小。
c.激光焊
原理:高能量密度激光束聚焦于工件表面,通过热传导(功率密度<10⁵ W/cm²)或深熔焊(功率密度≥10⁵ W/cm²,形成匙孔效应)实现材料熔化和连接。
特点:热影响区极窄,熔深大,焊接速度快,可实现精密焊接;但对材料表面反射率敏感,需严格控制工艺参数。
a-传统熔化焊 b-搅拌摩擦焊 c-激光焊
图1 电池托盘常用焊接技术原理
2-性能指标
a.热影响(HAZ)区对比
关键分析:
传统熔化焊:高热量输入导致HAZ宽,晶粒粗化和冶金缺陷(如气孔)显著降低材料性能。
FSW:固态连接避免熔池,HAZ分为TMAZ和HAZ,晶粒细化(NZ)与局部变形(TMAZ)共存。
激光焊:极窄HAZ(约0.1-0.5 mm)得益于高能量密度和快速冷却,但需注意匙孔效应对组织均匀性的影响。
b.接头强度对比
关键分析:
传统熔化焊:快速凝固导致粗晶和缺陷,接头强度显著降低。例如MIG焊铝合金的抗拉强度仅为母材的72.8%。
FSW:动态再结晶形成细晶(NZ),但TMAZ晶粒变形和HAZ强化相溶解可能成为薄弱区。
激光焊:高冷却速率抑制晶粒粗化,焊缝强度接近母材。
c.耐腐蚀性对比
关键分析:
传统熔化焊:粗晶和缺陷导致腐蚀优先发生在HAZ和熔合线。
FSW:NZ因细晶和均质化耐蚀性优,但HAZ晶粒粗化和第二相析出(如含Fe相)可能成为腐蚀敏感区。
激光焊:窄HAZ和均匀组织减少腐蚀活性点,但需注意表面氧化层对耐蚀性的影响。
3-适用场景
a.传统熔化焊
· 适用部位:
框架与底板连接:用于电池托盘主体结构的框架与底板焊接,例如比亚迪、北汽等车型采用间断焊或满焊工艺连接铝型材框架与底板。
边梁及小件补焊:因结构复杂或空间限制,部分边梁、加强筋等小件需配合其他工艺(如FSW)进行补焊。
· 适用焊件:
厚板焊接(如钢制托盘或铝合金厚板)。
非密封性要求的辅助结构(如电池包边角固定件)。
· 适用材料:
铝合金:6系列铝合金(如6061-T6)的厚板焊接,但接头强度较低(母材的70%-80%)。
钢材:钢制电池托盘的框架焊接,成本低但重量较大。
· 局限性:
热输入大导致变形显著,不适用于高精度或薄板焊接。
b.搅拌摩擦焊(FSW)
· 适用部位:
底板拼接:铝合金托盘的底板长焊缝拼接,如水冷通道一体化结构(广东迈泰技术案例)。
密封性要求高的区域:电池托盘与箱体连接处,因FSW焊缝致密无气孔,保障密封性(如吉利、小鹏车型的双面FSW结构)。
复杂型材连接:铝挤压型材的T型接头、中空型材焊接(双轴肩FSW技术可自支撑焊接)。
· 适用焊件:
铝合金挤压型材(如底板厚度10mm、壁厚2mm的双层截面设计)。
异种材料焊接(铝/铜、铝/镁等),但需特殊工艺优化。
· 适用材料:
铝合金:主流材料为6系列(6061-T6、6005A-T6、6063-T6),接头强度达母材80%-90%。
镁合金:轻量化托盘(如瑞松科技案例),但需控制热输入防止晶粒粗化。
· 技术优势:
固相连接避免熔焊缺陷,适用于轻量化、高密封性场景。
c.激光焊
· 适用部位:
高强钢托盘关键焊缝:如电池托盘与车身连接的高应力区域。
精密密封钉焊接:电池托盘盖板密封钉焊接,速度可达40 mm/s,热影响区极窄。
薄板拼接:铝或钢制托盘的薄板(<3mm)高效拼接,减少变形。
· 适用焊件:
高精度、自动化产线的焊接(如机器人激光焊接系统)。
异形结构(如曲面焊缝),需搭配高动态定位系统。
· 适用材料:
高强钢:抗拉强度≥1000MPa的钢材,激光焊可保留母材95%强度。
铝合金:需表面预处理(如阳极氧化或镀层)降低反射率,成本较高。
· 局限性:
厚板焊接需多道次(如>8mm铝合金),效率低于FSW。
我们会定期更新有关热设计与轻量化的技术与资讯,与您分享,供您参考,感谢您对迈泰的关注。
作为电池托盘制造厂的一线工程师,参与过多个新能源汽车电池壳体项目,深刻体会到行业在“轻量化-安全-成本”三角关系中的博弈。本文将从材料路线、制造工艺及未来趋势三个维度,结合实际案例,解析当前技术路线的选择逻辑与产业化挑战。
1-材料路线:轻量化与成本的权衡
电池壳体材料的选择直接影响整车性能与经济性,目前主流路线可归纳为铝合金、高强钢及复合材料三大类,各有适用场景。
a. 铝合金路线:轻量化的主力军
· 挤压铝型材:BYD的多款车型电池壳体均采用挤压铝型材制造,通过优化截面形状实现减重,同时提升结构刚度。
· 压铸一体化:特斯拉4680电池与CTC技术结合,减重超50%,但模具成本超2亿元,需年产50万件以上摊薄成本,适合头部车企规模化生产。
· 复合铝材:保时捷Taycan采用铝-碳纤维混合结构,进一步减重15%,但成本增加30%,仅限高端车型。
b. 高强钢路线:成本敏感市场的逆袭
热成型钢(如22MnB5)屈服强度达1500MPa,商用车渗透率超40%,单GWh成本比铝低40%,但能量密度牺牲约8%。因此,10万元以下车型普遍采用高强钢,兼顾成本与基础安全性。
c. 复合材料:高端化的试探
· SMC材料:电池包上壳体采用玻璃纤维增强复合材料,比钢减重30%,但需通过增加厚度(3mm+5mm加强筋)弥补抗冲击性短板。
· 碳纤维:宝马i3壳体比铝轻50%,但成本高达800元/kg,量产难度大,目前仅用于豪华车型。
实践总结:材料选择需匹配车型定位。中端市场(20-30万元)以铝基材料为主,低端市场依赖高强钢,而豪华车型则探索碳纤维复合方案。
2-制造工艺:效率与可靠性的平衡术
电池壳体的制造工艺直接影响生产效率和产品可靠性,当前主流技术路线包括压铸、挤压焊接及结构集成技术。
a. 压铸VS挤压焊接
· 挤压铝型材(通用Bolt采用):单件成本约800元,适合大批量生产,但工序复杂。
· 压铸铝(蔚来ET5):单件成本1500元,但生产效率提升5倍,适合快速爬产需求。
· 搅拌摩擦焊(FSW):较传统弧焊变形减少50%,抗疲劳性能提升30%,但设备投资需增加40%,适合对寿命要求高的商用车型。
b. 结构集成技术
· CTP无模组化(宁德时代麒麟电池):空间利用率从72%提升至85%,成本降幅15-20%,但需加强热失控防护设计。
· CTC底盘一体化(特斯拉Model Y):减少370个零件,续航提升54%,但维修成本增加300%,对售后体系提出挑战。
关键数据对比
产线经验:CTP技术因兼容性高,仍是当前主流;而CTC需车企与电池厂深度协同,短期内难以普及。
3-未来趋势:技术融合与智能化升级
a. 材料复合化
铝/碳纤维混合壳体(如保时捷Taycan概念)可减重15%并实现800MPa抗压强度,但界面结合强度需>25MPa(丰田bZ4X量产合格率仅65%),工艺稳定性待突破。
b. 功能集成创新
· 液冷板与壳体一体化(广汽弹匣电池):冷却接触面积增加50%,温差控制<5℃,但铝-铜异种焊接气孔率需通过激光摆动焊优化。
· 嵌入光纤传感器(大陆集团方案):实时监测壳体应变与温度,BMS响应速度提升30%,但需解决传感器耐久性问题。
c. 绿色循环体系
宝马闭环回收再生铝技术将碳排放降低60%,但再生材料性能损失需控制在10%以内。此外,大型薄壁压铸(如力劲9000T压铸机)需精确控制模具温差(±5℃),毛刺清理效率成为量产瓶颈。
工艺突破方向:
· 复合材料成型周期压缩(如LGF-PP注塑周期需从180秒缩短至90秒);
· 数字孪生技术应用,将碰撞仿真误差从±20%降至±5%,提升设计可靠性。
4-市场分层与产业化展望
短期(1-3年):CTP+挤压铝型材仍为主流,宁德时代凭借34%市占率持续领跑;
中期(5-10年):CTC与碳纤维在高端市场加速渗透,预计2030年碳纤维占比达25%;
长期目标:能量密度向400Wh/kg突破,同时在国标30分钟热失控防护基础上,进一步提升安全冗余。
5-结语
电池壳体技术路线的选择本质是“场景化适配”,需综合考虑车企定位、成本阈值及供应链成熟度。作为工程师,我们既要拥抱材料与工艺的创新,也需立足量产可行性,在轻量化、安全与成本的动态平衡中寻找最优解。未来,随着智能化与绿色制造技术的成熟,电池壳体将逐步从“被动防护”转向“主动安全”,为新能源汽车的全面普及提供坚实支撑。
我们会定期更新有关热设计与轻量化的技术与资讯,与您分享,供您参考,感谢您对迈泰的关注。
在实际的生产、组装及使用过程中,电池托盘的绝缘耐压失效问题时有发生,犹如隐藏在新能源产业高速发展的暗礁,威胁着车辆的行驶安全与储能系统的可靠运行,本文试图结合制造实际,对典型失效模式进行分析,以期为相关从业者提供一些粗浅的参考,助力行业同仁共同探索提升电池托盘绝缘耐压性能的有效途径。
下篇-常见失效分析
图1 绝缘耐压测试
1-常见失效产生机理分析
储能与新能源汽车用电池托盘应用场景存在差异,导致绝缘耐压要求及失效情况既有共性也有差异,具体如下:
a.差异点
动态载荷 :新能源汽车需应对 20 - 2000Hz 的高频机械振动,而储能系统主要面临长期静态形变,形变累积时间超 10 年。
电压等级 :新能源汽车电池托盘的绝缘耐压需达 3000VDC 及以上(依据 GB 38031),储能系统则要求绝缘耐压在 4200VAC 及以上(依据 IEC 61439)。
失效加速因子 :新能源汽车因每年超 2000 次的充放电循环产生热应力,加速绝缘失效;储能系统则因 7×24 小时运行,年均运行时长超 8000 小时,导致电化学老化,进而加速绝缘失效。
b.共性要点
两者均需通过绝缘电阻监测(冷态不低于 100MΩ,热态不低于 1MΩ/kV)以及局部放电量控制(小于 5pC),来实现绝缘失效的预警。
2-常见的制造缺陷引发的电池托盘绝缘耐压失效
(1)绝缘耐压施工阶段
a.潜在失效与原因分析
· 材料缺陷:
原因:绝缘材料耐压等级不足、受潮老化或表面污染(油污、金属碎屑)。
表现:绝缘电阻低(<100MΩ)、耐压测试漏电流超标或直接击穿。
· 工艺问题:
原因:金属碎屑残留(焊接/切割工艺粗糙)、绝缘涂层厚度不均或未固化。
表现:局部放电、绝缘层破损引发短路。
· 环境干扰:
原因:高温高湿导致材料吸潮、化学腐蚀。
表现:绝缘性能随环境恶化,冷凝水引发爬电。
· 测试失误:
原因:测试电压/时间设置错误(如未按GB/T 38661标准)、接地不良。
表现:误判合格或过压损坏部件。
b.应对策略
· 材料优化:选用耐压≥1000V DC的防潮材料(如碳纤维复合材料),涂覆防污涂层。
· 工艺管控:采用自动化焊接/喷涂设备,设置洁净车间。
· 环境管理:安装温湿度监控,施工前预烘干材料。
· 测试规范:分段测试(500V预检 + 1000V正式测试),校准仪器并记录数据。
(2)模组安装阶段
a.潜在失效与原因分析
· 装配误差:
原因:绝缘衬垫漏装、螺栓过紧压损绝缘层。
表现:模组与壳体间绝缘电阻低,耐压击穿。
· 机械损伤
原因:搬运工具划伤、金属碎屑刺穿绝缘膜。
表现:局部短路或运行中突发失效。
· 设计兼容性
原因:模组与托盘尺寸偏差导致电气间隙不足。
表现:寄生电容引发电压叠加击穿。
· 电气连接隐患:
原因:线束未固定导致磨损、连接器密封失效。
表现:高压线束绝缘层磨损漏电。
b.应对策略
· 防错设计:使用定位销工装防漏装,定制螺栓长度防过紧。
· 洁净操作:安装前吸尘清理,工具包裹防刮擦硅胶。
· 公差仿真:通过CAE验证模组与托盘的匹配度,确保间隙≥10mm。
· 过程检验:安装后兆欧表抽检(≥100MΩ),分段耐压测试定位故障点。
(3)系统集成阶段
a.潜在失效与原因分析
· 跨系统接口失效:
原因:部件绝缘参数不匹配(如连接器耐压等级差异)。
表现:高压母线连接处击穿或BMS受干扰。
· 寄生电容叠加:
原因:多模组并联后总寄生电容增大,容升效应显著。
表现:系统级测试漏电流超标。
· 环境应力失效:
原因:振动导致绝缘疲劳、冷却液渗入高压接口。
表现:运行中绝缘电阻周期性下降。
· 测试盲区:
原因:未模拟真实工况(高温/振动/湿度)。
表现:实验室通过但实际运行失效。
b.应对策略
· 兼容性设计:统一供应商部件标准。
· 寄生电容控制:增加聚酰亚胺隔离层,SPICE仿真优化布局。
· 工况模拟测试:执行“-40℃~85℃循环+5Hz~200Hz振动+耐压”复合测试。
· 智能监测:集成在线绝缘监测模块,AI预测潜在风险。
3-绝缘耐压测试
绝缘耐压测试既是安全保障手段,也可能成为失效诱因。绝缘耐压测试本身可能因操作不当、设备问题或设计缺陷引发失效,甚至对被测设备造成二次损伤。
(1)测试过程中常见的失效类型
(2)应对策略如下:
a.测试参数精准控制
· 电压与时间:按标准设定;对容性负载(如电池模组)启用动态补偿算法,抑制容升效应。
· 漏电流阈值:根据设备规格设定(如≤10mA),并区分直流/交流模式(DC测试需更低阈值)。
b.设备与操作规范
· 仪器校准:耐压测试仪每6个月校准一次,高压线绝缘层每日目视检查。
· 安全操作:测试前强制断开低压电路;采用机械臂或自动夹具避免人工接触高压区域。
c.失效预防与修复
· 分段测试:对复杂系统分模块测试(如先测高压母线,再测模组绝缘),定位击穿点。
· 失效修复:击穿后使用环氧树脂填补破损处,修复后需重新通过全电压梯度测试(如500V→1000V阶梯加压)。
d.环境与数据管理
· 环境控制:测试区湿度>75%时启动除湿机,或延迟测试至环境达标。
· 数据追溯:记录测试电压、漏电流曲线、环境参数,利用MES系统关联生产批次号。
我们会定期更新有关热设计与轻量化的技术与资讯,与您分享,供您参考,感谢您对迈泰的关注。
电池托盘使用绝缘材料主要是为了防止电流泄漏,保护人员安全,同时确保电池系统的正常运行。在选型时,需要考虑材料的绝缘性能、耐热性、化学稳定性和机械强度。这些因素共同决定了绝缘材料在电池托盘中的应用效果,从而影响整个电池系统的安全性和可靠性。
电池托盘电气绝缘安全丨中篇-耐压性能保障
图1 电动汽车电池托盘
1-绝缘材料选型与方案设计
在电池托盘绝缘材料的选型中,重点关注材料的介电性能、环境耐受性和机械性能。以下是电池托盘中常用的 6种绝缘材料及其相关信息:
方案设计时我们一般需综合考虑应用场景、性能要求及成本预算三大关键因素来选择合适的绝缘材料。如:
(1)根据应用场景选择:在像高压、大电流的储能电池系统中,电池托盘侧边若需要高性能绝缘材料,建议采用PI膜贴附方案;若绝缘性能要求不高,绝缘粉喷涂方案可供选择。对于电池托盘底板,若追求低成本绝缘方案,绝缘粉喷涂或绝缘漆涂覆方案较为合适。
(2)根据性能要求选择:当对绝缘性能、耐高温性能、耐化学腐蚀性能等要求较高时,PI膜贴附方案是较好的选择;若这些性能要求相对较低,绝缘粉喷涂或绝缘漆涂覆方案可满足需求。
(3)根据成本预算选择:成本预算有限时,绝缘粉喷涂或绝缘漆涂覆方案更经济;成本预算充足的情况下,可选择PI膜贴附方案。
2-电池托盘选用PI膜技术要求
(1)材料:PI,基膜厚0.1-0.14mm,背胶胶厚0.03mm,PI膜导热系数>0.3W/(m·k);
(2)耐压性:AC 3000V,60S,漏电流≤0.5mA;
(3)(冷贴)180°剥离强度≥15N/24mm;
(4)绝缘性:DC 1500V,60S,绝缘电阻>1000MΩ;
(5)耐温耐电解液绝缘性能:在500℃、700V DC电压,滴加2ml电解液下(测试面积13000mm<H>2<H>),保持1h,无击穿无跳火;
(6)耐温绝缘性能:500±2℃下,持续烘烤(马弗炉)0.5h,样品整体形态变化过程无自燃,且试样两过。表面施加AC 1000V,从0V到3000升压时间10S,继续持续60S,被测样品无击穿、无跳火;
(7)阻燃等级:UL94 V-0;
(8)高温高湿:1000小时85℃和85%湿度试验后,样品无开裂、无变形,满足国标《GBT 13542.6-2006 电气绝缘用薄膜 第6部分:电气绝缘用聚酰亚胺薄膜》中关于绝缘电阻、耐电压值、电气强度要求,拉伸强度、断裂伸长率、剥离强度相比本物料未老化时下降<30%;
(9)冷热冲击:85℃持续一小时切换至-40℃持续一小时,再切换至85℃这样高低温循环。切换时间包含在一小时内,切换时间≤3min。样件在高低温循环1000小时后,样品无开裂、无变形,满足国标《GBT 13542.6-2006 电气绝缘用薄膜 第6部分:电气绝缘用聚酰亚胺薄膜》中关于绝缘电阻、耐电压值、电气强度要求,拉伸强度、断裂伸长率、剥离强度相比本物料未老化时下降<30%。
(10)盐雾试验:GB/T 10125标准中的中性盐雾试验(NSS)测试,温度为35℃、湿度≥85%RH,试验溶液为(5±0.1%)(质量分数)NaCl ,PH=6.5~7.2,连续喷雾72h,盐雾试验后,样品无开裂、无变形,满足国标《GBT 13542.6-2006 电气绝缘用薄膜 第6部分:电气绝缘用聚酰亚胺薄膜》中关于绝缘电阻、耐电压值、电气强度要求,拉伸强度、断裂伸长率、剥离强度相比本物料未老化时下降<30%。
(11)产品符合RoHS。
图2 电池托盘用PI膜
3-绝缘耐压测试方法及常见问题解决方案
(1)绝缘耐压测试方法
绝缘耐压测试是评估电气设备绝缘性能的重要手段,主要包括直流耐压测试和交流耐压测试。直流耐压测试通过施加直流高电压,检测绝缘材料在规定时间内是否击穿,设备包括直流高压发生器、电压表等,步骤为施加电压、保持电压和降低电压。交流耐压测试则施加交流高电压,设备和步骤与直流测试类似。两种方法均需在测试前做好准备工作,确保设备接地良好,并在测试过程中密切观察绝缘材料的表面状况。
(2)常见问题及解决方案
绝缘耐压测试中常见的问题包括绝缘击穿、泄漏电流过大和测试设备故障。绝缘击穿可能由绝缘材料性能不足、内部缺陷或受潮引起,解决方案包括选择优质材料、加强维护和改进绝缘结构。泄漏电流过大可能由绝缘电阻降低、表面污染或测试设备精度不够导致,解决方案包括保持绝缘材料清洁、干燥和校准测试设备。测试设备故障可能由设备老化、维护不当或操作不当引起,解决方案包括定期维护、正确操作和及时维修。
我们会定期更新有关热设计与轻量化的技术与资讯,与您分享,供您参考,感谢您对迈泰的关注。
随着新能源汽车和储能技术的快速发展,电池系统作为核心能量载体,其安全性与可靠性备受关注。电池托盘作为电池模组的承载与防护结构,其电气绝缘性能直接关系到整车的安全运行、电池寿命及用户人身安全。电池托盘的电安全设计是电池系统安全性的基石,通过多层次防护,如:绝缘、结构、热、监测等,在复杂工况下保障电池稳定运行,降低因电气故障引发的火灾、爆炸或触电风险,同时延长电池寿命并提升系统可靠性。
本文围绕电池托盘的电气绝缘安全,系统阐述其设计原则、耐压性能的验证方法,以及典型失效案例的根因分析与改进策略,以期为电池系统的高安全设计提供理论支撑与实践参考。
上篇-设计要点
电池系统的电安全设计的核心在于“预防-控制-应急”三位一体:通过绝缘隔离、可靠连接、热管理等措施预防故障;借助传感器和BMS实现实时控制;利用防火、泄压等设计应对极端情况。各要点需协同作用,确保电池系统在全生命周期内的安全可靠,同时兼顾可维护性与合规性。电池托盘在电池系统中不仅是结构支撑,还承担电气隔离、热管理、防滑、机械保护、接地和模块化设计等多重功能,对保障电池系统的电气安全至关重要。
1-结构支撑确保电气连接可靠性
电池托盘通过固定电池模块、减少机械应力、抗振抗冲击、保持对齐、环境防护和热管理集成等,确保在复杂工况下电气连接的可靠性和安全性。
图1 电池托盘
A.物理支撑与固定,确保电气连接点(如汇流排、线束、接插件)的精确对位,避免因结构变形或位移导致的接触不良;提供刚性框架,固定电池模组和连接件,防止振动或冲击引起的松脱或断裂。
B.环境隔离与防护,通过密封设计(如IP67/IP68)防止水汽、灰尘、盐雾等侵入,避免腐蚀或绝缘失效导致的短路;阻隔外部机械冲击或异物撞击,保护高压连接部件。
C.热管理协同,集成散热结构(如液冷板、导热垫)均衡温度,防止局部过热导致连接点氧化或熔焊;通过隔热设计减少相邻模组间的热干扰,避免温度梯度引发的材料膨胀差异。
D.电磁兼容(EMC)支持,通过金属屏蔽层或导电涂层抑制电磁干扰,保护低压信号线路(如BMS通信线)免受高压回路干扰。
2-隔离防护构建高效隔离环境
电池电气隔离设计重点在于构建一个既能有效隔绝高压电、又能确保系统高效运行的环境,确保电池模块在任何工况下都能被安全地封装,防止电气能量意外释放,从而规避潜在的电气风险。
A.电池托盘结构兼顾承载和隔离防护:
l 优选铝合金材料,如挤压铝合金,以实现轻量化同时保持高刚性和抗冲击性,外框以承受整个电池系统的重量和外部冲击,采用封闭截面型材增强结构强度,内框设计用于支撑电池模组和水冷板等,确保它们的稳定性和散热需求。
l 使用绝缘材料作为衬垫或涂层,确保电池模块与托盘之间有良好的电气隔离,高压线束应有专门的管理路径和绝缘护套,保证与托盘的电气间隙和爬电距离。
l 采用搅拌摩擦焊等先进焊接技术,提高连接强度,同时减少热影响区,避免变形和潜在的裂纹,对于不便焊接的部分,使用螺栓连接或铆接,结合密封胶,确保机械连接的可靠性和电气隔离。
l 设计时考虑模块化,便于电池的更换和维护,同时不影响整体结构的稳定性。
图2 电气间隙与爬电距离示意
B.高低压隔离设计要点:
l 电池系统的正负点位必须与低压供电系统隔离,并且与电池托盘隔离,确保高压电路与低压控制电路之间有足够的电气间隙和爬电距离,以符合安全标准,防止高压泄露至低压系统
l 高低压隔离设计需考虑电磁兼容(EMC),确保隔离措施不会引入干扰,保持系统稳定运行。
l 高阻抗连接,高低系统之间通过高阻抗连接,只允许接到车身接地(电池托盘)以限制电流流动,确保高压系统故障蔓延至低压系统。
l 物理隔离措施,设计电池托盘时,可以将高压和低压组件布置在不同的封闭腔室内,通过物理分隔减少相互影响;在电池模组与托盘之间使用绝缘材料作为衬垫,如高分子塑料或橡胶,以确保物理和电气上的隔离。
l 设计时考虑隔离措施的可维护性,确保在需要时能够安全地进行维修或更换。
C.接触防护设计要点:
l 高压线束管理:高压线束应被妥善包裹在绝缘护套内,并通过固定夹或导线槽进行有序管理,避免裸露,减少直接接触的风险。
l 安全隔板:在电池模组之间和电池模组与托盘壁之间设置绝缘隔板,以防止在电池损坏时电解液泄露导致的间接电击风险。
l 高压部件封装:对高压连接器、继电器等关键部件进行封装处理,确保即使在托盘内部,这些部件也不会因意外而被直接触及。
l 封闭式设计:电池托盘整体设计为封闭结构,使用金属或复合材料外壳,确保内部高压组件不会外露,同时外壳本身也需具备良好的绝缘性能。
l 锁定机制:对于可维护的高压连接点,采用锁定机制,确保在非专业操作时不会轻易打开,减少误触风险。
l 绝缘材料应用:使用绝缘材料作为电池托盘与电池模块之间的隔离层,确保即使在托盘受损的情况下,也能防止人体直接接触带电部分。这些材料包括但不限于高分子塑料、橡胶垫片或涂层。
3-电气标识设计
电池托盘的电气标识不仅能够提升操作的安全性,还能简化维护流程,减少错误操作的风险。
A.明确标识
l 在电池托盘及周边高压组件上清晰标注“高压危险”、“勿接触”等警告标识,确保即使在紧急情况下也能快速识别。
l 使用国际通用的颜色编码,如红色或橙色标识高压区域,蓝色代表直流电,以直观区分不同电气特性。
l 应用标准化的电气安全符号,如IEC 60417中的图形符号,来表示高压、接地、断电点等,确保信息的全球可理解性。
l 包含电池托盘的序列号、生产日期和批次信息,便于追踪和召回管理。
l 选用耐磨损、耐腐蚀的材料和印刷技术,确保标识在电池托盘的整个生命周期内保持清晰可读。
B.警告标识
l 在电池托盘及周边区域明确标识高压危险,提醒维修人员注意电气安全,遵守操作规程。
l 指示安全操作距离,尤其是在高压连接器和裸露导体附近,提醒保持适当距离。
C.操作指引
l 明确标出电池系统和托盘的接地位置,确保正确实施接地措施。
l 标识出安全的测试点和维护接入点,这些点应设计为低电压或非带电状态下的操作点。
l 可以在托盘的非关键区域简要列出基本操作和安全指南,引导正确操作流程。
我们会定期更新有关热设计与轻量化的技术与资讯,与您分享,供您参考,感谢您对迈泰的关注。
目前比较流行的水冷头,基本上采用纯铜微通道型。铜底板直接进行铲齿加工,鳍片与底板一体,减少热阻。底板与盖板之间则采用钎焊或者扩散焊的方式,确保密封的可靠性。
下篇:铲齿工艺加工水冷头主要成本构成
1-铲齿工艺制造水冷头的优势
l 一体化设计:铲齿工艺可以将地板和鳍片进行一体化加工,有利于减少接触热阻,提升热传导性能。此外一体化的底板和鳍片设计还可以提升结构强度。
l 高精度加工:铲齿工艺可以加工出非常精细的齿片结构,齿高、齿厚和齿距可以精确控制,这使得散热鳍片密度更高,散热面积更大,进而更高效散热。同时也能更好的满足不同客户对形状、尺寸等个性化的需求。
l 生产效率高,铲齿工艺可以批量生产,与传统的CNC相比,铲齿工艺可以同时加工多个齿片,大大提高了生产效率。
图1:不同加工工艺的水冷头底座 a-铲齿 b-CNC c-冷锻
2-铲齿工艺水冷头成本构成
l 设计与开发成本:铲齿工艺水冷头的设计复杂度较高,尤其是在散热性能要求较高的情况下,需要进行复杂的工艺设计和优化。
l 材料成本:铲齿工艺中使用的材料主要是铝和铜合金。铝板与铜合金结合的设计方式在散热器制造中较为常见,且性价比较高,因此铝和铜的质量直接影响成本.
l 加工工艺成本:
铲齿工艺成本:铲齿工艺涉及高精度的数控加工设备,如三轴线轨数控机床。这种设备的使用需要较高的投入成本,同时对操作人员的技术要求也较高,这些都会增加生产成本。
焊接工艺成本:在水冷头的制造过程中,焊接工艺也是一个重要的成本因素。真空钎焊和扩散焊是两种常用的焊接方法。钎焊可以同时焊接多个接头、生产效率高,需要钎料,对工艺条件的要求较,质量控制难度大;扩散焊设备一次性投资较大,扩散焊不需要填料,但对工件表面的加工要求高。
表面处理成本:常见的表面处理方式有阳极氧化、镀层处理等。对于铝合金水冷头,阳极氧化处理可以提高表面硬度、耐磨性和耐腐蚀性,同时增加产品的美观度;对于铜质水冷头会进行镀层处理,如镀镍等,以防止铜的氧化和腐蚀,提供产品的使用寿命和可靠性。
l 其他成本:检验检测、包装运输等。
3-成本优化建议
l 优化材料使用:
选择合适的材料:如,铜的导热系数高,单密度大,单价高;铝的质量轻,单价低,导热系数稍差。
材料用量:通过精确计算材料厚度和余量,确保材料的高效利用,减少材料浪费。
图2:材料用量计算示意
l 优化生产流程
简化模具:设计简单的模具,减少模具的复杂度和成本。
减少废品率:通过精确的工艺控制和质量检测,减少废品率。
一次成型:优化工艺路线,减少多次加工工序,提高生产效率。
我们会定期更新有关热设计与轻量化的技术与资讯,与您分享,供您参考,感谢您对迈泰的关注。
水冷头作为液冷散热系统的关键部件,其设计需兼顾换热性能、结构强度、防腐蚀性、防泄漏性以及成本控制等多方面因素。水冷头内部通常设计有复杂的换热槽结构(即流道),其内部流道设计的优劣直接决定了整个系统的换热效率。
中篇:水冷头设计、加工工艺及挑战
1-不同场景对水冷头的设计要求
l 高性能计算:
高性能计算设备(如高性能CPU、GPU等)在运行过程中会产生大量热量,因此需要水冷头具备高效的散热能力。为了应对高热流密度散热需求,水冷头通常采用高密度微流道设计,以增大换热面积,提高散热效率。此外,一些设计将水冷头直接集成到CPU上,省去了涂抹硅脂的步骤,不仅简化了组装过程,还进一步提升了散热性能。可靠性方面,水冷头必须具备出色的密封性能,以防止泄漏,确保长期稳定运行。
l 显卡散热:
显卡是高热量产生区域,因此需要水冷头具备全覆盖设计,以确保显卡上各个发热部件均能得到有效散热。同时,显卡散热对冷却液的流量要求较高,需要水冷头内部结构设计支持高流量通过,以便快速带走热量。
l 数据中心:
在数据中心中,水冷头的结构设计需要满足高效散热、低噪音、高可靠性、适应高功率密度、智能化管理和环境适应性等多方面的要求,以确保数据中心的稳定运行和高效散热。
2-水冷头结构演化趋势
水冷头结构设计的演化趋势体现了技术创新和性能提升的双重追求,主要体现在以下几个方面:
l 散热性能提升:
增大接触面积:一些水冷头设计通过增加与发热元件的接触面积,提高散热性能。如,采用大面积铜底座设计,可以实现良好的接触和热传导。
优化内部结构:对内部水道进行优化,一种思路以优化流体流动为目标,如,由普通Fin片改为转向Fin片风格,呈现长条形流道,促进流动边界层分离,减少边界层厚度,提升热交换效率;另一种思路以增大热容面积为目标,如,从传统的粗水道向微流道设计转变,显著提高了冷却液与底板的接触面积,增强了散热效率。还有些设计中通过导流板将冷却液喷射至微水道底板,提升局部流速和乱流,大幅提高吸热效率。
l 集成化和智能化设计:
一体化设计:通过一体化设计将水泵、散热鳍片、导热底座等部件集成到一起,减少连接点,提高系统稳定性和散热效率。
多功能集成:除了散热性能,现代水冷头还具备温显、监测功能。
模块化设计:通过组合式扣具结构,提高组织的便利性和自由度。
图1:不同Fin厚水冷头底座
l 高性能材料和表面处理:
采用纯铜底座等高性能材料,结合镀镍等表面处理技术,提升导热效率和抗腐蚀性能。
3-加工工艺及挑战
l 材料特性影响加工:
材料硬度与韧性问题:不同材质的散热器,如铜、铝及其合金,硬度和韧性不同,对加工刀具和工艺的要求也不同。硬度较高的材料,刀具磨损加快,需更频繁地更换刀具;韧性好的材料,切削时易产生变形和毛刺。
铜铝复合材料加工复杂:铜铝复合材料铲齿散热片,需先采用连续铸造半熔态压制成型技术制成复合材料,再进行铲齿加工,工艺流程更复杂,对设备和工艺的精度要求更高。
l 尺寸精度要求高
齿高齿厚一致性难保证:对于一些高密齿散热器,其要求每个齿的高度和厚度都高度一致,以确保散热片的性能和均匀性。若齿高齿厚差异过大,会导致热传递不均匀,影响散热效果。加工过程中,需使用高精度设备和自动化控制系统,才能确保每个齿的规格一致。
齿间距控制难度大:散热片上的齿过于密集时,其密度和间距使得加工过程更加复杂,加工设备需具备更高的速度和精度,才能保持齿的均匀性。例如,当齿间距过小,刀具在切削时容易产生干涉,影响加工精度和表面质量。
l 表面质量要求严格
毛刺问题:加工过程中易产生毛刺,这不仅影响散热器的美观度,还可能阻碍空气流动,降低散热效果。毛刺的产生可能由材料切削精度低、加工工具刀具磨损等原因引起,需采取相应的去毛刺工艺来解决。
表面粗糙度:散热器的表面粗糙度影响其散热性能和后续的表面处理效果。过高的表面粗糙度会增加空气流动的阻力,降低散热效率,还需进行额外的表面处理来降低粗糙度,增加了加工成本和时间。
l 加工设备与工艺要求高
设备精度与稳定性:铲齿加工需要高精度的铲齿机,设备的精度直接影响齿的尺寸精度和表面质量。同时,设备需具备良好的稳定性,以保证长时间加工过程中尺寸的一致性。
刀具选择与磨损:合适的刀具对加工质量至关重要。刀具的材质、几何参数等需根据材料特性进行选择。加工过程中,刀具磨损会导致切削力增大、尺寸精度下降和表面粗糙度增加,需及时调整或更换刀具。
进给速度与切削深度:进给速度和切削深度的不合理设置,易导致加工缺陷。如进给速度过快,切削深度过大,会使刀具承受过大负荷,出现抢刀、弹刀、掉刀等现象,影响加工精度和表面质量。
图2:铲齿工艺
l 定制化需求高
不同的应用场景对散热器的尺寸、形状、齿高、齿厚、齿间距等参数有不同的要求,需根据具体需求进行定制化设计和加工。这要求加工厂家具备灵活的工艺调整能力和丰富的经验,以满足多样化的定制需求。
我们会定期更新有关热设计与轻量化的技术与资讯,与您分享,供您参考,感谢您对迈泰的关注。
随着全球人工智能算力的迅猛增长,以及芯片热设计功耗(TDP)的持续攀升,数据中心的冷却需求正面临前所未有的挑战。与此同时,全球范围内节能降碳政策的日益严格,进一步推动了冷却技术的革新。在这一背景下,传统的风冷方案已逐渐难以满足高效散热与节能的双重要求,液冷技术因其卓越的散热性能和显著的节能优势,正迅速崛起,成为数据中心冷却方案的主流选择。服务器作为数据处理和存储的核心设备,其性能与稳定性直接关系到整个系统的运行效率。服务器的核心组件——包括主板、CPU、内存、硬盘和显卡等——在持续高负荷运作下会产生大量热量,若不能及时有效地散热,将严重影响服务器的性能和寿命。为此,先进的液冷系统被引入到服务器散热解决方案中,直接安装在主要热源如CPU和显卡上,以显著提升散热效能。
上篇:水冷块结构及工作原理
液冷系统的核心部件之一是水冷块,它通常由高导热性的铜或铝材料制成,设计有精密的水道和散热片结构。这些水冷块紧密贴合在CPU、GPU等热源表面,通过内部流通的冷却水迅速吸收并转移热量。随后,热量被输送至散热片,通过水冷系统的循环,最终将热量散发到周围空气中。
图1:主流芯片制造商芯片热功耗趋势
1-常见水冷块类型及特点
l 微通道水冷头
特点:微通道水冷头采用精密的微小水道设计,水道结构细密且复杂,能够显著增加冷却液与发热部件的接触面积,从而大幅提升散热效率。微水道设计还能够在冷却液流动过程中产生强烈的湍流效应,进一步增强对流换热系数,实现高效的热量转移。
应用场景:特别适用于高发热量的CPU和GPU,尤其在高性能计算、超频以及数据中心等对散热要求极高的场景中表现卓越。
l 大流量水冷头
特点:大流量水冷头的内部结构相对简单,通常采用铜板或蚀刻凹槽设计,制造成本较低。其核心优势在于依靠高速水流快速带走热量,适合搭配大流量的水冷系统使用。虽然结构简单,但其高效的散热能力使其成为性价比极高的选择。
应用场景:适用于对散热效率有一定要求但预算有限的场景,例如中高端的DIY电脑系统或中小型服务器集群。
l 喷射型水冷头
特点:喷射型水冷头通过导流板将冷却液从狭小的喷嘴高速喷射到微水道底板上,形成强烈的湍流效应,显著提升散热效率。这种设计不仅增加了冷却液与底座的接触面积,还通过高速流动进一步优化了热交换性能。
应用场景:适用于高性能CPU和GPU,尤其在高散热需求和高流量场景中表现突出,例如超频计算、人工智能训练以及图形渲染等领域。
2-水冷块一般结构
水冷块是一个内部留有水道的金属块,通常由铜或铝制成,与CPU、显卡或其他发热不见接触,其结构设计直接决定了散热性能的优劣,典型的水冷块通常由以下几个关键部分构成:
l 底座,通常由高导热材料,如铜或铝合金,表面经过精细加工,以确保与发热部件的紧密接触。底座内部设有复杂的流道设计,以增加冷却液与底座的接触面积。
l 盖板,与底座一起形成流道密封腔,保护水冷块内部的流道、密封等组件,防止灰尘、杂质和外界物理损伤。
l 进出水口,进出水口是冷却液进出水冷头的接口,一般设计在水冷头侧面或顶部,要确保冷却液能够顺利的流入流出,其位置设计需要考虑流体的流动路径,以减少流阻,提高冷却液流动速度。
l 扣具,扣具是将水冷头牢固地固定在CPU或其他发热部件上,确保紧密基础,实现高效热传导。
图2:水冷块典型构造
3-散热性能综合优化
l 流道设计优化
增加流道接触面积:通过设计更窄、更密集的流道,可以显著增加冷却液与底座的接触面积,从而提高对流换热系数。例如,微水道设计通过其细密的水道结构,微通道水冷块的设计参数(如通道宽度、高度、间距)对其散热效率具有决定性影响:随着通道宽度的减小,换热系数显著增加,得益于窄通道内冷却液流动的湍流效应增强,从而提高了热交换效率;较高的通道高度有助于增加冷却液的流动空间,从而提升换热性能;较小的通道间距能够增加冷却液与热源的接触面积,从而提高散热效率。
还可以通过优化流道布局及减少流道弯道进行优化:合理的流道布局能够确保冷却液均匀覆盖发热部件的表面,减少局部温差。而流道中的弯道会增加水头损失和内部流阻,从而降低冷却效率。在设计中应尽量减少弯道数量,若无法避免,则需将弯道设计为圆滑过渡,以降低压降并优化流动性能。
l 高导热材料:水冷块的底座通常采用纯铜或铝合金等高导热材料,这些材料能够高效地将热量从热源传导至冷却液,从而提升整体散热性能。
l 结构参数优化,如:底座基板厚度、Fin片、扰流结构等。基板厚度的增加会导致最高温度上升,因此在设计中需要在散热效果与结构强度之间找到最佳平衡点;通过增加肋片的高度、厚度和间距,可以提升散热性能,但同时也会增加流阻,找到最佳的肋片设计组合,从而实现散热性能的最大化。扰流柱的形状能够有效增强湍流效应并提升热交换效率。
我们会定期更新有关热设计与轻量化的技术与资讯,与您分享,供您参考,感谢您对迈泰的关注。
本文从生产实际出发,总结了搅拌摩擦焊焊接过程中常见的问题、产生原因及改善方法,供大家参考。
1-表面缺陷
(1)表面沟槽
l 问题描述:表面沟槽又称犁沟缺陷,通常出现在焊缝的上表面,偏向于焊缝的前进边,呈沟槽状。
l 产生原因:焊缝周围的热塑性金属流动不充分,焊缝的塑性金属无法充分填充搅拌针行进过程中留下的瞬时空腔。
l 改善方法:增大轴肩直径,增大压力,降低焊接速度。
图1: 沟槽
(2)飞边毛刺
l 问题描述:飞边毛刺出现在焊缝的外边缘,呈波浪形。
l 产生原因:旋转速度和焊接速度的匹配不当,下压量过大。
l 改善方法:优化焊接参数,减少下压量。
图2:飞边毛刺
(3)表面起皮
l 问题描述:表面起皮或起丝呈皮状或丝状出现在焊缝的表面。
l 产生原因:大量的金属摩擦产热积累于焊缝的表层金属,使得表层的局部金属达到熔化状态。
l 改善方法:优化焊接参数,降低转速,提高焊速度。
图3:表面起皮
(4)背部焊瘤
l 问题描述:在焊缝的背面形成焊瘤。
l 产生原因:焊接过程中搅拌头的深度和压力控制不当。
l 改善方法:优化搅拌头的深度和压力设置。
2-内部缺陷
(1)未焊透
l 问题描述:焊缝底部未形成连接或者不完全连接而出现的“裂纹状”缺陷。
l 产生原因:搅拌针长度不足,导致焊缝下部的材料未能充分搅拌。
l 改善方法:选择合适的搅拌针长度,确保焊缝厚度上的材料能够被充分搅拌。
图4:未焊透
(2)孔洞
l 问题描述:焊缝底部未形成连接或者不完全连接而出现的“裂纹状”缺陷。
l 产生原因:焊接过程中,由于摩擦热量输入不够,使达到塑化状态的材料不足,造成不充分的材料流动,导致焊缝区未完全闭合的。
l 改善方法:优化焊接参数,改进搅拌针设计,控制焊接速度和转速。
图5:孔洞
我们会定期更新有关热设计与轻量化的技术与资讯,与您分享,供您参考,感谢您对迈泰的关注。
近段时间,小编注意到多家企业都在关注和布局浸没式液冷储能,浸没液冷技术在沉寂一段时间后再次受到关注,似乎又有“变火”的趋势,相信很多同行也都在关注这一进展。
1-浸没式液冷技术特点
储能电芯走向300+Ah、储能系统纷纷走向5MWh+,电芯越大产热越多、越难散热、越难保证温度一致性,并且储能系统由大量电芯堆叠组成,运行工况复杂多变,更容易造成产热不均、温度分布不均。散热、均温的问题若不能妥善解决,会导致电池的充放电性能、容量和寿命的下降,影响整个系统的性能。此外,安全一直是悬在锂电储能头上的“达摩克利斯之剑”,而提升安全的最普遍做法是向本征安全、主动安全、被动安全三个维度进发。
浸没式液冷是将电芯浸没在在一种绝缘、无毒、可散热的液体中,冷却液具有更高的导热率和比热容,这种直接的接触方式在提供极高的热传递效率的同时,也能够提高更好的均温性。并且,冷却液在作为温度控制的介质外,还可以作为储能系统消防液使用,使得温度控制与消防合二为一,也是浸没式液冷技术的显著特点。浸没式液冷在面对更高散热性能、更强安全性要求的产业背景下,无疑会更具优势。
图1:浸没式液冷储能电池Pack箱
2-浸没式液冷储能系统方案
浸没式液冷技术作为液冷技术一个分支,并非储能行业首创,最初是在高性能计算领域得到应用的,后来逐渐扩展到数据中心、人工智能、加密货币等。
浸没式液冷储能系统的设计初衷是为了解决传统风冷和间接液冷在冷却效率和电池温差控制方面的不足。南方电网梅州宝湖项目正式投运标志着浸没式液冷这一前沿技术在新型储能工程领域的成功应用。
l 冷却方式及冷却液循环方式
冷却方式分为单相和相变两种方式,采用单相浸没液冷,主要包括矿物油、硅油、天然酯等。而另一些方案则采用两相浸没液冷,以氢氟醚为主要代表,利用相变潜热进行散热,提高散热效率。据不完全统计,当前发布的浸没式液冷储能系统中以“单相浸没冷却”的方案居多。
据冷却液的循环方式的差异,在单相浸没液冷又有三条技术路线:自然对流、泵驱动、浸没式耦合冷板式液冷。自然对流利用液体受热后体积膨胀、密度减小的特性,实现热冷却液的上浮和冷却后的下沉,从而完成循环散热;泵驱动系统的核心是液冷机组驱动冷却液在液冷管路及电池浸没箱之间循环流动,完成整个循环散热过程;而浸没式耦合板式液冷的方案中,电池浸没在介电流体中,与介电流体接触的冷板用来带走热量,避免使用复杂的二次回路来冷却介电流体。
l 产品形态与集成方案
浸没式液冷储能系统的集成方案迭代是一个从整体到局部、再到细节的过程,每一步都在前一阶段的基础上进行优化和改进,以实现更高的性能和安全性。
从舱级到Pack级,系统集成技术呈现出场景定制特点。储能场景的多元化使得对储能系统的需求各一,单一产品与无法满足市场需求,模块化设计使得储能产品可以根据项目的规模和电力需求进行优化和扩容,允许根据不同的应用场景和需求快速调整和部署储能解决方案。
3-产业化进程中的挑战及落地场景
浸没式液冷储能系统在商业化过程中面临经济性、技术复杂性、市场接受度、产业链成熟度等多方面的挑战。
l 技术复杂性:相较于冷板式液冷系统,浸没式液冷系统的设计和实施更为复杂。
l 产业链成熟度:浸没式液冷技术的产业链尚未完全成熟,这限制了其在更广泛领域的应用。产业链的成熟度直接影响到技术的推广和商业化进程。
l 经济性挑战:在当前储能行业仍处于商业化发展的初期阶段,盈利性不足使得高成本的技术路线难以受到市场青睐。许多企业在为了一时订单而进行低价竞争,导致浸没式液冷的渗透率受到限制。
当前,储能行业的主要市场仍以风冷和冷板式液冷为主,浸没式液冷尚未完全被市场所接受。尽管浸没式液冷技术的市场渗透率与接受度不高,但在一些特殊的场景下可能展现不出可观的潜力,比如:
l 危化品行业:危化品企业对于储能设备的安全管控极为严格,因为其生产和存储的化学品大多具有高度易燃、易爆、有毒或腐蚀性,一旦发生事故,不仅会对企业自身造成严重损失,还可能引发环境污染和对周边社区造成危害。
l 基站、数据中心:基站、数据中心对热失控容忍度低,数据中心储能系统需保证性能稳定、不易发生热失控的电池,以确保系统的安全性。对电能质量的要求高,需要储能系统具有快速的响应能力,在电网发生故障或停电等紧急情况先,储能系统需能够直接切换至放电模式,以保证电力的连续性和稳定性。
l 快充电站:高倍率充放电时,电池在短时间内产生大量热量,会导致电池温度过高和温度不均,对电池的性能、寿命和安全性构成威胁,就意味着高倍率充放电场景下,电池的热管理变得尤为重要。
我们会定期更新有关热设计与轻量化的技术与资讯,与您分享,供您参考,感谢您对迈泰的关注。
电池包的气密性是电动汽车及储能系统中至关重要的指标,电池包的气密性检测主要针对电池包壳体、接口、连接件、冷却组件等进行检测,以保证电池包内部不受外界环境的灰尘、水气等杂质污染或侵入,冷却组件不发生漏液,确保电池包维持正常的性能和寿命,不发生短路或爆炸等安全事故。
1-电池包的防护等级与气密性检测标准的制定
国际防护等级认证(International Protection Making,IEC60529),也称作异物防护等级或IP代码(IP Code)。IP(Ingress Protection)防护等级系统是有国际电工委员会(IEC)制定的,用于对电气设备外壳对异物侵入和水侵入的防护等级进行分类的标准。电池包箱体的气密等级通常要求达到IP67或IP68,这就意味着电池包箱体需要完全防止灰尘进入(防尘等级6),并且能够在一定压力的水中浸泡一段时间,外壳进水量不致达到有害程度(防水等级7),更严格的要求电池包在1m深的水下浸泡60min而无水进入(防水等级8)。IP防护等级通常由两位数字组成,数字越大,表示防护等级越高,见图1:
图1:IP防护等级说明示意
为了确保电池包IP67、IP68的要求,电池包需要进行沉水测试,此方法耗时较长,对动力电池包具有破坏性,且具有一定的安全风险,并不适合作为动力电池的下线检测。因此使用气密检测来保证电池包满足IP67、IP68的要求成为行业通用做法。气密检测标准的制定需要考虑压降值与泄漏率之间的关系,以及孔径与漏水的关系。气密性检测标准制定时涉及从理论极端到实验验证的一系列步骤,以实现IP等级到气密性检测标准的转换。如,以IP68为例:
图2:气密检测标准制定步骤
2-气密性检测方法选择及检测难点分析
电池包设计和制造质量是影响气密性的关键要素,包括电池箱上盖的韧性和强度、电池包壳体、接口和连接件等部位的密封及防爆透气阀、电气接插件本身的密封性等。此外,使用过程中也会带来一些问题影响气密性,如:热膨胀收缩问题、材料老化及振动冲击影响等。在电池包壳体生产制造中我们更关注焊点和接头质量等问题造成的气密不良,比如焊点不均匀、不牢固或存在裂缝、气隙,接头连接部位密封不良等。
电池包气密性检测主要分为上壳体、下壳体、总装件的气密性测试,上下壳体的气密性测试必须满足总装后的气密性泄漏要求。选择电池包气密性测试方法时,一般会综合考虑电池包的特性、测试精度要求、生产效率以及成本等因素。
工程中电池包壳体测试一般会分为制程气密检测、出货气密检测。并且上下壳体的气密性测试必须满足总装后的气密性泄漏要求,对检测标准提出了更严格的要求。要保证气密性满足要求,实操中必须克服以下困难:
l 产品结构稳定性:焊缝的质量,包括塞块焊缝、水嘴焊缝、横梁焊缝、边框底板焊缝、边框前后封板焊缝等,焊缝漏气问题主要集中在起弧、收弧处及因烧穿导致的不良等;焊接变形应力造成的开裂,如底板腔体侧壁焊接、底板腔体材料分层,无法承受焊接变形应力等。
l 气密工装的适配性与稳定性:工装设计应紧密贴合被测件的外形和尺寸,确保在检测过程中被测件能够稳固的固定在工装上,减少因为位置偏移或晃动导致的测试误差。然而,实际上电池包尺寸和形状差异较大,就需要设计和制造多种不同的测试工装,增加成本和操作复杂性,如果设计一种通用型工装,这又会加大设计复杂度。
l 气密性检测结果的可重复性:气压、温度、测试工件/夹具的干燥状态等因素都会影响气密检测结果。
l 对于工件存在较多不贯穿的微小裂纹,受检测设备精度、检测参数等因素的影响,可能存在泄漏源未能发现,出现漏检现象。
图3:气密检测工装
3-工程中常用的电池包气密检测方案组合
电池包壳体制程气密测试一般会做气密性试验和浸水试验,在气密性试验中,电池箱上盖被密封,只留一个插接件口作为进气口。通过控制气压并观察是否漏气来判断电池包的气密性。而浸水试验则是将整个电池箱体完全浸入水中,通过检查箱体内是否浸水来判断其气密性。
氦气检漏法是一种利用氦气作为示踪气体,通过检测泄漏点的氦气浓度来实现泄漏检测的技术。当氦气进入被检测设备的内部或外部可能存在泄漏的部位时,如果存在漏孔,氦气会迅速通过漏孔进入或逸出系统,并被质谱仪检测到。氦气检漏法的检测效率较高,尤其是在检测微小泄漏方面。
图4:泄露检测方法比较
在实际生产中,通常会结合多种检测方法以提高检测效率和准确性。例如,氦气检漏法适用于高精度和微小泄漏检测,而压差法则具有高精度和快速响应的特点。此外,传统的水检法虽然检测精度低,但是直观且成本低,是定位泄漏点的便捷方式。
我们会定期更新有关热设计与轻量化的技术与资讯,与您分享,供您参考,感谢您对迈泰的关注。
储能液冷Pack的液密潜在失效会涉及多个方面,如:泄漏、腐蚀和沉积、冷凝水等故障模式。
1-流体互联及组成
在储能液冷系统中,流体互连负责在各个组件之间传输冷却液,通过有效的流体互连,确保冷却液在系统中的高效循环,从而带走电池充放电过程中产生的多余热量。
密封性良好的系统可以有效防止冷却液的泄露,泄漏不仅会导致冷却液的损失,需要频繁补充,还会影响系统的散热性能和稳定稳定性,在储能中冷却液泄露还可能会造成电池短路,引发安全问题。
2-流体互连系统液密设计
流体互连系统的液密设计是确保系统在各种操作条件下保持密封性和防止流体泄露的关键环节。
图1:储能液冷系统典型部署
(1)分析系统中可能的泄漏源与风险点:
l 液冷组件的自密封性,如,在液冷流道系统与Pack箱一体设计中,部件通过焊接进行连接,焊接质量缺陷,焊合不良、气孔、裂纹等,都可能导致渗液问题。
l 结构设计不合理,如液冷箱的定位孔或螺纹孔距离流道过近,焊合不良的部位容易成为渗液的通道。
l 连接部位:液冷系统的管道连接、阀门和接头等部位是常见的泄露点,若连接结构设计不合理或制造工艺不精良,接头内部存在微小缺陷,冷却液也可能从这些缺陷处泄漏出来。
l 由于安装不当、材料老化或损伤等原因导致的泄露。
(2)密封结构设计:
l 液冷PACK使用干湿分离式冷板冷却方式,在正常工作情况下,电芯与冷却液无接触,可保障电芯正常工作。储能液冷箱一种方案是通过挤压工艺成型,流道直接集成在冷板上,然后机械加工打通冷却循环路径。在这个过程中,选择合适的焊接工艺是确保密封性的重要步骤。具体详见《储能用下箱体拼焊工艺设计》。
l 液冷管路主要用于连接液冷源与设备之间、设备之间、设备与管路之间的过渡软(硬)管连接。主要连接方式有:
快插连接:储能液冷系统的连接方式之一是采用VDA或CQC快插连。
螺纹连接:连接结构的两端均滑动连接有管道,内螺纹圈与螺纹套的螺纹连接,增加了连接的牢固性。
限位管和螺母连接:管道一端卡接有连接管路,连接管路两侧固定安装有限位管,限位管内部固定安装有橡胶垫圈和凸圈,连接管头表面开设有限位圈槽,限位管顶部转动连接有螺母,通过螺纹与限位管进行转动连接。
密封圈连接:螺纹套的内壁通过强力胶粘附有密封圈,密封圈的内壁与管道的外表面活动连接,以防止使用过程中漏液。
(3)PACK液冷板、舱内接口、舱内管路等,均考虑在常用冷却液、常用温度、流速条件下的长期防腐蚀,可保障长时间工作不出现腐蚀。操作条件对液密性的影响:
l 温度。高温影响,随着温度的升高,液体的粘度通常会降低,这可能导致液体的密封性能下降,从而影响液密性。例如,某些密封材料在高温下可能会发生变形或老化,导致泄漏。低温影响,在低温环境下,液体可能会变得粘稠,增加了流动的难度,但也可能提高密封材料的性能,从而在一定程度上增强液密性。
l 压力。 高压环境,在高压下,液体的密度和粘度可能会增加,从而提高液体的密封性能。然而,过高的压力也可能对密封材料造成损坏,导致泄漏。低压环境,在低压下,液体的密封性能可能相对较弱,特别是如果密封材料本身存在缺陷或老化,更容易发生泄漏。
l 流速。高流速,液体在高速流动时,可能会对密封面产生较大的冲击力,导致密封材料的磨损或变形,从而影响液密性。低流速,在低流速下,液体的密封性能相对较好,但这也可能掩盖一些潜在的密封问题,如微小的材料缺陷。
3-腐蚀与沉积问题
l 堵塞对秘密性的影响:
冷却液中的颗粒物、沉淀物或微生物生长都可能导致管道内部堵塞,影响冷却液的流通性,进而降低冷却效率。
污垢和结垢:冷却液中的矿物质在长时间运行后可能会在管道内壁形成沉积物,即所谓的“水垢”;也可能会因为固体颗粒沉淀、结晶、腐蚀或微生物活动而形成污垢,这些污垢会堵塞管道和冷板,增加流动阻力,降低传热效率。
泡沫问题:液冷系统中可能会产生泡沫,泡沫会附着在冷板表面,导致传热效果下降,并可能增大系统运行中的阻力,对泵造成气穴腐蚀等,损坏设备。
l 涡流对气密性的影响:
当流体在管道或缝隙中流动时,速度变化会导致涡流产生,特别是在流体经过狭窄部分或障碍物时,涡流更容易形成。流体的粘度和密度也会影响涡流的产生。粘性较高的流体更容易形成涡流,而密度较大的流体可能减弱涡流的形成。
泄漏通道:涡流会在接触表面形成旋涡,这些旋涡可能会在缝隙或不规则表面形成微小的泄漏通道,从而导致气体或液体的泄露。
表面磨损:涡流流动会导致接触表面磨损,特别是在高速流动的情况下,这种磨损会进一步降低气密性,因为磨损的表面更容易形成新的泄漏通道。
热效应:涡流流动会产生热量,这可能会导致接触面材料的变形或热膨胀,从而影响气密性,特别是在温度变化较大的系统中。
4-冷凝水问题
在某些条件下,液冷管路可能会形成冷凝水,这可能会导致设备损坏或效率降低。保温失效:如果管道的保温材料破损或老化,会导致热量散失,影响冷却效果。特别是在低温环境下,保温失效会使管道表面结霜或结冰。冻裂:在寒冷环境中,如果没有采取适当的防冻措施,管道内的冷却液可能会冻结,导致管道破裂。
解决方案
l 密封措施:确保液冷管路的进/出水管口完全封堵,防止外界潮湿空气进入电池舱。
l 除湿设备:安装除湿空调或使用除湿功能,维持电池舱内的湿度在合适范围。
l 温度控制:通过安装空调或通风系统,控制储能柜所在环境的温度和湿度,例如将温度保持在20-25摄氏度,相对湿度控制在40%-60%。
l 隔离措施:对空着的电池架进行简易隔绝,防止湿气进入装有电池簇的舱室。
我们会定期更新有关热设计与轻量化的技术与资讯,与您分享,供您参考,感谢您对迈泰的关注。
储能Pack的全密封设计是确保其安全性和长期稳定运行的关键,密封本质上是用一种装置来密闭(密封)一个缝隙或使一处接合不漏流体(气体或液体)的。全密封计设能够有效防止电池单元内的液体和气体泄漏,这对于保证储能系统的安全和稳定运行至关重要。因此,设计时既要考虑气密性也要保证液体介质的密封性。
储能Pack密封设计在实际操作中需要综合考虑材料、工艺、检测设备、环境条件以及制造过程中的多个因素,以确保其密封性能能达到预期标准。本文从Pack箱体气密、液冷循环液密及液冷工质等方面阐述储能Pack密封设计在实际工程的应用实践及注意要点。
上篇:储能Pack箱体气密性设计
密封设计有助于维持储能Pack内部的温度和压力稳定,这对电池的正常工作和性能发挥起到关键作用;并且密封设计可以减少外界环境对电池内部的影响,比如湿气、尘埃和其他污染物等,从而提高系统的可靠性和使用寿命。此外,采用合适的密封材料和结构可以有效提高密封件的耐磨性和抗老化性能,增强整个储能系统的耐久性,减少维护成本。
气密设计的一般思路是通过箱体结构分析,找出可能存在泄漏的重点区域,然后针对不同区域具体性能、功能需求采取针对性的措施。
1-箱体结构分析
箱体不仅是电池模组、电气件等的物理载体,更是整个储能系统安全、可靠运行的重要保障,是储能Pack的“骨架,一般由上盖、下箱体、支撑组件、密封件及螺栓等组成。
图1:储能pack箱体示意图及密封设计重点关注区域(如,红色箭头标注)
如上图,找出潜在泄漏点可能出现区域:
l 多个零件连接处,如:箱体上盖与下箱体装配界面、高低压连接器与箱体安装界面、外露器件与电池箱体安装接口等。
l 如果采用螺栓固定连接,安装固定处亦可能存在泄漏风险,如,电气接口与箱体前面板安装界面。
l 箱体的上盖、下箱体不能出现漏洞、缝隙,确保箱体的密封性和防护性能。
图2:浸没式液冷下箱体(钣金边框+铝型材液冷底板)
2-上盖与下箱体安装界面密封设计
上盖一般可以分为平板式和异型式两种,它们的结构特点也各不相同,比如SMC复合材料、铝制,无论是何种材质,为了减少自密封结构的复杂性,电池壳的上盖通常采用整体式设计。此外,上盖的开孔要求也应符合接口的要求,并且应将其独立于密封界面,以减少对电池包密封的影响。上盖密封设计一般遵循以下原则:
l 采用一体式零件设计,避免分件设计,确保上盖“自密封”性能的稳定。
l 定位孔、定位特征设计在上盖边缘(上盖和下托盘密封界面外侧)。
l 上盖与下箱体密封界面,需要匹配面满足“均匀”、“连续”的密封要求。
目前储能Pack下箱体主流方案有:钣金箱体+液冷板、压铸箱体+液冷板、型材一体式箱体、压铸一体式箱体等,其中型材一体式箱体与其他方案对比,具备流道承重能力好、开模成本较低等优点,应用广泛。焊接工艺的选择对密封性能影响很大,对于不同材料、厚度的焊件,选择合适的焊接方法能有效提升焊缝的质量,以保证系统的整体强度和密封性能。
另外,下箱体密封设计应当遵循如下密封原则:
l 采用封闭截面型材进行框架的搭建,接头处采用自密封的线性连接技术,如CMT焊接技术。
l 铝型材拼接的电池托盘需要设计有连续的一道或多道密封胶体。
l 下箱体集成液冷板的情况下,需要考虑使用胶体密封或采用自密封的线性连接技术,如FSW搅拌摩擦焊技术。
l 上盖与下箱体密封界面,需要匹配面满足“均匀”、“连续”的密封要求,必要时进行机加工对密封界面进行打磨处理。
图3:箱体上盖与下箱体常见密封形式
通常,储能Pack箱上盖下箱体采用折弯翻边加密封垫设计,见图2。利用紧固螺栓使上盖、下箱体与密封垫充分压实耦合,保证Pack箱满足IP67的相关要求。
3-电气、通信接口与下箱体前面板安装界面密封设计
箱体前面板(如图3),在挤出成型的型材上进行机加工开孔,用于安装电气、通信等接口,实现电流传递、通讯交互、安全控制等功能。
图4:电气、通信接口与下箱体前面板安装界面
箱体与电气、通信等接口安装界面气密性遵循以下原则:
l 接口形状设计成流线型以减少气体和液体在接口处的积聚和渗透可能性。
l 精确对位,避免接口在安装时错位导致的缝隙。
l 安装前对接口进行预密封处理,增加防震垫或密封胶,以增强初始密封效果或减少因振动导致的密封失效。
另外,紧固件的选择方面,使用高强度、高扭矩的紧固件,并在安装过程中进行多次紧固,以确保接口的紧密性。如使用碰焊螺母,其特点是能够直接连接与被连接件(箱体前面板)的壁孔进行碰焊,这种结构设计能够显著提高连接部位的气密性。
图5:使用碰焊螺母增加气密性
4-密封件选择
密封件设计和选择至关重要,因为它们直接影响到系统的可靠性和使用寿命。以下是在设计和选择储能液冷系统密封件时应考虑的关键因素:
l 密封材料必须有一定的化学、压力兼容性,同时能够耐受系统工作温度范围,包括高温和低温环境。密封件的材料选择取决于使用环境和使用寿命要求。常见的密封件材料包括橡胶、聚四氟乙烯(PTFE)、尼龙、金属等。
l 泄漏自由度:密封件必须能够适应系统在工作过程中可能出现的微小变形,以确保在各种工况下均保持良好的密封效果。一般密封垫的变形量要大于30%,小于60%,密封界面压力大于30kPa。
我们会定期更新有关热设计与轻量化的技术与资讯,与您分享,供您参考,感谢您对迈泰的关注。
在纯电动汽车中,电池包的重量约占整备质量的30%左右,电池包轻量化,对于提升整车续航里程有着重大意义。因此,对电池包高比能量的研究是新能源汽车目前的主要研究方向之一,也是实现电动汽车轻量化的主要途径,实现动力电池包轻量化可从两个方向开展:提高单体电芯的能量密度,对电池包相关辅件进行优化设计。
多材料轻量化电池包开发旨在通过采用多种轻质材料,降低电池包的重量,提高能量密度和续航里程,同时保证安全性和可靠性。电池Pack各主要部件中,质量最大的是电芯本体,其次为Pack下箱体、上盖、BMS集成部件等。
1-电池包上盖轻量化
电池箱的上盖位于动力电池箱体的上方,不受动力电池箱体侧面的影响,也不会影响整个电池组的质量,其功能主要包括密封、保护等作用。为了提高整车能效,在设计中也会考虑轻量化,采用轻质材料,如铝合金、复合材料(SMC、FRP等),可以显著减轻电池包的重量。
此外,上盖的结构设计还需要考虑制造效率和批量化要求,在结构非常异形的情况下,采用冲压成型或折弯拼焊可能较为困难。上盖的设计还需要考虑到与下箱体、密封结构件等其他部件的连接与配合,确保整个电池箱体的结构稳定性和可靠性。
2-电池包下壳体轻量化
铝合金是电池包壳体制作的理想材料,因其密度低、比强度高、热稳定性好、耐腐蚀性强、导热性好、无磁性、成型容易以及回收价值高等诸多优点。常用的铝合金材料包括6061-T6、6005A-T6和6063-T6等,这些材料具有不同的屈服强度和抗拉强度,可以满足不同的结构需求。
电池包壳体通常由铝合金型材边框和底板构成,采用6系铝合金挤压型材拼焊而成。设计时需要考虑型材断面大小及复杂性、壁厚等因素,以适应不同的结构和功能要求。例如,边框、中间隔板、底板、横梁等部件可能会采用不同的断面设计。
通过合理的结构设计和连接方式,可以有效保证壳体整体强度,降低加工难度,实现壳体减重:
l 薄壁化:通过采用薄壁设计,配合加强筋来满足强度要求,可以有效减轻材料重量。
l 中空化:在结构设计中引入中空部分,以降低材料密度。
l 尺寸优化:优化电池包的尺寸,减少不必要的材料使用。
l 拓扑优化:通过优化电池包内部组件的布局,减少材料占用空间。
l 集成模块化设计:将冷却板、电池包吊耳等部件集成在箱体中,减少单独部件的数量和重量。
3-制造轻量化技术
l 材料成型
目前电池箱材料成型工艺主要有三类:冲压、铝合金压铸和铝合金挤压成型。动力电池箱整体工艺流程包括材料成型及连接工艺,其中材料成型工艺是动力电池箱体的关键工艺。当前上壳体以冲压为主,下壳体主要工艺为挤压成型及铝合金压铸成型两种方式。
l 连接技术
电池箱体连接工艺在新能源汽车制造中至关重要,涉及多种技术和方法,以确保电池箱的结构强度和密封性。
焊接是电池箱体加工中的主要连接工艺,应用广泛。主要包括以下几种方法:
①传统熔焊:如TIG(钨极惰性气体保护焊)和MIG(金属惰性气体保护焊)。TIG焊接速度低,质量高,适用于点固焊和复杂轨迹焊接,常用于边框拼焊和边梁小件焊接。MIG焊接速度高,熔透能力强,适用于边框底板总成内部整圈焊接。
②搅拌摩擦焊:通过摩擦产生热量实现焊接,具有接头质量好、生产效率高等特点。
③冷金属过渡技术:适用于薄板材料,焊接过程无热输入,减少变形。
④激光焊:高精度、高速度,适用于复杂结构焊接。
⑤螺柱焊和凸焊:用于特定部位的快速连接,螺柱焊通过螺柱和螺母实现紧固,凸焊则通过凸点压紧实现连接。
机械连接方式主要解决薄板材料在焊接中的易焊穿和螺纹滑牙问题,包括:
①拉铆螺母:用于箱体边框密封面和内腔底板的连接,具有紧固效率高、使用成本低等优点。适用于薄板与其他部件的螺纹联接。
②钢丝螺套:用于加强铝或其他低强度机体的螺孔,提高螺钉的承载能力和螺纹的受力分布,适用于电池模组安装孔和密封面安装孔。相对于拉铆螺母,钢丝螺套强度更高且易于修复,但一般不适用于薄壁安装。
我们会定期更新有关热设计与轻量化的技术与资讯,与您分享,供您参考,感谢您对迈泰的关注。
要应对大跨度、快迭代、丰富产品线等市场需求,还要保证降本增效保质,对汽车行业而言,通过产品标准化——造车平台化无疑是项不错的策略,通过电池平台化为不同的车型匹配同一个电池包方案,或者匹配由同一种电芯组成且结构相近的电池包方案,这就意味着尽可能的多零件通用化,可以缩短开发周期、节约成本、精简产线与提高生产效率。
一、电池平台化
电池平台化方案有利于产品的统筹规划、成本的降低和产能的优化。根据整车平台的电池平台化策略,需要考虑平台各车型需求的交集与带宽,用尽量少的电池与电池方案兼容尽可能多的车型。在纯电动项目的架构开发中,合理布置集成动力电池包是至关重要的,具体工作要素包括电量与动力性能需求、碰撞安全、布置位置与空间等。
1-空间尺寸边界与电芯标准化
l 电池包可用布置位置
目前主流的动力电池布置位置为地板下方,包含前座椅下方、后座椅下方、中通道位置及脚踏位置。这种布置方式能够最大限度的获得可用面积,并且有助于降低车身重心、提高整车操纵稳定性和优化碰撞传力路径。
图1:电动车发展过中电池包布置位置
l 电池包空间布置形式演化
分体式电池包:采用分体式的电池包空间布局形式,如江淮同悦系列,能量模块由两个电池包组成,一个放在原来油箱位置,一个放在车尾箱存放备胎位置。
此外,工程师们在燃油车原来架构上不断发掘可利用空间,电池包布局出现了“工”字形、“T”字形、“土”字形的形式。
此类设计是在传统燃油车基础上做较小的改动,空间非常有限,能够装载的电池包体积和重量都很受限,因此容量也很难提升,续航里程不高。
一体式电池包:这是一种全新的产品设计思路,整车设计围绕核心零部件——电池包展开,将电池包进行模块化设计,平铺在车辆底盘上,以最大限度获得可用空间。
l 电池包安装点布置
合理布置电池包至关重要,限制要素设计离地间隙、通过性、碰撞安全和电量需求等诸多方面。
图2:电池包尺寸设计约束
整车平台需定义平台内各车型的类别、级别与定位,进而确定了车辆的大小、轴距,整车布置根据整车空间分解出电池包在X、Y、Z方向的尺寸包络,电池需要在整车给定的包络内进行布置,保证整车各系统间不出现干涉,而整备质量指标可分解出电池包的系统质量要求。
在电池尺寸这一指标上,动力电池包的设计绕不开整车空间、整备质量等硬性参考指标,这就意味着电芯的设计存在阈值,受到这个阈值的约束,电芯尺寸就会往某个特定的区间进行集中,如:方形电芯长度范围150-220mm,宽度范围在20-80mm,高度范围在100mm左右徘徊。电芯尺寸规格的变化趋势正是造车平台化与电池标准化相辅相成的结果。
然而,各车企电池平台策略、承载车型及对标准化的理解也有所差别,致使当前所呈现出来的产品方案仍有较大差异。如比亚迪的标准化策略是全面更换刀片电池,刀片电池的尺寸标准锁定为960*13.5(14)*90(102)mm,单体电压3.2/3.3V。
2-续航边界与电池电量方案开发
动力电池为整车行驶提供能量:电池容量、放电深度、能量密度影响可供电量。为满足不同车型的需求,车型的电耗差异成为重要关注项目,车辆的续航里程会受电驱、电池、整备质量、风阻、机械阻力、低压电耗及能量回收等因素的影响。电耗差别大的车型间共用电池方案的可能性弱,就需要针对性的开发个性化的电池电量方案,包括电池尺寸、质量、电量及做功率性能优化,以满足续航性能的要求。
在造车平台纯电续航里程的约束下,电池需求净放电量会受不同车型电耗的影响,需要确认平台各车型的电耗分布,才能进一步将该电耗带宽转化为电池的需求电量分布,进而确定平台所需电池电量方案。
3-动力性能边界
整车的动力性包括不同SOC、不同环境温度下的加速工况、等速工况和保电工况下的动力表现,对应到电池的变量就是电池在不同SOC和温度下的功率-电压特性,电池的功率对应整车动力系统的功率要求,电压对应驱动电机的额定电压需求。
一般对整车平台电池方案评估从常温高电量下的百公里加速时间及其电池指标分解,逐步延伸到全域全工况的电池指标分解。
二、电池箱体开发
1-电池集成与模块化
优化电池模块的设计,提高电池组的集成度和模块化,减少非活性组件,提升电池组的能量密度。
当前流行的电池包集成技术有CTP、CTB、CTC等各种形式,零件的外形、材质和组合形式等都伴随集成技术的进步发生了改变,整体方向是一体化、集成化,通过减少独立零件数量、使用一个大零件替代几个零件,形成尺寸更大、功能更多的组件。
2-电池箱体方案设计
电池箱体是动力电池系统总成的载体,对产品的安全运行和防护起着关键作用,直接影响整车的安全性。电池箱体的结构设计主要包括电池箱上壳体、下壳体等部件的壳体材料选择,制造工艺方案选择等。电池箱体上盖主要起密封作用,受力不大;电池箱体下箱体是整个动力电池系统产品的承载件,电池模组主要布置在下箱体里面,因此电池箱体内部要有嵌槽、挡板等结构措施,使电池模组在车辆行驶的状况下可靠固定,在前后、左右、上下各个方向上均不发生窜动,避免对侧壁和上盖造成冲击,影响电池箱体寿命。
图3:电池下箱体方案,a-蒙皮框架、 b-FSW焊接+围框、c-FSW焊接+围框
l 电池包安装点结构设计与连接固定
电池包安装点通常采用安装梁结构,这种结构前后贯通,前端与前舱纵梁连接,形成有效、连贯的封闭梁结构,并根据电池包重量分布,合理布置安装点。电池包与整车的固定方式包括螺栓固定、机械固定+胶接混合连接、卡扣连接等。
图4:电池包布置与安装断面
动力电池包一般通过多个吊耳结构安装至整车上,吊耳处理要承受动力电池包自身较大的自重外,还要承受汽车行进时带来的路面激励,如石块路和深坑等,此类耐久工况和误用工况对吊耳结构的强度提出更高的要求。
图5:不同吊耳连接方案:a焊接吊耳 b铝挤边框吊耳
l 电池箱体安全与保护结构
机械强度和防护:电池箱体应具备足够的机械强度,以确保其内部电池免受机械撞击和冲击。电池箱体需要能够承受振动、挤压和机械冲击等,以确保在各种条件下电池的安全性。
碰撞保护:电池箱体的设计必须考虑碰撞安全性,特别是针对侧向碰撞和底部碰撞的情况。通常采用铝制或钢制材料,并通过外框架连接到下部托盘,以提供结构刚度并增强碰撞能量吸收能力。此外,还应设计适当的碰撞吸收结构,以防止电池外壳变形和电池单元损坏。
防水防尘和防腐蚀:电池箱体需要具备防水防尘功能,通常采用IP67级别的密封胶垫来保证气密性能。此外,还应考虑防腐蚀措施,如在外部喷涂PVC涂层以增强耐腐蚀性。
防爆和泄压设计:当电池发生爆炸时,应通过平衡防爆阀等装置使能量集中定向泄放,避免进入客户舱。此外,还应采取防爆措施(如部分破坏结构)以防止设备整体破裂。
l 密封设计
电池箱体上盖与下箱体之间密封面的设计对密封性起重要作用,其设计需要配合电池箱体结构和密封圈一起设计。密封面应尽可能保持在同一个平面,避免出现较多的曲面结构。由于上盖和下箱体是通过螺栓连接,所用螺栓数目较多,因此保证孔的同轴度尤其重要,需在合理布置螺栓孔位置的同时,位置尺寸尽量圆整,且在X、Y向呈对称布置。连接螺栓数目的选择需根据密封性高低和拆装工作量大小两方面综合考虑。
图6:上下箱体密封设计方案,1-电池上盖 2-密封垫 3-电池下盖 4-金属导管
l 电气安全和短路保护
连接可靠性:电池箱体内的连接器应具有正确的极性连接,确保电池箱体的过流能力和电气/机械连接的可靠性,包括放松措施等。
电气绝缘耐压设计:模组设计采用双重绝缘防护电芯本身有一层电芯蓝膜及电芯顶帖片可以满足绝缘耐压要求,端/侧板与电芯间、电芯与底部安装面间设置绝缘耐压防护。
l 热管理设计
电池热管理开发贯穿于电池包系统设计开发全周期,包含电池温度控制、冷板、管路系统等的设计。电池热管理系统设计的主要目标是在考虑空间布置、设计成本、轻量化等条件下,通过加热或冷却控制,保证电池系统工作在相对适宜的工作温度,同时减小单体间温差,保证一致性。
我们会定期更新有关热设计与轻量化的技术与资讯,与您分享,供您参考,感谢您对迈泰的关注。
电池包是新能源汽车的核心能量源,为整车提供驱动电能。我们一般会从效率(能量密度)、安全、制造及维修成本等维度评价电池包技术的优劣。
在电池设计中,单个电芯的电压只有3-4V左右,而电动车所需的电压最低都要100V以上,现在的新车甚至有700V/800V的电压,输出功率一般也在200W,所以就需要给电池升压。为了满足电动车的电流和电压需求,就需要将不同的电芯通过串联、并联组合的方式相连。
电池包是将电芯、电子电气系统、热管理系统等通过电池框架结构——底板(托盘)、框架(金属框)、上盖板、螺栓等包络构成的,一直以来,如何将这些部件、系统更高效更安全的“打包”成为一个整体,是整个行业持续不断研究探索的议题。
上篇:电池集成技术创新与发展
动力电池成组技术的由来可以追溯到20世纪50年代,起源于前苏联与欧洲等一些国家。这项技术最初是作为一种工程和制造理念,用于确定零件的物理相似性(通用工艺路线),并建立其有效生产。
成组技术(Group Technology, GT)的核心在于通过识别和发掘生产活动中有关事物的相似性,将相似的问题归类成组,寻求解决这一组问题的相对统一的最优方案,以取得经济效益。在动力电池领域,成组技术主要涉及将电池由单体集成为电池包(Pack)的技术,包括结构、热管理、电连接设计和电池管理系统(BMS)技术。
汽车领域较早的成组技术为MTP(Module To Pack),即先由电芯集成为模组,再由模组集成为Pack。这种技术的特征是模组可拆卸和更换,具有较好的可维护性,但成组效率较低。随着技术的发展,成组技术经历了从MTP到CTP(Cell To Pack)的转变,CTP技术指将电芯直接集成到Pack的技术,取消了传统的模组结构,提升了成组效率和生产效率。近年来,行业还在探索更高集成效率的CTC(Cell To Chassis)、CTB(Cell To Body & Bracket)和MTB(Module To Body)等成组技术。
在动力电池及电化学储能领域,锂电池主要的技术进步来源于结构创新和材料创新,前者是在物理层面对“电芯—模组—电池包”进行结构优化,达到兼顾提高电池包体积能量密度与降低成本的目的;后者是在化学层面对电池材料进行探索,达到兼顾提高单体电池性能与降低成本的目的。本文注重从电池包结构集成视角探讨不同结构集成技术对电池包制造技术的影响及创新发展方向,当前动力电池集成关键技术,见下图:
1-已被淘汰的MTP
在当前这波电动汽车发展潮流的伊始,很多油改电新能源车型上市,它们延续传统油车的空间布局与造型设计,工程师们将一定数量的电芯单体通过串/并联的方式,组成一个相对较大的电芯模组,然后再将几个这样的电芯模组布置到电池包中,也就是我们熟悉的“MTP”电池包,由于电池包需要“打包”两次以上,因此需要的零部件数量十分庞大,电池包也以“里三层外三层”的形象示人,过多冗余部件也占据更多的系统体积空间和重量,使得“MTP”电池包在体积能量密度、质量能量密度表现差;并且因为燃油车设计过程并没有专门为电池预留空间,电池系统只能“见缝插针”地塞进车内,产品力低下,用户体验欠佳。
自以特斯拉为代表的全新智能化电动车平台推出以后,原生纯电动车使得电池包以更高效、规整的安装在理想的空间位置上,三电系统可以更合理的布局,整车的电子电器架构及热管理设计实现更高效的集成,车辆的能效、续航、智能化维度的产品力极大加强。
2-集成技术2.0时代——CTP
MTP结构的电池包存在显著的空间利用率问题,电芯对模组的空间利用率为80%,模组对电池包的空间利用率为50%,整体空间利用率仅为40%,模组硬件费用约占电池电池总成本的14%,这种低空间利用率结构无法满足新能源汽车的发展要求。在电芯→模组→电池包→车身集成思路的框架下,整车想要在有限的底盘空间内尽可能装载更多电量,提高体积利用率,就要考虑每个集成步骤的标准化,随着市场对续航里程需求的不断攀升,单个电池模组的体积不断增大,间接带动了CTP方案的出现。
出于安全、封装复杂程度、降本等方面的考虑,CTP结构技术应运而生。在保证电芯安全的前提下,CTP技术减少了内部线缆和结构件,相比MTP技术,CTP技术没有模组结构,直接由电芯封装成电池包再安装到车上。
目前主要有两种思路,一是将Pack看成是一个完整大模组替代内部多个小模组的结构,以宁德时代为代表;二是设计时即考虑采用无模组方案,以电池本身作为强度的参与件去设计,例如比亚迪刀片电池。
CTP技术的核心点就是取消了模组设计,电芯直接与壳体相结合,减少了端板与隔板的使用,随之而来的问题是电池组的固定以及热管理问题。
实际上CTP电池包的最初产品并非是纯无模组的设计,而是将原有的小模组合并为3个大模组和2个中模组的设计,并且两端同样存在铝制端板,所以理论上依然是MTP,但结构上确有很大的进步。
而到CTP3.0之后,宁德时代给出了更为先进的制造方式,实现了彻底的无模组设计,电芯从原来的沿高度方向立置改为侧置,同时提盒电芯间采用了全新的冷却方案,除却散热外,冷板还承担了支撑、缓冲、隔热、温控等多种功能;底壳也做了限位固定设计。
图1:宁德时代麒麟电池CTP2.0与CTP3.0对比
3-集成技术3.0时代——CTB、CTC
a. CTB技术
CTP技术是电池结构创新的一大进步,却没有突破电池包本身,在CTP技术中,电池包仍然是一个独立的零部件,相较于CTP对电池包的精简策略,CTB技术把车身底板面板与电池包上盖合二为一,电池上盖与门槛及前后横梁形成的平整密封面,通过密封胶密封乘员舱,底部通过安装点与车身组装。在设计制造电池包的时候,把电池系统作为一个整体与车身集成,电池本身的密封及防水要求可以满足,电池与乘员舱的密封相对简单,风险可控。
这样将原来的“电池包上盖-电芯-托盘”的三明治结构转化成“车身底板集成电池包上盖-电芯-托盘”的整车三明治结构,减少了因车身与电池盖连接而产生的空间损失。这种结构模式下,电池包不仅仅是能量源,同时也作为结构体参与整车的受力与传力。
图2:CTB技术结构示意
b. CTC技术
采用CTC方式后,电池包不再是一个独立的总成,而是融合为车身的一部分,优化了产品设计和生产工艺,减少整车零件数量,特别是减少了电池内部结构件与连接件,具备轻量化的先天优势,最大程度提升空间利用率,为增加电池数量、提升续驶里程提供了空间。在电化学体系本身技术不变的条件下,能够通过提升电池数量增加续驶里程。
图3:特斯拉CTC技术结构示意
如,特斯拉等车企先后推出CTC技术车型,在电芯层面可采用多功能弹性夹层结构、大面积水冷技术,叠加一体化开发带来的电池包底部防撞击空间复用技术,兼顾了成组效率、散热性和安全性,从电芯优化和整车结构防护两个维度,推进CTC技术的应用。在整车一体化开发层面,将电芯直接集成到底盘,省去模组和电池包的环节。实现大三电系统(电机、电控、电池)、小三电系统(DC/DC、OBC、PDU)、底盘系统(传动系统、驾驶系统、转向系统、制动系统)以及自动驾驶相关模块的集成,并通过智能化动力域控制器优化动力分配和降低能耗。
4-CTP、CTB和CTC技术对电池盒的具体要求变化
在传统电池包结构中,电池模组起到支撑、固定和保护电芯的作用,而电池盒箱体主要承受外部的挤压力。CTP、CTB和CTC技术的应用对电池盒的提出新的要求,具体体现在:
电池盒箱体强度要求提升:由于CTP或CTB及CTC结构中减少了或取消了模组环节,电池盒箱体不仅要承受外部的挤压力,还需要承担原本由模组承担的来自电芯的膨胀力,因此对电池盒箱体的强度要求更高。
碰撞防护能力:利用CTP技术去除电池组的侧梁后,电池将直接承受碰撞的影响,因此CTP电池组需要具备足够的抗碰撞能力。
保温、绝缘和散热需求:CTP或CTB及CTC结构在底盘承载式结构箱体的基础上,把底板型材更改为水冷板,电池盒箱体不仅要承载电芯重量,还要为电池提供热管理等功能,结构更加紧凑、制造工艺优化、自动化程度较高。
维修性便利性降低:高度集成度设计使得电池包的更换变得复杂,如在CTC结构中,电池内部电芯间充填树脂材料,导致难易更换电芯,几乎不能进行维修。
5-电池包集成度提升对电动汽车充电基础设施的影响
选择不同的电池包集成技术同时隐含选择了不同的补偿方式,CTP倾向于换电,而集成化更高的CTB/CTC则倾向于快充。
高度集成化意味着在相同的空间内可以容纳更多的电池,从而增加了电动汽车的续航里程。用户可能不再需要频繁地进行短距离充电,而是更倾向于在长途旅行中进行快速充电。因此,充电基础设施的规划需要考虑到这些变化,以确保能够满足用户的需求。
由于电池包集成度的提升,电池包的物理尺寸和结构可能发生变化,这可能影响充电接口的设计和充电设备的兼容性。
此外,电池包集成度的提升也可能影响充电速度和效率。更高效的电池管理系统和充电技术可能需要被开发和部署,以确保快速且安全的充电过程。
我们会定期更新有关热设计与轻量化的技术与资讯,与您分享,供您参考,感谢您对迈泰的关注。
新能源汽车用电池托盘和储能液冷箱在生产过程中,必要适当的表面处理是一个关键步骤,如:采用涂装、氧化处理等在金属表面形成保护层,抵御腐蚀介质的侵蚀;对需要电气隔离的组件,如电芯、水冷板、模组壁等需要建立绝缘保护膜,一般通过喷涂绝缘粉末或绝缘漆来实现绝缘;选择合适的表面处理技术不仅能够提升托盘/液冷箱的耐用性和安全性,还能满足不同应用场景的需求。本文对常见表面处理技术进行整理,以供参考。
1-清洁、打磨
在生产过程中,托盘表面可能会积累加工油污、机油残留、粉屑、灰尘等杂质。这些杂质不仅会影响电池托盘的使用寿命,还可能对电池的性能和安全造成不利影响。通过清洁打磨,可以有效去除这些杂质,确保托盘表面的洁净。清洁打磨可以有效去除表面杂质、毛刺、焊渣,使其表面光滑、平整,从而提高电池托盘/箱体的整体质量。
a.化学清洗
碱洗:碱洗主要是利用碱性溶液(如氢氧化钠、碳酸钠等)去除铝合金表面的油脂、污垢和其他有机物。碱洗通过皂化作用、乳化作用和浸透润湿作用来去除油脂,同时生成可溶于水的沉淀物,从而达到清洁的效果。碱洗通常用于去除铝合金表面的油脂、灰尘和有机污染物。
酸洗:酸洗则是利用酸性溶液(如硝酸、盐酸等)去除铝合金表面的氧化皮、锈蚀和其他无机沉积物。酸洗通过酸与金属表面的氧化物反应,将其转化为可溶性盐类,从而去除表面杂质。酸洗主要用于去除铝合金表面的氧化皮膜、锈蚀和无机盐垢。酸洗常用于金属表面的最终处理,以提高其光洁度和平整度。
b.机械打磨
生产中,通过打磨工序可以去除加工余量、修正形状误差,确保托盘/箱体表面的平滑度和精度、满足装配要求,进而提高整体性能和使用寿命。
经过清洁打磨后的表面能增加涂装材料或其他材料的处理,对后续的防腐、密封、导热、绝缘、保温等涂层的施工非常重要,对这些材料牢固的附着在托盘/箱体起到关键作用。
2-涂覆与防护膜建立
除了基础的清洁、打磨外,托盘/箱体生产中通过会采用喷涂工艺进行表面处理用以形成保护层,防止氧化、腐蚀以及满足保温隔热、绝缘耐压等不同场景的需要。
a.保温隔热
电池托盘的防凝露和保温隔热可以通过综合设计隔热保温系统、使用高效保温隔热材料、应用气凝胶、进行电池包保温设计以及喷涂发泡保温材料等路径实现。
底面喷涂PVC、发泡材料
b.绝缘耐压
电池包箱体绝缘、液冷组件绝缘,主要是防止电流泄漏,保护人员免受电击,确保电池系统的正常工作。绝缘的实现通常采用喷粉和覆膜两种方案,主流的覆膜工艺包括:室温贴膜、热压、UV光照等。
内部喷涂绝缘粉、绝缘漆
3-标志、标识
在电池托盘的显著位置设置铭牌或标签,一般通过镭射、机械雕刻等方法实现。这些标识通常采用耐磨损、耐腐蚀的介质进行制作,以保证其在整个使用期内不易磨灭。
我们会定期更新有关热设计与轻量化的技术与资讯,与您分享,供您参考,感谢您对迈泰的关注。
储能变流器作为储能系统的核心设备,是电能转换、能量管理、确保电网稳定性,提高能源使用效率等的重要工具,随着储能变流器功率单元向着高度集成化、高工作频率和大容量的发展,对散热要求越来越高。
1-散热需求变化
a.匹配更大直流舱,变流器容量不断变大,高效散热技术确保设备可靠
伴随储能电芯单体容量愈来愈大,储能系统单机容量也在同步扩大。2023年初,市面上标准20呎单舱电池容量仅为3.35MWh,进入下半年多家电芯企业相继推出310+Ah储能产品,20呎单舱的电容量也扩容至5MWh。然而,5MWh模式更新不到半年,一些头部储能紧接着又发布6MWh、8MWh系统。根据一般经验,储能变流器按负荷容量的1.2倍配置,5MWh储能系统单机容量就必须大于2.5MW,大功率需要更高效的散热技术来确保设备在持续高负载下稳定运行。
储能系统集成拓扑方案迭代演化
b.直流高压技术的应用要求器件具备更高的耐压等级和绝缘强度,功率器件散热严峻
为匹配大容量储能系统,直流高压技术成为一种技术趋势,通过电压等级的提高,实现节能增效和性能提升,1500V电压升级源于光伏,现由光伏切入储能。然而,储能PCS高压演进之路还很长,一些厂商优化开始推向2000V。直流高压技术的应用迫使储能变流器中的电力电子器件需要具备更高的耐压等级、更高的绝缘强度以适应高压工作环境。高压环境下,功率器件的散热设计变得更为重要,功率器件的pn结温度一般不能超过125℃,封装外壳的温度不超过85℃。
c.构网型储能系统需要具备复杂的控制算法、电路设计及高功率密度储能变流器
不同于跟网型储能系统电流源的本质属性,构网型储能系统本质上是电压源,能够内部设定电压参数,输出稳定的电压与频率。因此要求构网型变流器模拟同步发电机的特性,提供电压和频率的支撑,增强电力系统的稳定性,这种控制策略要求变流器具备更高的功率密度和更加复杂的控制算法,并且需要更高性能的功率器件和更复杂的电路设计来实现控制策略。如何有效地管理由于高功率密度、复杂控制策略产生的热量,在保持高性能的同时减少散热系统体积和成本成为热设计的新挑战。
2-常用散热方案比较
储能变流器的散热方案在近年来经历了显著的迭代演化,主要体现在散热技术从传统的风冷向液冷技术的转变。
a.风冷方案
风冷是储能变流器初期采用的温控形式,以空气为介质,通过风扇和散热器来实现热量的散发。风冷方案通过不断降低能耗、优化结构、改进散热材料等途径提升散热效率。在2.5MW功率等级下,风冷仍能满足要求。
b.液冷方案
随着储能系统的功率密度和能量密度不断增加,液冷PCS因为采用了高导热系数的冷却液作为介质,通过水泵驱动冷却液在冷板内循环流动,并且不受海拔和气压等因素的影响,液冷系统拥有比风冷系统更高效的散热效率,液冷方案的匹配度更高,近一两年开始探索,普及。
除全液冷储能方案外,一些厂家推出储能直冷机,采用相变直冷,无水循环。直冷方案也正在进入储能领域。
我们会定期更新有关热设计与轻量化的技术与资讯,与您分享,供您参考,感谢您对迈泰的关注。
电池包是新能源汽车、储能一体柜及集装箱的关键部件,它是通过壳体包络构成能量源,为电动汽车提供动力,为储能柜与集装箱提供消纳能力。本文结合实际工程需要,通过分析电池包机械强度、安全性、热管理及轻量化等多方面要求,对电池包用型材设计要点进行总结说明。
1-电池包壳体设计要求
a.机械强度,耐振动强度和耐冲击强度,在试验后不能有机械损坏、变形及紧固不见松动的现象,锁止机构不应收到损坏。
b.密封性,电池包的密封性直接影响到电池系统的工作安全,通常要求达到IP67防护等级,以确保电池包密封防水。
c.电池包壳体设计需要考虑热管理性能,通过适当的热管理设计,保证电池在适合的范围内工作。
d.安装固定,壳体应留有铭牌和安全标志布置位置,并为采集线、各种传感元件等安装预留足够空间和固定基础。
e.所有无极基本绝缘的连接件、端子、电触头结合后应满足相应的防护等级需求。
f.轻量化,壳体轻量化对于提升电池包能量密度有着重大意义,铝合金质轻质优是当下最可行的选择,结合实际应用通过适当的极限设计提升轻量化水平。
g.耐久性,电池包壳体的设计寿命不得低于整体产品使用寿命,使用周期内不应发生明显的塑性变形,防护等级、绝缘性能不应降低;结构具备维护方便性,包括铭牌与安全标志布置、连接件防护等。
图1典型铝合金拼焊电池包壳体
2-典型铝合金电池包壳体方案
电池包壳体常用的铝合金材料有6061-T6、6005A-T6和6063-T6等,这些材料具有不同的屈服强度和抗拉强度,可以满足不同的结构需求。这几种材料的强度大小:6061-T6>6005A-T6>6063-T6。
当前电池包壳体成型方案有铝型材焊接、铝合金铸造、铸铝加型材铝、冲压铝板焊接等,铝型材拼焊方案因其灵活性和加工方便性成为主流选择,如图1,壳体主要有铝合金型材边框、铝合金型材底板构成,采用6系铝合金挤压型材拼焊而成。铝合金铸造方案因其简化工艺和降本潜力被视为未来发展方向。
3-型材断面设计
a.断面大小及复杂性:型材断面大小用外接圆来衡量,外接圆越大,所需要的挤压力就越大;型材断面通常由多个空腔组成,以提高结构刚度和强度,通常边框、中间隔板、底板、横梁等采用不同的断面设计以适应不同的结构和功能要求。
图2典型铝合金型材断面
b.铝型材壁厚:某一特定铝型材的壁厚最小值与型材外接圆半径、形状及合金成分有关,如,6063铝合金壁厚取为1mm时,6061铝合金就要取为1.5mm左右,同等断面挤压难度:6061-T6>6005A-T6>6063-T6。电池包用型材设计中,边框型材通常选用6061-T6铝合金材料,其典型断面由多个空腔组成,壁厚最薄处约为2mm左右;底板型材也由多个空腔组成,材质一般为6061-T6、6065A-T6,起壁厚最薄处也为2mm左右;另外,在底板承重的托盘及底板液冷集成的设计方案中,一般底板均采用双面结构,底板厚度一般为10mm,壁厚及腔体内壁约为2mm。
c.型材断面尺寸公差:断面尺寸公差应根据铝型材的加工余量、使用条件、型材挤压难易程度、形状的部位来确定,对一些挤压难度大的铝型材可以改变形状或增大工艺余量、尺寸公差,来减小挤压难度,挤压出近似要求的铝型材制品,然后通过或整形或者加工满足使用要求。
此外,进行型材断面设计时需要考虑不同焊接工艺对接头、坡口、壁厚等具体要求。
我们会定期更新有关热设计与轻量化的技术与资讯,与您分享,供您参考,感谢您对迈泰的关注。
电池托盘又称电池盒或PACK箱体等,作为新能源汽车开发中十分重要的部件日益受到重视,电池托盘的设计需要平衡重量、安全、成本、材料性能等因素之间的关系。铝合金由于其密度低、强度高等优点,在保证车身性能时仍能保证其刚性,在汽车轻量化工程中得到广泛应用。
1-电池托盘焊接部位及方法选择
铝制电池托盘以挤压铝型材为基础材料,通过焊接方式将各个部件组合为一个整体,形成完整的框架结构。类似的结构在储能Pack箱中也得到了广泛的应用。
电池托盘的焊接部位通常包括底板拼接、底板与侧边的连接、侧边框的连接、横纵梁、液冷系统组件焊接及支架、吊耳等配件的焊接。在焊接方法选择时,会根据不同的材料和结构要求选择不同的焊接方法,参见下表:
2-焊接热变形影响分析
焊接作为一种局部加热的加工方法,由于热源集中在焊缝处加热,因而造成焊件上温度分布不均匀,最终导致在焊接结构内部产生了焊接变形与焊接应力。焊接热变形就是在焊接过程中由于不均匀的热输入和热输出,导致被焊件的形状和尺寸发生改变的现象。结合实际的工程项目经验,对易产生焊接热变形的部位及影响因素进行了归纳总结:
a.长直线焊接部位
实际生产中,电池托盘底板一般由2~4块铝合金型材采用搅拌摩擦焊拼接而成,焊缝较长,底板与侧板、底板与间隔梁之间连接也有较长的焊缝。长焊缝由于热输入集中,容易导致焊接区域的局部过热,从而产生热变形。
电池托盘边框焊接
b.多部件拼接处
在多部件焊接处由于焊接过程中局部高温加热和随后的冷却导致的。在焊接过程中,焊件受到不均匀的热输入,使得焊缝区域与周围母材之间的温度差异显著,从而引起热膨胀和冷缩效应,引起被焊件变形。储能Pack箱电气安装端通常设有水嘴、线束支架、横梁等,焊缝密集,极易发生变形。
焊缝密集区,托盘前侧翘起变形
c.冷板流道侧壁
液冷板一体化集成设计的电池托盘中,结构刚度较小的部位,如薄板、管道结构等,在焊接过程中不能很好的抵抗热变形,容易发生变形,如:液冷板流道侧壁很薄,一般只有2mm左右,模组安装面焊接横梁、线束支架等零件时,容易造成流道侧壁有裂纹和变形褶皱,影响整体性能。
横梁焊接导致的液冷流道腔壁热裂纹缺陷
3-焊接热变形控制方法
a.分段焊、双面焊
对于强度要求相对较低的部件采取分段焊,将焊接过程分解成多个小段进行,对称布置焊缝,将焊缝对称地布置在构建截面中中和轴附近,以使焊缝产生的变形有可能互相抵消。同时,尽量减少焊缝长度和数量,避免焊缝过度集中或交叉,可以减小焊接温度梯度,从而减少焊接变形。对于底板、底板与侧面框等强度要求高的部位,采取双面焊,增加强度的同时减少因零件较大,焊道较长产生的弯曲变形。
b.优化焊接顺序
控制焊接变形,使用刚性较小的接头形式、避免双向、三向相交的焊缝位置,以及避开高应力区。优化焊接顺序,先焊刚度较弱的区域,最后焊刚度较好的区域,例如先焊角焊缝、再焊短焊缝、后焊长焊缝;先焊横焊缝、后焊纵焊缝。合理的焊接顺序可以有效控制焊接变形,从而控制焊缝外形尺寸。
c.焊接参数调整
控制焊接参数和流程,合理设置焊接速度、焊接层数和每层焊缝的厚度。对较厚的焊缝,采用多层多通道焊接方法,每层焊缝的厚度不大于4mm,多层焊能够减小结构显微组织,提高接头性能。精确控制焊接参数,合理选择焊接电流、电压、焊条型号和焊接速度等参数,可以确保熔池形状和大小一致,从而避免因参数选择不当造成的误差。
d.焊接技能提升
提高焊工操作技术水平(大型构件或要求严格节点采用机械加工),确保焊接过程中动作一致性和规范性,减少人为因素导致的尺寸问题。
我们会定期更新有关热设计与轻量化的技术与资讯,与您分享,供您参考,感谢您对迈泰的关注。
铝合金是工业中应用最广泛的一类有色金属结构材料,尤其在材料导热性能备受关注的场景下,在需要高效热传导的场合,如电子设备散热、电动汽车三电散热、电池储能系统散热以及航空航天领域,通常被用作制造散热器、导热板、电子元件等高效传热设备。
导热率也叫导热系数,是表征材料导热性能的参数指标,它表明单位时间、单位面积、负的温度梯度下的导热量,单位为W/m·K或W/m·℃。铝合金是一种由铝和其他金属组成的合金材料,其导热性能非常优异,导热系数通常在140-200W/(m•K)之间,铝作为地壳中含量最高的金属,因热传导系数较高、密度小、价格低而受到青睐。
1-铝合金材料的导热原理
当材料的相邻区域存在温度差时,热量就会从高温区域经接触部位流向低温区域,产生热传导。金属材料内有着大量的自由电子存在,自由电子可以在金属中快速运动,可以快速实现热量的传递,晶格振动是金属热传递的另一种方式,但相对自由电子传递方式来说处于次要地位。
金属与非金属的热传导方式对比
2-影响铝合金导热性的因素
a.合金化是影响热导率的主要因素之一。合金元素通过固溶原子、析出相和中间相形式存在,这些形式会带来晶体缺陷,如空位、位错和晶格畸变,这些缺陷会增加电子散射的几率,导致自由电子数量减少,从而降低合金的热导性。不同合金元素对Al基体产生晶格畸变程度不同,对热导率的影响也不同。这种差异是由合金元素的化合价、原子体积差异、核外电子排布、凝固反应类型等多因素共同作用的结果。
b.热处理是铝合金加工过程中非常重要的环节,通过改变铝合金微观结构和相变,可以显著影响其热导性。固溶处理是将铝合金加热到一定温度,使其溶质原子充分溶解于基体中,然后快速冷却,以获得均匀的固溶体。这种处理方式可以提高材料的力学性能,但通常会降低其热导率。时效处理是通过在固溶处理后进行适当的冷变形和再加热,可以优化合金的微观组织,提高其综合性能。时效处理兼顾了合金的力学性能和热导率,使合金在保持较高强度的同时,也具有较好的导热性。退火处理通过在较低温度下保温,使合金中的第二相析出并重新分布,从而改善合金的微观组织。退火处理可以提高铝合金的塑性和韧性,但对热导率的影响因具体情况而异。
Al-Cu合金在时效过程中的晶体结构变化示意图
c.其他因素影响,杂质和第二相粒子:铝合金中的杂质和第二相粒子(如氧化物、碳化物等)会散射热载流子(电子和声子),从而降低热导率。杂质含量越高,第二相粒子越粗大,热导率通常越低。铝合金的晶粒尺寸也会影响热导率。一般来说,晶粒尺寸越小,晶界越多,热导率越低。此外,铝合金的加工方式(如轧制、挤压、锻造等)会影响其微观结构和残余应力状态,进而影响热导率。加工硬化和残余应力会降低热导率。
综上,铝合金是高导热材料的理想选择,铝合金中合金元素类型及其存在形式、热处理方式、杂质情况、晶粒大小及成型方式等因素均会影响铝合金材料的热导率,在进行材料成分设计及工艺规划时应该综合考虑。
我们会定期更新有关热设计与轻量化的技术与资讯,与您分享,供您参考,感谢您对迈泰的关注。